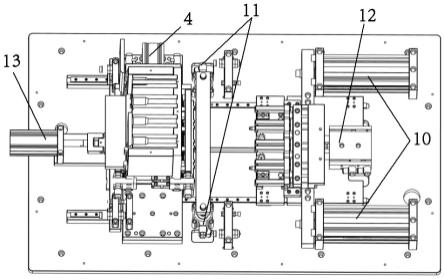
1.本发明涉及机械自动化设备技术领域,具体来说是一种自动装料装置。
背景技术:2.随着当前招工困难,人力成本高,和作业人员的安全,加工工艺上的变化等各方面环境下,过多的人力资源需求会增加人力成本,降低盈利。现有的机械生产过程中,通常需要人力装卸产品,搬运流动夹具,这会大大影响效率。因此,由机器替代人工完成装料过程时非常有必要的。
技术实现要素:3.本发明的目的在于解决现有技术中人工装料效率低下的问题,提供一种自动装料装置,能够大大提升工作效率。
4.为了实现上述目的,设计一种自动装料装置,其特征在于包括若干原材分离机构,所述原材分离机构上部为竖直设置的原料通道,原材分离机构为分离腔体,腔体内设有挡块,挡块位于原料通道下方,且和原料通道存有间隙,腔体内还设有拨块,由第一气缸驱动;若干夹具,夹具内设有弹簧夹紧机构,夹具由设置于自动装料装置的凸台驱动弹簧夹紧机构来控制启闭,所述弹簧夹紧机构一侧设有压块和弹簧,压块的端部为斜面,所述弹簧夹紧机构还包括无头螺丝,用于调整弹簧的压缩量。
5.本发明还包括如下优选的技术方案:1.若干原材分离机构沿同一水平横向设置,由第一气缸统一驱动。
6.2.分离腔体左侧底部和右侧底部分别设有两个不同的导向槽。
7.3.导向槽下方设有定位槽。
8.4.包括第二气缸,用于驱动夹具移动。
9.5.包括第三气缸,用于压住夹具。
10.6.包括第四气缸,用于顶出夹具内的残料。
11.7.包括第五气缸,用于把原材装入夹具。
12.本发明同现有技术相比,其优点在于:1.由机器替代人工进行装料,提升了工作效率,降低了人工成本。在设计过程中有过很多种机构的概念图;2.设计的弹簧夹具机构经过不断优化和模拟,结构简单,精度高,制作成本低,组装调试简便。
附图说明
13.图1 是本发明整体结构示意图;图2是本发明整体结构俯视图;图3是本发明原材分离机构结构示意图;
图4是本发明图3中a部分放大图;图5是本发明图3中b部分放大图;图6是本发明弹簧夹紧机构结构示意图;图7是本发明图6中c部分放大图;图8是本发明图7的放大图;图9是本发明第三气缸和第四气缸部分示意图;图10是本发明第五气缸部分结构示意图;图11是本发明图10中d部分放大图;图12是本发明夹具更换示意图;图中:1.原料通道
ꢀꢀ
2.挡块
ꢀꢀ
3.拨块
ꢀꢀ
4.第一气缸
ꢀꢀ
5.凸台
ꢀꢀ
6.弹簧夹紧机构
ꢀꢀ
7.压块
ꢀꢀ
8.弹簧
ꢀꢀ
9.无头螺丝
ꢀꢀ
10.第二气缸
ꢀꢀ
11.第三气缸
ꢀꢀ
12.第四气缸
ꢀꢀ
13.第五气缸
ꢀꢀ
14.原材
ꢀꢀ
15.镶块
ꢀꢀ
16.顶料销
ꢀꢀ
17.圆线弹簧。
具体实施方式
14.参见图1和图2,本发明设计一种自动装料装置,包括原材分离机构和夹具,所述原材分离机构上部为竖直设置的原料通道1,原材分离机构为分离腔体,腔体内设有挡块2,挡块2位于原料通道1下方,且和原料通道1存有间隙,腔体内还设有拨块3,由第一气缸4驱动;夹具内设有弹簧夹紧机构,夹具由设置于自动装料装置的凸台驱动弹簧夹紧机构来控制启闭,所述弹簧夹紧机构一侧设有压块和弹簧,压块的端部为斜面,所述弹簧夹紧机构还包括无头螺丝,用于调整弹簧的压缩量。
15.本发明所述的一种自动装料装置的工作原理及步骤如下:1.如图3-图5所示,原材分离机构为分离腔体,上部为竖直设置的原料通道1,分离腔体左侧底部和右侧底部分别设有两个不同的导向槽,导向槽下方设有定位槽。第一气缸4控制拨块3水平运动,通过拨块3的运动控制原材落入左边的导向槽或右边的导向槽。第一气缸4伸出,拨块3推动原材掉入右边的导向槽,导向旋转90
°
掉入下方定位槽内。第一气缸4缩回,拨块3推动原材掉入左边的导向槽,导向旋转90
°
掉入下方定位槽内。
16.2.如图6-图8所示,第二气缸10用于驱动夹具移动,夹具内设有弹簧夹紧机构,弹簧夹紧机构一侧设有压块和弹簧。第二气缸10伸出,夹具向前移动,当凸台5顶向夹具里面的弹簧时,夹具就会打开。
17.如图8所示,弹簧夹紧机构的工作原理如下:在设计弹簧夹紧机构过程中有过很多种机构的概念图。遇到问题是设计空间不够,不易组装调试,加工结构复杂,要求精度高和制作成本高等问题。最终经过不断优化改进和模拟,设计出如图8所示的弹簧夹紧机构。正常状态下为压紧状态。
18.a.无头螺丝是调节矩形弹簧的压缩量长度,压缩量长短直接影响压块7压持原材料力的大小;b.弹簧力向左经过斜面16度角度转换向下压持;c.顶料销清除废料后,由圆线弹簧复位。
19.3.如图9所示,第三气缸11用于压住夹具。第四气缸12用于顶出夹具内的残料。
20.4.如图10和图11所示,第五气缸13用于把原材装入夹具。
21.5.如图12,操作人员取出流动夹具,放入新的流动夹具,循环上述步骤。
22.以上所述,仅为此发明的具体实施方式,但本发明的保护范围不局限于此,任何熟悉本技术领域的技术人员在本发明揭露的技术范围内,根据本发明的技术方案和新型的构思加于等同替换或改变,都应涵盖在本发明的保护范围之内。
技术特征:1.一种自动装料装置,其特征在于包括若干原材分离机构,所述原材分离机构上部为竖直设置的原料通道,原材分离机构为分离腔体,腔体内设有挡块,挡块位于原料通道下方,且和原料通道存有间隙,腔体内还设有拨块,由第一气缸驱动;若干夹具,夹具内设有弹簧夹紧机构,夹具由设置于自动装料装置的凸台驱动弹簧夹紧机构来控制启闭,所述弹簧夹紧机构一侧设有压块和弹簧,压块的端部为斜面,所述弹簧夹紧机构还包括无头螺丝,用于调整弹簧的压缩量。2.如权利要求1所述的一种自动装料装置,其特征在于所述若干原材分离机构沿同一水平横向设置,由第一气缸统一驱动。3.如权利要求1或2所述的一种自动装料装置,其特征在于所述分离腔体左侧底部和右侧底部分别设有两个不同的导向槽。4.如权利要求3所述的一种自动装料装置,其特征在于所述导向槽下方设有定位槽。5.如权利要求1-4任一所述的一种自动装料装置,其特征在于还包括第二气缸,用于驱动夹具移动。6.如权利要求1-4任一所述的一种自动装料装置,其特征在于还包括第三气缸,用于压住夹具。7.如权利要求1-4任一所述的一种自动装料装置,其特征在于还包括第四气缸,用于顶出夹具内的残料。8.如权利要求1-4任一所述的一种自动装料装置,其特征在于还包括第五气缸,用于把原材装入夹具。
技术总结本发明涉及机械自动化设备技术领域,具体来说是一种自动装料装置,包括若干原材分离机构,所述原材分离机构上部为竖直设置的原料通道,原材分离机构为分离腔体,腔体内设有挡块,挡块位于原料通道下方,且和原料通道存有间隙,腔体内还设有拨块,由第一气缸驱动;若干夹具,夹具内设有弹簧夹紧机构,夹具由设置于自动装料装置的凸台驱动弹簧夹紧机构来控制启闭,所述弹簧夹紧机构一侧设有压块和弹簧,压块的端部为斜面,所述弹簧夹紧机构还包括无头螺丝,用于调整弹簧的压缩量,其优点在于:由机器替代人工进行装料,提升了工作效率,降低了人工成本。人工成本。人工成本。
技术研发人员:陆明勇 周红波 秦玉良
受保护的技术使用者:赫比(上海)金属工业有限公司
技术研发日:2022.06.14
技术公布日:2022/7/12