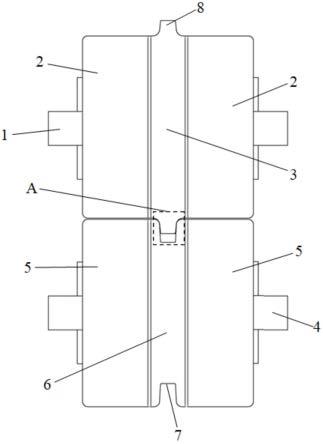
1.本实用新型涉及双金属复合轧制用轧辊技术领域,具体涉及一种双金属复合轧制用轧辊。
背景技术:2.使用两辊轧机轧制做复合轧制时,采用凸辊+凹辊模式,因复合条尺寸比较小,凹辊的凹槽比较小,凸辊的凸缘也比较小,凸辊受压非常大,轧辊的材质强度有限,在生产过程中因轧制的侧向力或者其他异常(原料宽度及厚度波动,材料的硬度波动等),凸辊非常容易损伤。
技术实现要素:3.有鉴于此,本实用新型公开了一种双金属复合轧制用轧辊,其能有效解决现有技术存在的上述问题。
4.为实现上述目的,本实用新型的技术方案是提供了一种双金属复合轧制用轧辊,其包括凸辊和凹辊,
5.所述凸辊包括上辊轴、上辊套及套接在上辊轴上的环状凸缘套,所述环状凸缘套两端通过上辊套固定;
6.所述凹辊包括下辊轴、下辊套及套接在下辊轴上的环状凹槽套,所述环状凹槽套两端通过下辊套固定;
7.所述环状凹槽套上设有与其同心设置的环状凹槽,所述环状凸缘套上设有与环状凹槽顶部相适配的环状凸缘,且所述环状凸缘的单边斜度大于所述环状凹槽的单边斜度。
8.进一步的,所述环状凹槽单边斜面角度2-8
°
。
9.进一步的,所述环状凹槽单边斜面角度3
°
。
10.进一步的,所述上辊套和环状凸缘套可拆卸安装于上辊轴上;所述下辊套和环状凹槽套可拆卸安装于下辊轴上。
11.进一步的,所述上辊套和环状凸缘套、及所述下辊套及环状凹槽套均为一体成型结构。
12.进一步的,所述环状凹槽的底部和顶部分别设有rf和rc角,所述环状凸缘底部和顶部分别设有re和rd角。
13.进一步的,所述环状凹槽顶部rc角小于所述环状凸缘顶部rd角。
14.进一步的,所述环状凹槽底部rf角小于所述环状凸缘底部re角。
15.进一步的,所述环状凹槽为下窄上宽的结构,所述环状凹槽的两侧面对称设置。
16.进一步的,所述环状凸缘为下窄上宽的结构,所述环状凸缘的两侧面对称设置,所述环状凸缘的高度小于环状凹槽的深度。
17.进一步的,所述环状凸缘与所述环状凹槽啮合轧制时,所述凸辊与凹辊间保持间隙。
18.本实用新型的优点和有益效果在于:
19.(1)环状凸缘套上环状凸缘单边斜度大于环状凹槽套上环状凹槽的单边斜度,例如凹辊上环状凹槽单边斜度3度,则凸辊上环状凸缘的单边斜度则大于3度。采用上述方式制作的凸辊与凹辊配合使用时,轧辊的受力区域将集中在环状凸缘套根部圆弧处,而不是环状凸缘套的顶部,通过这一改变,凸辊的使用寿命可以延长5-10倍,出现崩裂损坏的概率大大降低。
20.(2)环状凸缘套和环状凹槽套可拆卸设置,可便于不同尺寸环状凸缘套和环状凹槽套的更换,以满足不同尺寸双金属复合轧制,此外,环状凸缘套和环状凹槽套可拆卸设置,可便于损坏的环状凸缘套和环状凹槽套进行更换,避免凸辊和凹辊整体更换,节约成本。
附图说明
21.图1是本实用新型所述的一种双金属复合轧制用轧辊的结构示意图;
22.图2是图1中a的局部放大图;
23.图3是本实用新型的另一实施状态结构图;
24.上辊轴1、上辊套2、环状凸缘套3、下辊轴4、下辊套5、环状凹槽套6、环状凹槽7、环状凸缘8。
具体实施方式
25.下面结合附图和实施例,对本实用新型的具体实施方式作进一步描述。以下实施例仅用于更加清楚地说明本实用新型的技术方案,而不能以此来限制本实用新型的保护范围。
26.如图1-图3所示,一种双金属复合轧制用轧辊,其包括凸辊和凹辊,
27.所述凸辊包括上辊轴1、上辊套2及套接在上辊轴1上的环状凸缘套3,所述环状凸缘套3两端通过上辊套2固定;
28.所述凹辊包括下辊轴4、下辊套5及套接在下辊轴4上的环状凹槽套6,所述环状凹槽套6两端通过下辊套5固定;
29.所述环状凹槽套6上设有与其同心设置的环状凹槽7,所述环状凸缘套3上设有与环状凹槽7顶部相适配的环状凸缘8,且所述环状凸缘8的单边斜度大于所述环状凹槽7的单边斜度。
30.在上述技术方案中,环状凸缘套上环状凸缘单边斜度大于环状凹槽套上环状凹槽的单边斜度,例如凹辊上环状凹槽单边斜度3度,则凸辊上环状凸缘的单边斜度则大于3度。采用上述方式制作的凸辊与凹辊配合使用时,轧辊的受力区域将集中在环状凸缘套根部圆弧处,而不是环状凸缘套的顶部,通过这一改变,凸辊的使用寿命可以延长5-10倍,出现崩裂损坏的概率大大降低。
31.作为上述技术方案的优选,所述环状凹槽7单边斜面角度2-8
°
。
32.所述环状凹槽单边斜面角度3
°
。
33.作为上述技术方案的优选,所述上辊套2和环状凸缘套3可拆卸安装于上辊轴1上;所述下辊套5和环状凹槽套6可拆卸安装于下辊轴4上。
34.在上述技术方案中,环状凸缘套和环状凹槽套可拆卸设置,可便于不同尺寸环状凸缘套和环状凹槽套的更换,以满足不同尺寸双金属复合轧制;此外,环状凸缘套和环状凹槽套可拆卸设置,可便于损坏的环状凸缘套和环状凹槽套进行更换,避免凸辊和凹辊整体更换,节约成本。
35.作为上述技术方案的优选,如图3所示,所述上辊套2和环状凸缘套3、及所述下辊套5及环状凹槽套6均为一体成型结构。
36.作为上述技术方案的优选,所述环状凹槽7的底部和顶部分别设有rf和rc角,所述环状凸缘8底部和顶部分别设有re和rd角。环状凹槽底部rf角为了避免应力集中。
37.作为上述技术方案的优选,所述环状凹槽7顶部rc角小于所述环状凸缘8顶部rd角。
38.作为上述技术方案的优选,所述环状凹槽7底部rf角小于所述环状凸缘8底部re角。
39.作为上述技术方案的优选,所述环状凹槽7为下窄上宽的结构,所述环状凹槽7的两侧面对称设置。
40.作为上述技术方案的优选,所述环状凸缘8为下窄上宽的结构,所述环状凸缘8的两侧面对称设置,所述环状凸缘8的高度小于环状凹槽7的深度。
41.作为上述技术方案的优选,所述环状凸缘8与所述环状凹槽7啮合轧制时,所述凸辊与凹辊间保持间隙。另外,环状凸缘4底部宽度大于等于环状凹槽3底部宽度。
42.以上所述仅是本实用新型的优选实施方式,应当指出,对于本技术领域的普通技术人员来说,在不脱离本实用新型技术原理的前提下,还可以做出若干改进和润饰,这些改进和润饰也应视为本实用新型的保护范围。
技术特征:1.一种双金属复合轧制用轧辊,其特征在于,其包括凸辊和凹辊,所述凸辊包括上辊轴(1)、上辊套(2)及套接在上辊轴(1)上的环状凸缘套(3),所述环状凸缘套(3)两端通过上辊套(2)固定;所述凹辊包括下辊轴(4)、下辊套(5)及套接在下辊轴(4)上的环状凹槽套(6),所述环状凹槽套(6)两端通过下辊套(5)固定;所述环状凹槽套(6)上设有与其同心设置的环状凹槽(7),所述环状凸缘套(3)上设有与环状凹槽(7)顶部相适配的环状凸缘(8),且所述环状凸缘(8)的单边斜度大于所述环状凹槽(7)的单边斜度。2.根据权利要求1所述的一种双金属复合轧制用轧辊,其特征在于,所述环状凹槽(7)单边斜面角度2-8
°
。3.根据权利要求1或2所述的一种双金属复合轧制用轧辊,其特征在于,所述上辊套(2)和环状凸缘套(3)可拆卸安装于上辊轴(1)上;所述下辊套(5)和环状凹槽套(6)可拆卸安装于下辊轴(4)上。4.根据权利要求1或2所述的一种双金属复合轧制用轧辊,其特征在于,所述上辊套(2)和环状凸缘套(3)、及所述下辊套(5)和环状凹槽套(6)均为一体成型结构。5.根据权利要求1所述的一种双金属复合轧制用轧辊,其特征在于,所述环状凹槽(7)的底部和顶部分别设有rf和rc角,所述环状凸缘(8)底部和顶部分别设有re和rd角。6.根据权利要求5所述的一种双金属复合轧制用轧辊,其特征在于,所述环状凹槽(7)顶部rc角小于所述环状凸缘(8)顶部rd角。7.根据权利要求6所述的一种双金属复合轧制用轧辊,其特征在于,所述环状凹槽(7)底部rf角小于所述环状凸缘(8)底部re角。8.根据权利要求1所述的一种双金属复合轧制用轧辊,其特征在于,所述环状凹槽(7)为下窄上宽的结构,所述环状凹槽(7)的两侧面对称设置。9.根据权利要求6所述的一种双金属复合轧制用轧辊,其特征在于,所述环状凸缘(8)为下窄上宽的结构,所述环状凸缘(8)的两侧面对称设置,所述环状凸缘(8)的高度小于环状凹槽(7)的深度。10.根据权利要求1所述的一种双金属复合轧制用轧辊,其特征在于,所述环状凸缘(8)与所述环状凹槽(7)啮合轧制时,所述凸辊与凹辊间保持间隙。
技术总结本实用新型公开了一种双金属复合轧制用轧辊,其包括凸辊和凹辊,所述凸辊包括上辊轴、上辊套及套接在上辊轴上的环状凸缘套,所述环状凸缘套两端通过上辊套固定;所述凹辊包括下辊轴、下辊套及套接在下辊轴上的环状凹槽套,所述环状凹槽套两端通过下辊套固定;所述环状凹槽套上设有与其同心设置的环状凹槽,所述环状凸缘套上设有与环状凹槽顶部相适配的环状凸缘,且所述环状凸缘的单边斜度大于所述环状凹槽的单边斜度。通过本实用新型所述技术方案,凸辊的使用寿命得到提高,出现崩裂损坏的概率大大降低。概率大大降低。概率大大降低。
技术研发人员:朱卫 李鹏飞 张忠
受保护的技术使用者:江苏康瑞新材料科技股份有限公司
技术研发日:2022.05.25
技术公布日:2022/12/9