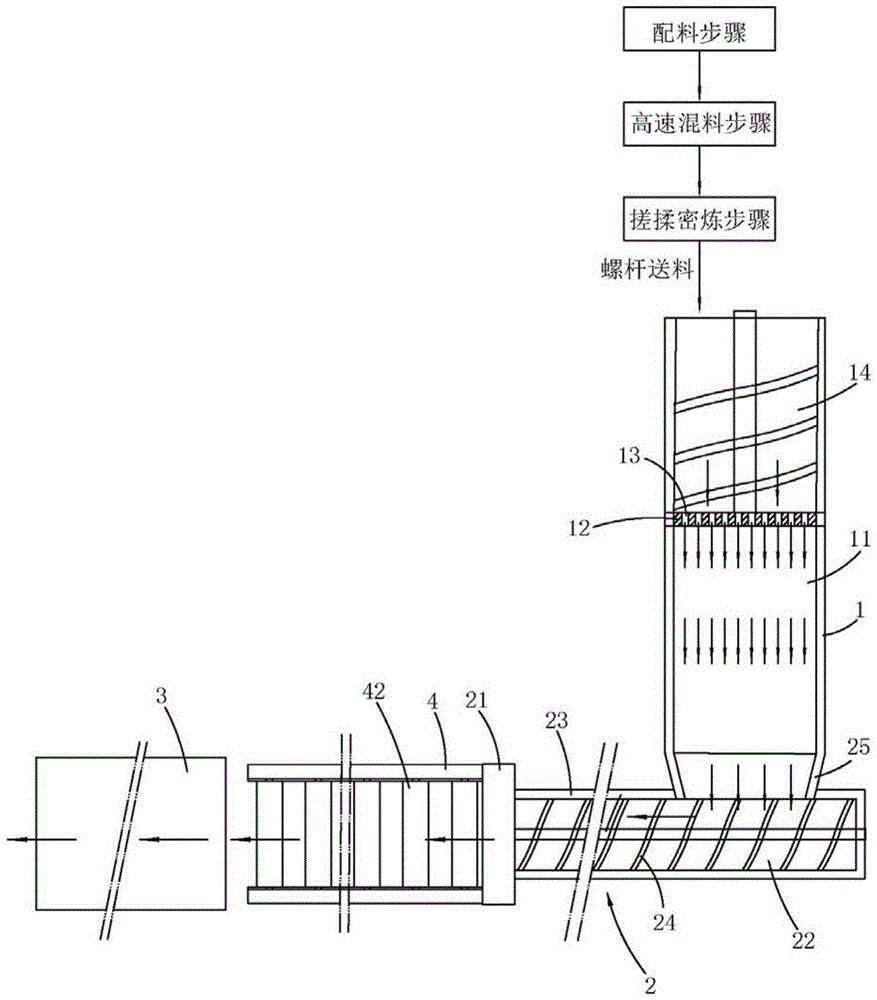
本发明涉及水泥复合板的生产方法
技术领域:
,尤其是涉及水泥复合板的生产方法和多层复合水泥板材的生产方法。
背景技术:
:目前,在水泥复合板的生产过程中,先将用于生产水泥复合板的各组份混合搅拌,得到浆状原料,再将其倒入模具成型,成型过程一般是一层浆状原料一层玻纤布,或者至少在底层和面层加入玻纤布,最终固化得到水泥复合板,在水泥复合板的生产过程中,是采用一模一板的逐片倒模成型的生产方法,水泥复合板不是连续生产的,每一个水泥复合板达到最佳固化强度的时间通常都需要15天,且水泥复合板的固化时间较长,生产各种尺寸规格的水泥复合板所需的成型模具多,这导致水泥复合板的生产效率极低,生产成本较高,另外,成型得到的水泥复合板的厚度厚度误差较大,厚度尺寸不稳定,不同批次生产的水泥复合板的结构强度和抗弯曲性能等性能的差异性也较大,成型固化后得到的水泥复合板还需要经过长时间的养护处理,以去除水泥复合板的内应力,然后还需要各种机械加工,以实现将水泥板的厚度控制在允许的厚度偏范围内,后续工艺步骤较多,加工过程的损耗也非常大,加过过程产生大量粉尘污染,因此有必要予以改进。技术实现要素:针对现有技术存在的不足,本发明的目的是提供水泥复合板的生产方法,连续生产水泥复合板,工艺简单,生产效率高,生产成本低。为了实现上述目的,本发明所采用的技术方案是:水泥复合板的生产方法,包括以下步骤,配料步骤,按重量百分比进行配置原料,包括水泥粉30-40%、木纤维10-20%、木质素5-10%、木质纤维素2-5%、滑石粉5-10%、黄原胶2-5%和减水剂0.5-5%和水10-15%;高速混料步骤,先将水泥粉、木纤维、木质素、木质纤维素、滑石粉、黄原胶和减水剂投入至高速混料机的高速搅拌室,然后开始搅拌,通过至少一喷头将水转变成水雾并喷入高速搅拌室内,在1-5分钟内将重量百分比为10-15%的水雾至高速搅拌室内,其中,水泥粉产生水化合反应而呈泥状,使高速混料机内的原料转变成泥状或小团状的凝胶体,凝胶体包括黄原胶形成的凝胶物以及均匀分布并包裹于凝胶物中的木纤维、木质素、木质纤维素、减水剂和滑石粉;搓揉密炼步骤,将凝胶体输送至搓揉设备,通过至少一搓揉设备的搓揉杆搓揉和密炼凝胶体,直至将凝胶体搓揉形成多个团状的具有塑性及黏性的团状体原料;真空除湿步骤,将团状体原料输送至真空处理室,通过真空处理室进行真空处理并抽离团状体原料中的气体和水分,从真空处理室排出后进而得到挤出成型用原料;挤出固化步骤,将挤出成型用原料输送至螺杆挤出成型机构,在常温下连续挤出成型,通过螺杆挤出成型机构的挤出模头连续挤出形状为片状的水泥板胚板,黄原胶使挤出得到的水泥板胚板经挤出成型即初步固化并基本定型,挤出得到的水泥板胚板的表面硬度达到邵氏硬度25-30度;定厚处理步骤,通过至少一定厚辊压设备对水泥板胚板进行定厚处理,得到具有设定厚度的水泥板材,水泥板材的表面硬度达到邵氏硬度35-40度;养护处理步骤,对水泥板材进行养护处理;成品步骤,经过养护处理步骤后得到成品水泥复合板,成品水泥复合板的表面硬度控制在80hv以上、抗弯曲强度达到20mpa以上。进一步的,所述搓揉密炼步骤,所述搓揉设备包括高速搓揉设备和低速搓揉设备,先将凝胶体输送至高速搓揉设备进行高速搓揉密炼,经过高速搓揉密炼再输送至低速搓揉设备进行低速搓揉密炼,低速搓揉设备的搓揉杆的转速低于高速搓揉设备的搓揉杆的转速;在搓揉密炼步骤中先通过高速搓揉设备先将凝胶体搓揉至凝胶体初步起团的状态,后通过低速搓揉设备继续搓揉,直至在低速搓揉设备的搓揉密炼室形成多个团状的具有塑性及黏性的所述团状体原料,通过低速搓揉设备连续输出团状体原料至所述真空处理室,以实现连续输出所述团状体原料;所述定厚处理步骤中,所述定厚辊压设备选用定厚带压送机构、定厚压辊组和压片式循环履带中的至少一种;通过定厚带压送机构对水泥板胚板进行定厚处理方法是通过安装在在定厚机架的循环输送带向前压送水泥板胚板,并在输送过程中通过循环输送带挤压滚压水泥板胚板;通过定厚压辊组对水泥板胚板进行定厚处理的方法是通过安装在定厚机架的多个定厚压辊组向前压送水泥板胚板,并在输送过程中通过定厚压辊组滚压水泥板胚板;通过压片式循环履带对水泥板胚板进行定厚处理的方法是通过安装在定厚机架的至少一压片式循环履带向前压送水泥板胚板,在输送过程中通过压片式循环履带挤压水泥板胚板;通过定厚压辊组的滚压或压片式循环履带的挤压以实现缩小水泥板胚板的厚度,在定厚处理步骤中将水泥板胚板的厚度控制在设定的误差范围内,同时实现挤压排水和加速固化定型速度,使得到的水泥板材的厚度等于或接近成品水泥复合板的厚度。进一步的,所述搓揉密炼步骤中,所述搓揉设备的下方分别安装有一搓揉输出机构,搓揉输出机构包括搓揉出料筒和安装在搓揉出料筒内的搓揉出料螺杆,搓揉出料筒的上侧设置有一连通搓揉设备所述搓揉密炼室的搓揉进料口、另一侧设置有搓揉出料口;所述高速搓揉设备固定在所述低速搓揉设备的上侧,固定在高速搓揉设备的下方的搓揉输出机构的搓揉出料口延伸至低速搓揉设备的搓揉密炼室的上方,凝胶体经过高速搓揉密炼处理后连续输送至低速搓揉设备进行低速搓揉密炼处理;高速搓揉设备的搓揉杆的转速为300-600转/分钟,低速搓揉设备的搓揉杆的转速为30-250转/分钟;所述定厚处理步骤中,通过定厚带压送机构进行定厚处理的,在所述定厚机架安装有上下两个所述循环输送带,两个循环输送带之间形成一前后贯穿的带体压送通道,通过安装在带体压送通道的上下两侧的压辊或压板抵顶位于带体压送通道的上下两侧循环输送带,使所述水泥板胚板通过带体压送通道,通过带体压送通道的上下两侧循环输送带挤压水泥板胚板;通过定厚压辊组进行定厚处理的,使水泥板胚板顺次通过多个定厚压辊组,一个定厚压辊组包括安装在定厚机架的两个上下间隔设置、竖直对齐且旋转方向相反的压辊,使水泥板胚板顺次通过各定厚压辊组的上下两个压辊同步滚压水泥板胚板的上下两面,沿水泥板胚板的前进方向各定厚压辊组的上下两个压辊之间的压板间距逐逐渐变小,对水泥板胚板进行分级逐步压缩,最终使水泥板胚板完全定型;通过压片式循环履带进行定厚处理的,在定厚机架的第一侧安装所述压片式循环履带、中部设置有一前后贯穿的压板通道、第二侧安装有压辊、循环输送带或压片式循环履带中的一种,通过压板通道向前输送和挤压水泥板胚板,其中,压片式循环履带是由多个压片顺次连接而成,压片的宽度大于水泥板胚板的宽度,压片的长度设置在3-20cm,压片式循环履带抵压水泥板胚板的一侧设定为压板侧,压板侧的内侧抵压水泥板胚板、外侧设置有至少一个压带辊;将经过定厚处理后得到的水泥板材的厚度误差控制在0.5%以下;至少通过安装在定厚机架的左右两侧的定宽板限制水泥板胚板的宽度。进一步的,在定厚机架安装有上下两组压片式循环履带,上下两组压片式循环履带之间设置有一压板通道,压片选用金属片,压片式循环履带为多个金属片顺次连接而成的循环输送带,在上下两个组压片式循环履带的压板侧的外侧分别间隔设置多个压带辊,上下两个组压片式循环履带的对应位置的压带辊竖直对齐,将水泥板胚板送入压板通道,通过上下两组压片式循环履带同时挤压水泥板胚板并向前输送水泥板胚。进一步的,所述真空除湿步骤中,通过密封安装在所述真空处理室的上方的送料挤料室朝向真空处理室连续挤入所述团状体原料;使团状体原料向下通过设置在送料挤料室或真空处理室的开设有多个挤料孔的分料挤料网板,分别从各挤料孔连续向下挤出得到多个条状料,使包含在团状体原料中的气体和水分释放至真空处理室中,通过分料挤料网板以及挤满各挤料孔的条状料密封隔开送料挤料室和真空处理室;使条状料向下穿过真空处理室,通过真空处理室抽除气体和水分;所述挤出固化步骤中,将螺杆挤出成型机构的挤出进料室密封安装在真空处理室的下方,使穿过真空处理室后的各条状料分别向下落入挤出进料室中,在挤出进料室中得到所述挤出成型用原料;在螺杆挤出成型机构的中部设置有挤出机筒,旋转安装在挤出机筒中的挤出成型推送螺杆的后侧延伸至挤出进料室中、前侧邻近安装在螺杆挤出成型机构的前侧的挤出模头,通过伸入至挤出进料室的挤出成型推送螺杆将连续落入至挤出进料室中的挤出成型用原料推出挤出进料室并送入挤出机筒中,挤出成型推送螺杆连续推送进料室中的挤出成型用原料;在常温下通过挤出成型推送螺杆的挤送作用和混合作用使进入挤出机筒内的挤出成型用原料混合成团,最后通过挤出模头连续挤出并得到所述水泥板胚板;其中,挤出机筒内的温度和挤出模头的挤出温度均控制在20-30℃;在定厚处理步骤之后增加一表干步骤,表干步骤,向前输送水泥板材并使水泥板材通过隧道式烘箱,通过隧道式烘箱对水泥板材进行表面烘干处理,得到完成固化的水泥板材,经表干后的水泥板材的含水率控制在15%以下、表面硬度达到邵氏硬度65-70度、抗弯曲强度达到15-18mpa。进一步的,在所述螺杆挤出成型机构的后侧安装有进料斗,进料斗的内腔设置成所述挤出进料室,在进料斗的上方密封安装有一真空处理装置,真空处理装置的内腔设置成所述真空处理室,在真空处理装置的上方密封安装有挤料装置,挤料装置的内腔设置成所述送料挤料室,送料挤料室、真空处理室和挤出进料室竖直对齐,真空处理室的上部连通送料挤料室的下部,真空处理室的下部连通挤出进料室;组装成一体的挤料装置、真空处理装置和螺杆挤出成型机构形成一除湿挤出复合设备,用于顺序实现所述真空除湿步骤和所述挤出固化步骤并实现连续生产;将所述团状体原料输送至挤料装置,通过设置在送料挤料室内的挤料器将送料挤料室内的团状体原料向下挤送;通过挤料器的挤送使团状体原料通过分料挤料网板的各挤料孔并分别向下挤出成型并进入真空处理室,通过堆挤在分料挤料网板的上方的团状体原料和挤压塞满各挤料孔的条状料在分料挤料网板处密封真空处理室的上部,通过真空处理室的负压环境辅助向下吸落各条状料;通过分料挤料网板将团状体原料挤压变成多个长度连续且横向截面更小、表面积更大、间隔分布的条状料,连续朝向真空处理室挤送条状料,各条状料受自重作用向下穿过具有设定高度的真空处理室;通过连接真空处理室的抽气装置持续抽除真空处理室的气体和水分,将真空处理室的真空度控制在0.5-2mpa;通过挤出成型推送螺杆挤送进入挤出机筒的条状料经挤出成型推送螺杆的搅拌混合作用混合成团,并随着挤出成型推送螺杆持续向前挤送而在挤出机筒内经过压缩处理、混炼处理和剪切处理,最通过挤出模头连续挤出。进一步的,所述配料步骤中,选用粘度为2000万的木质纤维素;所述高速混料步骤中,通过多个喷头朝向高速搅拌室喷酒水雾,水雾的平均颗粒控制在0.01-0.1mm,在高速混料步骤中搅拌至高速混料机内的原料初步起团,在高速搅拌过程中,黄原胶的溶胶分子形成超结合带状的螺旋共聚体,形成网状结构体,黄原胶的网状结构体在三维空间中相互交错,以实现包裹木纤维、木质素和木质纤维素并凝结形成多个相对分离的小团装或小块状的所述凝胶体;所述搓揉密炼步骤中,搓揉设备设置有搓揉密炼室,搓揉密炼室中安装有两个旋转方向相反的搓揉杆,两个搓揉杆分别设置有至少一沿径向凸出的搓揉部,两个搓揉杆的对应搓揉部沿轴向方向相邻设置且间隙配合,各搓揉部的外侧分别与搓揉密炼室的内壁间隙配合,将凝胶体投入搓揉密炼室并通过两个搓揉杆连续搓揉凝胶体以得到团状体原料,团状体原料的平均直径大于10cm;所述搓揉密炼步骤中,在搓揉和密炼过程中对凝胶体中黄原胶产生一低剪切作用,凝胶体中的黄原胶形成具有密集网格的网络胶筋,团状体原料各区均匀密布有网络胶筋,网络胶筋包裹团状体原料产生的气体和水分,在团状体原料在形成密布的气孔;所述真空除湿步骤中,从送料挤料室的上部开口连续投入团状体原料,通过安装在送料挤料室中的挤料螺杆将团状体原料向下推挤进入设置在挤料螺杆的下方的挤料通道,使团状体原料向下通过设置在挤料通道中或设置在挤料通道的下方的分料挤料网板,使团状体原料在分料挤料网板的上方堆积设定的高度并保护设定的挤压力,通过挤压并堆积在分料挤料网板上方的团状体原料密封分料挤料网板的上侧空间;将真空处理室的真空度控制在0.8-1.5mpa,在团状体原料经过挤料孔挤压并转变成多个条状料后,存在于团状体原料中的气孔分随之分散包裹在各相应的条状料中,条状料中的气孔的体积变小压力变大,在条状料进入真空处理室后,条状料外部的气压远小于条状料中的气孔内的压力,条状料中的各气孔分别膨胀破裂,使条状料内外遍布細微裂缝,存在于条状料中的气孔中的气体和水分径通过細微裂缝暴射进入真空处理室中,使条状料内外同时快速排出气体和水分;通过密封安装在送料挤料室的一侧的能够打开的第一门体进行维护、清洁或检修送料挤料室;通过密封安装在真空处理室的一侧的能够打开的第二门体进行维护、清洁或检修真空处理室;通过密封安装在挤出进料室的一侧的能够打开的第三门体维护、清洁或检修挤出进料室。所述表干步骤中,隧道式烘箱内的温度控制在60-100℃的热风吹干,以去除经过定厚处理后的水泥板材的余量水分并表干定型,将水泥板材通过隧道式烘箱的时间控制在5-30分钟;成品水泥复合板是具有多种复合材料且不含玻纤布层的单一结构层的板材。进一步的,所述挤出固化步骤,在通过挤出成型推送螺杆挤压推送挤出成型用原料的过程中使挤出成型用原料在挤出机筒中经过混合、密炼和剪切,在高剪切力作用下挤出机筒中的挤出成型用原料因其中的黄原胶粘度迅速下降而混合成具有高流动性的原料团,在原料团进入挤出模头并从挤出模头挤出后,因剪切力消失而使其中的黄原胶粘度迅速上升并而呈现假塑性,进而挤出成型得到初步固化并基本定型的所述水泥板胚板,挤出进料室、挤出机筒和挤出模头的温度均设置在20-30℃;所述定厚处理步骤,经过定厚处理后得到的水泥板材的厚度等于或接近成品水泥复合板的厚度,质量密度1.4±0.1g/mm3;裁切步骤,通过裁切设备裁切经过定厚处理后得到的水泥板材,得到具有设定的长度规格的水泥板材;所述表干步骤,隧道式烘箱内的温度控制在80-90℃的热风吹干,通过隧道式烘箱对经过自然养处理后的水泥板材进行表干处理,通过隧道式烘箱的时间控制在5-10分钟,通过抽气装置抽除隧道式烘箱内的水分;所述养护处理步骤,通过真空吸盘吸取移走经过表干处理的水泥板材,堆垛至托盘后送入养护房养护,将养护房的温度控制在40-60℃,经养护房养护24小时后推出养护房;自然养护处理步骤,对裁切得到的水泥板材进行自然养护处理5-7天,使其表面硬度控制在85-90hv;所述成品步骤,得到成品水泥复合板。本发明的另一技术方案,多层复合水泥板材的生产方法,包括以下步骤,成品水泥复合板的生产步骤,根据权上述的水泥复合板的生产方法,生产得到成品水泥复合板;复合步骤,在成品水泥复合板的上方复合有至少一表面耐磨层和装饰层,在成品水泥复合板的上方和/或下方复合有实木层、软垫层、静音层、防水层和平衡纸层中的至少一种,其中,表面耐磨层位于多层复合水泥板材的顶层,装饰层复合在表面耐磨层之下,得到多层复合水泥板材。进一步的,所述复合步骤中,在所述成品水泥复合板的上方复合有所述实木层、所述软垫层、所述防水层和所述静音层中的至少一种,在成品水泥复合板的下方复合有所述实木层、所述软垫层、所述防水层、所述静音层和所述平衡纸层中的至少一种;成品水泥复合板作为多层复合水泥板材的基材层或基材层以外的其中一种材料层;装饰层包括图案纸层、实木薄片层、瓷砖层或pvc彩膜层;所述复合包括热压复合方式、粘胶复合方式、喷涂复合以及使用模具一体成型的模内成型复合方式;所述表面耐磨层是复合在多层复合水泥板材的顶面的三聚氰胺浸胶纸层或耐磨纸层、三氧化二铝耐磨层、uv漆耐磨层和pvc耐磨片中的至少一种;复合得到的多层复合水泥板材按使用类型区分包括地板或墙板;生产得到的多层复合水泥板材按结构区分包括以下三种结构的其中一,1)、多层复合水泥板材包括设置在最顶层的表面耐磨层、复合在表面耐磨层的下方的装饰层和设置在最底层位置的成品水泥复合板,在装饰层和成品水泥复合板之间复合有实木层、软垫层、静音层、防水层和平衡纸层中的至少一种;2)、多层复合水泥板材包括设置在最顶层的表面耐磨层、复合在表面耐磨层的下方的装饰层和复合在表面耐磨层的下方的成品水泥复合板,在成品水泥复合板的下方复合有实木层、软垫层、静音层、防水层和平衡纸层中的至少一种;3)、多层复合水泥板材包括设置在最顶层的表面耐磨层、复合在表面耐磨层的下方的装饰层和设置在中间位置的成品水泥复合板,在成品水泥复合板的上方和下方分别复合有实木层、软垫层、静音层、防水层和平衡纸层中的至少一种。本发明和现有技术相比所具有的优点是:本发明实现连续生产水泥复合板,工艺简单,生产效率高,生产成本低,生产得到的水泥复合板不但结构强度高,而且尺寸稳定、物理性能稳定。本发明使用连续生产的方法生产水泥复合板,经定厚处理处表面平整度高,表面质量高,在后期不需要另外进行表面机械加工以提升其表面质量,且其长宽尺寸和厚度大小得到有效控制,水泥复合板的长宽误差和厚度误差十分稳定,综合品质稳定。本发明大幅度缩短水泥复合板固化时间,相对传统生产方法本发明的平均生产周期至少减少70%,且取消大量的后期的机械加工和后期处理步骤,同时减少粉尘污染,生产得到的水泥复合板不含有玻纤布层,但结构强度更高。附图说明下面结合附图和实施例对本发明进一步说明。图1是本发明的工艺流程示意图。图2是本发明使用定厚压辊组进行定厚处理的结构示意图。图3是本发明使用压片式循环履带进行定厚处理的结构示意图。图4是本发明的搓揉设备的结构示意图。图中标记:1真空处理装置11真空处理室12分料挤料网板13挤料孔14送料挤料室。2螺杆挤出成型机构21挤出模头22挤出进料室23挤出机筒24挤出成型推送螺杆25进料斗。3隧道式烘箱。4定厚机架41压片式循环履带42压辊43压带辊44搓揉出料筒45搓揉密炼室46搓揉杆47搓揉出料螺杆。5水泥板胚板。具体实施方式水泥复合板的生产方法,图1至4所示,包括以下步骤,配料步骤,按重量百分比进行配置原料,包括水泥粉30-40%、木纤维10-20%、木质素5-10%、木质纤维素2-5%、滑石粉5-10%、黄原胶2-5%和减水剂0.5-5%和水10-15%;木质纤维素选用粘度为2000万的木质纤维素。高速混料步骤,先将水泥粉、木纤维、木质素、木质纤维素、滑石粉、黄原胶和减水剂投入至高速混料机的高速搅拌室,然后开始搅拌,通过至少一喷头将水转变成水雾并喷入高速搅拌室内,在1-5分钟内将重量百分比为10-15%的水雾至高速搅拌室内,其中,水泥粉产生水化合反应而呈泥状。使高速混料机内的原料转变成泥状的凝胶体,较佳的搅拌至使高速混料机内的原料转变成小团状的凝胶体,凝胶体包括黄原胶形成的凝胶物以及均匀分布并包裹于凝胶物中的木纤维、木质素、木质纤维素、减水剂和滑石粉;在高速搅拌过程中,黄原胶的溶胶分子形成超结合带状的螺旋共聚体,形成网状结构体,黄原胶的网状结构体在三维空间中相互交错,以实现包裹木纤维、木质素、木质纤维素、减水剂和滑石粉,并凝结形成多个相对分离的小团装的凝胶体。具体的,在高速混料过程中,通过多个喷头朝向高速搅拌室喷酒水雾,通过喷头将水雾的平均颗粒控制在0.01-0.1mm,在高速混料步骤中搅拌至高速混料机内的原料初步起团,在高速搅拌过程中,黄原胶的溶胶分子形成超结合带状的螺旋共聚体,形成网状结构体,黄原胶的网状结构体在三维空间中相互交错,以实现包裹木纤维、木质素和木质纤维素并凝结形成多个相对分离的小团装或小块状的凝胶体。搓揉密炼步骤,将凝胶体输送至搓揉设备,通过至少一搓揉设备的搓揉杆46搓揉和密炼凝胶体,直至将凝胶体搓揉形成多个团状的具有塑性及黏性的团状体原料。具体的,将高速混料步骤得到的凝胶体输送至搓揉设备,通过搓揉设备的搓揉杆46搓揉和密炼凝胶体,直至将凝胶体搓揉形成多个团状的具有塑性及黏性的团状体原料;较佳的,搓揉设备设置有搓揉密炼室45,搓揉密炼室45中安装有两个旋转方向相反的搓揉杆46,两个搓揉杆46分别设置有至少一沿径向凸出的搓揉部,两个搓揉杆46的对应搓揉部沿轴向方向相邻设置且间隙配合,各搓揉部的外侧分别与搓揉密炼室45的内壁间隙配合,将凝胶体投入搓揉密炼室45并通过两个搓揉杆46连续搓揉凝胶体以得到团状体原料,团状体原料的平均直径大于10cm。具体的,在搓揉和密炼过程中对凝胶体中黄原胶产生一低剪切作用,凝胶体中的黄原胶形成具有密集网格的网络胶筋,团状体原料各区均匀密布有网络胶筋,网络胶筋的网状结构体包裹团状体原料产生的气体和水分,在团状体原料在形成密布的气孔。其中,搓揉设备包括高速搓揉设备和低速搓揉设备,先将凝胶体输送至高速搓揉设备进行高速搓揉密炼,高速搓揉设备的搓揉杆46的转速为300-600转/分钟,通过高速搓揉密炼使凝胶体快速起团,快速形成密集的网络胶筋,减少搓揉时间,提升生产效率,经过高速搓揉密炼再输送至低速搓揉设备进行低速搓揉密炼,低速搓揉设备的搓揉杆46的转速为30-250转/分钟,低速搓揉密炼提升搓揉效果,使其中生成的各网络胶筋的分布更加均匀,且可使其中纵横交错的各网络胶筋相互连接,进而形成更大体积规模的网络胶筋结构,低速搓揉设备的搓揉杆46的转速低于高速搓揉设备的搓揉杆46的转速;在搓揉密炼步骤中先通过高速搓揉设备先将凝胶体搓揉至凝胶体初步起团的状态,后通过低速搓揉设备继续搓揉,在提升搓揉效果的同时保证连续输出团状体原料。搓揉设备的下方分别安装有一搓揉输出机构,搓揉输出机构包括搓揉出料筒44和安装在搓揉出料筒44内的搓揉出料螺杆47,搓揉出料筒44的上侧设置有一连通搓揉设备搓揉密炼室45的搓揉进料口、另一侧设置有搓揉出料口;高速搓揉设备固定在低速搓揉设备的上侧,固定在高速搓揉设备的下方的搓揉输出机构的搓揉出料口延伸至低速搓揉设备的搓揉密炼室45的上方,凝胶体经过高速搓揉密炼处理后连续输送至低速搓揉设备进行低速搓揉密炼处理;直至在低速搓揉设备的搓揉密炼室45形成多个团状的具有塑性及黏性的团状体原料,通过低速搓揉设备连续输出团状体原料至真空处理室11,以实现连续输出团状体原料,实现不间断连续送料和不间断连续生产。真空除湿步骤,将团状体原料输送至真空处理室11,通过真空处理室11进行真空处理并抽离团状体原料中的气体和水分,从真空处理室11排出后进而得到挤出成型用原料。具体的,通过密封安装在真空处理室11的上方的送料挤料室14朝向真空处理室11连续挤入团状体原料;使团状体原料向下通过设置在送料挤料室14或真空处理室11的开设有多个挤料孔13的分料挤料网板12,分别从各挤料孔13连续向下挤出得到多个条状料,使包含在团状体原料中的气体和水分释放至真空处理室11中,通过分料挤料网板12以及挤满各挤料孔13的条状料密封隔开送料挤料室14和真空处理室11;使条状料向下穿过真空处理室11,通过真空处理室11抽除气体和水分。挤出固化步骤,将挤出成型用原料输送至螺杆挤出成型机构2,在常温下连续挤出成型,通过螺杆挤出成型机构2的挤出模头21连续挤出形状为片状的水泥板胚板5,黄原胶使挤出得到的水泥板胚板5经挤出成型即初步固化并基本定型,挤出得到的水泥板胚板5的表面硬度达到邵氏硬度25-30度;具体的,将螺杆挤出成型机构2的挤出进料室22密封安装在真空处理室11的下方,使穿过真空处理室11后的各条状料分别向下落入挤出进料室22中,在挤出进料室22中得到挤出成型用原料;在螺杆挤出成型机构2的中部设置有挤出机筒23,旋转安装在挤出机筒23中的挤出成型推送螺杆24的后侧延伸至挤出进料室22中、前侧邻近安装在螺杆挤出成型机构2的前侧的挤出模头21,通过伸入至挤出进料室22的挤出成型推送螺杆24将连续落入至挤出进料室22中的挤出成型用原料推出挤出进料室22并送入挤出机筒23中,挤出成型推送螺杆24连续推送进料室中的挤出成型用原料;在常温下通过挤出成型推送螺杆24的挤送作用和混合作用使进入挤出机筒23内的挤出成型用原料混合成团,最后通过挤出模头21连续挤出并得到水泥板胚板5,其中,挤出机筒23内的温度和挤出模头21的挤出温度均控制在20-30℃。较佳的,通过一除湿挤出复合设备顺次实现真空除湿步骤与挤出固化步骤。具体的,在螺杆挤出成型机构2的后侧安装有进料斗25,进料斗25的内腔设置成挤出进料室22,在进料斗25的上方密封安装有一真空处理装置1,真空处理装置1的内腔设置成真空处理室11,在真空处理装置1的上方密封安装有挤料装置,挤料装置的内腔设置成送料挤料室14,送料挤料室14、真空处理室11和挤出进料室22竖直对齐,真空处理室11的上部连通送料挤料室14的下部,真空处理室11的下部连通挤出进料室22;组装成一体的挤料装置、真空处理装置1和螺杆挤出成型机构2形成一除湿挤出复合设备,用于顺序实现真空除湿步骤和挤出固化步骤并实现连续生产。将团状体原料输送至挤料装置,通过设置在送料挤料室14内的挤料器将送料挤料室14内的团状体原料向下挤送;通过挤料器的挤送使团状体原料通过分料挤料网板12的各挤料孔13并分别向下挤出成型并进入真空处理室11。具体的,从送料挤料室14的上部开口连续投入团状体原料,通过安装在送料挤料室14中的挤料螺杆将团状体原料向下推挤进入设置在挤料螺杆的下方的挤料通道,使团状体原料向下通过设置在挤料通道中或设置在挤料通道的下方的分料挤料网板12,使团状体原料在分料挤料网板12的上方堆积设定的高度并保护设定的挤压力,通过挤压并堆积在分料挤料网板12上方的团状体原料密封分料挤料网板12的上侧空间。通过堆挤在分料挤料网板12的上方的团状体原料和挤压塞满各挤料孔13的条状料在分料挤料网板12处密封真空处理室11的上部,通过真空处理室11的负压环境辅助向下吸落各条状料;通过分料挤料网板12将团状体原料挤压变成多个长度连续且横向截面更小、表面积更大、间隔分布的条状料,连续朝向真空处理室11挤送条状料,各条状料受自重作用向下穿过具有设定高度的真空处理室11。具体的,将真空处理室11的真空度控制在0.8-1.5mpa,在团状体原料经过挤料孔13挤压并转变成多个条状料后,存在于团状体原料中的气孔分随之分散包裹在各相应的条状料中,条状料中的气孔的体积变小压力变大,在条状料进入真空处理室11后,条状料外部的气压远小于条状料中的气孔内的压力,条状料中的各气孔分别膨胀破裂,使条状料内外遍布細微裂缝,存在于条状料中的气孔中的气体和水分径通过細微裂缝暴射进入真空处理室11中,将真空处理室11的真空度控制在0.5-2mpa,使条状料内外同时快速排出气体和水分,通过连接真空处理室11的抽气装置持续抽除真空处理室11的气体和水分通过挤出成型推送螺杆24挤送进入挤出机筒23的条状料经挤出成型推送螺杆24的搅拌混合作用混合成团,并随着挤出成型推送螺杆24持续向前挤送而在挤出机筒23内经过压缩处理、混炼处理和剪切处理,最通过挤出模头21连续挤出。通过混炼处理和剪切处理不但可以适当降低其中的水泥的粘度,在通过通过挤出模头21挤出成型时更加顺畅,而且可以进一步使水泥与原料中的木纤维、木质素、木质纤维素、减水剂和滑石粉混合更充分,使木纤维、木质素和木质纤维素等中的纤维表面均匀地牢固地附着水泥浆,形成一水泥浆层,更可以使水泥浆层中的水泥浆渗透进入至纤维内部,使水泥浆层牢固地粘结在木纤维、木质素和木质纤维素中的纤维的表面,也使木纤维、木质素和木质纤维素中的不同纤维的相互接触位或搭接处具有极强的的粘结力,以在立体空间中形成立体结构的相互交错的网状结构的立体结构的连续分布在水泥复合板中的三维结构纤维网,三维结构纤维网大幅度增加水泥复合板的抗压结构强度、抗拉伸结构强度和抗弯曲强度等,参见表1实验对比参数,相对于传统的水泥复合板,本发明的水泥复合板的抗撞击性能提升20-30%,防晒防裂功能能提升30-50%。具体的,在通过挤出成型推送螺杆24挤压推送挤出成型用原料的过程中使挤出成型用原料在挤出机筒23中经过混合、密炼和剪切,在高剪切力作用下挤出机筒23中的挤出成型用原料因其中的黄原胶粘度迅速下降而混合成具有高流动性的原料团,在原料团进入挤出模头21并从挤出模头21挤出后,因剪切力消失而使其中的黄原胶粘度迅速上升并而呈现假塑性,进而挤出成型得到初步固化并基本定型的水泥板胚板5,挤出进料室22、挤出机筒23和挤出模头21的温度均设置在20-30℃,不需要进行加热,加工能耗低,确保挤出成型后立刻初步固化成板。较佳的,通过密封安装在送料挤料室14的一侧的能够打开的第一门体进行维护、清洁或检修送料挤料室14,通过密封安装在真空处理室11的一侧的能够打开的第二门体进行维护、清洁或检修真空处理室11,通过密封安装在挤出进料室22的一侧的能够打开的第三门体维护、清洁或检修挤出进料室22。定厚处理步骤,通过至少一定厚辊压设备对水泥板胚板5进行定厚处理,得到具有设定厚度的水泥板材,水泥板材的表面硬度达到邵氏硬度35-40度;通过定厚带压送机构对水泥板胚板5进行定厚处理方法是通过安装在在定厚机架4的循环输送带向前压送水泥板胚板5,并在输送过程中通过循环输送带挤压滚压水泥板胚板5;通过定厚带压送机构对水泥板胚板5进行定厚处理的,在定厚机架4安装有上下两个循环输送带,两个循环输送带之间形成一前后贯穿的带体压送通道,通过安装在带体压送通道的上下两侧的压辊或压板抵顶位于带体压送通道的上下两侧循环输送带,使水泥板胚板5通过带体压送通道,通过带体压送通道的上下两侧循环输送带挤压水泥板胚板5。较佳的,通过定厚压辊组对水泥板胚板5进行定厚处理的方法是通过安装在定厚机架4的多个定厚压辊组辊压输送水泥板胚板5,通过定厚压辊组向前压送水泥板胚板5,在压送过程中同时通过定厚压辊组滚压水泥板胚板5。通过定厚压辊组进行定厚处理的,使水泥板胚板5顺次通过多个定厚压辊组,一个定厚压辊组包括安装在定厚机架4的两个上下间隔设置、竖直对齐且旋转方向相反的压辊42,使水泥板胚板5顺次通过各定厚压辊组的上下两个压辊42同步滚压水泥板胚板5的上下两面,沿水泥板胚板5的前进方向各定厚压辊组的上下两个压辊42之间的压板间距逐逐渐变小,对水泥板胚板5进行分级逐步压缩,最终使水泥板胚板5完全定型。较佳的,通过压片式循环履带41对水泥板胚板5进行定厚处理的方法是通过安装在定厚机架4的至少一压片式循环履带41向前压送水泥板胚板5,同时通过压片式循环履带41在压送水泥板胚板5的过程中同时挤压水泥板胚板5。通过定厚压辊组的滚压或压片式循环履带41的挤压以实现缩小水泥板胚板5的厚度,也可以配合使用厚压辊42组和压片式循环履带41进行定厚处理,在定厚处理步骤中将水泥板胚板5的厚度控制在设定的误差范围内,同时实现挤压排水和加速固化定型速度,使得到的水泥板材的厚度等于或接近成品水泥复合板的厚度,至少通过安装在定厚机架4的左右两侧的定宽板限制水泥板胚板5的宽度,经过定厚处理后得到的水泥板材的厚度等于或接近成品水泥复合板的厚度,质量密度1.4±0.1g/mm3,将经过定厚处理后得到的水泥板材的厚度误差控制在0.5%以下。通过压片式循环履带41进行定厚处理的,在定厚机架4的第一侧安装压片式循环履带41、中部设置有一前后贯穿的压板通道、第二侧安装有定厚带压送机构、压辊42或压片式循环履带41,通过设置在中部的压板通道向前输送和挤压水泥板胚板5,其中,压片式循环履带41是由多个压片顺次连接而成,压片的宽度大于水泥板胚板5的宽度,压片的长度设置在3-20cm,压片式循环履带41抵压水泥板胚板5的一侧设定为压板侧,压板侧的内侧抵压水泥板胚板5、外侧设置有至少一个压带辊43。较佳的,在定厚机架4安装有上下两组压片式循环履带41,上下两组压片式循环履带41之间设置有一压板通道,压片选用金属片,压片式循环履带41为多个金属片顺次连接而成的循环输送带,在上下两个组压片式循环履带41的压板侧的外侧分别间隔设置多个压带辊43,上下两个组压片式循环履带41的对应位置的压带辊43竖直对齐,将水泥板胚板5送入压板通道,通过上下两组压片式循环履带41同时挤压水泥板胚板5并向前输送水泥板胚板5。在定厚处理中可以同时配合使用定厚带压送机构、定厚压辊组和压片式循环履带41。裁切步骤,通过裁切设备裁切经过定厚处理后得到的水泥板材,得到具有设定的长度规格的水泥板材。长度规格是指作为原材料板的长度规格,例如,裁切得到长2.4米、宽1.2米的水泥板材,用于作为加工其它板材的原材料板。表干步骤,向前输送水泥板材并使水泥板材通过隧道式烘箱3,通过隧道式烘箱3对水泥板材进行表面烘干处理,得到完成固化的水泥板材,经表干后的水泥板材的含水率控制在15%以下、表面硬度达到邵氏硬度65-70度、抗弯曲强度达到15-18mpa;较佳的,隧道式烘箱3内的温度控制在60-100℃的热风吹干,以去除经过定厚处理后的水泥板材的余量水分并表干定型,将水泥板材通过隧道式烘箱3的时间控制在5-30分钟。优选的,隧道式烘箱3内的温度控制在80-90℃的热风吹干,通过隧道式烘箱3对经过自然养处理后的水泥板材进行表干处理,通过隧道式烘箱3的时间控制在5-10分钟,通过抽气装置抽除隧道式烘箱3内的水分。养护处理步骤,对水泥板材进行养护处理;具体的,通过真空吸盘吸取移走经过表干处理的水泥板材,堆垛至托盘后送入养护房养护,将养护房的温度控制在40-60℃,经养护房养护24小时后推出养护房。自然养护处理步骤,对裁切得到的水泥板材进行自然养护处理5-7天,使其表面硬度控制在80hv以上,例如,将其表面硬度控制在80-85hv,或者,将其表面硬度控制在85-90hv。成品步骤,经过养护处理步骤后得到不含有玻纤布层的成品水泥复合板,成品水泥复合板的表面硬度控制在80hv以上,成品水泥复合板的抗弯曲强度达到20mpa以上,例如,成品水泥复合板的抗弯曲强度达到22-25mpa。较佳的,成品水泥复合板是具有多种复合材料且不含玻纤布层的单一结构层的板材。例如,经自然养护处理步骤后其表面硬度控制在80-85hv,成品水泥复合板的表面硬度即为80-85hv。经自然养护处理步骤后其表面硬度控制在85-90hv,则成品水泥复合板的表面硬度为85-90hv。得到的成品水泥复合板可以是实心的水泥复合板材,也可以成型有多个间隔设置的贯穿孔的中空的板材。本发明与传统方法生产的含有玻纤布的水泥板相对比,生产得到的水泥板的质量参数对比如表1所示。表面硬度抗弯曲强度吸水率传统方法生产含有玻纤布的水泥复合板70-7515-18mpa10-12%本发明85-9022-25mpa<3%表1质量参数对比本发明与传统方法生产的含有玻纤布的水泥板相对比,生产效率及生产周期对比如表2所示。表2生产效率周期对比实施例二多层复合水泥板材的生产方法,包括以下步骤,成品水泥复合板的生产步骤,包括实施例一的水泥复合板的生产方法,生产得到成品水泥复合板。如果所要生产的多层复合水泥板材的长宽尺寸小于成品水泥复合板的长宽尺寸,根据所要生产板材的长宽规格分切成品水泥复合板,例如将其分切成长60cm、宽60cm的小板,再进行后续的复合步骤或其它加工步骤。复合步骤,在成品水泥复合板的上方复合有至少一表面耐磨层和装饰层,表面耐磨层位于多层复合水泥板材的顶层,装饰层复合在表面耐磨层之下。在成品水泥复合板的上方或下方复合有实木层、软垫层、静音层、防水层和平衡纸层中的至少一种,或者,在成品水泥复合板的上方和下方分别复合有实木层、软垫层、静音层、防水层和平衡纸层中的至少一种,以得到多层复合水泥板材。其中,成品水泥复合板作为多层复合水泥板材的基材层或基材层以外的其中一种材料层。较佳的,在成品水泥复合板的上方复合有实木层、软垫层、防水层和静音层中的至少一种,在成品水泥复合板的下方复合有实木层、软垫层、防水层、静音层和平衡纸层中的至少一种,成品水泥复合板作为多层复合水泥板材的基材层。装饰层包括图案纸层、实木薄片层、瓷砖层或pvc彩膜层。复合包括热压复合方式、粘胶复合方式、喷涂复合以及使用模具一体成型的模内成型复合方式;表面耐磨层是复合在多层复合水泥板材的顶面的三聚氰胺浸胶纸层或耐磨纸层,表面耐磨层也可以是复合在多层复合水泥板材的顶面的三氧化二铝耐磨层、uv漆耐磨层和pvc耐磨片中的至少一种、复合得到的多层复合水泥板材按使用类型区分包括地板或墙板,即可以使用现有技术中的各种加工工艺将成品水泥复合板作为基材或其中的一个材料层并制成地板或墙板。根据多层复合水泥板材的生产方法生产得到多层复合水泥板材,多层复合水泥板材按结构区分包括以下三种结构,1)、多层复合水泥板材包括设置在最顶层的表面耐磨层、复合在表面耐磨层的下方的装饰层和设置在最底层位置的成品水泥复合板,在装饰层和成品水泥复合板之间复合有实木层、软垫层、静音层、防水层和平衡纸层中的至少一种。2)、多层复合水泥板材包括设置在最顶层的表面耐磨层、复合在表面耐磨层的下方的装饰层和复合在表面耐磨层的下方的成品水泥复合板,在成品水泥复合板的下方复合有实木层、软垫层、静音层、防水层和平衡纸层中的至少一种。3)、多层复合水泥板材包括设置在最顶层的表面耐磨层、复合在表面耐磨层的下方的装饰层和设置在中间位置的成品水泥复合板,在成品水泥复合板的上方和下方分别复合有实木层、软垫层、静音层、防水层和平衡纸层中的至少一种。以上内容仅为本发明的较佳实施例,对于本领域的普通技术人员,依据本发明的思想,在具体实施方式及应用范围上均会有改变之处,本说明书内容不应理解为对本发明的限制。当前第1页12