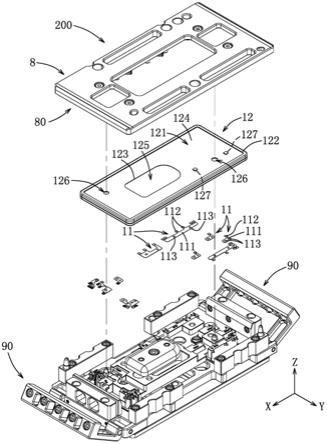
1.本发明涉及一种压合治具,特别是涉及一种用以将料片与工件压合定位以进行后续加工的压合治具。
背景技术:2.现有要进行手机壳与多个弹片之间的焊接时,操作人员需先将手机壳安装于一治具内,随后,将多个弹片依序放置于治具的对应定位槽内,再通过压板将所述弹片压紧于手机壳。之后,便能通过一焊接机将各弹片焊接于手机壳。
3.由于每个弹片、压板以及手机壳的厚度皆存在有制造公差,因此,压板压紧所述弹片时会因为前述制造公差的影响而造成压紧程度不一致,从而影响到后续焊接的效果。此外,由于弹片与定位槽之间存在有组装公差,因此,压板在压紧弹片的过程中会造成弹片于定位槽内晃动,从而影响弹片定位的精准度。再者,由于每个弹片的体积小,因此操作人员放置弹片于治具的定位槽的操作较为不便,且操作人员只能一个接着一个依序将所述弹片放置于治具内,大幅增添了放料的工时,从而造成弹片的组装效率差。
技术实现要素:4.因此,本发明的目的在于提供一种能够克服背景技术的至少一个缺点的压合治具。
5.本发明的目的及解决背景技术问题是采用以下技术方案来实现的,依据本发明提出的压合治具,适于将至少料片压合定位于工件。
6.所述压合治具包括基座、承载板、第一弹簧、承载滑块、第二弹簧及压制机构,所述承载板能够沿上下方向滑动地连接于所述基座并包括用以承载所述工件的第一承载面,所述第一弹簧用以对所述承载板向上施加弹力,所述承载滑块能够沿上下方向滑动地连接于所述基座并包括用以承载所述料片的第二承载面,所述第二弹簧用以对所述承载滑块向上施加弹力,所述第二承载面的高度低于所述第一承载面的高度,且所述料片间隔位于所述工件下方,所述压制机构用以下压所述工件使其先通过所述承载板压缩所述第一弹簧,而后所述工件再压合于所述料片使其通过所述承载滑块压缩所述第二弹簧。
7.本发明的压合治具,所述料片形成有两个相间隔的定位孔,所述承载滑块还包括两个凸设于所述第二承载面且相间隔的定位凸块,所述定位凸块用以卡掣于所述定位孔内。
8.本发明的压合治具,所述承载滑块形成有由所述第二承载面向下凹陷的嵌槽,所述压合治具还包括嵌设于所述嵌槽内用以吸附所述料片的磁铁。
9.本发明的压合治具,所述承载滑块还包括滑块体及凸设于所述滑块体一侧且邻近其底端的侧凸缘,所述基座包括导向板及限位件,所述导向板形成有供所述滑块体穿设的导向孔,所述导向板用以挡止所述侧凸缘以限制所述承载滑块的高度,所述限位件设置于所述导向板用以挡止所述承载板以限制其高度。
10.本发明的压合治具,所述压制机构包括压制模块及两个锁扣模块,所述压制模块包括用以定位于所述基座的定位板、位于所述定位板下方用以下压所述工件的压板及设置于所述定位板与所述压板之间的第三弹簧,所述第三弹簧用以对所述压板向下施加弹力,所述锁扣模块可转动地枢接于所述基座相反侧用以下压并锁扣所述定位板。
11.本发明的压合治具,所述压制模块还包括顶销及第四弹簧,所述顶销穿设于所述压板且部分凸伸出其底端,所述第四弹簧设置于所述定位板与所述顶销之间用以对所述顶销向下施加弹力。
12.本发明的压合治具,所述压制模块还包括多个等高螺丝,所述等高螺丝穿设于所述定位板并螺接于所述压板,所述定位板与所述压板相间隔且两者间形成有间隙。
13.本发明的目的及解决背景技术问题是采用以下技术方案来实现的,依据本发明提出的压合治具,适于将多个料片压合定位于工件。
14.所述压合治具包括基座、承载板、多个第一弹簧、多个承载滑块、多个第二弹簧及压制机构,所述承载板能够沿上下方向滑动地连接于所述基座并包括用以承载所述工件的第一承载面,所述第一弹簧用以对所述承载板向上施加弹力,所述承载滑块能够沿上下方向滑动地连接于所述基座,每一个所述承载滑块包括用以承载对应的所述料片的第二承载面,每一个所述第二弹簧用以对对应的所述承载滑块向上施加弹力,所述第二承载面的高度低于所述第一承载面的高度,且所述料片间隔位于所述工件下方,所述压制机构用以下压所述工件使其先通过所述承载板压缩所述第一弹簧,而后所述工件再压合于所述料片使其通过所述承载滑块压缩所述第二弹簧。
15.本发明的压合治具,所述压制机构包括压制模块,及两个锁扣模块,所述压制模块包括用以定位于所述基座的定位板、位于所述定位板下方用以下压所述工件的压板及多个设置于所述定位板与所述压板之间的第三弹簧,所述第三弹簧用以对所述压板向下施加弹力,所述锁扣模块可转动地枢接于所述基座相反侧用以下压并锁扣所述定位板。
16.本发明的压合治具,所述压制模块还包括多个顶销及多个第四弹簧,所述顶销穿设于所述压板且部分凸伸出其底端,每一个所述第四弹簧设置于所述定位板与对应的所述顶销之间用以对对应的所述顶销向下施加弹力。
17.本发明的有益效果在于:料片能够确实地压紧并定位于工件上,能提升后续焊接的效果。此外,借由承载滑块及磁铁相配合使料片能稳固地定位在承载滑块上,使得工件在压紧料片的过程中料片不会晃动,能提升料片定位于工件的定位精准度。再者,借由料片通过定位片体与一个或一个以上的焊接片体连接的设计方式,能提升操作人员组装操作的方便性以及组装效率。
附图说明
18.图1是本发明压合治具的实施例与工件及多个料片的立体分解图;
19.图2是所述实施例的立体分解图;
20.图3是所述实施例由另一视角观看的立体分解图;
21.图4是所述实施例的不完整俯视图,图中省略压制机构;
22.图5是沿图4中的v-v线所撷取的剖视图;
23.图6是沿图4中的vi-vi线所撷取的剖视图;
24.图7是所述实施例的不完整立体分解图,说明承载滑块与所述料片之间的组装关系;
25.图8是所述实施例的压制模块的立体分解图;
26.图9是所述实施例的所述压制模块的仰视图;
27.图10是沿图9中的x-x线所撷取的剖视图;
28.图11是沿图9中的xi-xi线所撷取的剖视图;
29.图12是所述实施例的不完整俯视图,说明所述料片组装于所述承载滑块上;
30.图13是所述实施例的不完整俯视图,说明所述工件组装于承载架上;
31.图14是沿图13中的xiv-xiv线所撷取的剖视图;
32.图15是沿图13中的xv-xv线所撷取的剖视图;
33.图16是所述实施例的不完整俯视图,说明所述压制模块组装于所述工件上;
34.图17是沿图16中的xvii-xvii线所撷取的剖视图;
35.图18是所述实施例的剖视图;
36.图19是类似于图17的剖视图,说明压板下压所述工件;
37.图20是图18的局部放大图;及
38.图21是类似于图15的剖视图,说明所述工件的焊接凸部压合于所述料片的焊接片体。
具体实施方式
39.下面结合附图及实施例对本发明进行详细说明。
40.在本发明被详细描述之前,应当注意在以下的说明内容中,类似的组件是以相同的编号来表示。
41.参阅图1,是本发明压合治具200的一个实施例,适于将多个料片11压合定位于工件12。每一个料片11为金属材质所制成并具有定位片体111,及至少连接于定位片体111一侧的焊接片体112。在本实施例中,部分的料片11具有一个焊接片体112,而另一部分的料片11具有两个或两个以上的焊接片体112。每一个料片11的定位片体111形成有两个相间隔的定位孔113。
42.工件12是以手机壳为例并具有一呈长板形的基板121,及一形成于基板121外周围的围绕壁122。基板121的长向沿前后方向x延伸并具有底面123及顶面124。基板121形成有邻近中间处的第一定位孔125及两个第二定位孔126,每一个第二定位孔126邻近于对应的角隅处。基板121还具有多个凸设于底面123的焊接凸部127,每一个焊接凸部127用以供对应的焊接片体112焊接。
43.参阅图2、图3及图4,压合治具200包括基座2、承载架3多个第一弹簧4、多个承载滑块5、多个磁铁6,多个第二弹簧7及压制机构8(如图1所示)。基座2包括导向板21、底板22、多个导向销23、多个限位件24、多个螺栓25、两个第一定位销26、两个第二定位销27及两个定位块28。导向板21呈长板形且长向沿前后方向x延伸。导向板21底面向上凹陷形成凹槽211。导向板21顶面向下凹陷形成多个导向孔212、多个开孔213及多个螺孔214,导向孔212、开孔213及螺孔214皆连通于凹槽211顶端且沿上下方向z延伸。导向孔212的数量与承载滑块5的数量相同。所述导向孔212的形状分别与所述承载滑块5的形状相配合且分别供所述承载滑
块5穿设。开孔213的数量与导向销23的数量及第一弹簧4的数量相同。所述开孔213分别供所述导向销23穿设。螺孔214的数量与限位件24的数量及螺栓25的数量相同。所述螺孔214分别供所述螺栓25螺接。
44.底板22呈长板形且长向沿前后方向x延伸并通过螺丝锁固于导向板21底面。底板22形成有多个连通于凹槽211底端的通孔221,所述通孔221分别对应于所述导向板21的开孔213下方。
45.参阅图3、图4及图5,每一个导向销23具有销杆231及凸缘232。销杆231沿上下方向z延伸并穿设于对应的开孔213且部分凸伸出导向板21顶面。凸缘232形成于销杆231外周面且邻近其底端,凸缘232位于凹槽211内且上下两端分别被导向板21及底板22所夹持,使得导向销23能固定在图5所示的位置。
46.参阅图3、图4及图6,每一个限位件24呈套筒状并具有抵接于导向板21顶面的筒体241及形成于筒体241外周面且位于筒体241顶端的限位周壁242。筒体241形成有连通于对应螺孔214顶端的穿孔243。每一个螺栓25穿设于对应的限位件24的穿孔243并螺接于对应的螺孔214,每一个螺栓25挡止于筒体241顶端以将限位件24锁固于导向板21顶面。
47.参阅图2、图3及图4,每一个第一定位销26固定地设置于导向板21顶面并沿上下方向z延伸,用以穿设于工件12的对应第二定位孔126(如图1所示)。每一个第二定位销27穿设于导向板21且部分凸伸出其顶面并沿上下方向z延伸,第二定位销27底端被导向板21阻挡,以防止第二定位销27向下移动而脱离导向板21。两定位块28通过螺丝锁固于导向板21顶面且分别邻近导向板21的两短边。
48.参阅图3、图4、图5及图6,承载架3包括承载板31及定位块33。承载板31具有底面311、位于顶端且相反于底面311的第一承载面312及两个相反于底面311的平面313。第一承载面312用以承载工件12的基板121(如图1所示)。两平面313沿前后方向x相间隔,且每一个平面313的高度低于第一承载面312的高度。承载板31形成有多个第一阶级孔314,多个第二阶级孔315及两个穿孔316。第一阶级孔314的数量与导向销23的数量相同,每一个第一阶级孔314具有一位于底面311的大孔径部317及位于第一承载面312的小孔径部318,小孔径部318的孔径小于大孔径部317的孔径。每一个导向销23的销杆231经由大孔径部317穿伸至小孔径部318内,通过导向销23的销杆231与小孔径部318相配合,限制承载板31只能沿上下方向z滑动。
49.参阅图3、图4及图6,第二阶级孔315的数量与限位件25的数量相同,每一个第二阶级孔315具有位于底面311的小孔径部320及位于对应的平面313的大孔径部321,大孔径部321的孔径大于小孔径部320的孔径。每一个限位件25穿设于对应的第二阶级孔315内,且限位周壁252用以挡止一位在小孔径部320与大孔径部321之间的肩面322,以控制承载板31往上滑动的高度。
50.每一个穿孔316供对应的第一定位销26穿设,每一个第一定位销26部分凸伸出承载板31的第一承载面312。定位块33通过螺丝锁固于承载板31的第一承载面312,定位块33形状与工件12的第一定位孔125(如图1所示)形状相同,用以穿设于第一定位孔125。定位块33的高度高于每一个第一定位销26的高度,使得工件12组装于承载架33的过程中,定位块33能先穿设于第一定位孔125内以初步导正并定位工件12。
51.参阅图3、图5及图6,第一弹簧4的数量与导向销23的数量相同,每一个第一弹簧4
为一套设于对应的导向销23的销杆231的压缩弹簧。每一个第一弹簧4底端抵接于导向板21顶面,而顶端则抵接于位于大孔径部317与小孔径部318之间的肩面319,用以对承载板31向上施加弹力以使承载板31往上浮。通过每一个第一弹簧4对承载板31向上施加弹力,使得承载板31恒保持并定位在肩面322抵接于限位周壁252的第一初始高度位置(如图6所示)。当承载板31在第一初始高度位置时,底面311与导向板21顶面之间形成有第一间隙g1,前述第一间隙g1界定承载板31相对于导向板21向下移动的行程。借此,使得承载板31可沿上下方向z相对于基座2滑动。
52.参阅图3、图4、图6及图7,每一个承载滑块5包括滑块体51、两个定位凸部52及两个侧凸缘53。滑块体51具有滑块部511及至少支撑肋条512。滑块体51的滑块部511穿设于对应导向孔212且部分凸伸出导向板21顶面,由于滑块体51的滑块部511经由横向剖切后的形状与对应导向孔212的形状相同且相配合,且两者皆呈非圆形,因此,限制滑块体51只能沿上下方向z滑动而不会在滑动过程中发生转动的情形。滑块部511界定出开槽513,开槽513位于底板22的对应通孔221上方。支撑肋条512呈长条形且凸设于滑块部511一侧并位于开槽513内,支撑肋条512顶端与滑块部511顶端齐平且两者共同界定出用以承载对应料片11的第二承载面514。第二承载面514具有由滑块部511所界定的第一面部515及由支撑肋条512所界定出的第二面部516。第一面部515用以承载对应料片11的定位片体111,第二面部516用以承载对应料片11的焊接片体112。两个定位凸部52凸设于第二承载面514的第一面部515且相间隔,两定位凸部52用以分别卡掣于对应料片11的两定位孔113内,借此,使得料片11不会相对于承载滑块5水平转动或移动。此外,第二承载面514的第一面部515向下凹陷形成有至少一个嵌槽517,用以供对应的磁铁6嵌设于内。磁铁6通过磁力吸附对应料片11的定位片体111以防止其向上移动。借此,使得料片11能稳固地定位在第二承载面514上。
53.两侧凸缘53分别凸设于滑块体51的滑块部511的两相反侧,两侧凸缘53位于导向板21的凹槽211内。导向板21底面用以挡止侧凸缘53,以控制承载滑块5往上滑动的高度。
54.参阅图3及图6,每一个承载滑块5的一底面518向上凹陷形成有至少两个容置槽519。每一个第二弹簧7为一容置于对应的容置槽519内的压缩弹簧。每一个第二弹簧7底端抵接于底板22顶面,而顶端则抵接于承载滑块5,用以对承载滑块5向上施加弹力以使承载滑块5往上浮。通过每一个第二弹簧7对承载滑块5向上施加弹力,使得承载滑块5恒保持并定位在侧凸缘53抵接于导向板21底面的一第二初始高度位置(如图6所示)。当承载滑块5在第二初始高度位置时,底面518与底板22顶面之间形成有第二间隙g2,前述第二间隙g2界定承载滑块5相对于底板22向下移动的行程。借此,使得承载滑块5可沿上下方向z相对于基座2滑动。此外,承载滑块5的第二承载面514在第二初始高度位置的高度低于承载架3的第一承载面312在第一初始高度位置的高度。
55.需说明的是,由于本实施例中部分的料片11的焊接片体112的数量为一个,而其余料片11的焊接片体112的数量为一个以上,因此,承载滑块5在设计时会随着所欲承载的料片11形状及焊接片体112数量而有不同的变化。例如本实施例中部分的承载滑块5的支撑肋条512数量为一个,而其余承载滑块5的支撑肋条512数量为一个以上。此外,每一个承载滑块5上的磁铁6数量能视需求设置一个以上,而第二弹簧7数量能视需求设置两个以上。
56.参阅图8、图9、图10及图11,压制机构8包括一压制模块80,及两个锁扣模块90(如图1所示)。压制模块80包括定位板81、压板82、多个螺丝83、多个第三弹簧84、多个顶销85及
多个第四弹簧86。定位板81呈长板形且其长向沿前后方向x延伸,并具有底面811及顶面812。定位板81形成有开孔813、两个定位孔814、多个阶级孔815、多个第一盲孔816及多个第二盲孔817。开孔813、定位孔814及阶级孔815延伸于底面811与顶面812之间。开孔813位于中间处并且用以供定位块33(如图2所示)容置。每一个定位孔814邻近于对应的角隅处用以供对应的第二定位销27(如图4所示)穿设。阶级孔815的数量与螺丝83的数量相同,所述阶级孔815分别供所述螺丝83穿设。每一个阶级孔815具有位于顶面812的大孔径部818,及位于底面811的小孔径部819。第一盲孔816的数量与第三弹簧84的数量相同,所述第一盲孔816排列在开孔813的左右两侧。每一个第一盲孔816是由底面811向上凹陷而成,用以供对应的第三弹簧84上半部容置。第二盲孔817的数量与顶销85的数量及第四弹簧86的数量相同,所述第二盲孔817排列在开孔813的左右两侧。每一个第二盲孔817是由底面811向上凹陷而成,用以供对应的顶销85及第四弹簧86上半部容置。
57.压板82呈长板形且其长向沿前后方向x延伸,并具有压制面821及顶面822。压板82形成有第一定位孔823、两个第二定位孔824、多个螺孔825、多个第三盲孔826及多个穿孔827。第一定位孔823、第二定位孔824、螺孔825及穿孔827延伸于压制面821与顶面822之间。第一定位孔823位在开孔813下方,第一定位孔823与定位块33的形状相同,用以供定位块33穿设。每一个第二定位孔824用以供对应的第一定位销26(如图4所示)穿设。螺孔825的数量与螺丝83的数量相同,所述螺孔825分别供所述螺丝83螺接。第三盲孔826的数量与第三弹簧84的数量相同,所述第三盲孔826排列在第一定位孔823的左右两侧。每一个第三盲孔826是由顶面822向下凹陷而成,用以供对应的第三弹簧84下半部容置。所述穿孔827排列在第一定位孔823的左右两侧。每一个穿孔827用以供对应的顶销85穿设。
58.本实施例的螺丝83是以等高螺丝为例,每一个螺丝83穿设于对应的阶级孔815并螺接于对应的螺孔825,且每一个螺丝83抵接于一位在大孔径部818与小孔径部819之间的肩面820,以控制压板82往下滑动的高度。
59.每一个第三弹簧84为一容置于对应的第一盲孔816及对应的第三盲孔826内的压缩弹簧,其顶底两端分别抵接于定位板81及压板82,用以对压板82向下施加弹力。通过每一个第三弹簧84对压板82向下施加弹力,使得压板82恒保持并定位在螺丝83抵接于肩面820的一第三初始高度位置(如图11所示)。当压板82在第三初始高度位置时,压板82的顶面822与定位板81的底面811之间形成有第三间隙g3,前述第三间隙g3界定定位板81相对于压板82向下移动的行程。借此,使得定位板81可沿上下方向z相对于压板82滑动。
60.每一个顶销85具有销杆851及凸缘852。销杆851穿设于对应的第二盲孔817及对应的穿孔827内,销杆851能沿上下方向z滑动并且部分凸伸出压板82的压制面821。销杆851形成有开口朝上的容置槽853。凸缘852形成于销杆851外周面且邻近其顶端,凸缘852位于对应的第二盲孔817内用以抵接于压板82的顶面822,以防止销杆851脱离穿孔827。
61.每一个第四弹簧86为设置于容置槽853内的压缩弹簧,其顶底两端分别抵接于定位板81及销杆851,用以对顶销85向下施加弹力,以使顶销85保持在如图11所示销杆851底部凸伸出压制面821的凸伸位置。
62.参阅图2,每一个锁扣模块90用以锁扣压制模块80并包括枢接柄91及多个锁扣件92。枢接柄91可转动地枢接于导向板21的位于短边的枢轴215。所述锁扣件92设置于枢接柄91上且沿左右方向y相间隔排列,每一个锁扣件92具有钢珠921及对钢珠921向下施加弹力
的弹簧922(如图18所示)。借此,使得钢珠921能对定位板81(如图8所示)产生锁扣压力。
63.以下将针对压合治具200将料片11压合定位于工件12的操作方式进行详细说明:
64.参阅图7及图12,首先,进行料片11组装于承载滑块5的步骤。将每一个料片11的定位片体111及焊接片体112分别对齐于对应承载滑块5的第二承载面514的第一面部515及第二面部516上方,以及将料片11的两定位孔113分别对齐承载滑块5的两定位凸部52上方。随后,将每一个料片11向下移动并放置于对应的第二承载面514上,使两定位凸部52分别卡掣于两定位孔113,以及磁铁6磁吸料片11的定位片体111。借此,料片11便能稳固地定位在第二承载面514上。由于本实施例的料片11的定位片体111体积大于焊接片体112体积,因此,操作人员通过握持体积较大的定位片体111并且将其组装于承载滑块5的操作过程较为方便。再者,由于本实施例的料片11是通过定位片体111与一个或一个以上的焊接片体112连接,因此,操作人员放料时能同时将一个以上的焊接片体112放置完成,与背景技术相较下能降低操作人员放料的工时以提升焊接片体112的组装效率。
65.参阅图13、图14及图15,接着,进行工件12组装于承载架3的步骤。先将工件12的第一定位孔125及第二定位孔126分别对齐于定位块33及第一定位销26上方。随后,将工件12向下移动,工件12下移过程中,高度较高的定位块33会先穿设于第一定位孔125内。当工件12下移过程中发生偏移而造成界定出第一定位孔125的孔缘触碰到定位块33的一倒圆角面331时,孔缘会沿着倒圆角面331往下移动而被导正位置,借此,定位块33能起到初步导正工件12以达到粗定位的效果。工件12被导正后,紧接着每一个第一定位销26会穿设于对应第二定位孔126内,借以达到精确定位的效果。
66.当基板121的底面123接触到承载板31的第一承载面312时,工件12便不会再继续往下移动。通过第一弹簧4对承载板31向上施加弹力使其恒保持并定位在第一初始高度位置(如图14所示),使得第一承载面312的高度高于第二承载面514的高度。因此,组装完成的基板121会间隔位于每一个料片11上方,且基板121的每一个焊接凸部127会间隔位于对应料片11的焊接片体112上方。此时,基板121的每一个焊接凸部127与对应料片11的焊接片体112顶面之间形成有一第四间隙g4。第四间隙g4小于第一间隙g1。前述第四间隙g4界定出工件12能够相对于料片11向下移动的行程。
67.参阅图16及图17,之后,进行压制模块80的组装步骤。先将压板82的第一定位孔823、第二定位孔824以及定位板81的定位孔814分别对齐于定位块33、第一定位销26以及第二定位销27上方。随候,将压制模块80向下移动,使定位块33、第一定位销26以及第二定位销27分别穿设于第一定位孔823、第二定位孔824以及定位孔814内。当每一个顶销85的销杆851底端接触工件1的基板121的顶面124时,压制模块80便不会再继续往下移动。此时,压板82的压制面821与基板121的顶面124之间形成有第五间隙g5,第五间隙g5界定出压板82向下移动的行程。
68.参阅图18及图19,最后,进行两锁扣模块90的锁扣步骤。先沿第一旋转方向r1及相反于第一旋转方向r1的第二旋转方向r2分别旋转两锁扣模块90的枢接柄91。当每一个锁扣件92旋转到其钢珠921接触定位板81的一连接于顶面812短边侧的侧缘810时,钢珠921施加于定位板81的下压力会促使定位板81往下移动,定位板81往下移动的过程中会通过第三弹簧84推动压板82往下移动,并且同时压缩第四弹簧86。当压板82移动到压制面821接触基板121的顶面124时,定位板81在持续下移的状态下会压缩第三弹簧84并靠近压板82的顶面
822,同时还会持续压缩第四弹簧86。
69.通过第五间隙g5(如图17所示)界定压板82下压移动行程的设计,能消除基板121及压板82厚度的制造公差,使压制面821能够确实压制于基板121的顶面124。此外,通过第三间隙g3(如图10所示)界定定位板81相对于压板82向下移动行程的设计,第三弹簧84被定位板81压缩后能施加更大的弹力于压板82上,能增加压制面821压紧基板121的顶面124的压紧程度。
70.参阅图18、图19、图20及图21,当锁扣件92继续带动定位板81往下移动时,压板82的压制面821及每一个顶销85会将基板121往下压使其往下移动。通过第四间隙g4(如图15所示)界定工件12向下移动的行程,能消除基板121及料片11的焊接片体112厚度的制造公差,使基板121的焊接凸部127能确实压制于料片11的焊接片体112顶面。由于第四间隙g4小于第一间隙g1(如图14所示),因此,当基板121的每一个焊接凸部127压制于对应料片11的焊接片体112顶面时,基板121会通过焊接凸部127带动料片11下移并连动承载滑块5下移而压缩第二弹簧7。通过第二间隙g2(如图6所示)界定承载滑块5相对于底板22向下移动的行程,能消除料片11的焊接片体112厚度的制造公差,以确保焊接凸部127确实压紧于料片11的焊接片体112顶面,并能确保所有的焊接凸部127压紧于所有的焊接片体112上的压紧程度一致。
71.当定位板81抵接于两定位块28并且被其阻挡时,定位板81便无法继续向下移动,此时,锁扣模块90转动到图18所示的锁扣位置。此时,锁扣件92的钢珠921锁扣于定位板81的顶面812,且工件12的焊接凸部127压合定位于料片11的焊接片体112顶面。借由第三弹簧84被压缩所产生的弹力将压板82向下压以及每一个第四弹簧86被压缩时所产生的弹力通过对应的顶销85将压板82向下压,使得工件12的焊接凸部127能够确实地向下压紧于焊接片体112上。借由第二弹簧7被压缩所产生的弹力通过对应的承载滑块5对料片11往上施力,使得焊接片体112能够确实地向上压紧于焊接凸部127上。借此,能确保焊接片体112与焊接凸部127的压紧程度。
72.之后,将压合治具200旋转180度使底板22朝向上方,接着,将压合治具200固定在一支撑架(图未示)上。一激光机(图未示)所产生的激光光束能通过底板22的通孔221以及承载滑块5的开槽513照射至焊接片体112上,以将焊接片体112与焊接凸部127焊接在一起。
73.归纳上述,本实施例的压合治具200,借由第一弹簧4、第二弹簧7及第三弹簧84的设计,使得承载板31、承载滑块5及压板82能够产生伸缩移动的作用,借此,能克服相关组件的制造公差对于压紧程度所造成的影响,使得焊接片体112能够确实地压紧并定位于焊接凸部127上,能提升后续焊接的效果。此外,借由承载滑块5及磁铁6相配合使料片11能稳固地定位在承载滑块5上,使得焊接凸部127在压紧焊接片体112的过程中焊接片体112不会晃动,能提升焊接片体112定位于焊接片体112的定位精准度。再者,借由料片11通过定位片体111与一个或一个以上的焊接片体12连接的设计方式,能提升操作人员组装操作的方便性以及组装效率,确实能达到本发明所诉求的目的。