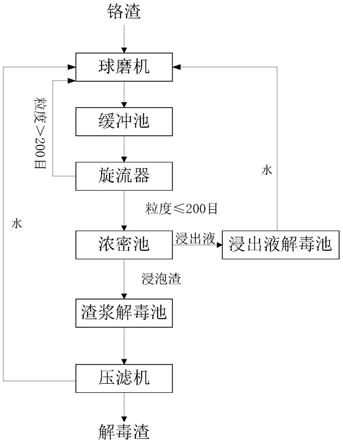
1.本发明涉及铬渣解毒技术领域,具体而言,涉及一种铬渣解毒方法。
背景技术:2.现有的铬渣湿法解毒方法是在铬渣研磨后加入废酸,将六价铬尽可能多的溶解于酸溶液中,然后添加还原剂,将六价铬还原成三价铬,再将三价铬稳定沉淀,使其达到无害化的过程。专利cn101816829a(一种铬渣解毒工艺)将铬渣研磨后进行酸浸还原反应后进行固液分离,分离后得到解毒铬渣。专利cn102614620b(一种碱性含六价铬废渣湿法解毒方法)将铬渣浆化后调节ph在7
‑
10之间,然后加入稳定剂和还原剂,将六价铬还原为三价铬,其能够长期稳定的存在于铬渣中。现有技术中还有将铬渣粉碎后清水浸泡,固液分离后加入氯化钡,然后过滤,固液分离后,将滤渣与水泥、砂石、碳酸钡、氯化钡混合压制成水泥砖块。
3.综上可知,现有技术大部分在铬渣研磨后加入酸,将水溶性六价铬和酸溶性六价铬浸出,后续加入还原剂将六价铬还原为三价铬后,再加入稳定剂将三价铬固化稳定化,此种技术方法需要消耗大量的酸,需要有废酸产生的企业为依托,在无产酸企业的地区增加了处理成本,同时三价铬稳定后仍有被再次氧化为毒性更高的六价铬风险,并没有彻底解决铬渣解毒的问题。也有少量现有技术采用清水浸泡研磨铬渣,但该技术无法将酸溶性铬全部溶出,进而需使用水泥固化滤渣,这样大大增加了滤渣产生量及处理滤渣的成本。
技术实现要素:4.本发明的主要目的在于提供一种铬渣解毒方法,以解决现有技术中存在成本较高、且无法彻底解决铬渣解毒的问题。
5.为了实现上述目的,根据本发明的一个方面,提供了一种铬渣解毒方法。方法包含以下步骤:s1,将铬渣和水混合后进行研磨处理,并在研磨处理的同时加入增溶剂,得到渣浆;s2,将渣浆进行分离筛选,得到粒度≤200目的渣浆;s3,将粒度≤200目的渣浆加入至浓密池中进行浸泡,得到浸出液及浸泡渣;s4,将浸出液加入至浸出液解毒池中进行第一稳定处理,得到沉淀产物;s5,将浸泡渣及沉淀产物加入至渣浆解毒池中进行第二稳定处理,得到解毒渣;其中,增溶剂为碳酸钠和/或碳酸氢钠;浸出液解毒池中投加第一稳定剂,第一稳定剂为氯化钡;渣浆解毒池中投加第二稳定剂,第二稳定剂为氯化钡和碳酸钡。
6.进一步地,增溶剂的投加量为铬渣重量的0.8~1.5%。
7.进一步地,向浓密池中注入水以进行浸泡,优选水和粒度≤200目的渣浆的重量比为(40~70):(1~3)。
8.进一步地,浸出液中铬酸钠的含量为0.26~1.28wt%;第一稳定剂的加入量为浸出液中铬酸钠重量的105~115%。
9.进一步地,浸泡渣中铬酸钠的含量为0.02~0.06wt%,铬酸钙的含量为0.9~1.49wt%;优选地,第二稳定剂中,氯化钡的加入量为浸泡渣中铬酸钠含量的105~110%,
碳酸钡的加入量为浸泡渣中铬酸钙含量的105~115%。
10.进一步地,浓密池中,浸出液和浸泡渣的重量比为(7~15):(3~5)。
11.进一步地,步骤s1中,渣浆的磨矿细度为200目;优选地,在将渣浆进行分离筛选时,方法还包括:将粒度>200目的颗粒筛选出来,将其返回步骤s1中继续研磨。
12.进一步地,研磨处理采用球磨机、管磨机、磨煤机、辊磨机或砂磨机。
13.进一步地,方法还包括步骤s6,将解毒渣进行脱水处理,得到的水返回步骤s1中循环利用;优选地,脱水处理采用板式压滤机、真空转鼓过滤机、盘式过滤机、水平胶带真空过滤机、浓密机或离心机。
14.进一步地,在将铬渣进行研磨处理后,方法还包括:先将渣浆加入至缓冲池中进行缓冲处理,然后再将渣浆加入至旋流器中进行分离筛选。
15.本发明通过解毒处理步骤间的层层协同递进,一方面,可以将更多的铬离子浸出溶于水中,然后对溶解在水中的六价铬离子进行稳定化处理,从而生成稳定的沉淀产物,相应地,铬渣中则存在较少的六价铬离子,进而降低了后续对铬渣中六价铬离子的稳定化处理成本。另一方面,本发明可以将原料铬渣中的水溶性及水难溶性六价铬离子更大限度地进行稳定化,从而实现高效铬渣解毒。综上,本发明无需加入酸,也无需将六价铬还原为三价铬(即不存在后续三价铬再次氧化为六价铬的问题)即可在成本较低的基础上生成稳定的无毒六价铬产物,彻底解决铬渣解毒的问题。而且,本发明的解毒方法流程更短,操作更简单。
附图说明
16.构成本技术的一部分的说明书附图用来提供对本发明的进一步理解,本发明的示意性实施例及其说明用于解释本发明,并不构成对本发明的不当限定。在附图中:
17.图1示出了本发明一种优选铬渣解毒过程的流程示意图。
具体实施方式
18.需要说明的是,在不冲突的情况下,本技术中的实施例及实施例中的特征可以相互组合。下面将参考附图并结合实施例来详细说明本发明。
19.正如背景技术部分所描述的,现有技术中存在成本较高、且无法彻底解决铬渣解毒的问题。为了解决这一问题,本发明提供了一种铬渣解毒方法,如图1所示,该方法包含以下步骤:s1,将铬渣和水混合后进行研磨处理,并在研磨处理的同时加入增溶剂,得到渣浆;s2,将渣浆进行分离筛选,得到粒度≤200目的渣浆;s3,将粒度≤200目的渣浆加入至浓密池中浸泡,得到浸出液及浸泡渣;s4,将浸出液加入至浸出液解毒池中进行第一稳定处理,得到沉淀产物;s5,将浸泡渣及沉淀产物加入至渣浆解毒池中进行第二稳定处理,得到解毒渣。其中,增溶剂为碳酸钠和/或碳酸氢钠;浸出液解毒池中投加第一稳定剂,第一稳定剂为氯化钡;渣浆解毒池中投加第二稳定剂,第二稳定剂为氯化钡和碳酸钡。
20.首先,本发明通过在铬渣研磨处理过程中同时加入增溶剂碳酸钠和/或碳酸氢钠,这样,一方面提供了弱碱性环境,使六价铬在渣浆中以cro
42
‑
形式存在,避免了以强氧化性cr2o
72
‑
形式存在,cr2o
72
‑
是一种有毒且致癌性的强氧化剂,被国际癌症研究机构划归为第一类至癌物质。另一方面,在研磨处理阶段同时加入铬渣、水及增溶剂,可以促使铬渣中更多
的cr2o3形成水溶性六价铬(主要是铬酸钠)和部分水难溶性六价铬(主要是铬酸钙),并更多的溶解在水中,使得铬离子在研磨过程中就开始浸出,提高了铬离子的浸出效率。同时,基于此,本发明增溶剂和铬渣的有效接触面积更大、混合效果更佳。
21.其次,本发明将研磨处理后的渣浆进行分离筛选,将粒度≤200目的渣浆筛选出来,并将其加入至浓密池中对其进行浸泡,进一步促使更多的铬酸钠及铬酸钙溶于水,铬离子浸出率更高。此时,浸出液中含有大量铬酸钠及部分铬酸钙,浸泡渣中含有少量铬酸钙及微量铬酸钠。然后,本发明将浓密池内的浸出液通过溢流方式加入至浸出液解毒池,并向浸出液解毒池中投加第一稳定剂氯化钡,从而对浸出液中大量的以铬酸钠形式存在的铬离子以及部分以铬酸钙形式存在的铬离子进行稳定化处理,得到沉淀产物铬酸钡及少量未反应的氯化钡固体。最后,将上述沉淀产物、少量未反应的氯化钡固体及上述浸泡渣一起加入至渣浆解毒池中,并向渣浆解毒池中投加第二稳定剂氯化钡和碳酸钡。其中,氯化钡主要针对浸泡渣中未浸泡出的微量铬酸钠进行稳定处理,碳酸钡主要针对浸泡渣内的少量铬酸钙进行稳定处理。
22.本发明通过上述步骤层层协同递进,一方面,可以将更多的铬离子溶于水中,然后对溶解在水中的六价铬离子进行稳定化处理,从而生成稳定的沉淀产物,相应地,铬渣中则存在较少的六价铬离子,进而降低了后续对铬渣中六价铬离子的稳定化处理成本。另一方面,本发明通过上述步骤层层协同递进,可以将原料铬渣中的水溶性及水难溶性六价铬离子更大限度地进行稳定化,从而实现高效铬渣解毒。综上,本发明通过上述操作,无需加入酸,也无需将六价铬还原为三价铬(即避免了后续三价铬再次氧化为六价铬的问题)即可在成本较低的基础上生成稳定的无毒六价铬产物,彻底解决铬渣解毒的问题。而且,本发明的解毒方法流程更短,操作更简单。
23.需说明的是,本发明铬渣中各成分占比为:sio2:25.7%~58.92%;cao:7.83%~26.92;mgo:2.30%~8.48%;fe2o3:4.51%~5.64%;al2o3:9.74~12.42%;cr2o3:0.02%~3.21%。
24.在一种优选的实施方案中,步骤s1中铬渣和水的重量比为(3~5):(7~10)。本发明在将研磨处理后的渣浆进行分离筛选时,将粒度>200目的颗粒筛选出来,将其返回步骤s1中继续研磨,粒度≤200目的渣浆则进入s3步骤中进行后续处理。步骤s1处理得到的渣浆中,六价铬的浸出浓度为17.82~176.24mg/l。
25.优选地,增溶剂的投加量为铬渣重量的0.8~1.5%,在此范围内六价铬达到最优浸出率范围,增溶剂的投加量低于此范围,六价铬浸出率大大下降,高于此范围时六价铬浸出率变化不明显,但成本更高。基于此,可以进一步促使更多的六价铬溶解到水中,对应地,铬渣中存在的六价铬量更少,进而降低了后续对铬渣中六价铬的稳定化处理成本,且稳定化处理效果更佳。在一种优选的实施方案中,渣浆中铬酸钠的含量为1.36wt%,铬酸钙的含量为1.49wt%。
26.基于进一步提高铬离子浸出率,进而达到更高效铬渣解毒的目的,优选向浓密池中注入水以进行浸泡,水和渣浆的重量比为(40~70):(1~3)。在一种优选的实施方案中,浓密池中,浸出液和浸泡渣的重量比为(7~15):(3~5)。
27.优选地,浸出液中铬酸钠的含量为0.26~1.28wt%;第一稳定剂的加入量为浸出液中铬酸钠重量的105~115%。这样,可以提高对浸出液中以铬酸钠形式存在的铬离子进
行稳定化处理的效率,进一步促使浸出液中的水溶性铬离子更大限度地转化为铬酸钡,以更稳定的沉淀产物的形式存在,稳定化处理效果更佳。
28.优选地,浸泡渣中铬酸钠的含量为0.02~0.06wt%,铬酸钙的含量为0.9~1.49wt%;第二稳定剂中,氯化钡的加入量为浸泡渣中铬酸钠含量的105~110%,碳酸钡的加入量为浸泡渣中铬酸钙含量的105~115%。这样,可以双管齐下,一方面促使浸泡渣中以铬酸钙形式存在的少量六价铬更大限度地转化为稳定产物铬酸钡,另一方面还可以对浸泡渣中残留的微量铬酸钠进行稳定化处理,从而可以更全面的将浸泡渣中的以各种形式存在的六价铬均实现稳定化处理要求。
29.在一种优选的实施方案中,在稳定化处理过程中充分考虑反应时间,每隔两个小时可对解毒池内的混合物进行检测,根据混合物中铬酸钠检测结果投加氯化钡,根据混合物中铬酸钙投加碳酸钡,直至检测结果达到《铬渣污染治理环境保护技术规范》(hj/t301
‑
2017)标准要求即停止稳定剂的投加,结束解毒。
30.优选地,步骤s1中,渣浆的磨矿细度为200目。基于此,该范围的磨矿细度更有利于提高后续工序的处理效率,可以更好地平衡后续浸出液及浸泡渣的稳定化处理效果,对原料铬渣的解毒效果更佳。
31.优选研磨处理采用球磨机、管磨机、磨煤机、辊磨机或砂磨机。基于此,不仅可以更高效地达到上述磨矿细度,还可以促使增溶剂和铬渣的混合更充分,增容效果更佳,更多的六价铬离子溶于水中,在研磨阶段即可达到很好的铬离子浸出效果。
32.优选地,方法还包括步骤s6,将解毒渣进行脱水处理,得到的水返回步骤s1中循环利用;优选地,脱水处理采用板式压滤机、真空转鼓过滤机、盘式过滤机、水平胶带真空过滤机、浓密机或离心机。基于此操作,本发明解毒过程中无二次废水产生,废水可实现循环利用,环保性更佳。
33.在一种优选的实施方案中,方法还包括步骤s7,将铬渣进行研磨处理后,上述方法还包括:先将渣浆加入至缓冲池中进行缓冲处理,然后再将渣浆加入至旋流器中进行分离筛选。
34.以下结合具体实施例对本技术作进一步详细描述,这些实施例不能理解为限制本技术所要求保护的范围。
35.实施例1
36.铬渣成分:铬渣中各成分占比sio2:58.92%;cao:26.92;mgo:8.48%;fe2o3:5.64%;al2o3:12.42%;cr2o3:3.21%。
37.对上述铬渣进行解毒:
38.将上述铬渣和水混合加入球磨机中进行研磨处理,并在研磨处理的同时加入增溶剂碳酸氢钠,得到渣浆。其中,铬渣和水的重量比为3:7;增溶剂的投加量为铬渣重量的0.8%;渣浆的磨矿细度为200目。
39.将上述渣浆加入至缓冲池中进行缓冲处理,然后再将渣浆通过旋流器进行分离筛选。将粒度≤200目的渣浆加入至浓密池中进行浸泡,浸泡8h,得到浸出液及浸泡渣;将粒度>200目的渣浆返回球磨机中继续研磨,至其粒度≤200目后再加入浓密池中进行浸泡。其中,浓密池中的水和渣浆的重量比为40:1;浸出液和浸泡渣的重量比为7:3;浸出液中铬酸钠的含量为1.2wt%;浸泡渣中铬酸钠的含量为0.06wt%,铬酸钙的含量为1.4wt%。浓密池
中处理后,铬离子浸出率为82%。
40.将浸出液加入至浸出液解毒池中,并向池中投加氯化钡进行第一稳定处理,得到沉淀产物铬酸钡。氯化钡的加入量为浸出液中铬酸钠重量的105%。
41.将浸泡渣及上述沉淀产物加入至渣浆解毒池中,并向池中投加氯化钡和碳酸钡进行第二稳定处理,得到解毒渣。此过程中氯化钡的加入量为浸泡渣中铬酸钠含量的105%,碳酸钡的加入量为浸泡渣中铬酸钙含量的105%。检测结果达到标准要求(hj/t301
‑
2017)。将上述解毒渣通过压滤机进行脱水处理,得到的水返回球磨机中再次循环利用。
42.实施例2
43.和实施例1的区别仅在于增溶剂的投加量为铬渣重量的1.5%。铬离子浸出率为88.5%。
44.实施例3
45.和实施例1的区别仅在于浓密池中的水和渣浆的重量比为70:3。铬离子浸出率为82.5%。
46.对比例1
47.和实施例1的区别在于:未加入任何增溶剂,铬离子浸出率为52%。
48.以上仅为本发明的优选实施例而已,并不用于限制本发明,对于本领域的技术人员来说,本发明可以有各种更改和变化。凡在本发明的精神和原则之内,所作的任何修改、等同替换、改进等,均应包含在本发明的保护范围之内。