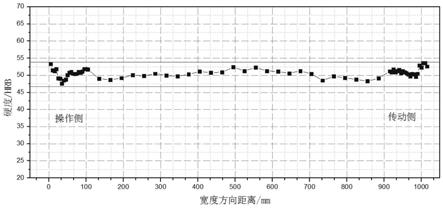
一种低碳钢及提高csp流程铁素体轧制低碳钢性能均匀性的制造方法
技术领域
1.本发明涉及薄板坯连铸连轧钢的生产工艺技术领域,特别涉及一种低碳钢及提高csp流程铁素体轧制低碳钢性能均匀性的制造方法。
背景技术:2.相对于常规工艺,csp铁素体轧制工艺生产碳含量<0.07%低碳钢屈服强度下降约15-25%,氧化铁皮厚度降低30-50%,并能显著降低轧机负荷及电耗,是目前世界钢铁行业在热轧领域的前沿工艺之一。然而由于其本身的工艺特点,csp铁素体轧制温度工艺窗口窄、奥氏体向铁素体转变临界区域材料组织性能受温度影响敏感性大、奥氏体向铁素体相转变的不一致性导致铁素体轧制低碳钢宽度方向性能均匀性相对较差、下道冷轧镀锌工序时易产生边浪,制约铁素体轧制工艺的批量推广应用。
3.关于csp流程采用铁素体轧制制造低碳钢的方法申报专利已有多项。例如:2016年12月21日,专利cn 106244921a公开了一种在csp产线采用铁素体轧制工艺生产低碳钢的方法,其化学成分及重量百分比含量为c:0.02-0.06%,si:0.01-0.04%,mn:0.1-0.3%,其余为p、s等杂质元素和fe。其工艺特点为采用低温加热、低温轧制和高温卷取温度,并控制f1与f2机架的压下率、f1-f3机架间冷却水量以及f4入口温度,最终获得2~6mm厚度的低碳钢组织为粗大的多边形铁素体,屈服强度为210mpa,抗拉强度为330mpa,屈服强度降低约27.33%,抗拉强度降低约13.40%。2020年9月8日公开的专利cn111633028a公开了一种在csp产线采用铁素体轧制生产薄规格低碳钢的方法,包括其铸坯厚度为50~60mm,加热温度990~1030℃,精轧入口温度900~950℃,终轧温度760~800℃,卷取温度680~720℃。钢卷下线后进入保温罩缓冷48h以上,产品厚度为1.0~2.0mm。目前关于csp流程开展铁素体轧制工艺研究主要集中在如何实现强度降低,改善带钢表面质量等方面。
4.2018年1月19日公开的关于esp流程采用铁素体轧制制造低碳钢的方法如专利cn107597844a公开了一种无头连铸连轧深冲用低微碳钢卷的铁素体轧制方法和装置,其铸坯厚度为80~130mm,粗轧机组在950~1020℃的奥氏体取进行粗轧,粗轧至中间坯厚度为7~25mm,随后在冷却同道中迅速冷却至730~850℃进行精轧,产品厚度为0.7~4mm,卷取温度为580~710℃。该专利适用于粗轧、精轧,且具备冷却通道的薄板坯连铸连轧产线。2018年12月14日专利cn108994081a公开了一种在esp生产线采用铁素体轧制生产低碳钢的方法,包括将粗轧后的带钢进行精轧,精轧时,带钢依次进入第一机架、第二机架、第三机架、第四机架、第五机架,对进入第一机架和第二机架之间、第二机架和第三机架之间的带钢进行冷却水冷却,使带钢精轧第三机架至第五机架间轧制在铁素体区进行。精轧入口温度950~1050℃,出口温度740~800℃,卷取温度650~700℃。该专利适用于具有粗轧、精轧的薄板坯连铸连轧生产线。
5.综上所述,目前,关于薄板坯连铸连轧产线采用铁素体轧制生产低碳钢的研究成果主要集中在如何实现铁素体轧制工艺、强度降低、提高表面质量,仍未有专利涉及提高
csp流程铁素体轧制低碳钢性能均匀性的制造方法。
技术实现要素:6.本发明的目的在于提供一种低碳钢及提高csp流程铁素体轧制低碳钢性能均匀性的制造方法,通过合理的冶炼、加热、热轧、冷却及卷取工艺,解决了csp流程铁素体轧制温度工艺窗口窄、奥氏体向铁素体转变临界区域材料组织性能受温度影响敏感性大、奥氏体向铁素体相转变的不一致性问题,提高材料性能的均匀性。这种低碳钢钢板宽度方向性能均匀性提高50%以上,解决了下道冷轧镀锌工序边浪问题。
7.本发明具体技术方案如下:
8.一种提高csp流程铁素体轧制低碳钢性能均匀性的制造方法,包括转炉冶炼、lf炉精炼、连铸、加热、轧制、层流冷却以及卷取工艺。
9.按照配方成分进行转炉冶炼、lf炉精炼、振动曲线采用高频低幅的原则,并连铸成厚度为60~70mm的铸坯;
10.所述加热,铸坯进入加热炉中进行加热,控制铸坯加热温度在1000-1050℃,边部温降小于50℃;
11.所述轧制,经过高压水除鳞后进行7机架精轧机轧制,入口压力设定≤300bar;出口压力设定≤300bar;f1机架间冷却和f2投用二次除鳞水系统,10mpa,其余机架间冷却水、除鳞水和辊缝润滑均关闭,控制f4机架入口宽度方向温度波动小于20℃;轧机楔度控制
±
30μm、凸度控制
±
20μm、平直度控制
±
50i。控制f1、f2、f3机架的道次压下率为40%-65%,f4机架的压下率小于10%。f4机架的入口温度不大于870℃,f7机架终轧温度控制在780-820℃,采用恒速轧制,f7机架出口轧制速度≥6m/s。
12.轧后钢板层流冷却后进行卷取,层流冷却方式为后段层流稀疏冷却、侧喷方式采用对称侧喷,侧喷为水喷或者气喷,控制冷却后的钢板卷取温度在700-740℃,优选为710-730℃。
13.按以上生产方法的热轧低碳钢卷卷取后放入缓冷坑或保温罩中缓冷至室温。
14.本发明生产的低碳钢,包括以下质量百分比成分含量:
15.c:≤0.070%;si:≤0.050%;mn:0.08-0.30%;p:≤0.025%;s:≤0.015%;al:0.020-0.060%;其余为fe及不可避免的夹杂。
16.本发明提供的本发明在加热工艺设计上,铸坯加热温度在1000-1050℃、宽度方向加热温度波动控制在
±
20℃。加热辊道空气过剩系数为1.05-1.2,其目的一方面是减少铸坯表面氧化烧损,防止加热温度过高,铸坯表面氧化铁皮难以去除;另一方面,减小加热温度和终轧温度的之间的温度差,给后续7机架精轧尽可能减少冷却水带来有力条件,改善热轧板表面的温度均匀性。此外,在轧制负荷分配、机架间冷却水、终轧温度等一定情况下,降低加热温度,可以降低铸坯精轧入口温度,进而可以提高轧制速度,提高生产效率。
17.本发明在轧制工艺设计上,f1-f3机架采用大压下率轧制,充分发挥轧件“高温大压下”特点,f4机架轧间温度处于奥氏体相向铁素体相转变的两相区,奥氏体向铁素体转变临界区域材料组织性能受温度影响敏感性大,为了解决奥氏体向铁素体相转变的一致性、提高材料的性能的稳定性,f3后所有机架间冷却水、除鳞水等均关闭且f4机架轧制压下率需小于10%;终轧温度控制在780-820℃,其目的是在铁素体相变温度区域轧制,降低轧制
压力,提高轧制稳定性;采用恒速轧制模式,控制f7机架轧制速度≥6.0m/s,主要目的是减少轧件在两相区轧制时间,提高产品组织性能稳定性。卷取温度控制在700-740℃,其目的一方面是为了让铁素体发生完全静态再结晶及晶粒充分长大,降低带钢的强度,提高其延伸率;另一方面提高卷取温度可以减小终轧温度和卷取温度的之间的温度差,改善层流冷却带来的温度不均匀性,提高热卷宽度方向性能均匀性。
18.本发明在层流冷却设计上,层流冷却方式为后段层流稀疏冷却、侧喷方式采用对称侧喷,其目的主要为了减少表面积水改善热轧板温度均匀性,进而提高铁素体轧制低碳钢性能均匀性。卷取后放入缓冷坑或保温罩中缓冷至室温,一方面,可以进一步使铁素体晶粒充分长大;另一方面,可以提高热轧卷长度、宽度方向的组织性能均匀性。
19.采用本发明生产的低碳钢钢板金相组织为多边形铁素体和少量珠光体,多边形铁素体体积占比95%-100%、少量珠光体体积占比0%-5%;铁素体晶粒度为7.5-8.5级;产品屈服强度rp0.2=210-239mpa,抗拉强度rm=322-356mpa,延伸率a
80
=38-44%,宽度方向屈服强度波动22mpa、抗拉强度34mpa、硬度波动12hrb、冷轧成品硬度波动4hr30t;而其他铁素体轧制工艺生产的低碳钢钢板屈服强度rp0.2=223-265mpa,抗拉强度rm=320-370mpa,延伸率a
80
=32-34%,宽度方向屈服强度波动41mpa、抗拉强度58mpa、硬度波动27hrb、冷轧成品硬度波动10.5hr30t。相对于其他铁素体轧制工艺,本发明生产的低碳钢钢板屈服强度和抗拉强度降低20mpa,延伸率提高约3%,热卷及冷轧成品宽度方向性能波动降低50%,可显著提高热卷及冷轧镀锌成品宽度方向性能均匀性,改善下道冷轧镀锌工序边浪问题。
附图说明
20.图1本发明实施例3对应的低碳钢宽度方向硬度波动;
21.图2本发明实施例3对应的低碳钢金相组织;
22.图3为本发明实施例3对应的低碳钢冷轧成品宽度方向硬度波动;
23.图4本发明实施例3对应的低碳钢冷轧成品金相组织;
24.图5为对比例1常规铁素体工艺对应的低碳钢宽度方向硬度波动;
25.图6为对比例1常规铁素体工艺对应的低碳钢金相组织;
26.图7为对比例1常规铁素体工艺对应的低碳钢冷轧成品宽度方向硬度波动。
27.图8为对比例1常规铁素体工艺对应的低碳钢冷轧成品金相组织。
具体实施方式
28.下面通过具体实施例对本发明的技术方案予以说明。
29.实施例1-实施例3
30.一种提高csp流程铁素体轧制低碳钢性能均匀性的制造方法,所述低碳钢化学成分及重量百分比含量为:c:≤0.070%,si:≤0.050%,mn:0.08-0.30%,p:≤0.025%,s:≤0.015%,als:0.020-0.060%,其余为fe及不可避免的夹杂。具体各实施例的成分含量如表1所示,表1中没有显示的余量为fe及不可避免的夹杂。
31.所述制造方法为:进行转炉冶炼、lf炉精炼、连铸、加热、轧制、层流冷却、卷取。
32.工艺控制为:
33.1)冶炼、连铸,按照上述要求1中的成分进行转炉冶炼、lf炉精炼、振动曲线采用高
频低幅的原则;并连铸成厚度为60~70mm的铸坯;
34.2)加热,铸坯进入加热炉中进行加热,控制铸坯加热温度在1000-1050℃,边部温降小于50℃;
35.3)轧制,经过高压水除鳞后进行7机架精轧机轧制,入口压力设定≤300(bar);出口压力设定≤300(bar);f1机架间冷却和f2投用二次除鳞水系统(10mpa),其余机架间冷却水、除鳞水和辊缝润滑均关闭,控制f4机架入口宽度方向温度波动小于20℃;轧机楔度控制
±
30μm、凸度控制
±
20μm、平直度控制
±
50i。控制f1、f2、f3机架的道次压下率为40%-65%,f4机架的压下率小于10%。f4机架的入口温度不大于870℃,f7机架终轧温度控制在780-820℃,采用恒速轧制,f7机架出口轧制速度≥6m/s。。
36.4)轧后钢板层流冷却后进行卷取,层流冷却方式为后段层流稀疏冷却、侧喷方式采用对称侧喷(水喷或者气喷),控制冷却后的钢板卷取温度在700-740℃,优选为710-730℃。
37.5)按以上生产的热轧低碳钢卷卷取后放入缓冷坑或保温罩中缓冷至室温。
38.实施例1-实施例3按照上述相同的方法生产,控制连铸坯厚度为60~70mm,控制加热温度、终轧温度、层流冷却速度以及卷取温度。具体实施例1-实施例3的工艺参数控制如表2、表3所示。
39.对比例1
40.一种低碳钢的制造方法,所述低碳钢化学成分及重量百分比含量为:如表1所示,表1中没有显示的余量为fe及不可避免的夹杂。
41.对比例1所述低碳钢的制造方法,与实施例相同,具体区别在于表2、表3中所示的参数。
42.表1实施例及对比例实测化学成分(质量百分数,wt%)
43.编号csimnpsal实施例10.0310.0200.110.0180.0040.024实施例20.0300.0180.110.0120.0030.024实施例30.0290.0200.110.0110.0030.025对比例10.0500.0280.100.0120.0030.025
44.表2实施例及对比例轧制工艺参数
[0045][0046]
[0047]
表3实施例及对比例轧制工艺参数
[0048][0049]
各实施例和对比例生产的产品性能参数如表4、表5所示。
[0050]
表4实施例及对比例力学性能
[0051][0052]
表5实施例及对比例力学性能
[0053][0054]
采用本发明生产的低碳钢钢宽度方向硬度波动10hrb,冷轧成品硬度波动4hr30t。常规铁素体轧制工艺生产的低碳钢金相组织为宽度方向硬度波动≥25hrb,冷轧成品硬度波动10.5hr30t。两种工艺对应的典型宽度方向硬度波动分别如图1、图3、图5、图7所示。