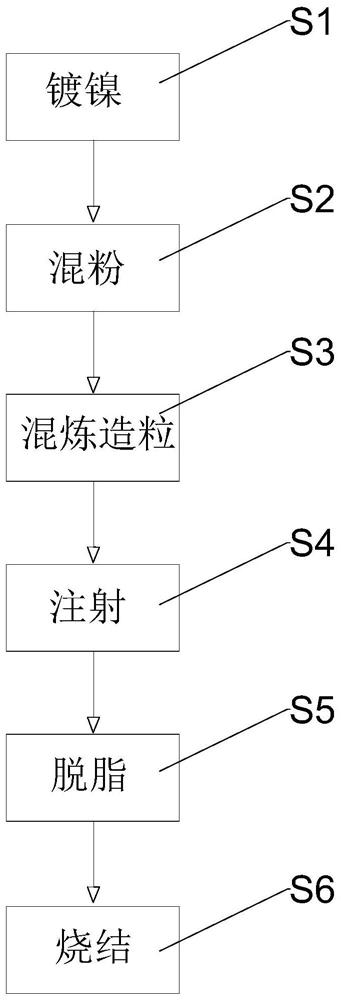
1.本发明涉及散热板技术领域,具体为翅柱式散热板及其成型工艺。
背景技术:2.在电动汽车的整体结构当中,整车控制系统、电池管理系统和电机控制器是电动汽车研发的三大关键技术。其中 igbt(insulated gate bipolar transistor)绝缘栅双极型晶体管是电动汽车的核心部件,igbt 是一种功率半导体开关,在运行过程中会存在功率损耗,损失的电能会以热的形式耗散到周围的环境当中。由于半导体材料对温度反应敏感,一旦散热不充分便会造成设备性能下降,甚至造成烧毁等不可逆损失,对汽车的安全行驶构成严重威胁;同时,igbt 模块价格昂贵。 另一方面,在 igbt 功率模块中,芯片的封装是由多种材料叠加而成的,各层材料的温度特性不同,热应力便是其中之一,热应力的产生对于设备的安全可靠运行构成了极大的威胁。针对 igbt 液冷散热模块,在翅柱式冷板研究方面,可以按照散热模块冷板结构将其分为三种,分别为带有铜基板的翅柱式液冷结构、不带有铜基板的平板式液冷结构以及不带有铜基板的翅柱式液冷结构。对于全铜的散热板而言,密度高,重量大,一般使用挤压成型工艺,这样的工艺不仅价格昂贵,而且成型出的散热板容易产生与芯片的热膨胀系数不匹配问题,造成芯片失效。
技术实现要素:3.为解决现有技术的不足,本申请提供了翅柱式散热板成型工艺,包括以下步骤:s1:镀镍,对碳化硅颗粒表面进行化学镀镍;s2:混粉,将镀镍后的碳化硅粉与铜粉进行混合以得到均匀混合粉末;s3:混炼造粒,将步骤s2中得到的均匀混合粉末与粘结剂在密炼机中混炼,混炼后的物料经造粒机制成喂料颗粒;s4:注射,将步骤s3中得到的喂料颗粒在注塑机中注射成型散热板生坯;s5:脱脂,将步骤s4中得到的散热板生坯在脱脂炉中进行脱脂;s6:烧结,在具有还原气氛或还原气与惰性气体混合气氛的烧结炉中进行高温烧结。
4.进一步的,采用β碳化硅,颗粒尺寸为10~20μm,镀镍介质为有机镍及硼氢化钠醇溶液,ph=9~9.5,溶液温度为40~60℃。
5.进一步的,所述步骤s2中,镀镍碳化硅颗粒体积分数为10~20%,采用球磨机进行球磨得到混合粉末。
6.进一步的,所述步骤s3中,粘结剂包括pom 75-85wt%、sa 1.2-2.2wt% 、小烛树蜡1.5-2.5wt% 、pp 4-8wt% 、bht 0.9-3.4wt% 和sebs 2.3-4.8 wt%。
7.进一步的,所述步骤s3中,将粘结剂与步骤s2中的混合粉末在密炼机中进行混炼,混炼的温度为160-190℃,混炼的时间为50-110min。
8.进一步的,所述步骤s3中,制成喂料颗粒的直径为2-5mm。
9.进一步的:所述步骤s4中,注射温度为140-190℃,注射压力为45-85mpa。
10.进一步的,所述步骤s4中,脱脂温度110-130℃,脱脂时间2-10h。
11.进一步的,所述步骤s5中,烧结温度900-1150℃,烧结时间为1-6h。
12.另外,本申请还提供一种由上述翅柱式散热板成型工艺制成的散热板。
13.本申请的有益之处在于:提供的翅柱式散热板成型工艺采用粉末注射成型,在形状上可以适应更复杂的散热结构设计,同时适应大批量生产,通过在粉末中加入镀镍的碳化硅颗粒作为铜的增强相,在保证散热板高热导率的基础上,实现散热板减重的同时降低热膨胀系数,使散热板热膨胀系数与硅片更为匹配,减少芯片失效风险。。
附图说明
14.图1为本申请翅柱式散热板成型工艺流程图。
具体实施方式
15.下面将结合附图和具体实施例对本发明进一步详细说明。
16.参见图1,本实施例提供了翅柱式散热板成型工艺,包括以下步骤:s1:镀镍,对碳化硅颗粒表面进行化学镀镍;具体而言,采用β碳化硅,颗粒尺寸10~20μm,镀镍介质为有机镍及硼氢化钠醇溶液,ph=9~9.5,水浴温度40~60℃,优选的,碳化硅颗粒尺寸为20μm,ph=9,水浴温度40℃。
17.s2:混粉,将镀镍后的碳化硅粉与铜粉进行混合以得到均匀混合粉末;具体而言,采用铜粉粒度为20~30um的铜粉,镀镍碳化硅颗粒粒度为10~20μm,镀镍碳化硅颗粒体积分数为10~20%,球磨机正转1h,转速150~200r/min ,反转1h,转速为150~200r/min,得到混合粉末。
18.优选的,采用24um的铜粉与碳化硅粉按照9:1的体积比在球磨机中混合,球磨参数为正转1h,转速150r/min ,反转1h,转速150r/min。
19.s3:混炼造粒,将步骤s2中得到的均匀混合粉末与粘结剂在密炼机中混炼,混炼后的物料经造粒机制成喂料颗粒;具体而言,将粘结剂与步骤s2中的混合粉末在密炼机中进行混炼,混炼的温度为160-190℃,混炼的时间为50-110min,粘结剂包括pom 75-85wt%、sa 1.2-2.2wt% 、小烛树蜡1.5-2.5wt% 、pp 4-8wt% 、bht抗氧化剂0.9-3.4wt% 和sebs 2.3-4.8 wt%,粘结剂加入顺序为pom、小烛树蜡、pp、sebs、bht、sa。
20.s4:注射,将步骤s3中得到的喂料颗粒在注塑机中注射成型散热板生坯;具体而言,注射温度为170-190℃,充填速度为30-50mm/s,注射时间为2-3s,保压60-80mpa,保压时间1-2s,背压为5~10mpa。
21.优选的,注射温度为190℃,充填速度为35mm/s,注射时间为2s,保压80mpa,保压时间1s,背压为5mpa。
22.s5:脱脂,将步骤s4中得到的散热板生坯在脱脂炉中进行脱脂;具体而言,在草酸气氛下脱脂,氮气作为保护气氛,脱脂温度110-130℃,脱脂时间2-10h,优选脱脂温度为120℃,脱脂时间8h。
23.s6:烧结,在具有还原气氛或还原气与惰性气体混合气氛的烧结炉中进行高温烧
结,烧结温度900-1150℃,烧结时间为1-6h,优选的,烧结温为980℃,烧结时间为3h。
24.其中,散热板生坯在脱脂炉和烧结炉中均放置在陶瓷承烧板上,脱脂完成后产品随陶瓷承烧板一起转移至烧结炉,以保证产品在转移过程中尺寸和结构不会发生变化。
25.上述步骤结束后得到散热基板,根据散热基板设计散热板框架,再通过模具压铸得到铝合金散热板框架,将散热基板通过搅拌摩擦焊接在散热板框架上。
26.尽管参照前述实施例对本发明进行了详细的说明,对于本领域的技术人员来说,其依然可以对前述各实施例所记载的技术方案进行修改,或者对其中部分技术特征进行等同替换,凡在本发明的精神和原则之内,所作的任何修改、等同替换、改进等,均应包含在本发明的保护范围之内。
技术特征:1.一种翅柱式散热板成型工艺,其特征在于,包括以下步骤:s1:镀镍,对碳化硅颗粒表面进行化学镀镍;s2:混粉,将镀镍后的碳化硅粉与铜粉进行混合以得到均匀混合粉末;s3:混炼造粒,将步骤s2中得到的均匀混合粉末与粘结剂在密炼机中混炼,混炼后的物料经造粒机制成喂料颗粒;s4:注射,将步骤s3中得到的喂料颗粒在注塑机中注射成型散热板生坯;s5:脱脂,将步骤s4中得到的散热板生坯在脱脂炉中进行脱脂;s6:烧结,在具有还原气氛或还原气与惰性气体混合气氛的烧结炉中进行高温烧结。2.根据权利要求1所述的翅柱式散热板成型工艺,其特征在于:所述步骤s1中,采用β碳化硅,颗粒尺寸为10~20μm,镀镍介质为有机镍及硼氢化钠醇溶液,ph=9~9.5,溶液温度为40~60℃。3.根据权利要求1所述的翅柱式散热板成型工艺,其特征在于:所述步骤s2中,镀镍碳化硅颗粒体积分数为10~20%,采用球磨机进行球磨得到混合粉末。4. 根据权利要求1所述的翅柱式散热板成型工艺,其特征在于:所述步骤s3中,粘结剂包括pom 75-85wt%、sa 1.2-2.2wt% 、小烛树蜡1.5-2.5wt% 、pp 4-8wt% 、bht 0.9-3.4wt% 和sebs 2.3-4.8 wt%。5.根据权利要求4所述的翅柱式散热板成型工艺,其特征在于:所述步骤s3中,将粘结剂与步骤s2中的混合粉末在密炼机中进行混炼,混炼的温度为160-190℃,混炼的时间为50-110min。6.根据权利要求1所述的翅柱式散热板成型工艺,其特征在于:所述步骤s3中,制成喂料颗粒的直径为2-5mm。7.根据权利要求1所述的翅柱式散热板成型工艺,其特征在于:所述步骤s4中,注射温度为140-190℃,注射压力为45-85mpa。8.根据权利要求1所述的翅柱式散热板成型工艺,其特征在于:所述步骤s5中,脱脂温度110-130℃,脱脂时间2-10h。9.根据权利要求1所述的翅柱式散热板成型工艺,其特征在于:所述步骤s6中,烧结温度900-1150℃,烧结时间为1-6h。10.一种由权利要求1-9任意一项所述的翅柱式散热板成型工艺制成的散热板。
技术总结本发明公开了翅柱式散热板及其成型工艺,包括以下步骤:S1:镀镍,对碳化硅颗粒表面进行化学镀镍;S2:混粉,将镀镍后的碳化硅粉与铜粉进行混合以得到均匀混合粉末;S3:混炼造粒,将上述得到的均匀混合粉末与粘结剂在密炼机中混炼,混炼后的物料经造粒机制成喂料颗粒;S4:注射,将S3中得到的喂料颗粒在注塑机中注射成型散热板生坯;S5:脱脂,将S4中得到的散热板生坯在脱脂炉中进行脱脂;S6:烧结,在具有还原气氛或还原气与惰性气体混合气氛的烧结炉中进行高温烧结。本申请采用粉末注射成型,在形状上可以更加多样,有利于批量生产,而且可以降低重量并降低热膨胀系数,减少与芯片的热膨胀系数不匹配的问题,减少芯片失效风险。减少芯片失效风险。减少芯片失效风险。
技术研发人员:邓凌曲 张露 王宇枭 王祥羽 雍鹏凌
受保护的技术使用者:南京泉峰汽车精密技术股份有限公司
技术研发日:2021.12.22
技术公布日:2022/5/6