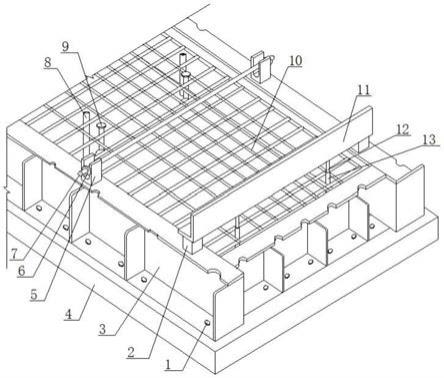
1.本发明涉及建筑制造技术领域,尤其涉及可循环预制装配式道路结构及其施工方法。
背景技术:2.我国在建筑制造业中产生的建筑垃圾已占到城市垃圾总量的30%,随着国家倡导绿色施工理念的不断深入,开展可循环装配式道路施工研究已势在必行,装配式道路循环使用可以减少资源浪费和建筑垃圾,能够实现节能减排,提高经济效益和社会效益。
3.目前国内工程项目施工现场的临时施工道路多采用现浇混凝土路面结构,但其养护时间长,且破除后会造成人工和材料的浪费,产生大量建筑垃圾,对环境造成危害。
技术实现要素:4.1.要解决的技术问题
5.本发明的目的是为了解决现有技术中工程项目施工现场的临时施工道路多采用现浇混凝土路面结构,但其养护时间长,且破除后会造成人工和材料的浪费,产生大量建筑垃圾,对环境造成危害的问题,而提出的可循环预制装配式道路结构及其施工方法。
6.2.技术方案
7.为了实现上述目的,本发明采用了如下技术方案:
8.可循环预制装配式道路结构,包括底模,所述底模的上端设有四个呈矩形分布的侧模,四个所述侧模墩放于底模上,所述底模与侧模均采取侧包底,所述底模与侧模结合部位嵌入橡胶条密封,所述侧模与底模之间设有m12螺栓与锁紧螺母,所述锁紧螺母焊接于底模下表面,所述侧模与底模之间通过m12螺栓与锁紧螺母固定连接,相邻两个所述侧模之间同样采用m12螺栓连接,纵向两相对所述侧模顶面均设有限位机构,四个所述侧模之间设有钢筋骨架、脱模吊点与拼装吊点,四个所述侧模之间浇筑有预制板,纵向两相对所述侧模顶面上均固定有支撑柱,所述支撑柱上设有钢承板,所述钢承板上固定有限位螺杆,所述预制板上固定有与限位螺杆对应的圆饼状限位器,所述限位螺杆与圆饼状限位器螺纹连接,所述钢承板与预制板之间设有螺栓,所述预制板的上端面设有与螺栓对应的螺栓孔,所述螺栓孔内设有限位螺母,所述限位螺母与螺栓之间螺纹连接。
9.优选地,所述限位机构包括两个支架,两个所述支架分别焊接在纵向两相对侧模的顶面上,两个所述支架之间设有拉杆,所述拉杆的两端分别贯穿两个支架并螺纹连接有固定螺母。
10.优选地,所述钢筋骨架包括两层钢筋网片,两层所述钢筋网片之间设有支撑筋,两层钢筋网片之间通过支撑筋连接,所述钢筋网片纵向筋为φ16mm,横向筋为φ14mm。
11.优选地,所述脱模吊点包括四支m24内螺纹套筒,所述m24内螺纹套筒尾部插入φ12mm螺纹钢筋,所述m24内螺纹套筒与钢筋骨架焊接在一起,所述脱模吊点预埋于预制板抹灰面一侧。
12.优选地,所述拼装吊点包括四支5t
×
210mm的吊点,所述吊点采用橡胶半球预埋于预制板清水面一侧,所述拼装吊点翻板后采用高强鸭嘴扣吊具配合吊车进行铺装。
13.本发明提供可循环预制装配式道路结构施工方法,所述可循环预制装配式道路结构施工方法包括如下步骤:
14.步骤一、路面板生产:(1)钢筋加工,钢筋半成品加工,按照规范要求,提出相应控制措施,确保钢筋半成品堆放规范化、质量标准化,钢筋笼加工时,采用胎架、卡具定位,保证钢筋笼加工质量;(2)模具工程,路面板施工的模具形式主要为“底包边”、“边包底”两种结构形式、采用定型模具可有效的控制路面板结构尺寸,模具安拆简便、施工工效高;(3)钢筋笼入模,钢筋笼由钢筋加工区集中加工制作,运送至预制区,由龙门吊吊装至已检验通过的模具中;(4)混凝土浇筑及养护,混凝土运输至生产车间,采用料斗均匀布料,浇筑成型后,采用电蒸汽设备恒温养护,路面板堆场中的路面板经养护达到脱模强度后,采用板车倒运至堆场区以备铺装使用;
15.步骤二、道路面板预制:(1)模具安装,检查侧模之间及侧模与底板接缝处胶条是否有脱落现象,如有及时纠正,避免漏浆,侧模组装时角度和顶部标高控制尤为关键,采用卷尺、直角尺、水平尺、游标卡尺等检测工具,保证路面板模具的组装精度,将组模偏差控制在1毫米内;(2)模具及模具控制
①
模具制造,采用专业设计,委托专门厂家加工制作,路面板模具全部采用高精度数控龙门铣床加工,侧模墩放于底模上,通过m12螺栓与焊接于底模下表面的螺母连接在一起,相邻侧模间同样采用m12螺栓连接,纵向两相对侧模顶面采用拉杆约束,充分保证路面板模具的组装精度,将偏差控制在毫米以内,
②
浇筑前检查螺栓牢固性,避免施工过程跑模、胀模、构件变形,检查模具完好,对使用过程中,变形、损毁的模具及时修复或报废,保证施工精度,
③
模台及模具清理干净,保持清洁,无残渣、残留,钢筋入模前均匀喷涂脱模剂,且保持洁净,不得有污染,
④
模具拆卸时,要求小心轻放,不得蛮横、粗暴作业,模具堆放在规定位置,底模与侧模采取侧包底,结合部位嵌入橡胶条密封,侧模与侧模间采用螺栓连接,侧模拼缝处的模具采用刨床刨边,以保证拼缝平整严密;(3)模具使用
①
模具及支架安装必须稳固牢靠,模具接缝严密,不得漏浆,用磨光机将模具干浆、浮锈打磨干净,涂刷脱模剂,用于封堵侧模与内模端部连接处缝隙的胶带要每次清理干净,否则会漏浆,
②
模具拆除:当板体混凝土强度达到20mpa以上,保证板体表面及棱角完整时可以拆模;
16.步骤三、钢筋加工:钢筋应平直、无局部弯折现象,清除钢筋表面的锈斑、灰尘、油脂及其它有害物质;施工时应在钢筋加工场将路面板钢筋骨架加工好,(1)钢筋大样图,进行分解后,根据试制确定下料长度,保证下料精确,采用数据加工中心下料,钢筋下料后,在模具上精确布筋,准确定位,保证数量,由作业工人绑扎成型;(2)设计固定吊具,将成型钢筋网片吊装入模;(3)钢筋保护层控制采用预制垫块,垫块强度与预制板混凝土标号一致,面板钢筋保护层控制采用上层钢筋网限位设置,避免钢筋网片在混凝土浇筑时产生上浮;
17.步骤四、预埋件安装:在路面板脱模吊点位置预埋吊装套筒,预埋吊装套筒由15cmφ32钢筋制作而成,中间内套m20丝口,安装时丝口端与板面齐平,(1)预留m24螺杆孔采用精加工预埋件,在模具底模上加工向上凸出的φ40
×
5mm圆饼状限位器,预埋件底部加工向内凹陷的φ41
×
6mm圆饼状凹槽,使预埋件底部与底模实现精准对位;(2)脱模吊点,吊装设置,采取内螺纹套筒,套筒定位设置定位筋,保证吊点定位,吊装作业时,混凝土强度应达到
20mpa,每个构件至少回弹3个点,取加权平均值,脱模吊点采用4支m24内螺纹套筒,尾部插入φ12mm螺纹钢筋且与板体钢筋网片焊接在一起,预埋于板体抹灰面一侧,配合高强吊环进行脱模;(3)翻板吊点,翻板吊点采用2支m24内螺纹套筒,尾部插入φ12mm螺纹钢筋且与板体钢筋网片焊接在一起,预埋于板体纵缝侧面,配合高强吊环进行翻板;(4)拼装吊点采用四支5t
×
210mm的吊点,通过配套的橡胶半球预埋于板体清水面一侧,翻板后采用高强鸭嘴扣吊具配合吊车进行铺装;
18.步骤五、混凝土浇筑:混凝土采用商品混凝土,混凝土质量容易保证,混凝土对到场后由质检人员检查混凝土到场状态,合格后方可浇筑,路面板采用反打法,c40混凝土浇筑成型,采用两次抹压成型工艺对其上表面抹平压槽,混凝土初凝后,进行养护,在混凝土浇筑后12小时内对混凝土加以覆盖并浇水养护,采用吸湿能力强的材料覆盖养护,不少于7天,临时道路板达到混凝土强度设计要求,方可投入使用;
19.步骤六、路基施工:(1)清表,路基填筑前,应首先对现状地面进行清表处理,清表深度约为30cm,再回填素土至路面结构层底,最后施工做路面结构层;(2)路堤填筑,填土区段按照网格化布料,用推土机或平地机摊铺平整,使填层在纵向和横向平顺均匀,以保证压路机碾压轮表面能基本均匀接触层面进行压实,路堤碾压完成后,压实层顶面稳定、无下沉、表面平整无车辙;(3)级配碎石基层施工,级配碎石采用配比为(10
‑
30mm):(10
‑
20mm):(5
‑
10mm):石粉=15%:35%:15%:35%,级配碎石铺设完成并检验合格后,在级配碎石上铺设防水土工布,要求防水土工布每侧超宽50cm铺设,铺设时防水土工布不得有破损,纵向路基方向不得有搭接,横向搭接宽度≥30cm,最后铺筑预制混凝土路面板;(4)铺设砂垫层,为保证路面板基层平整度,确保路面板受力均匀,在级配碎石铺设完成后用砂垫层进行精平,防止路面板下出现空洞;(5)防水土工布铺设,防水土工布铺设完成后铺筑中粗砂进行找平,最后铺筑预制混凝土路面板,根据道路断面图,测放防水土工布铺设边线,并立木桩进行位置标注,木桩间距20米,土工布检验合格后方可进行使用,(6)路堑开挖,先用破碎机破碎,然后用挖掘机配合开挖的方式,对于零星土方可用推土机推土堆积再用装载机或挖掘机配合自卸汽车运土,在施工中要根据所放桩位控制开挖深度,避免超欠挖,施工中要加强对地下管道、缆线或其它结构物的保护,路堑开挖应避免超挖或欠挖;
20.步骤七、路面板安装:吊车人工铺装,根据现场安排安排,在附近做面板存放场地,预制装配式面板安装前应对基层平整度进行检测,检测合格后方可进行路面板安装,面板运至现场后,首先检查到场预制面板的质量,外观无破损及裂缝,预制尺寸满足设计要求,检查橡胶条粘贴是否牢固,位置是否准确,如发现不合格产品,禁止使用,安装时,严格按照设计及规范要求控制安装偏差,确保面板安装质量,路面板铺装采用汽车吊,采用专用卡具保证板缝为3mm,路面板铺装时由6个工人配合,负责路面板的四个角,将路面板精确就位。
21.优选地,所述步骤二中模具拆除时气温急剧变化时不得拆模,环境温度低于0℃时,必须等待表层混凝土冷却至5℃以下方可拆模,在炎热或大风干燥季节,需采取边拆模边浇水(或涂养护剂),防止水分丧失过快。
22.优选地,所述步骤四中在预埋件顶部加工m16内螺纹孔,将m16配套螺杆通过固定于侧模上的钢承板上的预留孔拧入预埋件内,依靠底模上的φ40
×
5mm圆饼状限位器和m16螺杆实现预埋件的精准定位,连接槽口尺寸为φ80
×
70mm,螺杆孔尺寸为φ40
×
190mm,螺杆与孔间隙填塞聚氨酯泡沫材料。
23.优选地,所述步骤六中防水土工布铺设时土工布为两布一膜,防水土工布卷在使用前要用防紫外线照射的不透明塑料布遮盖,防止其受紫外线而老化,并且要保证标签和资料的完整,以便使用前进行核验,运输过程中,动作要尽可能的轻,保证防水土工布卷完好,土工布铺设前,检查基层表面无凸起杂物,基层表面平整,铺设采用人工滚铺的方式,保证防水土工布铺设平整,并留有一定的变形余量。
24.3.有益效果
25.相比于现有技术,本发明的优点在于:
26.(1)本发明中,通过可重复使用路面板能整体吊装拼接,周转多个工程使用,可减少建筑资源的浪费,有利于建筑企业降低成本、缩短施工周期,有利于开发新型的建筑临时设施租赁业务,扩展公司业务渠道。
27.(2)可以广泛应用于雄安新区短期使用道路、施工道路、停车及市民广场、货物堆场等工程。实现了快速装拆、循环利用、零排放、零固废的绿色生态可循环基础设施建设目标,充分体现了预制装配设施的灵活性、便捷性与适应性。装配式道路与传统现浇混凝土道路相比,具有环保、100%可循环、安拆方便、经济合理等优点。
28.(3)该可循环预制装配式道路结构不采用化学处理,拆除重建时能够迅速恢复地貌且不产出建筑垃圾,对环境影响小,级配碎石和路面板可重复使用,具有工期短、环保、可循环、工厂化生产、自动化程度高等优点,能够实现绿色环保、流程化快速建设及造价适宜的目的。
附图说明
29.图1为本发明提出的可循环预制装配式道路结构及其施工方法的结构示意图;
30.图2为本发明提出的可循环预制装配式道路结构及其施工方法的钢承板连接结构示意图;
31.图3为本发明提出的可循环预制装配式道路结构及其施工方法的m24螺杆孔工装设计结构示意图;
32.图4为本发明提出的可循环预制装配式道路结构及其施工方法的路面板生产工艺流程图;
33.图5为本发明提出的可循环预制装配式道路结构及其施工方法的路基施工工艺流程图。
34.图中:1m12螺栓,2支撑柱,3侧模,4底模,5支架,6固定螺母,7拉杆,8螺纹套筒,9拼装吊点,10钢筋骨架,11钢承板,12限位螺杆,13圆饼状限位器,14限位螺母,15预制板,16螺栓,17螺栓孔。
具体实施方式
35.下面将结合本发明实施例中的附图,对本发明实施例中的技术方案进行清楚、完整地描述,显然,所描述的实施例仅仅是本发明一部分实施例,而不是全部的实施例。
36.在本发明的描述中,需要理解的是,术语“上”、“下”、“前”、“后”、“左”、“右”、“顶”、“底”、“内”、“外”等指示的方位或位置关系为基于附图所示的方位或位置关系,仅是为了便于描述本发明和简化描述,而不是指示或暗示所指的装置或元件必须具有特定的方位、以
特定的方位构造和操作,因此不能理解为对本发明的限制。
37.实施例1:
38.参照图1
‑
5,可循环预制装配式道路结构施工方法包括如下步骤;
39.步骤一、路面板生产:(1)钢筋加工,钢筋半成品加工,按照规范要求,提出相应控制措施,确保钢筋半成品堆放规范化、质量标准化,钢筋笼加工时,采用胎架、卡具定位,保证钢筋笼加工质量;(2)模具工程,路面板施工的模具形式主要为“底包边”、“边包底”两种结构形式、采用定型模具可有效的控制路面板结构尺寸,模具安拆简便、施工工效高;(3)钢筋笼入模,钢筋笼由钢筋加工区集中加工制作,运送至预制区,由龙门吊吊装至已检验通过的模具中;(4)混凝土浇筑及养护,混凝土运输至生产车间,采用料斗均匀布料,浇筑成型后,采用电蒸汽设备恒温养护,路面板堆场中的路面板经养护达到脱模强度后,采用板车倒运至堆场区以备铺装使用;
40.步骤二、道路面板预制:(1)模具安装,检查侧模之间及侧模与底板接缝处胶条是否有脱落现象,如有及时纠正,避免漏浆,侧模组装时角度和顶部标高控制尤为关键,采用卷尺、直角尺、水平尺、游标卡尺等检测工具,保证路面板模具的组装精度,将组模偏差控制在1毫米内;(2)模具及模具控制
①
模具制造,采用专业设计,委托专门厂家加工制作,路面板模具全部采用高精度数控龙门铣床加工,侧模墩放于底模上,通过m12螺栓与焊接于底模下表面的螺母连接在一起,相邻侧模间同样采用m12螺栓连接,纵向两相对侧模顶面采用拉杆约束,充分保证路面板模具的组装精度,将偏差控制在毫米以内,
②
浇筑前检查螺栓牢固性,避免施工过程跑模、胀模、构件变形,检查模具完好,对使用过程中,变形、损毁的模具及时修复或报废,保证施工精度,
③
模台及模具清理干净,保持清洁,无残渣、残留,钢筋入模前均匀喷涂脱模剂,且保持洁净,不得有污染,
④
模具拆卸时,要求小心轻放,不得蛮横、粗暴作业,模具堆放在规定位置,底模与侧模采取侧包底,结合部位嵌入橡胶条密封,侧模与侧模间采用螺栓连接,侧模拼缝处的模具采用刨床刨边,以保证拼缝平整严密;(3)模具使用
①
模具及支架安装必须稳固牢靠,模具接缝严密,不得漏浆,用磨光机将模具干浆、浮锈打磨干净,涂刷脱模剂,用于封堵侧模与内模端部连接处缝隙的胶带要每次清理干净,否则会漏浆,
②
模具拆除:当板体混凝土强度达到20mpa以上,保证板体表面及棱角完整时可以拆模;
41.步骤三、钢筋加工:钢筋应平直、无局部弯折现象,清除钢筋表面的锈斑、灰尘、油脂及其它有害物质;施工时应在钢筋加工场将路面板钢筋骨架加工好,(1)钢筋大样图,进行分解后,根据试制确定下料长度,保证下料精确,采用数据加工中心下料,钢筋下料后,在模具上精确布筋,准确定位,保证数量,由作业工人绑扎成型;(2)设计固定吊具,将成型钢筋网片吊装入模;(3)钢筋保护层控制采用预制垫块,垫块强度与预制板混凝土标号一致,面板钢筋保护层控制采用上层钢筋网限位设置,避免钢筋网片在混凝土浇筑时产生上浮;
42.步骤四、预埋件安装:在路面板脱模吊点位置预埋吊装套筒,预埋吊装套筒由15cmφ32钢筋制作而成,中间内套m20丝口,安装时丝口端与板面齐平,(1)预留m24螺杆孔采用精加工预埋件,在模具底模上加工向上凸出的φ40
×
5mm圆饼状限位器,预埋件底部加工向内凹陷的φ41
×
6mm圆饼状凹槽,使预埋件底部与底模实现精准对位;(2)脱模吊点,吊装设置,采取内螺纹套筒,套筒定位设置定位筋,保证吊点定位,吊装作业时,混凝土强度应达到20mpa,每个构件至少回弹3个点,取加权平均值,脱模吊点采用4支m24内螺纹套筒,尾部插
入φ12mm螺纹钢筋且与板体钢筋网片焊接在一起,预埋于板体抹灰面一侧,配合高强吊环进行脱模;(3)翻板吊点,翻板吊点采用2支m24内螺纹套筒,尾部插入φ12mm螺纹钢筋且与板体钢筋网片焊接在一起,预埋于板体纵缝侧面,配合高强吊环进行翻板;(4)拼装吊点采用四支5t
×
210mm的吊点,通过配套的橡胶半球预埋于板体清水面一侧,翻板后采用高强鸭嘴扣吊具配合吊车进行铺装;
43.步骤五、混凝土浇筑:混凝土采用商品混凝土,混凝土质量容易保证,混凝土对到场后由质检人员检查混凝土到场状态,合格后方可浇筑,路面板采用反打法,c40混凝土浇筑成型,采用两次抹压成型工艺对其上表面抹平压槽,混凝土初凝后,进行养护,在混凝土浇筑后12小时内对混凝土加以覆盖并浇水养护,采用吸湿能力强的材料覆盖养护,不少于7天,临时道路板达到混凝土强度设计要求,方可投入使用;
44.步骤六、路基施工:(1)清表,路基填筑前,应首先对现状地面进行清表处理,清表深度约为30cm,再回填素土至路面结构层底,最后施工做路面结构层;(2)路堤填筑,填土区段按照网格化布料,用推土机或平地机摊铺平整,使填层在纵向和横向平顺均匀,以保证压路机碾压轮表面能基本均匀接触层面进行压实,路堤碾压完成后,压实层顶面稳定、无下沉、表面平整无车辙;(3)级配碎石基层施工,级配碎石采用配比为(10
‑
30mm):(10
‑
20mm):(5
‑
10mm):石粉=15%:35%:15%:35%,级配碎石铺设完成并检验合格后,在级配碎石上铺设防水土工布,要求防水土工布每侧超宽50cm铺设,铺设时防水土工布不得有破损,纵向路基方向不得有搭接,横向搭接宽度≥30cm,最后铺筑预制混凝土路面板;(4)铺设砂垫层,为保证路面板基层平整度,确保路面板受力均匀,在级配碎石铺设完成后用砂垫层进行精平,防止路面板下出现空洞;(5)防水土工布铺设,防水土工布铺设完成后铺筑中粗砂进行找平,最后铺筑预制混凝土路面板,根据道路断面图,测放防水土工布铺设边线,并立木桩进行位置标注,木桩间距20米,土工布检验合格后方可进行使用,(6)路堑开挖,先用破碎机破碎,然后用挖掘机配合开挖的方式,对于零星土方可用推土机推土堆积再用装载机或挖掘机配合自卸汽车运土,在施工中要根据所放桩位控制开挖深度,避免超欠挖,施工中要加强对地下管道、缆线或其它结构物的保护,路堑开挖应避免超挖或欠挖;
45.步骤七、路面板安装:吊车人工铺装,根据现场安排安排,在附近做面板存放场地,预制装配式面板安装前应对基层平整度进行检测,检测合格后方可进行路面板安装,面板运至现场后,首先检查到场预制面板的质量,外观无破损及裂缝,预制尺寸满足设计要求,检查橡胶条粘贴是否牢固,位置是否准确,如发现不合格产品,禁止使用,安装时,严格按照设计及规范要求控制安装偏差,确保面板安装质量,路面板铺装采用汽车吊,采用专用卡具保证板缝为3mm,路面板铺装时由6个工人配合,负责路面板的四个角,将路面板精确就位。
46.本发明中,步骤二中模具拆除时气温急剧变化时不得拆模,环境温度低于0℃时,必须等待表层混凝土冷却至5℃以下方可拆模,在炎热或大风干燥季节,需采取边拆模边浇水(或涂养护剂),防止水分丧失过快;步骤四中在预埋件顶部加工m16内螺纹孔,将m16配套螺杆通过固定于侧模上的钢承板上的预留孔拧入预埋件内,依靠底模上的φ40
×
5mm圆饼状限位器和m16螺杆实现预埋件的精准定位,连接槽口尺寸为φ80
×
70mm,螺杆孔尺寸为φ40
×
190mm,螺杆与孔间隙填塞聚氨酯泡沫材料;步骤六中防水土工布铺设时土工布为两布一膜,防水土工布卷在使用前要用防紫外线照射的不透明塑料布遮盖,防止其受紫外线而老化,并且要保证标签和资料的完整,以便使用前进行核验,运输过程中,动作要尽可能的
轻,保证防水土工布卷完好,土工布铺设前,检查基层表面无凸起杂物,基层表面平整,铺设采用人工滚铺的方式,保证防水土工布铺设平整,并留有一定的变形余量。
47.本发明中,通过m12螺栓1实现底模4与侧模3之间的安装,m12螺栓1同时用于两个相邻侧模3之间的固定安装,易于拆卸,在四个侧模3与底模4之间浇筑混凝土成型,采用两次抹压成型工艺对其上表面抹平压槽,混凝土初凝后,进行养护,在混凝土浇筑后12小时内对混凝土加以覆盖并浇水养护,在两个相邻的预制板15之间的钢承板11,通过预埋件顶部加工m16内螺纹孔,将m16配套螺杆通过固定于侧模上的钢承板11上的预留孔拧入预埋件内,依靠底模上的φ40
×
5mm圆饼状限位器13和m16螺杆实现预埋件的精准定位。
48.以上所述,仅为本发明较佳的具体实施方式,但本发明的保护范围并不局限于此,任何熟悉本技术领域的技术人员在本发明揭露的技术范围内,根据本发明的技术方案及其发明构思加以等同替换或改变,都应涵盖在本发明的保护范围之内。