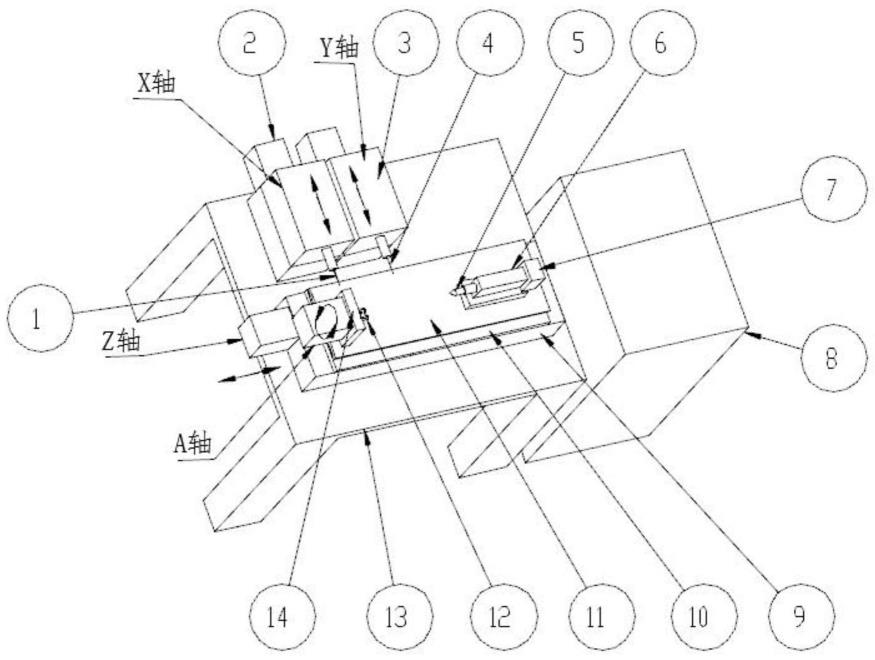
1.本发明涉及一种加工凸轮轴径向油孔的专用机床。
背景技术:2.目前加工凸轮轴径向油孔的工艺有手工钻孔工艺和加工中心钻孔工艺,手工钻孔工艺采用钻孔和孔口倒角两道工序,分别在两台式钻床上配合相应工装通过手工操作完成,手工工艺的生产效率低,为满足产能需求,往往投入的人力较多,人工操作工序多,漏加工的风险大,工人劳动强度比较大,产品质量稳定性差,加工中心钻孔工艺使用加工中心机床加工,加工中心机床完成加工需要配套的专用工装,而加工中心机床以及配套的工装成本高,导致加工成本提高。
技术实现要素:3.本发明的目的旨在提供一种加工凸轮轴径向油孔的专用机床,克服现有技术的不足,实现一次装夹完成钻孔及孔口倒角两步工序,提高生产效率,降低设备采购成本,提高产品质量稳定性,降低工人的劳动强度。
4.为实现上述目的,本发明的加工凸轮轴径向油孔的专用机床,包括定心钻、伺服电机、动力头、钻头、活动顶尖、尾座、气缸、控制系统、导轨座、拖板、工装底板、定位机构、工作台、传动头,工作台由四根等长度立柱分别与矩形面板四角固定连接形成,工作台面上一侧设置导轨座,导轨座与工作台面固定连接,导轨座上设置拖板,导轨座一端设置伺服电机(2z),伺服电机(2z)驱动拖板轴向移动,拖板上设置工装底板,工装底板随拖板轴向移动,工装底板一端设置伺服电机(2a),伺服电机(2a)前端设置传动头,传动头上设置定位机构,定位机构包括轴向定位块和角向定位销,工装底板另一端设置尾座,尾座前端设置活动顶尖后端连接气缸,活动顶尖可以旋转,气缸推动活动顶尖伸缩,工作台(13)面上另一侧设置两个平行的动力头(3x)和动力头(3y),动力头(3x)前端连接定心钻,动力头(3y)前端连接钻头,动力头(3x)和动力头(3y)下面设置导轨座和伺服电机,伺服电机引导动力头(3x)和动力头(3y)在工作台面上径向移动,导轨座与工作台面固定连接,控制系统置于控制柜内,控制柜置于工作台旁。
5.将凸轮轴前端与定位机构对接,通过定位机构的定位销定位角度,尾座气缸推动活动顶尖顶紧凸轮轴中心孔,使凸轮轴零位面贴紧定位机构,使凸轮轴准确定位在待加工位置,伺服电机(2z)驱动拖板轴向移动,控制凸轮轴轴向移动至每个待加工的油孔位置,伺服电机(2a)驱动定位机构旋转,控制凸轮轴周向转动至每个待加工的油孔位置,动力头(3x)通过伺服电机在拖板的引导下,控制定心钻钻凸轮轴周向所有孔口倒角,待孔口倒角全部加工完成后,动力头(3y)通过伺服电机在拖板的引导下,控制钻头依次钻凸轮轴所有径向油孔,待径向油孔钻孔完毕后,伺服电机(2z)、伺服电机(2a)、伺服电机(2x)和伺服电机(2y)复位。
6.本发明的加工凸轮轴径向油孔的专用机床与现有技术相比具有如下优异效果。
7.本发明的加工凸轮轴径向油孔的专用机床,采用一体式组装结构,通过传动头上的定位机构和顶尖座上活动顶尖将凸轮轴准确而牢固的定位在待加工位置,定位机构设计时直接选用凸轮轴零位面作为定位面,减少油孔长度累积误差,定位机构与凸轮轴无相对运动,避免了凸轮轴定位面划伤风险,在伺服电机(2z)和伺服电机(2a)的作用下,使凸轮轴周向各部位的径向油孔定位加工准确无误,在伺服电机(2x)和伺服电机(2y)的作用下,使孔口倒角和油孔加工顺畅、简洁,在一台机床上完成凸轮轴径向油孔加工,提高了生产效率,提高了产品质量稳定性,降低了工人的劳动强度,在保障凸轮轴径向油孔加工精度的质量下,规避了高端机床加工中心设备的购置,避免了高端机床加工中心设备高要求、高成本给企业带来的高成本投入。
附图说明
8.图1为本发明的加工凸轮轴径向油孔的专用机床示意图。
9.其中:1、为定心钻,2、为伺服电机,3、为动力头,4、为钻头,5、为活动顶尖,6、为尾座,7、为气缸,8、为控制系统,9、为导轨座,10、为拖板,11、为工装底板,12、定位机构,13、工作台,14、传动头。
具体实施方式
10.下面结合附图对本发明的加工凸轮轴径向油孔的专用机床做进一步的详细说明。
11.图1所示的加工凸轮轴径向油孔的专用机床,包括定心钻(1)、伺服电机(2)、动力头(3)、钻头(4)、活动顶尖(5)、尾座(6)、气缸(7)、控制系统(8)、导轨座(9)、拖板(10)、工装底板(11)、定位机构(12)、工作台(13)、传动头(14),工作台(13)由四根等长度立柱分别与矩形面板四角固定连接形成,工作台(13)面上一侧设置导轨座(9),导轨座(9)与工作台(13)面固定连接,导轨座(9)上设置拖板(10),导轨座(9)一端设置伺服电机(2z),伺服电机(2z)驱动拖板(10)轴向移动,拖板(10)上设置工装底板(11),工装底板(11)随拖板(10)轴向移动,工装底板(11)一端设置伺服电机(2a),伺服电机(2a)前端设置传动头(14),传动头(14)上设置定位机构(12),定位机构(12)包括轴向定位块和角向定位销,工装底板(11)另一端设置尾座(6),尾座(6)前端设置活动顶尖(5)后端连接气缸(7),活动顶尖(5)可以旋转,气缸(7)推动活动顶尖(5)伸缩,工作台(13)面上另一侧设置两个平行的动力头(3x)和动力头(3y),动力头(3x)前端连接定心钻(1),动力头(3y)前端连接钻头(4),动力头(3x)和动力头(3y)下面设置导轨座(9)和伺服电机(2),伺服电机(2)引导动力头(3x)和动力头(3y)在工作台(13)面上径向移动,导轨座(9)与工作台(13)面固定连接,控制系统(8)置于控制柜内,控制柜置于工作台(13)旁。
12.将凸轮轴前端与定位机构对接,通过定位机构的定位销定位角度,尾座气缸推动活动顶尖顶紧凸轮轴中心孔,使凸轮轴零位面贴紧定位机构,使凸轮轴准确定位在待加工位置,伺服电机(2z)驱动拖板轴向移动,控制凸轮轴轴向移动至每个待加工的油孔位置,伺服电机(2a)驱动定位机构旋转,控制凸轮轴周向转动至每个待加工的油孔位置,动力头(3x)通过伺服电机在拖板的引导下,控制定心钻钻凸轮轴周向所有孔口倒角,待孔口倒角全部加工完成后,动力头(3y)通过伺服电机在拖板的引导下,控制钻头依次钻凸轮轴所有径向油孔,待径向油孔钻孔完毕后,伺服电机(2z)、伺服电机(2a)、伺服电机(2x)和伺服电
机(2y)复位。
技术特征:1.一种加工凸轮轴径向油孔的专用机床,包括定心钻(1)、伺服电机(2)、动力头(3)、钻头(4)、活动顶尖(5)、尾座(6)、气缸(7)、控制系统(8)、导轨座(9)、拖板(10)、工装底板(11)、定位机构(12)、工作台(13)、传动头(14),其特征在于工作台(13)由四根等长度立柱分别与矩形面板四角固定连接形成,工作台(13)面上一侧设置导轨座(9),导轨座(9)与工作台(13)面固定连接,导轨座(9)上设置拖板(10),导轨座(9)一端设置伺服电机(2z),伺服电机(2z)驱动拖板(10)轴向移动,拖板(10)上设置工装底板(11),工装底板(11)随拖板(10)轴向移动,工装底板(11)一端设置伺服电机(2a),伺服电机(2a)前端设置传动头(14),传动头(14)上设置定位机构(12),定位机构(12)包括轴向定位块和角向定位销,工装底板(11)另一端设置尾座(6),尾座(6)前端设置活动顶尖(5)后端连接气缸(7),活动顶尖(5)可以旋转,气缸(7)推动活动顶尖(5)伸缩,工作台(13)面上另一侧设置两个平行的动力头(3x)和动力头(3y),动力头(3x)前端连接定心钻(1),动力头(3y)前端连接钻头(4),动力头(3x)和动力头(3y)下面设置导轨座(9)和伺服电机(2),伺服电机(2)引导动力头(3x)和动力头(3y)在工作台(13)面上径向移动,导轨座(9)与工作台(13)面固定连接,控制系统(8)置于控制柜内,控制柜置于工作台(13)旁。2.根据权利要求1所述的加工凸轮轴径向油孔的专用机床,其特征在于将凸轮轴前端与定位机构对接,通过定位机构的定位销定位角度,尾座气缸推动活动顶尖顶紧凸轮轴中心孔,使凸轮轴零位面贴紧定位机构,使凸轮轴准确定位在待加工位置,伺服电机(2z)驱动拖板轴向移动,控制凸轮轴轴向移动至每个待加工的油孔位置,伺服电机(2a)驱动定位机构旋转,控制凸轮轴周向转动至每个待加工的油孔位置,动力头(3x)通过伺服电机在拖板的引导下,控制定心钻钻凸轮轴周向所有孔口倒角,待孔口倒角全部加工完成后,动力头(3y)通过伺服电机在拖板的引导下,控制钻头依次钻凸轮轴所有径向油孔,待径向油孔钻孔完毕后,伺服电机(2z)、伺服电机(2a)、伺服电机(2x)和伺服电机(2y)复位。
技术总结本发明公开了一种加工凸轮轴径向油孔的专用机床,包括定心钻(1)、伺服电机(2)、动力头(3)、钻头(4)、活动顶尖(5)、尾座(6)、气缸(7)、控制系统(8)、导轨座(9)、拖板(10)、工装底板(11)、定位机构(12)、工作台(13)、传动头(14),通过传动头上的定位机构和顶尖座上活动顶尖将凸轮轴准确而牢固的定位在待加工位置,在一台机床上完成凸轮轴径向油孔加工,提高了生产效率,提高了产品质量稳定性,降低了工人的劳动强度,在保障凸轮轴径向油孔加工精度的质量下,规避了高端机床加工中心设备的购置,避免了高端机床加工中心设备高要求、高成本给企业带来的高成本投入。带来的高成本投入。
技术研发人员:朱振滔 杨启明 余天 纪金强 徐道广 俞协 余巧 程志生 王刚
受保护的技术使用者:江西同欣机械制造股份有限公司
技术研发日:2021.02.03
技术公布日:2022/8/4