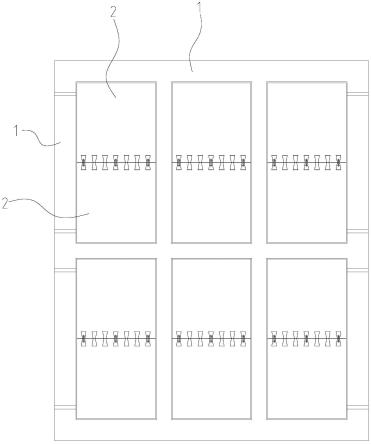
1.本实用新型涉及地下工程防水领域,尤其是一种地铁站装配式中板结构。
背景技术:2.近年来国外相关地下工程防水研究成果较少,这与各国环境条件及基础设施建设情况有关;国内近期研究成果较为丰富,涵盖隧道、地铁、综合管廊及各种地下空间,防水研究大多针对外围护体系,如底板、侧墙、顶板等部位采用全包或者全覆盖的防水方法,包括装配式地铁车站顶板及预制管廊仍采用全外包的方式防水,仅对盾构技术的管片采用接缝连接密封防水。从防水技术趋势看,单一的防水向复合防水发展,铺挂与喷涂结合、嵌缝与构造结合、材料防水与自防水结合等。现有对丙烯酸盐喷膜防水技术的报道较为系统,从研究成果看,较为全面,包括性能、工艺、装备、耐久性、适应性、可靠性等诸多方面,技术趋于成熟,在地下工程防水领域适应性较强,特点突出,是近年来发展较快、较新颖的一项技术。另一方面,绿色及可持续发展理念开始逐步渗透到地下工程之中,从低碳视角也对防水技术的发展提出新的要求。目前对预制装配式结构的防水研究还不完善,高水平的装配式地下工程防水研究成果不多,而地下工程装配式结构中板体系,也就是建筑物内部结构的防水研究成果还未见报道,这说明预制装配式中板结构的应用刚开始起步,还没有显现出受业界关注的问题;二是从传统防水的角度看中板属于室内楼面工程,其防水的必要性还未引起工程界的重视。
3.首先,设施内部水的来源具有多样性,如各种给排水设备因使用维护不当造成的渗漏、雨季城市内涝流入、荷载及地质条件变化使围护结构产生变形开裂、设施检修及清洁等都可能形成楼面积水,这使得即使内部楼面也有防水需求;第二,国家提出大力发展装配式建筑,装配式结构的地铁车站设计逐步进入工程应用,装配式构件存在大量的接缝,使得构造复杂,防水要求及渗漏水机理与现浇结构不同。第三,地铁车站人流密集,设备繁多,以地铁为纽带联系的各种功能空间愈来愈多,也愈加复杂,如果楼面中板结构产生渗漏,将影响各种设施的正常使用,并造成安全隐患,也会制约预制装配式结构在地下工程中应用与发展。因此,中板结构体系的防水问题不容回避,需要新的防水研究课题来填补其空白。
技术实现要素:4.本实用新型所要解决的技术问题是提供一种地铁站装配式中板结构,解决装配式中板结构接缝渗漏水问题。
5.为解决上述技术问题,本实用新型的技术方案是:一种地铁站装配式中板结构,包括若干纵横交错的支撑梁和预制板,纵横交错的支撑梁围成若干铺设区域,每个铺设区域内设有预制板组,所述预制板组由一块或两块以上首尾连接的预制板组成,所述支撑梁的内侧设有支座,所述支座的基面比预制板的顶面低,所述预制板组的两侧设在两侧支撑梁的支座基面上,所述预制板组的两端设在两端支撑梁的支座基面上,预制板组的顶面与预制板组的顶面平齐;预制板组侧面支撑梁的支座基面上设有第一丙烯酸盐喷涂层,预制板
组端面支撑梁的支座基面上设有第二丙烯酸盐喷涂层,所述预制板组四周侧面与支撑梁的侧面之间设有缝隙,所述缝隙内设有第三丙烯酸盐喷涂层,所述缝隙内于第三丙烯酸盐喷涂层的上方设有填充层;相邻预制板相对的端面上设有第四丙烯酸盐喷涂层。
6.与传统设计相比,装配式结构体系能够明显提升工程质量,加快施工进度,减少现场大量的模板、钢筋作业及脚手架工程量,减少施工场地占用面积,减少人工操作、减轻劳动强度,改变建造方式。丙烯酸盐瞬间聚合形成具有较强柔韧性的胶体,具有耐久性好、防水性能可靠、与混凝土能够很好的粘接及一定的损伤自愈性,喷涂方法简便快捷,适应各种复杂基面,不受其他工序施工影响,既可以现场操作,也可以满足工厂工装条件下的自动化喷涂,克服传统防水密封材料在施工及运输中易损问题。由于防水材料遇水有一定的膨胀性,满足结构密封防水要求;防水材料无毒无味、低碳环保,且具有防火阻燃性能,适合在密闭环境施工。
7.作为改进,预制板组中两块相邻的预制板之间通过连接件相互拉紧连接。
8.作为改进,所述预制板为混凝土板,所述预制板的一端或两端设有楔形槽,两相邻的预制板端部的楔形槽相对应,所述连接件设在楔形槽内。
9.作为改进,所述连接件包括螺杆、设在螺杆两端的压块和用于锁紧压块的螺母,所述螺杆的两端伸入两相邻预制板的楔形槽内,两压块分别位于两相邻预制板的楔形槽内。
10.作为改进,所述第一丙烯酸盐喷涂层和第二丙烯酸盐喷涂层的厚度为3~10mm。
11.作为改进,所述第三丙烯酸盐喷涂层的高度不小于20mm。
12.作为改进,所述第四丙烯酸盐喷涂层的厚度为3~5mm。
13.本实用新型与现有技术相比所带来的有益效果是:
14.与传统设计相比,装配式结构体系能够明显提升工程质量,加快施工进度,减少现场大量的模板、钢筋作业及脚手架工程量,减少施工场地占用面积,减少人工操作、减轻劳动强度,改变建造方式。丙烯酸盐瞬间聚合形成具有较强柔韧性的胶体,具有耐久性好、防水性能可靠、与混凝土能够很好的粘接及一定的损伤自愈性,喷涂方法简便快捷,适应各种复杂基面,不受其他工序施工影响,既可以现场操作,也可以满足工厂工装条件下的自动化喷涂,克服传统防水密封材料在施工及运输中易损问题。由于防水材料遇水有一定的膨胀性,满足结构密封防水要求;防水材料无毒无味、低碳环保,且具有防火阻燃性能,适合在密闭环境施工。
附图说明
15.图1为装配式中板结构局部示意图。
16.图2为一个铺设区域的纵向剖视图。
17.图3为图2的a处放大图。
18.图4为图2的b处放大图。
19.图5为一个铺设区域的横向剖视图。
20.图6为图5的c处放大图。
21.图7为装配式中板结构施工流程图。
具体实施方式
22.下面结合说明书附图对本实用新型作进一步说明。
23.如图1所示,一种地铁站装配式中板结构,包括若干纵横交错的支撑梁1和预制板2,纵横交错的支撑梁1围成若干铺设区域,每个铺设区域内设有预制板组,所述预制板组由一块或两块以上首尾连接的预制板2组成。
24.如图1、2、4所示,所述预制板2为混凝土板,其尺寸长
×
宽
×
厚为3400mm
×
2800mm
×
300mm。预制板组中相邻两块预制板2之间通过连接件8相互拉紧连接,所述预制板2的一端或两端设有楔形槽,两相邻的预制板2端部的楔形槽相对应;所述连接件8包括螺杆、设在螺杆两端的压块和用于锁紧压块的螺母,所述螺杆的两端伸入两相邻预制板2的楔形槽内,两压块分别位于两相邻预制板2的楔形槽内。
25.如图2至6所示,所述支撑梁1可以是混凝土现浇或钢结构焊接搭建而成,支撑梁1的内侧设有支座6,所述支座6的基面比预制板2的顶面低,所述预制板组的两侧设在两侧支撑梁1的支座6基面上,所述预制板组的两端设在两端支撑梁1的支座6基面上,预制板组的顶面与预制板组的顶面平齐。预制板组侧面支撑梁1的支座6基面上设有第一丙烯酸盐喷涂层10,所述第一丙烯酸盐喷涂层10的厚度为3~10mm;预制板组端面支撑梁1的支座6基面上设有第二丙烯酸盐喷涂层3,第二丙烯酸盐喷涂层3的厚度为3~10mm;本实施例中,预制板组侧面支撑梁1的支座6基面高度比端面支撑梁1的支座6基面高度低5mm,且侧面支座6基面上的第一丙烯酸盐喷涂层10的厚度为10mm,端面支座6基面上的第二丙烯酸盐喷涂层3的厚度为5mm,确保支座6基面的防水层平整;当预制板安装就位后,挤压防水层达到防水密封效果,考虑预制板支座6的平整度误差,最小喷膜厚度不应小于5mm,形成预制板周边防水密封,当误差达到5mm时,突出部位通过预制板自重将较为柔韧的防水层网周围挤压,板底能够与防水层密贴,聚丙烯酸盐防水材料遇水膨胀的性能可以阻止无压力水的渗透。所述预制板组四周侧面与支撑梁1的侧面之间设有缝隙,所述缝隙内设有第三丙烯酸盐喷涂层4,当误差大于5mm时,预制板底由于支点的不平整会产生间隙,则用丙烯酸盐防水材料以喷涂方式注入周边预留缝隙,在预制板与支座6的侧缝中形成竖向防水注浆层,注浆层高度不小于20mm并完全覆盖底板缝隙,同时,调整材料的聚合时间,使防水材料注入缝隙后有一定的流平,以灌入缝隙又不会从缝隙流出为标准,达到可靠的防水密封效果;所述缝隙内于第三丙烯酸盐喷涂层4的上方设有填充层5,所述填充层5为混凝土层,用于封堵侧缝隙。在两块预制板之间接缝处设置一道竖向防水带,考虑现在使用的预制板构造要在两板之间实施榫卯连接,防水层设置在板接缝立面沿底边向上100mm宽范围内,厚度不小于5mm;由于预制板没有设置防水层的企口,相邻预制板相对的端面上设置3mm厚的第四丙烯酸盐喷涂层9。
26.如图7所示,本实用新型施工方法,包括以下步骤:
27.(1)混凝土现浇纵横交错的支撑梁1,或钢结构焊接搭建纵横交错的支撑梁1;
28.(2)在预制板组侧面支撑梁1的支座6基面上喷涂丙烯酸盐防水材料形成第一丙烯酸盐喷涂层10;
29.(3)在预制板组端面支撑梁1的支座6基面上喷涂丙烯酸盐防水材料形成第二丙烯酸盐喷涂层3;
30.(4)在预制板的连接端端面喷涂丙烯酸盐防水材料形成第四丙烯酸盐喷涂层9;
31.(5)将预制板吊装至纵横交错的支撑梁1所形成的铺设区域内,且预制板的侧面与
支撑梁1的侧面之间留有缝隙;
32.(6)利用连接件将两相邻的预制板相互拉紧连接,使相邻预制板端面的第四丙烯酸盐喷涂层9相互挤压;预制板安装就位后利用预制板楔形槽设置连接螺栓,采用紧固螺栓产生的螺杆拉力使预制板缝之间产生压力将防水膜压紧;采用力矩扳手紧固螺栓,两板间距产生位移约1.4mm,最大力矩值250n/m,由于丙烯酸盐与混凝土产生的粘接力和摩擦力,当螺栓松开后,两板对板缝防水层产生的挤压不会消失,螺紧固栓可以作为永久性施加,也可作为施工临时加压手段;
33.(7)在缝隙内喷涂丙烯酸盐防水材料形成第三丙烯酸盐喷涂层4,第三丙烯酸盐喷涂层4的高度不小于20mm,注浆时调整丙烯酸盐防水材料的聚合时间,使材料注入缝隙后有一定的流平,以灌入缝隙又不会从缝隙流出为标准;
34.(8)在缝隙内于第三丙烯酸盐喷涂层4的上方加入填充材料形成填充层。
35.支座6和板缝防水层要在吊装前现场喷涂,喷涂作业在吊装前24小时完成,板缝两侧防水层沿板接缝贯通设置,延伸到转角端侧100mm,此防水层要求喷涂厚度均匀,厚度误差小于1mm,误差大于1mm时,采用人工打磨找平。
36.两板间接缝防水膜厚度6mm,采用两面各喷3mm实现,从工艺上容易实现,喷膜时与混凝土基面粘接效果好,经螺栓紧固挤压,固化后丙烯酸盐膜和膜之间粘接好于膜与混凝土的粘接。
37.支座6喷涂5mm厚防水膜基本能够达到预制结构有一定误差时通过防水膜的压缩去高补低,保证支座6较小不平整及膜厚不均匀时的防水性能。
38.当支座6平整度误差较大时,边缝的注浆密封作业明显,调整聚合时间到5s时,能够产生足够的流平作用,在边缝内形成与底部两侧很好粘贴的整体密封带,与支座6接缝喷膜防水结合,满足i级防水设计要求,其最小高度应视缝宽和聚合时间确定。
39.本实用新型采用的丙烯酸盐防水材料为双组分喷膜防水材料,包括a组分和b组分,a组分原料按重量份由以下组份组成:丙烯酸盐单体溶液100份,改性硅酮0.5~5份,羟乙基脲0.01~0.1份,填料5~20份;b组分原料按重量份由以下组份组成:丙烯酸盐单体溶液100份,改性硅酮0.5~5份,羟乙基脲0.01~0.1份,填料5~20份。
40.对于预制混凝土结构中板体系,其防水密封只要针对楼地面没有渗透压力的浮水,混凝土预制构件指防水能力保证梁板混凝土本身无渗漏,板缝及支座6构造是防水的关键。采用丙烯酸盐喷涂方法适应装配式结构各种接缝处的防水密封;本实用新型确定了一套施做简便、效果可靠的防水技术,从材料性能、施工工艺和作业过程看,丙烯酸盐喷膜防水对相关工序影响很小,适合现场完成;支座6基面平整可采用安装前喷膜施工,基面不平时可在安装完毕进行竖缝灌注法二次密封,2种方法结合可以满足i级防水要求且可靠性大大提高。
41.防水试验
42.1.加载试验及闭水检验
43.利用预制板b1和b2模拟装配式中板结构,为模拟两板接缝相对最大变形,只对板b1加载,加载采用1.5m3混凝土试块,每块重量3200kg,分两次加载,每次加载2块,2次加载间隔为2周。丙烯酸盐灌注侧缝后继续闭水试验,没有渗漏水现象后,立即对板b1进行第一次加载。经过48小时闭水试验后,将水撤掉后放置12天,考察暴露日晒的自然条件下防水膜
干缩状况,然后进行第二次加载并进行48小时闭水试验,排水后自然放置,3周后进行连续闭水试验
44.加载及闭水情况记录表:
[0045][0046]
2.防水膜硬度及干湿循环影响分析
[0047]
从不均衡加载到闭水试验的干湿循环,采用侧缝喷涂注浆防水后均没有发现渗漏水现象,而喷膜完成时硬度为4.0,24小时硬度为8.7,经过2周自然放置,加第2次荷载时硬度最高达到29.5,加载后闭水无渗漏。最长3周的自然放置,防水膜外露部分明显硬化,露出部位邵氏硬度从8.0达到36.0左右(从水放干水后24小时开始测)后闭水无渗漏。说明在干湿循环、结构变形等情况没有影响防水膜的防水性能。安装时防水膜硬度应控制在5~8之间,这样挤压作用下不易损坏,且能够通过变形调整由基面或者喷膜不平整造成的缝隙。
[0048]
防水膜避光放置硬度变化表
[0049][0050]
3.丙烯酸盐防水膜失水干硬后防水机理
[0051]
通过现场观察,丙烯酸盐防水膜在较为干燥的环境下自然放置3周后,邵氏硬度达到36并具有一定韧性。当防水膜夹在预制板和支座6之间时,干硬仅限于边缘外露部分,中间部位的防水膜受外界干湿度影响很小。从后期观察看,防水膜与混凝土板和支座6很好的粘接性,使得防水膜干燥收缩沿膜层向内进行,防水膜仅产生切向变形,并不会因为法相变形与混凝土产生脱离,由于防水膜外边缘干硬区产生3-4mm厚时,产生一节高密度硬化段,起到阻止水分向外继续蒸发的作用,可以保证内部防水膜长期处于柔韧状态。支座6和预制板防水膜宽度达到100mm,即使接缝外露处两边都产生5mm的干硬区,仍然有90mm的柔韧区保持防水膜的最佳防水性能,这也是防水膜能够适应干湿循环条件下的加载变形不会产生渗漏的机理。从干湿循环来看,即使防水膜干硬,吸水后即回归原状态,膜的表观及力学性能不会改变。
[0052]
4.加载及变形观测
[0053]
由于变形观测主要考察两板之间的相对变形对防水密封的影响,因此没有考虑自重影响,以加载前变形为初始值。
[0054]
加载变形观测值表
[0055][0056]
表中板b1支座6变形是由防水层压缩产生,跨中测量变形值减去支座6测量变形值即为加载后预制板跨中实测挠度值。
[0057]
5.试验结果分析
[0058]
经过全过程试验及2个月的观测,进行了2次加载试验,加载试块、板自重和0.1米闭水荷载等折算后略高于设计荷载值,可以模拟设计荷载。第1次加载后累计变形值为1.18mm,第2次加载累计变形值为0.94mm,加载后板b1累计变形值为2.12mm,板b2累计变形值为0.03mm,板b1与板b2最大变形差值为2.09mm。
[0059]
当剪切变形达到2.5mm,即超过缝宽25%时开始出现渗漏现象,本模型试验缝宽设计值为6mm。板b1跨中变形值只为测量不是板结构的精确值,受支座6基面不平整甚至两支座6边不在一个平面的影响,除了防水膜不均匀压缩变形,还受板翘曲的影响,变形小于允许变形值1/500跨度。2次加载全过程和2次干湿循环闭水试验,未见渗漏水现象发生,说明在干湿和不均衡加载产生最大变形条件下,丙烯酸盐防水膜防水密封效果没有影响。板b2在板b1在二次加载前,相对变形值为零,即第一次加载对板b2没有影响,螺栓紧固作用下,当荷载值较小时,传递的剪力很小,可以认为两板变形是独立的;在2次加载时产生0.03~0.04mm的变形量,说明在螺栓紧固作用下,两块板接缝之间的丙烯酸盐防水膜已经产生粘接力,2周时间的自然放置使防水膜硬度和韧性提高,能够传递一定的剪力,使板b2产生微小变形。也说明板缝之间的防水膜粘接有利于各板之间的协同工作。