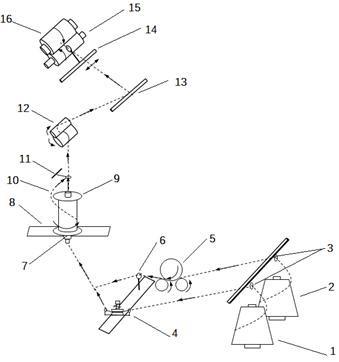
1.本发明属于纺纱技术领域,具体涉及一种包缠结构竹节纱的纺制方法及纺纱装置及竹节纱。
背景技术:2.竹节纱,顾名思义,是指具有类似竹节的粗细不匀外观的一种纱线。“竹节纱”,从本源上来看,是一种纱疵(纱线疵点),因为,在常规纺纱过程中,均匀度是纱线质量追求的品质指标之一,纺出的纱线产品,条干越均匀越好,如果纱线上存在规律的或不规律的竹节,则意味着纱线质量差。竹节纱作为一种纱疵,一般由纺纱过程中喂入纤维须条(粗纱或纤维条)粗细不匀、纺纱机牵伸装置或牵伸工艺缺陷、机构不良等因素导致。
3.但在生产实际中发现,由带有无规律分布竹节的纱线织制的织物,具有特殊的布面风格,并受到市场上部分消费者的青睐。于是生产中专门生产这种带有不规律分布竹节的纱线,仍称为“竹节纱”,且作为一种花式纱线品类,用于开发具有粗犷风格的面料。
4.目前,竹节纱主要在传统环锭细纱机上生产,在转杯纺、喷气涡流纺等其它纺纱设备上也可以加工。无论采用何种纺纱设备,竹节纱纺制的基本原理相似,都是要增加竹节纱控制装置,通过控制纤维须条喂入速度或牵伸装置牵伸倍数的随机变化,在纱线上产生节长(长度)、节距(间距)不同的竹节。以经典的环锭纺竹节纱为例,通过在设备上加装“竹节纱装置”(环锭细纱机可选配装置),可以控制牵伸装置的中、后罗拉随机变速(增速),从而改变牵伸装置的牵伸倍数,使牵伸后的纱线上产生长度和间距不同的竹节(牵伸倍数变小,输出纱线变粗,牵伸倍数恢复原大小,输出纱线又恢复原粗细)。竹节的长度、节距,以及竹节的粗细都可以通过设置控制参数进行调节。
5.常规竹节纱的技术特征,是竹节的节长、节距随机变化,才能在织物表面形成均匀的竹节分布,如果节长、节距均相同,则在织造时,竹节会在织物表面形成规律排列,形成条影,破坏想要获得的竹节均匀分布的布面效果。理论上也可以通过规律排列的竹节,在织物表面形成图案,但考虑到织造时的控制难度,以及可能发生的纱线断头(导致竹节形成的图案对不上),在实际应用中很难实现。
6.2段彩纱段彩纱,也属于花式纱线的一个品类(一种花色纱线),其特征是沿纱线长度方向的不同片段,呈现不同的颜色,用段彩纱织成的织物,具有区别于均色(染色)织物的特殊色彩和图案外观。
7.传统的段彩纱采用经过练漂后的白纱分段染色(段染)加工而成,因工艺复杂、色段长度和间隔可控性差而基本淘汰。
8.目前市场上的段彩纱产品多为采用色纺(纤维染色后再纺纱)技术纺制的短纤段彩纱,其基本技术方法是,采用2根及以上不同颜色的纤维须条喂入同一个纺纱单元的牵伸系统,不同颜色纤维须条的喂入速度可以分别进行单独控制(牵伸装置的后罗拉或中、后罗拉分节单独传动,以分别喂入不同颜色的纤维须条),并保证总的喂入定量(线密度)不变,
当不同颜色纤维须条的喂入比例发生变化时,输出纤维须条中不同颜色纤维的比例即发生变化,经加捻后形成的纱线,不同片段即呈现不同的颜色。(在纱线长度方向的不同片段上,用不同比例的不同颜色纤维,拼出不同的混色效果。)以不用颜色的有色纱线(长丝纱或短纤纱)为原料,进行复合加工,也可以加工具有段彩外观的复合纱。如采用2根及以上不同颜色的纱线组成多芯纱,利用空心锭包覆纺纱机进行包缠复合,由于外包缠纱对芯纱进行包缠时张力对芯纱产生的假捻效应,以及空心锭本身高速回转对芯纱的假捻效应,使多根并合的异色芯纱产生残留捻回而使不同片段呈现不同颜色(如一根黑色和一根白色纱线并在一起,扭转加捻后会呈现一段黑一段白),形成段彩外观,并经外包缠纱的包缠得到固定。(这一技术,本技术人已获发明专利授权。)类似竹节纱的竹节分布要求,段彩纱的技术特征,也要求各色段的长度和间隔随机变化而不能相等,这是本领域的公知常识。
9.3段彩竹节纱段彩竹节纱是结合段彩纱和竹节纱两种外观特征的花式纱线,即在纱线长度方向上分布着节长、节距不同的粗节(竹节),且粗节的颜色与正常粗细纱段的颜色不同。
10.目前段彩竹节纱的纺制方法有两种。第一种纺制方法:基纱粗纱由牵伸装置的中罗拉恒速、连续喂入,异色饰纱粗纱由后罗拉喂入,并与基纱粗纱并合在一起向前喂入。产生异色竹节的方法是,饰纱粗纱的喂入是断续的(后罗拉时停时转,由专门的控制机构控制)。这样,当饰纱粗纱喂入一段后停止喂入,就会在牵伸输出后加捻成纱上形成一个异色竹节。将后罗拉分节并分别单独传动,可以增加饰纱粗纱的喂入通道,增加产生竹节的颜色。
11.另一种产生彩色竹节的方法(方法二),是在前述等线密度短纤段彩纱加工技术的基础上,取消对不同颜色粗纱喂入总定量相同的限制,这样,增大不同颜色粗纱的喂入速度时,不但会改变不同颜色粗纱的比例,还会增大总的喂入定量,因而产生颜色变化的竹节。
12.方法一和方法二的主要区别,在于正常纱段的颜色,方法一纺制的段彩竹节纱,正常纱段由基纱牵伸加捻而成,为单一颜色;方法二中,正常纱段也由几种连续喂入的不同颜色的粗纱经牵伸、加捻混色而成,竹节部分是由于混色比例和粗细差异而呈现与正常纱段不同的颜色。
13.由于改变纤维须条喂入速度时喂入装置加速和减速存在惯性,因此由短纤维须条纺制而成的竹节纱,竹节呈两端细、中间粗的形态。
14.竹节纱作为织制特殊织物风格的花式纱线产品,因其织物风格受到部分消费者的喜爱,一直在纱线细分市场占有一定的份额,用于服饰面料或家用纺制品的开发。
15.如前所述的现有纺制竹节纱的技术,基本均以短纤维原料制成的纤维须条(条子或粗纱)为喂入原料形态,通过控制喂入速度的变化,间歇改变纤维须条的牵伸倍数,因而改变输出纱条的定量,产生竹节纱段,纺制具有竹节外观的纱线。通过调整牵伸倍数的变量大小、变速持续时间和变速时间间隔,可以调整竹节的粗细、节长和节距,是一种成熟的竹节纱生产技术,可用于各种原料短纤竹节纱及其复合纱的加工。这种竹节纱产品从其结构上,属于一种短纤纱。
技术实现要素:16.针对现有技术存在的不足,本发明的目的在于提供一种包缠结构竹节纱的纺制方法及纺纱装置及竹节纱。
17.为实现上述目的,本发明提供了如下技术方案:一种包缠结构竹节纱的纺制方法,其利用空心锭机构将主芯纱及超喂芯纱由外包缠纱螺旋线状包缠复合形成包缠结构竹节纱,所述主芯纱采用消极喂入方式,主芯纱从主芯纱纱筒上退绕下来,穿过位于纱筒中心线上方的导纱钩,转向穿过弹簧式张力装置,并从空心锭的中心管下端进入,从上端引出,所述超喂芯纱与主芯纱保持一定间距,采用积极喂入方式喂入,超喂芯纱从超喂芯纱纱筒上退绕下来,穿过位于纱筒中心线上方的导纱钩,进入由3根品字形配置的喂入罗拉组成的超喂芯纱喂入装置,穿过超喂芯纱导纱钩,与主芯纱之间形成夹角β,并一起进入空心锭的中心管的下端,所述超喂芯纱在空心锭的假捻作用下缠绕在主芯纱上,并间断产生往复折叠缠绕动作,形成竹节,附有竹节的芯纱并合体进入空心锭的中心管的下端,附有竹节的芯纱并合体由空心锭中心管的上端引出,在会合导纱钩处,受到随空心锭一起高速回转的锭管上的外包缠纱的螺旋线状包缠,形成包缠复合结构的竹节纱,其中所述超喂芯纱的喂入速度大于主芯纱的喂入速度。
18.所述超喂芯纱的颜色与主芯纱相同或不同。
19.所述超喂芯纱为一根或两根,且为两根时,位于主芯纱的两侧。
20.所述主芯纱及超喂芯纱与在空心锭高速转动下产生假捻作用,并形成捻回传递效应,在捻回传递效应作用下,超喂芯纱以主芯纱为轴,以螺旋线状缠绕到主芯纱上,且重复以下过程:超喂芯纱缠绕点相对慢速向主芯纱喂入点运动
→
缠绕角增大,超喂芯纱超喂长度积累、张力减小、涌动加剧
→
缠绕角瞬间超过90
°→
缠绕点运动瞬间倒向,快速向假捻点方向运动,消耗超喂芯纱的积累超喂长度
→
缠绕角减小、超喂芯纱张力增大
→
缠绕点运动再次倒向,恢复慢速向主芯纱喂入点运动,每次循环形成一个超喂芯纱往复折叠缠绕段,在已缠绕了超喂芯纱的主芯纱上形成一个竹节。
21.采用一根超喂芯纱一次包缠时产生的包缠复合结构的竹节纱,其竹节所在位置的线密度与正常纱段的线密度之比为(n
z
+3n
c
+n
w
)/(n
z
+n
c
+n
w
)=1+[2n
c
/(n
z
+n
c
+n
w
)],其中n
c
为超喂芯纱的线密度,n
z
为主芯纱的线密度,n
w
为外包缠纱的线密度。
[0022]
通过改变超喂芯纱的超喂比对竹节间距进行调节,通过改变主芯纱与超喂芯纱的间距对竹节长度和竹节间距进行调节。
[0023]
一种基于上述包缠结构竹节纱的纺制方法的纺纱装置,其包括:主芯纱喂入装置,用于消极喂入主芯纱,其包括依次设置的主芯纱纱筒、导纱钩及弹簧式张力装置;至少一个超喂芯纱喂入装置,设置在所述主芯纱喂入装置的一侧,用于积极喂入
超喂芯纱,其包括依次设置的超喂芯纱纱筒、导纱钩及超喂芯纱喂入装置;空心锭机构,用于产生假捻作用,并使喂入的超喂芯纱以主芯纱为轴,以螺旋线状缠绕到主芯纱上,并使得超喂芯纱反复往复折叠缠绕在主芯纱上形成竹节,并利用外包缠纱将竹节缠绕而固着于主芯纱上,形成包缠复合结构的竹节纱;管纱,用于卷绕纺制后形成的竹节纱,其中经由主芯纱喂入装置引出的主芯纱与经由超喂芯纱喂入装置引出的超喂芯纱呈一定夹角β进入空心锭机构的中心管中。
[0024]
一种纱/纱复合包缠结构竹节纱,主芯纱与超喂芯纱颜色一致时,通过上述的包缠结构竹节纱的纺制方法制成。
[0025]
一种包缠结构混色段彩竹节复合纱,主芯纱与超喂芯纱的颜色不一致时,通过上述的包缠结构竹节纱的纺制方法制成。
[0026]
本发明的有益效果:提供了一种全新的以纱线为原料,利用空心锭包缠(包覆)纺纱技术(行业中称为“机包”),纺制包缠复合结构竹节纱的技术。
[0027]
假捻效应的波动,决定竹节形成过程的波动性,再加上超喂芯纱在喂入惯性作用下向前涌动的非受控性,使竹节长度与竹节间距在一定范围内非受控、随机波动,满足了竹节纱对竹节长度与竹节间距不能相同的要求,使竹节在布面上分布均匀,不会形成条影图案。
附图说明
[0028]
图1为本发明的包缠复合竹节纱纺制工艺原理示意图。
[0029]
图2为本发明的空心锭中心管下端对芯纱的假捻作用示意图。
[0030]
图3a、图3b、图3c为竹节形成过程的示意图图4为实施例一的复合竹节纱纱外观示意图。
[0031]
图5为实施例一中不同超喂比纺制的竹节纱纱卡示意图,(a)超喂比1.2,(b)超喂比1.3,(c)超喂比1.4,(d)超喂比1.5。
[0032]
图6为实施例二中不同主芯纱与超喂芯纱间距纺制的竹节纱纱卡示意图,(a)间距65 mm,(b)间距90 mm,(c)间距125 mm。
[0033]
图7为实施例三中改变粗细比后的复合纱纱卡示意图。
[0034]
图8为实施例四的管纱外观和黑、白纱卡示意图,(a)外观图,(b)白纱卡,(c)黑纱卡,(d)黑纱卡局部。
[0035]
图9为实施例五的管纱外观和黑、白纱卡示意图,(a)外观图,(b)白纱卡,(c)黑纱卡,(d)黑纱卡局部。
[0036]
图10为实施例六的管纱外观和黑、白纱卡示意图,(a)外观图,(b)白纱卡,(c)黑纱卡,(d)黑纱卡局部。
[0037]
图11为实施例七的管纱外观和黑、白纱卡示意图,(a)外观图,(b)白纱卡,(c)黑纱卡,(d)黑纱卡局部。
具体实施方式
[0038]
下面将结合本发明实施例中的附图,对本发明实施例中的技术方案进行清楚、完
整地描述,显然,所描述的实施例仅仅是本发明的一部分实施例,而不是全部的实施例。基于本发明中的实施例,本领域普通技术人员在没有作出创造性劳动前提下所获得的所有其他实施例,都属于本发明保护的范围。
[0039]
需要说明,本发明实施例中所有方向性指示(诸如上、下、左、右、前、后
……
)仅用于解释在某一特定姿态(如附图所示)下各部件之间的相对位置关系、运动情况等,如果该特定姿态发生改变时,则该方向性指示也相应地随之改变。
[0040]
在本发明中,除非另有明确的规定和限定,术语“连接”、“固定”等应做广义理解,例如,“固定”可以是固定连接,也可以是可拆卸连接,或成一体;可以是机械连接,也可以是连接;可以是直接相连,也可以通过中间媒介间接相连,可以是两个元件内部的连通或两个元件的相互作用关系,除非另有明确的限定。对于本领域的普通技术人员而言,可以根据具体情况理解上述术语在本发明中的具体含义。
[0041]
如图1所示,本发明还公开了一种纺纱装置,基于上述纺制方法进行竹节纱的纺制:其包括:主芯纱喂入装置,用于消极喂入主芯纱,其包括依次设置的主芯纱纱筒(1)、导纱钩及弹簧式张力装置4;至少一个超喂芯纱喂入装置,设置在所述主芯纱喂入装置的一侧,用于积极喂入超喂芯纱,其包括依次设置的超喂芯纱纱筒2、导纱钩及超喂芯纱喂入装置5;空心锭机构,用于产生假捻作用,并使喂入的超喂芯纱以主芯纱为轴,以螺旋线状缠绕到主芯纱上,并使得超喂芯纱反复往复折叠缠绕在主芯纱上形成竹节,并利用外包缠纱将竹节缠绕而固着于主芯纱上,形成包缠复合结构的竹节纱;管纱,用于卷绕纺制后形成的竹节纱,其中经由主芯纱喂入装置引出的主芯纱与经由超喂芯纱喂入装置引出的超喂芯纱呈一定夹角β进入空心锭机构的空心锭中。
[0042]
所述空心锭机构与纱管之间依次设有会合导纱钩11、引纱辊12、导纱杆13、横动导纱器14及卷绕辊15。
[0043]
本发明公开了一种包缠结构竹节纱的纺制方法,其利用空心锭机构将主芯纱及超喂芯纱由外包缠纱螺旋线状包缠复合形成包缠结构竹节纱,所述主芯纱采用消极喂入方式,主芯纱从主芯纱纱筒1上退绕下来,穿过位于纱筒中心线上方的导纱钩3,其中导纱钩用于引导主芯纱沿纱筒轴向退绕,转向穿过弹簧式张力装置4,由弹簧式张力装置的喂入瓷眼进入,从上下两片夹片间穿过,在从输出瓷眼引出,张力夹片由弹簧施加一定的压力,主芯纱通过两张力夹片之间时要克服夹片作用在主芯纱上的摩擦力,给与主芯纱施加一定的张力,从弹簧式张力装置引出的主芯纱,从空心锭7的中心管下端进入,从上端引出,其中主芯纱的运行动力来自于引纱辊12的主动牵引。
[0044]
所述超喂芯纱与主芯纱保持一定间距,采用积极喂入方式喂入,超喂芯纱从超喂芯纱纱筒2上退绕下来,穿过位于纱筒中心线上方的导纱钩3,进入由三根呈品字形配置的喂入罗拉组成的超喂芯纱喂入装置5,,喂入罗拉采用金属罗拉或经抗静电处理的橡胶辊,超喂芯纱在喂入罗拉的握持下向前积极喂入(本技术利用空心锭包覆机原有的两根弹力纤维喂入辊,再加上一根上罗拉,骑跨在两根喂入辊上,组成三罗拉喂入装置,也可以采用一上一下两根喂入罗拉组成喂入装置),穿过超喂芯纱导纱钩6,与主芯纱之间形成夹角β,并
一起进入空心锭7的中心管的下端,并从上端引出,所述超喂芯纱在空心锭的假捻作用下缠绕在主芯纱上,并间断产生往复折叠缠绕动作,形成竹节,附有竹节的芯纱并合体进入空心锭的中心管的下端,附有竹节的芯纱并合体由空心锭中心管的上端引出,在会合导纱钩处,受到随空心锭一起高速回转的锭管上的外包缠纱的螺旋线状包缠,形成包缠复合结构的竹节纱,其中所述超喂芯纱的喂入速度大于主芯纱的喂入速度,二者之间的喂入线速度比为超喂比。
[0045]
如图2所示,由于空心锭在电机驱动的锭带的传动下高速回转(生产中实用速度在13000
‑
15000r/min),因此其中心管是高速回转的,主芯纱与超喂芯纱组成的双芯纱与空心锭中心管中心线成一定夹角α进入中心管,双芯纱便会在中心管下端形成一定的包围弧度,并在芯纱张力作用下紧贴在中心管的下端面上,高速回转的中心管下端弧面就会对双芯纱产生截面切向的摩擦力,使芯纱产生同向回转,因而产生假捻作用(类似本行业中,翼锭粗纱机上,高速回转的锭翼顶端对进入锭翼顶孔的粗纱的切向摩擦力产生的假捻作用)。芯纱在摩擦假捻作用下回转,产生的捻回由中心管下端向芯纱喂入方向传递(与芯纱运动方向相反)。
[0046]
由于假捻作用的捻回传递效应(由假捻点向喂入点传递),张力很小的超喂芯纱会以主芯纱为轴,以螺旋线状缠绕到主芯纱上,而且由于主芯纱与超喂芯纱之间存在一夹角,缠绕运动形成的沿主芯纱轴向的分速度,使超喂芯纱对主芯纱的缠绕点向主芯纱喂入点运动,超喂芯纱与主芯纱之间的夹角β随缠绕点向主芯纱喂入点运动而不断增大。螺旋线状缠绕对超喂芯纱的超喂长度有消耗作用。
[0047]
如果超喂芯纱的超喂比较小,当缠绕点向主芯纱喂入点运动到一定位置时,单位时间内缠绕作用消耗的超喂芯纱长度与超喂芯纱的超喂长度相匹配而达到平衡,缠绕点位置处于相对稳定状态,且由于超喂长度被消耗,超喂芯纱也保持相对稳定的张力。
[0048]
当超喂芯纱的超喂比较大时,单位时间内超喂芯纱对主芯纱螺旋线状缠绕额外消耗的超喂芯纱长度,已不能消耗超喂芯纱的超喂长度,超喂芯纱超喂长度不断积累,导致超喂芯纱的张力随缠绕点向主芯纱喂入点运动而不断减小,超喂芯纱与主芯纱夹角β不断增大,超喂芯纱对主芯纱缠绕螺旋线的捻回角也不断增大。当缠绕点运动到某一位置时,缠绕角β超过90
°
。
[0049]
发生缠绕角β超过90
°
的最根本原因是超喂芯纱的超喂和缠绕角β随缠绕点运动而不断增大,在超喂芯纱主动向前喂入和芯纱并合体向前运动的惯性作用下,使处于缠绕点和超喂芯纱喂入点(超喂芯纱导纱钩)之间的超喂芯纱段因超喂长度的不断积累产生向前涌动且涌动不断加剧,当缠绕角很大时,超喂芯纱段的不断加剧的向前涌动即很容易导致缠绕角β瞬间超过90
°
。缠绕角β超过90
°
,也可在主芯纱喂入点处输出瓷眼的机械作用下发生,一旦缠绕点运动到进入输出瓷眼,即在输出瓷眼的机械束缚作用下,使缠绕角瞬间超过90
°
。
[0050]
缠绕角一旦超过90
°
,超喂芯纱的缠绕方向即发生改变,由于此时超喂芯纱积累的超喂长度较大,张力很低,缠绕点快速向反方向运动,消耗掉超喂芯纱超喂长度,超喂芯纱张力增大,同时使缠绕角减小;当反向缠绕的缠绕角减小到一定程度,超喂芯纱的超喂长度被充分消耗,超喂芯纱张力增大到一定程度,超喂芯纱的缠绕方向再次发生改变,缠绕点恢
复向主芯纱喂入点运动,并恢复原来缠绕速度。这样一个“缠绕点运动倒向、快速反向运动
‑
缠绕点倒向、慢速正向运动”的缠绕运动往复倒向,就会在已缠绕了超喂芯纱的主芯纱上,附加一个超喂芯纱的折叠缠绕纱段,并由此形成一个竹节。而后,会继续重复以下过程:超喂芯纱缠绕点相对慢速向主芯纱喂入点运动
→
缠绕角增大,超喂芯纱超喂长度积累、张力减小、涌动加剧
→
缠绕角瞬间超过90
°→
缠绕点运动瞬间倒向,快速向假捻点方向运动,消耗超喂芯纱的积累超喂长度
→
缠绕角减小、超喂芯纱张力增大
→
缠绕点运动再次倒向,恢复慢速向主芯纱喂入点运动。
[0051]
以上过程不断循环,每次循环形成一个超喂芯纱往复折叠缠绕段,在已缠绕了超喂芯纱的主芯纱上形成一个竹节。
[0052]
即缠绕点在以较慢的速度到达主芯纱喂入点附近时,缠绕方向倒向,快速反向缠绕一定长度,再倒向并恢复慢速缠绕,在已缠绕超喂芯纱的主芯纱上折叠缠绕形成竹节。竹节是由超喂芯纱往复折叠缠绕形成。进入空心锭中心管下端的芯纱并合体,由两种纱段相间组成:一种是缠绕了超喂芯纱的主芯纱段(正常纱段);一种是在缠绕了超喂芯纱的主芯纱上再附加超喂芯纱折叠段的竹节纱段(竹节纱段)。
[0053]
其中竹节的形成过程如图3所示,图3a中,(a)~(c):超喂芯纱对主芯纱缠绕(第一次缠绕),且缠绕点向主芯纱喂入点运动,缠绕角不断增大,直至接近主芯纱张力装置输出瓷眼;图3b中,(d)缠绕方向瞬间倒向,超喂芯纱快速反向缠绕(第二次缠绕);图3b和图3c中,(e)~(g)缠绕方向再次倒向,恢复缠绕方向和速度,缠绕点向主芯纱喂入点运动(第三次缠绕);图3c中,(h)~(i)完成折叠缠绕纱段的缠绕运动,缠绕点向主芯纱喂入点运动,进入下一竹节形成循环。
[0054]
根据假捻理论,当纱线经过假捻点后,会发生解捻。即带有竹节(竹节)段的芯纱经过空心锭中心管下端后(进入中心管),即进行反向加捻,反向加捻捻度与已加捻度相同(假捻点两侧所加捻度相同、捻向相反)。对于正常纱段,会因解捻作用而解除超喂芯纱对主芯纱的缠绕状态,恢复基本无捻状态。对于竹节纱段,由于是超喂芯纱两次折叠缠绕在已经缠绕了超喂芯纱的主芯纱上,形成超喂芯纱对主芯纱的三重缠绕结构,且每次缠绕的捻度均不同(缠绕速度和缠绕直径不同),形成复杂的分层缠绕加捻结构。在经过假捻点后进行解捻时,在整体反向加捻作用下,不能进行解捻,而是形成更为复杂的分层加捻结构(最内缠绕层解捻,第二层和第三层解捻后反向加捻),不能回复基本无捻状态,因而使竹节纱段依旧能够以一定的缠绕结构附着在芯纱上。
[0055]
芯纱并合体走出空心锭中心管的上端后,在会合导纱钩11处,受到随空心锭7一起高速回转的锭管9上的外包缠纱10的螺旋线状包缠(空心锭7装在固定龙筋8上,由电机驱动的锭带统一传动)。竹节经外包缠纱螺旋线状包缠而固着于芯纱并合体上,即形成包缠复合结构的竹节纱。
[0056]
竹节纱经引纱辊12引出,绕过导纱杆13导向,再穿过横动导纱器14上的导纱瓷眼,在横动导纱器往复横动的引导下,卷绕到被卷绕辊15摩擦传动的管纱16上,完成卷绕成形。本技术中芯纱并合体喂入须与空心锭中心管的轴线呈一定夹角α,以在中心管下端形成一定的包围弧度,当空心锭高速回转时,中心管下端弧面就会对芯纱产生切向摩擦力,因而产
生假捻作用。假捻作用会使芯纱产生回转,回转产生的捻回由假捻点向芯纱喂入点传递,因此改变芯纱与中心管轴线的夹角,可改变假捻作用效果(假捻捻度大小),该参数是本技术的重要工艺参数,但因改变该参数需要改变机械机构的相对位置,实际操作性较差。本技术对该夹角的技术要求是不小于30
°
,以满足对假捻效果的技术要求。假捻点至主芯纱喂入点的之间区域,是捻回传递、竹节形成的区域,对节长和节距也会有影响,但由于改变此间距涉及设备机构位置的调整,一经确定不做调整。综合考虑设备机构安排、便于操作和假捻捻回传递的损失,二者之间的长度应控制在150 mm
‑
250 mm。
[0057]
芯纱由主芯纱和超喂芯纱组成,主芯纱采用消极喂入方式,通过引纱辊的牵引作用实现向前喂入,并通过张力装置施加一定张力;超喂芯纱采用积极喂入方式,由喂入装置积极喂入,喂入速度可调,且大于主芯纱速度,形成超喂,且应达到一定超喂比,喂入位置与主芯纱保持一定间距,使超喂芯纱在假捻捻回传递作用下缠绕到主芯纱上。主芯纱与超喂芯纱的喂入方式、喂入速度与喂入位置配置,也是本技术关键之一。纱线作为粘性弹性材料,张力大小会影响其扭转性能。主芯纱张力调整依据,是如前所述的“保证外包缠纱对芯纱的正常包缠作用实现”时的最低张力,保持芯纱张力在较低水平,加捻作用强,假捻捻度大,有利于本技术方案的实现。
[0058]
超喂芯纱在加捻捻回传递(回转)作用下缠绕到主芯纱上,由于超喂芯纱和主芯纱喂入位置和超喂比的配置,导致缠绕点由假捻点向主芯纱喂入点运动,并因以下作用机理产生竹节(竹节):超喂芯纱缠绕点向主芯纱喂入点运动
→
缠绕角增大,超喂芯纱超喂长度积累、张力下降、涌动加剧
→
缠绕角超过90
°→
缠绕点运动瞬间倒向,快速向假捻点方向运动,消耗超喂芯纱的超喂积累长度
→
缠绕角减小、超喂芯纱张力增大
→
缠绕点再倒向,恢复慢速向主芯纱喂入点运动。以上作用过程不断循环,每循环一次,产生一个竹节(竹节)。
[0059]
由于以上竹节特殊的形成过程,竹节部分实际上是由超喂芯纱的三次缠绕形成,由于每次缠绕的缠绕直径和缠绕运动速度不同,形成了复杂的分层缠绕结构。附加了竹节后的芯纱经过假捻点后,经退捻时的反向加捻作用,不能解捻,而是形成因解捻作用形成另一种复杂的缠绕结构,竹节部分能够继续附着在主芯纱和超喂芯纱组成的复合芯纱上,并经过空心锭机构的外包缠纱包缠作用,将竹节部分缠绕固定,形成稳定的纱线结构。竹节由超喂芯纱往复折叠缠绕形成,使整个竹节纱段各部分的粗细一致,这与改变牵伸倍数纺制的短纤竹节纱不同(由于牵伸装置的运动惯性,使竹节段两端比中间细),这是本技术方案纺制的竹节纱线的又一特征。
[0060]
采用一根超喂芯纱一次包缠时产生的包缠复合结构的竹节纱,其竹节处线密度与正常纱段的线密度之比(简称粗细比)计算如下。所述竹节所在位置的线密度与正常纱段的线密度之比为(n
z
+3n
c
+n
w
)/(n
z
+n
c
+n
w
)=1+[2n
c
/(n
z
+n
c
+n
w
)],其中n
c
为超喂芯纱的线密度,n
z
为主芯纱的线密度,n
w
为外包缠纱的线密度,为竹节处的线密度,为正常纱段的线密度。通过调整主芯纱、超喂芯纱和外包缠纱的线密度大小,可以调整竹节的粗细比,粗细比越大,竹节越显著。
[0061]
如果采用两组超喂芯纱形成双色竹节,则粗细比计算公式变为(n
z
+3n
c1
+n
c2
+n
w
)/(n
z
+n
c1
+n
c2
+n
w
)=1+[2n
c1
/(n
z
+n
c1
+n
c2
+n
w
)],其中n
c1
,n
c2
分别为两根超喂芯纱的线密度,由此可以看出,粗细比会有所降低,竹节部分的差异显著性会有所减弱。
[0062]
按本方案纺制的竹节纱的极限线密度比为3(此时主芯纱和外包缠纱线密度为0),
在实用中,线密度比是小于3的(小于常规短纤竹节纱的线密度比调控范围),属于一种“细竹节纱”。
[0063]
根据前述竹节形成原理,改变超喂芯纱的超喂比,单位时间内超喂芯纱的超喂长度积累增大,可改变单位时间内竹节形成循环的频次,因而可以改变竹节间距;改变芯纱间距,可以改变缠绕点与超喂芯纱喂入点之间超喂芯纱段的长度和包缠角度及其变化速率,因而改变储存超喂长度的大小和缠绕方向变换频次,从而改变竹节长度和竹节间距的大小。通过改变超喂芯纱超喂比改变竹节间距,通过改变芯纱间距改变竹节长度(节长)和竹节间距,是构成本技术方案的又一技术特征。在技术方案实施时,可分别或同时调整两个核心工艺参数,使节长和节距达到设计要求或满足客户要求。
[0064]
根据前述成纱原理,超喂芯纱通过缠绕运动方向的折返产生竹节,为保证竹节外观成形规整,要求超喂芯纱具有一定的柔软度,这样在竹节段两端弯曲折叠处(特别是第二次倒向时)才不会因超喂芯纱弯曲刚度大形成较大的环圈,影响竹节外观。这是本技术方案的技术要求之一。一种纱线是否适合作为超喂芯纱产生竹节,需要具有合适的弯曲性能和弹性,可通过纺纱试验进行尝试,如果不能形成稳定的往复折叠缠绕律动,或竹节两端产生的弯折环圈超出要求(下游客户的要求),则不能作为超喂芯纱,但不排除两端环圈能形成特殊风格,并为客户所接受。对于具有加捻结构的纱线(长丝纱或短纤纱,特别是短纤纱),尤其是残余扭矩较大的加捻结构纱线,由于易在张力较低时发生扭结,不易形成相对稳定的往复折叠缠绕律动,破坏竹节外形,是否适于作为超喂芯纱,需要通过纺纱试验进行判断。
[0065]
根据技术原理,对主芯纱和外包缠纱的技术要求,没有品种、规格方面的限制,只要能承受包缠复合加工基本的强力要求即可,一般常用纱线均可满足,可根据产品的性能要求与竹节粗细比等要求综合考虑、选配。
[0066]
外包缠纱对复合芯纱的包缠捻度(单位长度芯纱缠绕外包缠纱的圈数,取决于空心锭转速和引纱辊引纱速度),根据外包缠纱对竹节段的固定效果综合考虑确定,如果包缠捻度太低,外包缠纱对竹节段的固定效果差,复合纱在受到摩擦力作用时竹节段容易变形、起毛,且竹节两端也容易翘起(特别是第二次倒向端)。建议包缠捻度不低于600 捻/m。但捻度过大又会影响加工效率(增大捻度通过减小引纱速度实现,减小引纱速度,产量下降),因此,为增大竹节的包缠固结效果,也可采用两次包缠(工厂所谓的“双包”),此时,前述计算粗细比的计算方法须进行必要调整,在分子、分母中均应加上第二次包缠所用外包缠纱的线密度。竹节的包缠固结工艺,作为单一环节是熟悉本领域的公知常识,但也是构成本技术方案的技术环节之一,因为包缠工艺的选择不再是考虑包覆效果或复合结构,而要考虑对竹节的固结效果。
[0067]
当采用短纤纱作为主芯纱时,短纤纱本身带有一定捻度,此时,空心锭回转方向(包缠捻向)须与主芯纱捻向相匹配。由于空心锭中心管下端使竹节形成区芯纱产生假捻的捻向与空心锭包缠捻向相反,而如果竹节形成区产生并传递的假捻捻回与主芯纱自身捻度的捻向相反,就会导致对主芯纱解捻,进而断头。这就要求,采用有捻短纤纱作为主芯纱时,空心锭包缠捻向必须与主芯纱捻向相反,这样,竹节形成区产生并传递的假捻捻回的捻向就与主芯纱捻向一致,避免主芯纱在假捻捻回作用下解捻、断头。也就是说,采用有捻短纤纱作为主芯纱,如果主芯纱带有捻度的捻向为z捻,则空心锭包缠捻向须选择s捻。反之亦
然。
[0068]
芯纱与空心锭中心管下端的假捻效应源自空心管下端面对芯纱的截面周向的切向摩擦,而这种摩擦作用是非受控作用,摩擦效应会随着芯纱表面性质、芯纱直径、芯纱张力等的变化而变化,以下因素决定了假捻点处的假捻效应处于不断的波动、变化中:正常芯纱段上超喂芯纱对主芯纱的螺旋线缠绕结构形成不均匀表面结构;竹节芯纱段上超喂芯纱的往复缠绕结构形成不均匀的表面结构;竹节纱段与正常纱段直径的差异;主芯纱张力的波动;主芯纱线密度的变异;超喂芯纱线密度的变异,等等。假捻效应的波动,决定竹节形成过程的波动性,再加上超喂芯纱在喂入惯性作用下向前涌动的非受控性,使竹节长度与竹节间距在一定范围内非受控、随机波动。这恰恰满足了竹节纱对竹节长度与竹节间距不能相同的要求,使竹节在布面上分布均匀,不会形成条影图案。
[0069]
而本技术中的超喂芯纱可以根据颜色是否与主芯纱一致,可以获得不同品种的竹节纱,当两者颜色一致时可以纺制获得纱/纱复合包缠结构竹节纱,而当两者颜色不一致时可以纺制获得包缠结构混色段彩竹节复合纱。
[0070]
其中纱/纱复合包缠结构竹节纱的实施例如下:实例一:采用不同超喂比(超喂芯纱喂入线速度与主芯纱喂入线速度之比),纺制包缠复合竹节纱。
[0071]
具体纺纱工艺参数如下:主芯纱和超喂芯纱均选用涤纶dty(拉伸变形丝,低弹丝)长丝纱,规格为100d/48f,白色;外包缠纱选用锦纶6fdy(全拉伸丝)长丝纱,规格为40d/34f,颜色为本白色(sd半光纤维)。
[0072]
主芯纱喂入点(弹簧张力器输出瓷眼)与空心锭下端间长度为220 mm;芯纱喂入角(芯纱与空心锭中心管轴线夹角)为40
°
;超喂芯纱导纱钩与喂入装置间距为120 mm。
[0073]
空心锭转速15000 r/min,包缠捻向为s捻;引纱速度20 m/min,卷绕速度20 m/min。
[0074]
主芯纱与超喂芯纱间距设置为40 mm。
[0075]
分别采用超喂芯纱喂入速度24 m/min、26 m/min、28 m/min、30 m/min(超喂比依次为1.2、1.3、1.4、1.5)纺制4种复合纱。
[0076]
开机调整主芯纱张力装置,保证外包缠纱对芯纱为正常缠绕,芯纱不在外包缠纱张力作用下被拉偏离,之后不再调整。
[0077]
根据技术方案分析,可计算竹节部分与正常纱段的线密度比为(100d+100d+40d+100d
×
2)/(100d+100d+40d)=1+(100d
×
2)/(100d+100d+40d)=1+200/240≈1.83。
[0078]
为直观比较4种复合纱的竹节分布特征,分别将4种复合纱在a4黑卡纸上绕制成纱卡(横向绕纱,双面绕纱,纱间距5 mm);再分别在保证纱线伸直不伸长的情况下,连续计数每种纱线30个竹节的长度和竹节间距长度,进行统计分析。
[0079]
典型的复合纱成纱外观如图4所示。
[0080]
从图4中可以看出,复合纱竹节纱段与正常纱段的表观粗细差异。由于竹节是由超喂芯纱折叠缠绕形成,所以整个竹节纱段的粗细是相同的,没有变粗
‑
变细过程,而且经过外包缠纱的螺旋线状缠绕固定作用,竹节纱段呈波纹状起伏外观。
[0081]
4种纱线纱卡如图5所示。
[0082]
超喂比为1.2时,连续30个竹节的长度(mm)分别为:18、20、21、19、17、18、18、20、
16、17、19、18、18、17、19、18、20、17、20、19、20、20、19、18、19、18、20、18、21、19;竹节间距为:417、385、339、354、366、431、342、425、300、402、410、316、399、361、375、364、407、387、405、404、418、360、387、382、401、405、401、443、375、443。计算竹节长度均值为:18.7 mm,变异系数cv%值为:1.2%;计算竹节间距均值为:386.8 mm,变异系数cv%值为:34.1%。
[0083]
超喂比为1.3时,连续30个竹节的长度分别为:18、21、20、19、20、19、21、20、20、20、20、20、21、20、19、18、18、20、21、21、19、20、18、19、22、20、19、18、18、19;竹节间距为:202、201、201、183、204、191、204、195、202、190、208、191、210、196、196、186、196、205、202、205、211、180、193、203、205、192、207、209、181、217。计算竹节长度均值为:19.6 mm,变异系数cv%值为:1.1%;计算竹节间距均值为:198.9 mm,变异系数cv%值为:9.1%。
[0084]
超喂比为1.4时,连续30个竹节的长度依次为:21、19、22、23、22、19、19、21、19、20、22、22、20、20、22、23、19、20、20、21、20、19、21、22、21、21、19、21、20、21;竹节间距依次为:141、147、143、147、142、125、150、138、129、149、155、143、130、143、154、152、131、147、145、141、128、142、146、138、130、139、150、125、143、145。计算竹节长度均值为:20.6 mm,变异系数cv%值为:1.2%;计算竹节间距均值为:141.3 mm,变异系数cv%值为:8.3%。
[0085]
超喂比为1.5时,连续30个竹节的长度分别为:23、20、21、20、21、21、23、25、22、23、22、22、22、21、22、23、21、20、22、24、22、24、22、22、23、20、20、23、22、21;竹节间距为:100、111、104、106、105、108、120、98、108、108、107、112、114、115、98、102、101、113、107、104、109、102、113、94、110、110、105、115、91、110。计算竹节长度均值为:21.9 mm,变异系数cv%值为:1.3%;计算竹节间距均值为:106.7 mm,变异系数cv%值为:6.4%。
[0086]
从图5四种纱线的纱卡以及竹节长度、竹节间距测试结果可以看出:(1)竹节纱的竹节长度和竹节间距均不相等,而是在一定范围内波动,竹节长度的波动范围很小,而竹节间距波动范围较大,竹节在纱卡上分布均匀;(2)保持其它工艺参数不变,在一定范围内,随着超喂比的增大,竹节长度略有增加,而竹节间距会显著减小;(3)随着超喂比的增大,竹节间距波动幅度有所降低;(4)随着超喂比的增大,竹节部分的表观直径会有所增大(看上去更粗),这是由于随着超喂比增大,单位时间内的超喂芯纱超喂量增加,超喂芯纱缠绕主芯纱时的缠绕张力有所下降,形成的折叠缠绕纱段比较蓬松。当超喂比达到1.5时,出现了少量竹节段端头翘起、发毛的现象。
[0087]
因此,通过调整超喂比调整竹节间距,超喂比受到一定限制,如果超喂比过大,会使超喂芯纱折叠缠绕形成的竹节结构蓬松,对已缠绕了超喂芯纱的主芯纱的附着力下降,破坏竹节外观的形态。
[0088]
在本实例所涉及工艺配置范围内,超喂比宜控制在1.5以下。
[0089]
实施例2采用不同主芯纱与超喂芯纱喂入间距,纺制包缠复合竹节纱。
[0090]
采用与实例一相同的纱线原料和纺纱工艺参数,不同之处在于,保持超喂芯纱喂入速度28 m/min(超喂比为1.4)不变,依次改变超喂芯纱与主芯纱间距为65 mm、90 mm、125 mm,纺制3种复合纱,与实例一中超喂芯纱喂入速度28 m/min、主芯纱为超喂芯纱间距40 mm纺纱方案,共同组成不同喂入间距的实验系列。
[0091]
芯纱间距为65 mm时,连续30个竹节的长度依次为:30、30、29、31、31、28、32、30、29、29、30、30、30、29、29、31、30、31、29、32、34、32、30、30、29、31、30、34、30、33;竹节间距依
次为:199、190、204、196、178、208、186、190、197、191、192、207、190、184、206、199、189、187、196、202、206、185、189、193、193、192、201、188、197、193。计算竹节长度均值为:30.4 mm,变异系数cv%值为:1.5%;计算竹节间距均值为:194.2 mm,变异系数cv%值为:7.3%。
[0092]
芯纱间距为90 mm时,连续30个竹节的长度依次为:40、36、31、36、34、37、38、36、32、37、32、36、32、38、30、36、38、36、36、35、38、38、39、39、39、36、35、40、33、34;竹节间距依次为:240、205、244、238、256、233、256、230、232、208、222、241、222、243、228、242、263、232、255、228、249、261、235、231、224、239、236、238、227、240。计算竹节长度均值为:35.9 mm,变异系数cv%值为:2.6%;计算竹节间距均值为:236.6 mm,变异系数cv%值为:13.5%。
[0093]
芯纱间距为125 mm时,连续30个竹节的长度依次为:46、42、44、47、52、43、41、47、48、45、47、47、43、44、46、46、42、48、40、46、44、45、45、45、46、53、48、48、49、47;竹节间距依次为:286、315、295、325、307、276、292、334、288、294、315、300、292、302、293、300、315、288、295、300、285、318、311、296、332、315、324、332、322、324。计算竹节长度均值为:45.8 mm,变异系数cv%值为:2.8%;计算竹节间距均值为:305.7 mm,变异系数cv%值为:15.8%。
[0094]
从图5(c)和图6中3种竹节复合纱纱卡以及4种竹节长度和竹节间距测试结果可以看出:随着芯纱间距的增大,竹节长度和竹节间距均显著增大,而且二者的离散程度也有所增加。
[0095]
实例三:改变主芯纱线密度,纺制不同线密度比的包缠复合竹节纱。
[0096]
主芯纱采用规格为40d/34f的锦纶6长丝纱,超喂芯纱和外包缠纱规格同方案一;超喂比选择为1.4(超喂芯纱喂入速度28 m/min),主芯纱与超喂芯纱间距65 mm,其它工艺参数同方案一。该方案与方案二中芯纱间距65 mm方案形成对照关系,二者只有主芯线密度不同。
[0097]
按照本方案纺制的竹节纱的粗细比为:(40d+100d+40d+100d
×
2)/(40d+100d+40d)=1+(100d
×
2)/(40d+100d+40d)=1+200/180≈2.11。
[0098]
从图7中与图6(a)的对比可以看出,增大粗细比,竹节段与正常纱段的直径对比更强烈,竹节段表观更显著。
[0099]
包缠结构混色段彩竹节复合纱的正常纱段,由两根异色芯纱经外包缠纱包缠复合而成,呈现三者的混色。由于异色芯纱经过假捻点后解捻作用不均匀,再加上外包缠纱对芯纱进行包缠时张力产生的假捻作用,被外包缠纱包覆的芯纱并合体上残留无规律分布的捻回,使芯纱并合体不同片段呈现不同的颜色,并经外包缠纱的包缠加以固定。因此,正常纱段的混色效果,也会表现出段彩特征:外包缠纱对主芯纱包缠的混色色段,与外包缠纱对超喂芯纱包缠的混色色段,间隔分布。
[0100]
竹节纱段,由超喂芯纱对主芯纱的两次往复折叠三次缠绕后,再经外包缠纱包覆,因而呈现超喂芯纱和外包缠纱的混色,且由于竹节段表观直径大,呈色更明显。
[0101]
在主芯纱喂入装置(张力器)另一侧喂入另一颜色的超喂芯纱(采用同一喂入系统,芯纱间距相同或不同均可),可在芯纱并合体上形成两种颜色的竹节,纺制双色竹节纱。此时,正常纱段为主芯纱、两根超喂芯纱和外包缠纱的混色色段间隔分布,竹节纱段分别为两根超喂芯纱与外包缠纱的混色。
[0102]
芯纱与空心锭中心管下端的假捻效应源自空心管下端面对芯纱的截面周向的切向摩擦,而这种摩擦作用是非受控作用,摩擦效应会随着芯纱表面性质、芯纱直径、芯纱张
力等的变化而变化,以下因素决定了假捻点处的假捻效应处于不断的波动、变化中:正常芯纱段上超喂芯纱对主芯纱的螺旋线缠绕结构形成不均匀表面结构;竹节芯纱段上超喂芯纱的往复缠绕结构形成不均匀的表面结构;竹节纱段与正常纱段直径的差异;主芯纱张力的波动;主芯纱线密度的变异;超喂芯纱线密度的变异,等等。假捻效应的波动,决定竹节形成过程存在的波动性,使竹节长度与竹节间距在一定范围内随机波动。这恰恰满足了竹节纱对竹节长度与竹节间距不能相同的要求,使竹节在布面上分布均匀,不会形成条影图案。采用本技术加工竹节段彩纱,不需要专门的控制机制来实现节长、节距的随机变化,以确保节长节距不等长。
[0103]
超喂芯纱通过缠绕运动方向的折叠缠绕产生竹节,为保证竹节外观成形尽可能规整,要求超喂芯纱具有一定的柔软度,这样在竹节段两端弯曲折叠处(特别是第二次倒向时),才不会因超喂芯纱弯曲刚度大形成较大的环圈,影响竹节外观。一种纱线是否适合作为超喂芯纱产生竹节,需要具有合适的弯曲性能和弹性,可通过纺纱试验进行尝试,如果不能形成稳定的往复折叠缠绕律动,或竹节折叠端环圈大小超出要求(下游客户的要求),则不能作为超喂芯纱,但不排除两端环圈能形成特殊风格,并为客户所接受。对于具有加捻结构的纱线(长丝纱或短纤纱,特别是短纤纱),尤其是残余扭矩较大的加捻结构纱线,由于易在张力较低时发生扭结,不易形成相对稳定的往复折叠缠绕律动,破坏竹节外形。具有加捻结构的纱线是否适于作为超喂芯纱,需要通过纺纱试验进行判断。
[0104]
根据技术原理,对主芯纱和外包缠纱的技术要求,没有品种、规格方面的限制,只要能承受包缠复合加工基本的强力要求即可,一般常用纱线均可满足,可根据产品的性能要求与竹节粗细比等要求综合考虑、选配。
[0105]
为突出竹节纱段与正常纱段的颜色差异,本技术所采用的外包缠纱,建议选择低线密度(更细)的本色纱线,最好是具有一定透明度的长丝纱,这样,复合纱正常纱段基本显现主芯纱和超喂芯纱的混色,而竹节段则基本呈现超喂芯纱的颜色,颜色差异更分明,更能凸显混色段彩竹节纱的风格。
[0106]
外包缠纱对芯纱的包缠捻度,根据外包缠纱对竹节段的固定效果综合考虑确定,如果包缠捻度太低,外包缠纱对竹节段的固定效果差,复合纱在受到摩擦力作用时竹节段容易变形、起毛,且竹节两端也容易翘起(特别是第二次倒向端)。本技术方案建议包缠捻度不低于600 捻/m,以保证规整的竹节形态。
[0107]
采用短纤纱作为主芯纱时,短纤纱本身带有一定捻度,此时,空心锭回转方向(包缠捻向)须与主芯纱捻向相匹配。由于空心锭中心管下端使竹节形成区芯纱产生假捻的捻向与空心锭包缠捻向相反,而如果竹节形成区产生并传递的假捻捻回与主芯纱自身捻度的捻向相反,就会导致对主芯纱解捻,进而断头。这就要求,采用有捻短纤纱作为主芯纱时,空心锭包缠捻向必须与主芯纱捻向相反,这样,竹节形成区产生并传递的假捻捻回的捻向就与主芯纱捻向一致,避免主芯纱在假捻捻回作用下解捻、断头。也就是说,采用有捻短纤纱作为主芯纱,如果主芯纱带有捻度的捻向为z捻,则空心锭包缠捻向须选择s捻。反之亦然。
[0108]
超喂芯纱超喂比一般控制在1.2
‑
1.5之间。超喂比太小,竹节间距太大;超喂比太大,超喂芯纱张力太低,超喂芯纱对主芯纱的缠绕时的张力太低,竹节成形不好。超喂芯纱和主芯纱之间的芯纱间距,建议在30 mm
‑
100 mm以内调整,以调整竹节长度和间距。间距太小,竹节长度短,间距太大,超喂芯纱张力太低,不利于竹节的成形良好。超喂比和芯纱间
距,可根据主芯纱和超喂芯纱的规格、性能以及对竹节节长、节距的要求,通过探索实验进行选择和优化。
[0109]
实施例如下:实例四:锦/涤复合混色段彩竹节纱(一)主芯纱采用锦纶6全拉伸丝(fdy),红色,线密度为70d/48f;超喂芯纱采用涤纶低弹丝(dty),蓝色,线密度为100 d/48f;外包缠纱采用锦纶6全拉伸丝(fdy),本白色(半透明,半消光),线密度为40 d/34f。
[0110]
主要工艺配置为:空心锭中心管下端与主芯纱喂入点间距220 mm;芯纱与空心锭中心管中心线夹角为40
°
;空心锭速15000 r/min;引纱速度20 m/min(名义包缠捻度750 t/m);卷绕速度20 m/min;包缠捻向s;超喂芯纱喂入速度28 m/min,超喂比1.4。主芯纱与超喂芯纱间距65 mm。
[0111]
从图8(a)管纱外观可以看出,由于采用了低线密度白色化纤长丝纱作为外包缠纱,复合纱整体呈主芯纱(红色)和超喂芯纱(蓝色)的混色;从图8(b)、(c)白纱卡和黑纱卡可以看出,复合纱上均匀分布着超喂芯纱形成的竹节;从图8(d)可以看出,竹节部分呈蓝色超喂芯纱经白色(半透明)外包缠纱包缠的蓝
‑
白混色(外包缠纱对竹节段螺旋线状缠绕,形成“蓝
‑
白”色块分割),正常纱段则呈红色主芯纱与蓝色超喂芯纱经白色外包缠纱包缠后的“红
‑
白”、“蓝
‑
白”色块分割混色间隔排列。由于线密度(粗细)的差异,竹节部分和主芯纱部分的“蓝
‑
白”色块分割混色效果存在较大差异,能形成较为分明的对比,凸显竹节效果。
[0112]
实例五:锦/涤复合混色段彩竹节纱(二)主芯纱采用涤纶低弹丝(dty),白色,线密度为100 d/48f;超喂芯纱采用涤纶低弹丝(dty),蓝色,线密度为100 d/48f;外包缠纱采用锦纶6全拉伸丝(fdy),本白色(半透明,半消光),线密度为40 d/34f。
[0113]
主要工艺配置为与实例一相同[空心锭中心管下端与主芯纱喂入点间距220 mm;芯纱与空心锭中心管中心线夹角为40
°
;空心锭速15000 r/min;引纱速度20 m/min(名义包缠捻度750 t/m);卷绕速度20 m/min;包缠捻向s;超喂芯纱喂入速度28 m/min,超喂比1.4。主芯纱与超喂芯纱间距65 mm]。
[0114]
从图9可以看出,由于主芯纱采用了与外包缠纱同样的白色,正常纱段呈现“蓝
‑
白”混色与白色纱段间隔分布的外观,且“蓝
‑
白”混色与白色纱段的长度也无规律变化;竹节纱段仍呈“蓝
‑
白”色段分割的混色效果。
[0115]
实例四和实例五,给出的是采用不同种类、规格、颜色(包括本白色)的化纤长丝纱,纺制具有混色段彩竹节外观复合纱的实例。该应用表明,利用本技术可通过化纤长丝纱的复合加工,增加花色品种,进而拓展产品应用领域。
[0116]
实例六:天丝/涤纶/锦纶混色段彩复合纱主芯纱采用天丝(tencel)短纤纱,本白色,线密度为60英支(s);超喂芯纱采用涤纶低弹丝(dty),绿色,线密度为100 d/48f;外包缠纱采用锦纶6全拉伸丝(fdy),本白色(半透明,半消光),线密度为40 d/34f。
[0117]
主要工艺配置为:空心锭中心管下端与主芯纱喂入点间距220 mm;芯纱与空心锭中心管中心线夹角为40
°
;空心锭速15000 r/min;引纱速度20 m/min(名义包缠捻度750 t/m);卷绕速度20 m/min;包缠捻向s;超喂芯纱喂入速度24 m/min,超喂比1.2。主芯纱与超喂
芯纱间距40 mm。
[0118]
从图10可以看出,与实施例四和实施例五相比,由于减小了超喂比,竹节间距增大;芯纱间距的减小,导致了竹节长度的减小。采用本方案纺制的复合纱,由于主芯纱和超喂芯纱品种、规格配伍的变化,使得竹节部分超喂芯纱对主芯纱的缠绕结构变化,导致对芯纱的附着结构变化,经外包缠纱缠绕后,竹节两端折叠处环圈翘起较明显,这主要是由绿色超喂芯纱弯曲刚度稍大所致(柔软度稍低)。这在一定程度上可使竹节更突出,可被视为一种子风格。
[0119]
实例七:毛/腈/再生涤纶/聚乳酸纤维混色段彩竹节纱主芯纱采用精纺羊毛短纤混纺纱(50%巴素兰羊毛,50%腈纶),本白色,线密度为48公支;超喂芯纱为两根左右对称喂入,均为再生涤纶低弹丝(dty),线密度为100 d/48f,颜色分别为红色和蓝色;外包缠纱采用聚乳酸纤维全拉伸丝(pla),本白色(半透明,半消光),线密度为50 d/36f。
[0120]
主要工艺配置为:空心锭中心管下端与主芯纱喂入点间距220 mm;芯纱与空心锭中心管中心线夹角为40
°
;空心锭速15000 r/min;引纱速度20 m/min(名义包缠捻度750 t/m);卷绕速度20 m/min;包缠捻向s;超喂芯纱喂入速度24 m/min,超喂比1.2。主芯纱与两根超喂芯纱间距均为65 mm。
[0121]
从图11中可以看出:(1)复合纱正常纱段呈主芯纱(白色)、两根超喂芯纱(分别为红色和蓝色)经外包缠纱(白色)包缠、色块分割的混色色段间隔排列,且更色段长度无规分布;(2)复合纱长度方向上分布着两种颜色超喂芯纱经外包缠纱包缠后形成竹节段;(3)增加芯纱根数导致粗细比下降,彩色竹节的突出性有所下降。
[0122]
实例六和实例七,是采用本色(白色)短纤纱与有色(原液着色或染色)化纤长丝纱,纺制复合结构混色段彩竹节纱的应用。通过这一应用,(1)可实现多组分原料的复合,提高纱线的可加工性(提高强力和条干均匀度,控制短纤纱毛羽);(2)通过复合获取具有混色段彩外观,织制的织物不需要染色,提高产品的生态性;(3)多种原料复合,性能上相互弥补,可优化面料的性能(抗皱性、消除刺痒感等)。
[0123]
实施例不应视为对本发明的限制,但任何基于本发明的精神所作的改进,都应在本发明的保护范围之内。