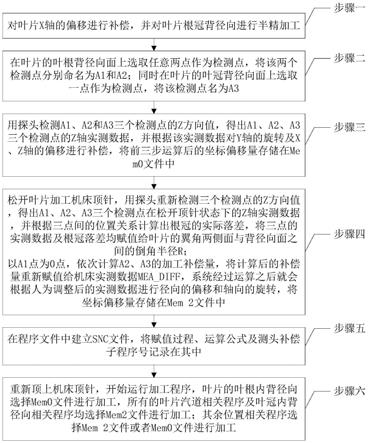
1.本发明涉及一种叶片的数控加工技术。
背景技术:2.对于y436型汽轮机组带翼角叶片,总长455.46mm,汽道长343mm,汽道薄且靠近叶冠侧弦宽很小,容易变形,五轴机床加工时受多因素影响,根冠径向位置度无法保证同一平面,叶冠相对叶根落差在0.1-0.8不等;现有的加工方案为:根据加工情况摸索根冠落差的大致规律,通过调整余量来保证根冠位置度的一致性,但此叶片落差值变化较大,给加工带来很大难度,并且通过现有的加工方式加工出来的叶片平面位置度以及一致性都很差。
技术实现要素:3.本发明的目的是为了解决利用现有的加工方式对叶片进行加工时,存在平面位置度差以及一致性差问题,提出了一种叶片自适应补偿平面位置度的数控加工方法。
4.本发明所述的一种叶片自适应补偿平面位置度的数控加工方法包括以下步骤:
5.步骤一、对叶片x轴的偏移进行补偿,并对叶片根冠背径向进行半精加工;
6.步骤二、在叶片的叶根背径向面上选取任意两点作为检测点,将该两个检测点分别命名为a1和a2;同时在叶片的叶冠背径向面上选取一点作为检测点,将该检测点名为a3;
7.步骤三、用探头检测步骤二选取的a1、a2和a3三个检测点的z方向值,得出a1、a2、a3三个检测点的z轴实测数据,并根据该实测数据对y轴的旋转及x、z轴的偏移进行补偿,将前三步运算后的坐标偏移量存储在mem 0文件中;其中,x轴为叶高方向,y轴为轴向方向,z轴为径向方向;
8.步骤四、松开叶片加工机床顶针,用探头重新检测步骤二选取的a1、a2和a3三个检测点的z方向值,得出a1、a2、a3三个检测点在松开顶针状态下的z轴实测数据,并根据三点间的位置关系计算出根冠的实际落差,将三点的实测数据及根冠落差均赋值给叶片的翼角两侧面与背径向面之间的倒角半径r;以a1点为0点,依次计算a2、a3的加工补偿量,将计算后的补偿量重新赋值给机床实测数据mea_diff,系统经过运算之后就会根据人为调整后的实测数据进行径向的偏移和轴向的旋转,将坐标偏移量存储在mem 2文件中;
9.步骤五、在程序文件中建立snc文件,将赋值过程、运算公式及测头补偿子程序号记录在其中;
10.步骤六、重新顶上机床顶针,开始运行加工程序,叶片的叶根内背径向选择mem 0文件进行加工,所有的叶片汽道相关程序及叶冠内背径向相关程序均选择mem 2文件进行加工;其余位置相关程序选择mem 2文件或者mem 0文件进行加工。
11.本发明的有益效果是:通过改变加工方式,使用程序自动调整,有效的解决了平面位置度差的问题,屏蔽掉了叶片弹性变形及顶针孔不一致带来的问题,消除了机床的换向间隙,一致性好,保证所有叶片根冠位置度均在0.05mm以内,提升了叶片质量,节省了加工周期。
附图说明
12.图1为具体实施方式一所述的一种叶片自适应补偿平面位置度的数控加工方法流程图。
具体实施方式
13.具体实施方式一:结合图1说明本实施方式,本实施方式所述的一种叶片自适应补偿平面位置度的数控加工方法,其特征在于,该加工方法包括以下步骤:
14.步骤一、首先对叶片x轴的偏移进行补偿,并对叶片根冠背径向进行半精加工,保证后续测量的准确性,方便补偿;
15.步骤二、在叶片的叶根背径向面上选取任意两点作为检测点,将该两个检测点分别命名为a1和a2;同时在叶片的叶冠背径向面上选取一点作为检测点,将该检测点名为a3;
16.步骤三、用探头检测步骤二选取的a1、a2和a3三个检测点的z方向值,得出a1、a2、a3三个检测点的z轴实测数据,并根据该实测数据对y轴的旋转及x、z轴的偏移进行补偿,,确保叶片在少余量且的顶紧的状态下处于理论位置,程序运行后生成0_bft文件,坐标偏移量存储在mem 0文件中;其中,x轴为叶高方向,y轴为轴向方向,z轴为径向方向;
17.步骤四、松开叶片加工机床顶针,用探头重新检测步骤二选取的a1、a2和a3三个检测点的z方向值,得出a1、a2、a3三个检测点在松开顶针状态下的z轴实测数据,并根据三点间的位置关系计算出根冠的实际落差,将三点的实测数据及根冠落差均赋值给机床变量r参数;以a1点为0点,依次计算a2、a3的加工补偿量,将计算后的补偿量重新赋值给机床实测数据,系统会根据人为调整后的实测数据进行径向偏移和轴向旋转的补偿,程序运行后生成2_bft文件,将坐标偏移量存储在mem 2文件中;
18.步骤五、在程序文件中建立snc文件,将赋值过程、运算公式及测头补偿子程序号记录在其中,用于保证程序计算后输出的文件自带该运算过程;
19.步骤六、重新顶上机床顶针,开始运行加工程序,叶片的叶根内背径向选择mem 0文件进行加工,所有的叶片汽道相关程序及叶冠内背径向相关程序均选择mem 2文件进行加工;其余位置相关程序选择mem 2文件或者mem 0文件进行加工。
20.在本实施方式中,按照测量点间的关系推算公式,计算根冠背径向面的落差;将实际测量数据赋值给r参数,并进行公式运算,以实测数据调整根冠位置度补偿量。
21.具体实施方式二:本实施方式是对具体实施方式一所述的一种叶片自适应补偿平面位置度的数控加工方法进一步限定,在本实施方式中,步骤四中得出补偿量的具体算法为:根据a1、a2和a3三个检测点的坐标值计算补偿系数k以及a1和a2两点之间的z向落差,得出叶冠的补偿量。
22.在本实施方式中,补偿量包括旋转量和偏移量。
23.具体实施方式三:本实施方式是对具体实施方式一所述的一种叶片自适应补偿平面位置度的数控加工方法进一步限定,在本实施方式中,补偿系数k的公式为:k=(a3-a1)/(a2-a1)。
24.在本实施方式中,补偿系数k等于7.1。
技术特征:1.一种叶片自适应补偿平面位置度的数控加工方法,其特征在于,该加工方法包括以下步骤:步骤一、对叶片x轴的偏移进行补偿,并对叶片根冠背径向进行半精加工;步骤二、在叶片的叶根背径向面上选取任意两点作为检测点,将该两个检测点分别命名为a1和a2;同时在叶片的叶冠背径向面上选取一点作为检测点,将该检测点名为a3;步骤三、用探头检测步骤二选取的a1、a2和a3三个检测点的z方向值,得出a1、a2、a3三个检测点的z轴实测数据,并根据该实测数据对y轴的旋转及x、z轴的偏移进行补偿,将前三步运算后的坐标偏移量存储在mem 0文件中;其中,x轴为叶高方向,y轴为轴向方向,z轴为径向方向;步骤四、松开叶片加工机床顶针,用探头重新检测步骤二选取的a1、a2和a3三个检测点的z方向值,得出a1、a2、a3三个检测点在松开顶针状态下的z轴实测数据,并根据三点间的位置关系计算出根冠的实际落差,将三点的实测数据及根冠落差均赋值给叶片的翼角两侧面与背径向面之间的倒角半径r;以a1点为0点,依次计算a2、a3的加工补偿量,将计算后的补偿量重新赋值给机床实测数据mea_diff,系统经过运算之后就会根据人为调整后的实测数据进行径向的偏移和轴向的旋转,将坐标偏移量存储在mem 2文件中;步骤五、在程序文件中建立snc文件,将赋值过程、运算公式及测头补偿子程序号记录在其中;步骤六、重新顶上机床顶针,开始运行加工程序,叶片的叶根内背径向选择mem 0文件进行加工,所有的叶片汽道相关程序及叶冠内背径向相关程序均选择mem 2文件进行加工;其余位置相关程序选择mem 2文件或者mem 0文件进行加工。2.根据权利要求1所述的一种叶片自适应补偿平面位置度的数控加工方法,其特征在于,步骤四中得出补偿量的具体算法为:根据a1、a2和a3三个检测点的坐标值计算补偿系数k,并根据a1和a2两点之间的z向落差,得出叶冠的补偿量。3.根据权利要求2所述的一种叶片自适应补偿平面位置度的数控加工方法,其特征在于,补偿系数k的公式为:k=(a3-a1)/(a2-a1)。
技术总结一种叶片自适应补偿平面位置度的数控加工方法,涉及一种叶片的数控加工技术,为了解决利用现有的加工方式对叶片进行加工时,存在平面位置度差以及一致性差问题。本发明对补偿X轴的叶片根冠背径向面进行半精加工,在叶根和叶冠背径向选取检测点;机床系统根据探头检测出的三点Z方向值,对叶片Y轴的旋转及X、Z轴的偏移进行补偿,并存储在Mem 0文件中;而后松开机床顶针,对三点重新进行测量,并根据三点间的位置关系计算出根冠的理论落差,再将计算后的补偿量重新赋值给机床实测数据,并存储在Mem 2文件中;叶根内背径向选择Mem 0文件,汽道相关程序及叶冠内背径向相关程序均选择Mem2文件。有益效果为消除了机床的换向间隙,一致性好。一致性好。一致性好。
技术研发人员:徐宝玉 刘蓉 闫原 杨佳财 车德健 齐琳倩 于华 董志峰 焦子虎
受保护的技术使用者:哈尔滨汽轮机厂有限责任公司
技术研发日:2021.12.21
技术公布日:2022/3/8