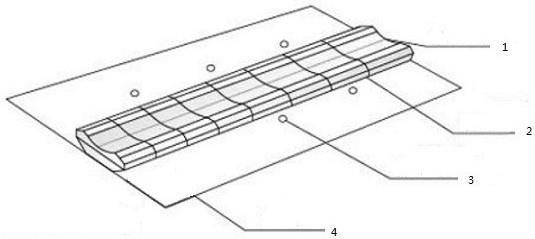
1.本发明属于管道焊接领域,具体涉及一种用于市政供水管道焊接的陶瓷贴片及其焊接工艺。
背景技术:2.埋弧焊是一种重要的传统焊接方法,也是当今生产效率较高的机械化焊接方法之一。埋弧焊在市政供水管道焊接中应用很普遍,其优点是高效、高自动化。但是,很多焊接缺点也在供水管道管体纵缝和环缝埋弧焊焊接的时候不断出现,如劳动强度大、不易于操作、材料和电能用量大。为解决这一问题和找到提高埋弧焊焊接效率和经济性的方法,尝试性地将陶瓷贴片引入进来。陶瓷贴片在市政供水管道焊接中应用极少,一般都采用双面埋弧焊工艺。双面埋弧焊是焊完一面后,必须将工件的另一面清根后再焊接另一面。在这种情况下,移动到另一面需要一定的时间,使得高效率埋弧焊的焊接效率大打折扣。
技术实现要素:3.为解决上述问题,本发明公开了一种用于市政供水管道焊接的陶瓷贴片及其焊接工艺,从而在保证质量的前提下,缩短工期,最终降低劳动强度,减少用工投入,提高施工速度。
4.为达到上述目的,本发明的技术方案如下:一种用于市政供水管道焊接的陶瓷贴片,其包括陶瓷贴片块、粘合剂和防贴纸,其特征在于:所述陶瓷贴片块的截面形状为矩形加上上宽下窄的倒梯形,其中矩形在倒梯形的正上方,矩形的长边与倒梯形的长边贴合。
5.作为本发明的一种改进,所述陶瓷贴片块的总高度为3-5 mm,其中上表面宽度为15-18 mm,下表面宽度为7-12 mm,并且上表面具有焊槽一,所述焊槽一的宽度为5-10 mm,深度为1-1.2 mm,下表面具有宽度为1-2 mm,深度为0.8-1 mm的焊槽二,焊槽一的中心处有一条红色中心线。
6.作为本发明的一种改进,所述粘合剂涂布于所述陶瓷贴片块的下表面,所述防贴纸包围所述陶瓷贴片块。
7.作为本发明的一种改进,所述防贴纸上沿着陶瓷贴片块的边缘有两行间隔相等的透气孔。
8.作为本发明的一种改进,所述陶瓷贴片块由耐高温、耐腐蚀的工程陶瓷制成。
9.作为本发明的一种改进,进一步提供一种用于市政供水管道焊接的陶瓷贴片的焊接工艺,其包括以下步骤:(1)所述市政供水管道采用q235b镇静钢管,厚度为18 mm,直径为2000 mm,单根长度为12 m;用吊车配合进行钢管的管口对接,预留4-6 mm的缝隙;(2)将2个管口切割成坡口,所述坡口为“v”型坡口,坡口角度40
°‑
45
°
,用手工或电动砂轮将坡口和管端距管口10 mm范围内的油污、铁锈、尘土清除干净,使其见到金属本色;
对管内的杂质、泥土进行清扫、冲洗;(3)将用于市政供水管道焊接的陶瓷贴片牢固地粘贴在打磨后的管道内部管口对接缝隙处,并在钢管两端添加长宽尺寸均大于150 mm的引弧板和熄弧焊板;(4)焊前揭去陶瓷贴片的防贴纸并将红线对准组对焊缝的中心线,在管道接口外表面四周采用埋弧焊单面焊接法进行环向焊接,随后采用人工火焰切割处理焊缝和坡口,并去除表面的氧化皮,将影响焊接质量的凹凸不平处打磨平整;(5)采用碳弧气刨或机械的方法去除焊缝根部区域,再重新把去除的区域焊上。
10.作为本发明的一种改进,步骤(4)中的埋弧焊焊接电流为690-700a,电压为35-36v,焊接速度为48-50 cm/min,焊丝的直径为1.2 mm,碳钢焊条选用低氢钠型焊条。
11.作为本发明的一种改进,步骤(4)中的埋弧焊采用15%-30%的氩气和70%-85%的co2作为保护气体。
12.采用陶瓷贴片埋弧焊单面焊双面成形焊接方法使得不需要在管体工件内外两面多次移动,仅仅在管体的一面就能焊接完成,不仅提高焊接效率,而且经济、简便,同时还具有改善焊工工作条件、降低埋弧焊焊工操作难度的作用。与其它的埋弧焊单面焊焊接方法相比,陶瓷贴片埋弧焊单面焊以其高效、优质、低成本的优点得到了迅速的发展,是一种可持续发展,并且引领国际潮流的新型环保焊接方法。
13.焊接中使用陶瓷贴片是使焊缝强制成形的高效、优质、低成本的焊接方法。这种焊接方法避免了清根、仰焊及狭窄封闭环境内作业,减轻了焊工劳动强度,降低了焊工操作技术的难度。使焊接生产效率成倍提高,焊接质量得到保障,同时对人体及环境不会造成危害,与传统焊接方法相比,是一种工艺先进、焊接质量高的可持续发展的绿色焊接方法。
14.本发明的有益效果为:具有合适的熔点:在电弧热的作用下,成形槽表面部分发生熔化,对焊缝金属起到润滑作用增加液态金属的流动性,使得焊缝的焊道背面成形良好、平滑。
15.焊缝含氢量低:陶瓷贴片按要求烘干后,吸湿性较小,焊缝含氢量低。
16.安装质量高:采用粘贴定位,避免和消除了各种焊剂贴片应用中由于工件移动、滚轮架窜动造成的贴片托力不均匀、贴片错位、焊漏及成形不良等问题。
17.安装适用性好:其长度可以根据需要裁定,适应于曲面结构件。
18.施工速度快、应用性好:采用陶瓷贴片埋弧焊单面焊双面成形焊接方法使得不需要在管体工件内外两面多次移动,仅仅在管体的外表面四周焊接就能完成焊接工作,不仅提高焊接效率,而且经济、简便,同时还具有改善焊工工作条件、降低埋弧焊焊工操作难度的作用。
附图说明
19.图1为用于市政供水管道焊接的陶瓷贴片的立体图;图2为钢管口的截面图;图3为陶瓷贴片的焊接工艺的流程图。
20.附图标识列表:1、红色中心线;2、陶瓷贴片块;3、透气孔;4、防贴纸;5、钢管口。
具体实施方式
21.下面结合附图和具体实施方式,进一步阐明本发明,应理解下述具体实施方式仅用于说明本发明而不用于限制本发明的范围。
22.如图1所示,本发明提供的陶瓷贴片的截面形状为矩形加上上宽下窄的倒梯形,其中矩形在倒梯形的正上方,矩形的长边与倒梯形的长边贴合。所述陶瓷贴片块的总高度为3-5 mm,其中上表面宽度为15-18 mm,下表面宽度为7-12 mm,并且上表面具有焊槽一,所述焊槽一的宽度为5-10 mm,深度为1-1.2 mm,下表面具有宽度为1-2 mm,深度为0.8-1 mm的焊槽二,焊槽一的中心处有一条红色中心线。在本发明的实施例中,陶瓷贴片块的总高度为4 mm,上表面宽度为18 mm,下表面宽度为12 mm,焊槽一的宽度为10 mm,深度为1.2 mm。
23.如图3所示,所述陶瓷贴片的焊接工艺如下:(一)施工准备:准备施工设备,检测材料以及考核焊接人员等。
24.(二)管口对接,预留4-6 mm缝隙:采用50t履带吊用吊车配合进行钢管的管口对接,预留4-6 mm的缝隙,要求内壁齐平。在各个实施例中,直管段两相临环向焊缝的间距不小于200
㎜
,管道任何位置不得有十字形焊缝。组对后检查组对构件的形状、位置、错边量、角变形、组对间隙等,确认其符合设计文件和施工规范的要求。
25.(三)打磨、清理坡口:(1)管口及管内清理:用手工或电动砂轮将坡口和管端距管口10mm范围内的油污、铁锈、尘土等清除干净,使其见到金属本色。对管内的杂物、泥土等进行清扫、冲洗。
26.(2)外观检测:对防腐管主要结构尺寸、坡口尺寸、坡口表面按规范标准进行外观检验,使其质量符合下列规定:a.结构尺寸符合设计文件的规定。b.坡口形式和尺寸符合设计文件、焊接作业指导书的规定。c.坡口表面不得有夹层、裂纹、加工损伤、毛刺。
27.(四)粘贴陶瓷:粘贴前检查坡口及坡口两侧的清理质量,其清理宽度及清理后的表面质量应符合本措施焊前准备的规定。管道内壁,将陶瓷贴片粘贴在预留的缝隙处,粘贴应牢固、紧贴、可靠。
28.(五)单面焊接、双面成形:(1)焊接前检查粘贴在钢管内壁接口缝隙的陶瓷贴片是否粘贴牢固、紧贴、可靠,检查符合条件才可进行焊接工作。
29.(2)焊前揭去陶瓷贴片的防固化纸并将红线对准组对焊缝的中心线。焊接电流选取690~700a,电压选取35~36v,焊接速度48~50 cm/min。焊丝采用t492t1-1c1a/φ1.2 mm,碳钢焊条选e4315系列。
30.(3)1、由焊接工艺评价合格的焊工施焊,保证焊接工艺评价的有效性。环向焊缝采用气体保护焊焊接。2、三通管节主、支管连接焊缝和弯管环向焊缝坡口采用人工火焰切割,去除表面的氧化皮,并将影响焊接质量的凹凸不平处打磨平整。3、焊缝要求:焊缝为3-4层,在焊第二层时,必须先清除前一层的焊渣和碎屑。纵向焊缝放在管道中心线上半圆内。在焊接上,填缝金属的组织成颗粒状,外壁成整齐鱼鳞状,不得有裂缝、气孔、灰渣等。
31.(六)打磨清根、填充焊缝:(1)为了保证焊缝根部能够熔透,采用碳弧气刨或机械的方法去除焊缝根部区域,再重新把去除的区域焊上。
32.(2)在保证热焊道焊接质量的前提下,才能进行填充焊道,填充焊的焊接要求基本上和热焊相同,送丝速度稍大于热焊,电压稍高于热焊。在填充焊道完成后,要求填充焊基本和母材表面平齐,所留坡口余量较大不得超过1.5 mm,以保证盖面焊时,立焊位置不会出现气孔或者低于母材,必要时要求填充焊增加一道立填焊。当填充焊完成后,在上述位置其填充表面距坡口表面相差较多,如直接盖面,完成焊道后,在上述位置会出现焊缝表面低于母材表面时才增加一道立填焊。立填焊必须起弧后一次完成,不得在焊接过程中断弧,因为在这一位置的焊接接头很容易出现接头密集气孔。立填焊通常不作横向摆动,带着熔池下行,可以在立焊位置获得微凸或平的填充焊道表面,这样可以避免盖面焊缝表面出现凹形和焊道中心低于母材。立填焊的焊接工艺参数选用原则是相对高的焊接送丝速度,相对低的焊接电压,这样可以避免出现气孔。
33.(3)在保证填充焊接质量的前提下,才能进行盖面焊接。由于半自动保护焊的高熔敷效率,盖面焊时要特别注意焊接工艺参数的选用。而工艺参数选用的关键是送丝速度、电压、后拖角、干伸长和焊接速度。为避免产生气孔,应选用较高的送丝速度,较低的电压(电压较正常的和送丝速度匹配的电压低一伏左右),较长的干伸长,对于焊接速度以保证焊接电弧始终位于焊接熔池的前方为原则。可增大干伸长改焊为推焊,这样可以获得较薄的焊道层,以避免在焊道的仰焊部位余高超高。为消除盖面焊在仰爬坡部位和立焊部位产生接头气孔,在立焊部位通常必须一次焊完。盖面焊的焊接工艺参数基本上和热焊相同,只是需要送丝速度稍大一些。
34.焊接完成后,焊接产生的废渣应及时整理,不得随意散落;施工产生的垃圾和废弃物质,应及时处理,不得裸露弃置,并且应随时进行洒水以使灰尘公害减至最小程度。焊缝在焊接完成后清除焊渣、飞溅物,清理干净焊缝隙表面,并进行焊缝外观检查,焊缝的外观质量要求见下表1:表1
序号项目技术要求1表面成型焊缝饱满,不得漏焊,不得有熔化的金属流到焊缝外未融化的母材上,焊缝和热影响区表面不得有裂纹、气孔、弧坑和灰渣等缺陷,表面光顺,均匀,焊道与母材平缓过渡。2焊缝宽度焊出坡口边缘2~3
㎜
3表面余高小于或等于1+0.2倍坡口边缘宽度,且不大于4
㎜
4咬边深度小于或等于0.5
㎜
,焊缝两边咬边总长不得超过焊缝长度的10%,且连续长不大于100
㎜
5错口小于或等于0.2倍壁厚,且不大于2
㎜
6未焊满不允许
焊缝按《承压设备无损检测》nb/t47013.3的ⅱ级标准进行超声波无损探伤检测,检验数量为100%,检验技术等级不得低于b级,检测设备要求具有数字信息存储功能,保留检测记录。并按《承压设备无损检测》nb/t47013.2的ⅲ级标准进行x射线探伤检验,每条焊缝检验至少分成上下左右4处检验,每处检测长度不小于200 mm,检验技术标准为ab级。对焊缝超声波检验时发现的不允许的缺陷,消除后进行补焊,并对补焊处按规定进行返修检验,直至合格。焊缝焊完后在距焊缝50 mm处打上施焊焊工的编号。焊缝的强度试验及气密性试验在x射线拍片检验后进行。
35.本工艺提高管道焊接安装水平,有效保证了管道焊接质量,加快了工期进度,节约用工投入。
36.表2成本分析对比表
对比项目传统工艺本工艺备注人员4人4人一个班组机械电焊机、电动砂轮、发电机电焊机、电动砂轮、发电机 辅助材料/陶瓷贴片 人均工作量1道/人2道/人 日均工作量4道/天8道/天 上表对比可知,虽然本工艺投入了陶瓷工艺较多、材料投入量较大,但是较传统工艺效率提高了2倍,能加快管道接口焊接安装任务,及时进行管道防腐、沟槽回填,提前完成管道安装。
37.需要说明的是,以上内容仅仅说明了本发明的技术思想,不能以此限定本发明的保护范围,对于本技术领域的普通技术人员来说,在不脱离本发明原理的前提下,还可以做出若干改进和润饰,这些改进和润饰均落入本发明权利要求书的保护范围之内。