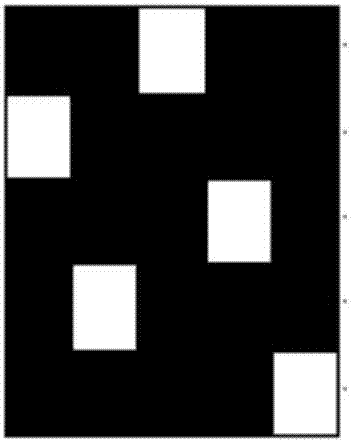
本发明属于家用纺织品面料
技术领域:
,具体涉及一种含棉和羊毛的防钻绒面料及其加工方法。
背景技术:
:羽绒被因其优良的保暖性能且对人体压迫小,而越来越受到欢迎。目前的羽绒被面料,通常具有较大的织造紧度,目的是阻止羽绒从面料中钻出,因此面料手感较硬挺,常有哗啦哗啦的响声。为了进一步提升面料的防钻绒性能,纯化纤的防钻绒面料通常会进行树脂涂层整理,全棉防钻绒面料在印染阶段会增加防钻绒整理剂,增加树脂和防钻绒整理剂会降低面料的吸湿透湿性能。影响人体睡眠质量好坏的关键因素是热湿舒适性能,如果在睡眠过程中产生的湿气和热气不能及时与外界空气交换,那么很容易产生闷热感,影响睡眠质量。羊毛纤维因其大分子链的螺旋构造和侧基的多样性,羊毛纤维具有优良的回弹性和吸湿放湿性能,如何将羊毛的优良特性应用到防羽面料,提高面料的吸湿放湿性能和良好的保型性非常重要。技术实现要素:本发明针对上述问题,提供含棉和羊毛的防钻绒面料及其加工方法,该面料具有优良的吸湿透湿性能、面料良好的回弹保型性进一步提升了面料防羽的持久性。为实现上述有益效果,本发明采用以下技术方案:一种含棉和羊毛的防钻绒面料,所述面料经纬纱均采用棉与羊毛的混纺纱,混纺纱的纱支为40s~80s,羊毛在混纺纱中所占的质量百分比为30%~50%;所述羊毛为细羊毛。优选地,所述含棉和羊毛的防钻绒面料坯布的经向盖覆紧度为50%~55%,纬向盖覆紧度为40%~45%。优选地,所述细羊毛平均直径为18~22μm。上述含棉和羊毛的防钻绒面料的加工方法,依次包括整经→浆纱→穿综穿筘→引纬织造→前处理→水洗→开幅→烘干→压光→预缩的工序;所述水洗工序是采用溢流机松式水洗。优选地,所述水洗工序的温度35~40℃,速度30~40m/min。优选地,所述水洗工序的工作液中渗透剂4~6g/l、消泡剂0.5~1g/l、纯碱2~5g/l,ph在8~9。优选地,所述烘干工序中采用滚筒烘干设备进行松式烘干,烘干温度为80~90℃。优选地,所述浆纱工序采用淀粉浆上浆。优选地,所述前处理工序中水浴温度为85~95℃。优选地,所述前处理工序中采用淀粉酶退浆。通过以上技术方案,本发明可以实现以下有益效果:本发明采用棉和羊毛纤维混纺纱,织成一定盖覆系数的面料,通过溢流水洗工艺对前处理后的面料进行水洗,该水洗工艺可以起到两个作用,一是消除织物的内应力,使织物本身充分收缩,二是使羊毛纤维发生缩绒,进一步填充织物的孔隙,从而提升面料的防钻绒性能。面料通过松式烘干将收缩后的尺寸稳固,最终面料不仅能达到防绒性要求和柔软蓬松的手感,且面料不增加防钻绒整理剂又兼具羊毛纤维优良的吸湿放湿性能和回弹性。附图说明图1是实施例1的织物组织结构图;图2是实施例2的织物组织结构图;其中,纵向的纱线表示经纱,横向的纱线表示纬纱,■表示经组织点,□表示纬组织点。具体实施方式下面通过具体实施方式对本发明作进一步详细说明。但本领域技术人员将会理解,下列实施例仅用于说明本发明,而不应视为限定本发明的范围。实施例中未注明具体技术或条件者,按照本领域内的文献所描述的技术或条件(例如参考赵涛编著的《染整工艺与原理》,中国纺织出版社,2009;沈兰萍著的《织物结构与设计》,中国纺织出版社,2005)或者按照产品说明书进行。所用试剂或仪器未注明生产厂商者,均为可以通过市购获得的常规产品。羊毛是由包覆在外部的鳞片层、组成羊毛实体的皮质层和毛干中心不透明的髓质层三部分组成,髓质层只存在于粗羊毛中,细羊毛中没有。本发明采用的均为细羊毛。羊毛在湿热条件下,经机械外力的反复作用,纤维集合体逐渐收缩紧密,并相互穿插纠缠,交编毡化,这一性能称为羊毛的缩绒性。本领域技术人员通常利用这一特性来处理羊毛衫的加工工艺称为羊毛衫缩绒。本发明利用羊毛缩绒的特性提供一种含棉和羊毛的防钻绒面料,经纬纱均混入一定比例的羊毛,通过后道松式水洗工艺,使得羊毛纤维收缩,织物变紧达到防钻绒的效果。其加工工艺流程为:整经→浆纱→穿综穿筘→引纬织造→前处理→水洗→开幅→烘干→压光→预缩而制成成品。面料采用棉和细羊毛进行混纺,细羊毛的平均直径为18~22μm,该细羊毛为带有鳞片层的羊毛,没有髓质层,该细羊毛表面的鳞片层因分布均匀、方向性一致性好,所以具有较好的缩绒性,且细羊毛的弹性好,强力高,刺痒性小,和棉纤维能够满足面料的强力要求和良好的接触感。其中细羊毛在混纺纱中所占的质量百分比为30%~50%。本发明发现在该范围内,细羊毛受到外界条件的影响,使混纺纱中的细羊毛因鳞片层发生羊毛纤维和羊毛纤维相互毡合纠缠,羊毛纤维和棉纤维相互穿插,棉纤维和棉纤维重叠交叉,且羊毛纤维较多的转移在纱线的中间,棉纤维较多地表现在纱线的表面,因此不仅具有较好的缩绒效果,且面料的刺痒感小,手感柔软。进一步地,为了达到较好的缩绒效果,保证面料良好的手感,不对面料强力造成较大损伤,面料采用溢流水洗工艺使面料产生轻微缩绒。其中水洗工艺参数为温度35~40℃,速度30~40m/min,羊毛纤维在该温度范围内具有较好的缩绒性能,且配合该车速所具有的的机械作用力比较适中,能够得到较好的缩绒效果。本发明采用棉和羊毛纤维进行混纺,在印染过程中为了能够得到较好的缩绒效果,必须控制好工作液的ph值,能够兼顾棉纤维的强力与羊毛纤维的强力,同时又可以具有较好的缩绒效果,本发明所用助剂渗透剂4~6g/l,消泡剂0.5~1g/l,纯碱2~5g/l,ph控制在8~9。面料在水洗过程中受到机械作用力,目的是一方面促使羊毛纤维的鳞片打开,羊毛纤维彼此毡合纠缠而缩绒,另一方面使织物中的内应力得到释放,最终导致面料收缩、织物紧度变大,从而提升防钻绒效果。进一步地,本发明通过设计水洗工艺起到收缩面料的密度,从而达到防钻绒目的,为此必须结合合理的坯布织造盖覆系数。本发明坯布经向盖覆紧度为50%~55%,纬向盖覆紧度为40%~45%。本发明发现在该覆盖系数范围内,羊毛棉坯布在水洗中不仅能有很好的浸润性,促使羊毛纤维的鳞片层充分打开,利于缩绒效果,而且该盖覆系数下羊毛棉坯布的拉伸回弹性能在经过水洗后发生收缩,其收缩后的织物紧密性正好能满足防钻绒要求,同时保证面料不至于缩的太多而手感发硬。所述面料在水洗后采用滚筒烘干设备进行松式烘干,烘干温度为80~90℃,该烘干方式可以进一步提升面料手感,并能将收缩后的面料尺寸固定。在加工过程中为了保护羊毛纤维的强力,所述面料采用全淀粉浆料上浆,在退浆过程中可用淀粉酶退净,避免采用烧碱退浆对羊毛纤维的强力造成损伤,且在整个印染前处理过程中水浴温度为85~95℃,目的是保护羊毛纤维的强力和手感。实施例1面料采用细羊毛纤维和棉纤维混纺织造而成,其中羊毛纤维的细度为18~22μm,混纺纱中细羊毛纤维所占的质量百分为30%。面料的组织结构为平纹,经向盖覆紧度为50%,纬向盖覆紧度为40%。在喷气织机上织造而成。面料上浆工艺采用全淀粉浆料上浆,在退浆过程中用淀粉酶退净,其印染前处理过程中水浴温度为85℃。面料通过溢流水洗工艺使面料发生收缩,其中水洗的工艺条件为渗透剂4g/l,消泡剂0.5g/l,纯碱2g/l,ph控制在8~9,温度35℃,速度30m/min。面料水洗后经开幅后,在滚筒烘干设备中进行烘干,其中烘干温度为80℃。实施例2所述面料采用羊毛纤维和棉纤维混纺织造而成,其中羊毛纤维的细度为18~22μm,混纺纱中羊毛纤维所占的质量百分为50%。面料的组织结构为五枚三飞经面缎纹组织,经向盖覆紧度为55%,纬向盖覆紧度为45%。在喷气织机上织造而成。面料上浆工艺采用全淀粉浆料上浆,在退浆过程中用淀粉酶退净,其印染前处理过程中水浴温度为95℃。面料通过溢流水洗工艺使面料发生收缩,其中水洗的工艺条件为渗透剂6g/l,消泡剂1g/l,纯碱5g/l,ph控制在8~9,温度40℃,速度40m/min。面料水洗后经开幅后,在滚筒烘干设备中进行烘干,其中烘干温度为90℃。对比例1本实施例与实施例1的区别在于:经向覆盖紧度50%纬向覆盖紧度30%。面料采用细羊毛纤维和棉纤维混纺织造而成,其中羊毛纤维的细度为18~22μm,混纺纱中细羊毛纤维所占的质量百分为30%。面料的组织结构为平纹,经向盖覆紧度为50%,纬向盖覆紧度为30%。在喷气织机上织造而成。面料上浆工艺采用全淀粉浆料上浆,在退浆过程中用淀粉酶退净,其印染前处理过程中水浴温度为85℃。面料通过溢流水洗工艺使面料发生收缩,其中水洗的工艺条件为渗透剂4g/l,消泡剂0.5g/l,纯碱2g/l,ph控制在8~9,温度35℃,速度30m/min。面料水洗后经开幅后,在滚筒烘干设备中进行烘干,其中烘干温度为80℃。对比例2本实施例与实施例1的区别在于:经向覆盖紧度40%纬向覆盖紧度40%。面料采用细羊毛纤维和棉纤维混纺织造而成,其中羊毛纤维的细度为18~22μm,混纺纱中细羊毛纤维所占的质量百分为30%。面料的组织结构为平纹,经向盖覆紧度为40%,纬向盖覆紧度为40%。在喷气织机上织造而成。面料上浆工艺采用全淀粉浆料上浆,在退浆过程中用淀粉酶退净,其印染前处理过程中水浴温度为85℃。面料通过溢流水洗工艺使面料发生收缩,其中水洗的工艺条件为渗透剂4g/l,消泡剂0.5g/l,纯碱2g/l,ph控制在8~9,温度35℃,速度30m/min。面料水洗后经开幅后,在滚筒烘干设备中进行烘干,其中烘干温度为80℃。对比例3本实施例与实施例1的区别在于:经向覆盖紧度50%纬向覆盖紧度50%。面料采用细羊毛纤维和棉纤维混纺织造而成,其中羊毛纤维的细度为18~22μm,混纺纱中细羊毛纤维所占的质量百分为30%。面料的组织结构为平纹,经向盖覆紧度为50%,纬向盖覆紧度为50%。在喷气织机上织造而成。面料上浆工艺采用全淀粉浆料上浆,在退浆过程中用淀粉酶退净,其印染前处理过程中水浴温度为85℃。面料通过溢流水洗工艺使面料发生收缩,其中水洗的工艺条件为渗透剂4g/l,消泡剂0.5g/l,纯碱2g/l,ph控制在8~9,温度35℃,速度30m/min。面料水洗后经开幅后,在滚筒烘干设备中进行烘干,其中烘干温度为80℃。对比例4本实施例与实施例1的区别在于:经向覆盖紧度60%纬向覆盖紧度40%。面料采用细羊毛纤维和棉纤维混纺织造而成,其中羊毛纤维的细度为18~22μm,混纺纱中细羊毛纤维所占的质量百分为30%。面料的组织结构为平纹,经向盖覆紧度为50%,纬向盖覆紧度为30%。在喷气织机上织造而成。面料上浆工艺采用全淀粉浆料上浆,在退浆过程中用淀粉酶退净,其印染前处理过程中水浴温度为85℃。面料通过溢流水洗工艺使面料发生收缩,其中水洗的工艺条件为渗透剂4g/l,消泡剂0.5g/l,纯碱2g/l,ph控制在8~9,温度35℃,速度30m/min。面料水洗后经开幅后,在滚筒烘干设备中进行烘干,其中烘干温度为80℃。将实施例1与对比例1至4进行性能测试,其中钻绒根数参照gb/t12705.2-2009织物防钻绒试验方法进行。结果如下:实施例1对比例1对比例2对比例3对比例4钻绒根数/根8172378手感柔软松软松软较硬挺较硬挺由以上结果可知,本发明的面料具有良好的防钻绒效果和柔软蓬松的手感。当前第1页12