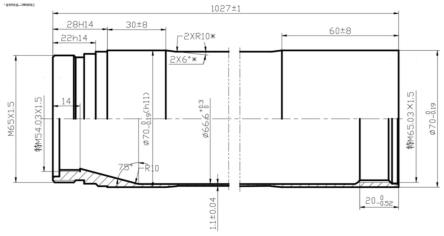
1.本发明涉及一种不同部位有不同力学性能筒体的成形方法,属于强力旋压成形技术领域。
背景技术:2.小直径、小壁厚、长径比大(直径d范围为:圆柱部壁厚t范围为:0.8~1.3
±
0.04)的筒形件结构如图1,材料为40cr,该零件不同部位有不同的力学性能要求,该筒形零件的左右两端为带内螺纹的厚壁环形连接部,该筒形零件的中部为薄壁筒体,且要求该筒形零件左端、中部、右端三部分的力学性能抗拉强度rm和断后伸长率a均不相同,具体力学性能要求见下表:
[0003] 左端中间右端rm(mpa)6701120980a(%)1559
[0004]
常规机加成形后热处理的方法存在以下问题:1、机械加工的方法成形材料浪费严重;2、壁厚精度难以保证,3、热处理工艺还无法满足不同部位具有不同的力学性能。
[0005]
选择用常规旋压+冷缩口的工艺,成品力学性能由旋压保证,旋后只进行去应力退火处理的方法进行加工,存在问题为:根据圆柱部力学性能要求按照传统思路进行连续的三道次旋压成形,右端的力学性能在第二道次的rm达不到,在第三道次的a无法保证,因此不能按照传统方法三道次成形。
技术实现要素:[0006]
本发明的目的是为了解决传统工艺无法加工不同部位有不同力学性能筒体的技术难点,而提供一种不同部位有不同力学性能筒体的成形方法。
[0007]
本发明的目的是通过以下技术方案实现的:
[0008]
本发明的一种不同部位有不同力学性能筒体的成形方法,具体成形步骤如下:
[0009]
1)对下料、粗加工后的管材进行正火,满足管材满足筒体产品左端性能要求;
[0010]
2)对正火后的管材进行旋前机加,使毛坯的左端尺寸与筒体产品左端环形连接部的尺寸相匹配;使毛坯的中部内径与筒体产品中部薄壁筒体的内径相匹配,且按照81%的材料减薄率计算毛坯中部的壁厚和外径;使毛坯的右端内径与筒体产品右端环形连接部的内径相匹配并留有缩口余量,且按照44%的材料减薄率计算毛坯右端的壁厚和外径;
[0011]
3)对毛坯进行四道次旋压,第一道次对毛坯右端进行的旋压,使毛坯右端外径达到冷缩口前尺寸;之后对毛坯中部采用三道次旋压至筒体产品要求壁厚。
[0012]
4)对旋压后的零件进行平端面,冷缩口使右端内外径与零件右端内外径相匹配,之后去应力退火,成品机加至零件尺寸,完成筒体的成形。
[0013]
有益效果
[0014]
本发明的成形方法,首次提出了对零件的轴向部位进行分割旋压,中间圆柱部按
照传统三道次旋压成形,右端按照其性能要求单独进行一道次旋压成形,即四道次连续旋压成形的理念,完成了筒体成形。通过本发明可提高零件的尺寸精度、满足零件不同部位力学性能的要求。
附图说明
[0015]
图1为待加工筒体产品的尺寸结构示意图;
具体实施方式
[0016]
下面结合附图和实施例对本发明的内容作进一步描述。
[0017]
实施例
[0018]
以加工某筒体产品为例,该筒体产品的结构尺寸如图1所示,其力学性能要求见下表:
[0019]
ꢀꢀ
特m54.03处圆柱部φ70处rm(mpa)6701120980a(%)1559
[0020]
筒体加工工艺流程:
[0021]
下料
→
粗加工
→
正火
→
旋前毛坯机加
→
旋压
→
平端面
→
冷缩口
→
去应力退火
→
成品机加。
[0022]
其具体的方法为:
[0023]
1、下料
[0024]
材料:40cr,规格:直径的圆钢,下料长度346+2 0mm。
[0025]
2、粗加工
[0026]
对圆钢进行平端面,钻孔。
[0027]
3、正火
[0028]
采用箱式电炉,装炉量≤40件/炉,工件散装于炉底板上加热,保温温度:(860
±
10)℃,保温时间:(1.5
±
0.5)h,保温至规定时间后空冷。
[0029]
正火后满足左端力学性能要求:rm≥670mpa,a≥15%。
[0030]
4、旋前毛坯机加
[0031]
左端按照零件图要求留够机加余量即可;中间圆柱部内径按照零件图要求确定,选取40cr材料的最大减薄率81%,根据零件壁厚要求计算旋前毛坯的壁厚,确定外径;使毛坯的右端内径与筒体产品右端环形连接部的内径相匹配并留有缩口余量,且按照44%的材料减薄率计算毛坯右端的壁厚和外径;
[0032]
5、旋压成形
[0033]
进行连续四道次旋压成形:第一道次按减薄率44%只单独旋压右端直径φ90处,该处性能即可满足产品要求。之后三道次只旋压中间圆柱部,按减薄率81%采用三道次旋压至壁厚1.1mm,旋压完成后保证产品内径、壁厚及该处的力学性能要求。
[0034]
6、平端面
[0035]
右端端面平齐,外圆倒角c1。
[0036]
7、冷缩口
[0037]
对右端进行缩口成形,满足零件图右端成品机加要求。
[0038]
8、去应力退火
[0039]
采用井式电炉,保温温度(370
±
10)℃,保温时间:(2~2.5)h,保温到规定时间后空冷。
[0040]
9、成品机加
[0041]
对第8步的零件两端进行机加,最后得到目标产品。
技术特征:1.一种不同部位有不同力学性能筒体的成形方法,其特征是具体成形步骤如下:1)对下料、粗加工后的管材进行正火,使管材满足筒体产品左端性能要求;2)对正火后的管材进行旋前机加,使毛坯的左端尺寸与筒体产品左端环形连接部的尺寸相匹配;使毛坯的中部内径与筒体产品中部薄壁筒体的内径相匹配,且按照81%的材料减薄率计算毛坯中部的壁厚和外径;使毛坯的右端内径与筒体产品右端环形连接部的内径相匹配并留有缩口余量,且按照44%的材料减薄率计算毛坯右端的壁厚和外径;3)对毛坯进行四道次旋压,第一道次对毛坯右端进行的旋压,使毛坯右端外径达到冷缩口前尺寸;之后对毛坯中部采用三道次旋压至筒体产品要求壁厚;4)对旋压后的零件进行平端面,冷缩口使右端内外径与零件右端内外径相匹配,之后去应力退火,成品机加至零件尺寸,完成筒体的成形。
技术总结本发明公开了一种不同部位有不同力学性能筒体的成形方法,该方法首先对下料、粗加工后的管材进行正火,使管材满足筒体产品左端性能要求;然后对正火后的管材进行旋前机加,使毛坯的左端尺寸与筒体产品左端环形连接部的尺寸相匹配;使毛坯的中部内径与筒体产品中部薄壁筒体的内径相匹配,且按照减薄率计算毛坯中部的壁厚和外径;使毛坯的右端内径与筒体产品右端环形连接部的内径相匹配并留有缩口余量,且按照减薄率计算毛坯右端的壁厚和外径;然后分别对毛坯的右端和中部进行旋压,再对旋压后的零件进行平端面,对右端冷缩口,之后去应力退火,成品机加至零件尺寸。本发明的成形方法,满足零件不同部位力学性能的要求。满足零件不同部位力学性能的要求。满足零件不同部位力学性能的要求。
技术研发人员:李婷 范国军 沈鑫 程小晋 董张成 段建霞 谭海兰 李明 戚远平 高军伟 李姝 李越 刘磊 史俊荣 陈晨 孙嘉浚
受保护的技术使用者:晋西工业集团有限责任公司
技术研发日:2022.10.26
技术公布日:2023/1/19