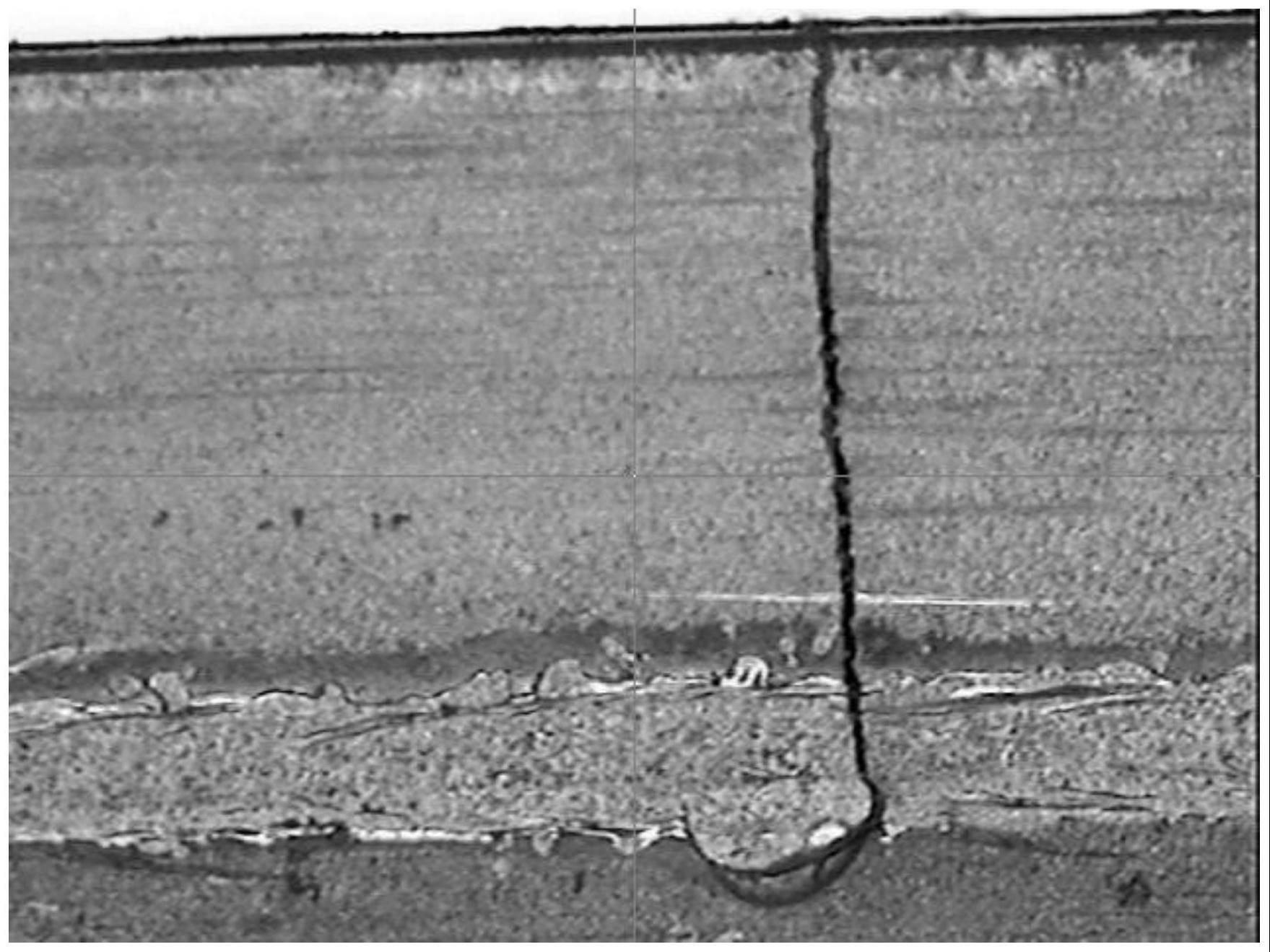
1.本发明涉及带锯条技术领域,特别是一种带锯条制造方法及带锯条。
背景技术:2.双金属带锯条是一种带状连续锯切工具,其外观尺寸对使用性能有非常大的影响,其中龟背主要影响锯切断面的垂直度,龟背过大极易造成切偏失效,因此双金属带锯条对龟背有严格要求。分齿量精度也是一个重要尺寸因素,分齿量公差过大不仅容易造成切偏,还容易造成切断面粗糙、锯切崩断等问题,大大降低带锯条的寿命。
3.双金属带锯条的锯齿为高合金钢,通常为高速钢,背部为高强度钢,通常为高强度弹簧钢,其为将高速钢钢丝和弹簧钢钢带通过激光焊或电子束焊结合在一起,然后通过铣齿、分齿、热处理等工序加工而成。比如公开号为cn106695268a的专利公开了一种双金属带锯的加工工艺,将锯背材料与锯齿材料激光焊接,然后进行光亮退火处理,利用二辊轧机焊缝进行平整处理,调平校直,反复挤压,定长备料后得到盘带,然后进行铣齿加工,齿材清洗、分齿加工、淬火处理、深冷处理,二次回火处理后进行滚轧校直、喷砂处理、喷码处理、根带对焊,得到双金属带锯。
4.在激光焊或电子束焊后,通常需要进行退火处理,目前通常采用的方式为将复合钢带盘卷后放入退火炉中进行整体退火。由于钢带在盘卷后会产生变形,如宽度方向会产生不平,即龟背,但此时的变形为弹性变形。但退火后这种变形将会被保留下来,形成永久变形,因此通常复合钢带在退火后需要进行调平校直处理。但此时钢丝仍呈连续状位于钢带的一侧或两侧,如果调平校直的压力过大,极易造成钢丝和焊缝开裂,如图1所示。为确保此时的调平校直后钢丝和焊缝不开裂,调平校直的压力需严格控制,但这样无法完全消除已形成的龟背,或者龟背虽可消除,但复合钢带的内应力无法消除。此时的内应力如果保留至淬火工序,在淬火后内应力将得到释放,这样极易重新形成龟背变形。这是龟背的形成的主要原因之一。通过加大调平校直的压力可以有效减小内应力,但如上所述,又极易造成复合钢带的钢丝和焊缝开裂。
5.双金属复合钢带为将高速钢钢丝和弹簧钢钢带通过激光焊或电子束焊结合的复合钢带,其中高速钢钢丝分布于弹簧钢钢带的一侧,钢带另一侧为钢带本体,没有高速钢钢丝。这样,钢带两侧的应力状态将会不同。为保证铣齿时的加工精度,通常铣齿前双金属复合钢带呈直线状,而将双金属复合钢带加工成双金属带锯条需将复合钢带的钢丝侧加工成锯齿形状,这样钢丝侧的应力得到释放,其结果是铣齿后双金属带锯条的刀弯发生变化,造成刀弯过大。铣齿后需将双金属带锯条进行分齿,通常的分齿为成组分齿,如果带锯条刀弯过大,一组齿内各个锯齿的夹持高度不同,其结果就是一组齿内各个锯齿的分齿量、分齿角度各不相同,造成分齿量公差过大。
6.双金属复合钢带铣齿时铣齿铣刀为单方向运动,这样铣齿后双金属带锯条的一侧容易形成加工毛刺(在文献《aspects of burr formation in bandsaw teeth manufactured by milling operation》有详细说明毛刺的成因),尤其在齿尖一侧容易残
留毛刺,而该位置即为带锯条分齿时分齿头击打或分齿量测量时顶针接触的位置,因此齿尖位置的残留毛刺势必对分齿时分齿量的精度造成影响。尤其单边的毛刺将造成分齿量不对称的问题。图2为铣齿后的侧边毛刺。
技术实现要素:7.本发明所要解决的技术问题是,针对现有技术不足,提供一种带锯条制造方法及带锯条,使淬火后的龟背、s弯变形得到很好的控制,并提高分齿的精度和对称度,从而提高了带锯条的质量和成材率。
8.为解决上述技术问题,本发明所采用的技术方案是:一种带锯条制造方法,包括以下步骤:将铣齿后的双金属带锯条依次进行调平校直、分齿、淬火、回火、表面处理,进而加工成双金属带锯条;
9.双金属带锯条在调平校直过程中,双金属带锯条表面温度升高,调平校直后双金属带锯条表面温度升高25
‑
50℃。
10.因铣齿时钢丝侧的应力得到释放,铣齿后双金属带锯条的刀弯发生变化,造成刀弯过大,为了保证分齿精度,需在铣齿和分齿之间增加调平校直工序,但是仅在铣齿和分齿之间增加调平校直工序仅能解决提高分齿精度的问题,不能解决龟背的问题。本发明不仅在铣齿和分齿之间增加了调平校直工序,而且研发出来适合带锯条制造的调平校直工艺参数。通常的调平校直将刀弯作为主要的控制参数,本技术将双金属带锯条调平校直后表面温度的升高作为控制参数,不仅可提高分齿精度,而且可有效改善龟背问题。
11.其中双金属带锯条调平校直后表面温度升高25
‑
50℃是指(双金属带锯条调平校直后表面温度)
‑
(双金属带锯条调平校直前表面温度)=25
‑
50℃。
12.进一步地,双金属带锯条调平校直后表面温度升高35
‑
50℃以上。
13.进一步地,调平校直采用的装置为调平辊,调平辊的出口间隙与带锯条厚度一致,调平辊的入口间隙小于出口间隙。出口间隙与带锯条厚度一致,使带锯条在调平辊的出口端不承受压力。调平辊的入口间隙小于出口间隙,是带锯条在入口端承受较大的压力,这样带锯条从入口至出口通过调平辊的过程中承受的压力逐渐减小至零,实现带状材料的校直。与此同时,由于带锯条在调平辊之间承受了压力,并且在调平辊中反复弯曲变形,使带锯条在通过调平辊的变形后表面温度升高。
14.如图3所示,调平辊的入口间隙指的是调平辊第一个辊与第二个辊之间的距离b,调平辊的出口间隙指的是调平辊最后一个辊与倒数二个辊之间的距离c。
15.进一步地,调平辊的入口间隙小于出口间隙的60%。在实际生产应用时,我们是依据带锯条通过调平辊后的温度进行判定,因此这里的方案也是根据温度进行判定。温度是判定间隙调整是否合适的原则。
16.进一步地,双金属带锯条调平校直后刀弯为
±
0.6mm/1000mm。使双金属带锯条保持较小的刀弯,或者没有刀弯(即带锯条成直线状),这可以有效提高后续分齿的精度。
17.进一步地,调平校直所采用的装置包括依次设置的导向机构、调平辊、驱动轮和刀弯检测装置,调平校直工序具体包括以下步骤:牵引双金属带锯条盘卷的料头依次通过导向机构、调平辊、驱动轮、刀弯检测装置。如果带锯条有过大的弯曲从而无法使料头固定于收料机上(收料机设置于刀弯检测装置之后),则需调整调平辊左右两侧的压下量,使带锯
条弯曲程度在合理范围内。此时无需保证带锯条必须呈直线状,因为在生产时刀弯检测装置可将检测结果反馈于调平辊进行调整。
18.进一步地,导向机构包括垫块,分别与所述垫块固定的上滚轮座、下滚轮座,所述上滚轮座上安装有上滚轮,所述下滚轮座上安装有下滚轮,水平展开的带锯条从所述上滚轮与所述下滚轮之间通过,并由所述上滚轮与所述下滚轮驱动,带锯条的底边沿着所述垫块侧面移动,带锯条的锯齿端朝向所述导向机构外侧。垫块侧面对带锯条的底边起定位作用。
19.进一步地,所述上滚轮、所述下滚轮所在平面与带锯条前进方向的夹角为a,夹角a不超过5
°
。使带锯条存在一个往垫块方向的力,这样可以使带锯条通过底边定位。
20.本发明还公开了一种利用上述带锯条制造方法制造的带锯条。
21.与现有技术相比,本发明所具有的有益效果为:
22.1)采用发明制造的带锯条,很好的减小甚至消除了带锯条的内应力,从而使淬火时由于内应力释放造成的变形很小,使龟背、s弯等淬火后的变形得到很好的控制,大大提高了带锯条的成材率。
23.2)采用发明制造的带锯条,确保了分齿前带锯条保持直线状态,使分齿时一组齿内各个锯齿的夹持高度和分齿模打击位置一致,从而大大提高了分齿质量的稳定性。
24.3)采用发明制造的带锯条,完全消除了分齿前带锯条的侧边毛刺,从而大大提高了分齿工序的分齿量精度。
附图说明
25.图1为现有带锯条制造工艺造成的钢丝和焊缝开裂。
26.图2为现有带锯条制造工艺造成的铣齿后的侧边毛刺。
27.图3为本发明中调平辊的结构示意图。
28.图4为本发明一实施例中导向机构的结构示意图。
29.图5为图4的俯视图。
30.图6为本发明一实施例的锯齿照片。
具体实施方式
31.1)一种双金属带锯条的制造工艺路线:将铣齿后的双金属带锯条先进行调平校直,然后进行分齿、清洗、淬火、回火、表面处理,进而加工成双金属带锯条。即:铣齿——调平校直——分齿——清洗——淬火——回火——表面处理。分齿前若有必要可进行绕卷以使带锯条反向。此处的表面处理包括辊压和喷砂的其中一道或两道工序。
32.铣齿之前的工序与现有技术一致,均为将锯背材料与锯齿材料激光焊接,然后进行光亮退火处理,利用二辊轧机焊缝进行平整处理,调平校直。
33.2)上述工艺路线中除调平校直外,其余工序均可采用通用的双金属带锯条加工工艺和方法制造。其中调平校直工序的具体操作方法:
34.a)将铣齿后的双金属带锯条盘卷装上放料机,并用挡圈固定。
35.b)牵引双金属带锯条盘卷的料头依次通过导向机构、调平辊、驱动轮、刀弯检测装置、自由端,然后固定于收料机上。刀弯为
±
0.6mm/1000mm。
36.此时注意在牵引料头通过调平辊时要使带锯条大致呈直线状。如果带锯条有过大的弯曲从而无法使料头固定于收料机上,则需调整调平辊左右两侧的压下量,使带锯条弯曲程度在合理范围内。此时无需保证带锯条必须呈直线状,因为在生产时刀弯检测装置可将检测结果反馈于调平辊进行调整。
37.调整调平辊的入口间隙和出口间隙,调整原则为:出口间隙与带锯条厚度一致,使带锯条在调平辊的出口端不承受压力;入口间隙小于出口间隙,使带锯条在通过调平辊的变形后表面温度升高25℃以上。
38.在实际生产应用时,我们是依据带锯条通过调平辊后的温度进行判定,因此这里的方案也是根据温度进行判定。温度是判定间隙调整是否合适的原则。
39.3)如图4
‑
5所示,导向机构包括垫块1,分别通过螺栓8与所述垫块1固定的上滚轮座2、下滚轮座3,所述上滚轮座2上安装有上滚轮4,所述下滚轮座3上安装有下滚轮5,水平放置的带锯条从所述上滚轮4与所述下滚轮5之间通过,并由所述上滚轮4与所述下滚轮5驱动,带锯条6的底边7沿着所述垫块1移动,带锯条6的锯齿端9朝向所述导向机构外侧。所述上滚轮4、所述下滚轮5所在平面与水平面垂直,所述上滚轮4、所述下滚轮5所在平面与带锯条前进方向(图4中箭头方向)的夹角为a,夹角a不超过5
°
。特点是:锯条的底边与垫块接触,锯齿部分不与任何部件接触,上滚轮和下滚轮与锯条运行方向呈最大不超过5
°
的角度,使带锯条存在一个往垫块方向的力,这样可以使带锯条通过底边定位。
40.4)采用上述方法加工的带锯条产品,特点是:龟背为带锯条宽度的0.5
‰
,锯齿两侧无毛刺,分齿量精度为
±
0.02mm以内。
41.实施例1
42.采用本发明的方法将1000m铣齿后的67*1.6
‑
1/1.5tpi规格带锯条进行调平校直,其入口间隙为0.5mm,出口间隙为1.6mm,入口间隙为出口间隙的31%。调平校直后表面温度升高40℃,刀弯为0.3mm/1000mm。然后进行分齿、清洗、淬火和回火工序的加工,加工后带锯条龟背平均0.028mm,最大值0.05mm,合格率100%(合格标准为0.07mm)。分齿量最大值与最小值的差值为0.03mm。
43.采用上述方法加工的双金属带锯条,特点是龟背<宽度的0.8
‰
,分齿量波动<0.03mm,如图6所示,锯齿无侧边毛刺。
44.对比例1
45.将1000m铣齿后的67*1.6
‑
1/1.5tpi规格带锯条直接进行分齿、清洗、淬火和回火工序的加工,加工后带锯条龟背平均0.054mm,最大值0.10mm,合格率71%(合格标准为0.07mm)。分齿量最大值与最小值的差值为0.07mm。
46.对比例2
47.将1000m铣齿后的67*1.6
‑
1/1.5tpi规格带锯条进行调平校直,其入口间隙为1.2mm,出口间隙为1.6mm,入口间隙为出口间隙的75%,调平校直后的温度仅升高10℃,调平校直后刀弯为0.3mm/1000mm。然后进行分齿、清洗、淬火和回火工序的加工。加工后带锯条龟背平均0.048mm,最大值0.09mm,合格率78%(合格标准为0.07mm)。分齿量最大值与最小值的差值为0.03mm。
48.从上述对比可见,采用本发明方法加工带锯条可有效改善龟背问题,并提高分齿精度。而如果不对调平校直后的温升进行控制,虽然可改善分齿精度,但龟背问题仍无法彻
底解决。