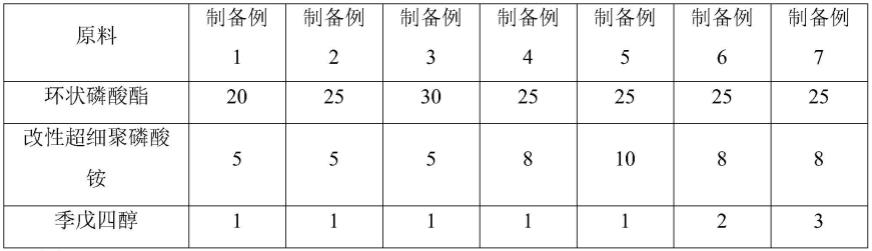
1.本技术涉及纺织用品领域,更具体地说,它涉及一种高弹阻燃涤纶面料及其制备方 法。
背景技术:2.涤纶是聚酯纤维,其是由有机二元酸和二元醇缩聚而成的聚酯,经纺丝和后处理所 得的合成纤维。涤纶的强度高、模量高、吸水性低,主要应用于民用织物及工业用织物。涤 纶面料的极限氧指数仅为20-22%,其阻燃性较差,且在燃烧时能够形成熔融滴落物,导致 火焰的传播和二次伤害。因此,提高涤纶面料的阻燃性能,是涤纶面料发展中非常有必要的。
3.相关技术中,阻燃涤纶面料主要是在后整理的上柔过程中添加阻燃助剂,该助剂附 着在纤维表面,在织物燃烧情况下吸收燃烧域中的热量,稀释和隔离空气,从而阻止燃烧, 但由于阻燃主机附着在纤维表面,多次洗涤助剂就会被洗褪,涤纶面料的阻燃性能就会减弱。
技术实现要素:4.为了提高涤纶面料的阻燃性,本技术提供了一种高弹阻燃涤纶面料及其制备方法。
5.第一方面,本技术提供一种高弹阻燃涤纶面料,其采用如下技术方案:一种高弹阻燃涤纶面料,其包括如下重量份的原料:pet切片80-90份、纤维素纤维15-20 份、纳米三氧化二铝2-4份、丙三醇6-9份、peg-400 8-10份和阻燃剂3-5份;所述阻燃剂 包括如下重量份原料:环状磷酸酯20-30份、改性超细聚磷酸铵5-10份和季戊四醇1-3份; 所述改性超细聚磷酸铵为疏水改性处理后的超细聚磷酸铵。
6.本技术涤纶面料原料可选用pet切片80-90份、纤维素纤维15-20份、纳米三氧化二 铝2-4份、丙三醇6-9份、peg-400 8-10份和阻燃剂3-5份,涤纶面料的各性能效果可预期, 且当pet切片85份、纤维素纤维18份、纳米三氧化二铝3份、丙三醇7.5份、peg-2000 9 份和阻燃剂4份时,效果最佳。
7.通过采用上述技术方案,采用pet切片作为涤纶面料的主要原料,其表面光滑有光 泽,具有优良的物理机械性能,电绝缘性优良,耐疲劳性、耐摩擦性和尺寸稳定性较高,保 证了涤纶面料的产品质量。
8.纤维素纤维是利用棉短绒、木材、竹子、甘蔗渣、芦苇等天然物质,通过一定的工 艺处理方法对其纤维素分子重塑而得。加入纤维素纤维,使涤纶面料具有良好的透气型,手 感柔顺,且纤维素纤维的吸湿性较强,更容易上色,上色纯正且色牢度好。
9.纳米三氧化二铝加入,可提高涤纶纤维的抗紫外性能。丙三醇加入具有润湿、吸湿 和防皱缩的作用,防止涤纶面料皱缩变形。peg-400作为抗静电剂和柔软剂加入,具有良好 的润湿性、抗静电、柔软和平滑性能,提高涤纶面料抗静电作用和手感。
10.阻燃剂中环状磷酸酯为高粘度透明液体,具有较高的热稳定性和优良耐水性,由于 p-c键的存在,其化学稳定性强,阻燃性能够持久。改性超细聚磷酸铵中的磷酸可以覆盖在 聚合物表面,隔绝空气,防止聚合物燃烧,含磷量和含氮量较高,且存在磷氮协同效应,具 有较高的阻燃性能,其ph值近中性,可与环状磷酸酯和季戊四醇复配,提高涤纶面料的阻 燃性。加入季戊四醇,可提高成炭稳定性,增强涤纶面料的阻燃效果。环状磷酸酯、聚磷酸 铵和季戊四醇复配,具有阻燃高效率、低烟、低毒等优点。
11.作为优选:一种高弹阻燃涤纶面料,其包括如下重量份的原料:pet切片84-88份、 纤维素纤维17-19份、纳米三氧化二铝2.5-3.5份、丙三醇7-8份、peg-2000 8.5-9.5份和阻 燃剂3.5-4.5份。
12.作为优选:所述阻燃剂还包括如下重量份的原料:氢氧化铝3-7份、三氧化二锑1-3 份。
13.通过采用上述技术方案,加入氢氧化铝裂解产生的氧化铝可增强催化炭化能力,提 高织物背面碳骨架强度,封闭可燃性气体的喷发,提高阻燃效果。同时,适量的氢氧化铝 封闭了阻燃剂的吸湿基团,且增加了膜的交联度,提高涤纶面料的手感。三氧化二锑作为阻 燃辅助剂加入,具有协效阻燃以及辅助抗熔滴的作用。
14.作为优选:所述改性超细聚磷酸铵的改性具体操作步骤为:在50-60℃条件下在超细 聚磷酸铵中加入甲基含氢硅油,搅拌均匀,继续加热至100-110℃,加入疏水二氧化硅,搅 拌均匀,冷却干燥,得到改性超细聚磷酸铵;所述超细聚磷酸铵、甲基含氢硅油和疏水二氧化硅的重量份配比为1:(2-3):(8-10)。
15.通过采用上述方案,甲基含氢硅油侧基含有大量的高反应活性的氢原子,存在分子 间的氢键作用,分子相互易接近,甲基内聚能密度小,具有良好的斥水性,采用其包覆超细 聚磷酸铵,使超细聚磷酸铵具有疏水性能,选用疏水二氧化硅与甲基含氢硅油包覆的超细聚 磷酸铵混合,疏水二氧化硅表面存在醇羟基,在甲基含氢硅油发生脱氢反应键合,疏水二氧 化硅会与甲基含氢硅油发生脱氢反应,填补甲基含氢硅油包覆的超细聚磷酸铵表面的空隙, 提高超细聚磷酸铵的疏水型。
16.作为优选:所述阻燃剂中还包括5-10重量份的n-苯基马来酰亚胺和10-20重量份的 单硬脂酸甘油酯。
17.通过采用上述技术方案,n-苯基马来酰亚胺可使涤纶面料在受热时产生智能自交联, 提高涤纶面料的抗熔滴性,与单硬脂酸甘油酯复配加入,可提高n-苯基马来酰亚胺在涤纶 面料原料体系中的分散均匀度,进一步提高n-苯基马来酰亚胺的抗熔滴性,防止在燃烧时 能够形成熔融滴落物,减少火焰的传播和二次伤害的情况发生。
18.作为优选:所述n-苯基马来酰亚胺与单硬脂酸甘油酯的重量份配比为1:(2-3)。
19.通过采用上述技术方案,调节n-苯基马来酰亚胺与单硬脂酸甘油酯重量份配比,可 进一步提高n-苯基马来酰亚胺在涤纶面料原料体系中的分散均匀度,从而提高n-苯基马来 酰亚胺的抗熔滴性。
20.作为优选:所述高弹阻燃涤纶面料还包括如下重量份的原料:ptt纤维10-20份。
21.通过采用上述技术方案,ptt纤维弹性较高,还具有易于染色、手感柔软和防污性 能的特点,提高涤纶面料的弹性。
22.第二方面,本技术提供一种上述任一项高弹阻燃涤纶面料的制备方法,具体通过以 下技术方案得以实现:一种高弹阻燃涤纶面料的制备方法,其包括以下操作步骤:将高弹阻燃涤纶面料各原料混合,采用熔融纺丝法进行纺丝,得到涤纶纤维;涤纶纤维按料比1:(20-30)放入纤维开孔液中,升温至120℃保温30min,漂洗,纺织成纺 纱线,染整,得到高弹阻燃涤纶面料;所述纤维开孔液为浓度15%的氢氧化钠水溶液,减量 率为10-11%。
23.综上所述,本技术包括以下至少一种有益技术效果:(1)本技术通过控制涤纶面料各原料的种类和掺量,使涤纶面料的极限氧指数、残炭量、 顶破强力和回弹率分别为34%、29%、326n和97.8%,提高了涤纶面料的阻燃性和弹性。
24.(2)本技术通过在阻燃剂原料中加入氢氧化铝和三氧化二锑,并调节两者掺量,使 涤纶面料的极限氧指数、残炭量、顶破强力和回弹率分别为37%、31%、341n和98.1%, 进一步提高涤纶面料的阻燃性。
25.(3)本技术通过在阻燃剂原料中加入n-苯基马来酰亚胺与单硬脂酸甘油酯,并调节 二者重量份配比,使涤纶面料的极限氧指数、残炭量、顶破强力和回弹率分别为39%、33%、 348n和98.5%,提高了涤纶面料的阻燃性。
26.(4)本技术通过在涤纶面料原料中加入ptt纤维,使涤纶面料的极限氧指数、残炭 量、顶破强力和回弹率分别为39%、34%、355n和98.9%,提高了涤纶面料的弹性。
具体实施方式
27.以下结合具体实施例对本技术作进一步详细说明。
28.本技术中的如下各原料均为市售产品,均为使本技术的各原料得以公开充分,不应 当理解为对原料的来源产生限制作用。具体为:pet切片,货号为al-558467457077;纤维 素纤维,尺寸2-3mm;纳米三氧化二铝,粒径为50nm;环状磷酸酯,150000max(25℃); 超细聚磷酸铵,粒径为200nm;甲基含氢硅油,有效物质含量为99.5%;疏水二氧化硅,粒 径为20nm;n-苯基马来酰亚胺,有效物质含量为90%;单硬脂酸甘油酯,货号为 jscw20201125;ptt纤维,牌号1161。
29.以下为阻燃剂的制备例制备例1制备例1的阻燃剂,通过如下方法制备得到:在50-60℃条件下,在0.8kg的超细聚磷酸铵中加入2kg甲基含氢硅油,搅拌均匀,继续加 热至100℃,加入7.2kg疏水二氧化硅,搅拌均匀,冷却干燥,得到改性超细聚磷酸铵,备 用;按照表1的掺量,将改性超细聚磷酸铵与环状磷酸酯和季戊四醇混合,搅拌均匀,得到阻燃 剂。
30.制备例2-7制备例2-7的阻燃剂与实施例1的制备方法及原料种类完全相同,区别在于各原料掺量不同, 具体详见表1所示。
31.表1制备例1-7阻燃剂的各原料掺量(单位:kg)制备例8-12制备例8-12的阻燃剂与实施例6的制备方法及原料掺量完全相同,区别在于阻燃剂中还添 加了氢氧化铝和三氧化二锑,具体掺量详见表2所示。
32.表2制备例8-12阻燃剂的各原料掺量(单位:kg)kg)制备例13-16制备例13-16的阻燃剂与实施例6的制备方法及原料掺量完全相同,区别在于阻燃剂中还添 加了n-苯基马来酰亚胺和单硬脂酸甘油酯,具体掺量详见表3所示。
33.表3制备例13-16阻燃剂的各原料掺量(单位:kg) 原料制备例13制备例14制备例15制备例16环状磷酸酯25252525改性超细聚磷酸铵8888季戊四醇2222n-苯基马来酰亚胺58510单硬脂酸甘油酯10201510制备例17制备例17的阻燃剂与实施例14的制备方法及原料掺量完全相同,区别在于阻燃剂中还添加 了5kg氢氧化铝和2kg三氧化二锑,其余原料种类与实施例14完全相同。
34.实施例1实施例1的涤纶面料,其通过如下操作步骤制备得到:按照表4的掺量,将pet切片、纤维素纤维、纳米三氧化二铝、丙三醇、peg-400和制备 例1制备的阻燃剂混合,采用熔融纺丝法进行纺丝,得到涤纶纤维;涤纶纤维按料比1:25放入纤维开孔液中,升温至120℃保温30min,漂洗,纺织成纺
纱线, 染整,得到高弹阻燃涤纶面料;所述纤维开孔液为浓度15%的氢氧化钠水溶液,减量率为 10%。
35.实施例2-3实施例2-3的涤纶纤维与实施例2的制备方法及原料种类完全相同,区别在于各原料掺量, 具体详见表4所示。
36.表4实施例1-3的涤纶纤维的各原料掺量(单位:kg)kg)实施例4-20实施例4-20的涤纶纤维与实施例2的制备方法及原料掺量完全相同,区别在于阻燃剂分别 选用制备例2-17制备得到的阻燃剂,其余原料种类与实施例2完全相同。
37.实施例21-23实施例21-23的涤纶纤维与实施例19的制备方法及原料掺量完全相同,区别在于涤纶纤维 原料中还包括15kg的ptt纤维,其余原料种类与实施例2完全相同。
38.对比例1对比例1的涤纶纤维与实施例1的制备方法完全相同,区别在于:将涤纶纤维原料中的阻燃 剂等量替换为硫代磷酸酯无卤环保阻燃剂,型号为rz-nld,其余原料及掺量与实施例1相 同。
39.对比例2对比例2的涤纶纤维与实施例1的制备方法完全相同,区别在于:所述涤纶纤维原料中的阻 燃剂原料中未添加改性超细磷酸聚酯,其余原料及掺量与实施例1相同。
40.对比例3对比例3的涤纶纤维与实施例1的制备方法完全相同,区别在于:将涤纶纤维原料中的阻燃 剂原料中的改性超细磷酸聚酯等量替换为聚磷酸酯,粒径为3mm,其余原料及掺量与实施 例1相同。
41.对比例4对比例4的涤纶纤维与实施例1的制备方法完全相同,区别在于:将涤纶纤维原料中的阻燃 剂原料中的改性超细磷酸聚酯等量替换为超细聚磷酸酯,其余原料及掺量与实施例1相同。
42.对比例5对比例5的涤纶纤维与实施例1的制备方法完全相同,区别在于:在涤纶纤维原料
中的阻燃 剂原料中未添加季戊四醇,其余原料及掺量与实施例1相同。
43.对比例6对比例6的涤纶纤维与实施例1的制备方法完全相同,区别在于:在涤纶纤维原料中的阻燃 剂原料中未添加环状磷酸酯,其余原料及掺量与实施例1相同。
44.性能检测采用如下检测标准或方法分别对不同的实施例1-23和对比例1-6进行性能检测,检测结果 详见表5所示。
45.极限氧指数:按照gb/t 5454-1997《纺织品燃烧性能试验氧指数法》对涤纶面料进 行极限氧指数的检测。
46.残炭量:采用残炭测定仪检测涤纶面料的残炭量。
47.顶破强力:按照gb/t 19976-2005《纺织品顶破强力的测定钢球法》对涤纶面料 进行110g/m2顶破强力的检测。
48.回弹率:按照fz/t 70006-2004《针织物拉伸弹性回复率试验方法》对涤纶面料进行 回弹率的检测。
49.表5不同涤纶面料的性能检测结果
由表5的检测结果表明,本技术得到的涤纶面料的极限氧指数、残炭量、顶破强力和回弹率 最高分别为29%、33%、312n和98.5%,在保证涤纶面料基本强度的情况下,提高了涤纶 面料的阻燃性和弹性。
50.实施例1-3中,实施例2涤纶面料的极限氧指数、残炭量、顶破强力和回弹率分别为 30%、26%、315n和96.8%,高于实施例1和实施例3,表明实施例2涤纶面料中的阻燃剂 掺量较为合适,可能与环状磷酸酯、聚磷酸铵和季戊四醇复配,具有阻燃高效率、低烟、低 毒等优点有关。
51.实施例4-6中,实施例5涤纶面料的极限氧指数、残炭量、顶破强力和回弹率分别为 32%、27%、320n和97.0%,高于实施例4和实施例6,表明实施例5涤纶面料阻燃剂中环 状磷酸酯掺量较为合适,可能与环状磷酸酯具有较高的热稳定性和优良耐水性,由于p-c键 的存在,其化学稳定性强有关。
52.实施例7-10中,实施例9涤纶面料的极限氧指数、残炭量、顶破强力和回弹率分别 为34%、29%、326n和97.8%,高于实施例7-8和实施例10,表明实施例9涤纶面料阻燃 剂中改性超细聚磷酸钠和季戊四醇掺量较为合适,可能与改性超细聚磷酸铵中的磷酸可以覆 盖在聚合物表面,隔绝空气,防止聚合物燃烧,含磷量和含氮量较高,且存在磷氮协同效应, 季戊四醇可提高成炭稳定性有关。
53.实施例11-15中,实施例14涤纶面料的极限氧指数、残炭量、顶破强力和回弹率分 别为37%、31%、341n和98.1%,高于实施例11-13和实施例15,表明实施例14涤纶面料 阻燃剂中氢氧化铝和三氧化二锑掺量较为合适,可能与加入氢氧化铝裂解产生的氧化铝可增 强催化炭化能力,提高织物背面碳骨架强度,封闭可燃性气体的喷发,提高阻燃效果,三 氧
化二锑作为阻燃辅助剂加入,具有协效阻燃以及辅助抗熔滴的作用有关。
54.实施例16-19中,实施例17涤纶面料的极限氧指数、残炭量、顶破强力和回弹率分 别为38%、32%、345n和98.4%,高于实施例16和实施例18-19,表明实施例17涤纶面料 阻燃剂中当n-苯基马来酰亚胺与单硬脂酸甘油酯的重量份配比为1:2.5时较为合适,可能 与n-苯基马来酰亚胺可使涤纶面料在受热时产生智能自交联,提高涤纶面料的抗熔滴性, 与单硬脂酸甘油酯复配加入,可提高n-苯基马来酰亚胺在涤纶面料原料体系中的分散均匀 度有关。
55.结合实施例20和实施例17涤纶面料的性能检测数据发现,实施例20涤纶面料的极 限氧指数、残炭量、顶破强力和回弹率分别为39%、33%、348n和98.5%,高于实施例20, 表明在阻燃剂原料的基础上同时加入改性超细聚磷酸钠、季戊四醇、氢氧化铝和三氧化二锑, 提高了涤纶面料的阻燃效果。
56.实施例21-23中,实施例22涤纶面料的极限氧指数、残炭量、顶破强力和回弹率分 别为39%、34%、355n和98.9%,高于实施例21和实施例23,表明实施例22涤纶面料中 加入ptt纤维,可提高涤纶纤维的回弹率,可能与ptt纤维弹性较高,还具有易于染色、 手感柔软和防污性能的特点,提高涤纶面料的弹性有关。
57.另外,结合对比例1-6和实施例1涤纶面料的各项指标数据发现,本技术在涤纶纤维 原料中加入阻燃剂,以及阻燃剂的配方,均可不同程度的提高涤纶面料的阻燃性。
58.本具体实施例仅仅是对本技术的解释,其并不是对本技术的限制,本领域技术人员 在阅读完本说明书后可以根据需要对本实施例做出没有创造性贡献的修改,但只要在本技术 的权利要求范围内都受到专利法的保护。