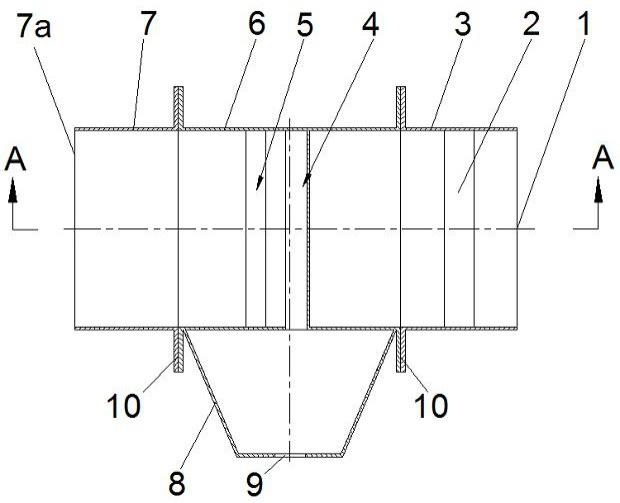
1.本实用新型专利涉及两相分离技术领域,具体而言,尤其涉及一种气液分离方法及装置。
背景技术:2.在天然气的输送过程中,天然气中的水气在运输过程中会冷凝、积聚形成大液滴甚至形成水膜滞留在管道或设备中,不仅会造成阻力的增加,更容易形成酸性水合物,加重对下游管道和阀门的腐蚀,影响整个天然气输送系统的安全和使用寿命。因此,天然气在进入管网运输前,需要进行脱水除湿处理。常用的天然气脱水除湿的方法主要有溶剂吸收法、低温冷却分离法,上述方法中均需要使用气液分离技术。至今为止现有的气液分离技术主要有丝网聚结结合旋流分离方法以及碰撞分离方法等。由于现有气液分离技术对于小尺度液滴分离效率低,适用气速以及液滴波动范围较窄,存在一定的技术缺陷,故对气液分离器发展提出的更高的要求。
技术实现要素:3.本实用新型基于附壁效应提出一种基于附壁效应的气液分离装置,利用射流附壁效应,提升气液分离过程整体的分离效率,可以作为天然气介质气液分离预处理装置,能够有效的解决现有气液分离技术存在的问题。
4.本实用新型采用的技术方案是:一种基于附壁效应的气液分离装置,采用扩压段、筒体和出口段依次连接的箱体结构,扩压段的端部设有进气口,出口段的端部设有出气口,所述扩压段采用锥形截面的箱形结构,扩压段的内壁上设置多个叶片分布器,筒体的内部设置多个连接筒体顶部和底部的气液分离元件,底部外侧设置与筒体内腔相通的储液槽,储液槽的底部设置排液口;
5.所述气液分离元件采用两个导流弧与一个分流板在端部固定连接,形成两个导流弧以分流板为对称的结构,并保持分流板的侧面与导流弧的内弧面为切向连接,在两个相邻的分流板之间设置连接筒体顶部和底部的折流槽,折流槽采用在折流板两端分别设有折边的梯形槽结构,折流槽的槽口与导流弧内弧面的导流方向相配合;
6.所述分流板的一侧与位于同一侧折流槽的折边之间形成喷射口。
7.所述喷射口的宽度c为50-150mm,导流弧与折边自由端之间的垂向间距d为50-150mm。
8.所述导流弧采用曲率半径r为50-150mm的圆弧形、椭圆弧形结构。
9.所述筒体与扩压段、出口段分别通过法兰连接。
10.本实用新型的有益效果是:一种基于附壁效应的气液分离装置,采用扩压段、筒体和出口段依次连接的箱体结构,扩压段的端部连接进气口,出口段的端部连接出气口,扩压段采用锥形截面的箱形结构,扩压段的内部设置多个连接扩压段顶部和底部的叶片分布器,筒体的内部设置多个连接筒体顶部和底部的气液分离元件,底部外侧设置储液槽。这种
基于附壁效应的气液分离装置结构简单,加工要求和成本较低,不易堵塞结垢,安装拆卸简易。该分离装置通过利用附壁效应,使得气体在附壁的过程中将夹带的小液滴聚集成更大的液滴,大液滴更易被气液分离装置分离,从而能够大大提高其分离效率。而且该分离装置的分离负荷范围广,在各种气速下都具有极高的分离效率,能够作为天然气脱水的预处理装置,进而大大提高天然气脱水性能。
11.附图说明:
12.图1是一种基于附壁效应的气液分离装置的结构主视图。
13.图2是图1中的a-a剖视图。
14.图3是一种基于附壁效应的气液分离装置的左视图。
15.图4是一种基于附壁效应的气液分离装置的右视图。
16.图5是图2中的b放大图。
17.图中:1、进气口,2、叶片分布器,3、扩压段,4、折流槽,4a、折边,4b、折流板,5、气液分离元件,5a、导流弧,5b、分流板,5c、喷射口,6、筒体,7、出口段,7a、出气口,8、储液槽,9、排液口,10、法兰。
具体实施方式
18.为了可以更清楚地理解本实用新型的上述目的、特征和优点,下面结合附图和具体实施方式对本实用新型进行进一步的详细描述。
19.图1-4示出了一种基于附壁效应的气液分离装置的结构图。图中,这种基于附壁效应的气液分离装置采用扩压段3、筒体6和出口段7依次连接的箱体结构,扩压段3的端部设有进气口1,出口段7的端部设有出气口7a。扩压段3采用锥形截面的箱形结构,扩压段3的内壁上设置多个叶片分布器2,筒体6的内部设置四个连接筒体6顶部和底部的气液分离元件5,底部外侧设置与筒体6内腔相通的储液槽8,储液槽8的底部设置排液口9。
20.气液分离元件5采用两个导流弧5a与一个分流板5b在端部固定连接,形成两个导流弧5a以分流板5b为对称的结构,并保持分流板5b的侧面与导流弧5a的内弧面为切向连接,在两个相邻的分流板5b之间设置连接筒体6顶部和底部的折流槽4,折流槽4采用在折流板4b两端分别设有折边4a的梯形槽结构,折流槽4的槽口与导流弧5a内弧面的导流方向相配合。分流板5b的一侧与位于同一侧折流槽4的折边4b之间形成喷射口5c。筒体6与扩压段3、出口段7分别通过法兰10连接。折流槽4与气液分离元件5与筒体焊接连接,也可以采用螺栓等方式连接。
21.喷射口5c的宽度c为50mm,导流弧5a与折边4b自由端之间的垂向间距d为100mm。导流弧5a采用曲率半径r为100mm的圆弧形(如图5所示)。
22.这种基于附壁效应的气液分离装置的工作过程:气液两相混合物从进气口1进入,经过焊接在扩压段3内壁上的叶片分布器2,叶片分布器2的叶片与入口两相气流呈一定角度设置,使流体分布更加均匀。随后,流体进入筒体6,气液混合物通过折流槽4与气液分离元件5之间的通道,即喷射口5c进入气液分离元件5。两相气流通过喷射口5c时,气流速度提升,形成射流。射流气体喷入气液分离元件5的导流弧5a后,在导流弧5a的内弧面内附壁流动,在附壁效应的作用下,两相流体中的液滴逐渐被导流弧5a内弧面的表面所捕集,被捕捉的液滴在重力作用下,沿着气液分离元件5壁面流至筒体6的底部。最后射流气体在导流弧
5a内弧面的终端切向冲向折流槽4的折流板4b,在折流板4b的表面附壁流动,在附壁效应的作用下,两相流体中更细小的液滴逐渐被折流板4b的表面所捕集,被捕捉的液滴在重力作用下,也沿着折流槽4的表面流至筒体6的底部。通过筒体6底部的出液口进入储液槽8,完成气液两相分离。经分离处理后气体通过筒体6进入出口段7。
23.折流槽4与气液分离元件5之间需要形成射流流道,其折流槽4结构可以采用型材折弯,也可以加工成型。喷射口5c的宽度c、导流弧5a的曲率半径r和导流弧5a与折边4b自由端之间的垂向间距d通过流体力学计算获得。储液槽8与筒体6可以采用螺栓连接或焊接,固定设置在筒体6的下方。
24.以上详细描述了本实用新型的较佳具体实施例。本领域的普通技术人员依据本实用新型的构思在现有技术的基础上通过逻辑分析、推理或者有限的实验可以得到的技术方案,皆应在由权利要求书所确定的保护范围内。
技术特征:1.一种基于附壁效应的气液分离装置,采用扩压段(3)、筒体(6)和出口段(7)依次连接的箱体结构,扩压段(3)的端部设有进气口(1),出口段(7)的端部设有出气口(7a),其特征在于,所述扩压段(3)采用锥形截面的箱形结构,扩压段(3)的内壁上设置多个叶片分布器(2),筒体(6)的内部设置多个连接筒体(6)顶部和底部的气液分离元件(5),底部外侧设置与筒体(6)内腔相通的储液槽(8),储液槽(8)的底部设置排液口(9);所述气液分离元件(5)采用两个导流弧(5a)与一个分流板(5b)在端部固定连接,形成两个导流弧(5a)以分流板(5b)为对称的结构,并保持分流板(5b)的侧面与导流弧(5a)的内弧面为切向连接,在两个相邻的分流板(5b)之间设置连接筒体(6)顶部和底部的折流槽(4),折流槽(4)采用在折流板(4b)两端分别设有折边(4a)的梯形槽结构,折流槽(4)的槽口与导流弧(5a)内弧面的导流方向相配合;所述分流板(5b)的一侧与位于同一侧折流槽(4)的折边(4a)之间形成喷射口(5c)。2.根据权利要求1所述的一种基于附壁效应的气液分离装置,其特征在于:所述喷射口(5c)的宽度c为50-150mm,导流弧(5a)与折边(4a)自由端之间的垂向间距d为50-150mm。3.根据权利要求1所述的一种基于附壁效应的气液分离装置,其特征在于:所述导流弧(5a)采用曲率半径r为50-150mm的圆弧形、椭圆弧形结构。4.根据权利要求1所述的一种基于附壁效应的气液分离装置,其特征在于:所述筒体(6)与扩压段(3)、出口段(7)分别通过法兰(10)连接。
技术总结一种基于附壁效应的气液分离装置,属于两相分离技术领域。该分离装置采用扩压段、筒体和出口段依次连接的箱体结构,扩压段的端部连接进气口,出口段的端部连接出气口。扩压段的内部设置多个叶片分布器,筒体的内部设置多个连接筒体顶部和底部的气液分离元件,底部外侧设置储液槽。这种基于附壁效应的气液分离装置结构简单,加工要求和成本较低,安装拆卸简易。该分离装置利用附壁效应,使得气体在附壁的过程中将夹带的小液滴聚集成更大的液滴,大液滴更易被气液分离装置分离,从而能够大大提高其分离效率。而且该分离装置的分离负荷范围广,在各种气速下都具有极高的分离效率,能够作为天然气脱水的预处理装置,进而大大提高天然气脱水性能。脱水性能。脱水性能。
技术研发人员:胡大鹏 于洋
受保护的技术使用者:大连弘科理工机电设备有限公司
技术研发日:2021.09.26
技术公布日:2022/6/23