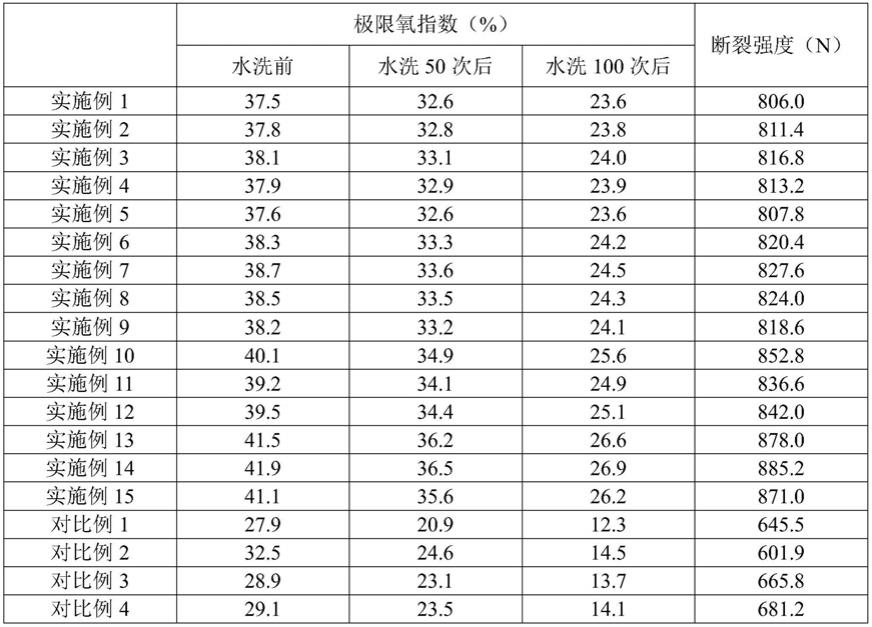
1.本技术涉及面料加工技术领域,更具体地说,它涉及一种阻燃纤维及其制备方法以及阻燃面料。
背景技术:2.服装三要素包括款式、面料、色彩,面料是用于制作服装的材料,随着人们生活水平的提高,人们对面料提出了越来越多功能性的方面的要求,比如提高面料的阻燃性能。
3.自生具有阻燃性能的纤维固然阻燃性能优异,但是服用性能较差,且造价较高,因此,目前大都的阻燃纤维都是对传统纤维进行阻燃改性。阻燃改性的方法大多是用阻燃剂对纤维进行整理,将通过浸轧的方法使得阻燃剂浸入到纤维中,起到阻燃作用。
4.针对上述相关技术,申请人发现,通过浸轧的方法用阻燃剂对纤维进行整理,制得的面料强度明显下降。
技术实现要素:5.为了提高阻燃面料的强度,本技术提供一种阻燃纤维及其制备方法以及阻燃面料。
6.第一方面,本技术提供一种阻燃纤维,采用如下的技术方案:一种阻燃纤维,由包括以下重量份的原料制备而成:聚对苯二甲酸乙二醇酯40
‑
90份、阻燃剂3
‑
12份;所述阻燃剂由包括以下重量份的原料制备而成:硼酸锌1
‑
6份、植酸水溶液1
‑
5份、新戊二醇0.1
‑
0.5份、尿素0.1
‑
0.5份。
7.通过采用上述技术方案,将阻燃剂与对苯二甲酸乙二醇酯混合熔炼制备阻燃纤维,相较于用阻燃剂对纤维进行表面整理,可以降低对阻燃剂对纤维结构的破坏,保证纤维的强度,使得阻燃纤维的断裂强度达到806.0
‑
885.2n。
8.纤维的热解过程包括在100℃以下的缓慢降解以及在达到熔点温度前的快速分解,本技术采用有机与无机复配形式的阻燃剂,有机成分接枝在纤维上,降低纤维的初始分解温度,阻燃剂在温度升高的过程中有机成分提前生成多磷酸,而多磷酸促进纤维素脱水成炭在基体表面生成致密炭层,从而起到保护纤维的作用,同时无机成分硼酸锌在受热温度达到300℃时发生热分解,释放出结晶水,起到吸热冷却和稀释空气中氧气的作用,另一方面,硼酸锌在高温下分解形成b2o3,附着在聚合物表面形成涂层,抑制可燃气体的产生,防止氧化反应和热分解,使得极限氧指数达到37.5
‑
41.9%,而且水洗100次后,极限氧指数依然可以达到23.6
‑
26.9%。
9.优选的,其由包括以下重量份的原料制备而成:聚对苯二甲酸乙二醇酯50
‑
80份、阻燃剂5
‑
10份;所述阻燃剂由包括以下重量份的原料制备而成:硼酸锌2
‑
5份、植酸水溶液2
‑
4份、新戊二醇0.2
‑
0.4份、尿素0.2
‑
0.4份。
10.通过采用上述技术方案,进一步优化原料的配比,提高阻燃纤维的阻燃性能。
11.优选的,所述阻燃剂的制备方法为:按重量份将植酸水溶液与新戊二醇进行酯化反应,然后将酯化产物与尿素反应得到有机成分;将有机成分与硼酸锌混合得到阻燃剂。
12.通过采用上述技术方案,首先将植酸水溶液、新戊二醇、尿素反应,得到新戊二醇植酸铵盐,即有机成分,然后再于硼酸锌无机成分混合得到阻燃剂。
13.优选的,所述阻燃剂外包裹有海藻酸钙,制成颗粒形阻燃剂。
14.通过采用上述技术方案,在阻燃剂外包裹海藻酸钙,在与聚对苯二甲酸丙二醇酯共混时,可作为聚对苯二甲酸丙二醇酯的缠绕位点,从而提高纤维的断裂强度,进而提高面料的断裂强度;另外,海藻酸钙自身优异的阻燃性能,可以进一步提高纤维的阻燃性能。
15.优选的,所述颗粒形阻燃剂的粒径为400
‑
500μm。
16.通过采用上述技术方案,此粒径范围内的阻燃剂可以在与聚对苯二甲酸丙二醇酯共混的过程中更大程度的发挥作用,提高纤维的强度。
17.优选的,其还包括3
‑
8份氧化石墨烯。
18.通过采用上述技术方案,将氧化石墨烯附着在纤维表面,氧化石墨烯具有较高的电子迁移率,进而具有良好的导热性,氧化石墨烯的二维层间结构可以作为壁垒减少热量释放,阻止可燃气体进入到纤维中,此外氧化石墨烯表面含有大量含氧官能团,在燃烧过程中会发生放热还原反应,氧化石墨烯的层状结构还可作为一种连续的保护性炭层,用来减缓热释放,抑制热质的传递,提高纤维的阻燃性能。此外,氧化石墨烯还可以进入到海藻酸钙内,进一步提高纤维的阻燃性能。
19.第二方面,本技术提供一种阻燃纤维的制备方法,采用如下的技术方案:一种前述任一项阻燃纤维的制备方法,包括以下步骤:按重量份将聚对苯二甲酸乙二醇酯与阻燃剂混合熔炼后,将熔炼产物拉丝成型,得到阻燃纤维。
20.通过采用上述技术方案,将阻燃剂与聚对苯二甲酸乙二醇酯共混制备阻燃纤维,在提高纤维的阻燃性能的同时,保证纤维的强度。
21.优选的,在所述熔炼产物拉丝成型后,加入到盐酸多巴胺溶液中,将氧化石墨烯也加入到盐酸多巴胺溶液中,混合浸泡后,过滤,洗涤,干燥,得到阻燃纤维。
22.通过采用上述技术方案,盐酸多巴胺溶液处理复合阻燃纤维,可使复合阻燃纤维表面带有正电荷,在与氧化石墨烯混合后,可吸附氧化石墨烯,使氧化石墨烯包覆于复合阻燃纤维表面,提高阻燃性能。
23.第三方面,本技术提供一种阻燃面料,采用如下的技术方案:一种阻燃面料,采用前述任一项阻燃纤维制得。
24.通过采用上述技术方案:在提高面料的阻燃性能保证面料强度。
25.综上所述,本技术具有以下有益效果:1、本技术采用有机成分与无机成分复配的阻燃剂与聚对苯二甲酸乙二醇酯熔融共混制备阻燃纤维,然后再用阻燃纤维纺织阻燃面料,制得的面料的极限氧指数达到37.5
‑
41.9%;而且水洗100次后,极限氧指数依然可以达到23.6
‑
26.9%;面料的断裂强度可以达到806.0
‑
885.2n,在提高阻燃性能的同时,保证面料的强度。
26.2、本技术中优选采用海藻酸钙对阻燃剂进行包裹,进一步提高面料的断裂强度,制得的面料的极限氧指数达到39.5
‑
41.9%;面料的断裂强度可以达到836.6
‑
885.2n。
具体实施方式
27.以下结合实施例对本技术作进一步详细说明。
28.原料和/或中间体的制备例原料聚对苯二甲酸乙二醇酯,采用re5333 nc010型号;植酸水溶液,质量分数为70%。
29.制备例制备例1阻燃剂的制备方法:将1kg植酸水溶液与0.5kg新戊二醇混合均匀,在145℃下反应3h,得到中间产物,然后降温至120℃,加入0.1kg尿素,继续反应2h,得到的产物用无水乙醇清洗,即为有机成分:然后将所得有机成分与6kg硼酸锌混合均匀得到阻燃剂。
30.制备例2与制备例1不同的是,阻燃剂原料配比的不同,详见表1。
31.表1制备例1
‑
5原料配比表(kg) 硼酸锌植酸水溶液新戊二醇尿素制备例1610.50.1制备例2520.40.2制备例3430.30.3制备例4240.20.4制备例5150.10.5
32.制备例6与制备例3不同的是,将1kg制备例3所得的阻燃剂与10l质量百分数为1.5%的海藻酸钙溶液混合均匀,将混合液加入单分散液滴发生器中,调节系统载气压力为0.8kg/cm2,脉冲发生器频率为10khz,分散风流量为9l/min,将混合液从200μm的喷嘴喷出形成分散液滴,液滴落入质量百分数为2%的cacl2溶液中固化30min,过滤洗涤得到颗粒形阻燃剂,其粒径为400
‑
500μm。
33.制备例7
‑
8与制备例6不同的是,制得的颗粒形阻燃剂粒径分别为50
‑
100μm、2000
‑
3000μm。实施例
34.实施例1一种阻燃纤维,其制备方法为:将40kg聚对苯二甲酸乙二醇酯投入到双螺杆设备的前部加料口,将12kg制备例1所得的阻燃剂投入到双螺杆设备中部加料口与聚对苯二甲酸乙二醇酯共混,高温剪切,得到纺丝熔体;其中,双螺杆设备中温度为295℃,压力为26mpa,螺杆转速为160转/分;然后将纺丝溶体进行定型处理,得到阻燃纤维。
35.实施例2与实施例1不同的是,聚对苯二甲酸乙二醇酯的量为50kg、阻燃剂的量为10kg。
36.实施例3与实施例1不同的是,聚对苯二甲酸乙二醇酯的量为65kg、阻燃剂的量为8kg。
37.实施例4与实施例1不同的是,聚对苯二甲酸乙二醇酯的量为80kg、阻燃剂的量为5kg。
38.实施例5与实施例1不同的是,聚对苯二甲酸乙二醇酯的量为90kg、阻燃剂的量为3kg。
39.实施例6
‑
12与实施例3不同的是,阻燃剂分别来自于制备例2
‑
8。
40.实施例13与实施例10不同的是,将纺丝溶体加入到盐酸多巴胺溶液中,纺丝溶体与盐酸多巴胺溶液的质量比为1:10,然后将3kg氧化石墨烯加入到盐酸多巴胺溶液与纺丝溶体的混合物中,在室温下混合浸泡5h,过滤后用去离子水洗涤干净后,在80℃的条件下干燥2h,然后进行定型处理,得到阻燃纤维。
41.实施例14
‑
15与实施例13不同的是,氧化石墨烯的加入量分别为5kg、8kg。
42.应用例1
‑
15一种阻燃面料,其分别使用实施例1
‑
15中的阻燃纤维纺织而成。
43.对比例对比例1与应用例1不同的是,制备面料的纤维为芳砜纶纤维。
44.对比例2与应用例2不同的是,制备面料的纤维为用制备例1得到的阻燃剂的水溶液对涤纶纤维进行浸轧处理得到的纤维。
45.对比例3与应用例1不同的是,制备面料的纤维中用等量有机成分替换无机成分。对比例4与应用例1不同的是,制备面料的纤维中用等量无机成分替换有机成分。
46.性能检测试验检测方法阻燃性能测试:根据gb/t5454—1997《纺织品燃烧性能试验氧指数法》的要求,利用极限氧指数仪测定应用例1
‑
15与对比例1
‑
4中面料的极限氧指数。
47.断裂强度测试:将应用例1
‑
15与对比例1
‑
4中面料制成5cm
×
20cm的试样,于万能拉力机中测试试样的断裂强度。
48.耐水洗性能测试:首先,根据aatcc61—2006《耐家庭和商业洗涤色牢度:快速法》,对应用例1
‑
15与对比例1
‑
4中面料进行50、100次水洗,,然后测试水洗后面料的阻燃性能,考察其耐水洗性能。洗涤条件:采用1.5g/l十二烷基苯磺酸钠作为洗涤剂,水温为49℃,洗涤时间为45min。
49.性能检测结果见表2
表2性能检测结果
50.结合应用例1
‑
15和对比例1
‑
4,并结合表2可以看出,本技术制1得的面料的阻燃性能优于对比例1
‑
4,同时,本技术制得的面料的断裂强度也明显优于对比例1
‑
4,对比例2中面料的阻燃性能相对其他对比例较优,但对比例2中面料的断裂强度明显低于本技术,即本技术的面料在提高阻燃性能的同时,还能保证面料的断裂强度。另外,本技术中面料在水洗50次甚至100次后,仍然可以保持较好的阻燃性能。
51.结合应用例1与对比例3
‑
4,并结合表2可以看出,在制备与聚对苯二甲酸乙二醇酯共混的阻燃剂时,将有机成分与无机成分复配作为阻燃剂,可以进一步提高面料的阻燃性能,这可能是因为有机成分主要在加热前段发挥作用,无机成分主要在加热的后半段发挥作用,两者协同提高阻燃性能。
52.结合应用例6
‑
12,并结合表2可以看出,在阻燃剂外包裹海藻酸钙制成颗粒状的阻燃剂,可以进一步提高阻燃性能,并且对断裂强度的提高更为明显,这可能是因为在与聚对苯二甲酸丙二醇酯共混时,海藻酸钙可作为聚对苯二甲酸丙二醇酯的缠绕位点,从而提高纤维的断裂强度,进而提高面料的断裂强度。
53.结合应用例10
‑
12,并结合表2可以看出,阻燃剂的粒径400
‑
500μm之间时,制得的面料的阻燃性能与断裂强度表现均更优,这可能是因为此粒径范围内的阻燃剂可以在与聚对苯二甲酸丙二醇酯共混的过程中更加均匀的结合,从而提升纤维的性能。
54.结合应用例10与应用例13
‑
15,并结合表2可以看出,在纤维外包覆氧化石墨烯,进一步提高了阻燃性能。
55.本具体实施例仅仅是对本技术的解释,其并不是对本技术的限制,本领域技术人员在阅读完本说明书后可以根据需要对本实施例做出没有创造性贡献的修改,但只要在本技术的权利要求范围内都受到专利法的保护。