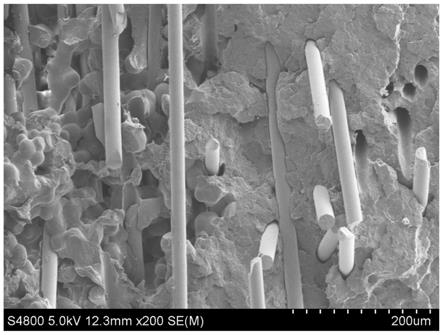
1.本发明涉及生物材料领域,具体涉及一种玻璃纤维增强生物降解高分子复合材料的制备方法。
背景技术:2.生物降解高分子材料在用作骨钉、骨板等骨修复医疗器械的时候通常面临两个问题:一是降解产物的酸性导致长期的炎症反应,骨细胞很难长入,在可吸收骨钉、骨板降解后会形成空洞;二是材料的强度和韧性不够,在手术使用的时候容易拧断。目前解决问题一的方案是通过羟基磷灰石或磷酸钙与生物降解高分子复合,利用其碱性中和降解产物的酸性,以避免空洞的产生。然而羟基磷灰石或磷酸钙均以粉末的形式直接填充到生物降解高分子材料中,由于两种材料之间的相容性差,使得复合后生物降解高分子材料的强度急剧降低。
3.现有技术增强高分子材料强度的方法是通过羟基磷灰石表面的羟基引发聚乳酸的聚合先形成复合物,再将其作为填料与聚乳酸混合。然而这类复合材料中羟基磷灰石的重量百分比通常小于15%,超过此数值强度也会急剧下降,无法满足使用要求。问题二的现有解决方案为通过将生物降解高分子材料晶粒细化的自增强工艺,可以大大增强其韧性,然而其强度还是偏低,不能用于承重部位的骨修复。并且此方法无法解决因降解产物的酸性导致的空洞问题。
4.因此亟需一种能增强生物降解性能的高分子复合材料,解决上述问题。
技术实现要素:5.本发明为了解决上述问题,提供了一种玻璃纤维增强生物降解高分子复合材料的制备方法,用玻璃纤维增强生物降解高分子材料解决其强度韧性和降解产物酸性的问题。
6.本发明目的之一在于提供一种增强生物降解能力的高分子复合材料的制备方法,具体技术方案如下:
7.一种增强生物降解能力的高分子复合材料的制备方法,包括如下步骤:
8.(1)玻璃纤维和可生物降解材料单体混合,催化反应,所述可生物降解材料单体为乙交酯(ga)、丙交酯(la)、对二氧环己酮(pdo)、ε
‑
已内酯(cl)中的至少一种;
9.(2)步骤(1)所得产物经有机溶剂溶解,纯化和干燥得到改性玻璃纤维;
10.(3)将改性玻璃纤维与可生物降解高分子材料混合,经有机溶剂溶解,浇筑得到高分子复合材料,所述可生物降解高分子材料为聚乙交酯、聚丙交酯、聚对二氧环己酮、聚已内酯及其共聚物中的至少一种。
11.进一步地,所述玻璃纤维和可生物降解材料单体的质量比为1:2~20。
12.进一步地,步骤(1)催化反应中的催化剂为50
‑
500ppm辛酸亚锡。
13.进一步地,步骤(1)催化反应的温度为90~170℃。
14.优选的,所述催化反应需在真空或惰性气体的保护下反应5~72小时。
15.进一步地,步骤(2)中的有机溶剂为氯仿,纯化步骤在乙醇中进行。
16.进一步地,步骤(3)中所述改性玻璃纤维与可生物降解高分子材料的质量比为1:1~10。
17.进一步地,步骤(3)中所述有机溶剂为氯仿或六氟异丙醇。
18.进一步地,步骤(3)中浇筑后还需待溶剂挥发。
19.制备过程中纯化能降低可生物降解材料单体残留率,提高材料强度,延长其降解时间。另外,通过纯化得到的生物降解高分子材料改性的玻璃纤维,能增加其与后续生物降解高分子材料复合的界面相容性,通过拉伸强度测试证明,未经过表面改性的将玻璃纤维和生物降解高分子直接复合测得的拉伸强度只有12~16mpa,经生物降解高分子单体引发表面聚合改性后的复合材料的拉伸强度可达到23~34mpa。
20.本发明目的之二在于提供一种由上述技术方案中所述制备方法制备得到的增强生物降解能力的高分子复合材料。
21.由上述制备方法制得的高分子材料中玻璃纤维的重量百分比为5
‑
70%,其强韧性较好,并能克服降解产物酸性的问题,具有很好的生物相容性。
22.本发明的有益之处在于:本发明以玻璃纤维表面羟基引发开环聚合并,先将玻璃纤维与可生物降解材料单体混合、聚合、纯化,得到生物降解高分子材料改性的玻璃纤维,增加其与后续生物降解高分子材料复合的界面相容性,其纯化步骤能降低可生物降解材料单体残留率,提高材料强度,延长其降解时间,使得本发明的复合材料强韧度较高,并能中和降解产物的酸性。
附图说明
23.图1为本发明的玻璃纤维增强生物降解高分子复合材料的断面sem图
具体实施方式
24.下面通过实施例和附图,对本发明进行进一步详细说明,应当理解,此处所描述的具体实施例仅用以解释本发明,并不用于限定本发明,本领域技术人员应该理解的是,在不偏离本发明的结构思路、使用范围下可以对本发明技术方案的细节和形式进行修改或替换,但这些修改和替换均落入本发明的保护范围内。
25.具体实施例
26.一种玻璃纤维增强生物降解高分子复合材料的制备方法:
27.(1)将玻璃纤维与乙交酯(ga)、丙交酯(la)、对二氧环己酮(pdo)、ε
‑
已内酯(cl)中的至少一种混合,玻璃纤维与上述可生物降解材料单体的质量比为1:2~20,加入50
‑
500ppm辛酸亚锡为催化剂,在90
‑
170℃真空或惰性气体,例如氮气或氩气等惰性气体的保护下反应5
‑
72小时。用氯仿溶解产物后,分离出玻璃纤维,在乙醇中沉淀纯化,纯化能降低可生物降解材料单体残留率,提高材料强度,延长其降解时间。真空干燥后,得到经生物降解高分子材料表面改性的玻璃纤维。
28.(2)将上述改性玻璃纤维与聚乙交酯、聚丙交酯、聚对二氧环己酮、聚已内酯及其共聚物中的至少一种混合,改性玻璃纤维与上述可生物降解高分子材料的质量比为1:1~10。然后通过有机溶剂例如氯仿或六氟异丙醇溶解,玻璃纤维的重量百分比为5
‑
70%。将得
到的溶液浇筑成膜,待溶剂挥发后,即可得到玻璃纤维增强生物降解高分子复合材料。
29.本方法主要以玻璃纤维表面羟基引发开环聚合并通过纯化,得到生物降解高分子材料改性的玻璃纤维,增加其与后续生物降解高分子材料复合的界面相容性。
30.实施例1
31.(1)将玻璃纤维与丙交酯(la)单体(玻璃纤维与单体的质量比为1:2混合,加入50ppm辛酸亚锡为催化剂,在130℃真空条件下反应72小时。用氯仿溶解产物后,分离出玻璃纤维,在乙醇中沉淀纯化,真空干燥后,得到聚丙交酯表面改性的玻璃纤维。
32.(2)将上述改性玻璃纤维与聚丙交酯按质量比为1:5混合,溶于氯仿。将得到的溶液浇筑成膜,待溶剂挥发后,即可得到玻璃纤维增强聚丙交酯高分子复合材料,如图1所示,玻璃纤维已和聚丙交酯充分结合。图中玻璃纤维在聚丙交酯的基材中分散均匀,呈层状排列,玻璃纤维与聚丙交酯的界面相容性良好。
33.实施例2
34.(1)将玻璃纤维与ε
‑
已内酯(cl)单体(玻璃纤维与单体的质量比为1:10混合,加入500ppm辛酸亚锡为催化剂,在170℃惰性气体保护条件下反应5小时。用氯仿溶解产物后,分离出玻璃纤维,在乙醇中沉淀纯化,真空干燥后,得到聚己内酯表面改性的玻璃纤维。
35.(2)将上述改性玻璃纤维与聚己内酯按质量比为1:10混合,溶于氯仿。将得到的溶液浇筑成膜,待溶剂挥发后,即可得到玻璃纤维增强聚己内酯高分子复合材料。
36.实施例3
37.(1)将玻璃纤维与对二氧环己酮单体,玻璃纤维与单体的质量比为1:20混合,加入200ppm辛酸亚锡为催化剂,在90℃惰性气体保护条件下反应60小时。用六氟异丙醇溶解产物后,分离出玻璃纤维,在乙醇中沉淀纯化,真空干燥后,得到聚对二氧环己酮表面改性的玻璃纤维。
38.(2)将上述改性玻璃纤维与聚对二氧环己酮按质量比为1:5混合,溶于六氟异丙醇。将得到的溶液浇筑成膜,待溶剂挥发后,即可得到玻璃纤维增强聚对二氧环己酮高分子复合材料。
39.实施例4
40.(1)将玻璃纤维与乙交酯和丙交酯混合单体(摩尔比为1:1),玻璃纤维与单体的质量比为1:10混合,加入100ppm辛酸亚锡为催化剂,在160℃惰性气体保护条件下反应12小时。用氯仿溶解产物后,分离出玻璃纤维,在乙醇中沉淀纯化,真空干燥后,得到聚(乙交酯
‑
r
‑
丙交酯)表面改性的玻璃纤维。
41.(2)将上述改性玻璃纤维与聚己内酯按质量比为1:10混合,溶于氯仿。将得到的溶液浇筑成膜,待溶剂挥发后,即可得到玻璃纤维增强聚已内酯高分子复合材料。
42.实施例5
43.(1)将玻璃纤维与乙交酯单体(玻璃纤维与单体的质量比为1:10混合,加入500ppm辛酸亚锡为催化剂,在130℃惰性气体保护条件下反应7小时。用六氟异丙醇溶解产物后,分离出玻璃纤维,在乙醇中沉淀纯化,真空干燥后,得到聚乙交酯表面改性的玻璃纤维。
44.(2)将上述改性玻璃纤维与聚丙交酯按质量比为1:1混合,溶于氯仿。将得到的溶液浇筑成膜,待溶剂挥发后,即可得到玻璃纤维增强聚丙交酯高分子复合材料。
45.对比实施例1
46.直接将玻璃纤维与聚丙交酯按质量比为1:5混合,溶于氯仿。将得到的溶液浇筑成膜,待溶剂挥发后,即可得到玻璃纤维增强聚丙交酯高分子复合材料。
47.对比实施例2
48.聚丙交酯溶于氯仿。将得到的溶液浇筑成膜,待溶剂挥发后,即可得到聚丙交酯高分子材料。
49.对比实施例3
50.直接将玻璃纤维与聚己内酯按质量比为1:10混合,溶于氯仿。将得到的溶液浇筑成膜,待溶剂挥发后,即可得到玻璃纤维增强聚己内酯高分子复合材料。
51.对比实施例4
52.聚已内酯溶于氯仿。将得到的溶液浇筑成膜,待溶剂挥发后,即可得到聚己内酯高分子材料。
53.对比实施例5
54.直接将玻璃纤维与聚对二氧环己酮按质量比为1:5混合,溶于六氟异丙醇。将得到的溶液浇筑成膜,待溶剂挥发后,即可得到玻璃纤维增强聚二氧环己酮高分子复合材料。
55.对比实施例6
56.聚二氧环己酮溶于六氟异丙醇。将得到的溶液浇筑成膜,待溶剂挥发后,即可得到聚二氧环己酮高分子材料。
57.对比实施例7
58.直接将玻璃纤维与聚己内酯按质量比为1:10混合,溶于氯仿。将得到的溶液浇筑成膜,待溶剂挥发后,即可得到玻璃纤维增强聚己内酯高分子复合材料。
59.对比实施例8
60.聚已内酯溶于氯仿。将得到的溶液浇筑成膜,待溶剂挥发后,即可得到聚己内酯高分子材料。
61.对比实施例9
62.直接将玻璃纤维与聚丙交酯按质量比为1:10混合,溶于氯仿。将得到的溶液浇筑成膜,待溶剂挥发后,即可得到玻璃纤维增强聚丙交酯高分子复合材料。
63.对比实施例10
64.聚丙交酯溶于氯仿。将得到的溶液浇筑成膜,待溶剂挥发后,即可得到聚丙交酯高分子材料。
65.具体实施例和对比实施例的性能分析:
[0066][0067]
根据1
‑
5组实验数据可知,按照本发明实施例制备方法制备的高分子复合材料的拉伸强度都高于组内的另外两组对比实施例制得的复合材料,说明本发明制备方法制得的高分子复合材料的拉伸强度得到了大幅度的提升。另外实施例1
‑
5制得的高分子复合材料降解30天后的ph值皆接近于中性,大部分呈现弱碱性,并且基本上相对于组内对比实施例制得的复合材料的ph值略高,克服了降解产物酸性的问题,具有很好的生物相容性。
[0068]
以上所述仅为本发明的较佳实施例,并不用以限制本发明,凡在本发明的精神和原则之内,所作的任何修改、等同替换、改进等均应包含在本发明的保护范围之内。