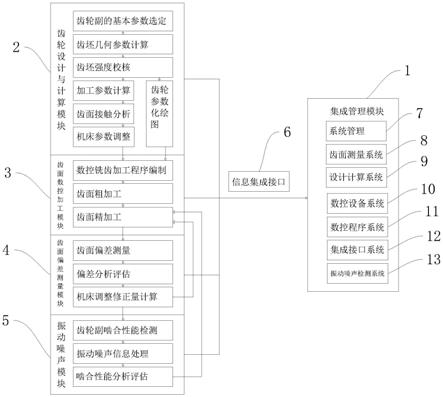
1.本发明涉及锥齿轮,更具体地说,它涉及一种弧齿锥齿轮制造工艺。
背景技术:2.弧齿锥齿轮是锥齿轮的一种,弧齿锥齿轮可分为:零度弧齿锥齿轮[等顶隙收缩齿和双重收缩齿(格里森齿制)]和弧齿锥齿轮[等顶隙收缩齿(格里森齿制,埃尼姆斯齿制)和等齿高(洛-卡氏齿制)],弧齿锥齿轮具有轮齿强度高、运行平稳、承载能力强等特点,广泛用于汽车、拖拉机、工程机械等。
[0003]
现有的弧齿锥齿轮的制造工艺包括:
[0004]
(一)车毛坯,使用数控车床加工锥齿轮毛坯零件,留出下平面精修磨量,使用斜面验具和塞规测量锥齿轮倾斜角度和中心孔径以保证所加工零件达到工艺要求。
[0005]
(二)滚齿,滚齿加工是展成法原理来加工齿轮,用滚刀来加工对轮相当于一对交错螺旋轮啮合。零件加工完成后要求齿内无毛刺,使用汽油清洗,防止零件生锈。
[0006]
(三)淬火,初回,淬火可以提高金属工件的硬度及耐磨性,淬火前需核对零件数量,检查零件有无裂纹、碰伤、缺边及锈蚀等影响淬火质量的缺陷,装炉工件均应干燥、不得有油污及其他脏物,按照图纸要求进行淬火,保温30分钟使工件内部温度均匀趋于一致,冷却阶段要保持零件的尺寸和形状精度。
[0007]
(四)串光,去除小毛刺以及棱边修钝。串光后,零件的棱边过渡圆滑,均匀一致,不可出现棱边不均匀的情况。
[0008]
(五)去刺,上光,使用去刺刀手工去除齿内细小毛刺,以保证齿形啮合效果。
[0009]
(六)回火,此道工序是工件获得所需性能的最后一道重要工序,避免回火脆性。
[0010]
(七)滚光,清洗,此道工序为光饰工序,利用铜泥为介质,利用滚光机旋转达到使零件光亮的目的。
[0011]
(八)钝化,此道工序为整个零件的最后一个工序,化学清洗的目的是为了零件的防腐蚀,清洗后的金属表面生成保护膜,减缓腐蚀,从而增加零件的使用寿命。
[0012]
由于齿面结构复杂,弧齿锥齿轮的制造精度和质量直接影响其所属设备的传动效率、噪声、运动精度和使用寿命等性能,使得现有的弧齿锥齿轮生产需要多次测量校准,而后再次加工,设计、加工、检测以及再次加工不能组成一个整体,使得生产效率低下。
[0013]
因此需要提出一种新的方案来解决这个问题。
技术实现要素:[0014]
针对现有技术存在的不足,本发明的目的在于提供一种弧齿锥齿轮制造工艺。
[0015]
本发明的上述技术目的是通过以下技术方案得以实现的:一种弧齿锥齿轮制造工艺,包括集成管理模块、齿轮设计与计算模块、齿面数控加工模块和齿面偏差测量模块,所述齿轮设计与计算模块、齿面数控加工模块和齿面偏差测量模块均通过信息集成接口与集成管理模块连接实现信息交互,其中:
[0016]
所述齿轮设计与计算模块通过弧齿锥齿轮的使用工况确认基本设计参数;
[0017]
所述齿面数控加工模块用于弧齿锥齿轮的加工;
[0018]
所述齿面偏差测量模块用于弧齿锥齿轮的偏差测量及分析;
[0019]
所述集成管理模块为弧齿锥齿轮网络化制造集成系统,包括系统管理、齿面测量系统、设计计算系统、数控设备系统、数控程序系统和集成接口系统;
[0020]
弧齿锥齿轮制造包括步骤:s1齿轮设计与计算模块将参数输入至集成管理模块;
[0021]
s2齿面数控加工模块根据集成管理模块数据加工弧齿锥齿轮;
[0022]
s3齿面偏差测量模块测量偏差并将数据传输给集成管理模块;
[0023]
s4齿面数控加工模块根据集成管理模块数据多次加工弧齿锥齿轮直至弧齿锥齿轮精度通过齿面偏差测量模块。
[0024]
通过采用上述技术方案,通过集成管理模块构建的网络化的集成环境,将弧齿锥齿轮的设计计算技术、数控加工技术、齿面数字化检测修正技术与管理控制技术进行结合,从而借助信息集成技术,实现在统一网络环境下,弧齿锥齿轮齿面数字化制造过程各环节的信息集成,并实现制造过程中齿面的设计、加工、测量等信息的集成管理,进而实现弧齿锥齿轮齿面制造过程的信息网络化和管理集成化,有效地提高其齿面的加工效率和质量。
[0025]
本发明进一步设置为:所述步骤s1包括:s11齿轮副的基本参数选定;s12齿坯几何参数计算;s13齿坯强度校核;s141加工参数计算;s151齿面接触分析;s161机床参数调整;s171齿轮设计与计算模块数据传输至集成管理模块。
[0026]
通过采用上述技术方案,齿轮设计与计算模块根据弧齿锥齿轮的使用工况条件,确定齿轮副的基本设计参数,进行大、小轮齿坯的几何参数计算、强度校核,而后计算出其相应的齿坯加工参数,并通过齿面接触分析,优化确定出机床调整参数,编制出机床铣齿调整卡,完成轮坯的参数化设计计算,而后齿坯的设计计算信息可通过网络传输到集成管理模块,进行统一的数据管理。
[0027]
本发明进一步设置为:所述步骤s2包括:s21集成管理模块传输数据至齿面数控加工模块;s22数控铣齿加工程序编制;s23齿面粗加工;s24齿面精加工;s25集成管理模块传输齿面偏差测量模块数据至齿面数控加工模块;s26齿面再次精加工,其中步骤s25和步骤s26可循环直至弧齿锥齿轮精度通过齿面偏差测量模块。
[0028]
通过采用上述技术方案,集成管理模块通过网络获取齿坯的设计信息,并根据对应机床切齿调整卡,进行齿面数控铣齿加工程序的编制,数控加工程序可通过网络集成到集成系统内;数控铣齿机床通过网络获取齿面的数控程序和机床铣齿调整卡,进行齿面的粗铣和精铣加工,并对于没有通过齿面偏差测量模块的弧齿锥齿轮进行再次的精加工。
[0029]
本发明进一步设置为:所述步骤s3包括:s31齿面偏差测量;s32偏差分析评估;s33机床调整修正量计算;s34传输齿面偏差测量模块数据传输至集成管理模块。
[0030]
通过采用上述技术方案,齿面偏差测量模块可通过网络获取齿坯的基本几何参数和加工参数,结合测量参数,利用齿面测量系统进行齿面偏差的测量,并在对齿面偏差数据进行评估与分析的基础上,建立齿面偏差的修正模型且解出机床调整参数的修正项和修正量,而后通过集成管理模块的网络通信,将数据传输到数控铣齿机床,进行齿面的数控修正铣齿,铣齿修正后可再次通过网络通信进行齿面偏差的测量与反调修正,直到弧齿锥齿轮的齿面偏差达到齿面精度要求为止。
[0031]
本发明进一步设置为:还包括通过信息集成接口与集成管理模块连接实现信息交互的振动噪声模块,振动噪声模块用于齿轮副振动噪声检测并将数据传输至集成管理模块,对检测未达精度要求的弧齿锥齿轮通过齿面数控加工模块再次加工,所述集成管理模块还包括振动噪声检测系统。
[0032]
通过采用上述技术方案,将弧齿锥齿轮的振动噪声检测技术通过集成管理模块构建的网络化的集成环境,与管理控制技术进行结合,进一步提高弧齿锥齿轮齿面的加工质量。
[0033]
本发明进一步设置为:所述振动噪声模块包括如下步骤:a1齿轮副啮合性能检测;a2振动噪声信息处理;a3弧齿锥齿轮啮合性能分析评估;a4振动噪声模块数据传输至集成管理模块;a5集成管理模块传输数据至齿面数控加工模块;a6齿面再次精加工。
[0034]
通过采用上述技术方案,振动噪声模块能通过检测出的弧齿锥齿轮的振动噪声信息计算出弧齿锥齿轮啮合性能,未达精度要求就再次加工,从而进一步提高弧齿锥齿轮的精度。
[0035]
本发明进一步设置为:所述齿轮设计与计算模块还包括齿轮参数化绘图,所述步骤s1还包括:s142齿轮参数化绘图;s143绘图数据传输至集成管理模块;s144集成管理模块将绘图数据传输至齿面数控加工模块且并入步骤s22数控铣齿加工程序编制。
[0036]
通过采用上述技术方案,齿轮设计与计算模块还能完成弧齿锥齿轮的参数化绘图,有利于数控铣齿加工程序的编制,提高弧齿锥齿轮加工的精度。
[0037]
综上所述,本发明具有以下有益效果:通过集成管理模块构建的网络化的集成环境,将弧齿锥齿轮的设计计算技术、数控加工技术、齿面数字化检测修正技术与管理控制技术进行结合,从而借助信息集成技术,实现在统一网络环境下,弧齿锥齿轮齿面数字化制造过程各环节的信息集成,并实现制造过程中齿面的设计、加工、测量等信息的集成管理,进而实现弧齿锥齿轮齿面制造过程的信息网络化和管理集成化,有效地提高其齿面的加工效率和质量。
附图说明
[0038]
图1为本发明的系统框架图。
[0039]
图中:1、集成管理模块;2、齿轮设计与计算模块;3、齿面数控加工模块;4、齿面偏差测量模块;5、振动噪声模块;6、信息集成接口;7、系统管理;8、齿面测量系统;9、设计计算系统;10、数控设备系统;11、数控程序系统;12、集成接口系统;13、振动噪声检测系统。
具体实施方式
[0040]
下面结合附图和实施例,对本发明进行详细描述。
[0041]
一种弧齿锥齿轮制造工艺,如图1所示,包括集成管理模块1、齿轮设计与计算模块2、齿面数控加工模块3、振动噪声模块5和齿面偏差测量模块4,齿轮设计与计算模块2、齿面数控加工模块3、振动噪声模块5和齿面偏差测量模块4均通过信息集成接口6与集成管理模块1连接实现信息交互,其中:齿轮设计与计算模块2采用设计工作站,并通过弧齿锥齿轮的使用工况确认基本设计参数;齿面数控加工模块3采用多个数控铣齿床,用于弧齿锥齿轮的加工;齿面偏差测量模块4采用齿轮测量中心,用于弧齿锥齿轮的偏差测量及分析;振动噪
声模块5采用滚动检查机,用于齿轮副振动噪声检测并将数据传输至集成管理模块1,对检测未达精度要求的弧齿锥齿轮通过齿面数控加工模块3再次加工;集成管理模块1为弧齿锥齿轮网络化制造集成系统,包括系统管理7、齿面测量系统8、设计计算系统9、数控设备系统10、数控程序系统11、振动噪声检测系统13和集成接口系统12,信息交互结口的通信协议为tcp/ip协议,集成管理模块1通过串口服务器设置每台入网数控铣齿机床的虚拟端口和独立的ip地址并设置对应的通信参数,实现与集成管理模块1不同模式的通信传输。
[0042]
如图1所示,弧齿锥齿轮制造包括步骤:s1齿轮设计与计算模块2将参数输入至集成管理模块1,其中包括s11齿轮副的基本参数选定;s12齿坯几何参数计算;s13齿坯强度校核;s141加工参数计算;s151齿面接触分析;s161机床参数调整;s171齿轮设计与计算模块2数据传输至集成管理模块1,s142齿轮参数化绘图;s143绘图数据传输至集成管理模块1;s144集成管理模块1将绘图数据传输至齿面数控加工模块3且并入步骤s22数控铣齿加工程序编制;
[0043]
s2齿面数控加工模块3根据集成管理模块1数据加工弧齿锥齿轮,其中包括:s21集成管理模块1传输数据至齿面数控加工模块3;s22数控铣齿加工程序编制;s23齿面粗加工;s24齿面精加工;s25集成管理模块1传输齿面偏差测量模块4数据至齿面数控加工模块3;s26齿面再次精加工,其中步骤s25和步骤s26可循环直至弧齿锥齿轮精度通过齿面偏差测量模块4;
[0044]
s3齿面偏差测量模块4测量偏差并将数据传输给集成管理模块1,其中包括:s31齿面偏差测量;s32偏差分析评估;s33机床调整修正量计算;s34传输齿面偏差测量模块4数据传输至集成管理模块1;
[0045]
s4齿面数控加工模块3根据集成管理模块1数据多次加工弧齿锥齿轮直至弧齿锥齿轮精度通过齿面偏差测量模块4;
[0046]
并通过振动噪声模块5检测弧齿锥齿轮的啮合性能,其中包括:a1齿轮副啮合性能检测;a2振动噪声信息处理;a3弧齿锥齿轮啮合性能分析评估;a4振动噪声模块5数据传输至集成管理模块1;a5集成管理模块1传输数据至齿面数控加工模块3;a6齿面再次精加工。
[0047]
工作原理:齿轮设计与计算模块2根据弧齿锥齿轮的使用工况条件,确定齿轮副的基本设计参数,进行大、小轮齿坯的几何参数计算、强度校核,而后计算出其相应的齿坯加工参数,并通过齿面接触分析,优化确定出机床调整参数,编制出机床铣齿调整卡,完成轮坯的参数化设计计算,齿轮设计与计算模块2还能完成弧齿锥齿轮的参数化绘图,而后齿坯的设计计算信息可通过网络传输到集成管理模块1,进行统一的数据管理,集成管理模块1通过网络获取齿坯的设计信息,并根据对应机床切齿调整卡,进行齿面数控铣齿加工程序的编制,数控加工程序可通过网络集成到集成系统内;数控铣齿机床通过网络获取齿面的数控程序和机床铣齿调整卡,进行齿面的粗铣和精铣加工,并对于没有通过齿面偏差测量模块4的弧齿锥齿轮进行再次的精加工,齿面偏差测量模块4可通过网络获取齿坯的基本几何参数和加工参数,结合测量参数,利用齿面测量系统8进行齿面偏差的测量,并在对齿面偏差数据进行评估与分析的基础上,建立齿面偏差的修正模型且解出机床调整参数的修正项和修正量,而后通过集成管理模块1的网络通信,将数据传输到数控铣齿机床,进行齿面的数控修正铣齿,铣齿修正后可再次通过网络通信进行齿面偏差的测量与反调修正,直到弧齿锥齿轮的齿面偏差达到齿面精度要求为止,振动噪声模块5能通过检测出的弧齿锥齿
轮的振动噪声信息计算出弧齿锥齿轮啮合性能,未达精度要求就再次加工,从而进一步提高弧齿锥齿轮的精度。
[0048]
通过集成管理模块1构建的网络化的集成环境,将弧齿锥齿轮的设计计算技术、数控加工技术、齿面数字化检测修正技术、弧齿锥齿轮的振动噪声检测技术与管理控制技术进行结合,从而借助信息集成技术,实现在统一网络环境下,弧齿锥齿轮齿面数字化制造过程各环节的信息集成,并实现制造过程中齿面的设计、加工、测量等信息的集成管理,进而实现弧齿锥齿轮齿面制造过程的信息网络化和管理集成化,有效地提高其齿面的加工效率和质量。
[0049]
以上所述仅是本发明的优选实施方式,本发明的保护范围并不仅局限于上述实施例,凡属于本发明思路下的技术方案均属于本发明的保护范围。应当指出,对于本技术领域的普通技术人员来说,在不脱离本发明原理前提下的若干改进和润饰,这些改进和润饰也应视为本发明的保护范围。