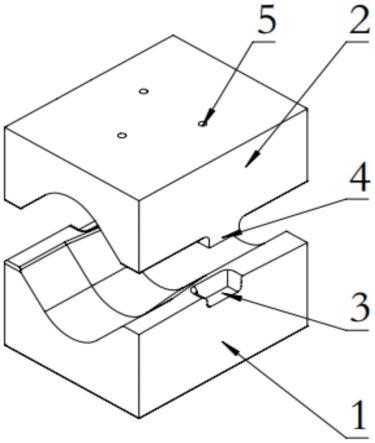
1.本实用新型属于钛合金锻造技术领域,涉及航空发动机用钛合金连杆锻件成型,具体涉及一种航空发动机用钛合金连杆体积成型专用模具。
背景技术:2.目前,钛合金管的生产主要采用较成熟的“径锻机”对钛合金管坯轧制锻造成型,能满足行业的一般应用。但是在一些特殊领技术域用的钛合金薄壁管连杆零件的管坯锻件就无法使用该种工艺生产的钛合金管作为坯料,需要采用一种特别的锻造加工技术来满足需求。例如,钛合金薄壁管应用于安装支撑大型航空发动机的连杆制造时,由于连杆两端需要锻造变径缩口或收口,亟待一种特制的钛合金连杆体积成型专用模具来满足技术需求。
技术实现要素:3.基于上述航空发动机连杆制造存在的技术问题和需求,本实用新型经过深入研究,设计了一种钛合金连杆体积成型专用模具来达到目的,具体技术方案如下。
4.一种航空发动机用钛合金连杆体积成型专用模具,包括下模(1)与上模(2),其特征在于,所述上模(2)和下模(1)通过下模定位凹槽(3)与上模定位凸块(4)相互对称嵌套配合使用,模具安装螺孔(5)则通过螺钉实现所述上模(2)与锻压机的锻锤的下端部固定连接;所述下模(1)的内表面为锻压加工面,包括相互光滑连接的底部加工面和两个对称设置的侧部加工面;所述底部加工面由开口端底部加工圆弧面(d1)、中段底部加工圆弧面(d2)和缩口端底部加工圆弧面(d3)依次光滑相接构成;
5.两个对称设置的所述侧部加工面成v型面,由开口端侧部加工圆弧面(v1)、中段侧部加工圆弧面(v2)和缩口端侧部加工圆弧面(v3)依次光滑相接构成;
6.所述下模(1)的内表面为锻压加工面的模具开口端最大内径d1、模具开口端最小内径d2、模具缩口端最小内径d3、模具缩口端最大内径d4的比例关系为d1>d4>d2>d3;
7.所述底部加工面和两个对称设置的侧部加工面的交接线与水平线的夹角为a,且2
°
<a<9.5
°
。
8.进一步的优化在于,d1=157.44mm、d2=76.65mm、d3=69.30mm、d4=142.74mm、 a=3.80
°
。
9.与现有技术相比,本实用新型的技术优势具体表现为:
10.1、由于采用本实用新型的体积成型专用模具,锻造后的钛合金管类工件表面直线度
11.2、钛合金连杆成套或成批的质量一致性好,成品率显著高提高。
12.3、专用模具底部加工面对工件的还起到收光的作用,光洁度显著高于径锻机锻压成型,外管壁的光洁度显著提高,避免加工形成裂纹等缺陷。
附图说明
13.图1,为本实用新型的航空发动机用钛合金连杆体积成型专用模具的立体示意图;
14.图2,为本实用新型图1的立体分解图;
15.图3,为本实用新型图1的下模俯视图;
16.图4,为本实用新型图1的上模仰视图;
17.图5,为本实用新型在加工工件后的示意图;
18.图6,为本实用新型在加工工件前的示意图;
19.图7,为本实用新型在加工工件前的开口端面示意图;
20.图8,为本实用新型在加工工件后的开口端面示意图;
21.图9,为图7的a-a方向剖视示意图;
22.图10,为图8的b-b方向剖视示意图。
23.图中,1
‑‑
下模、2
‑‑
上模、3—下模定位凹槽、4—上模定位凸块、5—上模安装螺孔、6—工件、d1—开口端底部加工圆弧面、d2—中段底部加工圆弧面、d3—缩口端底部加工圆弧面、v1
‑‑
开口端侧部加工圆弧面、v2
‑‑
中段侧部加工圆弧面、v3—缩口端侧部加工圆弧面、a-锥度、d1
‑‑‑
模具开口端最大内径、d2
‑‑
模具开口端最小内径、d3
‑‑
模具缩口端最小内径、d4
‑‑
模具缩口端最大内径。
具体实施方式
24.下面结合附图和实施例对本实用新型进一步详细陈述。
25.如图1~图2所示,为本实用新型的实施例,是航空发动机用钛合金连杆体积成型专用模具,它包括下模1与上模2,其中,所述上模2和下模1通过下模定位凹槽3与上模定位凸块4相互对称嵌套配合使用或放置在库房里,工作时分开使用。模具安装螺孔5则用来通过螺钉实现所述上模2与锻压机的锻锤的下端部固定连接,可实现上下往复锻压工作;所述下模1则可拆卸地安装在锻压机的锻压平台上。
26.如图3~图4所示,所述下模1与上模2的内表面互为对称为锻压加工面,包括相互光滑连接的底部加工面和两个对称设置的侧部加工面。所述底部加工面由开口端底部加工圆弧面d1、中段底部加工圆弧面d2和缩口端底部加工圆弧面d3依次光滑相接构成。两个对称设置的所述侧部加工面成v型面,由开口端侧部加工圆弧面v1、中段侧部加工圆弧面 v2和缩口端侧部加工圆弧面v3依次光滑相接构成。所述v型面用来承受锻压时的冲击压力。此时,所述v型面与钛合金管的锻压工件为线接触。所述下模1的内表面为锻压加工面的模具开口端最大内径d1、模具开口端最小内径d2、模具缩口端最小内径d3、模具缩口端最大内径d4的比例关系为d1>d4>d2>d3;且d1、d4、d2和d3所对应的圆心轴线相重合;所述底部加工面和两个对称设置的侧部加工面的交接线与水平线的夹角为a。
27.如图5~图10所示,为用本实用新型在加工钛合金管连杆类工件前、后的变化示意图,其中d1=157.44mm、d2=76.65mm、d3=69.30mm、d4=142.74mm、a=3.80
°
。所述侧部加工面成v型面和所述底部加工面的直线度和光洁度需满足航空航天用钛合金管的锻压工件6的需求;所述底部加工面对工件的还起到收光的作用,光洁度往往显著高于径锻机锻压成型的工件。
技术特征:1.航空发动机用钛合金连杆体积成型专用模具,包括下模(1)、上模(2),其特征在于,所述上模(2)与所述下模(1)相互对称,并通过下模定位凹槽(3)与上模定位凸块(4)嵌套配合使用,所述上模(2)的模具安装螺孔(5)则通过螺钉实现所述上模(2)与锻压机的锻锤的下端部固定连接;所述下模(1)的内表面为锻压加工面,包括相互光滑连接的底部加工面和两个对称设置的侧部加工面;所述底部加工面由开口端底部加工圆弧面(d1)、中段底部加工圆弧面(d2)和缩口端底部加工圆弧面(d3)依次光滑相接构成;两个对称设置的所述侧部加工面成v型面,由开口端侧部加工圆弧面(v1)、中段侧部加工圆弧面(v2)和缩口端侧部加工圆弧面(v3)依次光滑相接构成;所述下模(1)的内表面为锻压加工面的模具开口端最大内径d1、模具开口端最小内径d2、模具缩口端最小内径d3、模具缩口端最大内径d4,其比例关系为d1>d4>d2>d3;所述底部加工面和两个对称设置的侧部加工面的交接线与水平线的夹角为a。2.如权利要求1所述的航空发动机用钛合金连杆体积成型专用模具,其特征在于,所述夹角a角度为2
°
~9.5
°
。3.如权利要求1或2所述的航空发动机用钛合金连杆体积成型专用模具,其特征在于,所述d1=157.44mm、d2=76.65mm、d3=69.30mm、d4=142.74mm,夹角a为a=3.80
°
。
技术总结本实用新型提供的航空发动机用钛合金连杆体积成型专用模具,包括下模与上模,所述上模和下模通过下模定位凹槽与上模定位凸块相互对称嵌套配合使用,模具安装螺孔则通过螺钉实现所述上模与锻压机的锻锤的下端部固定连接;所述下模的内表面为锻压加工面,包括相互光滑连接的底部加工面和两个对称设置的侧部加工面;所述底部加工面由开口端底部加工圆弧面、中段底部加工圆弧面和缩口端底部加工圆弧面依次光滑相接构成。本实用新型锻造后的成套或成批的航空发动机用钛合金连杆表面直线度、质量一致性好,成品率显著提高,外管壁的光洁度显著提高,可以避免加工形成裂纹等缺陷。可以避免加工形成裂纹等缺陷。可以避免加工形成裂纹等缺陷。
技术研发人员:张宏丽 孙喜生 李鹏德
受保护的技术使用者:陕西钛博飞特航空制造股份有限公司
技术研发日:2021.10.26
技术公布日:2022/6/17