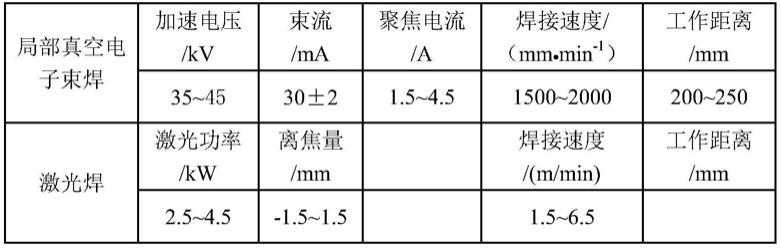
1.本发明属于连续管材生产技术领域,涉及纯钛或钛合金连续管材的生产制备方法。
背景技术:2.连续管(coiled tubing,缩写ct)是一种可用于海底穿光缆、跨海大桥穿电缆、油气井维修、测井、钻井、完井、油气输送等作业领域用的单根长度可达上万米的新型管材。随着工业生产和社会生活的不断发展以及石油天然气资源的过渡开采,浅层油气资源逐渐枯竭,油气开发已走向深井、超深井的油气藏资源和海洋石油天然气资源以及非常规油气藏,高温、高压、强腐蚀性的复杂工况环境,对高端油气开采装备提出了更高要求。特别在海洋油气藏开发、海底长距离穿线缆、跨海桥隧管路和线路设施以及含有h2s、co2、cl-等腐蚀性介质的海洋、内陆高酸性油气田开发过程中,普通材质的连续管材将发生系列腐蚀(点蚀、失重腐蚀、局部腐蚀等)并随着服役时间的延长腐蚀速率急剧加快甚至是失效(氢致开裂hic、硫化物应力腐蚀开裂sscc等),对工程建设及装备造成巨大经济损失和破坏。纯钛或钛合金材料具有质量轻、耐腐蚀性能卓越等特性,在海洋气候环境及海水浸润环境中材料表面仍然具有光泽,在酸性油气田也有非常好的耐腐蚀性,部分内陆酸性油气田已开始采用钛合金作为原料生产加工钻井装备和设施,并有初步应用成效。但是,一直没有纯钛或钛合金连续管材产品的生产和应用,关于纯钛或钛合金连续管材产品的研发、生产、制备等没有任何报道或消息,完全处于空白状态。而已有的常规连续管材生产制备技术却无法完成和实现纯钛或钛合金连续管材的生产制备。
3.因此,开发适用于海洋油气藏开采、海底长距离穿线缆、跨海桥隧管路和线路设施建设以及含有h2s、co2、cl-等腐蚀性介质的深海、内陆高酸性深井与超深井油气田用纯钛或钛合金连续管材对于解决海洋环境油气田、跨海桥隧、海底长距离穿线缆等特种管材装备的腐蚀破坏性问题具有极大优势。
4.目前,市场上常规连续管材主要以碳钢材料为主,也有少许高合金连续管材,对于纯钛或钛合金连续管材没有任何产品和相关技术的报道,其系统化的生产制备技术仍然处于空白期。现有常规连续管材和高合金连续管材的生产制备方法(连续排辊渐进压制成型+高频电阻焊+感应热处理),无论是从焊接方法上、工艺措施上和热处理方面均无法适应和满足纯钛或钛合金连续管的生产制备要求,按照常规连续管材和高合金连续管材的生产制备方法无法生产出满足使用要求的纯钛或钛合金连续管材,急需要一种既高效、又能保证连续管材高质量、高品质的生产制备方法。
技术实现要素:5.本发明的目的是提供一种纯钛或钛合金连续管材的生产制备方法,能够制备出具有优良的抗疲劳破坏能力、优良的塑韧性和耐腐蚀性能的纯钛或钛合金连续管材。
6.本发明所采用的技术方案是:
7.纯钛或钛合金连续管材的生产制备方法,包括以下步骤:
8.步骤1,将纯钛或钛合金原料卷按纵剪成宽度尺寸相同的带材;
9.步骤2,对相同宽度尺寸的前一卷带材的头和后一卷带材的尾进行焊接坡口的刮削加工;
10.步骤3,对完成头、尾刮削加工的纯钛或钛合金带材进行对头焊连接;
11.步骤4,采用连续排辊渐进压制成型方法将对头焊的纯钛或钛合金带材在线连续压制成一根连续的管状;
12.步骤5,在管状成型合缝点前进行焊接坡口的刮削加工;
13.步骤6,在管状成型的合缝点处进行在线连续纵缝焊接;
14.步骤7,对焊接完成后的内外焊缝余高进行连续刮削处理;
15.步骤8,全管体外表面进行纳米化处理,制备成纯钛或钛合金连续管;
16.步骤9,将制备成的纯钛或钛合金连续管连续缠绕在一定直径尺寸的卷筒装置上,完成制备。
17.本发明的特点还在于:
18.步骤1中纯钛或钛合金原料卷为ta0、ta1、ta2、ta3、ta4、ta5、ta6、ta7、ta8、ta8-1、ta9、ta9-1、ta10、ta11、ta15、ta17、ta18、tc1、tc2、tc3、tc4和tc4eli中的任意一种。
19.步骤2具体为:前一卷带材的头和后一卷带材的尾进行30~100
°
范围斜向的“y”型坡口刮削加工,坡口面夹角a为170~175
°
,坡口面宽度b为2.0~4.0mm,坡口面夹角深度c为0.1~0.5mm,钝边深度d为1.5~5.5mm。
20.步骤3具体的为:采用局部真空电子束焊接方法或激光焊接方法进行带材斜向对头连接焊形成焊缝,带材正、反面焊接高温区域附近长
×
宽=300mm
×
200mm范围内同时进行惰性气体保护。
21.步骤4中连续排辊渐进压制成型方法具体的为:先利用第一组特型辊压轮对对带材纵边进行连续折弯成形、接着由后续特型辊压轮对对带材由边部向里进行连续压弯变形、最后采用外置特型辊压轮对从外部进行挤压成形制成管状。
22.步骤5在管状成型合缝点前对管体合缝边进行刮削加工,采用“y”型坡口刮削加工坡口面夹角a为170~175
°
,坡口面宽度b为2.0~4.0mm,坡口面夹角深度c为0.1~0.5mm,钝边深度d为1.5~5.5mm。
23.步骤6具体为采用局部真空电子束焊接方法或激光焊接方法在合缝点处进行连续纵缝焊接形成连续管材焊缝,合缝点处坡口间隙为0,横向挤压量为0.5~3.0mm,管体内、外焊接高温区域附近长
×
宽=300mm
×
200mm范围内同时进行惰性气体保护。
24.步骤7中采用耐高温、耐粘刀的硬质合金刮刀对内外焊缝余高进行连续刮削处理,保证焊缝处与母材相平。
25.步骤8采用激光冲击喷丸技术对连续管材管体的外表面纳米化处理。
26.步骤9将制备成的纯钛或钛合金连续管材连续缠绕在直径尺寸为800~1800mm的卷筒装置上,管材末端用特制锁扣与卷筒外架装置锁住,端口用密封环保护。
27.本发明的有益效果是:
28.本发明提供了一种高性能纯钛或钛合金连续管材的生产制备方法,该技术方法可靠,具有很强的实用性,焊接坡口设计、焊材匹配、焊接方法确定、全管体外表面纳米化处理
等工序以及整套生产制备方法的提出均基于纯钛或钛合金连续管材的高质量生产,确保管材具有优良的抗疲劳破坏能力、优良的塑韧性和耐腐蚀性能,管材适用于海洋油气藏开采、海底长距离穿线缆、跨海桥隧管路和线路设施以及含有h2s、co2、cl-等腐蚀性介质的内陆高酸性深井与超深井油气田,解决海洋环境油气田、跨海桥隧、海底长距离穿线缆等特种管材装备的腐蚀破坏性问题,本发明的提出填补了纯钛或钛合金连续管材生产制造技术的空白处,处于国内领先水平。
附图说明
29.图1为本发明纯钛或钛合金连续管材的生产制备方法的流程图;
30.图2为本发明带材斜对头焊示意图;
31.图3为本发明带材斜对头处或管状成形合缝处“y”型焊接特型破口示意图;
32.图4为本发明连续排辊渐进压制管状成型工艺示意图;
33.图5为本发明纯钛或钛合金连续管材横截面结构示意图。
34.图中,1.前一卷带材的头部,2.后一卷带材的尾部,3.带材斜向对头焊缝,4.连续管材管体,5.连续管材焊缝。
具体实施方式
35.下面结合附图和具体实施方式对本发明进行详细说明。
36.本发明纯钛或钛合金连续管材的生产制备方法,如图1,具体按照以下步骤实施
37.步骤1,将纯钛或钛合金原料卷纵剪成宽度尺寸相同的带材;
38.步骤2,对相同宽度尺寸的两带材的头和尾进行坡口刮削加工;
39.步骤3,对完成头,尾坡口刮削加工的纯钛或钛合金带材进行对头焊连接,连接成单根长度达万米的纯钛或钛合金带材;
40.步骤4,采用连续排辊渐进压制成型方法将完成对头焊的纯钛或钛合金带材在线连续压制成一根连续的管状;
41.步骤5,在管状成型的合缝点前进行坡口刮削加工;
42.步骤6,在管状成型的合缝点处进行在线连续纵缝焊接;
43.步骤7,对焊接完成后的内外焊缝余高进行连续刮削处理;
44.步骤8,全管体外表面进行纳米化处理,制备成纯钛或钛合金连续管;
45.步骤9,将制备成的纯钛或钛合金连续管连续缠绕在一定直径尺寸的卷盘装置上,形成长度尺寸达万米的单根纯钛或钛合金连续管材新产品。
46.步骤1中纯钛或钛合金原料卷为ta0、ta1、ta2、ta3、ta4、ta5、ta6、ta7、ta8、ta8-1、ta9、ta9-1、ta10、ta11、ta15、ta17、ta18、tc1、tc2、tc3、tc4和tc4eli中的任意一种。
47.步骤1中纯钛或钛合金原料卷厚度为2.5~6.0mm,纵剪后的带材的宽度为80~600mm。
48.步骤2将前一卷带材的头1和后一卷带材的尾2进行30~100
°
范围(如图2所示)斜向的“y”型坡口刮削(具体设计如图3所示)加工使其露出新鲜金属光泽,坡口面夹角a为170~175
°
,坡口面宽度b为2.0~4.0mm,坡口面夹角深度c为0.1~0.5mm,钝边深度d为1.5~5.5mm;
49.步骤3采用局部真空电子束焊接方法或激光焊接方法进行带材斜向对头连接焊形成焊缝3,带材正、反面焊接高温区域附近长
×
宽=300mm
×
200mm范围内同时进行惰性气体保护;
50.步骤4中连续排辊渐进压制成型方法。具体成形过程如图4所示,先利用第一组特型辊压轮对对带材纵边进行连续折弯成形、接着由后续特型辊压轮对对带材由边部向里进行连续压弯变形、最后采用外置特型辊压轮对从外部进行挤压成形制成管状。
51.步骤5中进行管状成型合缝点前的纵向坡口刮削加工,具体按照图3中“y”型坡口刮削加工与步骤2中相同,坡口面夹角a为170~175
°
,坡口面宽度b为2.0~4.0mm,坡口面夹角深度c为0.1~0.5mm,钝边深度d为1.5~5.5mm。
52.步骤6中采用局部真空电子束焊接方法或激光焊接方法在合缝点处进行连续纵缝焊接形成连续管材焊缝5,合缝点处坡口间隙为0,横向挤压量为0.5~3.0mm,管体内、外焊接高温区域附近长
×
宽=300mm
×
200mm范围内同时进行惰性气体保护;
53.步骤7中采用耐高温、耐粘刀的硬质合金刮刀对内外焊缝余高进行连续刮削处理,保证焊缝处与母材相平;
54.步骤8中采用激光冲击喷丸技术进行连续管材管体4的外表面纳米化处理;
55.步骤9将制备成的纯钛或钛合金连续管(如图5)连续缠绕在直径尺寸为800~1800mm的卷筒装置上,管材末端用特制锁扣与卷筒外架装置锁住,端口用密封环保护。
56.实施例1
57.纯钛或钛合金连续管材的生产制备方法,具体按照以下步骤实施为:
58.步骤1、将壁厚为3.8mm、牌号为tc4的钛合金原料卷纵剪成230mm宽的带材;
59.步骤2、将前后两带材的头和尾刮削加工成斜向45
°
的“y”型坡口,坡口面夹角a=170
°
,坡口面宽度b=2.8mm,坡口面夹角的深度c=0.5mm,钝边深度d=3.3mm;
60.步骤3、采用局部真空电子束焊接方法进行带材斜向45
°
对头连接焊,纵向挤压量为2.0mm,带材正、反面焊接高温区域附近长
×
宽=300mm
×
200mm范围内同时进行惰性气体保护,焊接参数见下表1所示,连接成一根总长度达10000米的tc4钛合金带材;
61.或采用激光焊接方法进行带材斜向45
°
对头连接焊,纵向挤压量为1.4mm,带材正、反面焊接高温区域附近长
×
宽=300mm
×
200mm范围内同时进行惰性气体保护,焊接参数见下表1所示,连接成一根总长度达10000米的tc4钛合金带材;
62.步骤4、采用连续排辊渐进压制成型方法将10000米长tc4钛合金带材在线连续压制成一根连续的管状,压制工艺过程如图4所示;
63.步骤5、在管状成型合缝前进行管体合缝边纵缝的在线连续“y”型坡口刮削加工,坡口面夹角a=170
°
,坡口面宽度b=4.0mm,坡口面夹角的深度为c=0.5mm,钝边深度尺寸为d=3.3mm;
64.步骤6、在管状成型合缝点处采用局部真空电子束焊接方法进行连续纵缝焊接,横向挤压量为1.2mm,合缝点处坡口间隙为0,管体内、外焊接高温区域附近长
×
宽=300mm
×
200mm范围内同时进行惰性气体保护,焊接参数设置见下表2所示;
65.或在管状成型合缝点处采用激光焊接方法进行连续纵缝焊接,横向挤压量为1.0mm,合缝点处坡口间隙为0,管体内、外焊接高温区域附近长
×
宽=300mm
×
200mm范围内同时进行惰性气体保护,焊接参数设置见下表2所示;
66.步骤7、采用耐高温、耐粘刀的硬质合金刮刀对内外焊缝余高进行连续刮削处理;
67.步骤8、采用激光冲击喷丸技术进行全管体外表面纳米化处理,激光功率密度为16gw/cm2,激光脉冲宽度为15ns,光斑尺寸为4mm
×
4mm,覆盖率为100%。
68.步骤9、将制备成的规格为的tc4钛合金连续管在线连续缠绕在直径为1200mm的卷筒装置上,管材末端用特制锁扣与卷筒外架装置锁住,端口用密封环保护,这样就制备出长度尺寸达10000米的单根纯tc4钛合金连续管材新产品。
69.管材制备过程的焊接工艺参数设置如表1和表2所示,得到的tc4钛合金连续管材性能测试结果如表3;管材强度、塑性性能优良,弯曲疲劳次数和表面硬度均处于高水平。
70.表1带材斜向对头焊工艺参数
[0071][0072]
表2 tc4钛合金连续管材纵缝焊接工艺参数
[0073][0074]
表3 tc4钛合金连续管材性能测试结果
[0075]