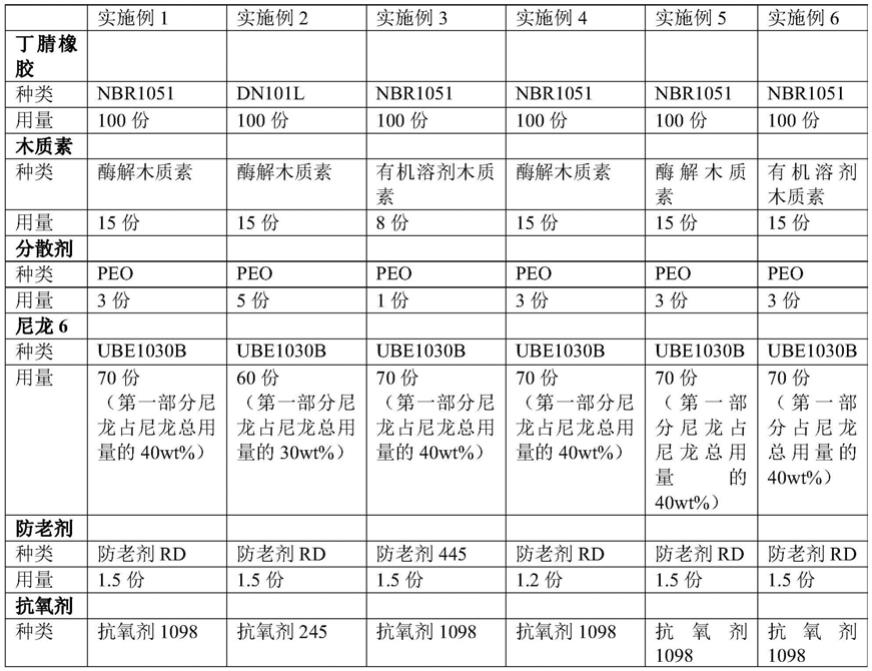
1.本发明涉及热塑性弹性体领域,具体地,涉及一种热塑性硫化橡胶组合物和热塑性硫化橡胶及其制备方法与应用。
背景技术:2.丁腈橡胶(nbr)和尼龙(pa)都具有极性基团,且二者表面能相匹配,具有较好的共混相容性,两者经动态硫化工艺制备的热塑性弹性体材料具有良好的力学性能、加工性能和耐油性能。
3.在丁腈橡胶/尼龙动态硫化体系中,具有实际应用潜力的尼龙熔点通常超过200℃,此条件下橡胶硫化速度很快,如果不设法将丁腈橡胶和尼龙混合均匀,很难制得具有“海岛”结构的热塑性弹性体。
4.因此,有必要从优化硫化体系和/或加工工艺的角度提升nbr/pa热塑性硫化橡胶的加工性能和综合性能。
5.同时,nbr/pa热塑性弹性体耐寒性、耐天候老化性能差。为了使nbr/pa热塑性弹性体能够在更苛刻的环境下使用,开发出力学性能优异且热塑性硫化橡胶,是当前要解决的重大难题。
技术实现要素:6.本发明的目的是在保证热塑性硫化橡胶优异的力学性能的前提下克服现有技术中丁腈橡胶/尼龙热塑性弹性体耐油耐寒性差的问题。
7.为了实现上述目的,本发明一方面提供一种热塑性硫化橡胶组合物,该热塑性硫化橡胶组合物中含有各自独立保存或者两者以上混合保存的以下组分:
8.丁腈橡胶、尼龙、木质素、分散剂、硫化剂、硫化助剂、防老剂、抗氧剂、稳定剂和增塑剂;
9.所述增塑剂选自尼龙酸酯中的至少一种;
10.在所述热塑性硫化橡胶组合物中,相对于100重量份的所述丁腈橡胶,所述尼龙的含量为25-90重量份,所述木质素的含量为5-20重量份,所述分散剂的含量为0.5-5重量份,所述硫化剂的含量为0.4-5重量份,所述硫化助剂的含量为0.2-5重量份,所述防老剂的含量为0.1-3重量份,所述抗氧剂的含量为0.1-2重量份,所述稳定剂的含量为0.1-2重量份,所述增塑剂的含量为2-10重量份。
11.本发明第二方面提供一种制备热塑性硫化橡胶的方法,该方法包括将上述热塑性硫化橡胶组合物中的各组分依次进行混炼和硫化。
12.本发明第三方面提供由本发明第二方面所述的方法制得的热塑性硫化橡胶。
13.本发明第四方面提供如上所述热塑性硫化橡胶在汽车输油管路、耐油密封件和耐油防尘罩中的应用。
14.本发明第五方面提供如上所述热塑性硫化橡胶组合物在制备热塑性硫化橡胶中的应用。
15.本发明的热塑性硫化橡胶组合物将特定配比的木质素引入丁腈橡胶和尼龙共混体系中,配合特定比例的分散剂、尼龙酸酯类增塑剂等组分的协同作用,在确保加工性能和力学性能优异的情况下,能够进一步改善热塑性弹性体的耐油性;同时,还能赋予热塑性弹性体优良的耐寒性能。
16.另外,本发明的配方和制备工艺的协同作用还能够使得制备得到的橡胶具有更加优异的力学性能、耐油性、耐低温性和加工性能。
具体实施方式
17.在本文中所披露的范围的端点和任何值都不限于该精确的范围或值,这些范围或值应当理解为包含接近这些范围或值的值。对于数值范围来说,各个范围的端点值之间、各个范围的端点值和单独的点值之间,以及单独的点值之间可以彼此组合而得到一个或多个新的数值范围,这些数值范围应被视为在本文中具体公开。
18.需要说明的是,在本发明的各方面中,针对各方面中的相同的组分,本发明仅在其中一方面中描述一次而不重复进行描述,本领域技术人员不应理解为对本发明的限制。
19.需要说明的是,本发明中所述的门尼粘度是在100℃使用门尼粘度仪大转子预热1min,转动4min测试获得的。
20.如前所述,本发明的第一方面提供了一种热塑性硫化橡胶组合物,该热塑性硫化橡胶组合物中含有各自独立保存或者两者以上混合保存的以下组分:
21.丁腈橡胶、尼龙、木质素、分散剂、硫化剂、硫化助剂、防老剂、抗氧剂、稳定剂和增塑剂;
22.所述增塑剂选自尼龙酸酯中的至少一种;
23.在所述热塑性硫化橡胶组合物中,相对于100重量份的所述丁腈橡胶,所述尼龙的含量为25-90重量份,所述木质素的含量为5-20重量份,所述分散剂的含量为0.5-5重量份,所述硫化剂的含量为0.4-5重量份,所述硫化助剂的含量为0.2-5重量份,所述防老剂的含量为0.1-3重量份,所述抗氧剂的含量为0.1-2重量份,所述稳定剂的含量为0.1-2重量份,所述增塑剂的含量为2-10重量份。
24.优选地,相对于100重量份的所述丁腈橡胶,所述尼龙的含量为60-70重量份,所述木质素的含量为8-15重量份,所述分散剂的含量为1-5重量份,所述硫化剂的含量为1-1.5重量份,所述硫化助剂的含量为1-1.5重量份,所述防老剂的含量为1.2-1.5重量份,所述抗氧剂的含量为0.5-0.8重量份,所述稳定剂的含量为0.5-0.8重量份,所述增塑剂的含量为5-8重量份。在该优选范围内,形成的热塑性硫化橡胶具有明显更优的力学性能和耐油性能。
25.优选地,所述丁腈橡胶中的丙烯腈结构单元的含量为35-50重量%,且所述丁腈橡胶的门尼粘度为40-85。在优选丁腈橡胶中丙烯腈结构单元含量的情况下,发明人发现,能够使得丁腈橡胶与本发明的组合物其他有效组分更好地相容,同时还有利于进一步改善热塑性弹性体的耐油性能。
26.优选地,所述尼龙为尼龙6。
27.优选地,所述木质素中的酚羟基含量≥3.0重量%,且所述木质素的数均分子量为2500-5500。
28.优选地,所述木质素选自有机溶剂木质素、硫酸盐木质素、酶解木质素、碱木质素中的至少一种。
29.本发明对有机溶剂木质素、硫酸盐木质素、酶解木质素、碱木质素的获得方式没有特别的限制,本领域技术人员能够通过商购获得。
30.特别优选地情况下,本发明中的木质素选自通过有机溶剂法从木质纤维中提取的有机溶剂木质素、由kraft法制浆废液中提取的硫酸盐木质素、发酵制乙醇提取出的酶解木质素和造纸碱法制浆得到的碱木质素中的至少一种。本发明的发明人发现,采用上述木质素绿色环保,还能够降低弹性体共混物中抗氧剂、防老剂等配合剂的用量,有效降低材料成本。
31.优选地,所述有机溶剂木质素、所述酶解木质素、所述碱木质素中的木质素含量各自独立地≥80重量%。
32.优选地,所述分散剂为聚环氧乙烷。更优选地,所述聚环氧乙烷的数均分子量为2
×
10
5-5
×
106。本发明人发现,在该优选范围内,能够使得聚环氧乙烷更好地渗入木质素团聚体,确保木质素在丁腈橡胶中分散更加均匀。
33.优选地,所述硫化剂与所述硫化助剂的含量重量比为1:(0.5-2)。本发明的发明人发现,在该优选范围内,可使丁腈橡胶的硫化时间获得较大提高,从而确保丁腈橡胶和尼龙之间剪切分散的更加充分。
34.优选地,所述硫化助剂为三烯丙基异三聚氰酸酯。
35.优选地,所述硫化剂为有机过氧化物。更优选地,所述硫化剂选自1,3-双(叔丁基过氧异丙基)苯、2,5-二甲基-2,5-二(叔丁基过氧基)己烷、2,5-二甲基-2,5-双(过氧化苯甲酰)己烷、2,5-二甲基-2,5-二(叔丁基过氧基)-3-己炔中的至少一种。
36.优选地,所述防老剂为胺类防老剂和/或喹啉类防老剂。更优选地,所述防老剂选自防老剂445、防老剂rd、防老剂mb中的至少一种。
37.优选地,所述抗氧剂为受阻酚类抗氧剂中的至少一种。更优选地,所述抗氧剂选自抗氧剂1098、抗氧剂245、抗氧剂1010、抗氧剂1076、抗氧剂1024中的至少一种。
38.优选地,所述稳定剂选自稳定剂168、稳定剂618中的至少一种。
39.优选地,所述增塑剂选自尼龙酸二异丁酯、尼龙酸二正丁酯、尼龙酸二辛酯中的至少一种。本发明的发明人发现,在该优选情况下,在保证产品的耐油特性的同时,还能够赋予产品优异的耐低温性能。
40.如前所述,本发明的第二方面提供了一种制备热塑性硫化橡胶的方法,该方法包括将上述第一方面的热塑性硫化橡胶组合物中的各组分依次进行混炼和硫化。
41.根据本发明的一种优选实施方式,所述将各组分依次进行混炼和硫化的操作包括以下步骤:
42.(1)将丁腈橡胶、木质素、分散剂、防老剂和增塑剂进行第一混炼,得到母炼胶;
43.(2)将抗氧剂、稳定剂、第一部分尼龙进行第一塑炼,得到第一塑炼物;
44.(3)将所述母炼胶与所述第一塑炼物进行第二混炼,得到混合料;
45.(4)将所述混合料进行挤出造粒i,得到混合料颗粒;
46.(5)将所述混合料颗粒与硫化剂、硫化助剂、第二部分尼龙进行动态硫化和挤出造粒ii。
47.本发明的发明人发现,将部分尼龙和丁腈橡胶预先混合均匀,进一步加入剩余部分尼龙,同时配合本发明的方法中其他工艺及工艺参数,能够使得全部橡胶和塑料在短时间内形成更为均匀的相态,有利于后续动态硫化中实现塑料相均匀包覆橡胶粒子,从而获得综合性能优异的热塑性弹性体。
48.本发明第二方面涉及的各个组分的用量与本发明第一方面所述的相应组分的含量相同,在此不再赘述,本领域技术人员不应理解为对本发明的限制。
49.优选地,所述第一部分尼龙占制备所述热塑性硫化橡胶所需尼龙总用量的10-100wt%,优选为20-60wt%。
50.优选地,所述第一混炼的条件包括:温度为100-150℃,时间为2-20min。
51.优选地,所述第一混炼在第一密炼机中进行,且所述第一密炼机转速为40-90rpm。
52.优选地,所述第一塑炼的条件包括:温度为190-230℃,时间为2-8min。
53.优选地,所述第二混炼的条件包括:时间为3-10min。
54.更优选地,所述第二混炼在第二密炼机中进行,且所述第二密炼机转速为60-90rpm。
55.优选地,所述挤出造粒i、所述挤出造粒ii和所述动态硫化各自独立地在单螺杆挤出机或双螺杆挤出机中进行。
56.根据一种优选的具体实施方式,所述挤出造粒i和所述挤出造粒ii均在单螺杆挤出机中进行。
57.优选地,所述挤出造粒i和所述挤出造粒ii的条件各自独立地包括:螺杆转速为50-220rpm,挤出温度为190-230℃。
58.根据另一种优选的具体实施方式,所述动态硫化在同向啮合双螺杆挤出机中进行。
59.优选地,所述动态硫化的条件包括:螺杆转速为180-350rpm,螺杆温度为190-230℃。
60.如前所述,本发明的第三方面提供了由本发明第二方面所述的方法制得的热塑性硫化橡胶。
61.如前所述,本发明的第四方面提供了如上所述热塑性硫化橡胶在汽车输油管路、耐油密封件和耐油防尘罩中的应用。
62.如前所述,本发明的第五方面提供了如上所述热塑性硫化橡胶组合物在制备热塑性硫化橡胶中的应用。
63.以下将通过实例对本发明进行详细描述。以下实例中,在没有特别说明的情况下,使用的各种原料均为市售品。
64.丁腈橡胶nbr1051:镇江南帝化工有限公司生产,丙烯腈结构单元的含量为41重量%,门尼粘度68。
65.丁腈橡胶dn101l:日本瑞翁株式会社生产,丙烯腈结构单元的含量为43重量%,门尼粘度60。
66.尼龙6:日本宇部兴产株式会社生产的ube1030b,熔融温度215℃。
67.有机溶剂木质素:广州市楹晟生物科技有限公司生产,棕褐色粉末,木质素含量≥85重量%,数均分子量3719,酚羟基含量≥3.0重量%。
68.酶解木质素:锦州市凌宇化工有限公司生产,棕色或褐色粉末,木质素含量≥80重量%,数均分子量3950,酚羟基含量≥3.0重量%。
69.聚环氧乙烷(peo):万百灵威科技有限公司生产,数均分子量6
×
105,分析纯。
70.防老剂rd:江苏圣奥化学科技有限公司生产的2,2,4-三甲基-1,2-二氢喹啉的聚合物。
71.防老剂445:美国科聚亚生产的4.4-双(α,α-二甲基苄基)二苯胺。
72.抗氧剂1098:德国巴斯夫生产的n,n
’-
1,6-亚己基-二-[3,5-二叔丁基-4-羟基苯丙酰胺]。
[0073]
抗氧剂245:德国巴斯夫生产的二缩三乙二醇双[β-(3-叔丁基-4-羟基-5-甲基苯基)丙酸酯]。
[0074]
稳定剂168:德国巴斯夫生产的三[2.4-二叔丁基苯基]亚磷酸酯。
[0075]
增塑剂:东营市鲁化化工有限公司生产的尼龙酸二异丁酯。
[0076]
增塑剂:潍坊德墨特化工有限公司生产的尼龙酸二辛酯。
[0077]
硫化剂:阿克玛化学公司生产的f flakes,片状,1,3-双(叔丁基过氧异丙基)苯(无味dcp),或101xl45,粉末状,2,5-二甲基-2,5-二(叔丁基过氧基)己烷(双25)。
[0078]
硫化助剂:百灵威科技有限公司生产的三烯丙基异三聚氰酸酯(taic),纯度99重量%。
[0079]
以下实例中的组分用量均为重量份(或每份),且每重量份表示10g。
[0080]
实施例1
[0081]
本实施例用于说明本发明所述的热塑性硫化橡胶组合物按照表1中的配方和工艺参数,并按如下所述的方法制备热塑性硫化橡胶。
[0082]
所述制备热塑性硫化橡胶的方法包括以下步骤:
[0083]
(1)在密炼机转子转速为60rpm,温度为140℃条件下,将丁腈橡胶、木质素、分散剂、防老剂和增塑剂在第一密炼机中进行第一混炼,充分混合6min,得到母炼胶;
[0084]
(2)在220℃下,将抗氧剂、稳定剂和第一部分尼龙(尼龙总用量的40wt%)进行第一塑炼,共混5min,得到第一塑炼物;
[0085]
(3)在密炼机转子转速为80rpm条件下,将步骤(1)中得到的母炼胶与所述第一塑炼物在第二密炼机中进行第二混炼,共混4min,得到混合料;
[0086]
(4)在螺杆转速为180rpm,挤出温度为210℃条件下,将混合料通过单螺杆挤出机进行挤出造粒i,得到混合料颗粒;
[0087]
(5)在螺杆转速为200rpm,螺杆温度为220℃条件下,将混合料颗粒与硫化剂、硫化助剂、第二部分尼龙在同向啮合双螺杆挤出机进行动态硫化,然后在螺杆转速为200rpm,挤出温度为220℃条件下,在单螺杆挤出机进行挤出造粒ii,制得热塑性硫化橡胶s1。
[0088]
在没有特别说明的情况下,其余实施例采用与实施例1相同的流程进行,不同的是所采用的橡胶组合物配方和工艺参数不同,具体参见表1中。
[0089]
实施例8
[0090]
本实施例采用与实施例1相似的配方和方法制备热塑性硫化橡胶,所不同的是:尼龙6全部加入与丁腈橡胶混合,具体参见表1。
[0091]
实施例9
[0092]
本实施例采用与实施例1相似的配方和方法制备热塑性硫化橡胶,所不同的是:动态硫化工艺参数不同,具体参见表1。
[0093]
实施例10
[0094]
本实施例采用与实施例1相似的配方和方法制备热塑性硫化橡胶,所不同的是:第一混炼温度为40℃,具体参见表1。
[0095]
对比例1
[0096]
本对比例采用与实施例1相似的配方和方法制备热塑性硫化橡胶cs1,所不同的是:配方中不添加增塑剂,具体参见表1。
[0097]
对比例2
[0098]
本对比例采用与实施例1相似的配方和方法制备热塑性硫化橡胶cs2,所不同的是:配方中增塑剂采用邻苯二甲酸二异丁酯替代尼龙酸二异丁酯,具体参见表1。
[0099]
对比例3
[0100]
本对比例采用与实施例1相似的配方和方法制备热塑性硫化橡胶cs3,所不同的是:配方中不添加木质素和分散剂,具体参见表1。
[0101]
表1
[0102]
[0103][0104]
表1(续表)
[0105]
[0106][0107]
测试例
[0108]
将实施例和对比例制得的产品进行拉伸性能、耐压变和耐油性测试,并记录动态硫化橡胶挤出外观,结果见表2。
[0109]
其中,拉伸强度、断裂伸长率按照gb/t 528-2009标准中的方法进行测试。
[0110]
压缩永久变形按照gb/t 7759.1-2015标准进行测试,测试条件:100℃
×
24h,预压缩率为25%,的圆柱形试样。
[0111]
耐油性能按照gb/t 1690-2010进行测试,测试条件:在甲苯与异辛烷体积比30/70的混合溶剂中,40℃
×
24h测试体积溶胀百分率。
[0112]
压缩耐寒系数参照hg/t3866-2008进行测试,测试条件:测试试样原高h0及压缩高h1(压缩20%),放入低温(-30℃)中冷冻5min,去除载荷后低温下(-30℃)恢复3min,读取恢复高h2,的圆柱形试样,压缩耐寒系数k=(h
2-h1)/(h
0-h1)。
[0113]
表2
[0114][0115]
从表2结果能够看出,本发明采用部分尼龙和橡胶预混合技术,结合木质素、稳定剂、增塑剂和硫化剂等各项配合剂比例的调控,可以获得力学性能、耐油性、耐低温性和加工性能均优异的热塑性硫化橡胶。
[0116]
分别比较实施例1、实施例8-10可以看出,采用尼龙分步加入和优化的动态硫化工艺,能够进一步改善热塑性硫化橡胶的耐油性、耐低温性、抗压变、力学性能和表面外观。
[0117]
比较实施例1和对比例1-2可以看出,加入尼龙酸酯类增塑剂,能够在保证产品的耐油特性前提下,显著改善热塑性橡胶的耐低温性能。
[0118]
比较实施例1和对比例3可以看出,加入木质素和分散剂,有利于进一步提高热塑性硫化橡胶的力学性能、压变和耐油性。
[0119]
以上详细描述了本发明的优选实施方式,但是,本发明并不限于此。在本发明的技术构思范围内,可以对本发明的技术方案进行多种简单变型,包括各个技术特征以任何其它的合适方式进行组合,这些简单变型和组合同样应当视为本发明所公开的内容,均属于本发明的保护范围。