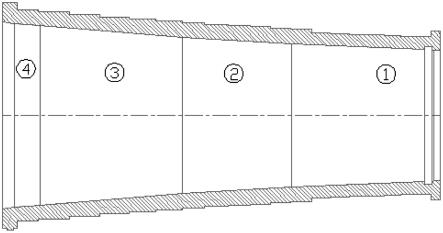
1.本发明涉及一种大型锥筒内孔与外圆表面粗加工提效的方法,属于锥筒加工技术领域。
背景技术:2.筒型工件粗加工方式通常将工件整合组装放置于立式车床进行内孔及外圆表面的粗加工,立式车床旋转工作台在加工过程中保证了对内孔及外圆表面的同轴度的控制。而在实际生产中,工件的形状尺寸存在着很大的变化,尤其是在工件尺寸过大,以及工件形状并不为圆筒型工件时,此类粗加工方法就无法得到有效的应用。同时采用这种粗加工方式加工过程效率低下,作业周期长,零件的摆放位置需要进行限定,即须将零件回转中心与回转工作台中心调整同心,操作过程复杂,对于大件生产过程中难以将重达数吨甚至数十吨的大体量零件调整至满足加工要求。
技术实现要素:3.本发明的目的是对现有锥筒型工件内孔及外圆表面粗加工技术进行优化,取消以往筒上、下半组装整体的立车传统加工作业方式,采用龙门铣数控车床装载滚铣刀具对工件上、下半锥型表面进行滚铣加工。实现零件位置摆放过程更加容易,并能够处理不同形状的工件类型,同时表面粗加工时间大幅减少,提高粗加工环节的加工效率。
4.为了实现上述的技术特征,本发明的目的是这样实现的:一种大型锥筒内孔与外圆表面粗加工提效的方法,它包括以下步骤:
5.步骤1:按主程序模块编制零件加工程序并存储于机床;
6.步骤2:零件拆分为上、下两半置工作台任意位置,保证工件哈夫面与工作台水平平行;
7.步骤3:根据锥筒的不同锥度段以及滚铣刀具有效加工尺寸计算滚铣半径变化范围与刀具滚铣次数;
8.步骤4:调用零件加工程序,按程序加工零件成品。
9.所述步骤1中机床采用龙门铣数控车床,通过建立锥筒龙门铣滚铣运动模型:
10.滚铣刀盘通过运动模型,自动根据锥筒锥度自动计算滚铣半径,保证滚铣刀盘沿锥筒内孔面或外表面作半圆弧运动;同时利用锥度尺寸与滚铣刀盘有效加工长度计算出相同锥度段内滚铣加工的次数,进而实现对多段锥度组合的锥筒工件的滚铣加工。
11.所述步骤1中主程序模块的设计过程为:
12.步骤1.1,设定机床加工基准;
13.步骤1.2,输入锥孔加工起始点与加工终点参数;
14.输入滚铣刀盘加工参数;
15.步骤1.3,计算滚铣理论加工次数;
16.步骤1.4,判断步骤1.3中理论加工次数是否为整数,并对其进行取整;
17.步骤1.5,计算每刀理论切削量;
18.步骤1.6,计算每刀滚铣半径;
19.步骤1.7,判断是否完成全部加工次数;若是,则结束,否则,赋值之后返回到步骤1.2中输入锥孔加工起始点与加工终点参数。
20.所述步骤1中参数具体设定过程为:
21.将待加工的锥筒根据锥度分为多段,选取锥度相同的锥孔段,并以相同锥度段的两端a、b作为加工起始点与加工终点,滚铣刀盘将沿ab段进行运动;确定选用的刀具加工宽度为r4,锥孔起始点纵坐标为r0=b,锥孔加工结束点纵坐标为r1=d,由此确定刀具滚铣距离范围为r3=r
0-r1;通过加工距离与刀具加工宽度得到粗略的加工次数r5=r3/r4,但计算结果可能不是一个整数,对r5进行取整处理,最终加工次数r6为取整值加一,同时计算加工过程中刀具向下的最终偏移距离为r7=r3/r6,利用刀具滚铣半径变化范围处于加工起点半径r8与加工终点半径r9之间,计算刀具每次滚铣坐标偏移值为下列公式,r
10
为滚铣半径每刀偏移量,下一次滚铣起点定位横向偏移坐标为r
11
,纵向偏移坐标为r
10
=r
0-r7:
[0022][0023]
程序运行次数达到r6时为程序运行终点。
[0024]
参数输入保护模块设计过程:
[0025]
由于加工起始点与加工终点通过操作人员进行设置,为了防止人为的输入偏差,造成不必要的危害,因此程序段建立输入保护模块,判断滚铣半径以及加工距离是否处于规定范围内,否者进入停止加工进入死循环。
[0026]
基于西门子840d数控系统开发,程序参数输入保护模块关键代码段如下:
[0027]
if r100》=200gotof pos_930判断输入刀具半径是否安全;
[0028]
pos_823:msg("dao ju ban jing bu dui");
[0029]
gotob pos_823进入死循环;
[0030]
pos_930:
[0031]
if 0《(r0-r1)《=r2 gotof pos_1判断加工是否在锥度范围内;
[0032]
gotob pos_823进入死循环;
[0033]
pos_1:。
[0034]
本发明有如下有益效果:
[0035]
通过本发明的实际应用,解除了零件在工作台上的摆放位置限制,零件在任意位置只需保证哈夫面与工作台水平平行即可。解决了对大型工件的尺寸限制,并且此项加工方法能够利用数控机床的编程优势,使加工的零件形状更具多样化。同时,大大缩短了产品加工周期,提高了粗加工环节的生产效率。
附图说明
[0036]
下面结合附图和实施例对本发明作进一步说明。
[0037]
图1为本发明中待加工锥筒的主视图。
[0038]
图2为本发明龙门铣粗加工原理。
[0039]
图3为本发明程序设计流程图。
具体实施方式
[0040]
下面结合附图对本发明的实施方式做进一步的说明。
[0041]
实施例1:
[0042]
参见图1-3,一种大型锥筒内孔与外圆表面粗加工提效的方法,它包括以下步骤:
[0043]
步骤1:按主程序模块编制零件加工程序并存储于机床;
[0044]
步骤2:零件拆分为上、下两半置工作台任意位置,保证工件哈夫面与工作台水平平行;
[0045]
步骤3:根据锥筒的不同锥度段以及滚铣刀具有效加工尺寸计算滚铣半径变化范围与刀具滚铣次数;
[0046]
步骤4:调用零件加工程序,按程序加工零件成品。
[0047]
实施例2:
[0048]
所述步骤1中机床采用龙门铣数控车床,通过建立锥筒龙门铣滚铣运动模型:
[0049]
滚铣刀盘通过运动模型,自动根据锥筒锥度自动计算滚铣半径,保证滚铣刀盘沿锥筒内孔面或外表面作半圆弧运动;同时利用锥度尺寸与滚铣刀盘有效加工长度计算出相同锥度段内滚铣加工的次数,进而实现对多段锥度组合的锥筒工件的滚铣加工。
[0050]
实施例3:
[0051]
所述步骤1中主程序模块的设计过程为:
[0052]
步骤1.1,设定机床加工基准;
[0053]
步骤1.2,输入锥孔加工起始点与加工终点参数;
[0054]
输入滚铣刀盘加工参数;
[0055]
步骤1.3,计算滚铣理论加工次数;
[0056]
步骤1.4,判断步骤1.3中理论加工次数是否为整数,并对其进行取整;
[0057]
步骤1.5,计算每刀理论切削量;
[0058]
步骤1.6,计算每刀滚铣半径;
[0059]
步骤1.7,判断是否完成全部加工次数;若是,则结束,否则,赋值之后返回到步骤1.2中输入锥孔加工起始点与加工终点参数。
[0060]
实施例4:
[0061]
所述步骤1中参数具体设定过程为:
[0062]
以加工
③
段锥孔为例,如图1、2所示。滚铣刀盘沿ab段进行运动,a、b两点为加工起始点与加工终点。将待加工的锥筒根据锥度分为多段,选取锥度相同的锥孔段,并以相同锥度段的两端a、b作为加工起始点与加工终点,滚铣刀盘将沿ab段进行运动;确定选用的刀具加工宽度为r4,锥孔起始点纵坐标为r0=b,锥孔加工结束点纵坐标为r1=d,由此确定刀具滚铣距离范围为r3=r
0-r1;通过加工距离与刀具加工宽度得到粗略的加工次数r5=r3/r4,但计算结果可能不是一个整数,对r5进行取整处理,最终加工次数r6为取整值加一,同时计算加工过程中刀具向下的最终偏移距离为r7=r3/r6,利用刀具滚铣半径变化范围处于加工起点半径r8与加工终点半径r9之间,计算刀具每次滚铣坐标偏移值为下列公式,r
10
为滚铣半径每刀偏移量,下一次滚铣起点定位横向偏移坐标为r
11
,纵向偏移坐标为r
10
=r
0-r7:
[0063][0064]
程序运行次数达到r6时为程序运行终点。
[0065]
实施例5:
[0066]
参数输入保护模块设计过程:
[0067]
由于加工起始点与加工终点通过操作人员进行设置,为了防止人为的输入偏差,造成不必要的危害,因此程序段建立输入保护模块,判断滚铣半径以及加工距离是否处于规定范围内,否者进入停止加工进入死循环。
[0068]
基于西门子840d数控系统开发,程序参数输入保护模块关键代码段如下:
[0069]
if r100》=200gotof pos_930判断输入刀具半径是否安全;
[0070]
pos_823:msg("dao ju ban jing bu dui");
[0071]
gotob pos_823进入死循环;
[0072]
pos_930:
[0073]
if 0《(r0-r1)《=r2 gotof pos_1判断加工是否在锥度范围内;
[0074]
gotob pos_823进入死循环;
[0075]
pos_1:。