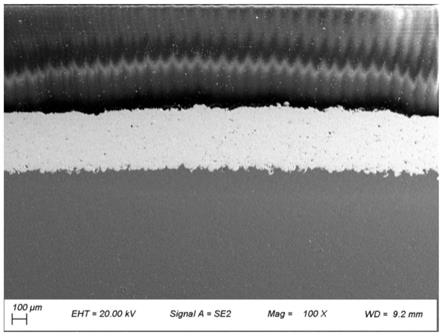
1.本发明涉及石油钻杆技术领域,具体涉及一种高强耐蚀铝合金钻杆及其制备方法。
背景技术:2.随着油气的开发逐渐向纵深发展,深井、超深井以及高压井的出现致使勘探开发难度逐渐增大,其面临的一系列完井问题的核心是完井管柱的材质选择。由于高温高压井和超高压高温井一般有苛刻的井底温度、压力及含co2、h2s和cl-等复杂腐蚀工况条件,迫切需要使用高强度的耐蚀石油管材。其中铝合金钻杆具有低密度、高比强度、耐酸性腐蚀、疲劳寿命高等优点,是解决超深井、大位移井及高含硫等复杂井的安全及高效钻井问题的主要结构材料之一,在石油勘探钻井领域具有广泛的应用前景,是当前高性能油井管材料研究的热点。
3.铝合金钻杆在美国、俄罗斯等少数发达国家的钻探领域已应用数十年,然而我国的石油工业和地质事业都是建国以后才开始发展起来的,虽开发了几个大油田,地质勘探事业也有了长足的进步,但钻探所用的钻杆几乎全部采用钢质钻杆,铝合金钻杆的研究起步较晚,研发时间尚短。目前的铝合金钻杆还是主要依靠进口,这极大地限制了我国钻采工业的发展,因此实现自主研发高强耐蚀铝合金钻杆对保障我国油气资源勘探开发的高效、安全及可持续性具有重要的意义。
技术实现要素:4.本发明的目的在于针对现有铝合金钻杆硬度低、耐磨性差以及不耐cl-腐蚀等缺点,提供了一种制备过程简单,生产效率高的高强耐蚀铝合金钻杆的制备方法,本发明制备的高强耐蚀铝合金钻杆具有高强度、高硬度以及耐盐雾腐蚀等特性。
5.本发明是通过如下技术方案实现的:
6.一种高强耐蚀铝合金钻杆的制备方法,包括如下步骤:
7.(1)铝合金精炼及浇注:将7xxx系铝合金铸锭进行精炼,去除铸锭中的氧化物和杂质;然后将精炼好的铝合金金属液快速浇注到用于喷射成形的坩埚中并保温;通过真空熔炼炉对7xxx系铝合金铸锭进行精炼;
8.(2)喷射成形:将所述坩埚中的铝合金金属液经过雾化、高压喷射、均匀沉积、快速凝固四个阶段,在承料板上形成晶粒细小的铝合金坯锭;
9.(3)双动反向挤压:将所述铝合金坯锭加热至半固态,然后采用双动反向挤压工艺进行致密化处理及无缝铝合金管材挤压成形;
10.(4)表面酸洗及喷砂:对所述铝合金管材进行酸洗,去除表面氧化皮,然后再进行喷砂处理,使表面毛化;
11.(5)超声清洗:对表面毛化后的所述铝合金管材进行超声清洗,去除表面杂质;
12.(6)超音速火焰热喷涂:对超声清洗后的铝合金管材进行超音速火焰热喷涂,形成
热喷涂涂层;
13.(7)热处理:对形成热喷涂涂层的铝合金管材进行t6热处理;
14.(8)封孔处理:热处理后将铝合金管材加热,然后浸渗在树脂溶液中进行封孔,获得高强耐蚀铝合金钻杆。
15.本发明提供的高强耐蚀铝合金钻杆的制备方法,其制备过程简单,生产效率高,所制备的铝合金钻杆屈服强度和抗拉强度高,且在盐雾环境具有明显的耐腐蚀性能。本发明制备的是一种600mpa级屈服强度的高强耐蚀铝合金钻杆。
16.进一步的,所述的高强耐蚀铝合金钻杆的制备方法:步骤(1)铝合金精炼及浇注:将7xxx系铝合金铸锭进行精炼,并采用铝钇合金作为精炼剂去除铸锭中的氧化物和杂质;然后将精炼好的铝合金金属液快速浇注到用于喷射成形的坩埚设备中并在650-750℃下保温;其中所述的7xxx系铝合金为7075或7055。
17.进一步的,所述的高强耐蚀铝合金钻杆的制备方法:步骤(2)喷射成形:中所述的高压喷射采用1-2mpa的惰性气体,沉积率10-50kg/h,铝合金坯锭的晶粒粒径10-15μm。
18.进一步的,所述的高强耐蚀铝合金钻杆的制备方法:步骤(3)所述双动反向挤压工艺:挤压温度为550-650℃,挤压力为1500-3000mpa,挤压比15-25,挤压速度8-20mm/s。
19.进一步的,所述的高强耐蚀铝合金钻杆的制备方法:步骤(4)表面酸洗及喷砂:采用酸洗液对所述铝合金管材进行酸洗,去除表面氧化皮,然后再进行喷砂处理,使表面毛化;其中所述的酸洗液由hcl:hno3按质量比2:3配制而成,酸洗时间当铝合金管材表面开始产生气泡就停止;喷砂处理后铝合金管材表面粗糙度为3-5μm。
20.进一步的,所述的高强耐蚀铝合金钻杆的制备方法:步骤(5)超声清洗:将所述铝合金管材置于乙醇中进行超声清洗,去除表面杂质;其中超声频率为100-200hz,超声清洗时间为15-20分钟。
21.进一步的,所述的高强耐蚀铝合金钻杆的制备方法:步骤(6)超音速火焰热喷涂:对超声清洗后的铝合金管材进行超音速火焰热喷涂,形成热喷涂涂层;其中所述超音速火焰热喷涂时丙烷与氧气的体积比为2:3,喷涂距离为200-240mm,喷涂粉体为ni60,粉体粒径10-40μm,送粉量为25-50g/min,获得ni60涂层厚度为0.3-0.5mm。
22.进一步的,所述的高强耐蚀铝合金钻杆的制备方法:步骤(7)热处理:对形成热喷涂涂层的铝合金管材进行t6热处理,且热处理温度为450-500℃,热处理时间2-5小时。
23.进一步的,所述的高强耐蚀铝合金钻杆的制备方法:步骤(8)封孔处理:热处理后将所述铝合金管材加热至100-150℃,然后浸渗在酚醛树脂溶液中1-2小时进行封孔,获得高强耐蚀铝合金钻杆。
24.本发明提供的高强耐蚀铝合金钻杆制备方法,采用了喷射成形技术快速凝固细化晶粒的方法,使晶粒得到了有效的细化制备出平均粒径约10-15μm细晶粒锭坯,而且晶界界面清晰、界面无析出物;通过半固态加工使喷射增材制造坯料精确成形,并使其高性能得以保持;通过在铝合金钻杆表面热喷涂ni60涂层与铝合金基体结合强度、耐腐蚀性和耐磨性好,应用于石油和勘探领域,可以从根本上解决当前我国对此种先进铝合金钻杆的迫切需求,也为设计和制造新型高性能超高强7xxx系铝合金结构材料提供新的思路和方法。
25.一种高强耐蚀铝合金钻杆,其特征在于,采用权上述的制备方法制得。本发明制备的是一种600mpa级屈服强度的高强耐蚀铝合金钻杆;所制备的铝合金钻杆具有高强度(屈
服强度和抗拉强度高)、高硬度以及耐盐雾腐蚀(在盐雾环境具有明显的耐腐蚀性能)等优点。
26.本发明的的有益效果:
27.(1)本发明提供了一种600mpa级屈服强度的高强耐蚀铝合金钻杆的制备方法,本发明采用喷射成形和双动反向挤压技术,成形的铝合金为无缝管,其屈服强度和抗拉强度高,从根本上解决当前铝合金钻杆弹性模量低和刚度差的问题,满足超深井和斜井钻探对钻杆力学性能的要求。
28.(2)本发明提供的一种600mpa级屈服强度的高强耐蚀铝合金钻杆的制备方法,本发明利用超音速火焰热喷涂工艺在铝合金钻杆表面建立了高强耐蚀保护层,涂层与铝合金基体结合牢固,涂层对cl-具有显著的耐腐蚀性,解决了现有铝合金钻杆不耐盐腐蚀的问题,提高了铝合金钻杆服役寿命。
29.(3)本发明提供的一种600mpa级屈服强度的高强耐蚀铝合金钻杆制备方法,本发明工艺简单、生产效率高、绿色环保对环境污染小,克服了现有技术铝合金钻杆防腐技术成本高、环境污染大的缺点。
30.(4)本发明制备的高强耐蚀的铝合金钻杆兼具高强度、高硬度、高耐磨性和耐腐蚀性等优点,其抗拉强度达到692mpa,屈服强度高达643mpa,腐蚀电位为-0.4v,表面硬度为750hv。
附图说明
31.为了更清楚地说明本发明实施例的技术方案,下面将对实施例描述中所需要使用的附图作简单地介绍,显而易见地,下面描述中的附图仅仅是本发明的一些实施例,对于本领域的技术人员来讲,在不付出创造性劳动的前提下,还可以根据这些附图获得其他附图。
32.图1为本发明实施例6所制备的高强耐蚀铝合金钻杆基体和ni60涂层截面sem图。
具体实施方式
33.下面将结合本发明实施例中的附图,对本发明实施例中的技术方案进行清楚、完整地描述,显然,所描述的实施例仅仅是本发明的一部分实施例,而不是全部的实施例。以下对至少一个示例性实施例的描述实际上仅仅是说明性的,决不作为对本发明及其应用或使用的任何限制。基于本发明中的实施例,本领域普通技术人员在没有作出创造性劳动前提下所获得的所有其他实施例,都属于本发明保护的范围。
34.实施例1
35.一种高强耐蚀铝合金钻杆的制备方法,包括如下步骤:
36.(1)铝合金精炼及浇注:通过真空熔炼炉将7055铝合金铸锭进行精炼,并采用铝钇合金作为精炼剂去除铸锭中的氧化物和杂质;然后将精炼好的铝合金金属液快速浇注到用于喷射成形的坩埚中,并在650℃下保温,备用;
37.(2)喷射成形:通过采用压力2mpa的氩气将坩埚流出的铝合金金属液经过雾化、高压喷射、均匀沉积、快速凝固四个阶段,沉积率50kg/h,在承料板上形成晶粒粒径10-15μm的圆柱形铝合金坯锭;
38.(3)双动反向挤压:将上述喷射成形的铝合金坯锭加热至650℃(半固态),然后采
用双动反向挤压工艺进行致密化处理及无缝铝合金管材挤压成形,挤压力为1500mpa,挤压比15,挤压速度8mm/s;
39.(4)表面酸洗及喷砂:采用酸洗液对上述铝合金管材进行酸洗,去除表面氧化皮,然后再进行喷砂处理,使表面毛化;其中所述的酸洗液由hcl:hno3按质量比2:3配制而成,酸洗时间当铝合金管材表面开始产生气泡就停止;喷砂处理后铝合金管材表面粗糙度为3-5μm;
40.(5)超声清洗:将表面毛化后的所述铝合金管材置于乙醇中进行超声清洗,去除表面杂质;其中超声频率为100hz,超声清洗时间为15分钟;
41.(6)超音速火焰热喷涂:对超声清洗后的铝合金管材进行超音速火焰热喷涂,形成热喷涂涂层;超音速火焰热喷涂时丙烷与氧气体积比为2:3,喷涂距离为240mm,喷涂粉体为ni60,粉体粒径20μm,送粉量为50g/min,获得ni60涂层(即热喷涂涂层)厚度为0.4mm;
42.(7)热处理:对形成热喷涂涂层的铝合金管材进行t6热处理,且热处理的温度为460℃、热处理时间2小时;
43.(8)封孔处理:热处理后将形成热喷涂涂层的铝合金管材再加热至150℃,然后浸渗在酚醛树脂溶液中2小时进行封孔,即获得高强耐蚀铝合金钻杆。
44.实施例2
45.一种高强耐蚀铝合金钻杆的制备方法,包括如下步骤:
46.(1)铝合金精炼及浇注:通过真空熔炼炉将7055铝合金铸锭进行精炼,并采用铝钇合金作为精炼剂去除铸锭中的氧化物和杂质;然后将精炼好的铝合金金属液快速浇注到用于喷射成形的坩埚中,并在650℃下保温,备用;
47.(2)喷射成形:通过采用压力2mpa的氩气将坩埚流出的铝合金金属液经过雾化、高压喷射、均匀沉积、快速凝固四个阶段,沉积率50kg/h,在承料板上形成晶粒粒径10-15μm的圆柱形铝合金坯锭;
48.(3)双动反向挤压:将上述喷射成形的铝合金坯锭加热至650℃(半固态),然后采用双动反向挤压工艺进行致密化处理及无缝铝合金管材挤压成形,挤压力为2000mpa,挤压比20,挤压速度15mm/s;
49.(4)表面酸洗及喷砂:采用酸洗液对上述铝合金管材进行酸洗,去除表面氧化皮,然后再进行喷砂处理,使表面毛化;其中所述的酸洗液由hcl:hno3按质量比2:3配制而成,酸洗时间当铝合金管材表面开始产生气泡就停止;喷砂处理后铝合金管材表面粗糙度为3-5μm;
50.(5)超声清洗:将表面毛化后的所述铝合金管材置于乙醇中进行超声清洗,去除表面杂质;其中超声频率为150hz,超声清洗时间为15分钟;
51.(6)超音速火焰热喷涂:对超声清洗后的铝合金管材进行超音速火焰热喷涂,形成热喷涂涂层;超音速火焰热喷涂时丙烷与氧气体积比为2:3,喷涂距离为220mm,喷涂粉体为ni60,粉体粒径25μm,送粉量为35g/min,获得ni60涂层(即热喷涂涂层)厚度为0.4mm;
52.(7)热处理:对形成热喷涂涂层的铝合金管材进行t6热处理,且热处理的温度为480℃、热处理时间2小时;
53.(8)封孔处理:热处理后将形成热喷涂涂层的铝合金管材再加热至150℃,然后浸渗在酚醛树脂溶液中1小时进行封孔,即获得高强耐蚀铝合金钻杆。
54.实施例3
55.一种高强耐蚀铝合金钻杆的制备方法,包括如下步骤:
56.(1)铝合金精炼及浇注:通过真空熔炼炉将7075铝合金铸锭进行精炼,并采用铝钇合金作为精炼剂去除铸锭中的氧化物和杂质;然后将精炼好的铝合金金属液快速浇注到用于喷射成形的坩埚中,并在700℃下保温,备用;
57.(2)喷射成形:通过采用压力2mpa的氩气将坩埚流出的铝合金金属液经过雾化、高压喷射、均匀沉积、快速凝固四个阶段,沉积率30kg/h,在承料板上形成晶粒粒径10-15μm的圆柱形铝合金坯锭;
58.(3)双动反向挤压:将上述喷射成形的铝合金坯锭加热至650℃(半固态),然后采用双动反向挤压工艺进行致密化处理及无缝铝合金管材挤压成形,挤压力为3000mpa,挤压比25,挤压速度20mm/s;
59.(4)表面酸洗及喷砂:采用酸洗液对上述铝合金管材进行酸洗,去除表面氧化皮,然后再进行喷砂处理,使表面毛化;其中所述的酸洗液由hcl:hno3按质量比2:3配制而成,酸洗时间当铝合金管材表面开始产生气泡就停止;喷砂处理后铝合金管材表面粗糙度为3-5μm;
60.(5)超声清洗:将表面毛化后的所述铝合金管材置于乙醇中进行超声清洗,去除表面杂质;其中超声频率为100hz,超声清洗时间为20分钟;
61.(6)超音速火焰热喷涂:对超声清洗后的铝合金管材进行超音速火焰热喷涂,形成热喷涂涂层;超音速火焰热喷涂时丙烷与氧气体积比为2:3,喷涂距离为200mm,喷涂粉体为ni60,粉体粒径15μm,送粉量为25g/min,获得ni60涂层(即热喷涂涂层)厚度为0.3mm;
62.(7)热处理:对形成热喷涂涂层的铝合金管材进行t6热处理,且热处理的温度为480℃、热处理时间3小时;
63.(8)封孔处理:热处理后将形成热喷涂涂层的铝合金管材再加热至120℃,然后浸渗在酚醛树脂溶液中1.5小时进行封孔,即获得高强耐蚀铝合金钻杆。
64.实施例4
65.一种高强耐蚀铝合金钻杆的制备方法,包括如下步骤:
66.(1)铝合金精炼及浇注:通过真空熔炼炉将7055铝合金铸锭进行精炼,并采用铝钇合金作为精炼剂去除铸锭中的氧化物和杂质;然后将精炼好的铝合金金属液快速浇注到用于喷射成形的坩埚中,并在750℃下保温,备用;
67.(2)喷射成形:通过采用压力1mpa的氩气将坩埚流出的铝合金金属液经过雾化、高压喷射、均匀沉积、快速凝固四个阶段,沉积率20kg/h,在承料板上形成晶粒粒径10-15μm的圆柱形铝合金坯锭;
68.(3)双动反向挤压:将上述喷射成形的铝合金坯锭加热至650℃(半固态),然后采用双动反向挤压工艺进行致密化处理及无缝铝合金管材挤压成形,挤压力为2000mpa,挤压比15,挤压速度20mm/s;
69.(4)表面酸洗及喷砂:采用酸洗液对上述铝合金管材进行酸洗,去除表面氧化皮,然后再进行喷砂处理,使表面毛化;其中所述的酸洗液由hcl:hno3按质量比2:3配制而成,酸洗时间当铝合金管材表面开始产生气泡就停止;喷砂处理后铝合金管材表面粗糙度为3-5μm;
70.(5)超声清洗:将表面毛化后的所述铝合金管材置于乙醇中进行超声清洗,去除表面杂质;其中超声频率为200hz,超声清洗时间为15分钟;
71.(6)超音速火焰热喷涂:对超声清洗后的铝合金管材进行超音速火焰热喷涂,形成热喷涂涂层;超音速火焰热喷涂时丙烷与氧气体积比为2:3,喷涂距离为230mm,喷涂粉体为ni60,粉体粒径40μm,送粉量为30g/min,获得ni60涂层(即热喷涂涂层)厚度为0.5mm;
72.(7)热处理:对形成热喷涂涂层的铝合金管材进行t6热处理,且热处理的温度为500℃、热处理时间4小时;
73.(8)封孔处理:热处理后将形成热喷涂涂层的铝合金管材再加热至130℃,然后浸渗在酚醛树脂溶液中1小时进行封孔,即获得高强耐蚀铝合金钻杆。
74.实施例5
75.一种高强耐蚀铝合金钻杆的制备方法,包括如下步骤:
76.(1)铝合金精炼及浇注:通过真空熔炼炉将7055铝合金铸锭进行精炼,并采用铝钇合金作为精炼剂去除铸锭中的氧化物和杂质;然后将精炼好的铝合金金属液快速浇注到用于喷射成形的坩埚中,并在720℃下保温,备用;
77.(2)喷射成形:采用压力1.5mpa的氩气将坩埚流出的铝合金金属液经过雾化、高压喷射、均匀沉积、快速凝固四个阶段,沉积率40kg/h,在承料板上形成晶粒粒径10-15μm的圆柱形铝合金坯锭;
78.(3)双动反向挤压:将上述喷射成形的铝合金坯锭加热至650℃(半固态),然后采用双动反向挤压工艺进行致密化处理及无缝铝合金管材挤压成形,挤压力为2000mpa,挤压比15,挤压速度12mm/s;
79.(4)表面酸洗及喷砂:采用酸洗液对上述铝合金管材进行酸洗,去除表面氧化皮,然后再进行喷砂处理,使表面毛化;其中所述的酸洗液由hcl:hno3按质量比2:3配制而成,酸洗时间当铝合金管材表面开始产生气泡就停止;喷砂处理后铝合金管材表面粗糙度为3-5μm;
80.(5)超声清洗:将表面毛化后的所述铝合金管材置于乙醇中进行超声清洗,去除表面杂质;其中超声频率为150hz,超声清洗时间为20分钟;
81.(6)超音速火焰热喷涂:对超声清洗后的铝合金管材进行超音速火焰热喷涂,形成热喷涂涂层;超音速火焰热喷涂时丙烷与氧气体积比为2:3,喷涂距离为210mm,喷涂粉体为ni60,粉体粒径40μm,送粉量为45g/min,获得ni60涂层(即热喷涂涂层)厚度为0.4mm;
82.(7)热处理:对形成热喷涂涂层的铝合金管材进行t6热处理,且热处理的温度为450℃、热处理时间5小时;
83.(8)封孔处理:热处理后将形成热喷涂涂层的铝合金管材再加热至140℃,然后浸渗在酚醛树脂溶液中1.5小时进行封孔,即获得高强耐蚀铝合金钻杆。
84.实施例6
85.一种高强耐蚀铝合金钻杆的制备方法,包括如下步骤:
86.(1)铝合金精炼及浇注:通过真空熔炼炉将7055铝合金铸锭进行精炼,并采用铝钇合金作为精炼剂去除铸锭中的氧化物和杂质;然后将精炼好的铝合金金属液快速浇注到用于喷射成形的坩埚中,并在650℃下保温,备用;
87.(2)喷射成形:通过采用压力2mpa的氩气将坩埚流出的铝合金金属液经过雾化、高
压喷射、均匀沉积、快速凝固四个阶段,沉积率50kg/h,在承料板上形成晶粒粒径10-15μm的圆柱形铝合金坯锭;
88.(3)双动反向挤压:将上述喷射成形的铝合金坯锭加热至650℃(半固态),然后采用双动反向挤压工艺进行致密化处理及无缝铝合金管材挤压成形,挤压力为2000mpa,挤压比15,挤压速度20mm/s;
89.(4)表面酸洗及喷砂:采用酸洗液对上述铝合金管材进行酸洗,去除表面氧化皮,然后再进行喷砂处理,使表面毛化;其中所述的酸洗液由hcl:hno3按质量比2:3配制而成,酸洗时间当铝合金管材表面开始产生气泡就停止;喷砂处理后铝合金管材表面粗糙度为3-5μm;
90.(5)超声清洗:将表面毛化后的所述铝合金管材置于乙醇中进行超声清洗,去除表面杂质;其中超声频率为100hz,超声清洗时间为15分钟;
91.(6)超音速火焰热喷涂:对超声清洗后的铝合金管材进行超音速火焰热喷涂,形成热喷涂涂层;超音速火焰热喷涂时丙烷与氧气比例为2:3,喷涂距离为240mm,喷涂粉体为ni60,粉体粒径10μm,送粉量为50g/min,获得ni60涂层(即热喷涂涂层)厚度为0.4mm;
92.(7)热处理:对形成热喷涂涂层的铝合金管材进行t6热处理,且热处理的温度为460℃、热处理时间2小时;
93.(8)封孔处理:热处理后将形成热喷涂涂层的铝合金管材再加热至150℃,然后浸渗在酚醛树脂溶液中2小时进行封孔,即获得高强耐蚀铝合金钻杆。
94.测试:采用sem扫描电镜对上述实施例6所制备的高强耐蚀铝合金钻杆的截面进行观察,其结果如图1所示;从图1中可以看出本发明制备的高强耐蚀铝合金钻杆涂层组织均匀,致密度高。
95.采用ti950纳米压痕仪对上述实施例1-6所制备的高强耐蚀铝合金钻杆的硬度进行测试,每个样品选取10个不同位置的测试点,测试ni60热喷涂层的硬度以及铝合金钻杆基体的硬度;采用lk1100a型电化学工作站对上述实施例1-6所制备的高强耐蚀铝合金钻杆进行电化学测试,测试热喷涂层的电位以及铝合金钻杆基体的电位;上述测试结果参见表1。
96.表1为实施例1-6制备的高强耐蚀铝合金钻杆测试结果
97.[0098][0099]
由上述实施例1-6的测试结果可以看出,本发明制备的高强耐蚀铝合金钻杆,可达到600mpa级的屈服强度。本发明的制备方法采用喷射成形技术快速凝固细化晶粒的方法,使晶粒得到了有效的细化制备出平均粒径约10-15μm细晶粒锭坯,而且晶界界面清晰、界面无析出物;通过半固态加工使喷射增材制造坯料精确成形并使其高性能得以保持;通过在铝合金钻杆表面热喷涂ni60涂层与铝合金基体结合强度、耐腐蚀性和耐磨性好,应用于石油和勘探领域,可以从根本上解决当前我国对此种先进铝合金钻杆的迫切需求,也为设计和制造新型高性能超高强7xxx系铝合金结构材料提供新的思路和方法。
[0100]
上述为本发明的较佳实施例仅用于解释本发明,并不用于限定本发明。凡由本发明的技术方案所引伸出的显而易见的变化或变动仍处于本发明的保护范围之中。