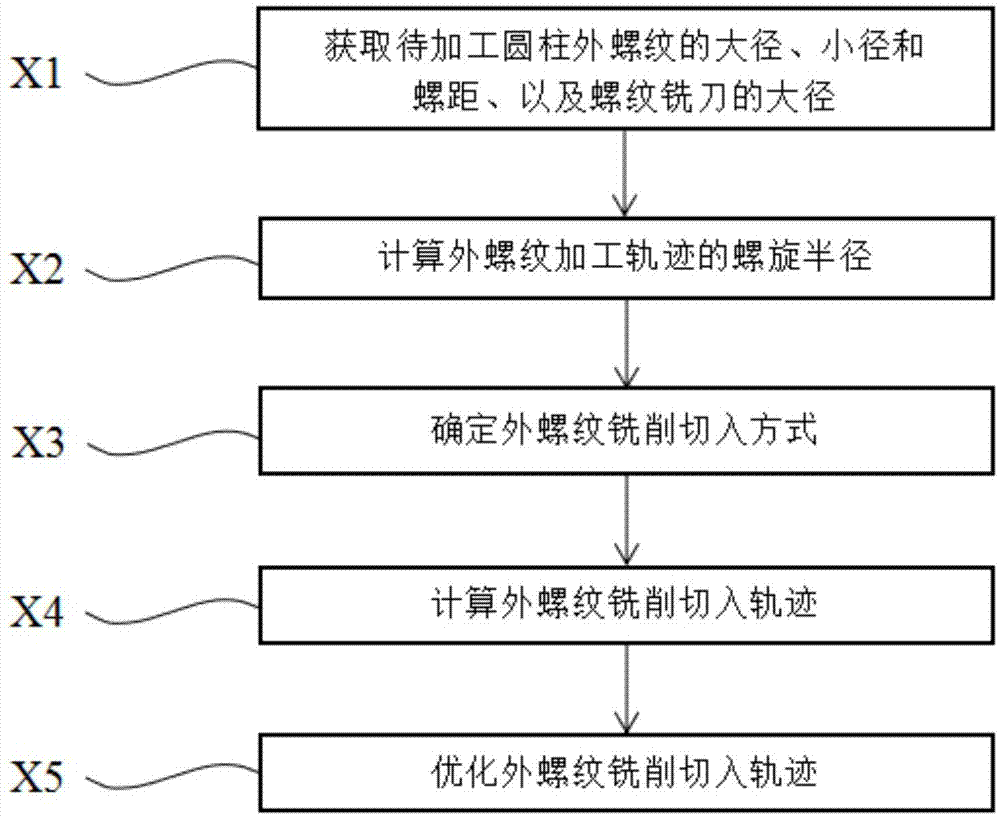
本发明涉及外螺纹铣削的加工工艺,尤其涉及一种圆柱外螺纹螺旋铣削切入轨迹优化方法。
背景技术:
螺纹应用广泛,在飞机、汽车以及航空航天设备中都随处可见,因此螺纹加工精度就显得尤为重要。传统的外螺纹加工一般采用螺纹车刀车削螺纹或采用板牙手工攻丝。随着数控机床的快速发展,螺纹铣削加工技术在机械制造业中的应用越来越广泛。并且,同一把螺纹铣刀可加工不同旋向的外螺纹和相同螺距不同直径的外螺纹,同时提高了螺纹的加工精度和加工效率。但是,当螺纹铣刀切入和切出工件时,铣刀会在工件上产生过切现象,极大地影响外螺纹的加工精度。因此,迫切需要提出一种圆柱外螺纹螺旋铣削切入轨迹优化方法,以减少外螺纹铣削切入过程产生的过切,从而提高圆柱外螺纹的加工精度。技术实现要素:因此,本发明的实施例提供一种圆柱外螺纹螺旋铣削切入轨迹优化方法,可减少干涉、提高螺纹的加工精度。一方面,本发明实施例提供一种圆柱外螺纹螺旋铣削切入轨迹优化方法,包括步骤:(x1)获取待加工圆柱外螺纹的大径d、小径d1和螺距p、以及螺纹铣刀的大径d;(x2)基于所述螺距p、所述小径d1和所述大径d确定外螺纹加工轨迹的螺旋半径rt;(x3)基于所述大径d和所述大径d确定外螺纹铣削切入方式,其中:当时,所述外螺纹铣削切入方式为半螺旋切入方式,螺旋切入夹角α2满足:0<α2<π,所述外螺纹铣削切入轨迹的螺旋半径rp满足:rp=ert,其中当时,所述外螺纹铣削切入方式为切向切入方式,在切向切入方式下螺纹铣刀径向运动轨迹沿y轴的位移变量t满足:0<t<f,其中计算外螺纹铣削切入轨迹,当所述外螺纹铣削切入方式为半螺旋切入方式时,所述外螺纹铣削切入轨迹满足:当所述外螺纹铣削切入方式为切向切入方式时,所述外螺纹铣削切入轨迹满足:优化所述外螺纹铣削切入轨迹,当所述外螺纹铣削切入方式为半螺旋切入方式时,优化后的所述外螺纹铣削切入轨迹满足:当所述外螺纹铣削切入方式为切向切入方式时,所述外螺纹铣削切入轨迹满足:另一方面,本发明实施例还提供一种圆柱外螺纹螺旋铣削切入轨迹优化方法,包括:获取待加工圆柱外螺纹的尺寸参数和螺纹铣刀的尺寸参数;基于所述待加工圆柱外螺纹的尺寸参数和所述螺纹铣刀的尺寸参数确定外螺纹加工轨迹的螺旋半径rt;基于所述外螺纹加工轨迹的螺旋半径rt和所述待加工圆柱外螺纹的尺寸参数确定外螺纹铣削切入轨迹;以及通过改变所述外螺纹铣削切入轨迹的轴向位移优化所述外螺纹铣削切入轨迹。在本发明一个实施例中,所述待加工圆柱外螺纹的尺寸参数包括所述待加工外螺纹的大径d、小径d1和螺距p,所述螺纹铣刀的尺寸参数包括所述螺纹铣刀的大径d。在本发明一个实施例中,所述基于所述待加工圆柱外螺纹的尺寸参数和所述螺纹铣刀的尺寸参数确定外螺纹加工轨迹的螺旋半径rt,其中外螺纹加工轨迹的螺旋半径rt满足:在本发明一个实施例中,所述基于所述外螺纹加工轨迹的螺旋半径rt和所述待加工圆柱外螺纹的尺寸参数确定外螺纹铣削切入轨迹的步骤,具体包括:确定外螺纹铣削切入方式;基于所述外螺纹加工轨迹的螺旋半径rt和所述待加工圆柱外螺纹的螺距p确定所述外螺纹铣削切入轨迹。在本发明一个实施例中,当外螺纹铣削切入方式为半螺旋切入方式,螺旋切入夹角α2满足:0<α2<π,所述外螺纹铣削切入轨迹的螺旋半径rp满足:rp=ert,其中e满足:当外螺纹铣削切入方式为切向切入方式,在切向切入方式下螺纹铣刀径向运动轨迹沿y轴的位移变量t满足:0<t<f,其中f满足:在本发明一个实施例中,当所述外螺纹铣削切入方式为半螺旋切入方式时,所述外螺纹铣削切入轨迹满足:当所述外螺纹铣削切入方式为切向切入方式时,所述外螺纹铣削切入轨迹满足:在本发明一个实施例中,当所述外螺纹铣削切入方式为半螺旋切入方式时,优化后的所述外螺纹铣削切入轨迹满足:当所述外螺纹铣削切入方式为切向切入方式时,所述外螺纹铣削切入轨迹满足:上述技术方案可以具有如下优点:本发明实施例提供的圆柱外螺纹螺旋铣削切入轨迹优化方法通过改变外螺纹铣削切入轨迹的轴向位移来减少螺纹铣刀切入时的干涉,从而提高圆柱外螺纹的加工精度。附图说明为了更清楚地说明本发明实施例的技术方案,下面将对实施例描述中所需要使用的附图作简单地介绍,显而易见地,下面描述中的附图仅仅是本发明的一些实施例,对于本领域普通技术人员来讲,在不付出创造性劳动的前提下,还可以根据这些附图获得其他的附图。图1为本发明一实施例提供的一种圆柱外螺纹螺旋铣削切入轨迹优化方法的流程示意图;图2为半螺旋切入方式下螺纹铣刀的轴向运动示意图;图3为半螺旋切入方式下螺纹铣刀的径向运动示意图;图4为切向切入方式下螺纹铣刀的轴向运动示意图;图5为切向切入方式下螺纹铣刀的径向运动示意图;图6为半螺旋切入方式下优化后的螺纹铣刀的径向运动轨迹示意图;图7为切向切入方式下优化后的螺纹铣刀的轴向运动轨迹示意图;图8为半螺旋切入方式下优化前、后的螺纹铣刀的运动轨迹的三维示意图;图9为半螺旋切入方式下优化前、后的螺纹铣刀的运动轨迹在x-y平面的投影示意图;图10为半螺旋切入方式下优化前、后的螺纹铣刀的运动轨迹在x-z平面的投影示意图;图11为半螺旋切入方式下优化前、后的螺纹铣刀的运动轨迹在y-z平面的投影示意图;图12为切向切入方式下优化前、后的螺纹铣刀的运动轨迹的三维示意图;图13为切向切入方式下优化前、后的螺纹铣刀的运动轨迹在x-y平面的投影示意图;图14为切向切入方式下优化前、后的螺纹铣刀的运动轨迹在x-z平面的投影示意图;图15为切向切入方式下优化前、后的螺纹铣刀的运动轨迹在y-z平面的投影示意图;具体实施方式下面将结合本发明实施例中的附图,对本发明实施例中的技术方案进行清楚、完整地描述,显然,所描述的实施例仅仅是本发明一部分实施例,而不是全部的实施例。基于本发明中的实施例,本领域普通技术人员在没有作出创造性劳动前提下所获得的所有其他实施例,都属于本发明保护的范围。参见图1,其为本发明一实施例提供的一种圆柱外螺纹螺旋铣削切入轨迹优化方法的流程示意图。本发明实施例提供的一种圆柱外螺纹螺旋铣削切入轨迹优化方法适用于多轴机床采用螺纹铣刀20加工圆柱外螺纹10(参见图2至图5)。所述多轴机床可例如为三轴(x-y-z)联动及以上(例如四轴甚至五轴)数控机床。螺纹铣刀20可例如为多齿侧铣螺纹铣刀。圆柱外螺纹10可例如为三角形螺纹(即普通螺纹)。具体地,请参阅图1至图7,本发明实施例提供的一种圆柱外螺纹螺旋铣削切入轨迹优化方法包括:步骤x1获取待加工圆柱外螺纹10的尺寸参数例如大径d、小径d1和螺距p、以及螺纹铣刀20的尺寸参数例如大径d。具体地,在得知圆柱外螺纹10的尺寸例如公称直径(大径d)和螺距p后,可通过计算得到小径d1。根据螺距p计算螺纹牙型的原始三角形高度h,计算式为:根据圆柱外螺纹10的大径d和螺纹牙型的原始三角形高度h计算圆柱外螺纹小径d1,计算式为:当然也可通过查询相关手册或者标准获取圆柱外螺纹10的小径d1。步骤x2,基于螺距p、小径d1和大径d确定外螺纹加工轨迹的螺旋半径rt。典型的,在螺纹铣刀20加工圆柱外螺纹10之前,需要规划和确定螺纹铣刀20的运动轨迹。螺纹铣刀20的运动轨迹例如指的是螺纹铣刀20底部端面中心点的运动轨迹,其可例如包括外螺纹铣削切入轨迹、外螺纹加工轨迹、外螺纹铣削切出轨迹。如图2至图5所示,r1为外螺纹加工轨迹,其为以经过o1点的z轴为轴线的螺旋线,r2为半螺旋切入轨迹,其为以经过o2点的垂直于x-y平面的直线为轴线的螺旋线,r3为切向切入轨迹,其为经过a点的平行y-z平面的直线,外螺纹加工轨迹r1分别与半螺旋切入轨迹r2和切向切入轨迹r3相连于过渡点a。根据圆柱外螺纹10的小径d1和螺纹铣刀20的大径d计算外螺纹加工轨迹r1的螺旋半径rt,计算式为:步骤x3,基于大径d和大径d确定外螺纹铣削切入方式。外螺纹铣削的切入方式例如包括直接径向切入方式、切向切入方式和螺旋切入方式。外螺纹铣削的切入方式不同,则其切入轨迹也不相同。本发明为简化说明,后续实施例仅举例对半螺旋切入方式和切向切入方式的切入轨迹进行优化。根据圆柱外螺纹10的大径d和螺纹铣刀20的大径d确定外螺纹铣削切入方式。参见图2和图3,当时,外螺纹铣削切入方式为半螺旋切入方式,半螺旋切入轨迹r2在在x-y平面内的投影为以o2为中心的半圆弧。此时,半螺旋切入轨迹r2上任意一点k(螺纹铣刀20底部端面中心点)与半螺旋切入轨迹r2的中心o2的连线ko2与x轴正向的夹角α2(简称为螺旋切入夹角α2)满足:0<α2<π,所述外螺纹铣削切入轨迹的螺旋半径rp满足:rp=ert(4)其中,e为满足的任意值。参见图4和图5,当时,外螺纹铣削切入方式为切向切入方式,切向切入轨迹r3在x-y平面和y-z平面的投影分别为垂直于z轴和平行y轴的直线段。切向切入轨迹r3在x-y平面投影的直线段上任意一点f到a点的距离t(简称为位移变量t)满足:0<t<f。其中f为满足的任意值。当时,外纹铣削切入方式可为半螺旋切入方式和切向切入方式两者中的任意一种。步骤4,计算外螺纹铣削切入轨迹。具体地,当外螺纹铣削切入方式为半螺旋切入方式时,根据半螺旋切入方式下半螺旋切入轨迹r2的螺旋半径rp、外螺纹加工轨迹r1的螺旋半径rt、螺旋切入夹角α2以及螺距p,建立半螺旋切入轨迹r2的数学模型n(α2)以计算半螺旋切入轨迹r2,计算式为:结合图3以及计算式(5)可以看出,给定半螺旋切入轨迹r2任意一点k的螺旋切入夹角α2,即可得到螺旋切入轨迹r2任意一点k的坐标也即半螺旋切入轨迹r2任意一点k的位移。当外螺纹铣削切入方式为切向切入方式时,根据切向切入方式下切向切入轨迹r3的位移变量t和外螺纹加工轨迹r1的螺旋半径rt建立切向切入轨迹r3的数学模型n(t)以计算切向切入轨迹r2,计算式为:结合图5以及计算式(6)可以看出,给定螺旋切入轨迹r2任意一点f的位移变量t,即可得到切向切入轨迹r3任意一点f的坐标也即切向切入轨迹r3任意一点f的位移。如图3和图5所示,在x-y平面内,外螺纹加工轨迹r1的圆心为o1。外螺纹加工轨迹r1任意一点t的轴向位移(z轴方向位移)由t点到圆心o1的连线to1与x轴正向的夹角α1确定。而螺旋切入轨迹r2的圆心为o2,螺旋切入轨迹r2任意一点k的轴向位移由k点的螺旋切入夹角α2确定。切向切入轨迹r3的轴向位移为0。因此,在外螺纹加工轨迹r1分别与螺旋切入轨迹r2和切向切入轨迹r3的连接过渡点a附近会出现轨迹曲线不光顺的现象,从而导致了螺纹铣刀20在切入时发生干涉,影响了圆柱外螺纹10的加工精度。步骤x5,优化所述外螺纹铣削切入轨迹。将半螺旋切入轨迹r2上任意一点k的轴向位移改为由以o1为顶点的夹角α1(即k点到圆心o1的连线ko1与x轴正方向的夹角)确定,以改变整个螺纹切入轨迹r2的轴向位移,使半螺旋切入轨迹r2和外螺纹加工轨迹r1的轴向位移均由同一变量α1确定,使半螺旋切入轨迹r2的螺旋线倾斜角与外螺纹加工轨迹r1的螺旋线倾斜角的值尽可能接近,且减少铣刀切入时的干涉。因此,如图6所示,当外螺纹铣削切入方式为半螺旋切入方式时,修改后的半螺旋切入轨迹r2的计算式为:根据外螺纹铣削加工原理分析螺纹铣刀20的运动轨迹与圆柱外螺纹10的轴线之间的几何关系,得到α1与α2的转换公式。因此,当所述外螺纹铣削切入方式为半螺旋切入方式时,优化后的半螺旋切入轨迹r2的计算式为:将切向切入轨迹r3改为与y轴成一定角度,以改变整个切向切入轨迹r3的轴向位移,使切向切入轨迹r3的倾斜角与外螺纹加工轨迹r1上a点倾斜角的值相同,以此减少铣刀切入时的干涉。如图7所示,当外螺纹铣削切入方式为切向切入方式时,优化后的切向切入轨迹r3的计算式为:为便于更好地理解本发明实施例,下面以普通圆柱右旋外螺纹m36×2为例详细说明本发明实施例提供的一种圆柱外螺纹螺旋铣削切入轨迹优化方法。1)根据计算式(1)和(2)计算m36圆柱外螺纹的小径d1:2)根据计算式(3)计算外螺纹加工轨迹的螺旋半径rt:3)由于m36螺纹孔大径d=36mm,螺纹铣刀大径d=18mm,d/d=1/2,两种切入方式均可选择。本发明实施例通过两种切入方式计算、优化螺旋切入轨迹。当外螺纹铣削切入方式为半螺旋切入方式时,根据计算式(4)计算半螺旋切入轨迹的螺旋半径rp,取e=2,满足rp=ert=2×25.9175=51.835mm当外螺纹铣削切入方式为半螺旋切入方式时,位移变量t满足:0<t<f,取f=10,满足4)根据计算式(5)和(9)计算外螺纹铣削切入方式为半螺旋切入方式时半螺旋切入轨迹和优化后的半螺旋切入轨迹。如图8、9和10所示,当外螺纹铣削切入方式为半螺旋切入方式时,半螺旋切入轨迹(未优化的半螺旋切入轨迹)为:优化后的半螺旋切入轨迹为:5)根据计算式(6)和(10)计算外螺纹铣削切入方式为切向切入方式时切向切入轨迹和优化后的切向切入轨迹。如图11、12和13所示,当外螺纹铣削切入方式为切向切入方式时,切向切入轨迹(未优化的切向切入轨迹)为:优化后的切向切入轨迹为:分别将半螺旋切入方式和切向切入方式下优化前后的外螺纹铣削切入轨迹与外螺纹加工轨迹在连接过渡点a处的倾斜角进行对比,如表1和表2所示。表1半螺旋切入方式下点a处各轨迹的倾斜角对比表2切向切入方式下点a处各轨迹的倾斜角对比从表1和表2的数据对比可知,与现有技术(优化前的切入轨迹)相比,本发明实施例提供的优化后的外螺纹铣削切入轨迹在a点处倾斜角与外螺纹加工轨迹在a点处倾斜角更加接近,且其轨迹线倾角的相对误差接近于零。所以,从轨迹线倾角的角度分析,本发明实施例提供的圆柱外螺纹螺旋铣削切入轨迹优化方法可有效改善现有技术中过渡点a处轨迹曲线不光顺的现象。进一步地,分别将半螺旋切入方式和切向切入方式下采用本发明实施例提供的圆柱外螺纹螺旋铣削切入轨迹优化方法得到的外螺纹铣削切入轨迹与现有技术得到的切入轨迹在vericut软件中进行加工仿真实验,对各外螺纹铣削切入轨迹的加工误差进行对比,如表3和表4所示。表3半螺旋切入方式下各切入轨迹加工误差对比轨迹最大过切量(mm)优化前切入轨迹0.65优化后切入轨迹0.36表4切向切入方式下各切入轨迹加工误差对比轨迹最大过切量(mm)优化前切入轨迹1.239优化后切入轨迹0.6503从表3和表4可知,经本发明实施例提供圆柱外螺纹螺旋铣削切入轨迹优化方法优化后的两种切入轨迹的最大过切量均小于现有技术中(优化前)的切入轨迹的最大过切量。因此,采用本发明实施例提供的一种圆柱外螺纹螺旋铣削切入轨迹优化方法能减少螺纹铣刀切入时的干涉。当前第1页12