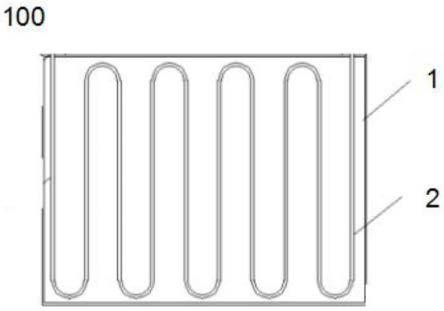
1.本实用新型涉及余热回收领域,特别是涉及一种管板式烟气换热器。
背景技术:2.烟气换热器主要应用于高温烟气的余热利用领域,其用于将燃烧产生的高温烟气的热能转换为液体的热能,传统的烟气换热器采用翅片管式,其结构烟气阻力大,导致烟气热利用率差,耐腐蚀性差,使用寿命短,造成了热能浪费。
技术实现要素:3.本实用新型的目的是提供一种管板式烟气换热器,以解决上述现有技术存在的问题,能够提高烟气余热利用率,且耐腐蚀性好,使用寿命长。
4.为实现上述目的,本发明提供了如下方案:
5.本实用新型提供一种管板式烟气换热器,包括换热器外壳和多个并排固定于所述换热器外壳内的管板换热单元,所述外壳上开设有进气口和出气口,所述外壳上设置有进液通道和出液通道,相邻的两个所述管板换热单元之间形成换气通道,且各所述换气通道一端与所述进气口连通,各所述换气通道另一端与所述出气口连通,所述管板换热单元包括换热管和分别固定于所述换热管两侧的两个耐腐蚀板,所述耐腐蚀板周向边缘固定连接并将所述换热管包覆住,各所述换热管的两端分别与所述进液通道和所述出液通道连通。
6.优选的,所述耐腐蚀板冲压成型有凹槽,所述换热管嵌入固定至所述凹槽内。
7.优选的,所述相邻管板换热单元之间相互平行设置。
8.优选的,所述相邻管板换热单元之间设置间距为80-120mm。
9.优选的,所述耐腐蚀板与所述换热管采用电阻焊接工艺连接。
10.优选的,所述换热管采用不锈钢蛇形管。
11.优选的,各所述管板换热单元均能够与所述换热器外壳能够拆卸地连接。
12.优选的,所述换热器外壳第一方向上的两端分别为第一端和第二端,所述进气口和所述出液通道均设置于所述第一端上,所述出气口和所述进液通道均设置于所述第二端上。
13.本实用新型相对于现有技术取得了以下技术效果:
14.本实用新型提供了一种管板式烟气换热器,包括换热器外壳和多个并排固定于换热器外壳内的管板换热单元,外壳上开设有进气口和出气口,用于烟气流通,外壳上设置有进液通道和出液通道,相邻的两个管板换热单元之间形成换气通道,且各换气通道一端与进气口连通,换气通道另一端与出气口连通,管板换热单元包括换热管和分别固定于换热管两侧的两个耐腐蚀板,耐腐蚀板周向边缘固定连接并将换热管包覆住,各换热管的两端分别与进液通道和出液通道连通,液体由进液通道进入换热管内部,在烟气流经换气通道时,换热管中的液体会吸收烟气中的热能,而后由出液通道流出,耐腐蚀板表面覆有致密的氧化膜,能够提高管板换热单元的耐腐蚀性,且由两个耐腐蚀板包覆换热管形成的板片式
结构,能够使在高烟气流速的状态下烟气阻力远远小于翅片管烟气阻力,这样在高烟气流速状态下换热器的换热系数和冷凝效果大幅度提升,有效提升余热利用率。
附图说明
15.为了更清楚地说明本实用新型实施例或现有技术中的技术方案,下面将对实施例中所需要使用的附图作简单地介绍,显而易见地,下面描述中的附图仅仅是本实用新型的一些实施例,对于本领域普通技术人员来讲,在不付出创造性劳动的前提下,还可以根据这些附图获得其他的附图。
16.图1为实施例一提供的一种管板式烟气换热器的结构示意图;
17.图2为管板换热单元侧视图;
18.图中:100-管板换热单元,1-耐腐蚀板,2-换热管,3-换热器外壳,4-进液通道,5-出液通道。
具体实施方式
19.下面将结合本实用新型实施例中的附图,对本发明实施例中的技术方案进行清楚、完整地描述,显然,所描述的实施例仅仅是本发明一部分实施例,而不是全部的实施例。基于本发明中的实施例,本领域普通技术人员在没有做出创造性劳动前提下所获得的所有其他实施例,都属于本发明保护的范围。
20.本实用新型的目的是提供一种管板式烟气换热器,以解决上述现有技术存在的问题,够提高烟气余热利用率,且耐腐蚀性好,使用寿命长。
21.为使本实用新型的上述目的、特征和优点能够更加明显易懂,下面结合附图和具体实施方式对本实用新型作进一步详细的说明。
22.本实用新型提供一种管板式烟气换热器,如图1~2所示,包括换热器外壳3和多个并排固定于换热器外壳内的管板换热单元100,外壳上开设有进气口和出气口,用于烟气流通,外壳上设置有进液通道4和出液通道5,相邻的两个管板换热单元之间形成换气通道,且各换气通道一端与进气口连通用于通入烟气,换气通道另一端与出气口连通用于烟气流出,管板换热单元100包括换热管2和分别固定于换热管两侧的两个耐腐蚀板1,耐腐蚀板1周向边缘固定连接并将换热管2包覆住,各换热管的两端分别与进液通道4和出液通道5连通,液体由进液通道4进入换热管2内部,在烟气流经换气通道时,换热管2中的液体会吸收烟气中的热能,而后由出液通道5流出,耐腐蚀板1表面覆有致密的氧化膜,能够提高管板换热单元的耐腐蚀性,且由两个耐腐蚀板1包覆换热管2形成的板片式结构,能够使在高烟气流速的状态下烟气阻力远远小于翅片管烟气阻力,这样在高烟气流速状态下换热器的换热系数和冷凝效果大幅度提升,有效提升余热利用率。
23.本实施例的可选方案中,较为优选的,耐腐蚀板1冲压成型凹槽,将换热管2嵌入固定至耐腐蚀板1的凹槽内,增加换热管2与耐腐蚀版的紧固性。
24.本实施例的可选方案中,较为优选的,相邻管板换热单元100之间相互平行设置,保证每个管板换热单元100受热均匀。
25.本实施例的可选方案中,较为优选的,相邻管板换热单元100之间设置间距为80-120mm,优选设置为80mm,能更好的能够提高烟气通过速度的同时保证烟气余热利用率。
26.本实施例的可选方案中,较为优选的,耐腐蚀板1与换热管2采用电阻焊接工艺连接,能够增加紧固性防止脱落。
27.本实施例的可选方案中,较为优选的,换热管2采用不锈钢蛇形管,增加与烟气接触时间。
28.本实施例的可选方案中,较为优选的,各管板换热单元1均能够与换热器外壳3能够拆卸地连接,当发现某一管板管热单元1损坏时,能够及时更换,增加维修便利性。
29.本实施例的可选方案中,较为优选的,如图1所示,换热器外壳3第一方向上的两端分别为第一端和第二端,进气口和出液通道5均设置于第一端上,出气口和进液通道4均设置于第二端上,烟气流通方向与水流方向相反,能够增加烟气与水的接触时间,充分利用烟气与水的温差。
30.本实用新型中应用了具体个例对本实用新型的原理及实施方式进行了阐述,以上实施例的说明只是用于帮助理解本实用新型的方法及其核心思想;同时,对于本领域的一般技术人员,依据本实用新型的思想,在具体实施方式及应用范围上均会有改变之处。综上所述,本说明书内容不应理解为对本实用新型的限制。
技术特征:1.一种管板式烟气换热器,其特征在于:包括换热器外壳和多个并排固定于所述换热器外壳内的管板换热单元,所述换热器外壳上开设有进气口和出气口,所述换热器外壳上设置有进液通道和出液通道,相邻的两个所述管板换热单元之间形成换气通道,且各所述换气通道一端与所述进气口连通,各所述换气通道另一端与所述出气口连通,所述管板换热单元包括换热管和分别固定于所述换热管两侧的两个耐腐蚀板,所述耐腐蚀板周向边缘固定连接并将所述换热管包覆住,各所述换热管的两端分别与所述进液通道和所述出液通道连通。2.根据权利要求1所述的管板式烟气换热器,其特征在于:所述耐腐蚀板冲压成型有凹槽,所述换热管嵌入固定至所述凹槽内。3.根据权利要求1所述的管板式烟气换热器,其特征在于:所述相邻管板换热单元之间相互平行设置。4.根据权利要求1所述的管板式烟气换热器,其特征在于:所述相邻管板换热单元之间设置间距为80-120mm。5.根据权利要求1所述的管板式烟气换热器,其特征在于:所述耐腐蚀板与所述换热管采用电阻焊接工艺连接。6.根据权利要求1所述的管板式烟气换热器,其特征在于:所述换热管采用不锈钢蛇形管。7.根据权利要求1所述的管板式烟气换热器,其特征在于:各所述管板换热单元均能够与所述换热器外壳能够拆卸地连接。8.根据权利要求1所述的管板式烟气换热器,其特征在于:所述换热器外壳第一方向上的两端分别为第一端和第二端,所述进气口和所述出液通道均设置于所述第一端上,所述出气口和所述进液通道均设置于所述第二端上。
技术总结本实用新型公开了一种管板式烟气换热器,涉及余热回收领域,管括换热器外壳和多个并排固定于换热器外壳内的管板换热单元,换热器外壳上开设有进气口和出气口,换热器外壳上设置有进液通道和出液通道,相邻的两个所述管板换热单元之间形成换气通道,且各换气通道一端与进气口连通,各换气通道另一端与所述出气口连通,管板换热单元包括换热管和分别固定于换热管两侧的两个耐腐蚀板,腐蚀板周向边缘固定连接并将换热管包覆住,各换热管的两端分别与进液通道和出液通道连通。本实用新型提供的管板式烟气换热器结构简单,余热回收利用率高,耐腐蚀性强,使用寿命长。使用寿命长。使用寿命长。
技术研发人员:陆超超 于涛 王宗耀
受保护的技术使用者:北京新兴合众科技有限公司
技术研发日:2022.04.22
技术公布日:2022/8/11