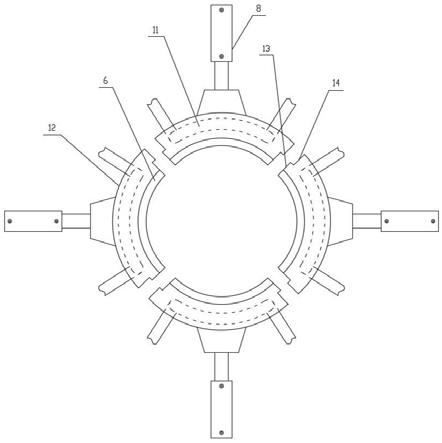
1.本实用新型涉及锻造模具技术领域,特别是一种起重机大直径双沿轮锻造用中模。
背景技术:2.起重机大直径双沿轮的轮槽是重要受力部位,尺寸精度要求比较严格,内部组织要求比较致密,为了达到性能和尺寸的要求,一般采用锻造毛坯,然后再对毛坯进行机加工,将轮槽部分的钢材切削、打磨掉,这种加工方式既浪费钢材原料,又浪费热加工电能,还浪费工工时、增加机床磨损、增加工人劳动强度。而且传统锻造模具的中模为一个整体且固定在机架上不能移动,中模的内腔为圆筒状,锻造完成时工件充满中模的内腔,不易脱模,部分模具为了降低脱模难度,中模的内腔设置有较大的拔模斜度,这虽然使脱模变得容易,但是会造成工件外表面加工量不均匀,不利于后续的机加工。
技术实现要素:3.本实用新型的目的是提供一种起重机大直径双沿轮锻造用中模,用于解决现有技术中起重机车轮的锻造模具脱模难度大,而且无法直接锻造出轮槽,使得后续机加工强度大,从而造成资源浪费的问题。
4.为实现上述目的,本实用新型采用以下技术方案:一种起重机大直径双沿轮锻造用中模,包括中模板,中模板为空心的圆柱状结构,中模板的内壁上设置有与轮槽形状相匹配的挡块;中模板由若干块弧形结构的分模板拼接而成,每块分模板的外侧水平设置有水平液压缸。
5.可选地,每块分模板的内部设置有冷却通道,冷却通道的两端分别为冷却水的进水口和出水口。
6.可选地,冷却通道为倒置的u型结构,冷却通道的水平段位于分模板中间高度的位置。
7.可选地,每块分模板的拼接处设置有拼接块和拼接槽,每块分模板上的拼接块与其相邻的分模板上的拼接槽相匹配。
8.可选地,水平液压缸设置在分模板外侧的中间位置,所有水平液压缸的轴线均相交在中模板的轴线上。
9.可选地,挡块的上下两个棱边均做圆角处理。
10.可选地,中模板的底部设置有用于定位的限位槽。
11.本实用新型的起重机大直径双沿轮锻造用中模具有以下优点:
12.(1)分模板能够在水平液压缸的作用下打开或闭合,闭合时水平液压缸向内推动分模板,使所有分模板围成一个整体的中模板进行锻压操作;打开时水平液压缸向外拉动分模板,使所有分模板打开,方便工件脱模;挡块的位置即为轮槽的结构,通过锻造能够直接加工出轮槽,减少了后续机加工的工作量,也减少了资源的浪费。
13.(2)各个分模板的内部均设置有冷却通道,锻造时冷却水不断流过冷却通道将中模板的热量吸收并带出,降低了中模板内表面变形、烧毁的风险,增加中模的使用寿命,还能够保证锻件尺寸形状精度准确,提高锻件质量。
14.(3)拼接块和拼接槽能够使分模板的拼接更精准、快速,确保中模板的完整性。
附图说明
15.图1是本实用新型的结构示意图。
16.图2是冷却通道的结构示意图。
17.图3是放置毛坯时上模、中模、下模的配合示意图。
18.图4是锻压时上模、中模、下模的配合示意图。
具体实施方式
19.下面结合附图对本实用新型做进一步说明。
20.如图1-图4所示,一种起重机大直径双沿轮锻造用中模,该中模需要与下模和上模配合使用,下模设置在中模的底部,下模包括下模板1和升降液压缸2,下模板1水平设置,升降液压缸2设置在下模板1的底部,升降液压缸2能够带动下模板1上下移动,下模板1的顶部固定连接有定位杆3,定位杆3用于定位毛坯的位置,下模板1的顶部还设置有环形的限位凸起4,限位凸起4用来定位中模板5的位置,定位杆3位于限位凸起4的圆心位置。
21.中模包括中模板5,中模板5为空心的圆柱状结构,中模板5的底部设置有限位槽7,中模板5的内壁上设置有与轮槽形状相匹配的挡块6,挡块6的上下两个棱边均做圆角处理,便于脱模。挡块6与中模板5的顶部、底部均间隔设置,挡块6与中模板5底部之间的间隔、挡块6与中模板5顶部之间的间隔即为双沿轮的两个沿。中模板5由若干块弧形结构的分模板12拼接而成,每块分模板12的拼接处设置有拼接块13和拼接槽14,每块分模板12上的拼接块13与其相邻的分模板12上的拼接槽14相匹配,拼接块13和拼接槽14能够使分模板12的拼接更精准、快速,确保中模板5的完整性。每块分模板12的外侧水平设置有水平液压缸8,水平液压缸8设置在分模板12外侧的中间位置,所有水平液压缸8的轴线均相交在中模板5的轴线上,锻压时,水平液压缸8向内推动分模板12,使分模板12底部的限位槽7与下模板1顶部的限位凸起4配合,分模板12拼接成一个完整的中模板5;脱模时,水平液压缸8向外拉动分模板12,使分模板12打开,毛坯很容易从模具中取出,模具不用预留拔模斜度,工件锻造出来之后很匀称,不会使后续机加工的加工量不均匀。每块分模板12的内部设置有冷却通道11,冷却通道11的两端分别为冷却水的进水口和出水口,冷却通道11为倒置的u型结构,冷却通道11的水平段位于分模板12中间高度的位置,锻压时,冷却水持续流过冷却通道11,将中模板5的热量吸收并带出,降低了中模板5内表面变形、烧毁的风险,延长中模的使用寿命,还能够保证锻件尺寸形状精度准确,提高锻件质量;而且降温后的毛坯不易与中模板5的内表面粘连,降低了脱模的困难程度。
22.上模位于中模的顶部,上模包括上模板9和锻压液压缸10,上模板9水平设置且底面平整,锻压液压缸10设置在上模板9的顶部,锻压时,锻压液压缸10能够带动上模板9对毛坯进行冲击,使毛坯填充满模具的型腔,初步锻造出带轮槽的双沿轮。
23.本实用新型的工作过程如下:在使用本申请中的中模进行锻造之前,毛坯需要进
行一次锻压操作,在毛坯的底部锻造出单沿,将毛坯的中心进行冲孔处理,然后再将锻压后的毛坯放在下模板1上,毛坯的中心套在定位杆3上,确定好毛坯的位置;随后利用水平液压缸8带动分模板12向中间靠拢拼接成一个完整的中模板5,中模板5底部的限位槽7与下模板1上的限位凸起4配合,确定好中模板5的位置;中模板5和下模板1共同组成一个型腔,毛坯位于型腔内,毛坯的单沿位于挡块6与下模板1之间的间隔内,然后利用锻压液压缸10带动上模板9对毛坯进行不断的冲压,使毛坯充满整个型腔,毛坯就被锻造成双沿轮的形状,其中定位杆3的高度要低于中模板5的高度,这样才不会影响上模板9对毛坯的锻压操作;在锻压过程中,冷却通道11内持续有冷却水流过;脱模时,水平液压缸8将分模板12打开,然后下模板1下行,将锻造后的工件取出,脱模操作简便快捷。锻造后的工件以具有双沿轮的基本雏形,后续机加工的工作量小,减少了钢材原料的浪费,减轻了工人的劳动强度。
24.以上所描述的实施例仅仅是本实用新型的部分实施例,而不是全部的实施例。基于本实用新型中的实施例,本领域普通技术人员在没有做出创造性劳动的前提下所获得的其他所有实施例,都属于本实用新型的保护范围。
技术特征:1.一种起重机大直径双沿轮锻造用中模,其特征在于:包括中模板,中模板为空心的圆柱状结构,中模板的内壁上设置有与轮槽形状相匹配的挡块;中模板由若干块弧形结构的分模板拼接而成,每块分模板的外侧水平设置有水平液压缸。2.如权利要求1所述的起重机大直径双沿轮锻造用中模,其特征在于:每块分模板的内部设置有冷却通道,冷却通道的两端分别为冷却水的进水口和出水口。3.如权利要求2所述的起重机大直径双沿轮锻造用中模,其特征在于:冷却通道为倒置的u型结构,冷却通道的水平段位于分模板中间高度的位置。4.如权利要求1所述的起重机大直径双沿轮锻造用中模,其特征在于:每块分模板的拼接处设置有拼接块和拼接槽,每块分模板上的拼接块与其相邻的分模板上的拼接槽相匹配。5.如权利要求1所述的起重机大直径双沿轮锻造用中模,其特征在于:水平液压缸设置在分模板外侧的中间位置,所有水平液压缸的轴线均相交在中模板的轴线上。6.如权利要求1所述的起重机大直径双沿轮锻造用中模,其特征在于:挡块的上下两个棱边均做圆角处理。7.如权利要求1所述的起重机大直径双沿轮锻造用中模,其特征在于:中模板的底部设置有用于定位的限位槽。
技术总结本实用新型公开了一种起重机大直径双沿轮锻造用中模,包括中模板,中模板为空心的圆柱状结构,中模板的内壁上设置有与轮槽形状相匹配的挡块;中模板由若干块弧形结构的分模板拼接而成,每块分模板的外侧水平设置有水平液压缸;本实用新型用于解决现有技术中起重机车轮的锻造模具脱模难度大,而且无法直接锻造出轮槽,使得后续机加工强度大,从而造成资源浪费的问题。费的问题。费的问题。
技术研发人员:高明利 王国防 任海涛 姬宏贇 王允 王庆豪 张士杰 陈海锋 郭献礼
受保护的技术使用者:河南省矿山起重机有限公司
技术研发日:2021.12.16
技术公布日:2022/4/26