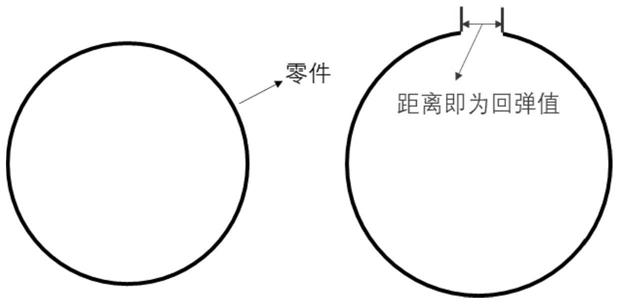
一种提高7a85合金挤压薄板大尺寸筒形零件成形精度的处理方法
技术领域
1.本发明涉及一种提高7a85合金挤压薄板大尺寸筒形零件成形精度的处理方法,属于变形铝合金工业化技术领域,具体为一种利用喷淋淬火、蠕变时效及超声振动结合来提高7a85合金挤压薄板大尺寸筒形零件成形精度的处理方法。
背景技术:2.al-zn-mg-cu合金(7xxx系铝合金)具有良好的加工性能,并且密度小,比强度高,是铝合金中强度最高的合金,被广泛应用于航空航天领域,如7075合金被应用于b-29型轰炸机、7085合金被应用于机翼主梁、上翼蒙皮等。7a85合金是我国自主研发的广泛应用于航空和航天中的受力结构件的al-zn-mg-cu合金。近年来航空航天装备轻量化和高可靠性制造的发展趋势对7a85合金加工性能提出了更高的要求,亟需提高该合金的成形精度,尤其是7a85合金板材,同时保证其力学性能。7a85合金板材的塑性加工工艺包括挤压和轧制,热处理工艺包括退火、固溶、淬火和时效等,在7a85合金板材塑性加工和热处理过程中(如挤压、轧制、淬火)会产生较大的残余应力,而残余应力是有害的,会引起零件发生翘曲或扭曲变形,甚至开裂等,对7a85合金板材零件的成形精度和可靠性具有很大的影响。本方法中的残余应力由x射线法测得,由于残余应力会使晶粒间距和晶面方向发生变化,样品的x射线会发生偏移,通过偏移量便可以计算出残余应力的大小。
3.郭世贵等人的研究表明喷淋淬火能提高7050铝合金(al-zn-mg-cu合金)厚板的淬透性(郭世贵.7050铝合金材料喷淋淬火的试验与模拟研究[d].中南大学,2010.)。任伟才等人的研究表明对于7000系铝合金厚板,喷淋淬火冷却强度大,所需时间短,均匀性好(任伟才,张磊,孙兆霞.7000系铝合金厚板喷淋淬火的数值模拟与分析[j].黑龙江科技学院学报,2010,20(2):124-126.)。辛志文等人的研究表明当7075铝合金(al-zn-mg-cu合金)板厚低于30mm时,喷淋淬火所产生的残余应力很小(辛志文.7075铝合金厚板淬火残余应力及其敏感性分析[d].南昌航空大学.)。陈康华等人优化了喷淋淬火工艺,使铝合金的残余应力降低(陈康华,娄瑾,陈送义,等.一种时效硬化型铝合金低残余应力的多级喷淋淬火工艺:,cn104195481a[p].2016.)。目前有一些关于al-zn-mg-cu合金喷淋淬火工艺的研究,但是没有关于7a85合金喷淋淬火工艺的研究,也没有为了提高7a85合金薄板零件成形精度而应用喷淋淬火工艺的研究。
[0004]
蠕变时效是将铝合金的人工时效与零件成形融为一体的工艺,也就是说通过时效处理使材料具有所要的性能,同时利用材料在弹性应作用下于人工时效温度发生蠕变变形获有设计形状的工件。黄霖等人利用有限元abaqus软件分析了7b04铝合金厚板的弯曲蠕变过程及回弹效应(黄霖,万敏,黄硕,等.7b04铝合金厚板蠕变时效成形有限元分析[j].航空制造技术,2007.)。陈愿情等人的研究表明与人工时效相比,蠕变时效试样的抗拉强度略有提高(陈愿情,邓运来,万里,等.蠕变时效对7050铝合金板材组织与性能的影响[j].材料工程,2012(1):71-76.)。目前还没有关于7a85合金蠕变时效的研究,也没有为了提高7a85合
金薄板零件成形精度而应用蠕变时效的研究。
[0005]
王壬炎的研究表明超声振动时效能更好地消除金属杆件的残余应力(王壬炎.超声振动时效消除残余应力机理分析与实验研究[d].太原理工大学,2014.)。张磊的研究表明超声振动时效对小型工件的残余应力的消除有很明显的效果(张磊,王时英.超声振动时效可行性分析及实验研究[j].机械设计与制造,2013(07):140-143.)。时效时超声振动有利于减小残余应力,但是目前没有关于7a85合金超声振动时效的研究,也没有为了提高7a85合金薄板零件成形精度而应用超声振动时效的研究。
[0006]
到目前为止还未见如何在保证大尺寸7a85合金挤压薄板大尺寸筒形零件的力学性能和可靠性的同时,提高零件的成形精度的相关报道。
技术实现要素:[0007]
为了在保证大尺寸7a85合金挤压薄板大尺寸筒形零件的力学性能和可靠性的同时,提高零件的成形精度,本发明提供了一种利用喷淋淬火、蠕变时效及超声振动结合来提高7a85合金挤压板材大尺寸筒形零件成形精度的处理方法。
[0008]
本发明一种提高7a85合金挤压薄板大尺寸筒形零件成形精度的处理方法;包括下述步骤:
[0009]
步骤一挤压成形:对7a85合金铸锭进行挤压,得到3~8mm的7a85合金薄板。步骤一中所用方法包括常规方法。
[0010]
步骤二退火处理:对7a85合金挤压薄板进行退火处理。步骤二中所用方法包括常规方法。
[0011]
步骤三固溶处理:对步骤二的薄板进行固溶处理,固溶处理时控制温度为460~477℃、保温时间为0.8~3h;
[0012]
步骤四喷淋淬火:对步骤三得到的薄板进行喷淋淬火,喷水压力为190~205kpa,水流密度为45~60l
·
m-2
·
s-1
,持续时间为8~17s。
[0013]
步骤五滚弯:
[0014]
对步骤四所得薄板进行滚弯处理,得到滚弯后的产品;
[0015]
步骤六超声振动蠕变时效:
[0016]
将步骤五的滚弯后的产品放入限位模具中,然后在蠕变时效的过程中辅以超声振动,得到零件;超声振动的频率为1.8~2.0khz,振幅为18~25μm,时间为13~20min,蠕变时效的温度为145~160℃,时间为20~30h;超声振动的引入节点包括在中间相转变时引入超声振动。
[0017]
步骤一中7a85合金的各元素含量分别为:zn:7.0~8.0wt%;mg:1.5~2.3wt%;cu:1.5~2.3wt%;zr:0.09~0.18wt%;fe:《0.05wt%;ti:《0.05wt%;si:《0.05%;al:余量。
[0018]
步骤一中挤压成形时铸锭预热温度为440~455℃,挤压温度为420~435℃,挤压比为30:1~40:1,挤压速度为2~2.5mm/s。
[0019]
步骤二中退火处理时退火温度为340~360℃,时间为28~32h。
[0020]
本发明所得零件的直径可为1.5m~2.3m。
[0021]
本发明零件的高度可达1m~1.3m。
[0022]
作为优选方案;本发明在蠕变时效5~12h时后,引入超声振动。
[0023]
超声振动的频率为1.85~2.0khz,振幅为19~21μm,时间为15~20min
[0024]
本发明一种提高7a85合金挤压薄板零件成形精度的处理方法;步骤六所得零件的抗拉强度大于580mpa,伸长率大于10%,残余应力小于48mpa,回弹小于等于10mm。
[0025]
本发明由于7a85薄板较大,很容易导致板材受热不均,产生应力且组织不均匀,所以使用喷淋淬火,如果这一步处理得不好,会导致零件力学性能不够,即使用寿命很短,甚至开裂,零件制不出来。
[0026]
本发明将滚弯处理工艺设置在喷淋之后时效之前,是因为:时效处理之后合金强度很高,滚弯难度大;在喷淋淬火之前滚弯,会导致淬火更加不均匀,残余应力更大,组织更不均匀,淬火之后只会有固溶强化,合金的强度不是很高,滚弯具有可操作性,所以在喷淋淬火之后时效之前滚弯。同时,滚弯又会使零件内部产生较大的残余应力,所以要通过后续的超声振动+蠕变时效来大幅减小残余应力,减小回弹值,提高成形精度。
[0027]
本发明如果纯属做时效的话,零件的回弹值还是滚弯时的回弹值甚至更大,所以需要将零件放到限位模具(即零件模具)里面进行时效,即蠕变时效,时效的过程中会有一部分应力的释放,但释放程度有限,时效的主要目的是增加合金中的析出相,提高强度,所以需要加入超声振动来进一步释放应力。
[0028]
本发明超声振动有两个目的:一个是可以释放应力,一个是可以提供一定的能量,促使gp区转变为强化效率更高的析出相(如η”和η’相)。
[0029]
在本发明的蠕变时效过程中,析出相的变化大致为两个阶段,第一阶段形成gp区,这个阶段时很容易实现,即使是将合金放在室温条件下一段时间也可以得到gp区,第二阶段是gp区转变为强化效率更高的析出相,这个阶段必须要在高温的人工时效的情况下才会发生,转变相对困难,然后析出相长大,尺寸相对稳定,达到最大的强化效率。所以我们不用在时效刚开始形成gp区时即本法明的时效前期加入振动,而应该在gp区向强化效率更高析出相转变的过程中即本发明的时效中期加入,一个是可以达到基本相同的释放应力的效果,一个是可以为相转变提供部分能量,促进析出相转变,如果是在析出相长大过程中即本发明的时效后期加入振动的话,没有促进析出相转变的这个作用,效果不够好。但是振动的时间如果太长,对零件模具的伤害会比较大,会大大缩减使用寿命,所以时间不宜过长。
[0030]
本发明具有如下优点:
[0031]
(1)在提高大尺寸7a85合金挤压薄板零件成形精度的同时,不影响其力学性能和可靠性。
[0032]
(2)经过本发明中的喷淋淬火、蠕变时效及超声振动处理,7a85合金挤压大尺寸薄板(3~8mm)零件的抗拉强度大于580mpa,伸长率大于10%,残余应力减小小于48mpa(优化后可达小于40mpa),成形精度大幅提高,回弹减小到小于10mm(优化后可达小于6mm)。
附图说明
[0033]
附图1回弹值表示方法;
[0034]
附图2拉伸试样尺寸;
[0035]
附图3模具示意图。
[0036]
本发明中的成形精度由回弹值表示,如附图1所示,回弹值越大,表明成形精度越
差,回弹值越小,表明成形精度越好。
[0037]
本发明中的力学性能由室温拉伸实验测得,拉伸试样的尺寸如附图2所示。
具体实施方式
[0038]
本发明所例举的实施例和对比例中,退火处理的条件为:温度为345℃,时间为29h。
[0039]
实施例一:
[0040]
(1)步骤一挤压成形:按常规方法对7a85合金铸锭进行挤压,得到5mm的7a85合金薄板;
[0041]
(2)步骤二退火处理:按照常规方法对7a85合金挤压薄板进行退火处理;
[0042]
(3)步骤三固溶处理:对步骤二的薄板进行固溶处理,固溶处理时控制温度为475℃、保温时间为1h;
[0043]
(4)步骤四喷淋淬火:对步骤三得到的薄板进行喷淋淬火,喷水压力为200kpa,水流密度为50l
·
m-2
·
s-1
,持续时间为12s;
[0044]
(5)步骤五滚弯;
[0045]
(6)步骤六超声振动蠕变时效:
[0046]
将步骤五的零件放入零件模具中(即限位模具)进行蠕变时效,蠕变时效的温度为155℃,时间为28h,在进行到5h时进行超声振动,超声振动的频率为1.85khz,振幅为20μm,时间为15min。
[0047]
经过上述处理,7a85合金挤压薄板零件的抗拉强度为580mpa,伸长率为13%,残余应力为48mpa,回弹值为10mm。所述零件的直径为2m、高度为1.1m。
[0048]
实施例二:
[0049]
(1)步骤一挤压成形:按常规方法对7a85合金铸锭进行挤压,得到5mm的7a85合金薄板;
[0050]
(2)步骤二退火处理:按照常规方法对7a85合金挤压薄板进行退火处理;
[0051]
(3)步骤三固溶处理:对步骤二的薄板进行固溶处理,固溶处理时控制温度为475℃、保温时间为1h;
[0052]
(4)步骤四喷淋淬火:对步骤三得到的薄板进行喷淋淬火,喷水压力为200kpa,水流密度为50l
·
m-2
·
s-1
,持续时间为12s;
[0053]
(5)步骤五滚弯;
[0054]
(6)步骤六超声振动蠕变时效:将步骤五的零件放入零件模具中进行蠕变时效,蠕变时效的温度为155℃,时间为28h,在进行到5h时进行超声振动,超声振动的频率为1.95khz,振幅为20μm,时间为15min。
[0055]
经过上述处理,7a85合金挤压薄板零件的抗拉强度为590mpa,伸长率为11%,残余应力为40mpa,回弹值为7mm。所述零件的直径为2m、高度为1.1m。
[0056]
实施例三:
[0057]
(1)步骤一挤压成形:按常规方法对7a85合金铸锭进行挤压,得到5mm的7a85合金薄板;
[0058]
(2)步骤二退火处理:按照常规方法对7a85合金挤压薄板进行退火处理;
[0059]
(3)步骤三固溶处理:对步骤二的薄板进行固溶处理,固溶处理时控制温度为475℃、保温时间为1h;
[0060]
(4)步骤四喷淋淬火:对步骤三得到的薄板进行喷淋淬火,喷水压力为200kpa,水流密度为50l
·
m-2
·
s-1
,持续时间为12s;
[0061]
(5)步骤五滚弯;
[0062]
(6)步骤六超声振动蠕变时效:将步骤五的零件放入零件模具中进行蠕变时效,蠕变时效的温度为165℃,时间为28h,在进行到5h时进行超声振动,超声振动的频率为1.85khz,振幅为20μm,时间为15min。
[0063]
经过上述处理,7a85合金挤压薄板零件的抗拉强度为595mpa,伸长率为10.5%,残余应力为45mpa,回弹值为9mm。所述零件的直径为2m、高度为1.1m。实施例四:
[0064]
(1)步骤一挤压成形:按常规方法对7a85合金铸锭进行挤压,得到5mm的7a85合金薄板;
[0065]
(2)步骤二退火处理:按照常规方法对7a85合金挤压薄板进行退火处理;
[0066]
(3)步骤三固溶处理:对步骤二的薄板进行固溶处理,固溶处理时控制温度为475℃、保温时间为1h;
[0067]
(4)步骤四喷淋淬火:对步骤三得到的薄板进行喷淋淬火,喷水压力为200kpa,水流密度为50l
·
m-2
·
s-1
,持续时间为12s;
[0068]
(5)步骤五滚弯;
[0069]
(6)步骤六超声振动蠕变时效:将步骤五的零件放入零件模具中进行蠕变时效,蠕变时效的温度为155℃,时间为30h,在进行到5h时进行超声振动,超声振动的频率为1.85khz,振幅为20μm,时间为15min。
[0070]
经过上述处理,7a85合金挤压薄板零件的抗拉强度为585mpa,伸长率为11.9%,残余应力为47mpa,回弹值为10mm。所述零件的直径为2m、高度为1.1m。
[0071]
实施例五:
[0072]
其他条件和实施例一一致,不同之处在于:步骤六超声振动蠕变时效:将步骤五的零件放入零件模具中进行蠕变时效,蠕变时效的温度为155℃,时间为28h,在进行到5h时进行超声振动,超声振动的频率为1.85khz,振幅为20μm,时间为20min。
[0073]
经过上述处理,7a85合金挤压薄板零件的抗拉强度为588mpa,伸长率为11.5%,残余应力为40mpa,回弹值为7.2mm。所述零件的直径为2m、高度为1.1m。
[0074]
实施例六:
[0075]
其他条件和实施例一一致,不同之处在于:步骤六超声振动蠕变时效:将步骤五的零件放入零件模具中进行蠕变时效,蠕变时效的温度为155℃,时间为28h,在进行到10h时进行超声振动,超声振动的频率为1.85khz,振幅为20μm,时间为20min。
[0076]
经过上述处理,7a85合金挤压薄板零件的抗拉强度为584mpa,伸长率为12%,残余应力为40mpa,回弹值为7.5mm。所述零件的直径为2m、高度为1.1m。实施例七:
[0077]
(1)步骤一挤压成形:按常规方法对7a85合金铸锭进行挤压,得到5mm的7a85合金薄板;
[0078]
(2)步骤二退火处理:按照常规方法对7a85合金挤压薄板进行退火处理;
[0079]
(3)步骤三固溶处理:对步骤二的薄板进行固溶处理,固溶处理时控制温度为475
℃、保温时间为1h;
[0080]
(4)步骤四喷淋淬火:对步骤三得到的薄板进行喷淋淬火,喷水压力为200kpa,水流密度为50l
·
m-2
·
s-1
,持续时间为17s;
[0081]
(5)步骤五滚弯;
[0082]
(6)步骤六超声振动蠕变时效:
[0083]
将步骤五的零件放入零件模具中(即限位模具)进行蠕变时效,蠕变时效的温度为155℃,时间为28h,在进行到6h时进行超声振动,超声振动的频率为2.0khz,振幅为20μm,时间为20min。
[0084]
经过上述处理,7a85合金挤压薄板零件的抗拉强度为590mpa,伸长率为12.5%,残余应力为36mpa,回弹值为5mm。所述零件的直径为2m、高度为1.1m。对比例一:
[0085]
(1)步骤一挤压成形:按常规方法对7a85合金铸锭进行挤压,得到5mm的7a85合金薄板;
[0086]
(2)步骤二退火处理:按照常规方法对7a85合金挤压薄板进行退火处理;
[0087]
(3)步骤三固溶处理:对步骤二的薄板进行固溶处理,固溶处理时控制温度为475℃、保温时间为1h;
[0088]
(4)步骤四淬火:对步骤三得到的薄板进行常规淬火,淬火介质为室温水;
[0089]
(5)步骤五滚弯;
[0090]
(6)步骤六超声振动蠕变时效:将步骤五的零件放入零件模具中进行蠕变时效,蠕变时效的温度为155℃,时间为28h,在进行到5h时进行超声振动,超声振动的频率为1.85khz,振幅为20μm,时间为15min。
[0091]
经过上述处理,7a85合金挤压薄板零件的抗拉强度为580mpa,伸长率为12.5%,残余应力为95mpa,回弹值为22mm。所述零件的直径为2m、高度为1.1m。
[0092]
对比例二:
[0093]
(1)步骤一挤压成形:按常规方法对7a85合金铸锭进行挤压,得到5mm的7a85合金薄板;
[0094]
(2)步骤二退火处理:按照常规方法对7a85合金挤压薄板进行退火处理;
[0095]
(3)步骤三固溶处理:对步骤二的薄板进行固溶处理,固溶处理时控制温度为475℃、保温时间为1h;
[0096]
(4)步骤四喷淋淬火:对步骤三得到的薄板进行喷淋淬火,喷水压力为200kpa,水流密度为50l
·
m-2
·
s-1
,持续时间为12s;
[0097]
(5)步骤五滚弯;
[0098]
(6)步骤六蠕变时效:将步骤五的零件放入零件模具中进行蠕变时效,蠕变时效的温度为155℃,时间为28h。
[0099]
经过上述处理,7a85合金挤压薄板零件的抗拉强度为565mpa,伸长率为14.5%,残余应力为75mpa,回弹值为18mm。所述零件的直径为2m、高度为1.1m。
[0100]
对比例三:
[0101]
其他条件和实施例一一致,不同之处在于:步骤六超声振动蠕变时效:将步骤五的零件放入零件模具中进行蠕变时效,蠕变时效的温度为155℃,时间为28h,在开始进行蠕变时效时超声振动,超声振动的频率为1.85khz,振幅为20μm,时间为15min。
[0102]
经过上述处理,7a85合金挤压薄板零件的抗拉强度为570mpa,伸长率为14%,残余应力为44mpa,回弹值为9.8mm。所述零件的直径为2m、高度为1.1m。
[0103]
对比例四:
[0104]
其他条件和实施例一一致,不同之处在于:步骤六超声振动蠕变时效:将步骤五的零件放入零件模具中进行蠕变时效,蠕变时效的温度为155℃,时间为28h,在进行到24h时超声振动,超声振动的频率为1.85khz,振幅为20μm,时间为15min。
[0105]
经过上述处理,7a85合金挤压薄板零件的抗拉强度为568mpa,伸长率为14.1%,残余应力为43mpa,回弹值为9.7mm。所述零件的直径为2m、高度为1.1m。