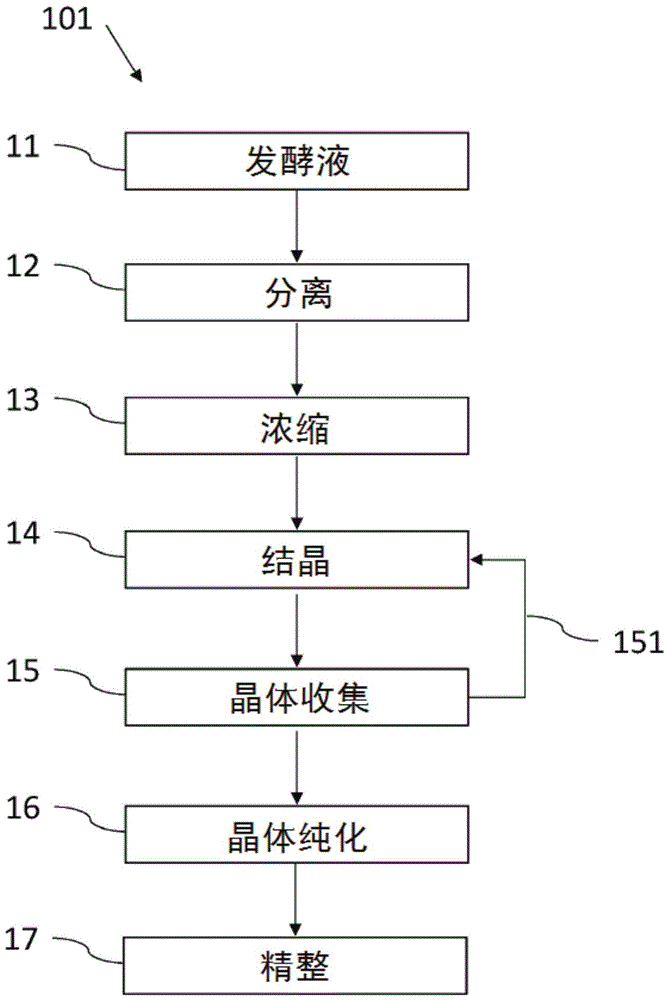
本发明涉及从发酵液中纯化乳酸镁的方法,所述发酵液具有高含量的杂质(包括可溶性和不溶性杂质)并且含有可溶形式的乳酸镁,所述方法包括分离杂质、浓缩、结晶和纯化的步骤。
背景技术:
:乳酸是最广泛存在的羟基羧酸(joglekar,h.g.,等人"comparativeassessmentofdownstreamprocessingoptionsforlacticacid."separationandpurificationtechnology52.1(2006):1-17)。它是一种用途广泛的化学品,在食品、化学、制药和化妆品行业中都有应用(huang,hetal.(2004)ahollow-fibermembraneextractionprocessforrecoveryandseparation.biochemistryandbiotechnology,113)。这种天然存在的有机酸可以通过化学合成或微生物发酵来生产。它已经天然地或作为原位微生物发酵的产物存在于许多食品(例如酸奶、酪乳和许多其他发酵食品)中(datta,r.,等人(2006)lacticacid:recentadvancesinproducts,processesandtechnologies–areview,1129(may),1119–1129)。当通过微生物发酵来生产时,在发酵过程中,发酵罐中的ph通常需要保持在5-7。由于乳酸的产生,ph降低,这对于微生物的产率而言不是理想的。加入诸如铵、钠、钾、镁或氢氧化钙的碱可以通过中和乳酸并形成乳酸盐来维持ph值。为了获得粗制乳酸,通常实施使用例如硫酸的再酸化步骤。与传统的石化产品相比,基于可再生资源的乳酸发酵多年来受到越来越多的关注。然而,为了与传统的化学生产途径竞争,需要优化基于生物的乳酸生产的成本。大约60-80%的生产成本来自下游工艺,包括从发酵液中纯化、浓缩和分离乳酸/乳酸盐。另外,期望减少或消除副产物(例如盐)的产生。先前已经提出了各种方法来从发酵液中回收和纯化乳酸和/或乳酸盐。例如,wangyong等人在“efficientmagnesiumlactateproductionwithinsituproductremovalbycrystallization(采用原位分离技术通过结晶来有效生产乳酸镁)”,bioresourcetechnology198(2015):658-663中描述了基于结晶的乳酸镁纯化方法。在不添加晶种的情况下42℃进行结晶。发酵罐中使用的发酵培养基包含酵母提取物、葡萄糖、nacl、乙酸钠、柠檬酸三铵、kh2po4、mgso4·7h2o和mnso4·7h2o。与原位产物移出(insituproductremoval,ispr)结合的发酵的产物浓度、生产率和产量分别达到143gl-1、2.41gl-1h-1和94.3%。美国专利第9,689,007号描述了通过发酵从“低糖”植物提取物中生产乳酸盐或乳酸的方法,包括提供发酵培养基,该发酵培养基包含至少25wt.%的含可发酵碳水化合物的植物提取物,并在苛性镁盐存在下,通过产乳酸微生物对发酵培养基进行发酵,以提供发酵结束时含至多9.5wt.%乳酸镁的发酵液,在发酵过程中和发酵结束时,乳酸镁为可溶形式。为了在发酵结束时发酵液中乳酸镁浓度至多为9.5wt.%,含植物提取物的发酵培养基优选含有浓度至多9.5wt.%的可发酵碳水化合物。美国公开号2014/0012041描述了一种生产乳酸盐的方法,包括:使包含相对于所述乳酸盐不小于7.0重量%的甲酸盐的乳酸盐水溶液进行结晶,并回收所述乳酸盐。所述乳酸盐水溶液中的乳酸盐浓度为10.0~30.0重量%。美国公开号2017/0218408描述了一种用于制备包括乳酸的发酵产物的方法,该方法包括:a)在水存在下用苛性镁盐处理颗粒状态且具有0.1至250mm的平均粒径的木质纤维素材料,以提供处理过的木质纤维素水性材料;b)在水解酶存在下将处理过的木质纤维素材料糖化,以提供包含可发酵碳水化合物和固体木质纤维素级分的糖化木质纤维素水性材料;c)与步骤b)同时,在形成乳酸的微生物和苛性镁盐都存在下发酵糖化的木质纤维素水性材料,以提供包含乳酸镁和固体木质纤维素级分的水性发酵液;d)从发酵液中回收乳酸镁,其中糖化和发酵同时进行。美国公开号2017/0218408的方法的原料是木质纤维素材料,其包括含纤维素、半纤维素和木质素的材料,例如可以源自植物生物质。优选的木质纤维素材料选自下列组成的组:小麦秸秆;甘蔗渣;玉米秸秆;和它们的混合物。wo公开号2017/178426描述了一种用于从碳源生产乳酸镁的发酵方法,包括步骤:-在发酵反应器中提供包含可发酵碳源的发酵培养基;-在碱性镁盐存在下通过产乳酸微生物来发酵该发酵培养基,以提供包含乳酸镁的发酵液,以及-从包含乳酸镁的发酵液中回收固体乳酸镁,其中在发酵过程的至少40%的操作时间中,发酵液中固体乳酸镁的浓度保持在5-40体积%的范围内,以总的发酵液中的固体乳酸镁晶体计算。可发酵碳源的实例是c5糖、c6糖、它们的低聚物(例如二聚c12糖)和/或它们的聚合物。wo公开号2017/207501描述了一种从固体发酵产物中分离生物质的方法,其中将包含生物质和固体发酵产物的浆料提供至生物质分离器单元的顶部,并将水性介质提供至生物质分离器单元的底部,同时从生物质分离器单元的底部抽出包含固体发酵产物的产物流,并从生物质分离器单元的顶部抽出包含生物质的废物流。所述固体发酵产物是发酵产物,其以高于其饱和浓度的浓度存在于水性介质中,并且可以是结晶产物或无定形产物。上述纯化方法被设计用于源自具有低可溶性和不溶性杂质含量的基本上均质的基于生物质的进料流的发酵液。然而,需要利用更多可用且更便宜的非均质原料进行发酵,例如来自市政、工业和商业来源的混合食物垃圾。这些非均质原料包含杂质,例如盐、脂质、蛋白质、颜色组分和惰性材料。源自所述非均质原料的发酵液也不能通过当前可用的方法有效地加工,从而以成本有效的方式获得纯的乳酸镁产品。从源自具有大量混合杂质含量的非均质原料的发酵液中纯化和分离乳酸镁的高回收率的简单、成本有效的方法,仍然存在未满足的需求。技术实现要素:本发明提供了从具有大量杂质的复杂发酵液中分离和纯化乳酸镁的方法,包括分离不溶性杂质、浓缩、结晶和纯化的步骤。有利地基于废料的复杂发酵液的使用使得该方法在经济上和环境上都是有益的。本发明部分基于出乎意料的发现,即通过少量的纯化过程步骤就可以从复杂、非均质的发酵液中获得纯度超过85%、超过92%或超过95%的乳酸镁晶体。在该方法中,将具有大量杂质并包含可溶形式乳酸镁的复杂、非均质的发酵液与不溶性杂质分离,在高温下浓缩至特别高浓度的乳酸镁,然后通过逐步受控冷却将其冷却。出乎意料的是,即使发酵液中含有大量杂质,该方法仍以成本有效方式产生了高纯度的晶体。本领域已知的纯化方法被设计用于源自基本上均质的基于生物质的进料流的发酵液,其含有相对少量的可溶性和不溶性杂质。这些已知方法不是成本有效的,或者不适用于源自具有高浓度可溶性和不溶性杂质的非均质和复杂原料的发酵液。本发明人发现了一种从非均质发酵液中获得高纯度乳酸镁晶体的简单而经济的方法。该发酵液从包含来自市政、工业和商业来源的高浓度可溶性和不溶性杂质的原料中获得。不溶性杂质可包含有机基杂质和无机基杂质。不溶性有机基杂质的非限制性实例包括:微生物、脂肪和油、脂质、聚集蛋白、骨碎片、头发、沉淀的盐、细胞碎片和残留未处理废物(例如食物壳、种子、食物不溶性颗粒和碎片等)。不溶性无机基杂质的非限制性实例包括:塑料、玻璃、食品包装中的残留物和沙子。可溶性杂质的非限制性实例包括:种子碎片、盐、颜色组分等。根据一些实施方案,本发明的方法包括在分离和浓缩的初始步骤中,将发酵液保持在约45-75℃的温度下,此时乳酸镁为可溶形式,使得在从不溶性杂质中澄清发酵液并将其浓缩至所需浓度之前,基本没有形成晶体。本发明人已经发现,在非均质原料(例如来自市政、工业和商业来源的混合食物废物)的发酵过程中以及澄清和浓缩之前,乳酸镁晶体的形成导致大量可溶性和不溶性杂质(例如颜色组分)掺入其中的低纯度乳酸镁晶体,以及不期望的多晶型晶体。所述低纯度乳酸镁晶体将需要用于其纯化的额外的处理步骤和机械,因此不是成本有效的或是不期望的。根据一些实施方案,本发明的方法包括将发酵液浓缩至乳酸盐的期望浓度为约180g/l-220g/l;在受控的冷却下使所述发酵液结晶以获得乳酸镁晶体;并收集获得的晶体。收集晶体后剩余的液体(在本文中称为“母液”)可以循环使用,并进行额外的结晶。因此,在一些实施方案中,本发明的方法还包括浓缩母液并进行至少一种另外的结晶。不希望受理论或作用机理的束缚,可以预期的是,所获得的乳酸镁晶体达到了高纯度,由于发酵液的浓度和结晶步骤的条件,例如温度,ph和冷却速度,使乳酸镁能够形成致密堆积的晶体并能够排斥可溶性杂质(例如颜色组分),从而得到具有超过约93%的高纯度的乳酸镁晶体。本发明人发现,将发酵液浓缩至不同的浓度(低于或高于本文上面所期望的浓度)和/或利用不同的不受控结晶条件,产生具有大量可溶性和不溶性杂质掺入其中的低纯度乳酸镁晶体。所获得的低纯度乳酸镁晶体将需要用于其纯化的额外处理步骤和机器,因此不是成本有效的或是不期望的。因此,本发明提供了使用包含高浓度可溶性和不溶性杂质的原料从非均质发酵液中获得乳酸镁的改进方法。所述改进的方法简单,成本有效并且导致高产量。可以在发酵产生乳酸盐之前或之后除去不溶性杂质。根据一些实施方案,在发酵之前分离大部分杂质(不溶性杂质)是更经济的。在一些实施方案中,在发酵和产生乳酸盐之后,可以通过微滤除去剩余的杂质。因此,根据第一方面,提供了一种从发酵液中分离和纯化乳酸镁的方法,包括步骤:a)提供其中不溶性杂质已经被去除的澄清发酵液,所述澄清发酵液包括作为发酵过程的结果的可溶形式乳酸镁,发酵液的温度为约45℃至约75℃;b)将步骤(a)中的澄清发酵液浓缩至乳酸盐浓度为约150g/l至约220g/l;c)对来自步骤(b)的浓缩的澄清发酵液进行至少一次冷却结晶,以获得乳酸镁晶体;和d)收集获得的乳酸镁晶体。在一些实施方案中,不溶性杂质包括不溶性有机基杂质、不溶性无机基杂质和可溶性杂质中的至少一种。在一些实施方案中,步骤(a)的发酵液的温度为约55℃至约65℃。在一些实施方案中,不溶性杂质的分离包括选自以下的至少一种技术:过滤、离心、浮选、沉降、絮凝和倾析。在一些实施方案中,不溶性杂质的分离包括离心。在一些实施方案中,不溶性杂质的分离进一步包括微滤。在一些实施方案中,不溶性杂质的分离包括离心和微滤。在一些实施方案中,步骤(b)的浓缩通过蒸发、纳滤、反渗透或其组合来进行。在一些实施方案中,在步骤(b)将发酵液浓缩至乳酸盐浓度为约160g/l至约220g/l。在一些实施方案中,在步骤(b)将发酵液浓缩至乳酸盐浓度为约170g/l至约220g/l。在一些实施方案中,在步骤(b)将发酵液浓缩至乳酸盐浓度为约180g/l至约220g/l。在一些实施方案中,在步骤(c)中,至少一次冷却结晶在选自约50至约75℃范围内的第一温度下开始。在一些实施方案中,在步骤(c)中,至少一次冷却结晶在选自约50至约70℃范围内的第一温度下开始。在一些实施方案中,在步骤(c)中,至少一次冷却结晶在选自约50至约65℃范围内的第一温度下开始。在一些实施方案中,在步骤(c)中,至少一次冷却结晶步骤在选自约10至约1℃范围内的第二温度下结束。在一些实施方案中,在步骤(c)中,至少一次冷却结晶在选自约6至约2℃范围内的第二温度下结束。在一些实施方案中,在步骤(c)中,至少一次冷却结晶的冷却速率在约10至约0.5℃/h的范围内。在一些实施方案中,在步骤(c)中,至少一种冷却结晶的冷却速率在约5至约1℃/h的范围内。在一些实施方案中,在步骤(c)中,至少一次冷却结晶之前,浓缩的澄清发酵液的ph在约6至约7的范围内。在一些实施方案中,通过选自微滤和纳滤的方法将步骤(d)获得的乳酸镁晶体与剩余液体分离。在一些实施方案中,对来自步骤(d)的剩余液体进行浓缩,然后进行至少一种另外的结晶,以获得另外的乳酸镁晶体。在一些实施方案中,将另外获得的乳酸镁晶体与所述液体分离。在一些实施方案中,将获得的乳酸镁晶体与另外的获得的乳酸镁晶体合并,从而形成合并的乳酸镁晶体。在一些实施方案中,该方法进一步包括步骤(e):洗涤和/或纯化获得的乳酸镁晶体或合并的乳酸镁晶体。在一些实施方案中,步骤(e)包括利用选自下组的有机溶剂洗涤和/或纯化获得的乳酸镁晶体或合并的乳酸镁晶体:乙醇、丙醇、异丁醇、环己烷、丙酮、乙酸乙酯及其组合。在一些实施方案中,步骤(e)包括用水溶液洗涤和/或纯化获得的乳酸镁晶体或合并的乳酸镁晶体。在一些实施方案中,步骤(e)中的溶剂或溶液的特定温度选自约0.5至约8℃。在一些实施方案中,步骤(e)进一步包括选自提取、微滤、纳滤、活性炭处理、蒸馏、干燥和研磨中的至少一个精整步骤。在一些实施方案中,步骤(e)进一步包括为运输目的进行包装。应当理解,本文所公开的各个方面和实施方案的任何组合都明确地包含在本发明的公开内容之内。通过下文给出的详细说明书,本发明的其他实施例和适用范围将变得显而易见。然而,应当理解,具体实施方式和具体实施例虽然指示了本发明的优选实施方案,但是仅以举例说明方式给出,因为根据该具体实施方式,在本发明的精神和范围内的各种改变和修改对于本领域技术人员而言将是显而易见的。附图说明这里参考附图描述了本发明的一些实施方案。说明书连同附图一起使本领域普通技术人员显而易见如何可以实施一些实施方案。附图是出于说明性描述的目的,并且没有试图比对于本发明的基本理解所必需的更详细地示出实施方案的结构细节。为了清楚起见,附图中描绘的一些对象未按比例绘制。图1:描绘了根据本发明的乳酸镁分离和纯化方法的示意图。图2a-2c:描绘了根据本发明一些实施方案的不溶性杂质的分离:具有含乳酸镁的发酵液的分液漏斗(图2a);布希纳(büchner)过滤器(4μm-9μm纸板过滤器(图2b));和从发酵液中分离出来之前的脂肪颗粒(图2c)。图3a-e:乳酸镁的结晶(b2):烧瓶侧面上的乳酸镁沉淀(图3a);乳酸镁的自发沉淀(图3b);球形乳酸镁晶体(图3c);球形晶体的重结晶(图3d);和分离精细乳酸镁晶体的布希纳(büchner)过滤(图3e)。图4:乳酸镁晶体(b3):未洗涤(左下角);用200ml冷乙醇洗涤(顶部);和在干燥前用200ml冷水洗涤(右下角)。图5a-b:用乙醇洗涤乳酸镁晶体(b3)后获得的滤液:用乙醇洗涤晶体后获得的悬浮液(图5a);和滤液过滤后的滤饼(图5b)。图6:不同乳酸镁晶体级分(b3)的纯度结果。图7:纯乳酸镁晶体和乳酸(sigma-aldrich)的溶解度曲线。图8:乳酸镁和乳酸(来自b2的球形晶体)的溶解度曲线。图9:乳酸镁和乳酸(来自b2的精细晶体)的溶解度曲线图10:三种不同乳酸镁样品的tga热分析图。具体实施方式本发明提供了一种从非均质发酵液中分离和纯化乳酸镁晶体的方法,所述发酵液包含可溶形式的乳酸镁,所述发酵液是从包含来自市政、工业和商业来源的高浓度可溶性和不溶性杂质的原料获得的。所述方法包括分离不溶性杂质、浓缩、结晶和纯化的步骤。可以在发酵产生乳酸盐之前或之后除去不溶性杂质。根据一些实施方案,分离大部分不溶性杂质是在发酵后进行的。例如,可以对复杂的有机废物进行热处理并直接泵入发酵罐中以生产乳酸。发酵后,离心,例如倾析离心机,除去大部分不溶性杂质。然后通过微滤实现澄清。根据其他实施方案,不溶性杂质的分离在发酵之前进行。例如,在一些实施方案中,可以对复杂的有机废物进行热处理,随后进行酶处理,然后离心(例如倾析离心机)除去大部分不溶性杂质。将上清液(仍具有一些杂质)泵入发酵罐中以生产乳酸。发酵后,通过陶瓷膜微滤将发酵液澄清。在迄今为止描述的乳酸发酵方法中,用于从发酵液中分离乳酸的下游处理方法包括几个步骤。第一步通常涉及除去不溶性颗粒(例如脂肪颗粒和油),并从发酵液中分离细胞及其碎片。微滤和/或离心是该步骤的常用技术。第二步通常是产物分离或初步回收,其目的是去除或分离与所需乳酸产物有很大差异的提取物成分,例如盐和蛋白质。此步骤的常用技术包括超滤、溶剂提取、盐沉淀和排斥提取。通常需要进一步纯化以除去具有相似物理和化学性质的污染物。这些污染物通常最具挑战性且去除成本最高。这需要灵敏而复杂的技术和设备。此步骤的常用技术包括结晶、蒸馏、纳滤、电渗析和各种色谱法(例如吸附或离子交换)。水或其他溶剂通常被认为是主要的“杂质”。浓缩或纯化涉及除去大部分溶剂或捕获羧酸,以实现浓缩。通常在该步骤之后,除去残留的杂质。此步骤的常用技术包括蒸发水(可选地在真空下)和/或通过反渗透(ro)过滤进行浓缩。可以应用其他精整步骤,例如用适当的溶剂洗涤,溶剂提取、干燥等。通常设计本领域已知的纯化方法用于源自固体杂质含量相对较低的基本上均质的基于生物质的进料流的发酵液,并且所述方法中的一些在发酵步骤过程中利用结晶和/或将乳酸盐保持在颗粒状态。另外,一些已知方法被设计用于在发酵过程开始时在原料流中使用特定量的碳水化合物,从而在发酵过程结束时产生特定量的乳酸镁产物。例如,美国专利第9,689,007指定,发酵培养基在该过程开始时应包含至少25重量%的含可发酵碳水化合物的植物提取物,并且在发酵结束时发酵液应含有至多9.5重量%的乳酸镁。然而,已知的方法对源自更复杂的原料的发酵液不适用或不是成本有效的,例如来自市政、工业和商业来源的非均质混合食物垃圾,其含有高含量的可溶性和不溶性杂质。另外,已知方法不适用于源自具有多种可能的初始可发酵碳水化合物浓度的复杂原料的发酵液,其导致发酵液具有多种乳酸盐浓度。出人意料的是,本发明人发现了一种简单且经济的方法,用于从非均质发酵液中获得高纯度的乳酸镁晶体,该发酵液从包含高浓度可溶性和不溶性杂质的复杂原料中获得。另外,与其他已知方法不同,本方法可以基于具有多种初始乳酸盐浓度的发酵液提供高纯度的乳酸镁晶体。因此,本方法不受初始有机原料的来源或初始有机原料中可发酵碳水化合物的量的局限或限制。因此,根据第一方面,本发明提供了一种从发酵液中分离和纯化乳酸镁的方法,包括以下步骤:a)提供其中不溶性杂质已经被去除的澄清发酵液,所述澄清发酵液包括作为发酵过程的结果的可溶形式乳酸镁,发酵液的温度为约45℃至约75℃;b)将步骤(a)的澄清发酵液浓缩至乳酸盐浓度为约150g/l至约220g/l;c)对来自步骤(b)的浓缩的澄清发酵液进行至少一次冷却结晶,以获得乳酸镁晶体;和d)收集获得的乳酸镁晶体。在一些实施方案中,从发酵液中分离和纯化乳酸镁的方法,包括步骤:(a)作为发酵过程的结果,提供包含可溶形式乳酸镁的发酵液,发酵液的温度为约45℃至约75℃;(b)从所述发酵液中分离出不溶性杂质,以获得澄清的发酵液;(c)将来自步骤(b)的澄清发酵液浓缩至乳酸盐浓度为约150g/l至约220g/l;(d)对来自步骤(c)的浓缩的澄清发酵液进行至少一次冷却结晶,以获得乳酸镁晶体;和(e)收集获得的乳酸镁晶体。如本文所用,术语“可发酵的碳水化合物”是指可以在发酵过程中被产乳酸微生物发酵的碳水化合物。如本文所用,术语“乳酸”是指化学式为ch3ch(oh)co2h的羟基羧酸。乳酸的镁盐形式称为“乳酸镁”,具有式mg(la)2。术语乳酸盐可以指乳酸盐的立体异构体:l-乳酸盐,d-乳酸盐或其组合。在一些示例性的实施方案中,乳酸盐是l-乳酸盐。在其他实施方案中,乳酸盐是d-乳酸盐。根据一些实施方案,所述发酵液是非均质发酵液。根据一些实施方案,发酵液得自包含可溶性和不溶性杂质的有机废物原料的发酵过程。有机废物原料可以源自食物垃圾的有机部分,其选自市政、家庭、农业、工业、商业和医院垃圾,或其组合。有机废物可以另外来自动物和人类排泄物、蔬菜和水果残余物、植物、熟食、蛋白质残余物、屠宰废物及其组合。每种可能性代表本发明的单独实施方案。工业有机食品废物可以包括工厂废物,例如副产品、工厂弃物、市场退货或不可食用的食物部分(例如皮肤、脂肪、硬皮和果皮)的切边。商业有机食品废物可以包括来自购物中心、饭店、超市等的废物。在一些实施方案中,不溶性杂质包括不溶性有机基杂质和不溶性无机基杂质。不溶性有机基杂质的非限制性实例包括:微生物、脂肪、油、脂质、聚集蛋白、骨碎片、头发、沉淀的盐、细胞碎片、纤维(例如水果和/或蔬菜皮)、未处理的残留食物残渣(例如食物壳、种子、食物不溶性颗粒和碎片),及其组合。微生物可以包括产生乳酸的微生物,例如但不限于酵母、细菌和真菌。每种可能性代表本发明的单独实施方案。不溶性无机基杂质的非限制性实例包括:塑料、玻璃、食品包装中的残留物、沙子以及它们的组合。每种可能性代表本发明的单独实施方案。可溶性杂质的非限制性实例包括:水、溶剂、多糖、淀粉、纤维素、半纤维素、木质素、盐、颜色组分(例如单宁、类黄酮和类胡萝卜素)及其组合。每种可能性代表本发明的单独实施方案。在一些实施方案中,发酵液的可溶性和不溶性杂质含量与用于发酵过程的原料的可溶性和不溶性杂质含量相同。在进一步实施方案中,与用于发酵过程的原料的可溶性和不溶性杂质含量相比,发酵液的可溶性和不溶性杂质含量小至少约1重量%。在更进一步的实施方案中,与用于发酵过程的原料的可溶性和不溶性杂质含量相比,发酵液的可溶性和不溶性杂质含量小至少约5重量%、约10重量%、约15重量%、约20重量%、约30重量%、约40重量%或约50重量%。本方法可以基于具有多种初始乳酸盐浓度的发酵液提供高纯度的乳酸镁晶体。在一些实施方案中,步骤(a)中的发酵液包含约50至约120g/l的初始乳酸盐浓度。在一些实施方案中,步骤(a)中的发酵液包含可溶形式乳酸镁,以及不溶性有机基杂质、不溶性无机基杂质和可溶性杂质中的至少一种,如本文上文所述。在其他实施方案中,步骤(a)中的发酵液包含可溶形式乳酸镁和以下至少一种:不溶性有机基杂质(例如脂肪、产乳酸微生物、油、脂质、蛋白质、骨碎片、头发、沉淀的盐、细胞碎片和未处理的残留食物废物)、不溶性无机基杂质(例如塑料、玻璃、食品包装中的残留物和沙子)、可溶性杂质(例如多糖、种子碎片、盐和各种颜色组分),及其组合。在一些实施方案中,来自步骤(a)的发酵液的干物质含量为约1重量%至约50重量%。如本文所用,术语“干物质”是指来自步骤(a)的发酵液中不溶性的基于有机和无机的杂质含量。在进一步的实施方案中,来自步骤(a)的发酵液的干物质含量为约5重量%至约30重量%。在一些示例性实施方案中,来自步骤(a)的发酵液的干物质含量为约10重量%至约25重量%。在一些实施方案中,来自步骤(a)的发酵液中至少约50重量%的不溶性有机和/或无机基杂质为颗粒形式。在进一步的实施方案中,来自步骤(a)的发酵液中至少约60重量%、约70重量%、约80重量%、约90重量%或约95重量%的不溶性有机和/或无机基杂质为颗粒形式。在更进一步的实施方案中,来自步骤(a)的发酵液中约100重量%的不溶性有机和/或无机基杂质为颗粒形式。在进一步的实施方案中,所述不溶性有机和/或无机基颗粒的特征在于具有在约1μm至约5mm范围内的粒径。在更进一步的实施方案中,所述不溶性有机和/或无机基颗粒的特征在于具有约1μm至约2mm范围内的粒径。在更进一步的实施方案中,所述不溶性有机和/或无机基颗粒的特征在于具有约10μm至约1mm范围内的粒径。如本文所用,术语“粒径”是指颗粒在其最长尺寸上的长度。该颗粒具有选自球形、非球形、片状、板状、海绵状及其组合的形状。在一些实施方案中,步骤(a)的发酵液为选自约45℃至约75℃的温度。在进一步的实施方案中,步骤(a)的发酵液为选自约50℃至约70℃的温度。在更进一步的实施方案中,步骤(a)的发酵液为选自约55℃至约65℃的温度。仍在更进一步的实施方案中,步骤(a)的发酵液为选自约55℃至约60℃的温度。在一些实施方案中,当发酵后进行不溶性杂质的分离时,分离过程中发酵液为选自约45℃至约75℃的温度。在进一步的实施方案中,分离过程中发酵液为选自约50℃至约70℃的温度。在更进一步的实施方案中,分离过程中发酵液为选自约55℃至约65℃的温度。仍在更进一步的实施方案中,分离过程中发酵液为选自约55℃至约60℃的温度。在一些实施方案中,浓缩步骤过程中发酵液为选自约45℃至约75℃的温度。在进一步的实施方案中,浓缩步骤过程中发酵液为选自约50℃至约70℃的温度。在更进一步的实施方案中,浓缩步骤过程中发酵液为选自约55℃至约65℃的温度。仍在更进一步实施方案中,浓缩步骤过程中发酵液为选自约55℃至约60℃的温度。在一些实施方案中,将发酵液保持在选自约45℃至约75℃的温度。在进一步的实施方案中,将发酵液保持在选自约55℃至约65℃的温度。本发明的方法包括将发酵液保持在约45-75℃的温度,其中乳酸镁为可溶形式,直到冷却结晶步骤,使得在发酵液被除去不溶性杂质而澄清并浓缩至所需浓度之前基本上没有晶体形成。在一些实施方案中,在冷却结晶步骤之前形成少于约5重量%的乳酸镁晶体。在进一步的实施方案中,在冷却结晶步骤之前形成小于约4重量%、约3重量%、约2重量%或约1重量%的乳酸镁晶体。每种可能性代表本发明的单独实施方案。在一些实施方案中,在冷却结晶步骤之前形成小于约0.5重量%的乳酸镁晶体。不希望受到任何理论的束缚,可以预期的是,所述不溶性杂质的去除和发酵液的浓缩应在约45-75℃的温度进行,该温度高于乳酸镁的溶解温度,因此保持乳酸镁为可溶形式并防止乳酸镁沉淀。本发明人惊奇地发现,在非均质原料的发酵过程中以及在澄清和浓缩之前乳酸镁晶体的形成导致大量可溶性和不溶性杂质(例如颜色组分)掺入其中的低纯度乳酸镁晶体,以及不希望的多晶型晶体。另外,本发明人发现,在结晶之前,澄清和/或浓缩过程中形成乳酸镁晶体导致乳酸镁晶体纯度低,其具有掺入其中的大量可溶性和不溶性杂质。在一些实施方案中,不溶性颗粒的分离包括使包含可溶形式乳酸镁的发酵液经历固/液分离和/或液/液分离。在进一步的实施方案中,所述固/液和/或液/液分离提供了澄清的乳酸镁发酵液和包含不溶性杂质的残余物。在一些实施方案中,固/液分离包括选自以下的至少一种技术:过滤、离心、浮选、沉降、絮凝和倾析。每种可能性代表本发明的单独实施方案。在一些实施方案中,液/液分离包括至少一种选自以下的技术:离心、过滤、混合沉降器、溶剂提取及其组合。在进一步的实施方案中,不溶性颗粒的分离包括选自以下的至少一种技术:过滤、离心、浮选、沉降、絮凝、倾析及其组合。在一些实施方案中,不溶性颗粒的分离包括离心。过滤可以选自超滤和微滤。在一些实施方案中,不溶性颗粒的分离包括微滤。可以通过以下至少一种方法进行微滤:中空纤维膜、陶瓷滤膜、压滤机或本领域已知的其他方法。每种可能性代表本发明的单独实施方案。在一些实施方案中,不溶性颗粒的分离包括离心和微滤。在一些实施方案中,通过除水、过滤或通过本领域已知的其他方法进行浓缩。可以在减压(例如蒸发)下进行水的去除。过滤可以包括纳米过滤或反渗透。在一些实施方案中,通过蒸发、纳滤,反渗透或其组合进行浓缩。在一些实施方案中,在结晶容器中通过减压实施结晶进行浓缩。在一些实施方案中,将发酵液浓缩至乳酸盐浓度为约160g/l至约220g/l。在进一步的实施方案中,将发酵液浓缩至乳酸盐浓度为约170g/l至约220g/l。在更进一步的实施方案中,将发酵液浓缩至乳酸盐浓度为约180g/l至约220g/l。在进一步的实施方案中,将发酵液浓缩至乳酸盐浓度为约150g/l至约195g/l。仍在更进一步的实施方案中,将发酵液浓缩至乳酸盐浓度为约155g/l至约190g/l。在更进一步的实施方案中,将发酵液浓缩至乳酸盐浓度为约160g/l至约185g/l。仍在更进一步的实施方案中,将发酵液浓缩至乳酸盐浓度为约175g/l至约185g/l。本发明人惊奇地发现,将非均质发酵液浓缩至不同浓度,即低于约150g/l的乳酸盐或高于约220g/l的乳酸盐,导致在结晶过程中形成低纯度的乳酸镁晶体。所述低纯度乳酸镁晶体表现出其中掺入大量杂质。这样的低纯度乳酸镁晶体将需要用于其纯化的额外处理步骤和机器,因此从上述非均质发酵液中分离和纯化乳酸镁不是成本有效的或是不期望的,如上所述。在一些实施方案中,在至少一次冷却结晶之前,浓缩的澄清发酵液的初始ph在约6至约7的范围内。根据浓缩的澄清发酵液的初始ph,可以通过添加碱或酸来调节ph。所述酸可以包含h2so4或本领域中其他已知的酸。所述碱可以选自苛性盐,例如但不限于苛性镁盐,苛性钠盐,苛性钾盐,苛性钙盐和苛性铵盐。苛性盐的非限制性实例可以选自mgo、mg(oh)2、mgco3、mg(hco3)2、ba(oh)2、naoh、na2co3、nahco3、koh、k2co3、khco3、cao、ca(oh)2、caco3、nh4oh、(nh4)2co3。每种可能性代表本发明的单独实施方案。在一些实施方案中,至少一次冷却结晶在选自约50至约75℃范围内的第一温度下开始,该第一温度高于乳酸镁的溶解温度,因此乳酸镁保持为可溶形式。在进一步的实施方案中,至少一次冷却结晶在选自约50至约70℃范围内的第一温度下开始。仍在更进一步的实施方案中,至少一次冷却结晶在选自约50至约65℃范围内的第一温度下开始。在一些实施方案中,至少一次冷却结晶步骤在选自约15至约0.5℃范围内的第二温度下结束。在进一步的实施方案中,至少一次冷却结晶步骤在选自约10至约1℃范围内的第二温度下结束。仍在更进一步的实施方案中,至少一次冷却结晶在选自约6至约2℃的范围内的第二温度下结束。在一些实施方案中,至少一种冷却结晶的冷却速率在约50至约0.1℃/h的范围内。在进一步的实施方案中,至少一次冷却结晶的冷却速率在约10至约0.5℃/h的范围内。在一些示例性实施例中,至少一次冷却结晶的冷却速率在约5至约1℃/h的范围内。在冷却结晶过程中和/或之后获得乳酸镁晶体。本发明人发现,如上所述的受控结晶的特定条件,即初始温度、最终温度、ph和冷却速率,使得能够形成高纯度的乳酸镁晶体。所述高纯度的乳酸镁晶体的特征在于具有致密堆积的构型,这使它们能够在结晶过程中排斥可溶性杂质,例如颜色组分。在不受控制的条件下进行结晶导致形成低纯度的乳酸镁晶体。冷却结晶后,收集获得的乳酸镁晶体,并与剩余的母液分离。如本文所用,术语“母液”是指乳酸镁晶体结晶后剩余的液体。在一些实施方案中,通过选自微滤、纳滤或本领域已知的另一种方法将获得的乳酸镁晶体与剩余液体分离。在一些实施方案中,为了获得额外的乳酸镁晶体,对剩余液体(母液)进行浓缩,然后进行至少一次额外的冷却结晶。在一些实施方案中,另外的浓缩条件与第一浓缩步骤的条件相同,如上所述。在进一步的实施方式中,至少一个另外的冷却结晶的条件与第一冷却结晶的条件相同。在一些实施方案中,为了获得额外的乳酸镁晶体,至少一次额外的冷却结晶是通过将剩余的液体(母液)再循环回到结晶器中进行的。在进一步的实施方案中,为了获得另外的乳酸镁晶体,至少一次另外的冷却结晶是通过将剩余的液体(母液)置于另外的单独结晶器中进行的。在一些实施方案中,剩余的液体(母液)经历至少两个另外的浓缩和冷却结晶循环。在进一步的实施方案中,剩余的液体(母液)经历至少3个、至少4个、至少5个或至少10个另外的浓缩和冷却结晶循环。每种可能性代表本发明的单独实施例方案。在一些实施方案中,通过本文以上提出的方法将另外的乳酸镁晶体与剩余的液体(母液)分离。在进一步的实施方案中,第一次冷却结晶获得的乳酸镁晶体与来自至少一次另外的冷却结晶的另外的乳酸镁晶体合并,从而形成合并的乳酸镁晶体。在更进一步的实施方案中,收集来自另外的浓缩和冷却结晶循环的另外的乳酸镁晶体,并将其与先前获得的乳酸镁晶体合并,从而形成合并的乳酸镁晶体。在一些实施方案中,本发明的方法进一步包括洗涤和/或纯化步骤,包括洗涤和/或纯化获得的乳酸镁晶体或合并的乳酸镁晶体。在进一步的实施方案中,洗涤和/或纯化步骤包括利用有机溶剂或水溶液洗涤和/或纯化获得的乳酸镁晶体或合并的乳酸镁晶体。在一些实施方案中,有机溶剂选自:乙醇、丙醇、异丁醇、环己烷、丙酮、乙酸乙酯及其组合。每种可能性代表本发明的单独的实施方案。水溶液可以包含水。在一些实施方案中,洗涤和/或纯化步骤中的有机溶剂或水溶液具有特定温度,选自约0.5至约15℃。在进一步的实施方案中,有机溶剂或水溶液具有选自约0.5至约8℃的特定温度。在一些实施方案中,洗涤和/或纯化步骤还包括至少一个精整步骤,选自提取、微滤、纳滤、活性炭处理、蒸馏、干燥和研磨。在进一步的实施方案中,洗涤和/或纯化还包括用于运输目的的包装。在一些实施方案中,在洗涤和/或纯化步骤之后,所得乳酸镁晶体的特征在于具有超过约85重量%的高纯度。在进一步的实施方案中,所得乳酸镁晶体的特征在于具有超过约90%、约92%、约94重量%、约95重量%、约96重量%、约97重量%、约98重量%,或约99重量%的高纯度。在一些实施方案中,乳酸镁晶体包含低于约15重量%的可溶性杂质。在进一步的实施方案中,乳酸镁晶体包含低于约10重量%、约9重量%、约8重量%、约7重量%、约6重量%、约5重量%、约4重量%、约3重量%、约2重量%,或低于约1重量%的可溶性杂质。现在参照图1。图1是乳酸镁回收和纯化的优选实施方案的示意图。参照图1,作为发酵过程的结果,包含可溶形式乳酸镁的发酵液11进入乳酸镁回收和纯化过程101。在一些实施方案中,将发酵液保持在至少约45℃至约75℃的温度。利用分离步骤12将包含不溶性有机和无机基杂质(例如颗粒)的不溶性杂质与发酵液11分离,从而形成澄清的发酵液。在分离步骤12中不溶性颗粒与发酵液的分离可以利用离心和/或微滤。然后通过蒸发将澄清的发酵液在浓缩步骤13浓缩至乳酸盐浓度为约160g/l至约220g/l。浓缩的发酵液进入结晶步骤14,并经历第一次结晶以获得乳酸镁晶体。为了获得具有高纯度的致密堆积晶体,结晶在选自约50至约65℃范围内的第一温度,约5至约1℃/h的冷却速率下开始,并在选自约5至约2℃范围内的第二温度结束。澄清的发酵液的初始ph(在结晶步骤的开始)在约6至约7的范围内。在结晶过程中形成致密堆积的晶体,其能够排斥可溶性杂质,因此产生高纯度,例如纯度超过94%。所述高纯度晶体包含低于约6重量%的可溶性杂质。在结晶步骤14结束时,在晶体收集步骤15中,通过过滤将获得的乳酸镁晶体与剩余的母液分离。剩余的母液经过再循环步骤151进入结晶器,以进行至少一个另外的结晶步骤14。在步骤15中,将至少一次另外的结晶中获得的乳酸镁晶体与剩余的母液分离,并与第一次结晶获得的晶体合并。合并的晶体经历纯化步骤16,其包括用选自乙醇、丙醇、异丁醇、环己烷、丙酮、乙酸乙酯、它们的组合或本领域已知的其他合适溶剂组成的组中的有机溶剂洗涤。纯化的晶体经历最后的精整步骤17,所述步骤包括至少一个另外的精整步骤,选自提取、微滤、纳滤、活性炭处理、蒸馏、干燥和研磨。所述另外的精整步骤可以包括用于包装和运输的纯化晶体的制备。术语“约”是指指定值的±10%、±5%、±1%或±0.1%。然而,在整个说明书的描述和权利要求书中,词语“包含”、“包括”、“含有”和“含”意为“包括但不限于”,并且无意于(并且不)排除其他部分、添加剂、组分、整数或步骤。如本文所用,单数形式的“一个”、“一种”和“该”包括复数形式,除非上下文另外明确指出。因此,例如,提及“多糖”包括多糖的组合。提出以下实施例以更充分地说明本发明的一些实施方案。但是,它们绝不应被解释为限制本发明的广泛范围。在不脱离本发明范围的情况下,本领域技术人员可以容易地设计出本文公开的原理的许多变型和修改。实施例实施例1:去除不溶性杂质和微滤这个步骤的目的是从发酵液中分离出不溶性杂质,以减少在进一步的下游处理步骤中结垢的可能性。以下所有实施例均使用两种含乳酸镁的发酵液(称为b2和b3),其含有不同的乳酸盐初始浓度(下文表1)。两种发酵液均源自商业食品垃圾,将来自餐厅的按源分类的食品垃圾与面包店的工厂弃物合并。所述商业食物垃圾被切碎、热处理并利用产乳酸微生物进行发酵。发酵后,每种发酵液含有乳酸镁、不溶性有机基杂质、不溶性无机基杂质和可溶性杂质。发酵液含有约20重量%的不溶性杂质。不溶性有机和无机基杂质含有平均粒径为约1μm至约2mm的颗粒。表1:不同发酵液的概述样品发酵液乳酸盐浓度(g/l)b2mg(la)278.9b3mg(la)285.5使用hplc检测器(uv-visandrid,agilent1260infinity)测定乳酸盐浓度。使用分液漏斗和安装在真空泵上的布希纳(büchner)过滤器(4-9μm纸板过滤器,颇尔公司k250)从发酵液中除去不溶性杂质。为了使乳酸镁保持为可溶形式,在除去不溶性杂质的过程中,发酵液的温度应保持在55-60℃。一旦堵塞,用新的过滤器替换过滤器。也可以使用具有0.5μm纸板膜的平板过滤器(buonvinominijet过滤器)进行微滤。发酵液最初含有可能堵塞过滤器的黄色油相(由不溶性有机基颗粒产生)。过滤前使用分液漏斗(图2a、2c)有助于将所述脂肪颗粒从发酵液中分离出去。此方法用于发酵液b2和b3。油相存在于顶层,而乳酸镁水溶液存在于底层。发酵液过滤后得到澄清、深色和稀释的乳酸盐溶液。b2和b3的初始浓度分别为78.9g/l和85.8g/l乳酸盐。过滤后,b2的乳酸盐浓度为75.7g/l,b3的乳酸盐浓度为82.9g/l。不希望受到任何理论或机制的束缚,预期在结晶之前除去不溶性颗粒(例如脂肪颗粒)是至关重要的,因为不溶性颗粒可干扰晶格并由此降低纯度和改变所得乳酸晶体的多态性。另外,重要的是在高于乳酸镁溶解温度的温度(在上述实施例中,在55-60℃之间)进行这些颗粒的去除。否则,乳酸镁可能沉淀并损害结晶过程。为了获得更高的组合产率,可以进行两步过滤过程(渗滤)。在脂肪颗粒中未检测到乳酸镁的痕迹,这表明在过滤过程中没有质量损失。实施例2:浓度这个步骤的目的是浓缩分离不溶性杂质后获得的澄清发酵液。将实施例1中获得的澄清的b2和b3分别浓缩至乳酸盐220g/l和175.9g/l。通过蒸发进行浓缩。使用旋转蒸发仪(r-100,büchi)在约60℃的温度下进行蒸发。也可以在结晶容器中进行浓缩步骤。当尝试蒸发温度为80℃时,结晶后获得的乳酸镁晶体不是优选的多晶型形式的致密堆积晶体。不希望受任何理论或机制的束缚,可以想到浓缩发酵液在结晶过程中具有更好的产量。由于乳酸镁在20℃的溶解度为100g/l(乳酸镁的sds,jostchemicals),因此在结晶后,由于乳酸镁晶体在母液中溶解,母液中会发生明显的质量损失。饱和发酵液的浓度减少了母液的体积,因此减少了乳酸镁的损失。这使得必须进行蒸发以获得合理的工艺产量。观察到将澄清发酵液浓缩至乳酸盐浓度低于150g/l或高于220g/l会导致形成低纯度乳酸镁晶体,具有不期望的球形形状并含有大量掺入其中的可溶性杂质(例如颜色组分,结果显示为棕色)。这种方法的产率低。例如,当将澄清的b3浓缩至乳酸盐140g/l时,获得的产率为46.5%,并且获得的晶体表现出不期望的球形和褐色,表明存在大量掺入晶体中的可溶性杂质。实施例3:乳酸镁(b2)的结晶过程-(对比实施例)对实施例2中获得的浓缩的澄清b2进行了几次结晶实验。实验在500和2000mlradleysreactor-readytm实验室反应器中进行,并使用huberpetitfleur温控器控制温度。如以上实施例2所述,为了减少可溶解所得晶体的母液的量,必须进行蒸发以提高结晶产率。在蒸发过程中,可以看到烧瓶侧面有乳酸镁沉淀(图3a)。在实施例2中获得的浓缩的澄清b2含有220g/l的乳酸盐。浓缩的澄清的b2的ph为约7。将该浓缩的澄清发酵液通过以下部分中描述的两种方法进行结晶。第一种方法蒸发后,使用第一种方法进行乳酸镁的结晶:1.将浓缩的微滤液在室温下冷却而不控制冷却速率。乳酸镁在冷却过程中自发地结晶为不期望的球形晶体(图3b)。2.分离从步骤1(图3c)获得的部分球形晶体,并在70℃干燥。该级分用于溶解度测定。3.从步骤1获得的部分球形晶体被分离并通过将所述晶体在60℃溶解至219.8g/l的浓度而进行重结晶(图3d)。4.在不控制冷却速率的情况下将溶液冷却至16-17℃。5.使用布希纳过滤从母液中分离出获得的mg(la)2晶体(图3e)。结果:从步骤5获得总量102g的mg(la)2,干物质含量为64.8%w/w,其对应于58.8g乳酸盐。产率为60.8%。第二种方法接下来,使用第二种方法进行乳酸镁的结晶。使用与第一结晶方法相同的步骤(与第一方法相同的步骤1-5),随后将获得的母液浓缩并结晶,从而允许更高的总产率。进行以下附加步骤:6.使用旋转蒸发浓缩母液,然后进行与上述相同的结晶步骤。在结晶过程中,将浓缩的母液冷却至2℃。7.将第一次结晶和母液结晶得到的晶体在70℃干燥并研磨成细粉。结果:获得的方法总合并产率为78.7%。母液结晶获得的晶体比第一次结晶获得的晶体含有更多可见的棕色组分,这表明晶体内掺入了更多量的杂质。实施例4:乳酸镁(b3)的结晶过程使用radleysreactor-readytm实验室反应器和huberpetitfleur温控器调节和控制实施例2中获得的浓缩澄清b3的结晶。如上所述,浓缩的澄清b3的乳酸盐浓度为175.9g/l。浓缩的澄清的b3的ph为约7。将该浓缩的澄清发酵液通过以下部分中描述的两种方法进行结晶。第一种方法:1.将浓缩的微滤液在60℃加入到反应器中,并以2℃/h的速率以受控的方式冷却至2℃。2.使用偏振光显微镜在结晶过程中(在54℃、20℃和2℃)测定形成的多晶型晶体。在54℃已经开始形成mg(la)2晶体,并获得了所需的致密堆积晶体形式。在冷却期间,晶体的尺寸增加。3.使用布希纳过滤将获得的晶体与母液分离。该阶段的晶体的干质量含量为81.3%w/w。4.然后,将获得的晶体在70℃干燥并研磨。干物质含量增加到88%w/w,而其余的12%w/w可能归因于残留水。5.另外的最终精整步骤是可选的,例如用合适的溶剂洗涤获得的晶体,以进行纯化、干燥和研磨。结果:获得的结晶产率为58.5%,与在b2的结晶中获得的产率(实施例3,第一种方法的产率为60.8%)几乎相同。因为控制了结晶和冷却过程,所以未观察到不期望的晶形(球形晶体)。第二种方法:接下来,使用第二种方法进行乳酸镁的结晶。使用与第一种结晶方法相同的步骤(与第一种方法中的步骤1-5相同),随后将获得的母液浓缩并结晶,因此允许更高的合并总收率65.4%。从母液中分离出三个级分的从初始溶液中获得的晶体,并用于寻找最合适的洗涤液或溶剂。实验中这个步骤的目的是提高晶体纯度并除去任何残留杂质。这些级分经历以下处理:·mg(la)2晶体,无清洗·用200ml冷乙醇(2℃)洗涤的mg(la)2晶体·用200ml冷水(2℃)洗涤的mg(la)2晶体结果可见不同级分之间颜色的明显差异。与未洗涤的晶体相比,用水或乙醇洗涤的晶体更白、更清洁。用水洗涤的晶体部分溶解,并且在洗涤水中测得乳酸盐损失9.9g/l。70℃干燥后,晶体再次变为固体(图4)。用冷乙醇洗涤mg(la)2晶体后,所得滤液(洗涤后残留的乙醇)含有两个悬浮液形式的级分(图5a)。使用布希纳过滤器过滤悬浮液,得到薄饼(图5b)。滤液的乳酸盐浓度为2.9g/l。该悬浮液可能是难溶于乙醇的杂质和盐的混合物。将所有三个级分干燥(70℃)、研磨,并根据重量(重量与同一样品在hplc上的测量值之差)和定量峰面积来确定其纯度。乙醇冲洗的晶体的纯度高达97%(图6)。用水冲洗对纯度没有好处(72%)。对于完全不冲洗的晶体,纯度最低(65%)。实施例5:乳酸镁的结晶溶解度这个实验的目的是确定合适的溶解度曲线,因为这将成为开发有效结晶方法的关键工具。在水中测定乳酸镁的溶解度。通过评估几个温度下的溶解度来估计温度对溶解度的影响。分析了三种不同类型的mg(la)2样品:1.来自sigma-aldrich的乳酸镁2.来自b2的乳酸镁(球形晶体,实施例3–步骤2)3.来自b2的乳酸镁(精细晶体,球状晶体重结晶后,实施例3–步骤3-5)。使用以下方法确定乳酸镁在不同温度下在水中的溶解度:1.将5ml装有水(约0.5ml)的eppendorf管冷却至10℃,并置于eppendorfthermomixer中。2.加入过量的干燥的mg(la)2并混合至少2小时。3.对每个试管重复步骤2,直到产品不再溶解为止。4.使未溶解的级分沉淀,或如果需要,将其短暂离心。5.使用容积式移液器收集20μl上清液,并用980μlro水稀释。为了避免hplc过程中的重结晶/固化,必须进行稀释。6.使用0.2μmpes过滤器过滤稀释后的样品,然后进行hplc。7.通过hplc确定乳酸盐的毫克浓度。8.将温度从10升高到60℃,并对每个温度重复步骤1-6。结果来自sigma-aldrich的乳酸镁分析了来自sigma-aldrich的纯mg(la)2晶体(图7)。在20℃时的溶解度为74.1g/l,与从文献中获得的数据相比,其溶解度要低得多。来自sigma-aldrich的样品是无水和含水mg(la)2的混合物,导致溶解度低于无水mg(la)2。水合物中的无水化合物在水中的溶解度通常高于水合物形式。通过从晶体结构中除去水分子可以获得无水化合物。来自b2的乳酸镁(球形晶体和细粉)分析了两种类型的晶体在水中的溶解度。从蒸发后的mg(la)2沉淀获得球形晶体(图8)。球形晶体重结晶后获得了精细晶体(图9)。由于不同的多态性,精细晶体的溶解度(在20℃:72.4g/lmg(la)2)低于球形晶体(在20℃:78.2g/lmg(la)2)。不希望受任何理论或机制的束缚,可以预期任何材料的最稳定的多晶型形式是化学势最低的一种。球形晶体可能含有一些杂质,因为它们是通过不受控制的沉淀形成的。这些杂质可能进入晶格并降低结构的稳定性(影响化学势)。发现球形晶体(在60℃:90.0g/lmg(la)2)随时间推移比精细mg(la)2晶体(在60℃:99.7g/lmg(la)2)的溶解度降低。实施例6:热重分析(tga)该实验的目的是获得有关热降解后mg(la)2晶体组成的更多信息,并研究结晶过程中生成的晶体为二水合物形式(即mg(la)2·2h2o)的假设。使用ta仪器的tgaq500进行热分析。分析了以下样本:来自sigmaaldrich的纯mg(la)2洗涤前来自b3的mg(la)2(实施例4)用乙醇洗涤后,来自b3的mg(la)2(实施例4)将少量的每个样品放在铝盘上。最大样品重量为1g。加热速率为10℃/min,范围为50℃至800℃。在tga分析中,将氮气用作载气。结果在三个样品的tga热分析图中,可以看到三个转变(图10):100℃至200℃之间325℃至350℃之间350℃至450℃之间100℃-200℃的第一个转变归因于未结合水的蒸发和水合物水的释放。这种转变约占样品总重量的15%,并得到理论计算的支持,该理论计算基于mg(la)2·2h2o的质量中的水质量。325℃-450℃的第二和第三个转变归因于mg(la)2产生的乳酸燃烧。由于载气为n2,因此乳酸可能会燃烧成碳而不是碳氧化物。该转变约占样品总重量的68%,与mg(la)2·2h2o中乳酸的理论量相比较少:在实验结束时,mg(la)2·2h2o总初始量的约17%剩余,这与mg(la)2·2h2o中的mgo含量相对应:基于tga结果可以得出结论,所产生的mg(la)2以及所购买的sigma-aldrich样品均为二水合物形式。实施例7:大规模分离和纯化这个实验的目的是从发酵液中大规模纯化乳酸镁。发酵液源自腐烂的食物垃圾,和以下物质所含的残留物:香蕉、橙子、苹果(带有塑料贴纸)、土豆、白菜、黄瓜、胡萝卜、西红柿、豆腐、大米、面包、牛奶、奶酪(脂肪含量为3%)和葵花籽油以及水。将所述食物垃圾切碎、热处理并利用产乳酸微生物进行发酵。发酵后,发酵液包含乳酸镁、不溶性有机基杂质、不溶性无机基杂质和可溶性杂质。发酵液的体积约为1000升,并含有初始浓度为76.3g/l的乳酸盐。将不溶性杂质从发酵液中除去,是利用倾析机分离出固体,随后通过液-液离心分离脂肪/油脂,最后通过陶瓷膜微滤。将纯化的发酵液的温度保持在55-60℃。然后通过蒸发将纯化的发酵液浓缩至乳酸盐浓度为216.8g/l,并在受控条件下进行冷却结晶,类似于实施例4所示的结晶条件:将浓缩的纯化发酵液在60℃添加至结晶反应器中并以2℃/h的速度以受控方式冷却至2℃。将所得晶体与母液分离,用冷乙醇洗涤、干燥并研磨。获得了98.6%的高纯度。前述具体实施方案的描述将如此充分地揭示本发明的一般性质,以至于其他人可以通过应用当前的知识而容易地修改和/或改变这样的具体实施方案的各种应用,而无需过度的实验并且不背离通用概念,并且因此,这样的改变和修改应当并且旨在被理解为在所公开实施方案的等同形式的含义和范围内。应当理解,本文采用的措词或术语是出于描述的目的而非限制。用于执行各种公开的功能的装置、材料和步骤可以采取多种替代形式,而不背离本发明。当前第1页12