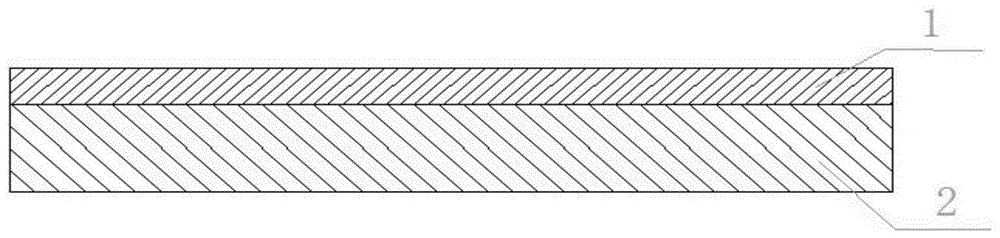
本实用新型涉及电子器件焊接
技术领域:
,特别涉及一种表面预覆软焊料层的被焊件及其制备方法。
背景技术:
:软焊料是液相线温度(熔点)不超过450℃的焊料。软钎焊是通过将软焊料加热到低于被焊件(母材)熔点而高于软焊料熔点的温度而实现连接的一类连接方法。软钎焊工艺,是采用软焊料通过润湿作用铺展在工件表面上,或通过毛细作用铺展在紧密贴合的连接表面上,被广泛应用于轨道交通、通讯电缆、航空航天、家用电器、新能源汽车、风力和光伏发电等各种电子器件领域。目前的软钎焊工艺,主要是后期采用一定的焊接工艺通过软焊料将被焊件之间衔接起来。然而目前的这种软钎焊工艺会带来如下问题:(1)某些被焊件表面极易氧化,在后期软钎焊之前,其被焊表面就已被严重氧化,导致焊接空洞率偏高,不利于达到良好的焊接质量。(2)某些被焊件由于组装工艺的特殊性,客户在后期软钎焊时,被焊件和软焊料之间不便定位,甚至无法定位,容易造成焊点错位,严重的话,会因为错位引起桥连短路。(3)某些被焊件表面没有过渡软焊料层,无法达到良好的焊接效果。(4)某些软焊料外形特殊、较薄或者质软,在包装运输组装过程中,容易变形,给客户使用造成不便,甚至影响焊接质量。(5)某些软焊料外形特殊,无法实现有序包装,客户无法将软焊料进行自动化贴片焊接,大大影响生产效率。(6)某些需要涂覆有助焊剂的软焊料,涂覆时容易变形,或者由于助焊剂有黏性,软焊料彼此之间容易粘连,生产、包装和客户使用不便。技术实现要素:有鉴于此,有必要针对上述现有技术的不足,提供一种表面预覆软焊料层的被焊件及其制备方法。为实现上述第一目的,本实用新型采取以下的技术方案:一种表面预覆软焊料层的被焊件,包括被焊件及其表面上预覆的软焊料层。进一步的,所述被焊件表面材质为铜、镍、银、金、铝中的至少一种。进一步的,所述软焊料层为锡基、铅基、铟基、铋基软焊料中的至少一种。进一步的,所述软焊料层厚度为0.02~0.5mm。进一步的,所述被焊件表面为平面或曲面。进一步的,所述软焊料层表面还包括助焊剂层。为实现上述第二目的,本实用新型采取以下的技术方案:一种表面预覆软焊料层的被焊件的制备方法,包括以下步骤:步骤1)将配置好的软焊料制备成所需厚度的料带;步骤2)将步骤1)中的料带裁剪成与被焊件表面尺寸相当的焊片;步骤3)将步骤2)中的焊片与被焊件组装在一起;步骤4)将步骤3)中组装好的焊片与被焊件,通过加热方式使焊片熔化,进而在被焊件表面形成软焊料层,或者通过物理压合或粘合方式将焊片与被焊件贴合在一起,从而在被焊件表面形成软焊料层。步骤4所述的加热熔化温度应高于焊片的熔点,而低于被焊件的熔点。进一步的,所述加热方式可以为常压回流焊方式、真空回流焊、感应加热焊、热压焊或普通加热台。作为优选的,采用所述常压回流焊方式、感应加热焊、热压焊、普通加热台方式时,在所述步骤2)的焊片上涂上助焊剂进行助焊;采用所述真空回流焊时,焊接过程通过加入甲酸进行助焊。本实用新型在常压环境下加热使被焊件表面形成软焊料层时,加入助焊剂用于去除被焊面和软焊料表面的氧化膜,促进焊接,还可以降低软焊料熔化后的表面张力,起界面活性作用,有助于软焊料在焊接面上的润湿和铺展。焊接完成前,助焊剂还可以保护软焊料和焊接面,防止焊接过程中二次氧化。焊接完成后,助焊剂消耗或者挥发出去,残留很少甚至基本无残留。而在真空环境下加热使被焊件表面形成软焊料层时,则利用甲酸来进行助焊,甲酸可去除被焊面和软焊料表面的氧化膜,促进焊接。本实用新型的有益效果为:(1)被焊件表面因客户软钎焊之前就预覆软焊料层,可以防止被焊件表面被进一步氧化,可以有效地降低焊接空洞率,达到良好的焊接质量。(2)被焊件表面因客户软钎焊之前就预覆软焊料层,客户后期无需再组装软焊料,省去了被焊件和软焊料定位工序,不易造成焊点错位、桥连短路问题。(3)被焊件表面因预覆软焊料层,解决了某些被焊件表面没有过渡软焊料层,无法良好焊接的问题。(4)因将软焊料预覆在被焊件表面形成了软焊料层,客户无需再额外使用软焊料,解决了某些软焊料外形特殊、较薄或者质软,导致在包装运输组装过程中,容易变形,给客户使用造成不便,甚至影响焊接质量的问题。(5)因将软焊料预覆在被焊件表面形成了软焊料层,客户无需再额外使用软焊料,解决了某些软焊料外形特殊,无法实现有序包装,客户无法将软焊料进行自动化贴片焊接的问题,提高了生产效率。(6)因将软焊料预覆在被焊件表面形成了软焊料层后,预覆的软焊料层表面可以涂覆助焊剂,客户无需再额外使用表面涂覆有助焊剂的软焊料,解决了某些需要涂覆有助焊剂的软焊料在涂覆时容易变形,或者由于助焊剂有黏性,软焊料彼此之间容易粘连,产品不便生产、包装和使用的问题。附图说明图1a、图1b、图1c、图1d、图1e、图1f,为一种单面预覆软焊料层的被焊件的局部剖视图;图2a、图2b、图2c和图2d,为一种双面预覆软焊料层的被焊件的局部剖视图;图3为比较例1焊接后样品超声波检测空洞率图,图4为实施例1焊接后样品超声波检测空洞率图,其中图3和图4中白色部分表示焊接空洞,黑色部分表示焊接良好;图5为比较例2焊接后样品超声波检测空洞率图,图6为实施例2焊接后样品超声波检测空洞率图,其中图5和图6中白色部分表示焊接空洞,黑色部分表示焊接良好;图7为实施例2中常压回流焊工艺操作参数曲线图;图8为实施例4中真空甲酸还原回流焊工艺操作参数曲线图;图中:温度曲线为焊接过程的设置温度,氮气和甲酸曲线分别为真空度和充入的气体气压,纵坐标100表示常压,0表示抽真空至所能达到的最低气压;图9为实施例8中常压回流焊工艺操作参数曲线图;图10为实施例9的真空甲酸还原回流焊工艺操作参数曲线图;图中:温度曲线为焊接过程的设置温度,氮气和甲酸曲线分别为真空度和充入的气体气压,纵坐标100表示常压,0表示抽真空至所能达到的最低气压;图11为实施例10的真空甲酸还原回流焊工艺操作参数曲线图;图中:温度曲线为焊接过程的设置温度,氮气和甲酸曲线分别为真空度和充入的气体气压,纵坐标100表示常压,0表示抽真空至所能达到的最低气压。附图标记:1-软焊料层;2-被焊件;3-助焊剂层。具体实施方式为使本实用新型的目的、技术方案和优点更加清晰,下面将结合本实用新型实施例,对本实用新型的技术方案作进一步清晰、完整地描述。需要说明的是,所描述的实施例仅仅是本实用新型的一部分实施例,而非全部实施例。基于本实用新型中的实施例,本领域普通技术人员在未做出创造性劳动前提下所获得的所有其他实施例,都属于本实用新型保护的范围。实施例1图1a中的被焊件2表面材质为铜,软焊料层1成分为铅基焊料中的pb92.5sn5ag2.5,所述软焊料层1厚度为0.06mm,其制备方法,包括以下步骤:步骤1)将配置好的pb92.5sn5ag2.5软焊料通过压延方法制备成所需厚度的料带;步骤2)将步骤1)中的料带裁剪成与被焊件表面尺寸相当的焊片,并在焊片上涂上适合铜件焊接的松香型助焊剂;步骤3)将步骤2)中的焊片与被焊件组装在一起;步骤4)将步骤3)中组装好的焊片与被焊件通过热压焊工艺:在220℃温度下预热30秒,然后用温度为400℃的石墨热压头接触组装好的焊片与被焊件,并保持20秒,待焊片熔化后,移开热压头,然后风冷被焊件至软焊料层凝固,从而使焊片与被焊件冶金结合在一起,在被焊件2表面形成pb92.5sn5ag2.5软焊料层1。实施例2图1b中的被焊件2表面材质为镍,软焊料层1成分为锡基焊料中的sn96.5ag3cu0.5,所述软焊料层1厚度为0.1mm,其制备方法,包括以下步骤:步骤1)将配置好的sn96.5ag3cu0.5软焊料通过压延方法制备成所需厚度的料带;步骤2)将步骤1)中的料带裁剪成与被焊件表面尺寸相当的焊片,并在焊片上涂上适合镀镍件焊接的松香型助焊剂;步骤3)将步骤2)中的焊片与被焊件组装在一起;步骤4)将步骤3)中组装好的焊片与被焊件,通过如图7的常压回流焊工艺使焊片与被焊件冶金结合在一起,在被焊件表面形成sn96.5ag3cu0.5软焊料层。步骤5),在步骤4)中形成的sn96.5ag3cu0.5软焊料层1表面涂有助焊剂层3。实施例3图1c中的被焊件2表面材质为铝,软焊料层1成分为锡基焊料中的sn83.6in8.8zn7.6,所述软焊料层1厚度为0.4mm,其制备方法,包括以下步骤:步骤1)将配置好的sn83.6in8.8zn7.6软焊料通过压延方法制备成所需厚度的料带;步骤2)将步骤1)中的料带裁剪成与被焊件表面尺寸相当的焊片,并在焊片上涂上适合铝件焊接的松香型助焊剂;步骤3)将步骤2)中的焊片与被焊件组装在一起;步骤4)将步骤3)中组装好的焊片与被焊件,通过感应焊工艺:温度控制在230℃~250℃,待焊片熔化后,移开被焊件,然后风冷被焊件至软焊料层凝固,从而使焊片与被焊件冶金结合在一起,在被焊件2表面形成sn83.6in8.8zn7.6软焊料层1。实施例4图1d中的被焊件2表面材质为银,软焊料层1成分为锡基焊料中的sn95sb5,所述软焊料层1厚度为0.2mm,其制备方法,包括以下步骤:步骤1)将配置好的sn95sb5软焊料通过压延方法制备成所需厚度的料带;步骤2)将步骤1)中的料带裁剪成与被焊件表面尺寸相当的焊片;步骤3)将步骤2)中的焊片与被焊件组装在一起;步骤4)将步骤3)中组装好的焊片与被焊件,通过如图8的真空甲酸还原回流焊工艺使焊片与被焊件冶金结合在一起,在被焊件表面形成sn95sb5软焊料层。步骤5),在步骤4)中形成的软焊料层1表面涂覆助焊剂层3。实施例5图1e中的被焊件2表面材质为金,软焊料层1成分为铟基焊料中的in60pb40,所述软焊料层2厚度为0.25mm,其制备方法,包括以下步骤:步骤1)将配置好的in60pb40软焊料通过压延方法制备成所需厚度的料带;步骤2)将步骤1)中的料带裁剪成与被焊件表面尺寸相当的焊片;步骤3)将步骤2)中的焊片与被焊件组装在一起;步骤4)将步骤3)中组装好的焊片与被焊件,利用冲床使焊片与被焊件压合在一起,在被焊件2表面形成in60pb40软焊料层1。实施例6图1f中的被焊件2表面材质为镍,软焊料层1成分为锡基焊料中的sn63pb37,所述软焊料层1厚度为0.2mm,其制备方法,包括以下步骤:步骤1)将配置好的sn63pb37软焊料通过压延方法制备成所需厚度的料带;步骤2)将步骤1)中的料带裁剪成与被焊件表面尺寸相当的焊片,并在焊片上涂上助焊剂;步骤3)将步骤2)中的焊片与被焊件组装在一起;步骤4)将步骤3)中组装好的焊片与被焊件,通过适合镀镍件焊接的并具有黏性的助焊剂,将焊片与被焊件粘合在一起,在被焊件表面形成sn63pb37软焊料层。步骤5),在步骤4)中形成的软焊料层1表面涂覆助焊剂层3。实施例7图2a中的被焊件2表面双面材质均为铜,两面软焊料层1成分均为铅基焊料中的pb88sn10ag2,所述软焊料层1厚度为0.1mm,其制备方法,包括以下步骤:步骤1)将配置好的pb88sn10ag2软焊料通过压延方法制备成所需厚度的料带;步骤2)将步骤1)中的料带裁剪成与被焊件表面尺寸相当的焊片;步骤3)将步骤2)中的焊片与被焊件组装在一起;步骤4)将步骤3)中组装好的焊片与被焊件,利用冲床使焊片与被焊件压合在一起,在被焊件2两面均形成pb88sn10ag2软焊料层1。实施例8图2b中的被焊件2表面材质一面为铜,一面为镍。其中,铜层外面的软焊料层1成分为锡基焊料中的sn96.5ag3.5,软焊料层1厚度为0.2mm;镍层外面的软焊料层1成分为锡基焊料中的sn99.3cu0.7,软焊料层1厚度为0.15mm,其制备方法,包括以下步骤:步骤1)分别将配置好的sn96.5ag3.5软焊料和sn99.3cu0.7软焊料通过压延方法制备成所需厚度的料带;步骤2)将步骤1)中的料带分别裁剪成与被焊件表面尺寸相当的焊片,并在sn96.5ag3.5成分的焊片上涂上适合铜件焊接的松香型助焊剂,在sn99.3cu0.7成分的焊片上涂上适合镀镍件焊接的松香型助焊剂;步骤3)将步骤2)中的焊片与被焊件组装在一起;步骤4)将步骤3)中组装好的焊片与被焊件,通过如图9的常压回流焊工艺使焊片与被焊件冶金结合在一起,在被焊件两面分别形成0.2mm厚的sn96.5ag3.5软焊料层和0.15mm厚的sn99.3cu0.7软焊料层。步骤5),在步骤4)中形成的软焊料层1表面涂覆助焊剂层3。实施例9图2c中的被焊件2表面材质一面为铜,一面为金。其中,铜层外面的软焊料层1成分为铋基焊料中的sn77.2in20ag2.8,软焊料层1厚度为0.2mm;金层外面的软焊料层1成分为铟基焊料中的in60pb40,软焊料层1厚度为0.05mm,其制备方法,包括以下步骤:步骤1)分别将配置好的sn77.2in20ag2.8软焊料和in60pb40软焊料通过压延方法制备成所需厚度的料带;步骤2)将步骤1)中的料带分别裁剪成与被焊件表面尺寸相当的焊片;步骤3)将步骤2)中的焊片与被焊件组装在一起;步骤4)将步骤3)中组装好的焊片与被焊件,通过如图10的真空甲酸还原回流焊工艺使焊片与被焊件冶金结合在一起,在被焊件两面分别形成0.2mm厚的sn77.2in20ag2.8软焊料层和0.05mm厚的in60pb40软焊料层。实施例10图2d中的被焊件2表面材质一面为镍,一面为银。其中,镍层外面的软焊料层1成分为铟基焊料中的in97ag3,软焊料层1厚度为0.2mm;银层外面的软焊料层1成分为铋基焊料中的sn42bi57ag1,软焊料层1厚度为0.1mm,其制备方法,包括以下步骤:步骤1)分别将配置好的in97ag3软焊料和sn42bi57ag1软焊料通过压延方法制备成所需厚度的料带;步骤2)将步骤1)中的料带分别裁剪成与被焊件表面尺寸相当的焊片;步骤3)将步骤2)中的焊片与被焊件组装在一起;步骤4)将步骤3)中组装好的焊片与被焊件,通过如图11的真空甲酸还原回流焊工艺使焊片与被焊件冶金结合在一起,在被焊件两面分别形成0.2mm厚的in97ag3软焊料层和0.15mm厚的sn42bi57ag1软焊料层。步骤5),在步骤4)中形成的软焊料层1表面涂覆助焊剂层3。为进一步验证本实用新型效果,以下对本实用新型的表面预覆软焊料层的被焊件进行焊接空洞率检测试验:实验例1样品基本情况和实验过程:比较例1:市售表面未预覆软焊料层的被焊件,即2mm厚的无氧铜板。焊接方式:两块无氧铜板中间夹0.12mm厚的pb92.5sn5ag2.5合金成分的焊片,进行真空甲酸回流焊工艺焊接。本实用新型实施例1:实施例1的表面预覆软焊料层的被焊件,即市售的2mm厚的无氧铜板表面预覆0.06mm厚的pb92.5sn5ag2.5软焊料层。焊接方式:两块表面预覆有0.06mm厚的软焊料层的无氧铜板,软焊料层对软焊料层叠放,然后进行真空甲酸回流焊工艺焊接,以确保焊后的焊缝高度与比较例1相同。焊接面积:比较例1和实施例1的焊接面积均是38.5mm*31.5mm。检测空洞率设备:超声波检测仪。比较例1和本实用新型实施例1各焊接20组数据,然后采用超声波检测仪分别检测焊接空洞率,记录,计算各组平均值。结果见表1。表1实施例1和比较例1检测结果编号(比较例1)焊接空洞率(%)编号(实施例1)焊接空洞率(%)1#1.7921#0.612#1.5222#0.763#1.7523#0.524#1.6724#0.685#1.9025#0.736#1.9126#0.587#1.3327#0.778#1.9228#0.659#1.8829#0.6110#1.6630#0.7511#1.6231#0.7212#1.4832#0.6713#1.8133#0.7514#1.9434#0.7815#1.6335#0.7416#1.7336#0.5817#1.9437#0.7518#1.7638#0.6919#1.8039#0.5320#1.4340#0.71平均值1.72平均值0.68为了更直观的表示焊接空洞率结果对比,图3和图4分别为比较例1和实施例1样品,进行焊接后的超声波检测空洞率图,其中图3和图4中白色部分表示焊接空洞,黑色部分表示焊接良好。对比可明显看出,本实用新型的表面预覆软焊料层的被焊件焊接空洞率明显少于未预覆软焊料层的被焊件,表明表面预覆软焊料层后的被焊件的焊接质量明显优于未预覆软焊料层的被焊件的焊接质量。实验例2样品基本情况和实验过程:比较例2:市售表面未预覆软焊料层的被焊件,即1.5mm厚的镀镍陶瓷板。焊接方式:两块镀镍陶瓷板中间夹0.2mm厚的sn96.5ag3cu0.5合金成分的焊片,焊片两面各涂覆0.5%含量的助焊剂,然后进行常压回流焊工艺焊接。本实用新型实施例2:实施例2的表面预覆软焊料层的被焊件,即市售的1.5mm厚的镀镍陶瓷板表面预覆有0.1mm厚的sn96.5ag3cu0.5软焊料层,并在软焊料层表面涂覆与比较例同款助焊剂,助焊剂含量0.5%,以确保焊接前助焊剂含量与比较例助焊剂含量相同。焊接方式:两块表面预覆有0.1mm厚的软焊料层的镀镍陶瓷板,软焊料层对软焊料层叠放,然后进行常压回流焊工艺焊接,以保证焊后的焊缝高度与比较例2相同。焊接面积:比较例2和实施例2的焊接面积均是57mm*48.5mm。检测空洞率设备:超声波检测仪。比较例2和本实用新型实施例2各焊接20组数据,然后采用超声波检测仪分别检测焊接空洞率,记录,计算各组平均值。结果见表2。表2实施例2和比较例2检测结果编号(比较例2)焊接空洞率(%)编号(实施例2)焊接空洞率(%)1#12.3721#6.742#12.1822#6.663#12.6223#6.114#13.624#6.615#14.5325#6.756#14.3126#6.797#15.5127#7.008#14.9828#7.229#13.1429#6.7610#14.5830#6.0411#12.1731#6.8112#14.0732#6.9013#12.8433#7.1014#13.3434#7.0215#14.8735#6.8416#16.1436#6.3517#12.5137#7.4018#13.1138#7.0819#14.7339#6.7720#15.1140#7.03平均值13.84平均值6.80为了更直观的表示焊接空洞率结果对比,图5和图6分别为比较例2和实施例2样品,进行焊接后的超声波检测空洞率图,其中图5和图6中白色部分表示焊接空洞,黑色部分表示焊接良好。对比可明显看出,本实用新型的表面预覆软焊料层的被焊件焊接空洞率明显少于未预覆软焊料层的被焊件,表明表面预覆软焊料层后的被焊件的焊接质量明显优于未预覆软焊料层的被焊件的焊接质量。以上所述实施例仅表达了本实用新型的几种实施方式,其描述较为具体和详细,但并不能因此理解为对本实用新型专利范围的限制。应当指出的是,对于本领域的普通技术人员来说,在不脱离本实用新型构思的前提下,还可做出若干变形和改进,这些均属于本实用新型的保护范围。因此,本实用新型专利的保护范围应以所附权利要求为准。当前第1页12