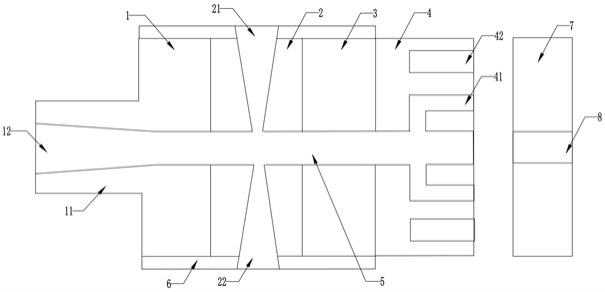
一种用于复合塑料型材挤出成型的模具及方法
1.技术领域:本发明涉及复合塑料成型技术领域,具体涉及一种用于复合塑料型材挤出成型的模具及方法。
2.
背景技术:复合塑料型材通常采用挤出成型设备加工而成,其中挤出成型模具是挤出成型设备的重要部件,现有的挤出成型模具还存在成型效率低、冷却效果差、模具抛光清洗不便等缺陷。
3.公开于该背景技术部分的信息仅仅旨在增加对本发明的总体背景的理解,而不应当被视为承认或以任何形式暗示该信息构成已为本领域一般技术人员所公知的现有技术。
4.
技术实现要素:本发明的目的在于提供一种用于复合塑料型材挤出成型的模具,从而克服上述现有技术中的缺陷。
5.为实现上述目的,本发明提供一种用于复合塑料型材挤出成型的模具,包括依次设置的主进料段、副进料段、混料段、辅助成型段和定型段,其中主进料段、副进料段、混料段和辅助成型段依次连接,所述主进料段侧面延伸有主进料区,所述主进料段、副进料段、混料段和辅助成型段内部设置有连续的物料挤出通道,所述定型段内设置有物料定型通道,所述物料定型通道与物料挤出通道配套,所述主进料区内设置有主进料口,所述主进料口与物料挤出通道的端部连通,所述辅助成型段内设置有风冷通道和水冷通道,所述风冷通道连通物料挤出通道和外界,所述水冷通道位于风冷通道以外。
6.所述副进料段上设置有副进料口一和副进料口二,所述副进料口一、副进料口二分别与物料挤出通道内部连通。
7.所述主进料段、副进料段、混料段及辅助成型段为分体式结构。
8.所述主进料段、副进料段、混料段外壁还设置有一体式加热圈,所述加热圈与主进料段、副进料段、混料段外壁之间为可拆卸式连接。
9.所述主进料段整体为t形结构,主进料口与副进料口一、副进料口二之间均为垂直结构。
10.一种复合塑料型材挤出成型的方法,包括以下步骤:1)复合塑料原料a、原料b、原料c分别从主进料口、副进料口一、副进料口二处加入到物料挤出通道内,也可均从主进料口处加入到物料挤出通道内;2)在加料过程中加热圈工作,将主进料段、副进料段内的原料a、原料b、原料c加热熔融;3)熔融后的原料a、原料b、原料c在混料段内混合均匀后引流到辅助成型段内挤出初步定型的复合塑料型材;4)往辅助成型段的风冷通道内通入冷却风、水冷通道内通入冷却水对物料进行初步冷却定型;5)初步冷却定型的复合塑料型材进入到定型段后定型成复合塑料型材成品。
11.与现有技术相比,本发明具有如下有益效果:(1)本发明辅助成型段采用风冷配合水冷,可提高初步冷却定型的效率,有利于流动性强的复合塑料进入到定型段定型,可提高整体加工的效率;(2)本发明采用多段之间采用分体式设计,更便于对不同工段的模具进行清洁抛光等维护操作;(3)本发明设置多个进料口,可根据需要将多种物料分别从不同的进料口进料,避免不同物料之间交叉污染,也更便于根据不同物料之间的特性来控制物料的进料顺序;附图说明:图1为本发明的一种用于复合塑料型材挤出成型的模具的示意图;附图标记为:1-主进料段、11-主进料区、12-主进料口、2-副进料段、21-副进料口一、22-副进料口二、3-混料段、4-辅助成型段、41-风冷通道、42-水冷通道、5-物料挤出通道、6-加热圈、7-定型段、8-物料定型通道。
12.具体实施方式:下面对本发明的具体实施方式进行详细描述,但应当理解本发明的保护范围并不受具体实施方式的限制。
13.除非另有其它明确表示,否则在整个说明书和权利要求书中,术语“包括”或其变换如“包含”或“包括有”等等将被理解为包括所陈述的元件或组成部分,而并未排除其它元件或其它组成部分。
14.如图1所示,一种用于复合塑料型材挤出成型的模具,包括依次设置的主进料段1、副进料段2、混料段3、辅助成型段4和定型段7,其中主进料段1、副进料段2、混料段3、辅助成型段4依次连接,所述主进料段1侧面延伸有主进料区11,所述主进料段1、副进料段2、混料段3和辅助成型段4内部设置有连续的物料挤出通道5,所述定型段7内设置有物料定型通道8,所述物料定型通道8与物料挤出通道5配套,所述主进料区11内设置有主进料口12,所述主进料口12与物料挤出通道5的端部连通,所述辅助成型段4内设置有风冷通道41和水冷通道42,所述风冷通道41连通物料挤出通道5和外界,所述水冷通道42位于风冷通道41以外。
15.进一步的,为便于不同物料分别进料,所述副进料段2上设置有副进料口一21和副进料口二22,所述副进料口一21、副进料口二22分别与物料挤出通道5内部连通。
16.进一步的,为便于对不同工段进行拆解维护,所述主进料段1、副进料段2、混料段3及辅助成型段4为分体式结构。
17.进一步的,为提高加热的稳定性和均匀性,所述主进料段1、副进料段2、混料段3外壁还设置有一体式加热圈6,所述加热圈6与主进料段1、副进料段2、混料段3外壁之间为可拆卸式连接。
18.进一步的,为提高整体结构的对称稳定性,所述主进料段1整体为t形结构,主进料口12与副进料口一21、副进料口二22之间均为垂直结构。
19.一种复合塑料型材挤出成型方法,包括如下步骤:1)复合塑料原料a、原料b、原料c分别从主进料口12、副进料口一21、副进料口二22处加入到物料挤出通道内,可根据不同物料的特性分别控制物料加入的顺序,也可均从主进料口12处加入到物料挤出通道内;2)在加料过程中加热圈工作,将主进料段1、副进料段2内的原料a、原料b、原料c加
热熔融;3)熔融后的原料a、原料b、原料c在混料段3内混合均匀后由辅助成型段4挤出初步定型的复合塑料型材;4)往辅助成型段4的风冷通道41内通入冷却风、水冷通道42内通入冷却水对物料进行冷却定型,对物料进行初步冷却定型;5)初步冷却定型的复合塑料型材进入到定型段7后定型成复合塑料型材成品。
20.本发明多段之间采用分体式设计,更便于对不同工段的模具进行清洁抛光等维护操作;多个进料口的设置,可将多种物料分别从不同的进料口进料,可避免不同物料之间交叉污染,也更便于根据不同物料之间的特性来控制物料的进料顺序;;辅助成型段采用风冷配合水冷,可提高初步冷却定型的效率,更便于后续加工;加热圈采用采用可拆卸式连接,更便于对加热圈进行拆解维护。
21.前述对本发明的具体示例性实施方案的描述是为了说明和例证的目的。这些描述并非想将本发明限定为所公开的精确形式,并且很显然,根据上述教导,可以进行很多改变和变化。对示例性实施例进行选择和描述的目的在于解释本发明的特定原理及其实际应用,从而使得本领域的技术人员能够实现并利用本发明的各种不同的示例性实施方案以及各种不同的选择和改变。本发明的范围意在由权利要求书及其等同形式所限定。
技术特征:1.一种用于复合塑料型材挤出成型的模具,其特征在于:包括依次设置的主进料段、副进料段、混料段、辅助成型段和定型段,其中主进料段、副进料段、混料段和辅助成型段依次连接,所述主进料段侧面延伸有主进料区,所述主进料段、副进料段、混料段和辅助成型段内部设置有连续的物料挤出通道,所述定型段内设置有物料定型通道,所述物料定型通道与物料挤出通道配套,所述主进料区内设置有主进料口,所述主进料口与物料挤出通道的端部连通,所述辅助成型段内设置有风冷通道和水冷通道,所述风冷通道连通物料挤出通道和外界,所述水冷通道位于风冷通道以外。2.根据权利要求1所述的一种用于复合塑料型材挤出成型的模具,其特征在于:所述副进料段上还设置有副进料口一和副进料口二,所述副进料口一、副进料口二分别与物料挤出通道内部连通。3.根据权利要求1所述的一种用于复合塑料型材挤出成型的模具,其特征在于:所述主进料段、副进料段、混料段及辅助成型段为分体式结构。4.根据权利要求1所述的一种用于复合塑料型材挤出成型的模具,其特征在于:所述主进料段、副进料段、混料段外壁还设置有一体式加热圈,所述加热圈与主进料段、副进料段、混料段外壁之间为可拆卸式连接。5.根据权利要求2所述的一种用于复合塑料型材挤出成型的模具,其特征在于:所述主进料段整体为t形结构,主进料口与副进料口一、副进料口二之间均为垂直结构。6.一种复合塑料型材挤出成型的方法,其特征在于:包括以下步骤:1)复合塑料原料a、原料b、原料c分别从主进料口、副进料口一、副进料口二处加入到物料挤出通道内,也可均从主进料口处加入到物料挤出通道内;2)在加料过程中加热圈工作,将主进料段、副进料段内的原料a、原料b、原料c加热熔融;3)熔融后的原料a、原料b、原料c在混料段内混合均匀后引流到辅助成型段内挤出初步定型的复合塑料型材;4)往辅助成型段的风冷通道内通入冷却风、水冷通道内通入冷却水对物料进行初步冷却定型;5)初步冷却定型的复合塑料型材进入到定型段后定型成复合塑料型材成品。
技术总结本发明公开了一种用于复合塑料型材挤出成型的模具及方法,所述模具包括依次设置的主进料段、副进料段、混料段、辅助成型段和定型段,其中主进料段、副进料段、混料段和辅助成型段依次连接,所述主进料段侧面延伸有主进料区,所述主进料段、副进料段、混料段和辅助成型段内部设置有连续的物料挤出通道,所述定型段内设置有物料定型通道,所述物料定型通道与物料挤出通道配套,所述主进料区内设置有主进料口,所述主进料口与物料挤出通道的端部连通,所述辅助成型段内设置有风冷通道和水冷通道,所述风冷通道连通物料挤出通道和外界,所述水冷通道位于风冷通道以外。冷通道位于风冷通道以外。冷通道位于风冷通道以外。
技术研发人员:张进
受保护的技术使用者:华塑(广州)材料有限公司
技术研发日:2022.03.28
技术公布日:2022/6/28