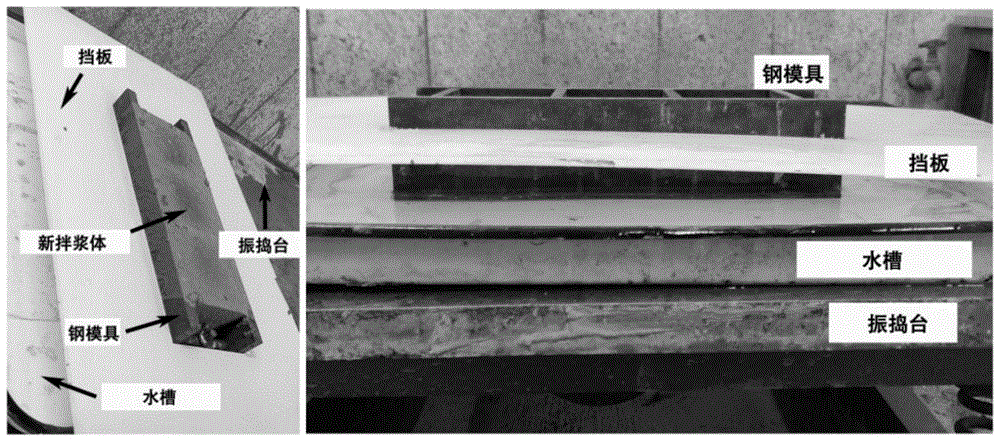
本发明属于建筑材料
技术领域:
,具体涉及一种通过冷水浴振捣成型法制备高强度改性硫磺混凝土的工艺。
背景技术:
:硫磺混凝土是一种以硫磺、矿物填料、骨料混合而成的新型可持续性建筑材料,也称硫磺混凝土。区别于传统的硅酸盐混凝土,硫磺作为粘结剂,既不是水硬性也不是气硬性材料,硬化原理是硫磺的冷却结晶,属于物理变化。因此,硬化过程极快,在常温下冷却数分钟即可硬化成型,数小时后即可接近基体的最终强度,是极佳的早强型材料。硫磺混凝土具有较高的抗压强度,改性纯硫磺的抗压强度更是高达30mpa,抗折强度有3.5mpa,而掺入填料、骨料制备成混凝土后,抗压强度可达87.2mpa。除了较好的力学性能外,硫磺混凝土还具有极高的抗渗性,抗酸、盐腐蚀性,在环境恶劣的工程内有极好的应用前景。另外,基于硫磺的物理性质,高温可让硬化后的硫磺混凝土恢复可塑性,是可持续性的体现。虽然硫磺混凝土具有优异的力学性能和耐久性,但其制备过程复杂,且具有一定的危险性。传统的制备工艺需要油浴保温搅拌,并且制备过程中改性剂有一定的毒性,会对人体造成伤害,这也是目前国内对这种材料研究不多的原因。同时,硫磺冷却时发生的体积收缩是目前较为严重的问题,通过传统工艺制备得到的试样力学性能离散型大,基体孔洞多。因此,要更好地研究与发展这种新型材料,则必须对现有制备工艺进行改进,以提高其力学性能,使其力学性能稳当且优异。技术实现要素:为了克服上述现有技术的不足,本发明提出了一种通过冷水浴振捣成型法制备高强度改性硫磺混凝土的工艺,使用该工艺可以大幅减小硫磺收缩形成的孔洞,得到密实程度高,力学性能优异且稳定的改性硫磺混凝土。为了实现上述目的,本发明所采用的技术方案是:本发明提供了一种通过冷水浴振捣成型法制备高强度改性硫磺混凝土的工艺,所述改性硫磺混凝土包括以下质量百分比的成分:改性硫磺11.5%-14.2%、填料11.5%-14.2%、普通河砂22%-30%、骨料混合物42.6%-51.0%;所述改性硫磺包括97%的硫磺和3%的双环戊二烯,所述填料包括但不限于水泥、矿渣、粉煤灰,所述骨料混合物包括粒径为5mm-9mm的花岗岩碎石与粒径为10mm-15mm的花岗岩碎石,所述粒径为5mm-9mm的花岗岩碎石与粒径为10mm-15mm的花岗岩碎石的质量比为3:1;所述改性硫磺混凝土的制备工艺包括以下步骤:s1、物料的预处理:s11、将河砂与填料预先干拌1-2分钟得到河砂-填料混合物;s12、将硫磺、河砂-填料混合物、骨料混合物置于135-145℃下预热1-2小时;s13、往预热融化后的硫磺中加入双环戊二烯,经反应后得到改性硫磺;s14、往改性硫磺中相继倒入河砂-填料混合物和骨料混合物,得到硫磺混凝土预混物;s15、将搅拌好的硫磺混凝土预混物放回135-145℃下保温10分钟,将混凝土的温度提高到135-145℃,得到待成型硫磺混凝土;s2、通过冷水浴振捣成型法装模成型:所述冷水浴振捣成型法需用到震动装置、水槽、开口挡板和模具,所述开口挡板的面积大于水槽的面积,所述开口挡板的中间开有符合模具大小的孔洞;s21、在震动装置的震动状态下快速地将步骤s15的待成型硫磺混凝土浇入模具内,装模同时振捣30-60s;s22、初振捣密实后,抹平混凝土表面,并将模具置于水槽内,注入高度为模具1/5-1/4的水;s23、将挡板套于模具边缘,将水槽多余表面完全遮挡;s24、开启震动装置,并固定挡板防止移位,待硫磺混凝土上表面的颜色由深绿转浅绿后关闭震动装置,取出模具静置1-2小时,拆模即得改性硫磺混凝土。优选地,所述改性硫磺混凝土包括以下质量百分比的成分:改性硫磺13.3%、水泥13.3%、普通河砂24.9%、粒径为5mm-9mm的花岗岩碎石36.4%,粒径为10mm-15mm的花岗岩碎石12.1%;所述改性硫磺包括97%的硫磺和3%的改性剂双环戊二烯。优选地,步骤s12中,预热的温度为140℃,时间为1小时。优选地,步骤s13中,反应的温度为135-145℃,时间为2-3小时。进一步地,反应的温度为140℃,时间为2小时。优选地,所述水槽和模具在使用前,与硫磺、河砂-填料混合物、骨料混合物一起进行步骤s12中的预热处理。优选地,步骤s14中,先将河砂-填料混合物分两次加入改性硫磺中,每次搅拌30秒,然后将骨料混合物同样分2次加入,每次搅拌30秒,最后得到硫磺混凝土预混物。优选地,所述震动装置包括但不限于震动台、震动棒。进一步地,所述震动装置为震动台。与现有技术相比,本发明的有益效果是:针对现有的硫磺混凝土制备过程复杂,且制备得到的试样力学性能离散型大,基体孔洞多,力学性能不够稳定、优异等不足,本发明提供了一种改性硫磺混凝土的冷水浴振捣成型工艺,该工艺主要应用于硫磺混凝土的装模成型阶段,能够较大程度地提高硫磺基体的密实度,即避免硫磺基体冷却收缩形成的孔洞对强度造成的不良影响,并且操作简便,装置制作简单;经测试发现,采用本发明方法制备的改性硫磺混凝土的抗压强度最低达77mpa,试块内部孔洞极少,密实程度高,试块之间的强度离散性低,抗压强度稳定。同时,还发明还优化了装模成型阶段前硫磺混凝土预混料的最佳配比,应用于该最佳混凝土配比结合冷水浴振捣成型工艺制备出来的改性硫磺混凝土的抗压强度平均达87mpa,部分试块抗压强度超90mpa。详细而言,本发明具有以下优点:(1)本发明的冷水浴振捣成型工艺所使用的装置简单,普通的铁制水槽以及混凝土震动装置即可胜任;(2)采用本发明的冷水浴振捣成型工艺制备得到的改性硫磺混凝土的内部孔洞少,基体密实程度高;(3)采用本发明的冷水浴振捣成型工艺制备得到的改性硫磺混凝土,抗压强度最低达到77mpa,并且试块之间的强度离散性低,抗压强度比使用普通成型方法的试样稳定;(4)采用本发明的高强度硫磺混凝土配合比,能制备得到抗压强度达87mpa的试样,并有部分试块抗压强度超90mpa,;(4)本发明所述的硫磺混凝土硬化速度相较于传统工艺更快,数分钟内已初步硬化成型,可拆模;在数小时内即可达到最终强度的80%,并且不需要标准的养护条件,对于工程抢险有较大意义;(5)采用本发明的冷水浴振捣成型工艺制备得到的改性硫磺混凝土,具有较好的抗渗透性,抗酸、盐腐蚀性,适用于海洋工程、化工建筑、城市管道修补等。并且具有较好的抗冻性,可在低温环境下施工,制备过程与养护皆不需水的参与,是干旱缺水地区的极佳替代方案。(6)采用本发明的冷水浴振捣成型工艺制备得到的改性硫磺混凝土,是绿色可持续材料,主材料硫磺粉末是大部分工业的副产物,来源丰富,骨料可使用人工砂以及再生骨料,对性能影响极小,硫磺混凝土在硬化成型后,置于一定温度下可恢复可塑性,具有良好的可持续利用性。(7)本发明所述的硫磺混凝土是目前最有机会成为太空建筑材料的新型符合材料,具有极高的火星环境适应性,并且基于火星就地取材制备硫磺混凝土相对简单。(8)本发明所述的硫磺混凝土除上述优点外,具有普通硅酸盐水泥混凝土的特性。附图说明图1为改性硫磺混凝土冷水浴振捣成型工艺的实操图;图2为普通成型方法(a)和冷水浴振捣成型方法(b)制备的改性硫磺混凝土试样;图3为改性硫磺混凝土的可持续利用性测试过程。具体实施方式下面对本发明的具体实施方式作进一步说明。在此需要说明的是,对于这些实施方式的说明用于帮助理解本发明,但并不构成对本发明的限定。此外,下面所描述的本发明各个实施方式中所涉及的技术特征只要彼此之间未构成冲突就可以相互组合。下述实施例中的实验方法,如无特殊说明,均为常规方法,下述实施例中所用的试验材料,如无特殊说明,均为可通过常规的商业途径购买得到的。实施例1高强度改性硫磺混凝土冷水浴振捣成型工艺的建立及优化一、改性硫磺混凝土冷水浴振捣成型工艺的建立改性硫磺混凝土包括以下质量百分比的成分:改性硫磺11.5%-14.2%、填料(p.o.42.5水泥、矿渣、粉煤灰等矿物填料)11.5%-14.2%、普通河砂22%-30%、骨料混合物【粒径为5mm-9mm的花岗岩碎石与粒径为10mm-15mm的花岗岩碎石=3:1(质量比)】42.6%-51.0%;所述改性硫磺包括97%的硫磺和3%的改性剂双环戊二烯。具体制备步骤如下:1、物料的预处理1.1、按照上述配比称取对应量的填料、河砂、骨料混合物(粒径为5mm-9mm的花岗岩碎石与粒径为10mm-15mm的花岗岩碎石)、硫磺和改性剂双环戊二烯;1.2、将河砂与填料预先干拌1分钟得到河砂-填料混合物;1.3、将硫磺、河砂-填料混合物、骨料混合物以及用于盛装物料的小型金属圆筒(直径15cm-20cm,高至少为20cm)和7.07cm×7.07cm×7.07cm的三联钢制模具(即一个模具是3个7.07×7.07的试样,模具的长边加上厚度,大约接近23cm)一同置于140℃的恒温干燥箱中预热一小时,防止温度过低,使新拌硫磺混凝土浆体倒入时边缘瞬间硬化;1.4、往融化后的硫磺中加入双环戊二烯改性剂(常温下为胶状固体),并用细铁棒搅拌均匀,置于140℃的恒温干燥箱中反应2小时,得到改性硫磺(该步骤及后面步骤需做好保护措施,双环戊二烯预热易挥发并有一定毒性);1.5、将改性硫磺倒入已预热的小型金属圆筒容器内,将预热的河砂-填料混合物分两次加入,各搅拌(400r/min)30秒,共1分钟;然后将混合的骨料同样分2次加入,各搅拌(400r/min)30秒,共1分钟,得到新拌硫磺混凝土浆体。1.6、将搅拌好的硫磺混凝土预混物放回140℃的保温箱中,保温20分钟,保证新拌浆体的温度在装模时保持在140℃左右(因为搅拌的过程中浆体的温度会有所下降,不控制温度会使浆体在浇筑前便开始硬化,难以装模),得到待成型硫磺混凝土(即新拌硫磺混凝土或新拌浆体)。2、通过冷水浴振捣成型法装模成型冷水浴振捣成型法需用到混凝土震动台(河北华汇阀门有限公司,型号为hzj-0.5)、坚固水槽(尺寸为80cm×40cm×4cm)、矩形开口挡板(尺寸为90cm×45cm,材质可选用钢板或者亚克力板),能完全覆盖水槽,挡板内部的开口尺寸约为23cm×7.5cm,略大于模具。如图1所示,具体操作步骤如下:2.1、将预热的钢制模具(1.2步骤)置于震动台上,开启震动台(振动频率为2860次/分),并快速地将待成型硫磺混凝土浇入钢制模具内,然后振捣30秒;2.2、初振捣密实后,用预热后的铁质抹子抹平混凝土表面,快速将水槽置于震动台上,并将模具置于水槽内,注入高度为模具1/5-1/4的自来水;2.3、将挡板套于模具边缘,将水槽多余表面完全遮挡;因为开启震动台后,水槽内的水花极易飞溅于新拌硫磺浆体的上表面,使得上面的硫磺瞬间硬化,所以要加一个挡板,将水槽完全遮挡,这样就能有效防止水花飞溅在新拌浆体的上表面。2.4、开启震动台,人为固定挡板防止移位。2.5、待硫磺混凝土上表面硬化后,标志为颜色由深绿转浅绿,关闭震动台,取出模具置于自然环境下静置1小时,拆模,得到改性硫磺混凝土块体。二、改性硫磺混凝土冷水浴振捣成型工艺的优化1、传统成型工艺与冷水浴振捣成型工艺对改性硫磺混凝土力学性能的影响按照表1和表2所示的成分配比和用量(各成分的质量百分比及相应的用量),按照冷水浴振捣成型工艺(“一、改性硫磺混凝土冷水浴振捣成型工艺的建立”中的方法)制备3块70.7mm×70.7mm×70.7mm的立方体试块(分别记为t1、t2、t3);同时用传统成型工艺(即普通冷却成型法:直接将新拌硫磺混凝土浇筑于预热的钢模后,在振捣台上振捣1分钟,随即置于常温下固化即可)也制备3块70.7mm×70.7mm×70.7mm的立方体试块(同样记为t1、t2、t3),在自然环境下冷却3天后,使用微机液压试验机测试其抗压强度。表格中改性硫磺为97%纯硫磺粉末及3%双环戊二烯改性剂反应后所得,碎石1为粒径5-9mm的花岗岩碎石,碎石2为粒径10-15mm的花岗岩碎石,填料使用粉煤灰。由表3的实验结果可知,采用冷水浴振捣成型法制备得到的试块强度最高有81.4mpa,最低75.7mpa,同组之间相差最大有9.8mpa(t1),而普通冷却成型法得到的试块最高60.4mpa,最低41.0mpa,同组之间相差最大有13.8mpa。可见,冷水浴振捣成型法不仅试块抗压强度的有明显的提高,并且各组内的试块之间强度差距有缩小,即强度的离散程度有所下降,力学性能更加稳定。图2为分别使用传统成型方法以及冷水浴振捣成型方法制备的硫磺混凝土试样实体图,观察发现,使用传统方法制备的试样表面具有多个不规则的孔洞,极大的降低了试样的力学性能。而使用本发明所述的冷水浴振捣成型方法制备的试样,表面均匀、平整,几乎没有孔洞的存在,说明了这种成型方法能够有效得提高基体的密实度,减少硫收缩孔的数量和体积。表1改性硫磺混凝土的配比单位:wt%编号改性硫磺粉煤灰河砂碎石1碎石2t113.912.724.936.412.1t213.313.324.936.412.1t312.713.924.936.412.1表2改性硫磺混凝土各成分的用量(对应表1的配比)单位:kg/m3表3改性硫磺混凝土试块的抗压强度单位:mpa同时,以t1组中采用冷水浴振捣成型法制备的改性硫磺混凝土试块为例,测试改性硫磺混凝土的可持续利用特性。具体方法为(如图3所示):将t1组中经过力学性能测试的3块改性硫磺混凝土试样使用铁锤粗略地破碎,然后放入铁制圆筒中,置于140℃的恒温干燥箱内加热120分钟,并将加热后的硫磺混凝土浆体重新浇筑于模具中,使用冷水浴振捣成型方法重新浇筑成型,测试成型后试样的抗压强度,考察硫磺混凝土是否重新获得可塑性。如表4所示,改性硫磺混凝土在重新加热后,即回到了成型前的状态,具有良好的可塑性,这是水泥混凝土所没有的特点。该试样使用冷水浴振捣工艺初次成型后的抗压强度为75.7mpa(见表3),而使用冷水浴振捣工艺再次成型后所测得的抗压强度为64.5mpa,虽然强度比起初次成型下降了14.8%,但仍具有较好的抗压性能,同时也较好地证实了本发明的改性硫磺混凝土具有良好的可持续利用性。表4t1组的改性硫磺混凝土试样再次成型后的抗压强度单位:mpa2、矿物填料种类以及填料掺量对改性硫磺混凝土力学性能的影响根据表5-10所示的成分配比和用量(各成分的质量百分比及相应的用量),按照冷水浴振捣成型工艺(“一、改性硫磺混凝土冷水浴振捣成型工艺的建立”中的方法)制备70.7mm×70.7mm×70.7mm大小的试块各三块,然后通过微机液压试验测试力学性能,计算平均值。所选用的三种填料为目前使用广泛,易于获取的粉煤灰、水泥(p.o.42.5水泥)、矿渣,各种填料设置3组,碎石1为粒径5-9mm的花岗岩碎石,碎石2为粒径10-15mm的花岗岩碎石,各组的改姓硫磺与填料的比值不同,其余组分材料不变。如表11所示的抗压强度测试结果,掺水泥填料的改性硫磺混凝土的强度最高,为86.9mpa,掺入水泥作为填料整体强度比粉煤灰与矿渣要高,并且改性硫磺与填料的质量比为1:1,即水泥的掺量为13.3%时,改性硫磺混凝土的力学性能最佳。表5掺粉煤灰的改性硫磺混凝土的配比单位:wt%表6掺粉煤灰的改性硫磺混凝土各成分的用量(对应表5的配比)单位:kg/m3表7掺水泥的改性硫磺混凝土的配比单位:wt%表8掺水泥的改性硫磺混凝土各成分的用量(对应表7的配比)单位:kg/m3表9掺矿渣的改性硫磺混凝土的配比单位:wt%表10掺矿渣的改性硫磺混凝土各成分的用量(对应表9的配比)单位:kg/m3表11掺不同填料的改性硫磺混凝土的抗压强度单位:mpa3、骨料掺量对改性硫磺混凝土力学性能的影响根据表12-15所示的成分配比和用量(各成分的质量百分比及相应的用量),按照冷水浴振捣成型工艺(“一、改性硫磺混凝土冷水浴振捣成型工艺的建立”中的方法)制备70.7mm×70.7mm×70.7mm各三块,然后通过微机液压试验测试力学性能,计算平均值。选用的填料为水泥(p.o.42.5水泥),各组改性硫磺与水泥的比值不变,碎石包括粒径5-9mm的花岗岩碎石和粒径10-15mm的花岗岩碎石(质量比3:1)。a组为保持砂率相同而改变骨料总含量,b组为保持骨料总含量相等而改变砂率(骨料总量为河砂质量+碎石质量,而砂率为河砂质量与骨料总质量的比值)。如表16所示的抗压强度测试结果,骨料总量方面,随着骨料总量的增长,改性硫磺混凝土的抗压强度先增后减,峰值为a2,骨料总量为73.4%,抗压强度为85.6mpa。砂率方面,随着砂率的提高,改性硫磺混凝土的抗压强度先增后减,峰值为b2,砂率为0.34,抗压强度为84.6mpa。由此可得当骨料总量为73.4%,砂率为0.34时有最高的抗压强度。表12不同骨料含量的改性硫磺混凝土的配比单位:wt%编号改性硫磺水泥河砂碎石骨料总量a114.114.125.346.571.8a213.313.325.847.673.4a312.512.526.348.775.0a411.711.726.849.876.6表13不同骨料含量的改性硫磺混凝土各成分的用量(对应表12的配比)单位:kg/m3表14不同砂率的改性硫磺混凝土的配比单位:wt%编号改性硫磺水泥砂碎石砂率b113.313.322.051.40.30b213.313.324.948.50.34b313.313.327.845.60.38b413.313.330.742.70.42表15不同砂率的改性硫磺混凝土各成分的用量(对应表14的配比)单位:kg/m3编号改性硫磺水泥砂碎石砂率b1410.3410.3678.71585.70.30b2410.3410.3768.21496.20.34b3410.3410.3857.61406.70.38b4410.3410.3947.11317.30.42表16不同骨料含量和砂率的改性硫磺混凝土的抗压强度单位:mpa抗压强度抗压强度a178.2b180.5a285.6b287.2a381.2b385.1a464.8b484.3综上所述,采用本发明的冷水浴振捣成型工艺制备改性硫磺混凝土时,最佳的组分及配比关系为:改性硫磺13.3%、p.o.42.5水泥13.3%、普通河砂24.9%、碎石73.4%(粒径为5mm-9mm的花岗岩碎石36.4%,粒径为10mm-15mm的花岗岩碎石12.1%);所述改性硫磺包括97%的硫磺和3%的改性剂双环戊二烯。采用该最佳组分及配比,按照冷水浴振捣成型工艺(“一、改性硫磺混凝土冷水浴振捣成型工艺的建立”中的方法)制备的改性硫磺混凝土试块,使用微机液压试验机测得其抗压强度达87.2mpa,抗压强度优异,内部孔洞少,基体密实程度高,同时具有良好的可持续利用性。以上对本发明的实施方式作了详细说明,但本发明不限于所描述的实施方式。对于本领域的技术人员而言,在不脱离本发明原理和精神的情况下,对这些实施方式进行多种变化、修改、替换和变型,仍落入本发明的保护范围内。当前第1页12