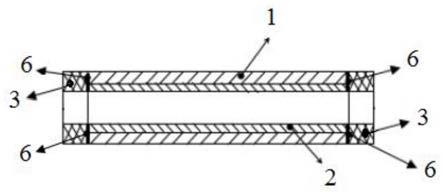
1.本发明涉及管材制备技术领域,特别是涉及一种双金属复合管的制备方法。
背景技术:2.目前油气等化石能源仍然是主要使用的能源种类,但是易于开发的化石能源越来越少,油气田开采不得不向更加深层次的地层,环境更加恶劣的地区发展。随着一些高酸性油气不断的开发,高酸性环境中的co2,h2s等对油气运输造成了很大的困难。传统运输的低碳管线钢由于其耐蚀性较差,极易失效造成介质泄漏事故。如若采用不锈钢镍基合金等耐蚀合金作为运输管线,其成本将会极大的增加。因此,双金属复合管以优异的性能和较高的性价比获得快速的发展,目前,国内多家油田单位广泛的使用双金属复合管,而且逐渐由陆地管线发展到海底管线。双金属复合管还在化工、水利、环保以及海水淡化等领域得到了广泛地应用。
3.双金属复合管采用机械或冶金等方法制备。机械结合制备方法有拉拔复合法、包覆式焊接法以及压力胀合法等。冶金结合制备方法有离心铸造法、热加工法(挤压、轧制)、扩散复合法、钎焊法以及爆炸焊接法。冶金结合制备方法均存在着工艺难度大、成本高、成材率低、管型控制差等方面的不足。同时,机械结合制备方法存在机械复合管的结合界面易分层,焊接性较差,低硬度金属、薄覆层金属管等难以制造的问题。由于机械复合法制备的复合管层间有间隙,因此,涉及管端头封焊的问题,专利cn104197104b、cn107143703b、cn105817780b等均采用在复合管两端开坡口,然后堆焊的方式将基层管与覆层管焊接在一起,过程复杂,难度大。
技术实现要素:4.为解决以上技术问题,本发明提供一种双金属复合管的制备方法,制备过程简单方便,工艺难度低,制备效率高。
5.为实现上述目的,本发明提供了如下方案:
6.本发明提供一种双金属复合管的制备方法,包括以下步骤:
7.步骤一、进行原料准备,准备一个基层管、一个覆层件和两个封头,所述覆层件与所述基层管长度相同,所述基层管与所述覆层件的材质不同,所述封头与所述覆层件的材质相同;
8.步骤二、将所述覆层件由所述基层管的一端嵌入得到复合体,并将两个所述封头分别与所述复合体两端进行点焊得到两端点焊的复合体;
9.步骤三、将两端点焊的复合体放入电子束焊机内,抽真空,并采用电子束焊接的方法将两个所述封头与所述复合体的两端焊接加固得到复合坯件;
10.步骤四、将所述复合坯件进行塑性加工得到复合管;
11.步骤五、对所述复合管进行热处理并矫直得到成品双金属复合管。
12.优选地,在步骤一中,所述覆层件为覆层管,所述封头为环状封头;在步骤三中得
到的复合坯件为复合管坯;在步骤四中,将所述复合管坯进行挤压和轧制得到所述复合管,轧制方式为热轧或冷轧。
13.优选地,所述环状封头的长度为20~50mm,所述环状封头的外径与所述基层管的外径相同,所述环状封头的壁厚等于所述基层管的壁厚、所述覆层管的壁厚以及所述基层管和所述覆层管之间的间隙之和。
14.优选地,在步骤四中,所述复合管坯挤压时的加热温度为980℃~1100℃,所述复合管坯挤压时的保温时间为t1,所述复合管坯的厚度值为d1,t1的数值范围为(d1×
0.8)~(d1×
0.8+120)。
15.优选地,在步骤一中,所述覆层件为覆层棒,所述封头为圆饼状封头;在步骤三中得到的复合坯件为复合棒坯;在步骤四中,将所述复合棒坯进行斜轧穿孔和轧制得到所述复合管,轧制方式为热轧或冷轧。
16.优选地,所述圆饼状封头的长度为20~50mm,所述圆饼状封头的外径与所述基层管的外径相同。
17.优选地,在步骤四中,所述复合棒坯斜轧穿孔时的加热温度为1000℃~1250℃,所述复合棒坯斜轧穿孔时的保温时间为t2,所述复合棒坯的厚度值为d2,t2的数值范围为(d2×
0.8)~(d2×
0.8+120)。
18.优选地,在步骤二中,所述基层管与所述覆层件之间的间隙≤0.5mm。
19.优选地,在步骤三中,抽真空至10
‑1~10
‑2pa,焊接电流为200~300ma,焊接电压为60~85kv,焊接速度为200~400mm/s,焊接深度为70~100mm。
20.优选地,所述基层管的材质为碳钢或低合金钢,所述覆层件的材质为不锈钢、镍合金、铜或铜合金。
21.本发明相对于现有技术取得了以下技术效果:
22.本发明提供的双金属复合管的制备方法,先准备一个基层管、一个覆层件和两个封头,覆层件与基层管长度相同,基层管与覆层件的材质不同,封头与覆层件的材质相同,然后将覆层件由基层管的一端嵌入得到复合体,并将两个封头分别与复合体两端进行点焊得到两端点焊的复合体,抽真空,并采用电子束焊接的方法将两个封头与复合体的两端焊接加固得到复合坯件,将复合坯件进行塑性加工得到复合管,对复合管进行热处理并矫直得到成品双金属复合管。本发明中采用真空电子束焊接以实现管端头封焊,无需开坡口,简化操作步骤,焊接工艺难度低;采用塑性加工的方法制备双金属复合管,实现基层与覆层之间的冶金结合,使得制备过程简单方便,制备效率高。
附图说明
23.为了更清楚地说明本发明实施例或现有技术中的技术方案,下面将对实施例中所需要使用的附图作简单地介绍,显而易见地,下面描述中的附图仅仅是本发明的一些实施例,对于本领域普通技术人员来讲,在不付出创造性劳动的前提下,还可以根据这些附图获得其他的附图。
24.图1为本发明的实施例一中复合管坯的制备过程示意图;
25.图2为本发明的实施例三中复合棒坯的制备过程示意图;
26.图3为本发明的实施例一中316l不锈钢/紫铜合金复合管结合界面金相图;
27.图4为本发明的实施例三中x65钢/inconel825镍合金复合管结合界面宏观图。
28.附图标记说明:1、基层管;2、覆层管;3、环状封头;4、覆层棒;5、圆饼状封头;6、电子束焊接面。
具体实施方式
29.下面将结合本发明实施例中的附图,对本发明实施例中的技术方案进行清楚、完整地描述,显然,所描述的实施例仅仅是本发明一部分实施例,而不是全部的实施例。基于本发明中的实施例,本领域普通技术人员在没有做出创造性劳动前提下所获得的所有其他实施例,都属于本发明保护的范围。
30.本发明的目的是提供一种双金属复合管的制备方法,制备过程简单方便,工艺难度低,制备效率高。
31.为使本发明的上述目的、特征和优点能够更加明显易懂,下面结合附图和具体实施方式对本发明作进一步详细的说明。
32.实施例一:
33.如图1所示,本实施例提供一种双金属复合管的制备方法,包括以下步骤:
34.步骤一、进行原料准备,准备一个基层管1、一个覆层件和两个封头,覆层件与基层管1长度相同,基层管1与覆层件的材质不同,封头与覆层件的材质相同;
35.步骤二、复合体制备,将覆层件由基层管1的一端嵌入得到复合体,并将两个封头分别与复合体两端进行点焊得到两端点焊的复合体;
36.步骤三、复合坯件制备,将两端点焊的复合体放入电子束焊机内,抽真空,并采用电子束焊接的方法将两个封头与复合体的两端焊接加固得到复合坯件,封头与复合体之间形成电子束焊接面6;
37.步骤四、复合管制备,将复合坯件进行塑性加工得到复合管;
38.步骤五、对复合管进行热处理并矫直得到成品双金属复合管。
39.本发明中采用真空电子束焊接以实现管端头封焊,与现有技术中在复合管两端开坡口并进行堆焊的方式相比,无需开坡口,简化操作步骤,焊接工艺难度低;采用塑性加工的方法制备双金属复合管,实现基层与覆层之间的冶金结合,使得制备过程简单方便,制备效率高,适用范围广。具体地,先采用点焊将封头与复合体初步固定,再采用电子束焊接的方法将两个封头与复合体的两端焊接牢固,实现了封头与复合体的牢固连接。
40.具体地,在步骤一中,覆层件为覆层管2,封头为环状封头3;在步骤三中得到的复合坯件为复合管坯;在步骤四中,将复合管坯进行挤压和轧制得到复合管,轧制方式为热轧或冷轧。
41.具体地,环状封头3的长度为20~50mm,环状封头3的外径与基层管1的外径相同,环状封头3的壁厚等于基层管1的壁厚、覆层管2的壁厚以及基层管1和覆层管2之间的间隙之和。
42.在步骤四中,复合管坯挤压时的加热温度为980℃~1100℃,复合管坯挤压时的保温时间为t1,复合管坯的厚度值为d1,t1的数值范围为(d1×
0.8)~(d1×
0.8+120)。
43.在步骤二中,基层管1与覆层件之间的间隙≤0.5mm。
44.在步骤三中,抽真空至10
‑1~10
‑2pa,焊接电流为200~300ma,焊接电压为60~
85kv,焊接速度为200~400mm/s,焊接深度为70~100mm。
45.具体地,基层管1的材质为碳钢或低合金钢,覆层件的材质为不锈钢、镍合金、铜或铜合金。
46.于本具体实施例中,在步骤一中,准备φ350
×
35.8
×
1000mm的316l不锈钢管作为基层管1,准备φ277.7
×
34.9
×
1000mm的紫铜合金管作为覆层管2,准备两个φ350
×
71.05
×
20mm的紫铜合金环作为封头。在步骤二中,将紫铜合金管从316l不锈钢管的一端嵌入得到复合体,然后将两个紫铜合金环分别点焊在复合体两端。在步骤三中,将点焊后的复合体放入电子束焊机内,抽真空至10
‑2pa,采用电子束焊接的方法将两个紫铜合金环与复合体的两端焊牢,焊接电流为200ma,焊接电压70kv,焊接速度400mm/s,焊接深度71.05mm,得到φ350
×
71.05
×
1060mm的316l不锈钢/紫铜合金复合管坯。在步骤四中,将复合管坯进行950℃加热,保温55~175min,然后进行挤压得到φ280
×
14mm的半成品管,再进行冷轧,得到φ219
×7×
13000mm的316l不锈钢/紫铜合金复合管,其中覆层厚度为3mm,如图3所示,316l不锈钢/紫铜合金复合管结合良好。该复合管可作为海水淡化装置的取水管道或海水热交换器用管。
47.实施例二:
48.本实施例中所采用的覆层件为覆层管2,于本具体实施例中,在步骤一中,准备φ260
×
51.7
×
2000mm的16mn钢管作为基层管1,准备φ155.9
×
21.5
×
2000mm的inconel625镍合金管作为覆层管2,准备两个φ260
×
73.55
×
30mm的inconel625镍合金环作为封头。在步骤二中,将inconel625镍合金管从16mn钢管的一端嵌入得到复合体,并将两个inconel625镍合金环分别点焊在复合体两端。在步骤三中,将点焊后的复合体放入电子束焊机内,抽真空至10
‑2pa,将两端封头焊牢,焊接电流为260ma,焊接电压60kv,焊接速度200mm/s,焊接深度73.55mm,得到φ260
×
73.55
×
2000mm的16mn钢/inconel625镍合金复合管坯。在步骤四中,将复合管坯进行1100℃加热,保温58~178min,然后进行挤压+轧制,得到φ133
×
13
×
12000mm的16mn钢/inconel625镍合金复合管,其中覆层厚度为3mm。该复合管可用做石油、天然气输送管。
49.实施例三:
50.如图2所示,本实施例与实施例一的区别在于所采用的覆层件为覆层棒4,具体地,在步骤一中,选择覆层棒4作为覆层件,封头为圆饼状封头5;在步骤三中得到的复合坯件为复合棒坯;在步骤四中,将复合棒坯进行斜轧穿孔和轧制得到复合管,轧制方式为热轧或冷轧。
51.具体地,圆饼状封头5的长度为20~50mm,圆饼状封头5的外径与基层管1的外径相同。
52.在步骤四中,复合棒坯斜轧穿孔时的加热温度为1000℃~1250℃,复合棒坯斜轧穿孔时的保温时间为t2,复合棒坯的厚度值为d2,t2的数值范围为(d2×
0.8)~(d2×
0.8+120)。
53.于本具体实施例中,在步骤一中,准备φ200
×
70.5
×
1000mm的x65钢管作为基层管1,准备φ58.6
×
1000mmmm的inconel825镍合金棒作为覆层棒4,准备两个φ200
×
50mm的inconel825镍合金棒作为封头。在步骤二中,将φ58.6mm的inconel825镍合金棒从x65钢管的一端嵌入得到复合体,然后将两个φ200的inconel825镍合金棒分别与复合体的两端点
焊。在步骤三中,将复合体放入电子束焊机内,抽真空至10
‑1pa,将两端封头焊牢,焊接电流为300ma,焊接电压80kv,焊接速度300mm/s,焊接深度100mm,得到x65钢/inconel825镍合金复合棒坯。在步骤四中,将复合棒坯进行1250℃加热,保温160~280min,然后进行斜轧穿孔+轧制,得到φ168
×
16
×
12000mm的x65钢/inconel825镍合金复合管,其中覆层厚度为3mm,如图4所示,x65钢/inconel825镍合金复合管结合良好。该复合管可用做石油、天然气输送管。
54.实施例四:
55.本实施例中所采用的覆层件为覆层棒4,于本具体实施例中,在步骤一中,准备φ260
×
79.8
×
2000mm的q235钢管作为基层管1,准备φ100
×
2000mm的316l不锈钢棒作为覆层棒4,准备两个φ260
×
50mm的316l不锈钢棒作为封头。在步骤二中,将φ100的316l不锈钢棒从q235钢管的一端嵌入得到复合体,然后将两个φ260的316l不锈钢棒分别点焊在复合体的两端。在步骤三中,将复合管放入电子束焊机内,抽真空至10
‑2pa,将两端封头焊牢,焊接电流为300ma,焊接电压85kv,焊接速度200mm/s,焊接深度100mm,得到q235钢/316l不锈钢复合棒坯。在步骤四中,将复合棒坯进行1000℃加热,保温160~280min,然后进行斜轧穿孔+轧制,得到φ219
×
15
×
11000mm的q235钢/316l不锈钢复合管,其中覆层厚度为3mm。该复合管可用做石油、天然气输送管及油井复合管。
56.本说明书中应用了具体个例对本发明的原理及实施方式进行了阐述,以上实施例的说明只是用于帮助理解本发明的方法及其核心思想;同时,对于本领域的一般技术人员,依据本发明的思想,在具体实施方式及应用范围上均会有改变之处。综上,本说明书内容不应理解为对本发明的限制。