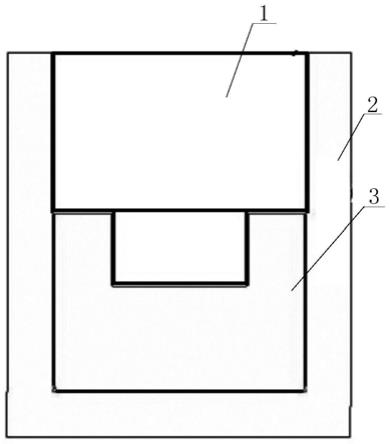
1.本发明涉及高压容器领域,尤其涉及一种高压容器单层厚壁筒体的分段式挤压成形方法及容器。
背景技术:2.高压容器应用广泛,几乎涉及到国计民生的各部门和领域,如化工、机械、冶金、能源、环保、海洋等领域。高压容器中筒体的作用是提供承压空间并最大限度的承受内压,是压力容器中最主要的受压元件之一。高压容器筒体的设计制造过程首先要提高其承载能力,充分保证高压容器筒体的安全性。其次,随着现代化设计理念、原材料和加工技术的发展,降低高压容器筒体的生产加工成本也已经成为相关人员关注的焦点。目前,高压容器的筒体的结构形式包括单层厚壁式、多层厚壁式、绕丝式、剖分块式等,其中,单层厚壁式高压容器筒体是目前应用最广泛的一种。
3.目前,高压容器单层厚壁筒体主要的加工方式有两种。一种是整体锻造法,即首先在钢坯中间穿孔,然后将坯料加热,随后在坯料的孔心处穿过一个芯轴,然后在水压机上经多次锻造获得所需尺寸的圆筒体,最后再进行机械加工,将圆筒体加工成最终所需的筒体形状尺寸,该方法需要的设备吨位大、材料利用率低、能耗大,不符合绿色低碳制造的发展趋势。另一种高压容器单层厚壁筒体的常用生产方法是单层卷焊式方法,即采用钢板在大型卷板机上卷成一个圆通或两个半圆筒,然后将对接处经焊接形成筒体,该方法目前应用广泛,但随着容器尺寸增大,受钢板幅面尺寸所限,一个筒体上通常会产生多条焊缝,焊缝处容易产生缺陷。此外,卷板方法容易造成钢板内部产生细微裂纹等。因此,迫切需要设计开发新型的高压容器单层厚壁制造技术,在保证筒体可靠性的同时,降低筒体的生产制造成本。
4.挤压时材料处于三向压应力状态,塑性显著提升,可实现零部件的近净成形。此外,挤压模具结构形状相对简单,制造容易,便于批量化生产和更换模具。因此,采用挤压工艺生产高压容器筒体,可使其金属变形均匀,材料内部组织和性能得到改善,且挤压成形零件尺寸接近高压容器最终尺寸,减少了零件后期加工工作量,提高材料利用效率。但是,高压容器原材料一般为高强钢,其挤压生产中设备载荷较大,能耗较高且模具磨损速度快,这就对挤压和润滑工艺提出了极高的要求。
技术实现要素:5.针对上述现有技术中的不足,本发明提供一种高压容器单层厚壁筒体的分段式挤压成形方法及容器,克服了长径比较大的高强钢挤压件成形过程中模具温度过高、冲头软化和摩擦力较大的问题。
6.为了实现上述目的,本发明提供一种高压容器单层厚壁筒体的分段式挤压成形方法,包括步骤:
7.s1:坯料下料步骤,将一圆柱形棒料经锯切下料,获得所需长度的所述坯料;
8.s2:预备成形步骤,采用密闭墩粗工艺在所述坯料上端锻出一凹坑;
9.s3:采用高频加热方式加热所述坯料,将所述坯料放置入一挤压筒内,在所述凹坑内放置玻璃润滑垫,在所述坯料的外周采用玻璃润滑管将所述坯料与所述挤压筒隔开;通过一压机推动一挤压凸模下压,挤压出部分高压容器筒壁,完成初步挤压;
10.s4:将所述挤压凸模拔出,采用盐浴介质冷却所述挤压凸模或更换所述挤压凸模实现降温,并在所述高压容器筒壁内再次放置所述玻璃润滑垫补充润滑剂,然后推动所述挤压凸模继续下压直至挤压出的高压容器满足所需长度。根据容器实际尺寸、凸模温度升高和玻璃润滑剂使用情况,可进行2次或多次分段挤压,亦可进行两次或多次放置玻璃润滑垫。
11.优选地,所述坯料的初始直径小于所述挤压筒的内径1~2mm。
12.优选地,所述s2步骤中,所述预备成形步骤采用密闭锻造方法,锻出的所述凹坑应位于所述坯料的正中间,所述凹坑的深度为或接近300mm。
13.优选地,所述s3步骤中,所述玻璃润滑垫的直径比所述凹坑的直径小0.5~1mm。
14.优选地,所述s3步骤中,所述玻璃润滑管厚度为或接近10mm,所述挤压筒入口和所述玻璃润滑管上端压设有一密封圈。
15.优选地,所述s3步骤中,所述挤压凸模包括一挤压冲头和一挤压杆,所述挤压冲头螺接于所述挤压杆下端;所述挤压冲头采用耐热的金属陶瓷镍基碳化钨材料制成,所述挤压杆采用模具钢制成。
16.优选地,所述s3步骤中,所述挤压筒的壁厚大于所述坯料初始直径的70%;所述挤压筒内设冷却水循环系统。
17.优选地,所述s4步骤中,所述冷却介质采用质量百分比浓度为或接近20%的盐水。
18.本发明的一种由本发明所述的高压容器单层厚壁筒体的分段式挤压成形方法制备获得的容器。
19.本发明由于采用了以上技术方案,使其具有以下有益效果:
20.1、本发明中分段挤压工艺显著减少挤压冲头和坯料的连续接触时间,且在分段挤压工序之间可以更换挤压冲头或者对挤压冲头进行合理冷却,避免挤压杆过热,从而提高挤压冲头强度和使用寿命。
21.2、两次或多次玻璃润滑垫放入提高了润滑剂的稳定性,避免了用光润滑剂导致的挤压冲头和坯料即刻粘连焊合失效,从而减少挤压冲头的磨损及“焊合”风险,保证挤压顺利进行,同时可降低摩擦力,显著减少成形吨位,提高挤压模具寿命。
22.3、采用组合式挤压凸模,挤压冲头头部采用耐热的金属陶瓷镍基碳化钨材料ct510制作而成,保证冲头的高温强度。通过充分润滑以及挤压冲头头部的“挤压带”设计,保证挤压冲头杆不与坯料直接接触,避免挤压凸模温度升高,保证挤压冲头的强度和使用寿命。
23.4、设置玻璃润滑管密封圈,防止玻璃润滑管长时间与挤压筒接触融化后的“喷出”用光,保证挤压筒与坯料之间始终存在均匀的玻璃润滑膜。相应的,挤压筒内部设置冷却水循环系统,保证坯料与挤压筒在长时间分段挤压过程中不发生焊合。
24.5、本发明中容器的采用挤压工艺,与传统整体锻造或卷板工艺相比,变形过程中坯料始终保持三向压应力状态,有利于材料内部缺陷的锻合,且材料内部纤维分布合理,有
利于提高材料利用率。
附图说明
25.图1为本发明实施例的预备成形阶段的挤压状态图;
26.图2为本发明实施例的初步挤压阶段的挤压状态图;
27.图3为本发明实施例的完成挤压阶段的挤压状态图;
28.图4为本发明实施例的挤压模具的结构示意图。
具体实施方式
29.下面根据附图图1~图4,给出本发明的较佳实施例,并予以详细描述,以便更好地理解本发明的功能、特点。
30.请参阅图1~图4,本发明实施例的一种高压容器单层厚壁筒体的分段式挤压成形方法,包括步骤:
31.s1:坯料下料步骤,将一圆柱形棒料经锯切下料,获得所需长度的坯料;
32.坯料的初始直径小于挤压筒8的内径1~2mm。
33.s2:预备成形步骤,采用密闭墩粗工艺在坯料上端锻出一凹坑,获得预成形件3;
34.s2步骤中,预备成形步骤采用密闭锻造方法,锻出的凹坑应位于坯料的正中间,凹坑的深度为或接近300mm。
35.本实施例中,凹坑的截面直径为285mm,比玻璃润滑垫5尺寸大1~2mm,便于将玻璃润滑垫5置入初步成形的坯料底部并定位。
36.s3:将坯料放置入一挤压筒8内,在凹坑内放置玻璃润滑垫5,在坯料的外周采用玻璃润滑管7将坯料与挤压筒8隔开,采用高频加热方式加热坯料;通过一压机推动一挤压凸模4下压,挤压出部分高压容器筒壁,完成初步挤压,获得初步挤压件件6;
37.s3步骤中,玻璃润滑垫5的直径比凹坑的直径小0.5~1mm。
38.s3步骤中,玻璃润滑管7厚度为或接近10mm,挤压筒8入口和玻璃润滑管7上端压设有一密封圈9。
39.本实施例中,密封圈9采用耐高温的陶瓷材料,且在内圈顶部设置约30
°
的导向角,方便坯料放入挤压筒8中。
40.s3步骤中,挤压凸模4包括一挤压冲头42和一挤压杆41,挤压冲头42螺接于挤压杆41下端;挤压冲头42采用耐热的金属陶瓷镍基碳化钨材料ct510制成,挤压杆41采用模具钢制成。
41.s3步骤中,挤压筒8的壁厚大于坯料初始直径的70%;挤压筒8内设冷却水循环系统10。
42.玻璃润滑垫5厚度在100mm左右,玻璃润滑剂的融化温度与挤压温度要匹配好,通过调控挤压温度与玻璃润滑垫5的成分,控制玻璃润滑垫5的融化速度,保证在热坯料与挤压冲头42之间形成均匀的玻璃膜。
43.s4:将挤压凸模4拔出,采用盐浴介质冷却挤压凸模4或更换挤压凸模4实现降温,并在高压容器筒壁内再次放置玻璃润滑垫5补充润滑剂,然后推动挤压凸模4继续下压直至挤压出的高压容器满足所需长度。
44.s4步骤中,冷却介质采用质量百分比浓度为或接近20%的盐水。
45.冷却方法一般是盐浴介质冷却,可预防挤压冲头42开裂。采用盐浴介质冷却挤压凸模4或更换挤压凸模4,控制挤压冲头42温度降至300℃以下。
46.本发明实施例的一种由本实施例的高压容器单层厚壁筒体的分段式挤压成形方法制备获得的容器。
47.圆柱形棒料的来源广泛,经锯床下料即可获得坯料。经过密闭墩粗在坯料上端锻出凹坑,可用于放置玻璃润滑垫5,从而有效避免润滑垫错位、倒翻,保证玻璃润滑剂在挤压凸模4和变形材料之间分布均匀。此外,密闭墩粗过程可保证坯料成形准确,锻合坯料内部可能存在的缺陷,提高坯料内部组织均匀性。
48.分段挤压是整个挤压过程中的关键,其基本要求是避免挤压冲头42和热坯料的直接接触、避免坯料和挤压凸模4直接接触,避免挤压凸模4温度过分升高而发生强度下降和寿命降低。为此,本发明采用分段式挤压生产过程,即密闭锻造预备成形
→
加玻璃润滑垫5首次挤压
→
拔出凸模冷却
→
再次添加玻璃润滑垫5
→
再次挤压成形。本方法通过分段挤压、中间冷却减少了挤压冲头42与坯料的“连续接触”时间,可有效防止挤压冲头42高温软化;此外,第二阶段首次挤压完成后,被挤出部分筒壁温度在挤压凸模4拔出后温度急速降低,减少了对第三阶段挤压冲头42的加热能量,进一步避免了挤压冲头42的高温软化。
49.本工艺流程中分两次放置玻璃润滑垫5,可以保证润滑剂足够,提高润滑剂稳定性和挤压安全性,有效避免了挤压冲头42和热坯料的直接接触,避免了用光导致的即刻粘连焊合失效,从而减少挤压冲头42的磨损及焊合风险,保证挤压顺利进行。同时可降低挤压过程的摩擦力大小,显著减少成形吨位,还可降低对许可挤压温度区间控制和润滑剂性能的要求。坯料外周采用玻璃润滑管7把坯料与挤压筒8材料隔开,并在玻璃润滑管7上端、挤压筒8入口处设置一个陶瓷的密封圈9,可有效防止玻璃润滑管7融化后溢出而过早消耗完。
50.本工艺过程中采用玻璃润滑管7和玻璃润滑垫5,由于玻璃优越的隔热作用,且在挤压筒8内设置冷却水循环系统10,如图4所示,从而减少热坯料与挤压筒8的热干涉,提高挤压筒8的使用寿命,保证挤压筒8与热钢坯不焊合粘连。
51.本工艺方法采用挤压方式进行筒形件成形,制备获得的容器其几何形状与尺寸精度容易保障,流线分布合理,且无原材料浪费,具有成形精确、效率高且挤压件内部质量好的特点。
52.例如:
53.需要制备的容器,其材料为4130x高强结构钢,外径为406mm,厚度为60mm,长度为2000mm,筒体总体积约为1.381
×
108mm3,选用直径为406mm,高度为1100的坯料进行分段挤压,坯料总体积为1.424
×
108mm3。4130x高强钢具有较高的热强度和韧性,在500℃以下可承受较大的压应力,一般在调制状态下使用。容器长径比较大,难以采用简单原始棒料直接一次锻造成形,直接挤压成形可能造成挤压冲头42温升过快、模具变形和磨损等诸多问题,因此,合理的挤压和润滑工艺设计就成为高压容器厚壁筒体挤压生产的关键环节。
54.首先,考虑到实际挤压时,由于几何不对称,温度不对称以及润滑不对称等影响,经过反挤压得到的筒形件往往会出现偏离理想形状的问题。因此,在正式开始反挤压之前,设计了密闭墩粗的预成形工艺,即利用预成形加压凸模1和预成形加压凹模2在坯料上端锻出直径为285mm、深度约为300mm的凹坑,获得预成形件3,一方面便于后续放置玻璃润滑垫
5,另一方面,密闭墩粗得到的形状较为精确,可诱导后续加工过程中坯料沿着理想形状变形。
55.其次,考虑到该容器长度为2000mm,挤压过程中挤压冲头42压下量为1000mm左右,钢坯加热温度为1100℃左右,长时间挤压可能导致模具变形、挤压冲头42过热软化等问题。首先,设计了组合式挤压凸模4,挤压冲头42部分直径为286mm,采用耐热的金属陶瓷镍基碳化钨材料ct510制成。采用模具钢制作挤压杆41,其直径为256mm,挤压杆41和挤压冲头42通过螺纹连接。其次,设计了分段式挤压工艺,在预成形的凹坑内放置厚度约为100mm,直径280mm的固体玻璃润滑垫5,将预成形的坯料初步挤压至高压容器筒壁长度达到1000mm左右时,将挤压冲头42拔出,采用盐水对挤压冲头42进行冷却,使其温度降低到300℃以下。并在高压容器筒壁内再次放置厚度约为100mm,直径280mm的固体玻璃润滑垫5,再次推动挤压冲头42使筒壁高度上升1000mm,最终完成总长度为2000mm的高压容器筒壁的挤压过程。两次放置玻璃润滑垫5,保证挤压过程中挤压冲头42始终不与坯料接触,避免坯料与挤压冲头42发生粘合,同时显著降低变形摩擦力和变形产热,降低变形载荷。此外,为避免坯料与挤压筒8焊合,在坯料与挤压筒8之间以及设置于挤压筒8底部的挤压砧座12与坯料之间放置厚度为10mm左右的玻璃润滑管7,保证坯料在变形过程中不与挤压筒8和挤压砧座12直接接触。并在玻璃润滑管7上端设置陶瓷密封圈9,以防融化后的玻璃润滑剂喷出,其导入口的导向角的角度设计为30
°
左右,以便预成形件3放入。进一步的,为了实现对挤压筒8筒壁的及时冷却,挤压筒8厚度设计为坯料直径的70%以上,约为300mm,挤压筒8内设计冷却水循环系统10。
56.请参阅图4,针对本发明设计分段式挤压工艺流程,其挤压模具结构如图4所示,包括挤压杆41;挤压冲头42;密封圈9;挤压筒8;冷却水循环系统10;挤压砧座12;坯料制备而成的预成形件3;螺纹连接结构11。
57.请参阅图1~图4,本发明涉及的预成形件3分段挤压模具工作原理为:将玻璃润滑垫5置于预成形件3的凹坑内,玻璃润滑管7置于挤压筒8底部和侧边,第一阶段通过密闭墩粗获得的预成形件3置于玻璃润滑管7上方,挤压杆41与热模锻压机滑块相连,滑块向下移动,带动挤压冲头42向下移动。推动预成形件3向下移动,同时预成形件3底端的玻璃润滑垫5融化填充到挤压冲头42与预成形件3之间,避免坯料与挤压冲头42的直接接触而焊合。挤压冲头42向下移动至高压容器筒壁高度上升至1000mm左右时,与热模锻压机滑块相连的挤压杆41上移,待挤压冲头42移出高压容器筒壁后将其进行盐浴冷却,随后,在高压容器筒壁底部再次放置玻璃润滑垫5,然后与热模锻压机滑块相连的挤压杆41下移,推动高压容器筒壁上升至2000mm,完成最终的挤压成形。
58.综上所述,高压容器单层厚壁筒体的分段挤压工序为:锯床下料、密闭墩粗获得预成形件3、初次添加玻璃润滑垫5并挤压成形获得挤压件、拔出挤压凸模4冷却并添加玻璃润滑剂、最终挤压获得最终挤压件,所示。
59.本实施例锻造成形过程为:
60.步骤(1):采用直径为406mm的圆柱形棒料,经锯切下料,获得1100mm长的坯料,坯料体积为1.424
×
108mm3。
61.步骤(2):将坯料通过高频加热至1100℃,通过密闭锻造在钢坯上端锻出深度为300mm,直径为285mm凹坑,获得如图1所示的预成形件3。
62.步骤(3):在挤压筒8底部和圆周处放置10mm厚的将玻璃润滑管7,随后将通过高频加热至1100℃的预成形件3沿着轴向放入挤压筒8中,并在预成形件3的凹坑内放置厚度为100mm的玻璃润滑垫5,通过反挤压获得如图2中所示形状的初步挤压件6,该过程中玻璃润滑管7融化填充到挤压筒8与坯料之间,玻璃润滑垫5融化填充至挤压冲头42与坯料之间。
63.步骤(4):将挤压冲头42拔出,采用20%的盐水对挤压冲头42进行降温冷却,再次在初步挤压件6底部添加玻璃润滑垫5,随后继续推动挤压冲头42向前移动,挤压坯料至所需的长度,完成分段挤压过程。
64.步骤(5):分段挤压结束后,顶出挤压件,然后进行相应的变形后热处理。
65.以上结合附图实施例对本发明进行了详细说明,本领域中普通技术人员可根据上述说明对本发明做出种种变化例。因而,实施例中的某些细节不应构成对本发明的限定,本发明将以所附权利要求书界定的范围作为本发明的保护范围。