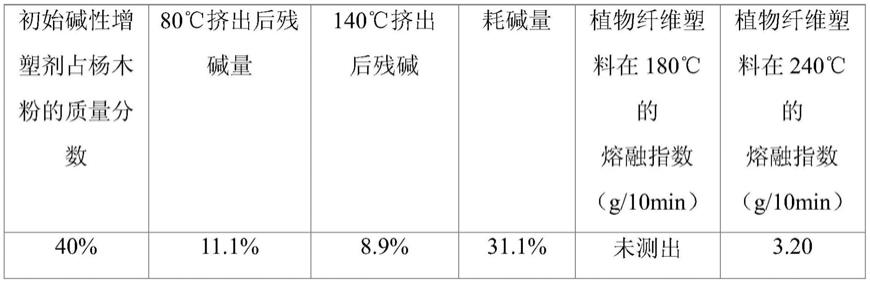
1.本发明属于植物纤维生物质材料技术领域,具体涉及一种具有生物可降解性的植物纤维塑料及其制备方法。
背景技术:2.塑料制品应用领域广泛,已成为人们生活中不可或缺的一部分。然而塑料原料来源紧张、塑料废弃物的不可降解产生“白色污染”等带来资源和环境问题,制约人类社会的可持续发展。因此,加强农林作物和木材的利用,致力于开发生物可降解性的塑料,制备出新型环保的植物纤维塑料以代替传统塑料制品具有重大意义。
3.然而,目前植物纤维塑料的制备主要有以下问题:植物纤维本身不具有热可塑性,因此不能在高温条件下熔融加工;传统的酯化、醚化、离子液体和低共熔溶剂等塑化反应虽然可实现植物纤维的塑化加工,但改性后会引起原料较大程度的降解,导致材料力学性能变差。
4.中国专利cn109721770a公开一种氧化还原性的热塑性和韧性调控方法,包括以下步骤:(1)植物纤维的前处理;(2)加入氧化剂溶液反应后经过滤洗涤得到氧化改性植物纤维;加入还原剂溶液反应后过滤洗涤得到氧化还原改性植物纤维;(3)加入增塑剂与氧化还原改性植物纤维混合均匀;所述增塑剂包含羟基类、离子液体类、低共熔溶剂类、酯类、胺类、缩水甘油醚类或无机盐类。该方法虽然能降低植物纤维原料的玻璃化转变温度,达到加工温度,具有较好的热可塑性,但是需要使用大量氧化剂、还原剂、离子液体类和低共熔溶剂类增塑剂,使成本提高,而且污染环境,工艺操作复杂,难以实现工业化生产,偏离了未来材料绿色可持续发展的原则。
技术实现要素:5.为了克服上述存在的问题,本发明基于高温高碱、高剪切和/或挤压、熔融塑化原理对植物纤维直接塑化,提供一种具有生物可降解性的植物纤维塑料及其制备方法。所述方法可以降低植物纤维塑料的玻璃化温度及加工温度,绿色环保,操作简单高效,能耗低,获得的植物纤维塑料具有优异的流动性和熔融指数,同时也具有良好的生物可降解性,可替代传统的不可降解塑料。
6.第一方面,本发明提供一种具有生物可降解性的植物纤维塑料的制备方法。所述制备方法包括以下步骤:将包含植物纤维与碱性增塑剂的原料混合均匀得到混合物,其中碱性增塑剂占植物纤维的20
‑
100wt%,优选为30
‑
40wt%,更优选为35
‑
40wt%;将混合物投入塑炼装置,在高温高碱作用下混合物熔融并经过挤压和/或剪切,通过增塑形成微观无明显纤维形状、流动性好的植物纤维塑料。
7.本发明所述制备方法,基于高温高碱、高剪切挤压熔融塑化原理,将植物纤维与碱性增塑剂混炼直接塑化成植物纤维塑料。碱性增塑剂在高温高碱与高剪切挤压条件下破坏植物纤维,使得植物纤维中的三大组分
‑
木质素、半纤维素及纤维素发生酚型木质素酸碱中
和反应、酯键木质素皂化反应、半纤维素的乙酰基的皂化反应、半纤维素聚木糖的己烯糖醛酸反应、纤维素剥皮反应等。以上反应大量消耗了碱性增塑剂,也使得三大组分各自的聚合度和分子量降低。而降解的木质素小分子及溶出抽提物又在混炼时发挥着增塑剂的作用。小分子增塑剂与上述三大组分的分子量降低产生协同作用,降低植物纤维的玻璃化转变温度。整个塑化过程中,植物纤维在碱性增塑剂的高温高碱、高剪切熔融塑化作用下由固态转变成黏弹态,最终制备获得黏度低、流动性好、熔融指数高的生物可降解性的植物纤维塑料。
8.较佳地,所述碱性增塑剂为氢氧化钠、氢氧化钙、氢氧化钾和氢氧化锂中的一种或多种的混合物,优选氢氧化钠。
9.较佳地,所述植物纤维包括木材原料纤维、非木材原料纤维、纸浆中的至少一种。
10.较佳地,所述塑炼装置的加热温度为80
‑
300℃,优选为120
‑
160℃,更优选为140
‑
160℃。
11.较佳地,所述塑炼装置为单螺杆挤出机、双螺杆挤出机或多螺杆挤出机;优选地,单螺杆挤出机的转速为10
‑
120转/分钟;双螺杆挤出机的转速为100
‑
1200钟;多螺杆挤出机的转速为100
‑
600转/分钟。
12.较佳地,所述塑炼装置为开炼机或密炼机;优选地,开炼机的前后辊转速比为1.0
‑
1.5;密炼机的前后辊转速比为1.0
‑
1.2。
13.本发明的制备方法以价格低廉、来源广泛的木材原料纤维、非木材原料纤维、和再加工的各种纸浆等为原料,通过特定工艺获得生物可降解性的、均相混合的植物纤维塑料。
14.第二方面,本发明提供上述任一项所述的制备方法获得的植物纤维塑料。
15.较佳地,所述植物纤维塑料的玻璃化转变温度低于其热降解温度;优选地,所述植物纤维塑料的玻璃化转变温度为160
‑
180℃;更优选地,所述植物纤维塑料的玻璃化转变温度为164
‑
172℃。
16.较佳地,所述植物纤维塑料在180
‑
260℃的熔融指数为1
‑
90.9g/10min,优选为16
‑
40g/10min,更优选为20
‑
40g/10min。
17.较佳地,根据酸碱滴定法植物纤维塑料中碱性增塑剂的残余量为6
‑
9wt%,优选为8.6wt%
‑
8.9wt%。
18.本发明的植物纤维塑料具有良好的热塑性和机械强度,可应用于地膜材料、包装材料、建筑材料、汽车材料等领域,具有良好的工业前景。而且,植物纤维本身无熔融指数,塑化后的植物纤维塑料的熔融指数相较于植物纤维得以大幅度提升,流动性也获得提高。而且,所得植物纤维塑料能适用于热压、模压、注塑成型等各种成型加工工艺。
附图说明
19.图1是植物纤维原料杨木粉的扫描电镜图;图2是实施例3制备的植物纤维塑料的照片;图3是实施例4制备的植物纤维塑料的表面扫描电镜图;图4是实施例4制备的植物纤维塑料的tg曲线(a)和dsc曲线(b);图5是实施例5制备的植物纤维塑料的截面扫描电镜图;图6是实施例5制备的植物纤维塑料的tg曲线(a)和dsc曲线(b);
图7是实施例1
‑
5制备的植物纤维塑料的tg对比曲线;图8是实施例5制备的植物纤维塑料的注塑成型样条;图9是对比例2挤出获得的黄粉。
具体实施方式
20.以下通过下述实施方式进一步说明本发明,应理解,下述实施方式仅用于说明本发明,而非限制本发明。在本发明未作具体说明的情况下,“碱性增塑剂”也可以称为“碱增塑剂”。
21.将植物纤维与碱性增塑剂按比例混合,经塑炼装置在一定温度和转速下反复剪切、混炼,通过高温热处理和强物理机械作用,制备出可多次加工的、混合均匀的生物可降解性植物纤维塑料。该塑料可通过塑料加工工艺形成各种塑料制品。
22.以下示例性说明本发明所述具有生物可降解性的植物纤维塑料的制备方法。
23.将植物纤维与碱性增塑剂按比例混合。碱性增塑剂占植物纤维的质量比为20%
‑
100%。碱性增塑剂包括但不局限于氢氧化钠、氢氧化钙、氢氧化钾和氢氧化锂中的一种或多种的混合物。所述植物纤维原料包括但不局限于木材原料纤维、非木材原料纤维、纸浆中的至少一种。应理解任何形式的含植物纤维的原材料均可以作为本发明的植物纤维使用。
24.上述混合方式优选为干法混合。即、植物纤维塑料的制备优选在无水体系下进行。
25.作为优选,碱性增塑剂占植物纤维的质量比为30
‑
40%。在同等塑炼条件参数下,当碱性增塑剂占植物纤维的质量比在上述范围时,足够的碱性增塑剂达到植物纤维熔融塑化反应的可及度,耗碱量达到合适的范围,因而获得的植物纤维塑料塑化效果好、熔体流动速率高。
26.作为进一步优选的实施方式,碱性增塑剂占植物纤维的质量百分比为35
‑
40%。在该范围内,所得植物纤维塑料不仅具有良好的热塑性,而且具有优异的熔融性能。
27.所述植物纤维的目数为20
‑
1000目,优选为20
‑
100目。
28.将混合物投入塑炼装置,在高温高碱作用下,经过挤压和/或剪切,混合物熔融并得以增塑形成微观无明显纤维形状、流动性良好的植物纤维塑料。
29.所述塑炼装置的加热温度为80
‑
300℃,优选为120
‑
160℃。该加热温度范围可以达到塑化加工温度而又不超过材料的降解温度。塑炼装置的加热温度过低,即使在高碱性增塑剂的浓度下,也依然无法实现良好的塑化效果。这是因为加热温度对碱性增塑剂打开纤维细胞壁有着重要的作用,低温仅能使得木粉润胀,而无法促使植物纤维细胞壁被熔融塑化,这也进一步导致碱性增塑剂没有与植物纤维的主要组分发生相应反应。以上均不利于植物纤维塑料的塑化效果。然而加热温度较高,例如在180
‑
220℃,植物纤维降解产生的具有增塑作用的小分子逸出,这也不利于植物纤维塑料的充分塑化。更优选地,塑炼装置的加热温度为140
‑
160℃。
30.碱性增塑剂的质量分数、塑炼装置的加热温度、以及塑炼装置的高剪切或者挤压作用对植物纤维的高温高碱熔融塑化共同起着决定作用。充分混合后的物料在塑炼装置的高温高碱、高剪切和/或挤压作用下,植物纤维原料的流动性和热塑性得以改善,得到黏度低、流动性好、熔融指数高的生物可降解塑料。
31.一些实施方式中,利用单螺杆挤出机对混合料进行剪切、混炼。例如,将混合料送
入单螺杆挤出机,在单螺杆挤出机的机械挤压、剪切作用下进行混炼。单螺杆挤出机的加热温度为80~300℃,转速优选为10~120转/分钟。
32.一些实施方式中,利用双螺杆挤出机对混合料进行剪切、混炼。例如,将混合料送入双螺杆挤出机,在双螺挤出机杆的机械挤压、剪切作用下进行混炼。双螺杆挤出机的加热温度为80~300℃(优选为120~160℃),转速为100~1200转/分钟(优选200
‑
600转/分钟)。
33.一些实施方式中,利用多螺杆挤出机对混原料进行剪切、混炼。例如,将混合料送入多螺杆挤出机,在多螺杆挤出机的机械挤压、剪切作用下进行混炼。多螺杆挤出机的加热温度为80~300℃(优选为120~300℃),转速优选为100~600转/分钟。
34.一些实施方式中,利用开炼机对混合料进行剪切、混炼。例如,将混合料送入开炼机,在开炼机的机械挤压、剪切作用下进行混炼。开炼机的加热温度80~300℃(优选为150~300℃),前后辊转速比优选为1.0~1.5。前、后辊的转速在10转/分钟以下。
35.一些实施方式中,利用密炼机对混合料进行剪切、混炼。例如,将混合料送入密炼机,在密炼机的机械挤压、剪切作用下进行混炼。密炼机的加热温度80~300℃(优选为150~300℃),前后辊转速比优选为1.0~1.2。前、后辊的转速在10转/分钟以下。
36.本发明的制备方法与现有技术相比,原料来源广、价格低廉,绿色环保,增塑剂无毒易得,所得产品应用范围广,具有良好的工业前景。
37.本发明的制备方法所得植物纤维塑料的微观形貌中观察不出纤维形态,而且没有明显的分层现象,说明植物纤维塑化效果好,可直接制备得到生物可降解性的塑料。
38.本发明的制备方法所得植物纤维塑料的玻璃化转变温度低于其热降解温度。玻璃化转变温度(tg)远低于其热降解的温度,说明该材料具有良好的热可塑性。
39.通常植物纤维的热降解温度在275℃左右。作为优选,本发明植物纤维塑料的玻璃化转变温度在160
‑
180℃之间。可以看出植物纤维塑料的玻璃化转变温度相较于植物纤维原料的热降解温度大幅度降低。
40.所述植物纤维塑料的熔融指数为1
‑
90.9g/10min,优选为16
‑
40g/10min,更优选为20
‑
40g/10min。植物纤维塑料的熔融指数优异,说明该材料能适用于塑料制品的热压和注塑加工成型。
41.根据酸碱滴定法表明碱性增塑剂占植物纤维原料质量比的30%
‑
40%制备的植物纤维塑料中碱性增塑剂的残余量为6
‑
9wt%(优选8.6%
‑
8.9%)。可以计算得出碱性增塑剂的消耗量可达到20%
‑
35%(优选21%
‑
31%),这也从侧面证实高温、高碱、高剪切和/或挤压对植物纤维原料形成较好的塑化效果具有促进作用。
42.本发明的制备方法所得植物纤维塑料还具有良好的机械强度。包括拉伸强度、断裂伸长率和弯曲强度。
43.下面进一步例举实施例以详细说明本发明。应理解,以下实施例只用于对本发明进行进一步说明,不能理解为对本发明保护范围的限制,本领域的技术人员根据本发明的上述内容作出的一些非本质的改进和调整均属于本发明的保护范围。下述示例具体的工艺参数等也仅是合适范围中的一个示例,即本领域技术人员可以通过本文的说明做合适的范围内选择,而并非要限定于下文示例的具体数值。
44.植物纤维塑料的扫描电镜图(sem)通过fei quanta
‑
200型号的扫描电子显微镜,在20kv的加速电压下对试样的断面或表面形貌进行表征。
45.植物纤维塑料的拉伸强度使用utm6503型电子万能试验机,根据标准gb/t 1040.3
‑
2006,计算公式为:σ
t
:拉升强度,mpa;a:横截面积,mm2;b:试样宽度,mm;d:试样厚度,mm;f:最大负荷,n。
46.植物纤维塑料的断裂伸长率使用utm6503型电子万能试验机,根据标准gb/t1040.3
‑
2006,计算公式为:ε
t
:断裂伸长率,%;l0:试样长度,mm;l1:断裂时长度,mm。
47.植物纤维塑料的弯曲强度使用utm6503型电子万能试验机,根据标准gb/t 1040.3
‑
2006,计算公式为:σ
f
:弯曲强度,mpa;f:最大载荷,n;l:跨度,mm;b:宽度,mm;d:厚度,mm。
48.植物纤维塑料的热重分析(tga)采用ta
‑
60型号的热重分析仪,流动气氛为氮气,氮气流量是20
‑‑
30ml/min,温度范围为30
‑
600℃,升温速率为10℃/min。
49.植物纤维塑料的差式扫描量热采用dsc214型号的差示扫描量热仪,流动气氛为氮气,氮气流量是40
‑
60ml/min,温度范围为30
‑
220℃,升温速率为10℃/min。
50.植物纤维塑料的残碱测定方法采用酸碱滴定法。一些实施方式中,用千分之天平称量m0=1.43g的植物纤维塑料,溶于98.5ml的去离子水中磁力搅拌12h,待其完全溶解,形成待测碱液备用。另外,再准备0.1mol/l的标准稀hcl溶液备用。根据酸碱滴定法,用移液管每次量取25ml待测碱液置于烧杯中,ph计测定实时酸碱值。用100
‑
1000μl移液枪进行酸碱滴定,待ph值示数为7.00
±
0.05即滴定结束,记录下0.1mol/l hcl标准溶液的消耗体积v1,并进行3次平行实验取平均值。c1*v1=c2*v2。c1指的是标准稀hcl溶液浓度,为0.1mol/l。c2指的是植物纤维塑料配置的待测碱液的浓度,v2指的是移液管量取的待测碱液的体积。残碱的质量分数(%)=(c2*v0*m
naoh
)/m0*100%。其中,v0指的是配置的待测碱液体积,m
naoh
指的是氢氧化钠的相对分子质量,m0指的是用于配置待测碱液的植物纤维塑料的质量。
51.植物纤维塑料的熔融指数是试样在一定温度下,熔体在10min内流经标准毛细管的质量值,单位是g/10min。使用xrz
‑
400
‑
1型熔融指数测试仪。
52.下面进一步例举实施例以详细说明本发明。同样应理解,以下实施例只用于对本发明进行进一步说明,不能理解为对本发明保护范围的限制,本领域的技术人员根据本发明的上述内容作出的一些非本质的改进和调整均属于本发明的保护范围。下述示例具体的工艺参数等也仅是合适范围中的一个示例,即本领域技术人员可以通过本文的说明做合适的范围内选择,而并非要限定于下文示例的具体数值。
53.实施例1一种具有生物可降解性的植物纤维塑料的制备方法,具体为:称取200g风干杨木粉待用。称取80g片状固体naoh(碱性增塑剂占杨木粉质量的40%),溶于100g水中形成碱溶液。将上述杨木粉与碱溶液混合均匀得到混合料。设置双螺杆挤出机ⅰ、ⅱ、ⅲ、ⅳ、
ⅴ
、
ⅵ
、
ⅶ
、
ⅷ
、
ⅸ
、
ⅹ
、xi各区段温度均为80℃。将混合料加入双螺杆挤出机,设置转速250转/分钟,完成第一次挤出。第一次挤出得到的物料是比较大粒径的颗粒状,物料塑化效果不佳,通过热压机在160℃热压得到的膜片没有很好的延展流动性。随即将双螺杆挤出机各区段的温
度升温至140℃,进行第二次挤出以获得更好的塑化效果。
54.植物纤维本身不具备热塑性,经热压机热压后仍保持原来的木粉状。该实施例制备的植物纤维塑料通过热压后,物料形成膜片则说明了该植物纤维塑料具有较好的热塑性。植物纤维在有水体系条件下完成塑化,虽然挤出物料具备一定的热塑性,但是熔融指数即熔体流动速率低,仅为3.20g/10min。这是因为在有水体系下,碱性增塑剂为碱溶液体系,水在挤出过程中起到了润化作用使得塑化过程中的剪切作用降低,导致碱性增塑剂与植物纤维中的三大组分(纤维素、半纤维素与木质素)的反应可及度降低,也即反应程度降低。因而该条件下挤出物料的分子量相较于无水体系挤出物料的分子量高,熔融指数低。实施例1的残碱和熔融指数测定
55.实施例2一种具有生物可降解性的植物纤维塑料的制备方法,具体为:称取300g风干杨木粉待用。称取120g片状固体naoh(碱性增塑剂占杨木粉质量的40%)。将杨木粉与naoh混合均匀得到混合料。设置双螺杆挤出机ⅰ、ⅱ、ⅲ、ⅳ、
ⅴ
、
ⅵ
、
ⅶ
、
ⅷ
、
ⅸ
、
ⅹ
、xi各区段温度均为150℃。将混合料加入双螺杆挤出机,设置转速250转/分钟,挤出得到植物纤维塑料。
56.该实施例使用无水体系,在高温高碱、高剪切挤压的作用下,制备得到拉丝片状的植物纤维塑料。且该植物纤维塑料具有良好的热塑性和优异的熔融指数。实施例2的残碱和熔融指数测定
57.实施例3与实施例2基本相同,区别仅在于:碱性增塑剂占杨木粉的质量分数为30%,即使用90g片状固体naoh。该实施例同样制备得到拉丝状的植物纤维塑料(见图2)。该实施例制备的植物纤维塑料使用热压机在160℃热压时热塑性较差,而在220℃热压时则有较好的热塑性。实施例3的残碱和熔融指数测定
58.实施例4一种具有生物可降解性的植物纤维塑料的制备方法,具体为:称取300g风干杨木粉待用。称取105g片状固体naoh(碱性增塑剂占杨木粉质量的35%)。将杨木粉与naoh混合均匀得到混合料。设置双螺杆挤出机ⅰ、ⅱ、ⅲ、ⅳ、
ⅴ
、
ⅵ
、
ⅶ
、
ⅷ
、
ⅸ
、
ⅹ
、xi各区段温度均为150℃。将混合料加入双螺杆挤出机,设置转速250转/分钟,挤出形成熔融拉丝的植物纤维塑料。利用sem对实施例4的试样进行扫描分析(见图3),可以看出该植物纤维塑料没有明显纤维形态,形貌平整光滑,说明已经被塑化。对实施例4制备的植物纤维塑料进行热重和dsc分析(见图4中的a和b),该植物纤维复合塑料的外推起始降解温度(外推起始温度是指热重基线与tg线最大斜率切线交点,其更准确的反应了该样品的初始分解温度)在243℃左右,最大降解温度在278℃左右,玻璃化转变温度在160℃左右。玻璃化转变温度低于初始降解温度,说明该植物纤维塑料具有良好的热可塑性。
59.实施例5一种具有生物可降解性的植物纤维塑料的制备方法,具体为:称取300g风干杨木粉待用。称取120g片状固体naoh(碱性增塑剂占杨木粉质量的40%)和90g甘油(甘油占杨木粉质量的30%)。将杨木粉、naoh和甘油混合均匀得到混合料。设置双螺杆挤出机ⅰ、ⅱ、ⅲ、ⅳ、
ⅴ
、
ⅵ
、
ⅶ
、
ⅷ
、
ⅸ
、
ⅹ
、xi各区段温度均为140℃。将混合料加入双螺杆挤出机,设置转速250转/分钟,挤出形成光泽感好、拉丝效果优异的植物纤维塑料。
60.该实施例在植物纤维塑料的配方中添加甘油,物料光泽感变好,颜色变浅为棕色。将本实施例植物纤维塑料通过注塑机注塑成型,设置模头温度160℃、压力0.5mpa,注塑成型,制备出标准样条。利用电子万能拉力试验机进行机械性能检测。可看出该植物纤维塑料具有很好的机械性能。实施例5的机械强度测定
61.对植物纤维的sem图(图1)与本实施例试样的sem图(图5)进行比较,可以看出该植物纤维塑料无纤维形态且没有明显界面分层现象,说明该塑料粒子塑化效果好,这是因为甘油的添加有利于碱性增塑剂与杨木粉的熔融塑化反应。植物纤维本身并无吸收峰,没有玻璃化温度。对本实施例试样进行tg和dsc分析(图6),可以看出该植物纤维塑料的外推起始降解温度在236℃左右,最大降解温度在276℃左右,玻璃化转变温度在175℃左右,该玻
璃化温度低于初始降解温度。说明该植物纤维塑料具有热塑性。
62.由tg对比曲线图分析可知,实施例5挤出的植物纤维塑料和纯碱性增塑剂挤出的植物纤维塑料在热稳定性能方面没有过大差异,其中初始分解温度均在236℃
‑
243℃范围,玻璃化转变温度均低于初始分解温度。总的来说,纯碱性增塑剂挤出的植物纤维塑料与实施例5有着几乎相同的塑化效果,较为不同的是甘油的加入使得该条件下制备的物料有着更好的光泽感。根据tg对比曲线(图7)可以看出,相比于纯碱物料该样品加入甘油后的分解温度稍微提前。
63.对比例1一种具有生物可降解性的植物纤维塑料的制备方法,具体为:称取300g风干杨木粉待用。称取60g片状固体naoh(碱性增塑剂占杨木粉质量的20%)。将杨木粉与碱性增塑剂混合均匀待用,得到混合料。设置双螺杆挤出机ⅰ、ⅱ、ⅲ、ⅳ、
ⅴ
、
ⅵ
、
ⅶ
、
ⅷ
、
ⅸ
、
ⅹ
、xi各区段温度均为150℃。将混合料加入双螺杆挤出机,设置转速250转/分钟,挤出的物料大部分为粉末,且在挤出过程中有大量黄烟逸出,没有得到塑化的粒子。
64.该对比例证实当碱性增塑剂占植物纤维的质量比低于30%时,没有获得良好的塑化效果。挤出所得物料在热压机分别为160℃和220℃的情况下热压效果均较差。对比例1残碱和熔融指数测定
65.对比例2一种具有生物可降解性的植物纤维塑料的制备方法,具体为:称取300g风干杨木粉待用。称取90g片状固体naoh(碱性增塑剂占杨木粉质量的30%),并将naoh溶于180g水中形成碱溶液待用。将上述杨木粉与碱溶液混合均匀,得到混合料。设置双螺杆挤出机ⅰ、ⅱ、ⅲ、ⅳ、
ⅴ
、
ⅵ
、
ⅶ
、
ⅷ
、
ⅸ
、
ⅹ
、xi各区段温度均为50℃。将混合料加入双螺杆挤出机,设置转速250转/分钟,完成第一次挤出。随即将双螺杆挤出机各区段的温度升温至150℃,进行第二次挤出。在第二次挤出过程中,有大量挥发性小分子逸出产生大量黄烟,物料在挤压过程中形成暗黄粉(见图9)。该粉料在热压后无热塑性,原因是虽然该对比例中碱性增塑剂的质量虽然达到杨木粉的30%,但是体系的含水率较高(约为31%),使得碱性增塑剂的浓度被稀释,物料在升温至150℃后,水分以水蒸气的形式被蒸发,并且大量的碱性增塑剂也随着水蒸气被带出。这导致:在高温时木粉更多地受到摩擦作用而不是熔融塑化,混合料直接被磨成粉料;以及,降解产生的大量的起到增塑作用的小分子随着水蒸气汽化逸出。从以上两点得出结论:含水体系不利于通过高温高碱、高剪切熔融塑化制备植物纤维塑料。综上所述,即使在高温高碱、高剪切挤出的条件下,含水率较高的植物纤维增塑体系也不能较好地实现熔融塑化,即植物纤维的三大组分(纤维素、半纤维素以及木质素)没有与碱性增塑剂发生一系列的化学反应,更多的反应过程是植物纤维原料受到螺杆的摩擦作用而不是熔融
塑化,所以导致植物纤维直接被磨成粉料。
66.对比例3
67.一种具有生物可降解性的植物纤维塑料的制备方法,具体为:称取300g风干杨木粉待用。称取600g片状固体naoh(碱性增塑剂占杨木粉质量的200%),将naoh溶于300g水中形成碱溶液。将杨木粉与碱溶液混合均匀得到混合料。设置双螺杆挤出机ⅰ、ⅱ、ⅲ、ⅳ、
ⅴ
、
ⅵ
、
ⅶ
、
ⅷ
、
ⅸ
、
ⅹ
、xi各区段温度均为50℃。将混合料加入双螺杆挤出机,设置转速250转/分钟。即使重复五次上述挤出过程,该对比例得到的挤出物料仍然呈橡皮泥状,基本没有塑化。这说明即使在大量碱性增塑剂条件下,低温加工条件使得木粉仅发生润胀,没有与植物纤维的三大组分发生相应反应形成塑化。
68.这也证实高剪切挤压过程中,加工温度对碱性增塑剂打开纤维细胞壁有着重要的作用。植物纤维原料的主要三大组分是纤维素、半纤维素以及木质素,在在高温高碱、高剪切挤出条件下破坏植物纤维原料的细胞壁,使得三大组分木质素、半纤维素及纤维素发生酚型木质素酸碱中和反应、酯键木质素皂化反应、半纤维素的乙酰基的皂化反应、半纤维素聚木糖的己烯糖醛酸反应、纤维素剥皮反应等,以上反应大量消耗了碱性增塑剂(naoh),也使得三大组分各自的聚合度和分子量降低。而降解的木质素小分子及溶出物又再混炼时发挥着增塑剂的作用,使得三大组分的分子量降低,从而降低了植物纤维的玻璃化转变温度。整个塑化过程中,植物纤维原料在碱性增塑剂(naoh)的高温高碱、高剪切熔融塑化作用下由固态转变成黏弹态,最终制备获得黏度低、流动性好、熔融指数高的生物可降解性的植物纤维塑料。