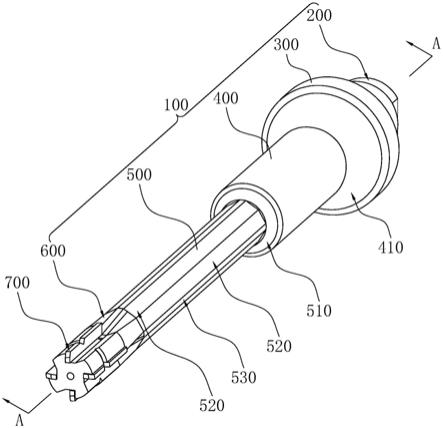
一种pcd刀片以及使用该刀片的pcd铰刀
技术领域
1.本实用新型涉及机加工刀具的领域,尤其是涉及一种pcd刀片以及使用该刀片的pcd铰刀。
背景技术:2.pcd刀具,也称聚晶金刚石刀具,具有硬度高、抗压强度高、导热性好及耐磨性好等特性,可在高速切削中获得很高的加工精度和加工效率。铰刀是机加工刀具中专用于扩孔或修孔的刀具,而pcd铰刀则是使用聚晶金刚石作为刀片的专用于扩孔或修孔的刀具。
3.发明人认为,使用目前的pcd铰刀对工件进行扩孔或者修孔时,加工精度较低。
技术实现要素:4.为了提高加工精度,进而提高工件上孔的内壁的平整度,本实用新型提供一种pcd刀片以及使用该刀片的pcd铰刀。
5.第一方面,本实用新型提供的一种pcd刀片,采用如下的技术方案:
6.一种pcd刀片,包括第一切削部与第二切削部;
7.所述第一切削部设有第一前刀面、第一主后刀面以及第一副后刀面,所述第一前刀面与所述第一主后刀面的交线构成第一主切削刃,所述第一前刀面与所述第一副后刀面的交线构成第一副切削刃;
8.所述第二切削部设有第二前刀面、第二主后刀面以及第二副后刀面,所述第二前刀面与所述第二主后刀面的交线构成第二主切削刃,所述第二前刀面与所述第二副后刀面的交线构成第二副切削刃;
9.所述第一副后刀面与所述第二副后刀面均为弧面,且所述第一副后刀面与所述第二副后刀面同轴;
10.所述第一切削部与所述第二切削部之间设置有回弹槽。
11.通过采用上述技术方案,在对工件进行扩孔或者修孔时,pcd刀片绕第一副后刀面的弧心进行旋转,第一切削部先与工件接触并对工件进行初步切削,之后第二切削部再与工件接触并对工件进行再次切削;当第一切削部完成对工件的初步切削时,第一副后刀面会与工件上的孔的内壁抵接,使第一副后刀面对工件的孔的内壁施加压力,进而使工件发生变形,由于第一切削部与第二切削部之间设置有回弹槽,工件在回弹槽处不再承受径向力进而开始回弹,之后第二切削部再对回弹的工件进行切削,如此减小了第二副后刀面施加给工件上孔的表面压力,减轻了工件上孔的表面被第二副后刀面揉搓变形的现象,提高了工件上孔的表面的光洁度。
12.可选的,所述第一副后刀面的直径大于所述第二副后刀面的直径。
13.由于第一切削刃对工件进行粗加工,切削量较大,第一切削部对工件进行切削后,第一副后刀面会对工件的孔的内壁施加压力,第一副后刀面揉搓工件的孔的内壁后,使工件的孔的内壁不平整;通过采用上述技术方案,第一切削刃对工件进行切削后可保有较大
的切削余量,第二切削刃对工件进行再次切削后可将工件的孔的内壁切削平整,进一步提高了工件上孔的表面光洁度。
14.可选的,所述第一主后刀面为锥面,所述第一主后刀面的轴心与所述第一副后刀面的轴心同轴。
15.通过采用上述技术方案,第一切削部对工件进行切削时,第一主后刀面对pcd刀片进行定心,在切削工件时使pcd刀片不易发生抖动,提高了工件的孔的圆度以及直线度。
16.可选的,所述第二主后刀面为锥面,所述第二主后刀面的轴心与所述第二副后刀面的轴心同轴。
17.通过采用上述技术方案,第二切削部对工件进行切削时,第二主后刀面再次对pcd刀片进行定心,在切削工件时进一步使pcd刀片不易发生抖动,提高了工件的孔的圆度、直线度以及表面光滑度。
18.第二方面,本技术实用新型提供的一种pcd铰刀,采用如下的技术方案:
19.一种pcd铰刀,包括刀具本体以及多个如第一方面所述的pcd刀片,
20.所述刀具本体包括安装部以及与主轴连接的连接部,所述安装部与所述连接部连接;
21.所述安装部的截面呈圆形设置,所述安装部的外周面上开设有多个排屑槽,一个所述排屑槽与一个所述pcd刀片对应;
22.所述pcd刀片固定连接在所述排屑槽的一侧壁上,所述第一副后刀面的轴心与所述安装部的轴心同轴,所述第二副后刀面的轴心与所述安装部的轴心同轴;所述第一副后刀面的直径不小于所述安装部的直径。
23.通过采用上述技术方案,在对工件进行扩孔或者修孔时,刀具本体绕安装部的轴心进行旋转,第一切削部先与工件接触并对工件进行切削,之后第二切削部再与工件接触并对工件进行再次切削,切削产生的废屑通过排屑槽排出。当第一切削部完成对工件的初步切削时,第一副后刀面会与工件上的孔的内壁抵接,使第一副后刀面对工件的孔的内壁施加压力,进而使工件发生变形,由于第一切削部与第二切削部之间设置有回弹槽, 工件在回弹槽处不再承受径向力进而开始回弹,之后第二切削部再对回弹的工件进行切削,如此减小了第二副后刀面施加给工件上孔的表面压力,减轻了工件上孔的表面被第二副后刀面揉搓变形的现象,提高了工件上孔的表面的光洁度。
24.可选的,所述第一副后刀面的直径大于所述安装部的直径。
25.通过采用上述技术方案,在对工件进行扩孔或者修孔时,安装部不易与工件发生相对摩擦,降低了刀具本体升温的速率,进而减轻了刀具本体受热膨胀的现象,减缓了pcd刀片的磨损速率,同时提高了工件的孔的圆柱度。
26.可选的,所述安装部包括第一安装段与第二安装段,所述第一安装段与所述第二安装段同轴设置,所述第一安装段与所述第二安装段抵接;所述第一切削部固定设置在所述第一安装段上,所述第二切削部固定设置在所述第二安装段上。
27.通过采用上述技术方案,当第一切削部磨损至不可再用时,可在回弹槽处将第一切削部切除,将第一切削部切除后,第一安装段便可与第二安装段断开;对pcd刀片进行修复后,pcd铰刀便可继续使用,进一步提高了pcd铰刀的寿命,同时提高了pcd材料的利用率。
28.可选的,所述第一安装段靠近所述第二安装段的一端固定连接有卡块,所述第二
安装段靠近所述第一安装段的一端开设有卡槽,所述卡块与所述卡槽卡接;
29.或,所述第二安装段靠近所述第一安装段的一端固定连接有卡块,所述第一安装段靠近所述第二安装段的一端开设有卡槽,所述卡块与所述卡槽卡接。
30.通过采用上述技术方案,第一安装段与第二安装段安装在一起后,第一安装段与第二安装段不易沿自身的轴心发生相对转动,在切削工件时,减小了第一切削部与第二切削部之间的受力,降低了pcd刀片在回弹槽处断裂的概率。
31.可选的,所述刀具本体还包括导向部,所述导向部设置在所述安装部与所述连接部之间;
32.所述导向部与所述安装部同轴设置,所述安装部远离所述第一切削部的一端与所述导向部固定连接,所述导向部的外周面上设置有多个导向条,所述导向条远离所述刀具本体轴心的一端面为导向面,所述导向面呈弧形设置,且所述导向面的弧心与所述刀具本体的轴心同轴。
33.通过采用上述技术方案,在对工件进行切削时,导向部伸入工件的孔中,此时导向条上的导向面与工件的孔的内壁抵接,进而对铰刀进行导向,在切削工件时使刀具本体不易发生抖动,提高了工件的孔的圆度、直线度以及表面光滑度。
34.可选的,所述导向条的长度方向与所述导向部的轴向平行。
35.通过采用上述技术方案,由于导向条的长度方向与导向部的轴向平行,当导向部伸入工件的孔中时,导向面与工件的孔的内壁呈面接触,进一步提高了对铰刀的导向性,在切削工件时降低了刀具本体发生抖动的概率,提高了工件的孔的圆度、直线度以及表面光滑度。
36.综上所述,本实用新型包括以下至少一种有益技术效果:
37.通过第一切削部、第二切削部以及回弹槽的设置,第一切削部对工件进行切削后,工件可在回弹槽处进行回弹,之后第二切削部再对回弹的工件进行切削,减小了第二切削部所受到的径向力,减缓的刀片的磨损速率,延长了刀片的寿命。
38.通过将第二副刀面的直径设置为大于第一副刀面的直径,第一切削刃对工件进行切削后可保有较大的切削余量,第二切削刃对工件进行再次切削后可将工件的孔的内壁切削平整,进一步提高了工件的表面光洁度。
39.通过将第一副刀面的直径设置为大于安装部的直径,在对工件进行扩孔或者修孔时,安装部不易与工件发生相对摩擦,降低了刀具本体升温的速率,进而减轻了刀具本体受热膨胀的现象,减缓了pcd刀片的磨损速率,同时提高了工件的孔的圆柱度。
40.通过第一安装段与第二安装段的设置,当第一切削部磨损至不可再用时,可在回弹槽处将第一切削部切除,将第一切削部切除后,第一安装段便可与第二安装段断开;对pcd刀片进行修复后,pcd铰刀便可继续使用,进一步提高了pcd铰刀的寿命,同时提高了pcd材料的利用率。
附图说明
41.图1是相关技术中pcd刀片的整体结构示意图;
42.图2是本技术实施例1中pcd铰刀的整体结构示意图(从安装部方向观测);
43.图3是图2中安装部处的部分结构示意图,目的在于展现pcd刀片与安装部的连接
关系;
44.图4是本技术实施例1的pcd刀片的整体结构示意图;
45.图5是本技术实施例1中刀具本体的安装部的部分结构示意图;
46.图6是本技术实施例1中pcd铰刀的整体结构示意图(从连接部方向观测);
47.图7是图2中a-a向的剖视示意图;
48.图8是图7中安装部的处部分结构示意图,目的在于展现冷却支通道的开设方式;
49.图9是本技术实施例2中pcd铰刀的安装部处的部分结构示意图,目的在于展现pcd刀片与安装部的连接关系;
50.图10是本技术实施例2中刀具本体的安装部处的爆炸结构示意图(从第一安装段方向观测),目的在于展现卡块的设置方式;
51.图11是本技术实施例2中刀具本体的安装部处的爆炸结构示意图(从第二安装段方向观测),目的在于展现卡槽的开设方式;
52.图12是本技术实施例3中pcd铰刀的安装部处的部分结构示意图,目的在于展现pcd刀片与安装部的连接关系;
53.图13是本技术实施例3中刀架本体的安装部处的部分结构示意图;
54.图14是本技术实施例3中刀架本体的安装部处的爆炸结构示意图。
55.附图标记说明:100、刀具本体;110、冷却通道;200、连接部;210、施力段;211、第二平槽;220、定位段;221、退刀槽;230、螺纹孔;300、限位部;400、支撑部;410、第二倒圆角;500、导向部;510、第一倒圆角;520、第一平槽;530、导向条;600、安装部;610、第一安装段;611、卡块;620、第二安装段;621、卡槽;630、排屑槽;631、定位块;640、冷却支通道;650、适应槽;700、pcd刀片;710、第一切削部;711、第一前刀面;712、第一主后刀面;713、第一副后刀面;714、第一主切削刃;715、第一副切削刃;720、第二切削部;721、第二前刀面;722、第二主后刀面;723、第二副后刀面;724、第二主切削刃;725、第二副切削刃;730、回弹槽;800、pcd刀片;810、前刀面;820、主后刀面;830、副后刀面;840、主切削刃;850、副切削刃。
具体实施方式
56.以下结合附图1-14对本实用新型作进一步详细说明。
57.参照图1,目前的相关技术中,pcd刀片800大多设置有前刀面810、主后刀面820以及副后刀面830,前刀面810与主后刀面820的交线构成主切削刃840,前刀面810与副后刀面830的交线构成副切削刃850;副后刀面830呈弧形设置,且副后刀面830的弧心与副切削刃850平行。在对工件进行切削时,pcd刀片800绕副后刀面830的弧心进行旋转,主切削刃840先对工件进行切削,之后副切削刃850再对工件进行切削;主切削刃840承担主要的切削任务,副切削刃850参与部分的切削任务。
58.由于绝大部分工件都具有弹性,主切削刃840对工件进行切削时需要先压迫工件,工件在受压迫的状态下被主切削刃840切削,使得工件在被切削时发生弹性形变;工件被主切削刃840切削后,工件上的孔的直径仍小于副后刀面830的直径,但在主切削刃840的压迫作用下,使pcd刀片800得以伸入工件的孔中。
59.之后副切削刃850伸入工件上的孔中,由于工件此前被主切削刃840压迫,此时工件便会施加给副切削刃850以及副后刀面830压力,但工件施加给副切削刃850的压力不足
以使副切削刃850对工件进行切削,副后刀面830便会与工件的孔的内壁发生剧烈摩擦,降低了工件上孔的表面的光洁度。
60.为此,本技术实施例提出了一种pcd铰刀。
61.参照图2,pcd铰刀包括刀具本体100以及安装在刀具本体100上的pcd刀片700。
62.刀具本体100包括与主轴连接的连接部200,连接部200的一端同轴一体成型有限位部300,限位部300远离连接部200的一端同轴一体成型有支撑部400,支撑部400远离限位部300的一端同轴一体成型有导向部500,导向部500远离支撑部400的一端同轴一体成型有安装部600,pcd刀片700安装在安装部600上。在对工件进行扩孔或者修孔时,主轴带动刀具本体100转动,pcd刀片700先伸入工件上的孔中并对工件进行切削,之后导向部500伸入工件上的孔中并对刀具本体100进行导向。
63.参照图3,安装部600的外周面上开设有多个排屑槽630,本技术实施例中排屑槽630设置有四个,pcd刀片700的数量与排屑槽630的数量相同,且一个排屑槽630中对应安装一个pcd刀片700。
64.参照图4,pcd刀片700包括互相一体成型的第一切削部710与第二切削部720。
65.参照图4,第一切削部710设有第一前刀面711、第一主后刀面712以及第一副后刀面713。第一前刀面711为平面;第一主后刀面712为锥形面,第一副后刀面713为弧面,第一副后刀面713的弧心与第一主后刀面712的轴心同轴,且第一副后刀面713与第一主后刀面712之间的夹角为钝角。第一前刀面711与第一主后刀面712的交线构成第一主切削刃714,第一前刀面711与第一副后刀面713的交线构成第一副切削刃715。
66.参照图4,第二切削部720设置在第一切削部710远离第一主后刀面712的一端。
67.参照图4,第二切削部720设有第二前刀面721、第二主后刀面722以及第二副后刀面723。第二前刀面721为平面,且第二前刀面721与第一前刀面711共面。第二主后刀面722设置在第二切削部720靠近第一切削部710的一端,第二主后刀面722为锥形面,且第二主后刀面722与第一主后刀面712平行。第二副后刀面723为弧面,第二副后刀面723的弧心与第一副后刀面713的弧心同轴。第二前刀面721与第二主后刀面722的交线构成第二主切削刃724,第二前刀面721与第二副后刀面723的交线构成第二副切削刃725。
68.参照图4,pcd刀片700上还开设有回弹槽730,回弹槽730设置在第一副后刀面713与第二副后刀面723之间。回弹槽730沿第一副后刀面713的轴心周向设置,且回弹槽730的截面呈三角形;回弹槽730靠近第二切削部720的一侧壁与第二主后刀面722平齐。
69.参照图3至图5,排屑槽630的一个侧壁上一体成型有定位块631,定位块631设置在该侧壁靠近导向部500的一端。将pcd刀片700安装在安装部600上时,将与第一前刀面711相对的一端面抵接在排屑槽630设置有定位块631的侧壁上,并使第二切削部720远离第一切削部710的一端面抵接在定位块631上,之后将pcd刀片700焊接在排屑槽630中,如此即可完成pcd刀片700的安装。pcd刀片700安装在排屑槽630中后,第一副后刀面713的轴心与安装部600的轴心同轴,第一主切削刃714从安装部600远离导向部500的一端伸出排屑槽630。
70.参照图3至图5,在对工件进行扩孔或者修孔时,第一切削部710会施加给工件压力进而使工件发生弹性变形,同时第一切削部710对工件进行粗切削。之后工件在回弹槽730处不再承受来自pcd刀片700的压力进而开始回弹,为了降低安装部600对工件回弹造成的影响,安装部600的外周面上开设有适应槽650,适应槽650在安装部600径向上的深度不浅
于回弹槽730的深度;工件回弹后,第二切削部720再对回弹的工件进行精切削。
71.由于第二切削部720对工件进行切削时的切削量小于第一切削部710对工件进行切削时的切削量,因此第二切削部720施加给工件的压力小于第一切削部710施加给工件的压力,工件在第二切削部720处的变形量小于第一切削部710处的变形量,使得工件受第二副后刀面723磨损的影响较小,提高了工件上孔的表面的光洁度。
72.参照图3至图5,安装部600的直径小于pcd刀片700上第一副后刀面713的直径,在使用pcd刀片700切削工件时,工件上孔的内壁不易与安装部600的周面接触,减轻了工件上孔的内壁被安装部600磨损的现象,提高了加工精度;同时由于工件上孔的内壁不易与安装部600的周面接触,降低了工件与安装部600摩擦生热的速率,进而降低了切削温度,延长了pcd刀片700的寿命。
73.参照图5及图6,导向部500的外周面上开设有多个第一平槽520,使导向部500上形成多个导向条530,本技术实施例中第一平槽520设置有八个,形成的导向条530的数量为四个,相邻的两个导向条530之间夹设有两个第一平槽520,导向条530的长度方向平行于导向部500的轴向。导向条530的外周面为导向面,导向面的直径大于安装部600的直径且小于第二副后刀面723的直径。当安装部600完全伸入工件的孔中后,导向部500随之伸入工件的孔中,此时导向面与工件的孔的内壁抵接,如此导向部500便可对刀具本体100进行导向,提高了加工精度;而第一平槽520的设置减小了导向部500与工件的接触面积,进而减少了导向部500因摩擦而生成的热量,降低了导向部500膨胀卡死在工件的孔中的概率。
74.参照图6,支撑部400的直径大于导向面的直径,且导向部500与支撑部400之间设置有第一倒圆角510;限位部300的直径大于支撑部400的直径,且限位部300与支撑部400之间设置有第二倒圆角410。由于第一倒圆角510的设置,使支撑部400与导向部500的连接处不易出现应力集中的现象,进而降低了刀具本体100从导向部500与支撑部400之间断开的概率。由于第二倒圆角410的设置,使支撑部400与限位部300的连接处不易出现应力集中的现象,进而降低了刀具本体100从限位部300与支撑部400之间断开的概率。
75.参照图6及图7,连接部200包括互相一体成型的施力段210与定位段220,定位段220与限位部300一体成型,施力段210设置在定位段220远离限位部300的一端。施力段210的截面呈圆形设置,且施力段210的外周面上开设有两个第二平槽211,两个第二平槽211分别设置在施力段210轴心的两侧;定位段220呈圆台型设置,且定位段220与施力段210同轴设置,定位段220靠近施力段210的一端的直径小于远离施力段210一端的直径;限位部300的直径还大于定位段220的直径。连接部200上沿自身的轴心开设有螺纹孔230,螺纹孔230贯穿施力段210以及定位段220。
76.将连接部200安装在主轴上时,第二平槽211与主轴上对应的面贴合,使刀具本体100无法与主轴发生相对转动;定位段220的外周面与主轴上对应的面贴合,以提高刀具本体100与主轴的同轴度;之后将主轴上的螺杆螺纹连接在螺纹孔230中,使定位段220的外周面与主轴上对应的面压紧,且限位部300不与主轴接触,如此便可完成刀具本体100的定位。主轴驱动刀具本体100转动时,在第二平槽211的作用下,螺纹孔230上的螺牙以及主轴上螺杆的螺牙不易受力变形,进而便于刀具本体100与主轴之间的拆装。
77.参照图6,当限位部300与主轴接触时,证明定位段220的外周面已经磨损至无法对刀具本体100进行导向,应当及时更换刀具本体100。为了能够及时证明定位段220的外周面
已经磨损至无法对刀具本体100进行导向,定位段220靠近限位部300的一端开设有退刀槽221,退刀槽221的设置使定位段220与限位部300之间便不易形成圆角,进而使限位部300能够及时与主轴抵触。
78.参照图7及图8,刀具本体100上同轴开设有冷却通道110,冷却通道110贯穿安装部600、导向部500、支撑部400以及限位部300,冷却通道110靠近连接部200的一端与螺纹孔230连通。主轴上的螺杆上设置有喷油口,螺杆螺纹连接在螺纹孔230内后,喷油口与冷却通道110连通。安装部600上开设有与排屑槽630数量相同的冷却支通道640,一个冷却支通道640与一个排屑槽630对应,冷却支通道640的一端与冷却通道110连通,冷却支通道640的另一端与排屑槽630连通,且冷却支通道640靠近冷却通道110的一端朝导向部500倾斜。
79.在对工件进行加工的过程中,喷油口向冷却通道110内喷射冷却润滑油,进而对刀具本体100进行冷却;部分冷却润滑油经冷却支通道640流动至排屑槽630中,使冷却润滑油直接对pcd刀片700进行冷却和润滑,延长了pcd刀片700的寿命,同时冷却润滑油对排屑槽630中的碎屑进行冲击,便于碎屑快速脱离排屑槽630。
80.本技术实施例一种pcd刀片700以及使用该刀片的pcd铰刀的实施原理为:
81.在对工件进行扩孔或者修孔时,第一切削部710先伸入工件上的孔内,此时第一主切削刃714施加给工件压力进而使工件发生弹性变形,同时第一切削部710对工件进行粗切削;之后第一副后刀面713伸入工件上的孔内,此时第一副后刀面713与工件上孔的内壁抵接,进而对第一切削部710进行导向;之后回弹槽730伸入工件上的孔内,此时工件在回弹槽730处不再承受压力进而开始回弹;之后第二切削部720伸入工件上的孔内,此时第二切削部720对工件进行精切削;之后第二副后刀面723伸入工件上的孔内,此时第二副后刀面723与工件上孔的内壁抵接,进而对第二切削部720进行导向;之后导向部500伸入工件上的孔内,此时导向部500对刀具本体100进行整体导向。
82.由于第二切削部720对工件进行切削时的切削量小于第一切削部710对工件进行切削时的切削量,因此第二切削部720施加给工件的压力小于第一切削部710施加给工件的压力,工件在第二切削部720处的变形量小于第一切削部710处的变形量,使得工件受第二副后刀面723磨损的影响较小,提高了工件上孔的表面的光洁度。
83.实施例2:
84.本技术实施例提出了一种pcd铰刀,本技术实施例与实施例1的区别在于,参照图9至图11,安装部600包括第一安装段610以及第二安装段620,第二安装段620与导向部500同轴一体成型,第一安装段610同轴安装在第二安装段620远离导向部500的一端,适应槽650开设在第一安装段610靠近第二安装段620的外周面上。第二安装段620靠近第一安装段610的一端的中心处一体成型有截面不为圆形卡块611,第一安装段610靠近第二安装段620的一端的中心处开设有卡槽621,卡块611与卡槽621的截面相同。第一安装段610安装在第二安装段620上时,卡块611卡接在卡槽621中。pcd刀片700的第一切削部710焊接在第一安装段610上,pcd刀片700的第二切削部720焊接在第二安装段620上。
85.在其它实施例中,卡块611可设置在第一安装段610靠近第二安装段620的一端面上,卡槽621开设在第二安装段620靠近第一安装段610的一端面上,只要能使第一安装段610与第二安装段620可沿自身的轴向发生相对滑移,但无法沿自身的轴心发生相对转动即可。
86.本技术实施例一种pcd刀片700以及使用该刀片的pcd铰刀的实施原理为:
87.本技术实施例的实施远离与实施例1的实施原理大致相同,其区别在于,由于第二切削部720的磨损速率低于第一切削部710的磨损速率,当第一切削部710磨损至无法再用时,使用者可将在回弹槽730处将pcd刀片700切断,如此第一安装段610便可与第二安装段620分离。当第一安装段610与第二安装段620分离后,安装部600上仅剩余第二安装段620,安装部600上仅焊接有第二切削部720,且第二切削部720上的第二主切削刃724从远离导向部500的一端伸出排屑槽630,使得pcd铰刀可继续使用。
88.实施例3:
89.本技术实施例提出了一种pcd铰刀,本技术实施例与实施例2的区别在于,参照图12至图14,冷却通道110在安装部600上仅开设在第二安装段620上,第一安装段610上不开设冷却通道110。当第一安装段610安装在第二安装段620上后,第一安装段610将冷却通道110靠近第一安装段610的一端封死。
90.本技术实施例一种pcd刀片700以及使用该刀片的pcd铰刀的实施原理为:
91.本技术实施例的实施远离与实施例2的实施原理大致相同,其区别在于,由于第一安装段610将冷却通道110靠近第一安装段610的一端封死,使冷却通道110中的冷却润滑油只能从冷却支通道640中流出,如此提高了pcd刀片700的冷却效率,同时提高了冷却润滑油对排屑槽630中碎屑的冲击力,降低了碎屑堆积在排屑槽630中的概率。
92.以上均为本实用新型的较佳实施例,并非依此限制本实用新型的保护范围,故:凡依本实用新型的结构、形状、原理所做的等效变化,均应涵盖于本实用新型的保护范围之内。