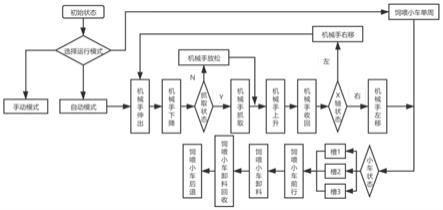
1.本发明涉及控制技术领域,尤其是一种智能饲喂控制系统、方法、计算机设备和计算机可读存储介质。
背景技术:2.目前我国家禽养殖业产业化发展程度较低,质量控制管理体制没有合理的体系进行管理,职能部门职责划分不明确;养殖集约化水平较低,千家万户的农户养殖方式难以管理和控制。散养方式是以前我国禽畜养殖的主流方式,这种方式对机械化和自动化程度要求较低,但随着养殖数量的不断增加,规模化养殖逐渐代替了散养方式。目前国内大多是以单片机(single-chip microcomputer,scm) 为主控制器的养殖场环境监控,数据采样、数据存储控制都是由单片机完成的,可编程逻辑控制器(programmable logic controller,plc)作为主控制器还未得到普及。
技术实现要素:3.发明目的:提供一种能够解决自动化养殖成本高的问题、优于单片机控制效果的智能饲喂控制系统、方法、计算机设备和计算机可读存储介质。
4.技术方案:
5.一种智能饲喂控制系统,用于对饲喂装置进行控制,所述饲喂装置包括料仓、机械手、饲喂小车及多个依次排列的食料槽,所述智能饲喂控制系统包括:模式选择单元,具有一手动模式和一自动单周模式,用于在所述手动模式下人工控制饲喂装置运行,用于在所述自动单周模式下自动控制饲喂装置运行;可编程逻辑控制单元,用于在所述自动单周模式下生成并发送取料信号、运输信号及卸料信号;取料控制单元,用于接收所述取料信号,控制机械手抓取料仓内容置的饲料并向饲喂小车提供抓取饲料;运输控制单元,用于接收所述运输信号,控制饲喂小车将抓取饲料搬运至食料槽预设位置处;卸料控制单元,用于接收所述卸料信号,控制饲喂小车向对应食料槽分配饲料。
6.进一步的,还包括:预设单元,用于使系统初始化为一初始状态;急停单元,用于控制系统运行停止。
7.进一步的,所述模式选择单元包括手动模式开关和自动单周模式开关;所述取料控制单元包括系统上电开关、系统运行指示灯、自动单周启动开关、机械手指示灯;所述运输控制单元包括饲喂小车单周启动开关、饲喂小车指示灯,其中所述饲喂包括饲喂小车前进运行状态指示灯、饲喂小车返回运行状态指示灯;所述卸料控制单元包括饲喂小车卸料和卸料回收指示灯、传感器;所述可编程逻辑控制单元包括可编程逻辑控制器,用以通过所述系统上电开关启动控制所述系统运行指示灯亮、通过自动单周启动开关控制所述机械手运行、通过所述饲喂小车单周启动开关启动控制所述饲喂小车运行,根据所述传感器采集的压力信号控制所述饲喂小车卸料和卸料回收,以及通过所述急停开关启动信号控制系统停止运行。
8.一种智能饲喂控制方法,利用智能饲喂控制系统控制饲喂装置运行,其中所述饲喂装置包括料仓、机械手、饲喂小车以及多个依次排列的食料槽,所述智能饲喂控制方法包括以下步骤:
9.系统预设及初始化,系统初始化为初始状态;
10.系统模式选择,通过模式选择定义系统运行方式为自动单周模式和手动模式,其中在手动模式下通过人工控制饲喂装置运行,在自动单周模式下自动控制饲喂装置运行;
11.在自动单周模式下,可编程逻辑控制单元生成并发送取料信号、运输信号及卸料信号;
12.取料控制单元接收所述取料信号,控制机械手抓取料仓内容置的饲料,并控制机械手向饲喂小车提供抓取饲料后返回至初始状态;
13.运输控制单元接收所述运输信号,控制饲喂小车单周模式运行以将抓取饲料搬运至多个预设食料槽位置处;
14.卸料控制单元接收所述卸料信号,控制饲喂小车卸载抓取饲料以向对应食料槽分配饲料并控制饲喂小车卸料回收,直至对所述多个预设食料槽的对应次数的卸料完成后,控制饲喂小车返回至初始状态。
15.进一步的,在控制机械手抓取料仓内容置的饲料,并控制机械手向饲喂小车提供抓取饲料后返回至初始状态的步骤中,所述机械手的运行状态包括六自由度运行状态、夹紧状态、放松状态,且还包括以下步骤:
16.控制系统上电开关启动、自动单周启动开关启动,可编程逻辑控制器向机械手发送取料信号;
17.控制机械手沿一第二方向、一第三方向运行后停止;
18.判断机械手的抓取状态为机械手夹紧状态时,控制机械手抓取料仓内的饲料;
19.控制机械手沿所述第三方向的反方向、所述第二方向的反方向运行以收回至初始状态;
20.判断机械手在所述第一方向上的位置状态相对饲喂小车较左时,控制机械手沿所述第一方向运行以右移到饲喂小车位置后停止;
21.控制机械手沿所述第二方向、所述第三方向运行后停止;
22.判断机械手的抓取状态为机械手放松状态时,控制机械手向饲喂小车提供抓取饲料,并控制机械手返回至初始状态。
23.进一步的,在控制饲喂小车单周模式下运行以将抓取饲料搬运至多个预设食料槽位置处的步骤中,还包括以下步骤:
24.在机械手抓取料仓内的饲料并向饲喂小车提供抓取饲料后,可编程逻辑控制器向饲喂小车发送运输信号并控制饲喂小车单周启动开关启动,以驱动饲喂小车向右移动后停止。
25.进一步的,在控制饲喂小车卸载抓取饲料以向对应食料槽分配饲料并控制饲喂小车卸料回收的步骤中,还包括以下步骤:
26.可编程逻辑控制器向饲喂小车发送卸料信号并控制饲喂小车卸料和卸料回收开关启动,以驱动饲喂小车卸载抓取饲料以向对应食料槽分配饲料并控制饲喂小车卸料回收;
27.多次卸料完成后,控制饲喂小车后退,直至返回初始状态,饲喂小车自动单周模式运行结束。
28.进一步的,通过压力传感器采集饲喂小车内容置抓取饲料的压力值,判断压力值是否等于压力阈值,直至该压力值等于压力阈值时,多次卸料完成,饲喂小车返回至初始状态,否则饲喂小车继续卸载抓取饲料以向对应食料槽分配饲料并进行饲喂小车卸料回收。
29.一种计算机设备,包括存储器、处理器及存储在存储器上并可在处理器上运行的计算机程序,所述处理器执行所述计算机程序时实现如上所述方法的步骤。
30.一种计算机可读存储介质,其上存储有计算机程序,所述计算机程序被处理器执行时实现如上所述的方法的步骤。
31.有益效果:本发明与现有技术相比,其具有的优点:
32.1、该智能饲喂控制系统,能够实现对饲喂装置进行手动控制和自动控制。通过可编程逻辑控制单元控制向取料控制单元提供抓取饲料、控制运输控制单元将抓取饲料运输至预设位置的食料槽,控制向卸料控制单元分配饲料,从而实现工作稳定性,能够大幅减少维护工作量,提高设备使用率。
33.2、该智能饲喂控制系统结构紧凑、体积小,功能全面,使用寿命长,市场效果好。
附图说明
34.图1为饲喂装置的结构示意图;
35.图2为本发明智能饲喂控制系统的结构示意图;
36.图3为本发明智能饲喂控制方法的流程图。
具体实施方式
37.以下结合附图,对本发明提供的技术方案做详细说明。
38.如图1至图3所示,所述的智能饲喂控制系统100,用于对饲喂装置10进行控制操作。其中,所述智能饲喂控制系统100包括预设单元110、模式选择单元120、可编程逻辑控制单元130、取料控制单元140、运输控制单元150、卸料控制单元160,以及急停单元170。并且,所述饲喂装置10包括料仓1、机械手 2、饲喂小车3、以及多个食料槽5;所述食料槽5为依次排列设置,每一食料槽 5的规格型号一致;料仓1至少为一个,图1示意性地给出一个料仓,料仓1内容置有饲料;所述饲喂小车3位于料仓1与食料槽5之间,所述机械手2设置于料仓1与所述饲喂小车3之间,所述机械手2用于抓取料仓1内的饲料并向所述饲喂小车3提供抓取饲料,所述饲喂小车3用于从料仓1一侧移动至某一特定食料槽5。
39.所述预设单元110用以使系统初始化为一初始状态,即所述饲喂装置10以及所述智能饲喂控制系统100复位为所述初始状态,等待系统上电后启动;所述模式选择单元120具有一手动模式和一自动模式,用于在手动模式下独立地人工控制饲喂装置10运行,用于在自动模式下独立地自动控制饲喂装置10运行;所述可编程逻辑控制单元130用以生成并发送取料信号、运输信号、卸料信号;所述取料控制单元140用以接收所述取料信号,控制所述机械手2抓取所述料仓1 内容置的饲料并向所述饲喂小车3提供抓取饲料;所述运输控制单元150用以接收所述运输信号,控制所述饲喂小车3将其内容置的所述抓取饲料搬运至某一食料槽5;所述卸料控制单元160,用于接收所述卸料信号,控制卸载所述饲喂小车3内的
所述抓取饲料以向对应的食料槽5提供分配饲料;所述急停单元170,用于控制系统运行停止。
40.为了独立地实现系统模式选择,所述模式选择单元120包括手动模式开关 121和自动单周模式开关122,通过手动按下所述手动模式开关121控制所述智能饲喂控制系统100进入手动模式,通过所述可编程逻辑控制单元130控制所述自动单周模式开关122启动即处于闭合状态控制所述智能饲喂控制系统100进入自动单周模式。
41.为了实现所述可编程逻辑控制单元130自动生成并发送取料信号、运输信号以及卸料信号,所述可编程逻辑控制单元130与所述预设单元110、所述模式选择单元120、所述取料控制单元140、所述运输控制单元150、所述卸料控制单元160电连接。
42.为了进一步实现根据取料信号控制所述机械手2向所述饲喂小车3提供抓取饲料,所述取料控制单元140包括一第一控制组件141、系统运行指示灯、机械手状态指示灯。所述第一控制组件141包括系统上电开关、自动单周开关。
43.当所述取料控制单元140处于工作状态时,所述第一控制组件141处于闭合状态,所述系统运行指示灯亮以及所述机械手状态指示灯亮;当所述取料控制单元140处于不工作状态时,所述第一控制组件141处于断开状态;所述可编程逻辑控制单元130用于根据所述取料信号,通过所述第一控制组件141控制所述机械手2向所述饲喂小车3提供所述抓取饲料。其中,机械手状态指示灯包括机械手沿第一方向运行状态指示灯、机械手沿第二方向运行状态指示灯、机械手沿第三方向运行状态指示灯、机械手夹紧状态指示灯、机械手放松状态指示灯。
44.并且为了实现根据所述运输信号控制所述饲喂小车3将其所容置的抓取饲料搬运至某一指定的食料槽5位置处,所述运输控制单元150包括一第二控制组件151、饲喂小车指示灯。其中,所述第二控制组件151包括饲喂小车单周开关;所述饲喂小车指示灯包括饲喂小车前进运行状态指示灯、饲喂小车返回运行状态指示灯。
45.当所述运输控制单元150处于工作状态时,所述第二控制组件151即饲喂小车单周开关处于闭合状态,所述饲喂小车指示灯即饲喂小车前进运行状态指示灯或饲喂小车返回运行状态指示灯亮;当所述运输控制单元150处于不工作状态时,所述第二控制组件151处于断开状态,所述饲喂小车指示灯暗;所述可编程逻辑控制单元130用以接收所述运输信号,通过所述第二控制组件151控制所述运输控制单元150搬运所述抓取饲料至任一食料槽5,即控制所述饲喂小车前进运行状态指示灯亮。
46.以及为了实现根据所述卸料信号控制卸载所述饲喂小车3的抓取饲料并向对应的食料槽5分配饲料,所述卸料控制单元160包括一第三控制组件161、饲喂小车卸料和卸料回收指示灯。所述第三控制组件161包括传感器。
47.当所述卸料控制单元160处于工作状态时,所述饲喂小车卸料和卸料回收指示灯亮,当所述卸料控制单元160处于不工作状态时,所述饲喂小车卸料和卸料回收指示灯暗;所述可编程逻辑控制单元130用以控制所述卸料控制单元160 向对应的食料槽5提供所述分配饲料,并用以根据所述传感器采集的压力信号控制所述饲喂小车运行,并控制所述饲喂小车返回运行状态指示灯亮。
48.具体地,所述传感器用于监测所述饲喂小车3内容置的所述抓取饲料的压力,以生成并发送压力信号至所述可编程逻辑控制单元130。所述可编程逻辑控制单元130基于所述
压力信号,判断所述卸料是否完成。具体地,当接收的所述压力信号为零时,所述可编程逻辑控制单元130基于所述压力信号为零的情况下,生成并发送卸料终止信号;所述卸料控制单元160用以根据接收的所述卸载终止信号,控制所述饲喂小车3停止卸料。
49.为了实现机械手2向饲喂小车3内提供抓取饲料,所述运输控制单元140 将其容置的抓取饲料搬运至某一特定的食料槽5或某一指定的食料槽5位置处;所述运输控制单元还包括位置传感器,用于监测机械手2相对于饲喂小车3的相对位置、饲喂小车3与相对于食料槽5的预设位置相匹配时的位置,并发送上述的位置信号至所述可编程逻辑控制单元110,所述可编程逻辑控制单元110用于根据位置信号控制机械手2相对于饲喂小车3定位、以及控制饲喂小车3相对食料槽5定位。
50.此外,为了实现在系统故障时通过所述急停单元170驱动系统运行停止,所述急停单元170包括急停开关,所述可编程逻辑控制单元130通过控制所述急停开关启动,以实现系统运行停止。且在手动模式下,通过手动关闭所述急停开关也可紧急终止系统运行。
51.所述控制系统还具有故障报警单元,用以在所述控制系统故障时发出报警信息,并通过手动或自动关闭所述急停单元170以紧急终止所述控制系统的运行。
52.所述系统上电开关、所述自动单周模式开关、所述饲喂小车单周开关、所述自动单周开关、所述急停开关可以为电磁阀开关、气动阀开关的任一种。
53.所述可编程逻辑控制单元130包括可编程逻辑控制器,所述可编程逻辑控制器的输入端连接至所述传感器、所述系统上电开关、所述自动单周模式开关、所述自动单周开关、所述饲喂小车单周开关、所述急停开关;所述可编程逻辑控制的输出端连接至所述系统运行指示灯、所述机械手状态指示灯、所述饲喂小车状态指示灯、所述饲喂小车卸料和卸料回收指示灯。所述可编程逻辑控制器用以通过所述系统上电开关启动控制所述系统运行指示灯亮、通过自动单周启动开关启动控制所述机械手运行、通过所述饲喂小车单周启动开关启动及所述传感器采集的压力信号控制所述饲喂小车运行,以及通过所述急停开关启动控制系统停止运行。
54.所述可编程逻辑控制单元130包括:处理器模块、数字量模块和模拟量模块;其中,所述处理器模块用于运行所述基于可编程逻辑控制器的智能饲喂控制系统的程序,并生成相应的控制信号;所述数字量模块用于基于所述处理器模块生成的控制信号,将数字量信号发送至各个模块;所述模拟量模块用于将接收到的各个单元发送的信号以数字量信号的形式发送至所述处理器模块。
55.本发明还提供一种智能饲喂控制方法,利用智能饲喂控制系统控制饲喂装置运行,其中所述饲喂装置包括料仓、机械手、饲喂小车以及多个依次排列的食料槽,其特征在于,所述智能饲喂控制方法包括以下步骤:
56.(1)、系统预设及初始化,系统初始化为初始状态;
57.获取初始状态下的系统控制参数信号,包括启动、停止、急停、设备运行状态、系统控制参数监控、故障信息;
58.(2)、系统模式选择,通过模式选择定义系统运行方式为自动单周模式和手动模式,其中在手动模式下通过人工控制饲喂装置运行,在自动单周模式下自动控制饲喂装置运行;
59.在本步骤中,通过控制自动单周模式开关启动,使系统处于自动单周模式,通过控
制手动开关启动,使系统处于手动模式。
60.当用户选择手动模式时,即用户手动驱动所述手动开关处于闭合状态,所述机械手2、所述饲喂小车3根据用户需求进行定量移动,可通过独立地控制所述取料控制单元140的所述第一控制件141闭合或断开、所述运输控制单元150 的所述第二控制件151的闭合或断开、所述卸料控制单元160工作。
61.当系统处于手动模式下,根据满足用户需求的预设位置可单独控制所述机械手2、所述饲喂小车3运行。
62.当无人操作时,所述模式选择单元120默认为处于自动单周模式。
63.(3)、在自动单周模式下,可编程逻辑控制单元生成并发送取料信号、运输信号及卸料信号;
64.(4)、取料控制单元接收取料信号,控制机械手抓取料仓内容置的饲料,并控制机械手向饲喂小车提供抓取饲料后返回至初始状态;
65.在本步骤中,所述机械手的运行状态包括六自由度运行状态、夹紧状态、放松状态;
66.(5)、运输控制单元接收所述运输信号,控制饲喂小车单周模式运行以将抓取饲料搬运至多个预设食料槽位置处;
67.在本步骤中,在机械手2抓取料仓内的饲料并向饲喂小车3提供抓取饲料后,可编程逻辑控制器向饲喂小车3发送运输信号并控制饲喂小车单周按钮启动,以驱动饲喂小车3向右移动后停止。
68.(6)、卸料控制单元接收所述卸料信号,控制饲喂小车卸载抓取饲料以向对应食料槽分配饲料并控制饲喂小车卸料回收,直至对所述多个预设食料槽的对应次数的卸料完成后,控制饲喂小车返回至初始状态;
69.本步骤具体包括以下步骤:
70.(61)、可编程逻辑控制器向饲喂小车3发送卸料信号并控制饲喂小车卸料和卸料回收按钮启动,以驱动饲喂小车3卸载抓取饲料以向对应食料槽5分配饲料并控制饲喂小车卸料回收;
71.(62)、多次卸料完成后,控制饲喂小车3后退,直至返回初始状态,饲喂小车3自动单周模式运行结束。
72.在步骤(62)中,通过压力传感器采集饲喂小车3内容置抓取饲料的压力值,判断压力值是否等于压力阈值,直至该压力值等于压力阈值时,三次卸料完成,饲喂小车3返回至初始状态,否则饲喂小车3继续卸载抓取饲料以向对应食料槽分配饲料并进行饲喂小车卸料回收。
73.在步骤(3)至步骤(6)中,系统处于自动单周模式,系统在自动单周模式下的工作过程为:跳转至取料控制单元140,取料控制单元140根据取料信号控制机械手2即机械手从料仓1内单次等量抓取饲料,抓取饲料结束后,机械手2 移至饲喂小车3的上方,将定量分配饲料投放入饲喂小车3内,完成取料环节;跳转至运输控制单元150,运输控制单元150控制饲料小车3将抓取饲料运送至指定食料槽5前,其中饲喂小车3根据预设位置的设定,进行等距顺序移动,并停至食料槽5前;然后跳转至卸料控制单元160,卸料控制单元160控制饲喂小车3将饲料投放入食料槽5中,其中基于传感器121采集的饲喂小车3内的抓取饲料的重量
值为零时,饲喂小车3的整个卸料工作完成;期间,若所述控制系统在运行中出现故障,基于故障报警单元发出报警信息,通过按压急停单元170 的急停按钮,使得系统立即停止工作,确保生命财产安全。在任意模式内按下所述急停按钮,程序立即停止,确保安全。
74.在一具体实施例中,结合图3和表1,表1为可编程逻辑控制器的输入输出端口节点分配表,其中i-19表示控制系统上电,i-20表示自动单周模式启动,i-21 表示饲喂小车单周启动,i-23表示急停,o-11表示控制系统运行指示灯,o-12、 o-13、o-14分别表示机械手x、y、z轴运动状态指示灯,o-15表示机械手夹紧状态指示灯,o-16、o-17分别表示饲喂小车前进、返回状态指示灯,o-18表示饲喂小车卸料和卸料收回状态指示灯,当指示灯亮起时表示该状态处于运行中。系统运行过程如下:
75.该控制系统初始状态时:当可编程逻辑控制器(plc)初始化通电之后复位所有的输出o-11至o-18,等待上电后启动。
76.手动模式/自动单周模式下运行:当控制系统处于手动模式的运行状态时,每按下一次自动单周模式开关和饲喂小车单周开关,机械手2和饲喂小车3才会进行相应的移动;当控制系统处于自动运行状态时,该控制系统自行运转;所述控制系统通电后,开始选择运行模式即包括自动单周模式和手动模式,控制系统默认处于自动单周模式。
77.表1可编程逻辑控制器的输入输出端口节点分配表
[0078][0079]
自动单周模式下,该控制系统进入取料控制单元140运行,过程具体包括以下步骤,其中,下述的第一方向为x轴,第二方向为y轴,第三方向为z轴:
[0080]
(41)、控制系统上电开关启动、自动单周启动开关启动,可编程逻辑控制器向机械手2发送取料信号;
[0081]
即,自动单周模式开关i-20启动后,控制系统运行指示灯o-11亮,该控制系统进入运行状态;
[0082]
(42)、控制机械手2沿一第二方向运行以伸出后停止;
[0083]
即,机械手2伸出,y轴运动状态指示灯o-13亮红灯,运行10秒后,y轴运动状态指示灯灭,机械手y轴停止运行。
[0084]
(43)、控制机械手沿一第三方向运行以下降后停止;
[0085]
即,接着机械手2下降,z轴运动状态指示灯o-14亮红灯,运行5秒后,z 轴运动状态指示灯灭,机械手2沿着z轴停止运行。
[0086]
(44)、判断机械手的抓取状态为机械手夹紧状态时,控制机械手抓取料仓内的饲料;
[0087]
即,机械手2夹紧,夹紧状态指示灯o-15亮红灯,运行2秒后,夹紧状态指示灯灭。
[0088]
(45)、控制机械手沿所述所述第三方向的反方向运行以上升后停止;
[0089]
即,机械手2上升,z轴运动状态指示灯o-14亮红灯,运行5秒后,z轴运动状态指示灯灭,机械手2沿着z轴停止运行。
[0090]
(46)、控制机械手沿所述第二方向的反方向运行以收回至初始状态;
[0091]
即,机械手2收回,y轴运动状态指示灯o-13亮红灯,运行10秒后,y轴运动状态指示灯灭,机械手y轴停止运行。
[0092]
(47)、判断机械手在所述第一方向上的位置状态相对较左时,控制机械手沿所述第一方向运行右移后停止;
[0093]
即,机械手2右移,x轴运动状态指示灯o-12亮红灯,运行35秒后,x轴运动状态指示灯灭,机械手x轴停止运行。
[0094]
(48)、控制机械手沿所述第二方向运行以伸出后停止;
[0095]
即,机械手2伸出,y轴运动状态指示灯o-13亮红灯,运行10秒后,y轴运动状态指示灯灭,机械手y轴停止运行。
[0096]
(49)、控制机械手沿所述第三方向运行以下降后停止;
[0097]
即,机械手2下降,z轴运动状态指示灯o-14亮红灯,运行5秒后,z轴运动状态指示灯灭,机械手z轴停止运行。
[0098]
(50)、判断机械手2的抓取状态为机械手放松状态时,控制机械手2向饲喂小车3提供抓取饲料,并控制机械手2返回至初始状态。
[0099]
即,机械手2放松,将抓取饲料投放入饲喂小车3中。将抓取饲料投放入饲喂小车3后,机械手2自行回到初始状态,以此往复,机械手2完成向饲喂小车 3提供抓取饲料。
[0100]
接着,跳转至运输控制单元150后,机械手2每次抓取定量的分配饲料放入饲喂小车3后,饲喂小车3开始向右移动,饲喂小车3前进运行状态指示灯o-16 亮红灯,运行10秒后,饲喂小车3前进运行状态指示灯灭,饲喂小车3停止运行。
[0101]
接着,饲喂小车3进入到卸料控制单元160,饲喂小车卸料和卸料回收状态指示灯o-18亮红灯,运行13秒后,饲喂小车卸料和卸料回收状态指示灯灭,卸料和卸料回收完成。对相邻的三个食料槽共进行三次卸料后,通过饲喂小车3 上装有的压力传感器感知,当饲
喂小车重量恢复到装料前的重量时,即压力传感器监测到的饲喂小车3内容置的抓取饲料的重量值为零时,饲喂小车3整个卸料工作完成;饲喂小车3进入到返回状态,饲喂小车3左移,饲喂小车返回运行状态指示灯o-17亮红灯,运行40秒后,饲喂小车返回运行状态指示灯灭,饲喂小车3停止运行,回到了初始状态,等待下一次机械手投放饲料,自动单周循环结束。
[0102]
独立地按下饲喂小车单周开关i-21后,饲喂小车3的运行过程与自动单周模式中的饲喂小车3的运行过程一样。
[0103]
在急停单元170中,当独立地按下急停开关i-23,无论该控制系统处于自动单周模式下,还是处于手动模式下,控制系统的运行程序都会立即停止,确保人员生命财产安全。
[0104]
本发明还提供一种计算机设备,包括存储器、处理器及存储在存储器上并可在处理器上运行的计算机程序,所述处理器执行所述计算机程序时实现如上所述方法的步骤。
[0105]
本发明还提供一种计算机设备,其上存储有计算机程序,所述计算机程序被处理器执行时实现如上所述的方法的步骤。
[0106]
所述的智能饲喂控制系统、方法、计算机设备、计算机设备,能够实现对饲喂装置10进行自动控制。通过可编程逻辑控制单元130控制向取料控制单元140 提供抓取饲料、运输控制单元150将抓取饲料运输至特定的食料槽5,以及向卸料控制单元160分配饲料,从而实现该控制系统的工作稳定性,基于对可编程逻辑控制器(plc)的运用,能够大幅减少维护工作量,提高设备使用率。该控制系统结构紧凑、体积小,功能全面,使用寿命长,市场效果好。