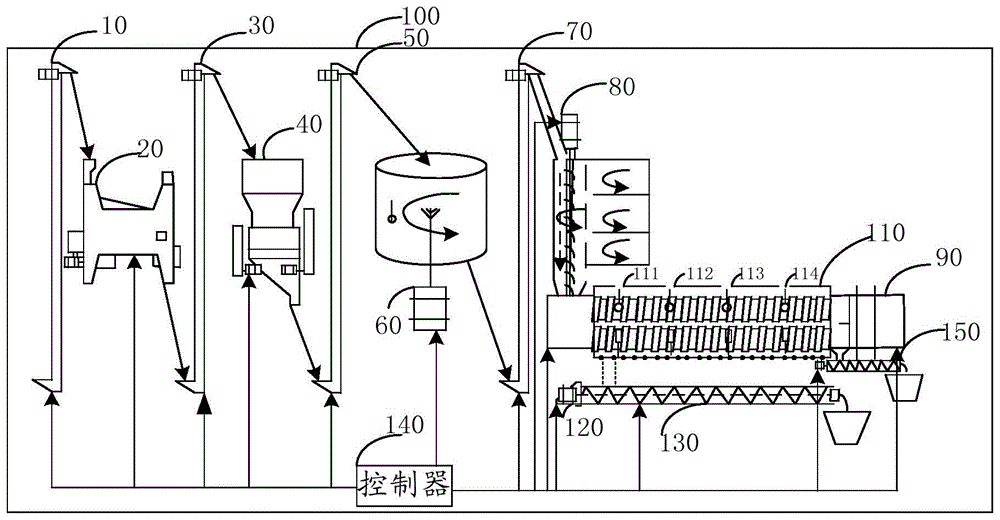
本实用新型涉及自动化
技术领域:
,尤其涉及一种多功能榨油生产线控制系统。
背景技术:
:国内榨油机控制系统,均处于手动控制阶段,首先通过人工将加工产品放入振动清理筛、扎胚机以及蒸炒锅进行初步加工,然后再将加工产品依次放入喂料电机、榨膛、搅拌电机以及榨油机中进行二次加工,通常在加工过程中生产功能单一。技术实现要素:本实用新型的主要目的在于提出一种多功能榨油生产线控制系统,旨在解决在自动化生产的基础上实现多功能的榨油生产线。为实现上述目的,本实用新型提供一种多功能榨油生产线控制系统,所述多功能榨油生产线控制系统包括依次连接的第一链式提升机、振动清理筛、第二链式提升机、扎胚机、第三链式提升机、蒸炒锅,第四链式提升机、喂料电机、榨膛、搅拌电机、榨油机以及油绞龙;所述多功能榨油生产线控制系统还包括控制器以及饼绞龙,所述控制器分别与所述第一链式提升机、振动清理筛、第二链式提升机、扎胚机、第三链式提升机、蒸炒锅,第四链式提升机、喂料电机、榨膛、搅拌电机以及榨油机连接,所述饼绞龙连接所述搅拌电机。优选地,所述榨膛包括入榨段、出油段、沥干段以及出饼段;所述入榨段的输入端连接所述喂料电机,所述入榨段的输出端连接所述出油段的输入端,所述出油段的输出端连接所述沥干段的输入端,所述沥干段的输出端连接所述出饼段的输入端,所述出饼段的输出端连接所述搅拌电机。优选地,所述多功能榨油生产线控制系统还包括温度传感器以及压力传感器;所述温度传感器分别设在所述入榨段、出油段、沥干段以及出饼段内;所述压力传感器分别设在所述入榨段、出油段、沥干段以及出饼段内。优选地,所述多功能榨油生产线控制系统还包括控制电路;所述控制电路包括控制器、上位机、监控器以及变频器,所述上位机、监控器以及变频器分别连接所述控制器。优选地,所述控制器包括主控芯片,数据输入输出电路、电能采集电路以及交换机,所述数据输入输出电路、电能采集电路以及交换机均与所述主控芯片连接。优选地,所述数据输入输出电路包括数字信号输入输出电路以及模拟信号输入电路,所述数字信号输入输出电路以及模拟信号输入电路均与所述主控芯片连接。优选地,所述数字信号输入输出电路分别与所述提升机、振动清理筛、扎胚机、蒸炒锅,喂料电机、搅拌电机、榨油机、油绞龙以及饼绞龙连接;所述数字信号输入输出电路,用于读取提升机、振动清理筛、扎胚机、蒸炒锅,喂料电机、搅拌电机、榨油机、油绞龙以及饼绞龙的工作状态;所述数字信号输入输出电路,还用于控制提升机、振动清理筛、扎胚机、蒸炒锅,喂料电机、搅拌电机、榨油机、油绞龙以及饼绞龙的启停。优选地,所述模拟信号输入电路分别与所述温度传感器以及压力传感器连接;所述模拟信号输入电路,用于采集所述温度传感器以及压力传感器读取的温度信息以及压力信息,并将所述温度信息以及压力信息通过电信号输出至所述主控芯片。优选地,所述扎胚机、蒸炒锅,喂料电机、搅拌电机以及榨油机上均设有电能表;所述电能采集电路与所述电能表连接;所述电能采集电路,用于采集扎胚机、蒸炒锅、喂料电机、搅拌电机以及榨油机所消耗的电能。优选地,所述交换机与所述变频器连接,所述变频器分别与所述喂料电机以及搅拌电机连接;所述交换机,用于接收所述主控芯片的控制电信号,并将所述控制电信号输出至所述变频器,通过所述变频器控制所述喂料电机以及榨油机电机的转速。本实用新型提出的多功能榨油生产线控制系统,所述多功能榨油生产线控制系统包括依次连接的第一链式提升机、振动清理筛、第二链式提升机、扎胚机、第三链式提升机、蒸炒锅,第四链式提升机、喂料电机、榨膛、搅拌电机、榨油机以及油绞龙;所述多功能榨油生产线控制系统还包括控制器以及饼绞龙,所述控制器分别连接第一链式提升机、振动清理筛、第二链式提升机、扎胚机、第三链式提升机、蒸炒锅,第四链式提升机、喂料电机、榨膛、搅拌电机以及榨油机,所述饼绞龙连接所述搅拌电机,从而通过控制器与各个加工设备的有效配合,在自动化生产的基础上实现多功能榨油生产线。附图说明图1为本实用新型多功能榨油生产线控制系统第一实施例的结构示意图;图2为本实用新型多功能榨油生产线控制系统第二实施例的结构示意图。附图标号说明:100表示多功能榨油生产线控制系统,10表示第一链式提升机,20振动清理筛,30表示第二链式提升机,40表示扎胚机,50表示第三链式提升机,60表示蒸炒锅,70表示第四链式提升机,80表示喂料电机,90表示搅拌电机,110表示榨膛,111表示入榨段,112表示出油段,113表示沥干段,114表示出饼段,120表示榨油机,130表示油绞龙,140表示控制器,141表示主控芯片,142表示数据输入输出电路,1421表示数字信号输入输出电路,1422表示模拟信号输入电路,143表示电能采集电路,144表示交换机,150表示饼绞龙,160表示上位机,170表示监控器,180表示变频器。本实用新型目的的实现、功能特点及优点将结合实施例,参照附图做进一步说明。具体实施方式下面将结合本实用新型实施例中的附图,对本实用新型实施例中的技术方案进行清楚、完整地描述,显然,所描述的实施例仅仅是本实用新型的一部分实施例,而不是全部的实施例。基于本实用新型中的实施例,本领域普通技术人员在没有作出创造性劳动前提下所获得的所有其他实施例,都属于本实用新型保护的范围。需要说明,若本实用新型实施例中有涉及方向性指示(诸如上、下、左、右、前、后……),则该方向性指示仅用于解释在某一特定姿态(如附图所示)下各部件之间的相对位置关系、运动情况等,如果该特定姿态发生改变时,则该方向性指示也相应地随之改变。另外,若本实用新型实施例中有涉及“第一”、“第二”等的描述,则该“第一”、“第二”等的描述仅用于描述目的,而不能理解为指示或暗示其相对重要性或者隐含指明所指示的技术特征的数量。由此,限定有“第一”、“第二”的特征可以明示或者隐含地包括至少一个该特征。另外,各个实施例之间的技术方案可以相互结合,但是必须是以本领域普通技术人员能够实现为基础,当技术方案的结合出现相互矛盾或无法实现时应当认为这种技术方案的结合不存在,也不在本实用新型要求的保护范围之内。本实用新型提出一种多功能榨油生产线控制系统100。参照图1,图1为一种多功能榨油生产线控制系统100一实施例的结构示意图。在本实用新型实施例中,所述多功能榨油生产线控制系统100包括:所述多功能榨油生产线控制系统100包括依次连接的第一链式提升机10、振动清理筛20、第二链式提升机30、扎胚机40、第三链式提升机50、蒸炒锅60,第四链式提升机70、喂料电机80、榨膛110、搅拌电机90、榨油机120以及油绞龙130。需要说明的是,所述第一链式提升机10连接振动清理筛20,在对振动清理筛20进行给料时,为了避免对振动清理筛20进行位置迁移,可通过第一链式提升机10确定给料口的位置,方便将待处理产品送入振动清理筛20进行处理,相应的,第二链式提升机30也是便于将振动清理筛20处理后的产品送入扎胚机40进行处理、第三链式提升机50则将扎胚机40处理后的产品送入蒸炒锅60进行处理,第四链式提升机70则将蒸炒锅60处理后的产品送入喂料电机80进行处理。所述多功能榨油生产线控制系统100还包括控制器140以及饼绞龙150,所述控制器140分别与所述第一链式提升机10、振动清理筛20、第二链式提升机30、扎胚机40、第三链式提升机50、蒸炒锅60,第四链式提升机70、喂料电机80、榨膛110、搅拌电机90以及榨油机120连接,所述饼绞龙150连接所述搅拌电机90。为了实现自动化生产,所述多功能榨油生产线控制系统100设有控制器140,所述控制器140分别与所述第一链式提升机10、振动清理筛20、第二链式提升机30、扎胚机40、第三链式提升机50、蒸炒锅60,第四链式提升机70、喂料电机80、榨膛110、搅拌电机90以及榨油机120连接,从而实现对多功能榨油生产线中各个设备的控制,通过所述控制器140可对喂料电机80、搅拌电机90以及榨油机120的电机转速进行调节。需要说明的是,所述榨油机120连接的榨膛110上设有漏孔,通过漏孔将加工后的产品送入榨油机120中,通过所述榨油机120完成榨油工作,并且所述搅拌电机90还连接所述饼绞龙150,通过所述饼绞龙150剩余产品进行重复利用,制作成便于储藏运输的饼残渣进行二次利用,可见,在本实施例中的多功能榨油生产线在完成自动化榨油的同时,可将残渣同时进行处理,在保证环境卫生的情况下避免产品资源的浪费。本实施例提供的技术方案,所述多功能榨油生产线控制系统100包括依次连接的第一链式提升机10、振动清理筛20、第二链式提升机30、扎胚机40、第三链式提升机50、蒸炒锅60,第四链式提升机70、喂料电机80、榨膛110、搅拌电机90、榨油机120以及油绞龙130;所述多功能榨油生产线控制系统100还包括控制器140以及饼绞龙150,所述控制器140分别连接第一链式提升机10、振动清理筛20、第二链式提升机30、扎胚机40、第三链式提升机50、蒸炒锅60,第四链式提升机70、喂料电机80、榨膛110、搅拌电机90以及榨油机120,所述饼绞龙150连接所述搅拌电机90,从而通过控制器140与各个加工设备的有效配合,实现多功能榨油生产线的自动化生产。在一实施例中,所述榨膛110包括入榨段111、出油段112、沥干段113以及出饼段114,所述入榨段111的输入端连接所述喂料电机80,所述入榨段111的输出端连接所述出油段112的输入端,所述出油段112的输出端连接所述沥干段113的输入端,所述沥干段113的输出端连接所述出饼段114的输入端,所述出饼段114的输出端连接所述搅拌电机90。为了便于对待处理的产品的加工工艺进行更细化的划分,在喂料电机80与榨油榨油机120之间设有榨膛110,将榨膛110划分为入榨段111、出油段112、沥干段113以及出饼段114,从而实现对不同加工阶段的区分。在一实施例中,所述多功能榨油生产线控制系统100还包括温度传感器以及压力传感器,所述温度传感器分别设在所述入榨段111、出油段112、沥干段113以及出饼段114内,以及所述压力传感器分别设在所述入榨段111、出油段112、沥干段113以及出饼段114内。可以理解的是,在所述入榨段111、出油段112、沥干段113以及出饼段114内一一对应设有温度传感器以及压力传感器,通过所述温度传感器以及压力传感器采集入榨段111、出油段112、沥干段113以及出饼段114内的温度信息以及压力信息,例如入榨段111温度信息、出油段112温度信息以及入榨段111压力信息、出油段112压力信息等。在本实施例中,在所述蒸炒锅60内也设有温度传感器,通过所述温度传感器采集蒸炒锅60内的实时温度信息,其中,榨膛110内部温度压力传感器采用高温熔体压力变送器ptl110,压力范围0-100mpa,温度范围0-150度,4-20ma输出,蒸炒锅60温度传感器采用pt100温度传感器。可以理解的是,所述入榨段111、出油段112、沥干段113以及出饼段114内还设有温度控制装置,所述控制器140还连接所述温度控制装置,通过所述控制器140控制所述入榨段111、出油段112、沥干段113以及出饼段114内的温度,从而达到高温压榨、适温预榨以及低温冷榨的目的,实现一机多用,一台机器同时实现高温压榨,适温预榨和低温冷榨。参照图2,图2为一种多功能榨油生产线控制系统100另一实施例的结构示意图。在本实用新型实施例中,所述多功能榨油生产线控制系统100还包括控制电路,所述控制电路包括控制器140、上位机160、监控器170以及变频器180,所述上位机160、监控器170以及变频器180分别连接所述控制器140。需要说明的是,如图2所示的,所述控制器140采用西门子simatic1200系列,可编程逻辑控制器(programmablelogiccontroller,plc),所述控制器140包括主控芯片141,数据输入输出电路142、电能采集电路143以及交换机144,所述数据输入输出电路142、电能采集电路143以及交换机144分别连接所述主控芯片141。可以理解的是,所述主控芯片141,即中央处理器(centralprocessingunit,cpu)采用1215c型号,系统采用晶体管输出,通信方式为profinet标准的通信方式,所述数字输入输出模块电路采用24v输入和晶体管输出,读取电机状态和控制电机启停,所述电能采集电路143为板载485模块采集电能,用于采集电能计量采集的电流信息,采用施耐德dm2350智能电表采集总电耗,所述交换机144采用csm1277,用于汇集profinet信号,从而实现数据的采集与输出。在本实施例中,还设有上位机160,人机界面采用西门子tp900comfort,用于显示温度压力参数,设备运行状态参数,数据管理采用北京亚控科技组态王,采用以太网连接,用于远程监控,并实现数据库统计管理功能,在所述喂料电机80以及所述榨油机120上还设有变频器180,所述变频器180采用的是西门子g120重载且带滤波功能变频器180,通过profinet方式控制电机转速和读取电机相关数据。在一实施例中,所述数据输入输出电路142包括数字信号输入输出电路1421以及模拟信号输入电路1422,数字信号输入输出电路1421以及模拟信号输入电路1422均与所述主控芯片141连接。在一实施例中,所述数字信号输入输出电路1421分别与所述提升机、振动清理筛20、扎胚机40、蒸炒锅60,喂料电机80、搅拌电机90、榨油机120、油绞龙130以及饼绞龙150连接;所述数字信号输入输出电路1421,用于读取提升机、振动清理筛20、扎胚机40、蒸炒锅60,喂料电机80、搅拌电机90、榨油机120、油绞龙130以及饼绞龙150的工作状态,所述数字信号输入输出电路1421还用于控制提升机、振动清理筛20、扎胚机40、蒸炒锅60,喂料电机80、搅拌电机90、榨油机120、油绞龙130以及饼绞龙150的启停,例如输出数字信号“1”或“0”,输出为“1”至喂料电机80时,表示控制喂料电机80开启等。在一实施例中,所述模拟信号输入电路1422分别与所述温度传感器以及压力传感器连接,所述模拟信号输入电路1422,用于采集所述温度传感器以及压力传感器读取的温度信息以及压力信息,并将所述温度信息以及压力信息通过电信号输出至所述主控芯片141。需要说明的是,所述温度信息包括蒸炒锅60温度信息、入榨段111温度信息、出油段112温度信息、沥干段113温度信息以及出饼段114温度信息,所述压力信息包括入榨段111压力信息、出油段112压力信息、沥干段113压力信息以及出饼段114压力信息,所温度传感器与压力传感器与所述主控芯片141连接,将采集的温度信息以及压力信息通过模拟信号输入电路1422传输至所述主控芯片141进行分析处理,如表1所示的模拟量采集数据表,各个数据信息通过编号进行管理,例如编码t1表示蒸炒锅60温度信息,编码p1表示入榨段111压力信息,从而实现对各个数据的有效管理。编号采集信号t1蒸炒锅温度t2入榨段温度t3出油段温度t4沥干段温度t5出饼段温度p1入榨段压力p2出油段压力p3沥干段压力p4出饼段压力表1在本实施例中,如表2所示的数据输入输出数据表,设有故障输入、工作状态输入以及设备驱动输出,其中,故障输入通过热继电器输出信号,工作状态输入通过接触器输出信号,设备驱动输出通过驱动接触器工作信号进行输出,且都是采用数字输入输出的方式进行采集,当任意一台电机过载或出现故障,过载指的是热继电器跳闸,故障指的是变频器报警,则依次停止来料方向电机,并自动记录故障时间,并给与提示,还可将生产状态自动添加生产数据到access数据库。输入输出说明数字输入输出信号采集方式故障输入热继电器输出信号数字输入输出工作状态输入接触器输出信号数字输入输出设备驱动输出驱动接触器工作信号数字输入输出表2在一实施例中,所述扎胚机40、蒸炒锅60,喂料电机80、搅拌电机90以及榨油机120上均设有电能表,所述电能采集电路143与所述电能表连接,所述电能采集电路143,用于采集扎胚机40、蒸炒锅60、喂料电机80、搅拌电机90以及榨油机120所消耗的电能。可以理解的是,为了实现对榨油生产线中各个电机设备的能耗分析,可将各个电机设备上设有电能表,通过所述电能表采集当前电机设备消耗的电能,并通过电能采集电路143输出至主控芯片141,从而达到实时监控电机设备的目的,其中,电能表采集的电能包括扎胚机40电流、蒸炒锅60电流、喂料电机80电流、榨油机120电流以及总能耗,如表3所示的电表采集数据表,通过编号、电能采集信号以及通信方式进行说明,其中,编号r1表示总电能表,通信方式为rs485的通信方式等。编号电能采集信号通信方式r1总电能表rs485r2喂料电机电能表rs485r3榨油机电能表rs485表3在一实施例中,所述交换机144与所述变频器180连接,所述变频器180分别与所述喂料电机80以及榨油机129连接,所述交换机144,用于接收所述主控芯片141的控制电信号,并将所述控制电信号输出至所述变频器180,通过所述变频器180控制所述喂料电机80以及榨油机120电机的转速,在本实施例中的通过profinet方式连接的设备均汇集于交换机,例如上位机、监控器、变频器以及控制器等。本实施例提供的技术方案,设置于控制器140连接的数据输出输出电路、电能采集电路143以及变频器180等,实现控制器140对各个电机设备的管理,从而达到自动化生成的目的。以上仅为本实用新型的优选实施例,并非因此限制本实用新型的专利范围,凡是利用本实用新型说明书及附图内容所作的等效结构或等效流程变换,或直接或间接运用在其他相关的
技术领域:
,均同理包括在本实用新型的专利保护范围内。当前第1页1 2 3