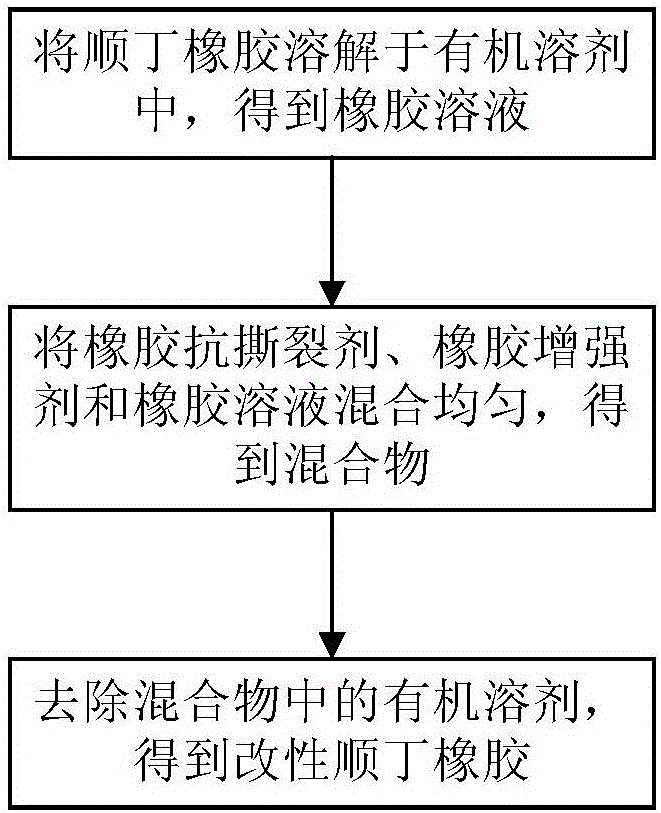
本发明属于橡胶改性
技术领域:
,具体涉及一种改性顺丁橡胶及其制备方法和应用,尤其涉及一种高抗撕裂性能的改性顺丁橡胶及其改性工艺,以及该改性顺丁橡胶在汽车轮胎等橡胶制品中的应用。
背景技术:
:顺丁橡胶(br)是顺式-1,4-聚丁二烯橡胶的简称,是由丁二烯单体聚合而成的结构规整的合成橡胶,其顺式结构含量在95%以上。由于顺丁橡胶的分子结构较为规整,分子链非常柔顺,因此,与天然橡胶或者丁苯橡胶等合成橡胶相比,顺丁橡胶通常具有更突出的柔顺性、弹性、耐磨性、耐屈挠性能、耐低温性能等,因此在汽车轮胎、制鞋和建筑领域等,都有着非常广泛的应用。尤其是,采用顺丁橡胶为原料,经硫化处理等加工后制得的汽车轮胎具有高抗湿滑性和低滚动阻力等特点;同时,由于顺丁橡胶的制备工艺已发展的较为成熟,原料成本和加工成本都较低,因此,顺丁橡胶是一直是汽车轮胎用橡胶的首选材料。但是,由于顺丁橡胶自身分子结构的限制,造成其后续加工得到的硫化橡胶及汽车轮胎等橡胶制品的撕裂强度较低,耐刺扎能力及耐崩花掉块能力也都不理想。因此,在用于制备汽车轮胎等橡胶制品时,顺丁橡胶必须要与丁苯橡胶等其它胶种并用,同时顺丁橡胶的用量应通常不大于30%,以在维持高抗湿滑性和低滚动阻力的同时,保证汽车轮胎的撕裂强度、耐刺扎能力及耐崩花掉块能力满足相关要求。因此,如何对顺丁橡胶进行改性,使得到的改性顺丁橡胶在用于硫化橡胶或者进一步用于汽车轮胎等橡胶制品时,能够具有良好的撕裂强度、耐刺扎能力和耐崩花掉块能力,是目前有待解决的技术问题。技术实现要素:针对现有技术中存在的上述问题,本发明提供一种改性顺丁橡胶及其制备方法,用于提高顺丁橡胶在用于硫化橡胶及橡胶制品时的撕裂强度、耐刺扎能力和耐崩花掉块能力;本发明还提供上述改性顺丁橡胶在橡胶制品中的应用,以及采用上述改性顺丁橡胶所加工得到的硫化橡胶。为提高顺丁橡胶的撕裂强度,本发明首先提供一种改性顺丁橡胶的制备方法,包括:将顺丁橡胶溶解于有机溶剂中,得到橡胶溶液;将橡胶抗撕裂剂、橡胶增强剂和上述橡胶溶液混合均匀,得到混合物;去除上述混合物中的有机溶剂,得到改性顺丁橡胶。上述制备方法,实际上是采用橡胶抗撕裂剂和橡胶增强剂对顺丁橡胶进行改性的过程。在此改性过程中,实现橡胶抗撕裂剂、橡胶增强剂与顺丁橡胶之间的充分混合是关键。本发明首先将顺丁橡胶溶解于有机溶剂中,使顺丁橡胶作为“溶质”,均匀地分散于有机溶剂这一“溶剂”中,得到了较为均一的橡胶溶液;然后将橡胶溶液与橡胶抗撕裂剂、橡胶增强剂混合,使橡胶抗撕裂剂和橡胶增强剂能够分散于顺丁橡胶的分子结构中。相较于传统方法中以固态形式直接物理混合,或者通过加热熔融搅拌实现混合,本发明所提供的混合方法,更易实现橡胶抗撕裂剂和橡胶增强剂在顺丁橡胶中的均匀分散。并且,研究发现,与采用未改性顺丁橡胶制得的硫化橡胶相比,采用上述混合方式得到的改性顺丁橡胶,其再经硫化处理得到的硫化橡胶,其撕裂强度、耐刺扎能力及耐崩花掉块能力都有了明显改善。发明人分析,可能是由于橡胶抗撕裂剂和橡胶增强剂的加入,改变了顺丁橡胶原本的分子链结构。所以在后续对改性顺丁橡胶进行硫化等加工以制备硫化橡胶以及橡胶制品的过程中,顺丁橡胶的分子网络结构也发生改变,有利于提高改性顺丁橡胶与填料之间的相互作用力,进而能够提高硫化橡胶甚至汽车轮胎等橡胶制品的撕裂强度、耐刺扎能力及耐崩花掉块能力。上述混合过程,可以是将橡胶抗撕裂剂和橡胶增强剂加入到顺丁橡胶溶剂中,然后实施充分的搅拌,即可将橡胶抗撕裂剂和橡胶增强剂均匀地分散于顺丁橡胶中。然后,即可去除上述混合物中的有机溶剂。去除混合物中有机溶剂的过程,可采用本领域常规的技术手段进行。作为本发明中的一种优选实施方式,可以采用终止剂,去除混合物中的有机溶剂。具体的,是向混合物中加入终止剂,使混合物中的橡胶抗撕裂剂、橡胶增强剂和顺丁橡胶从有机溶剂中析出,然后经固液分离,得到的块状的弹性固体即为改性顺丁橡胶。可以理解,上述所用的终止剂,能够使混合物中的顺丁橡胶、橡胶抗撕裂剂和橡胶增强剂从有机溶剂中析出,并且在此过程中,还不影响顺丁橡胶、橡胶抗撕裂剂和橡胶增强剂之间的均匀混合。具体的,上述终止剂可以根据有机溶剂及橡胶抗撕裂剂、橡胶增强剂的理化性质等因素合理选择,比如该终止剂中可以含有甲醇、乙醇、乙二醇和丙三醇中的至少一种。在本发明具体实施过程中,通常所使用的终止剂是甲醇、乙醇、乙二醇或丙三醇,以将有机溶剂与顺丁橡胶、橡胶抗撕裂剂和橡胶增强剂充分分离。在本发明具体实施过程中,将上述终止剂加入到混合物中,则含有顺丁橡胶、橡胶抗撕裂剂和橡胶增强剂的固体混合物与含有有机溶剂和终止剂的液体混合物发生分层,然后经固液分离,最终得到改性后的顺丁橡胶,具体为块状的弹性固体。可以理解,上述块状的弹性固体中可能还残留有少量有机溶剂,因此还可以对其进一步实施干燥处理,以彻底去除其中的有机溶剂。可以理解,在上述对顺丁橡胶改性的过程中,合理控制顺丁橡胶、橡胶抗撕裂剂和增强剂之间的比例,能够使最终得到的硫化橡胶及橡胶制品能够保持顺丁橡胶本身原有的性能优势,并同时提高撕裂强度、耐刺扎能力及耐崩花掉块能力。在本发明具体实施过程中,顺丁橡胶:橡胶抗撕裂剂:橡胶增强剂的重量比为100:(1~50):(1~10)。也即,以顺丁橡胶的重量为100份计,橡胶抗撕裂剂的重量为1~50份,橡胶增强剂的用量为1~10份。本发明所用于改性的顺丁橡胶,可以是本领域常用的顺丁橡胶,比如目前制备汽车轮胎所常用的顺丁橡胶原料。可以理解,合理控制顺丁橡胶的分子量及分子量分布,对于使改性橡胶保持顺丁橡胶原有的低滚动阻力和高抗湿滑性能等优势是有利的,通常可控制顺丁橡胶的数均分子量为80,000~120,000,分子量分布指数(重均分子量与数均分子量的比值)为1.5~5.0。相应的,上述用于溶解顺丁橡胶的有机溶剂,可以是本领域为制备胶液所常用的有机溶剂,包括但不限于己烷、环己烷、甲苯和四氢呋喃中的一种或多种。本发明中所用的橡胶抗撕裂剂,也称为抗撕裂改性剂。研究发现,若橡胶抗撕裂剂的分子结构中含有双键官能团和/或氨基基团,对于提高顺丁橡胶在硫化后的撕裂强度、耐刺扎能力及耐崩花掉块能力是非常有利的。在本发明具体实施过程中,所用的橡胶抗撕裂剂选自酚醛树脂、萜烯树脂、碳五石油树脂(碳5树脂)、碳九石油树脂(碳9树脂)、丙烯酰胺和聚丙烯酰胺中的至少一种。进一步的,上述抗撕裂改性剂与顺丁橡胶之间的质量比,可以为(20~50):100,通常为(20~30):100。本发明中所用的橡胶增强剂,可以是目前橡胶加工过程中常用的增强剂。在本发明具体实施过程中,所用的橡胶增强剂可以是炭黑、白炭黑、碳酸钙和氧化镁中的至少一种,也可以是其它增强剂。具体的,上述橡胶增强剂与顺丁橡胶之间的质量比可以为(1~8):100,通常控制橡胶增强剂与顺丁橡胶之间的质量比为(5~8):100。本发明还提供一种采用上述制备方法制得的改性顺丁橡胶。可以理解,由于上述制备方法,能够使得到的改性顺丁橡胶在用于制备硫化橡胶及橡胶制品时,能够显著改善硫化橡胶及橡胶制品的撕裂强度、耐刺扎能力及耐崩花掉块能力。本发明其次提供一种硫化橡胶,是采用上述改性顺丁橡胶经硫化加工得到。具体的,目前对顺丁橡胶所进行硫化加工的工艺,均可适用于本发明所提供的改性顺丁橡胶,比如可按照《gb/t8660-2008溶液聚合型丁二烯橡胶(br)评价方法》中记载的标准试验配方(表1,非充油胶)以及方法c2进行混炼硫化。具体混炼配方为:100重量份的上述改性顺丁橡胶、2重量份的硬脂酸、3重量份的氧化锌、0.9重量份的促进剂tbbs、60重量份的通用工业参比炭黑、15重量份的astm103#操作油和1.5重量份的硫磺。经测试,相较于未改性的顺丁橡胶制备得到的硫化橡胶,本发明所提供的硫化橡胶,在撕裂强度、耐刺扎能力和耐崩花掉块能力方面都有显著提升。本发明最后提供上述改性顺丁橡胶在橡胶制品中的应用。上述橡胶制品,比如可以是汽车轮胎、胶鞋等。如上所述,本发明所提供的改性顺丁橡胶在用于汽车轮胎等橡胶制品时,能够赋予该橡胶制品较为突出的撕裂强度。以制造汽车轮胎为例,以本发明所提供的改性顺丁橡胶作为原料,替换原有的顺丁橡胶,能够改善汽车轮胎的撕裂强度,并且仍旧能够保持顺丁橡胶所带来的性能优势。而且,增大顺丁橡胶在汽车轮胎中的使用量,不仅能够提高汽车轮胎的撕裂强度,而且高抗湿滑性和低滚动阻力等其它性能也依然能够很好的保持,从而显著降低了汽车轮胎的原料成本。本发明提供了一种改性顺丁橡胶,该改性顺丁橡胶在用于硫化橡胶时,其撕裂强度、耐刺扎能力和耐崩花掉块能力都有明显改善,其中硫化橡胶的撕裂强度较改性前提高了30%~60%,耐刺扎能力提高了45%~65%,耐崩花掉块能力也有明显提升。本发明提供了上述改性顺丁橡胶的制备方法,该制备方法步骤简单可行,便于大规模的推广和应用。本发明还提供了一种硫化橡胶,是由上述改性顺丁橡胶硫化加工得到。本发明所提供的硫化橡胶,较未改性的顺丁橡胶所得到的硫化橡胶,在撕裂强度、耐刺扎能力和耐崩花掉块能力方面都有明显改善。本发明还提供了上述改性顺丁橡胶在汽车轮胎等橡胶制品中的应用。采用本发明的改性顺丁橡胶为原料制造汽车轮胎等橡胶制品时,在顺丁橡胶高使用量的条件下,不仅能够改善橡胶制品抗撕裂性能,而且其原有的抗湿滑性能和低滚动阻力等性能优势依然得到了很好的保持,因而能够显著降低橡胶制品的原料成本;而在相同使用量的前提下,能够改善橡胶制品的撕裂强度、耐刺扎能力和耐崩花掉块能力,而顺丁橡胶所赋予橡胶制品的优良性能也依然能够很好的保持。附图说明此处的附图被并入说明书中并构成本说明书的一部分,示出了符合本公开的实施例,并与说明书一起用于解释本公开的原理。图1为本发明实施例所提供的改性顺丁橡胶制备方法的流程图。通过上述附图,已示出本公开明确的实施例,后文中将有更详细的描述。这些附图和文字描述并不是为了通过任何方式限制本公开构思的范围,而是通过参考特定实施例为本领域技术人员说明本公开的概念。具体实施方式为使本发明实施例的目的、技术方案和优点更加清楚,下面将结合本发明实施例中的附图,对本发明实施例中的技术方案进行清楚、完整地描述,显然,所描述的实施例是本发明一部分实施例,而不是全部的实施例。基于本发明中的实施例,本领域普通技术人员在没有做出创造性劳动前提下所获得的所有其他实施例,都属于本发明保护的范围。本发明中,撕裂强度的测试遵照国家标准《gb/t529-2008硫化橡胶或热塑性橡胶撕裂强度的测定》。耐刺扎性能采用橡胶动态切割试验机测定,刺扎频率为100次/分钟,刺扎前后称量质量,通过硫化橡胶质量减量评价耐刺扎性能。耐崩花掉块能力通过观察橡胶动态切割试验机实验完毕后的样品的外观测定,不超过0.5cm的胶块为优,0.5cm~1.0cm的胶块为良,超过1.0cm的胶块为差。以下实施例和对比例中所用顺丁橡胶,均购自中石油独山子石化公司。实施例1本实施例提供一种改性顺丁橡胶的制备方法,具体工艺流程参见表1,包括如下步骤:将100重量份的顺丁橡胶溶解在己烷中,得到橡胶溶液,其中顺丁橡胶的数均分子量约为8.2万,分子量分布指数为1.8;向上述橡胶溶液中加入20重量份的酚醛树脂和5重量份的炭黑,搅拌均匀后,得到混合物;向上述混合物中加入乙醇,使由顺丁橡胶、酚醛树脂和炭黑组成的固体混合物析出分层,经固液分离,并对得到的固体混合物进行加热干燥,进一步去除其中的有机溶剂,得到改性顺丁橡胶。按照《gb/t8660-2008溶液聚合型丁二烯橡胶(br)评价方法》中表1记载的标准试验配方(非充油胶)以及记载的方法c2,将100重量份的改性顺丁橡胶、2重量份的硬脂酸、3重量份的氧化锌、0.9重量份的促进剂tbbs、60重量份的通用工业参比炭黑、15重量份的astm103#操作油和1.5重量份的硫磺,在混炼硫化在开放式炼胶机中混炼、硫化,得到硫化橡胶。测试硫化橡胶的抗撕裂性能、耐刺扎性能和耐崩花掉块能力,具体测试结果如表1所示。对比例1将实施例1中改性前的顺丁橡胶作为生胶,按照实施例1中的配方和方法制备硫化橡胶。即,将100重量份的顺丁橡胶、2重量份的硬脂酸、3重量份的氧化锌、0.9重量份的促进剂tbbs、60重量份的通用工业参比炭黑、15重量份的astm103#操作油和1.5重量份的硫磺,在开放式炼胶机中混炼、硫化,得到硫化橡胶。测试硫化橡胶的抗撕裂性能、耐刺扎性能和耐崩花掉块能力,具体测试结果如表1所示。对比实施例1和对比例1的测试结果可知,采用实施例1中的改性顺丁橡胶作为原料制得的硫化橡胶,其抗撕裂性能提高了38.2%、耐刺扎性能提高了63.5%,耐崩花掉块能力也有了明显改善。实施例2本实施例提供一种改性顺丁橡胶的制备方法,具体工艺流程参见表1,包括如下步骤:将100重量份的顺丁橡胶溶解在甲苯中,得到橡胶溶液,其中顺丁橡胶的数均分子量约为10.5万,分子量分布指数为2.0。向上述橡胶溶液中加入25重量份的萜烯树脂和6重量份的白炭黑,搅拌均匀,得到混合物;向上述混合物中加入甲醇,使由顺丁橡胶、萜烯树脂和白炭黑组成的固体混合物析出分层,经固液分离,并对得到的固体混合物进行加热干燥,进一步去除其中的有机溶剂,得到改性顺丁橡胶。按照实施例1中的配方和方法,将本实施中的改性顺丁橡胶在开放式炼胶机中混炼、硫化,得到硫化橡胶。测试硫化橡胶的抗撕裂性能、耐刺扎性能和耐崩花掉块能力,具体测试结果如表1所示。对比例2将实施例2中改性前的顺丁橡胶作为生胶,按照实施例1中的配方和方法制备硫化橡胶。即,将100重量份的顺丁橡胶、2重量份的硬脂酸、3重量份的氧化锌、0.9重量份的促进剂tbbs、60重量份的通用工业参比炭黑、15重量份的astm103#操作油和1.5重量份的硫磺,在开放式炼胶机中混炼、硫化,得到硫化橡胶。测试硫化橡胶的抗撕裂性能、耐刺扎性能和耐崩花掉块能力,具体测试结果如表1所示。对比实施例2和对比例2的测试结果可知,采用实施例2中的改性顺丁橡胶作为原料制得的硫化橡胶,其抗撕裂性能提高了56.5%、耐刺扎性能提高了56.0%,耐崩花掉块能力也有了明显改善。实施例3本实施例提供一种改性顺丁橡胶的制备方法,具体工艺流程参见表1,包括如下步骤:将100重量份的顺丁橡胶溶解在四氢呋喃中,得到橡胶溶液,其中顺丁橡胶的数均分子量约为11.2万,分子量分布指数为3.5。向上述橡胶溶液中加入30重量份的碳五石油树脂和8重量份的碳酸钙,搅拌均匀后,得到混合物;向上述混合物中加入乙二醇,使由顺丁橡胶、碳五石油树脂和碳酸钙组成的固体混合物析出分层,经固液分离,并对得到的固体混合物进行加热干燥,进一步去除其中的有机溶剂,得到改性顺丁橡胶。按照实施例1中的配方和方法,将本实施中的改性顺丁橡胶在开放式炼胶机中混炼、硫化,得到硫化橡胶。测试硫化橡胶的抗撕裂性能、耐刺扎性能和耐崩花掉块能力,具体测试结果如表1所示。对比例3将实施例3中改性前的顺丁橡胶作为生胶,按照实施例1中的配方和方法制备硫化橡胶。即,将100重量份的顺丁橡胶、2重量份的硬脂酸、3重量份的氧化锌、0.9重量份的促进剂tbbs、60重量份的通用工业参比炭黑、15重量份的astm103#操作油和1.5重量份的硫磺,在开放式炼胶机中混炼、硫化,得到硫化橡胶。测试硫化橡胶的抗撕裂性能、耐刺扎性能和耐崩花掉块能力,具体测试结果如表1所示。对比实施例3和对比例3的测试结果可知,采用实施例3中的改性顺丁橡胶作为原料制得的硫化橡胶,其抗撕裂性能提高了44.4%、耐刺扎性能提高了52.1%,耐崩花掉块能力也有了一定的改善。实施例4本实施例提供一种改性顺丁橡胶的制备方法,具体工艺流程参见表1,包括如下步骤:将100重量份的顺丁橡胶溶解在环己烷中,得到橡胶溶液,其中顺丁橡胶的数均分子量约为12.3万,分子量分布指数为4.6。向上述橡胶溶液中加入25重量份的丙烯酰胺和7重量份的氧化镁,搅拌均匀后,得到混合物;向上述混合物中加入丙三醇,使由顺丁橡胶、丙烯酰胺和氧化镁组成的固体混合物析出分层,经固液分离,并对得到的固体混合物进行加热干燥,进一步去除其中的有机溶剂,得到改性顺丁橡胶。按照实施例1中的配方和方法,将本实施中的改性顺丁橡胶在开放式炼胶机中混炼、硫化,得到硫化橡胶。测试硫化橡胶的抗撕裂性能、耐刺扎性能和耐崩花掉块能力,具体测试结果如表1所示。对比例4将实施例4中改性前的顺丁橡胶作为生胶,按照实施例1中的配方和方法制备硫化橡胶。即,将100重量份的顺丁橡胶、2重量份的硬脂酸、3重量份的氧化锌、0.9重量份的促进剂tbbs、60重量份的通用工业参比炭黑、15重量份的astm103#操作油和1.5重量份的硫磺,在开放式炼胶机中混炼、硫化,得到硫化橡胶。测试硫化橡胶的抗撕裂性能、耐刺扎性能和耐崩花掉块能力,具体测试结果如表1所示。对比实施例4和对比例4的测试结果可知,采用实施例4中的改性顺丁橡胶作为原料制得的硫化橡胶,其抗撕裂性能提高了48.6%、耐刺扎性能提高了46.9%,耐崩花掉块能力也有了明显改善。实施例5本实施例提供一种改性顺丁橡胶的制备方法,具体工艺流程参见表1,包括如下步骤:将100重量份的顺丁橡胶溶解在四氢呋喃中,其中顺丁橡胶的数均分子量约为10.5万,分子量分布指数为2.0。向上述橡胶溶液中加入30重量份的聚丙烯酰胺和5重量份的炭黑,搅拌均匀后,得到混合物;向上述混合物中加入乙二醇,使由顺丁橡胶、聚丙烯酰胺和炭黑组成的固体混合物析出分层,经固液分离,并对得到的固体混合物进行加热干燥,进一步去除其中的有机溶剂,得到改性顺丁橡胶。按照实施例1中的配方和方法,将本实施中的改性顺丁橡胶在开放式炼胶机中混炼、硫化,得到硫化橡胶。测试硫化橡胶的抗撕裂性能、耐刺扎性能和耐崩花掉块能力,具体测试结果如表1所示。实施例6本实施例提供一种改性顺丁橡胶的制备方法,具体工艺流程参见表1,包括如下步骤:将100重量份的顺丁橡胶溶解在四氢呋喃中,得到橡胶溶液,其中顺丁橡胶的数均分子量约为11.2万,分子量分布指数为3.5。向上述橡胶溶液中加入20重量份的碳九石油树脂和8重量份的白炭黑,搅拌均匀后,得到混合物;向上述混合物中加入乙二醇,使由顺丁橡胶、碳九石油树脂和白炭黑组成的固体混合物析出分层,经固液分离,并对得到的固体混合物进行加热干燥,进一步去除其中的有机溶剂,得到改性顺丁橡胶。按照实施例1中的配方和方法,将本实施中的改性顺丁橡胶在开放式炼胶机中混炼、硫化,得到硫化橡胶。测试硫化橡胶的抗撕裂性能、耐刺扎性能和耐崩花掉块能力,具体测试结果如表1所示。表1实施例与对比例中的硫化橡胶的性能数据表性能撕裂强度/kn·m-1耐刺扎性能/g耐崩花掉块能力实施例152.80.19优对比例138.20.52差实施例261.20.22优对比例239.10.50差实施例355.60.23良对比例338.50.48差实施例458.10.26优对比例439.10.49差实施例553.10.21优实施例654.20.25优实施例7以实施例1中的改性顺丁橡胶为原料,制备汽车轮胎,所用原料及其质量如下:20重量份的改性顺丁橡胶、82.5重量份的充油丁苯橡胶(齐鲁石化,牌号1712)、20重量份的市售工业用smr20天然橡胶、62.5重量份的炭黑n234、15重量份的白炭黑、4重量份的偶联剂、3.5重量份的芳烃油,防老体系(1重量份的防老剂4020、2重量份的防老剂rd、2重量份的防护蜡),2重量份的硬脂酸,3重量份的氧化锌,1.2重量份的促进剂tbbs、2重量份的硫磺。采用橡塑试验密炼机(容量1l),密炼机起始温度为80±5℃,转子转速为70转/分;薄通和返炼用xk-200型8英寸蒸汽加热开放式炼胶机,前辊温度:50±5℃,后辊温度:50±5℃,具体混炼工艺参见表2。表2汽车轮胎的混炼工艺下片后停放12小时以上进行硫化,硫化使用xlb-400×40平板硫化机,硫化条件为150℃×30min。对轮胎胎面胶的撕裂和力学性能进行测试,具体结果参见表3。对比例5将实施例7中的改性顺丁橡胶替换为顺丁橡胶(数均分子量约为8.2万,分子量分布指数为1.8),其它原料及用量保持不变;并按照实施例7中所提供的工艺方法,进行混炼和硫化,得到汽车轮胎胎面胶。对得到的汽车轮胎胎面胶的撕裂性能和力学性能进行测试,具体测试结果参见表3。对比实施例7与对比例5的结果可知,在相同加入量的条件下,采用改性顺丁橡胶替换普通的顺丁橡胶,所得到的汽车轮胎的撕裂强度有所提高,且湿滑摩擦系数、回弹值、硬度、拉伸强度、压缩疲劳温升等性能参数则基本维持,说明实施例7所提供的改性顺丁橡胶能够改善汽车轮胎的抗撕裂性能,高抗湿滑性和低滚动阻力等性能优势依然得到了很好的保持。实施例8以实施例1中的改性顺丁橡胶为原料,制备汽车轮胎,其中:所用原料及其质量如下:82.5重量份的改性顺丁橡胶、20重量份的充油丁苯橡胶(齐鲁石化,牌号1712)、20重量份的市售工业用smr20天然橡胶,其它所用原料及配方与实施例7相同。采用与实施例7完全一致的工艺条件,得到汽车轮胎,对轮胎胎面胶的撕裂和力学性能进行测试,具体测试结果参见表3。根据表3可知,随着改性顺丁橡胶用量的增加,汽车轮胎的撕裂强度和扯断伸长率也随之增加,同时,汽车轮胎的硬度、压缩疲劳温升、湿滑摩擦系数、回弹值等参数基本保持不变,说明所制得的汽车轮胎保持了原有顺丁橡胶所带来的优势。表3实施例与对比例中的汽车轮胎的性能测试结果实施例7对比例5实施例8邵a硬度,度656665拉伸强度,mpa22.7121.6523.15扯断伸长率,%467459489拉伸永久变形,%121311撕裂强度,kn/m726581压缩疲劳温升,℃24.128.223.0功率消耗,j/r2.051.991.98湿滑摩擦系数383737回弹值,%353334最后应说明的是:以上各实施例仅用以说明本发明的技术方案,而非对其限制;尽管参照前述各实施例对本发明进行了详细的说明,本领域的普通技术人员应当理解:其依然可以对前述各实施例所记载的技术方案进行修改,或者对其中部分或者全部技术特征进行等同替换;而这些修改或者替换,并不使相应技术方案的本质脱离本发明各实施例技术方案的范围。当前第1页12