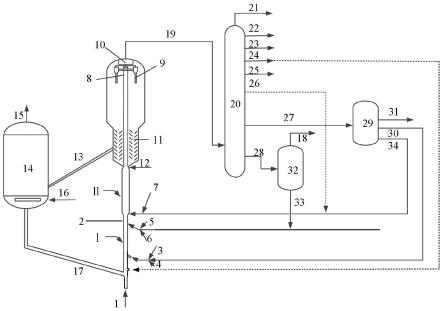
1.本技术涉及石油炼制及石油化工加工过程,具体涉及一种制取低碳烯烃的催化转化方法。
背景技术:2.低碳烯烃,如碳原子数为4或以下的烯烃,是现代化工行业重要的化工原料,其中以乙烯、丙烯和丁烯为代表,在现代生活中发挥着日益重要的作用。一方面,随着经济不断加速发展,各行各业对轻质油品、清洁燃料油的需求量也迅速增长。另一方面,随着油田开采量的不断增加,常规原油可供产量日趋减少,原油品质越来越差,趋于劣质化、重质化,虽然我国轻质烯烃的生产能力增长较快,但目前仍不能满足国内市场对轻质烯烃的需求。基于低碳烯烃获得的常用工业产品包括:采用乙烯生产的聚乙烯、环氧乙烷、乙二醇、聚氯乙烯、苯乙烯、醋酸乙烯等;采用丙烯生产的丙烯腈、环氧丙烷、丙酮等;采用丁烯生产的丁二烯、甲基乙基酮、仲丁醇、环氧丁烷及丁烯聚合物和共聚物;采用异丁烯生产的丁基橡胶、聚异丁烯橡胶及各种塑料。可以看出多种重要有机化工原料的生产工艺中均涉及乙烯、丙烯和丁烯的使用。
3.世界范围内制取低碳烯烃分为石油和非石油路线。采用传统的蒸汽裂解制乙烯、丙烯路线,对轻烃、石脑油等化工轻烃需求量较大,预计2025年需化工轻油70万吨/年,而国内原油普遍偏重,化工轻油难以满足生成乙烯、丙烯和丁烯原料的需求,在石油资源不足的情况下,蒸汽裂解原料的多样化已成为乙烯、丙烯工业发展趋势。蒸汽裂解原料主要有轻烃(如乙烷、丙烷和丁烷)、石脑油、柴油、凝析油和加氢尾油,其中,石脑油的质量分数约占50%以上,典型石脑油蒸汽裂解的乙烯收率约29%-34%,丙烯收率为13%-16%,较低的乙丙烯产出比难以满足当前低碳烯烃需求的现状。
4.cn101092323a中公开了一种采用c4-c8烯烃混合物为原料,在反应温度400-600℃,绝对压力为0.3-1.1kpa的条件下进行反应,经分离装置将c4馏分30-90重量%循环进反应器再次裂解制备乙烯和丙烯的方法。该方法重点通过c4馏分循环,提高了烯烃转化率,得到的乙烯和丙烯不少于原料烯烃总量的62%,但其乙烯/丙烯比较小,无法根据市场需求灵活调节,而且反应选择性低。
5.cn101239878a中公开了一种采用碳四及以上烯烃的富烯烃混合物为原料,在反应温度400-680℃,反应压力为-0.09-1.0mpa,重量空速为0.1~50小时-1的条件下进行反应,产物乙烯/丙烯较低,低于0.41,随着温度升高乙烯/丙烯增加,同时氢气、甲烷和乙烷增多。
6.非石油路线制取低碳烯烃主要是以甲醇或二甲醚为代表的有机含氧化合物为原料生产以乙烯和丙烯为主的低碳烯烃工艺简称mto。甲醇或二甲醚是典型的有机含氧化合物,用以生产低碳烯烃的反应特点是快速反应、强放热、剂醇比较低且反应诱导期较长,但mto工艺具有催化剂易失活的弊端。
7.因此,本领域尚缺乏能够整合多种催化转化反应形式并提高高价值低碳烯烃乙烯和丙烯的产量,改善乙烯和丙烯的选择性的催化转化模式。
技术实现要素:8.本公开的目的在于提供一种制取低碳烯烃的催化转化方法,本公开提供的催化转化方法能够显著提高乙烯、丙烯和丁烯的产率和选择性。
9.为了实现上述目的,本公开提供了一种制取低碳烯烃的催化转化方法,该方法包括如下步骤:(1)在第一催化转化反应条件下,将富含烯烃的原料与温度在650℃以上的催化转化催化剂在催化转化反应器的第一反应区中接触并进行第一催化转化反应,得到第一混合料流;所述富含烯烃的原料中含有50重量%以上的烯烃;(2)在第二催化转化反应条件下,使重质原料、有机含氧化合物原料在所述催化转化反应器的第二反应区中与来自所述第一反应区的所述第一混合料流接触并进行第二催化转化反应,得到反应油气和待生催化剂;(3)使所述反应油气进行第一分离处理,分离出乙烯、丙烯、丁烯、有机含氧化合物、第一催化裂化馏分油和第二催化裂化馏分油;所述第一催化裂化馏分油的初馏点为大于20℃且小于140℃的任意温度,所述第二催化裂化馏分油的终馏点为小于550℃且大于250℃的任意温度,所述第一催化裂化馏分油和所述第二催化裂化馏分油之间的切割点为140-250℃之间的任意温度;使所述第一催化裂化馏分油进行第二分离处理,分离出富含烯烃的物流;(4)使所述富含烯烃的物流返回所述催化转化反应器中继续反应。
10.可选地,该方法包括:使所述反应油气进入产物分馏装置进行第一分离处理,分离出乙烯、丙烯、丁烯、所述有机含氧化合物、所述第一催化裂化馏分油和所述第二催化裂化馏分油;使所述第一催化裂化馏分油进入烯烃分离装置进行第二分离处理,分离出所述富含烯烃的物流;使所述富含烯烃的物流返回所述催化转化反应器的第一反应区继续反应。
11.可选地,该方法包括:使所述反应油气进入产物分馏装置进行第一分离处理,分离出乙烯、丙烯、丁烯、所述有机含氧化合物、所述第一催化裂化馏分油和所述第二催化裂化馏分油;使所述第一催化裂化馏分油进入烯烃分离装置进行第三分离处理,分离出大分子烯烃物流和小分子烯烃物流;使所述小分子烯烃物流作为所述富含烯烃的物流返回所述催化转化反应器的第一反应区继续反应;使所述大分子烯烃物流返回所述催化转化反应器的第二反应区继续反应。
12.可选地,该方法还包括:使分离出的丁烯返回所述催化转化反应器的第一反应区继续反应;优选地,返回所述催化转化反应器中继续反应的所述丁烯先于所述富含烯烃的物流与所述催化转化催化剂接触。
13.可选地,所述丁烯返回所述催化反应器中继续反应的反应条件包括:反应温度为650-800℃,反应压力为0.05-1mpa,反应时间为0.01-10秒,所述催化转化催化剂与返回的所述丁烯的重量比为(20-200):1;优选地,反应温度为680-780℃,反应压力为0.1-0.8mpa,反应时间为0.05-8秒,所述催化转化催化剂与返回的所述丁烯的重量比为(30-180):1。
14.可选地,所述第一催化转化反应条件包括:反应温度为600-800℃,优选为630-780℃;反应压力为0.05-1mpa,优选为0.1-0.8mpa;反应时间为0.01-100秒,优选为0.1-80秒;所述催化转化催化剂与所述富含烯烃的原料的重量比为(1-200):1,优选为(3-180):1。
15.可选地,所述第二催化转化反应条件包括:反应温度为300-650℃,优选为400-600℃;反应压力为0.01-1mpa,优选为0.05-1mpa;反应时间为0.01-100秒,优选为0.1-80秒;所述催化转化催化剂与所述重质原料的重量比为(1-100):1,优选为(3-70):1;所述催化转化催化剂与所述有机含氧化合物原料的重量比为(1-100):1,优选为(3-50):1;所述第一催化
转化反应的反应温度比所述第二催化转化反应的反应温度高30-380℃。
16.可选地,以所述有机含氧化合物原料的进料位置为界,根据反应物的流向将所述第二反应区分为第二反应区上游和第二反应区下游,所述第二反应区下游位于所述有机含氧化合物原料的进料位置之后;该方法还包括:使来自所述第一反应区的所述第一混合料流在所述第二反应区上游与所述重质原料接触并进行催化转化反应,得到第二混合料流;然后使所述第二混合料流在所述第二反应区下游与所述有机含氧化合物原料接触并进行催化转化反应,得到所述反应油气和所述待生催化剂。
17.可选地,所述重质原料与所述第一混合料流在所述第二反应区上游中的催化转化反应条件包括:反应温度为400-650℃,优选为450-600℃;反应压力为0.05-1mpa,优选为0.1-0.8mpa;反应时间为0.01-100秒,优选为0.1-80秒;所述催化转化催化剂与所述重质原料的重量比为(1-100):1,优选为(3-70):1;所述有机含氧化合物原料与所述第二混合料流在所述第二反应区下游中的催化转化反应条件包括:反应温度为300-550℃,优选为400-530℃;反应压力为0.01-1mpa,优选为0.05-1mpa;反应时间为0.01-100秒,优选为0.1-80秒;所述第二反应区上游中的反应温度比所述第二反应区下游中的反应温度高0-200℃,优选高10-190℃;所述催化转化催化剂与所述有机含氧化合物原料的重量比为(1-100):1,优选为(3-50):1。
18.可选地,该方法还包括:使分离出的所述有机含氧化合物返回所述催化转化反应器的第二反应区继续反应。
19.可选地,所述催化转化反应器为提升管反应器,优选为变径提升管反应器。
20.可选地,该方法还包括:使所述待生催化剂进行烧焦再生,得到再生催化剂;使所述再生催化剂作为所述催化转化催化剂返回所述催化转化反应器的第一反应区。
21.可选地,所述富含烯烃的原料中烯烃的含量为80重量%以上,优选为90重量%以上,更优选为纯烯烃原料;所述重油选自石油烃和/或矿物油;所述石油烃选自减压瓦斯油、常压瓦斯油、焦化瓦斯油、脱沥青油、减压渣油、常压渣油和重芳烃抽余油中的一种或几种;所述矿物油选自煤液化油、油砂油和页岩油中的一种或几种;可选地,所述有机含氧化合物原料包含甲醇、乙醇、二甲醚、甲乙醚和乙醚中的至少一种。
22.可选地,所述富含烯烃的原料来自烷烃脱氢装置产生的碳五以上馏分、炼油厂催化裂解装置产生的碳五以上馏分、乙烯厂蒸汽裂解装置产生的碳五以上馏分、mto副产的碳五以上的富烯烃馏分、mtp副产的碳五以上的富烯烃馏分中的至少一种;可选地,所述烷烃脱氢装置的烷烃原料来自石脑油、芳烃抽余油和其他轻质烃中的至少一种。
23.可选地,以所述催化转化催化剂总重量为基准,所述催化转化催化剂包含1-50重量%的分子筛、5-99重量%的无机氧化物和0-70重量%的粘土;所述分子筛包括大孔分子筛、中孔分子筛和小孔分子筛中的一种或几种;以所述催化转化催化剂总重量为基准,所述催化转化催化剂还包括0.1重量%-3重量%的金属离子,所述金属离子选自viii族金属、iva族金属和稀土金属中的一种或多种。
24.可选地,在加氢反应条件下,使所述第二催化裂化馏分油与加氢催化剂接触反应,得到加氢第二催化裂化馏分油,使所述加氢第二催化裂化馏分油返回所述催化转化反应器继续反应;其中,所述加氢反应条件包括:氢分压为3.0-20.0mpa,反应温度为300-450℃,氢油体积比为300-2000,体积空速为0.1-3.0小时-1
,以所述加氢催化剂总重量为基准,所述加
氢催化剂包括20-90重量%的载体、10-80重量%的负载金属和0-10重量%的添加剂;其中,所述载体为氧化铝和/或无定型硅铝,所述添加剂选自氟、磷、钛和铂中至少一种,所述负载金属为vib族金属和/或viii族金属;优选地,所述vib族金属为mo或/和w,所述viii族金属为co或/和ni。
25.可选地,所述富含烯烃的物流中的烯烃为c5以上烯烃;所述富含烯烃的物流中c5以上烯烃的含量为50重量%以上,优选为80重量%以上。
26.通过上述技术方案,本公开提供了一种制取低碳烯烃的催化转化方法,该方法首先使富含烯烃的原料进行第一催化转化反应,再将得到的第一混合料流与重质原料、有机含氧化合物原料进行第二催化转化反应,生成反应油气和待生催化剂;对反应油气进行分离处理后即可获得乙烯、丙烯、丁烯、未转化的有机含氧化合物以及富含烯烃的物流,本公开的方法将石油路线与非石油路线制取低碳烯烃工艺集成于同一催化转化方法中,充分发挥了不同路线工艺的优势,提高了低碳烯烃的产量和选择性,尤其是乙烯和丙烯的产量和选择性;本公开还将分离得到的富含烯烃的物流返回催化转化反应器中继续进行反应,进一步提高了石化资源利用率;本公开还将重质原料引入生产工艺中,实现了对重油的回收利用、降低成本。
27.本公开的其他特征和优点将在随后的具体实施方式部分予以详细说明。
附图说明
28.附图是用来提供对本公开的进一步理解,并且构成说明书的一部分,与下面的具体实施方式一起用于解释本公开,但并不构成对本公开的限制。在附图中:图1是本公开第一种具体实施方式提供的制取低碳烯烃的催化转化方法流程示意图。图2是本公开第二种具体实施方式提供的制取低碳烯烃的催化转化方法流程示意图。图3是本公开第三种具体实施方式提供的制取低碳烯烃的催化转化方法流程示意图。图4是本公开第四种具体实施方式提供的制取低碳烯烃的催化转化方法流程示意图。
29.附图说明标记
[0030]ⅰ第一反应区
ꢀꢀꢀꢀꢀꢀꢀⅱ
第二反应区
[0031]
1管线
ꢀꢀꢀꢀꢀꢀꢀꢀꢀꢀꢀꢀꢀꢀ
2反应器
ꢀꢀꢀꢀꢀꢀꢀꢀꢀꢀꢀꢀꢀꢀ
3管线
[0032]
4管线
ꢀꢀꢀꢀꢀꢀꢀꢀꢀꢀꢀꢀꢀꢀ
5管线
ꢀꢀꢀꢀꢀꢀꢀꢀꢀꢀꢀꢀꢀꢀꢀꢀ
6管线
[0033]
7管线
ꢀꢀꢀꢀꢀꢀꢀꢀꢀꢀꢀꢀꢀꢀ
8出口段
ꢀꢀꢀꢀꢀꢀꢀꢀꢀꢀꢀꢀꢀꢀ
9沉降器
[0034]
10集气室
ꢀꢀꢀꢀꢀꢀꢀꢀꢀꢀꢀ
11汽提段
ꢀꢀꢀꢀꢀꢀꢀꢀꢀꢀꢀꢀꢀ
12管线
[0035]
13斜管
ꢀꢀꢀꢀꢀꢀꢀꢀꢀꢀꢀꢀꢀ
14再生器
ꢀꢀꢀꢀꢀꢀꢀꢀꢀꢀꢀꢀꢀ
15管线
[0036]
16管线
ꢀꢀꢀꢀꢀꢀꢀꢀꢀꢀꢀꢀꢀ
17管线
ꢀꢀꢀꢀꢀꢀꢀꢀꢀꢀꢀꢀꢀꢀꢀ
18管线
[0037]
19大油气管线
ꢀꢀꢀꢀꢀꢀꢀ
20产物分离装置
ꢀꢀꢀꢀꢀꢀꢀ
21管线
[0038]
22管线
ꢀꢀꢀꢀꢀꢀꢀꢀꢀꢀꢀꢀꢀ
23管线
ꢀꢀꢀꢀꢀꢀꢀꢀꢀꢀꢀꢀꢀꢀꢀ
24管线
[0039]
25管线
ꢀꢀꢀꢀꢀꢀꢀꢀꢀꢀꢀꢀꢀ
26管线
ꢀꢀꢀꢀꢀꢀꢀꢀꢀꢀꢀꢀꢀꢀꢀ
27管线
[0040]
28管线
ꢀꢀꢀꢀꢀꢀꢀꢀꢀꢀꢀꢀꢀ
29烯烃分离装置
ꢀꢀꢀꢀꢀꢀꢀ
30管线
[0041]
31管线
ꢀꢀꢀꢀꢀꢀꢀꢀꢀꢀꢀꢀꢀ
32加氢处理反应器
ꢀꢀꢀꢀꢀ
33管线
[0042]
34管线
具体实施方式
[0043]
以下对本公开的具体实施方式进行详细说明。应当理解的是,此处所描述的具体实施方式仅用于说明和解释本公开,并不用于限制本公开。
[0044]
本公开发明人经过进行大量的烷烃和烯烃催化裂化试验,出乎意料地发现,采用烯烃和烷烃分别在相同的催化裂化反应条件下进行反应,由烯烃裂化生产的低碳烯烃的产率以及选择性显著地优异于烷烃;并且烯烃与烷烃催化裂化的产品分布差异性也较为明显。发明人还发现,在石油路线制取低碳烯烃的工艺中,引入非石油路线工艺的有机含氧化合物原料共同制取低碳烯烃,可以显著提高产物中低碳烯烃的产率和选择性。
[0045]
本公开提供了一种制取低碳烯烃的催化转化方法,该方法包括如下步骤:(1)在第一催化转化反应条件下,将富含烯烃的原料与温度在650℃以上的催化转化催化剂在催化转化反应器的第一反应区中接触并进行第一催化转化反应,得到第一混合料流;所述富含烯烃的原料中含有50重量%以上的烯烃;(2)在第二催化转化反应条件下,使重质原料、有机含氧化合物原料在所述催化转化反应器的第二反应区中与来自所述第一反应区的所述第一混合料流接触并进行第二催化转化反应,得到反应油气和待生催化剂;(3)使所述反应油气进行第一分离处理,分离出乙烯、丙烯、丁烯、有机含氧化合物、第一催化裂化馏分油和第二催化裂化馏分油;所述第一催化裂化馏分油的初馏点为大于20℃且小于140℃的任意温度,所述第二催化裂化馏分油的终馏点为小于550℃且大于250℃的任意温度,所述第一催化裂化馏分油和所述第二催化裂化馏分油之间的切割点为140-250℃之间的任意温度;使所述第一催化裂化馏分油进行第二分离处理,分离出富含烯烃的物流;(4)使所述富含烯烃的物流返回所述催化转化反应器中继续反应。
[0046]
本公开提供了一种制取低碳烯烃的催化转化方法,该方法首先使富含烯烃的原料进行第一催化转化反应,再将得到的第一混合料流与重质原料、有机含氧化合物原料进行第二催化转化反应,生成反应油气和待生催化剂;对反应油气进行分离处理后即可获得乙烯、丙烯、丁烯、有机含氧化合物以及富含烯烃的物流。本公开的方法将石油路线与非石油路线制取低碳烯烃工艺集成于同一催化转化方法中,充分发挥了不同路线工艺的优势,提高了低碳烯烃的产量和选择性,尤其是乙烯和丙烯的产量和选择性;本公开还将分离得到的富含烯烃的物流返回催化转化反应器中继续进行反应,进一步提高了石化资源利用率;本公开还将重质原料引入生产工艺中,实现了对重油的回收利用、降低成本。
[0047]
在一种优选实施方式中,所述富含烯烃的原料中烯烃的含量为80重量%以上,优选为90重量%以上,更优选为纯烯烃原料;所述富含烯烃的原料中的烯烃选自碳原子数为4及以上的烯烃或碳原子数为5及以上的烯烃。发明人在研究中发现,采用的富含烯烃的原料中烯烃的含量的提高有利于产物中低碳烯烃的产率及选择性的提高。
[0048]
本公开中,一种实施方式,富含烯烃的原料可以仅来自重油原料催化转化产物中分离出的含碳五及以上烯烃的含烯烃物流,即富含烯烃的原料为系统内部循环回用的烯烃;另一实施方式中,富含烯烃的原料除了包含上述的含碳五及以上烯烃的含烯烃物流之外,还可以包含外加的烯烃原料,外加的烯烃原料的量没有特别要求。
[0049]
在本公开的一些实施方式中,富含烯烃的原料可来自下述来源中的任意一种或几种:烷烃脱氢装置产生的碳五以上馏分、炼油厂催化裂解装置产生的碳五以上馏分、乙烯厂蒸汽裂解装置产生的碳五及以上馏分、mto(甲醇制烯烃)及副产的碳五及以上的富烯烃馏
分、mtp(甲醇制丙烯)副产的碳五及以上的富烯烃馏分中的至少一种。在进一步的实施方式中,烷烃脱氢生产富含烯烃的原料所采用的烷烃原料可以来自石脑油、芳烃抽余油和/或其他轻质烃中的至少一种。在实际生产中,也可以采用其他不同石油化工装置生产获得的烷烃产品。
[0050]
进一步地,在丁烯产物回炼的实施方式中,所述烃油原料中的烯烃来自烷烃原料脱氢产生的c4以上馏分、炼油厂催化裂解装置产生的c4以上馏分、乙烯厂中蒸汽裂解装置产生的c4以上馏分、mto副产的c4以上的富烯烃馏分、mtp副产的c4以上的富烯烃馏分;所述烷烃原料选自石脑油、芳烃抽余油和其他装置的轻质烃中的至少一种。
[0051]
在一种具体实施方式中,可以采用下述方法进行烷烃脱氢处理:在脱氢反应条件下,使烷烃与脱氢催化剂在脱氢处理反应器中进行接触反应,得到富含烯烃的原料。
[0052]
其中,脱氢反应条件包括:脱氢处理反应器的入口温度为400-700℃,烷烃的体积空速为500-5000小时-1
,接触反应的压力为0.04-1.1bar。
[0053]
所述脱氢催化剂由载体以及负载在载体上的活性组分和助剂组成;可选地,以所述脱氢催化剂总重量为基准,所述载体的含量为60-90重量%,所述活性组分的含量为8-35重量%,所述助剂的含量为0.1-5重量%;可选地,所述载体为含有改性剂的氧化铝;其中,以所述脱氢催化剂总重量为基准,所述改性剂的含量为0.1-2重量%,其中,所述改性剂可以为la和/或ce;可选地,所述活性组分为铬;可选地,所述助剂可为铋和碱金属组合物或者铋和碱土金属组分组合物;其中,铋与所述活性组分的摩尔比为1:(5-50);铋与碱金属组分的摩尔比为1:(0.1-5);铋与碱土金属组分的摩尔比为1:(0.1-5);所述碱金属组分可以选自li、na和k中的一种或多种;所述碱土金属组分可以选自mg、ca和ba中的一种或多种。
[0054]
在一种优选实施方式中,本公开采用的重油选自石油烃和/或矿物油;所述石油烃选自减压瓦斯油、常压瓦斯油、焦化瓦斯油、脱沥青油、减压渣油、常压渣油和重芳烃抽余油中的一种或几种;所述矿物油选自煤液化油、油砂油和页岩油中的一种或几种。
[0055]
在一种实施方式中,所述有机含氧化合物原料包含甲醇、乙醇、二甲醚、甲乙醚和乙醚中的至少一种。一种具体实施方式,所述有机含氧化合物原料可以来自合成气转化为含氧化合物工艺,例如合成气制甲醇工艺、合成气制乙醇工艺,其中合成气例如为煤基合成气和/或天然气基合成气。
[0056]
在一种具体实施方式中,所述第一催化转化反应条件包括:反应温度为600-800℃,优选为630-780℃;反应压力为0.05-1mpa,优选为0.1-0.8mpa;反应时间为0.01-100秒,优选为0.1-80秒;所述催化转化催化剂与所述富含烯烃的原料的重量比为(1-200):1,优选为(3-180):1;所述第二催化转化反应条件包括:反应温度为300-650℃,优选为400-600℃;反应压力为0.01-1mpa,优选为0.05-1mpa;反应时间为0.01-100秒,优选为0.1-80秒;所述催化转化催化剂与所述重质原料的重量比为(1-100):1,优选为(3-70):1;所述催化转化催化剂与所述有机含氧化合物原料的重量比为(1-100):1,优选为(3-50):1。可选地,所述第一催化转化反应的反应温度比所述第二催化转化反应的反应温度高30-380℃。
[0057]
本公开中,第一催化转化的反应温度是指第一反应区的出口温度;第二催化转化的反应温度是指第二反应区的出口温度。
[0058]
本公开中,使重质原料、有机含氧化合物原料在所述催化转化反应器的第二反应区中与来自所述第一反应区的所述第一混合料流接触并进行第二催化转化反应包括以下
情况:1)重质原料和有机含氧化合物原料一起进入第二反应区与第一混合料流接触并发生反应,例如图4所示,将重质原料和有机含氧化合物原料混合后所得的混合原料送入第二反应区与第一混合料流接触反应;2)如图3所示,使所述第一混合料流先与重质原料接触发生反应后,获得的混合料流再和有机含氧化合物原料接触反应;3)所述第一混合料流先与有机含氧化合物原料接触发生反应后,获得的混合料流再和重质原料接触反应。
[0059]
在一种优选实施方式中,如图3所示,以所述有机含氧化合物原料的进料位置为界,根据反应物的流向将所述第二反应区分为第二反应区上游和第二反应区下游,所述第二反应区下游位于所述有机含氧化合物原料的进料位置之后;该方法还包括:
[0060]
使来自所述第一反应区的所述第一混合料流在所述第二反应区上游与所述重质原料接触并进行催化转化反应,得到第二混合料流,然后使所述第二混合料流在所述第二反应区下游与所述有机含氧化合物原料接触并进行催化转化反应,得到反应油气和待生催化剂。这一实施方式能够进一步提高乙烯和丙烯产率和选择性。
[0061]
本公开中,第二反应区上游和第二反应区下游是按照催化转化反应器中物流的流动方向定义的。
[0062]
这一具体实施方式中,进一步地,所述重质原料与所述第一混合料流在所述第二反应区上游中的催化转化反应条件包括:反应温度为400-650℃,优选为450-600℃;反应压力为0.05-1mpa,优选为0.1-0.8mpa;反应时间为0.01-100秒,优选为0.1-80秒;所述催化转化催化剂与所述重质原料的重量比为(1-100):1,优选为(3-70):1;所述有机含氧化合物原料与所述第二混合料流在所述第二反应区下游中的催化转化反应条件包括:反应温度为300-550℃,优选为400-530℃;反应压力为0.01-1mpa,优选为0.05-1mpa;反应时间为0.01-100秒,优选为0.1-80秒;所述第二反应区上游中的反应温度比所述第二反应区下游中的反应温度高0-200℃,优选高10-190℃;所述催化转化催化剂与所述有机含氧化合物原料的重量比为(1-100):1,优选为(3-50):1。
[0063]
具体地,本公开中,第二反应区上游中的反应温度是指第二反应区上游的出口温度,第二反应区下游中的反应温度是指第二反应区下游的出口温度。
[0064]
在一种实施方式中,该方法还可以包括:使分离出的所述有机含氧化合物返回所述催化转化反应器的第二反应区继续反应。
[0065]
在一种具体实施方式中,使分离出的所述有机含氧化合物返回所述第二反应区下游继续反应。
[0066]
在一种具体实施方式中,本公开提供的催化转化方法还包括:使所述反应油气进入产物分馏装置进行第一分离处理,分离出乙烯、丙烯、丁烯、所述有机含氧化合物、所述第一催化裂化馏分油和所述第二催化裂化馏分油;
[0067]
使所述第一催化裂化馏分油进入烯烃分离装置进行第二分离处理,分离出所述富含烯烃的物流;
[0068]
使所述富含烯烃的物流返回所述催化转化反应器的第一反应区继续反应。
[0069]
在另一种具体实施方式中,本公开提供的催化转化方法还包括:使所述反应油气进入产物分馏装置进行第一分离处理,分离出乙烯、丙烯、丁烯、所述有机含氧化合物、所述第一催化裂化馏分油和所述第二催化裂化馏分油;使所述第一催化裂化馏分油进入烯烃分离装置进行第三分离处理,分离出大分子烯烃物流和小分子烯烃物流;使所述小分子烯烃
物流作为所述富含烯烃的物流返回所述催化转化反应器的第一反应区继续反应;使所述大分子烯烃物流返回所述催化转化反应器的第二反应区继续反应。该实施方式将第一催化裂化馏分油分离出大分子烯烃物流和小分子烯烃物流,并将两种烯烃物流返回催化转化反应器的不同位置继续反应,可以充分利用不同分子的烯烃物流自身性质,提高反应转化率,避免副反应发生。
[0070]
本公开中,所述大分子烯烃物流是指第一催化裂化馏分油中包含的分子较大的烯烃,如c10及以上的烯烃;所述小分子烯烃物流是指第一催化裂化馏分油中包含的分子较小的烯烃,如c5-c9烯烃。
[0071]
本公开中,第二分离处理和第三分离处理为本领域常规选择的分离方式。
[0072]
在一种实施方式中,本公开提供的催化转化方法还包括:使分离出的丁烯返回所述催化转化反应器的第一反应区继续反应。
[0073]
在一种优选实施方式中,返回所述催化转化反应器中继续反应的所述丁烯先于所述富含烯烃的物流与所述催化转化催化剂接触。在该实施方式中,催化转化反应器中,高温的催化转化催化剂先与返回反应器的丁烯接触反应,然后再与富含烯烃的物流接触反应。烃类裂化的难度随着碳数减小不断加大,丁烯裂化需要的能量较高,因此本公开使丁烯优先和高温的催化转化催化剂接触,再使含c4以上烯烃后和催化转化催化剂接触,不仅能够提高丁转化率和产品乙烯、丙烯选择性,并且避免烯烃同时进料生成较多副产品,实现资源的高效利用。
[0074]
在一种具体实施方式中,所述丁烯返回所述催化反应器中继续反应的反应条件包括:反应温度为650-800℃,反应压力为0.05-1mpa,反应时间为0.01-10秒,所述催化转化催化剂与返回的所述丁烯的重量比为(20-200):1。
[0075]
优选地,反应温度为680-780℃,反应压力为0.1-0.8mpa,反应时间为0.05-8秒,所述催化转化催化剂与返回的所述丁烯的重量比为(30-180):1。
[0076]
在一种实施方式中,本公开催化转化方法还包括:使分离出的所述有机含氧化合物返回所述催化转化反应器的第二反应区继续反应,进一步提升了原料转化率和乙烯、丙烯产率。
[0077]
在一种实施方式中,本公开提供的催化转化方法还可以包括:在加氢反应条件下,使所述第二催化裂化馏分油与加氢催化剂接触反应,得到加氢第二催化裂化馏分油,使所述加氢第二催化裂化馏分油返回所述催化转化反应器继续反应。本公开将第二催化裂化馏分油进行加氢处理后可以作为催化裂化原料继续进行反应,扩大了原料来源,提高了资源利用率,进一步提高了低碳烯烃的产率。
[0078]
在一种具体实施方式中,所述加氢反应条件包括:氢分压为3.0-20.0mpa,反应温度为300-450℃,氢油体积比为300-2000,体积空速为0.1-3.0小时-1
。
[0079]
在一种具体实施方式中,本公开提供的催化转化方法包括:使所述加氢第二催化裂化馏分油返回所述催化转化反应器的第二反应区上游继续反应。在该实施方式中,使高温的催化转化催化剂先与返回反应器的富含烯烃的物流接触反应,然后再与返回催化转化反应器的加氢第二催化裂化馏分油接触反应,从而使得加氢第二催化裂化馏分油含有的碳数较大的饱和烃在相对缓和的反应条件下先裂化成c5-c9的烯烃,然后使获得的烯烃返回催化裂化反应器再次进行高温裂化,从而进一步提高乙烯收率。
[0080]
在一种具体实施方式中,本公开采用的催化转化反应器可以选自提升管、等线速的流化床、等直径的流化床、上行式输送线和下行式输送线中的一种或两种串联组合,其中所述提升管可以为等直径提升管反应器或者变径流化床反应器,流化床反应器可以为等线速的流化床或等直径的流化床。
[0081]
在一种优选实施方式中,本公开采用提升管反应器作为催化转化反应器;在一种更优选实施方式中,催化转化反应器为变径提升管反应器。
[0082]
在一种优选实施方式中,本公开还可以使所述待生催化剂进行烧焦再生,得到再生催化剂;使所述再生催化剂作为所述催化转化催化剂返回所述催化转化反应器的第一反应区,实现了催化转化催化剂的循环利用。
[0083]
在一种具体实施方式中,以所述催化转化催化剂总重量为基准,所述催化转化催化剂包含1-50重量%的分子筛、5-99重量%的无机氧化物和0-70重量%的粘土。
[0084]
所述分子筛作为催化转化催化剂的活性组分,可选自所述分子筛包括大孔分子筛、中孔分子筛和小孔分子筛中的一种或几种。
[0085]
在一种实施方式中,所述中孔分子筛可以为zsm分子筛,进一步地,zsm分子筛可以选自zsm-5、zsm-11、zsm-12、zsm-23、zsm-35、zsm-48中的一种或几种。
[0086]
种实施方式中,所述小孔分子筛可以为sapo分子筛和/或ssz分子筛,进一步地,sapo分子筛可以选自sapo-34、sapo-11、sapo-47中的一种或几种,ssz分子筛可以选自ssz-13、ssz-39、ssz-62中的一种或几种。在进一步的实施方式中,中孔分子筛占分子筛总重量的50重量%-100重量%,优选70重量%-100重量%,小孔分子筛占分子筛总重量的0重量%-50重量%,优选0重量%-30重量%。
[0087]
一种实施方式中,所述大孔分子筛可以选自稀土y分子筛、稀土氢y分子筛、超稳y分子筛、高硅y分子筛、beta分子筛和其它类似结构的分子筛之中的一种或一种以上的混合物。
[0088]
在一种优选实施方式中,还可以在分子筛上负载金属离子,金属离子可选自viii族金属、iva族金属和稀土金属中的一种或多种;在一种更优选的实施方式中,以催化转化催化剂总重量为基准,负载的金属离子重量含量为0.1%-3%,可以进一步提高催化转化催化剂的催化能力。
[0089]
在一种优选实施方式中,无机氧化物作为粘接剂,选自二氧化硅(sio2)和/或三氧化二铝(al2o3);粘土作为基质(即载体),选自高岭土和/或多水高岭土。
[0090]
在一种实施方式中,所述加氢催化剂包括载体以及负载在载体上的金属组分和任选的添加剂,所述载体为氧化铝和/或无定型硅铝,所述金属组分为vib族金属和/或viii族金属,所述添加剂选自氟、磷、钛和铂中至少一种。所述vib族金属为mo或/和w,所述viii族金属为co或/和ni;以加氢催化剂总重量为基准,所述添加剂的含量为0-10重量%,vib族金属的含量为12-39重量%,viii族金属的含量为1-9重量%。
[0091]
在一种实施方式中,所述富含烯烃的物流中的烯烃为c5以上烯烃;所述富含烯烃的物流中c5以上烯烃的含量为50重量%以上,优选为80重量%以上。
[0092]
在一种具体实施方式中,可以将分离系统分离得到的含烯烃物流继续采用烯烃分离系统进一步分离,达到了含烯烃物流浓缩的效果,使得返回催化转化反应器中的含烯烃物流中烯烃含量得到提升,也可以提升低碳烯烃的产率和选择性。
[0093]
参见图1,在第一种具体实施方式中,所述制取低碳烯烃的催化转化方法包括以下步骤:
[0094]
在第一反应区ⅰ,预提升介质经管线1由催化转化反应器2底部进入,来自管线17的再生催化转化催化剂在预提升介质的提升作用下沿催化转化反应器2向上运动,富含烯烃的原料(烯烃含量≥50%)经管线3与来自管线4的雾化蒸汽一起注入反应器2第一反应区ⅰ底部,与温度在650℃以上的催化转化催化剂接触并发生反应,得到第一混合料流且继续向上运动;
[0095]
在第二反应区ⅱ,重质原料油经管线5与来自管线6的雾化蒸汽一起注入催化转化反应器2第二反应区ⅱ底部,并将有机含氧化合物原料(如甲醇)经管线7引入第二反应区ⅱ底部,重质原料油与有机含氧化合物原料分别与催化转化反应器2已有的来自第一反应区ⅰ的第一混合料流接触并发生反应。
[0096]
生成的反应产物和失活的待生催化剂经出口段8进入沉降器9中的旋风分离器,实现待生催化剂与反应产物的分离,反应产物进入集气室10,催化剂细粉由料腿返回沉降器。沉降器中待生催化剂流向汽提段11,与来自管线12的汽提蒸汽接触。从待生催化剂中汽提出的油气经旋风分离器后进入集气室10。汽提后的待生催化剂经斜管13进入再生器14,主风经管线16进入再生器,烧去待生催化剂上的焦炭,使失活的待生催化剂再生。烟气经管线15进入烟机。再生后的催化剂经管线17进入提升管。
[0097]
反应产物(反应油气)经过大油气管线19进入后续的产物分离装置20进行第一分离处理,分离得到的氢气、甲烷和乙烷经管线21引出,乙烯经管线22引出,丙烯经管线23引出,丁烯经管线24引出,丁烯可以返回或不返回催化转化反应器2的第一反应区ⅰ底部继续反应,丙烷和丁烷经管线25引出,未转化的有机含氧化合物经管线26引出,可以返回或不返回催化转化反应器第二反应区底部继续反应;初馏点为大于20℃且小于140℃的任意温度的第一催化裂化馏分油经管线27引入到烯烃分离装置29进行第三分离处理,分离得到不含烯烃的物流、小分子烯烃物流以及大分子烯烃物流:将不含烯烃的物流由管线31引出,将小分子烯烃物流作为富含烯烃的物流经管线30引入催化转化反应器第一反应区ⅰ底部继续反应,将大分子烯烃物流经管线34返回催化转化反应器2第二反应区底部继续反应;将终馏点为小于550℃且大于250℃的任意温度的第二催化裂化馏分油经管线28引入加氢处理反应器32(第一催化裂化馏分油和第二催化裂化馏分油之间的切割点为140-250℃之间的任意温度),加氢处理后获得轻组分和加氢催化裂化第二馏分油:轻组分由管线18引出,加氢催化裂化第二馏分油由管线33引入催化转化反应器2第二反应区底部继续反应。
[0098]
参见图2,在第二种具体实施方式中,所述制取低碳烯烃的催化转化方法包括以下步骤:
[0099]
在第一反应区ⅰ,预提升介质经管线1由催化转化反应器2底部进入,来自管线17的再生催化转化催化剂在预提升介质的提升作用下沿催化转化反应器2向上运动,富含烯烃的原料(烯烃含量≥50%)经管线3与来自管线4的雾化蒸汽一起注入反应器2第一反应区底部,与温度在650℃以上的催化转化催化剂接触并发生反应,得到第一混合料流且继续向上运动;
[0100]
在第二反应区ⅱ,将重质原料油经管线5与来自管线6的雾化蒸汽一起注入催化转化反应器2的第二反应区上游,使重质原料油与来自第一反应区的第一混合料流接触并发
生反应,获得第二混合料流并继续向上运动;将有机含氧化合物原料(如甲醇)经管线7引入第二反应区下游,使有机含氧化合物原料与第二混合料流接触并发生反应。
[0101]
生成的反应产物和失活的待生催化剂经出口段8进入沉降器9中的旋风分离器,实现待生催化剂与反应产物的分离,反应产物进入集气室10,催化剂细粉由料腿返回沉降器。沉降器中待生催化剂流向汽提段11,与来自管线12的汽提蒸汽接触。从待生催化剂中汽提出的油气经旋风分离器后进入集气室10。汽提后的待生催化剂经斜管13进入再生器14,主风经管线16进入再生器,烧去待生催化剂上的焦炭,使失活的待生催化剂再生。烟气经管线15进入烟机。再生后的催化剂经管线17进入提升管。
[0102]
反应产物(反应油气)经过大油气管线19进入后续的产物分离装置20进行第一分离处理,分离得到的氢气、甲烷和乙烷经管线21引出,乙烯经管线22引出,丙烯经管线23引出,丁烯经管线24引出,丁烯可以返回或不返回催化转化反应器2的第一反应区ⅰ底部继续反应,丙烷和丁烷经管线25引出,未转化的有机含氧化合物经管线26引出,可以返回或不返回催化转化反应器第二反应区下游继续反应;初馏点为大于20℃且小于140℃的任意温度的第一催化裂化馏分油经管线27引入到烯烃分离装置29进行第三分离处理,分离得到不含烯烃的物流、小分子烯烃物流以及大分子烯烃物流:将不含烯烃的物流由管线31引出,将小分子烯烃物流作为富含烯烃的物流经管线30引入催化转化反应器第一反应区ⅰ底部继续反应,将大分子烯烃物流经管线34返回催化转化反应器2的第二反应区上游继续反应;将终馏点为小于550℃且大于250℃的任意温度的第二催化裂化馏分油经管线28引入加氢处理反应器32(第一催化裂化馏分油和第二催化裂化馏分油之间的切割点为140-250℃之间的任意温度),加氢处理后获得轻组分和加氢催化裂化第二馏分油:轻组分由管线18引出,加氢催化裂化第二馏分油由管线33引入催化转化反应器2的第二反应区上游继续反应。
[0103]
参见图3,在第三种具体实施方式中,所述制取低碳烯烃的催化转化方法包括以下步骤:
[0104]
在第一反应区ⅰ,预提升介质经管线1由催化转化反应器2底部进入,来自管线17的再生催化转化催化剂在预提升介质的提升作用下沿催化转化反应器2向上运动,富含烯烃的原料(烯烃含量≥50%)经管线3与来自管线4的雾化蒸汽一起注入反应器2的第一反应区底部,与温度在650℃以上的催化转化催化剂接触并发生反应,得到第一混合料流且继续向上运动;
[0105]
在第二反应区ⅱ,重质原料油经管线5与来自管线6的雾化蒸汽一起注入催化转化反应器2第二反应区上游,并与催化转化反应器2已有的来自第一反应区ⅰ的第一混合料流接触,重质原料油在热的催化剂上发生反应,得到第二混合料流并向上运动;将有机含氧化合物(如甲醇)经管线7引入第二反应区下游,与来自第二反应区上游的第二混合料流接触并发生反应。
[0106]
生成的反应产物和失活的待生催化剂经出口段8进入沉降器9中的旋风分离器,实现待生催化剂与反应产物的分离,反应产物进入集气室10,催化剂细粉由料腿返回沉降器。沉降器中待生催化剂流向汽提段11,与来自管线12的汽提蒸汽接触。从待生催化剂中汽提出的油气经旋风分离器后进入集气室10。汽提后的待生催化剂经斜管13进入再生器14,主风经管线16进入再生器,烧去待生催化剂上的焦炭,使失活的待生催化剂再生。烟气经管线15进入烟机。再生后的催化剂经管线17进入提升管。
[0107]
反应产物(反应油气)经过大油气管线19进入后续的产物分离装置20进行第一分离处理,分离得到的氢气、甲烷和乙烷经管线21引出,乙烯经管线22引出,丙烯经管线23引出,丁烯经管线24引出,丁烯可以返回或不返回催化转化反应器2的第一反应区ⅰ底部继续反应,丙烷和丁烷经管线25引出,分离出未转化的有机含氧化合物经管线26引出,可以返回或不返回催化转化反应器2的第二反应区下游继续反应;初馏点为大于20℃且小于140℃的任意温度的第一催化裂化馏分油经管线27引入到烯烃分离装置29进行第二分离处理,分离得到不含烯烃的物流和富含烯烃的物流:不含烯烃的物流由管线31引出,富含烯烃的物流经管线30引入催化转化反应器第一反应区ⅰ底部继续反应;将终馏点为小于550℃且大于250℃的任意温度的第二催化裂化馏分油经管线28引入加氢处理反应器32(第一催化裂化馏分油和第二催化裂化馏分油之间的切割点为140-250℃之间的任意温度),加氢处理后获得轻组分和加氢催化裂化第二馏分油:轻组分由管线18引出,加氢催化裂化第二馏分油由管线33引入催化转化反应器2的第二反应区上游继续反应。
[0108]
参见图4,在第四种具体实施方式中,所述制取低碳烯烃的催化转化方法包括以下步骤:
[0109]
在第一反应区ⅰ,预提升介质经管线1由催化转化反应器2底部进入,来自管线17的再生催化转化催化剂在预提升介质的提升作用下沿催化转化反应器2向上加速运动,富含烯烃的原料(烯烃含量≥50%)经管线3与来自管线4的雾化蒸汽一起注入反应器2的第一反应区底部,与温度在650℃以上的催化转化催化剂接触并发生反应,得到第一混合料流且继续向上运动;
[0110]
在第二反应区ⅱ,重质原料油经管线5与来自管线6的雾化蒸汽一起注入催化转化反应器2的第二反应区ⅱ底部,将有机含氧化合物原料(如甲醇)经管线7与重质原料油一起进入第二反应区ⅱ底部,并与来自第一反应区ⅰ的第一混合料流接触并发生反应。
[0111]
生成的反应物流和失活的待生催化剂经出口段8进入沉降器9中的旋风分离器,实现待生催化剂与反应物流的分离,反应物流进入集气室10,催化剂细粉由料腿返回沉降器。沉降器中待生催化剂流向汽提段11,与来自管线12的汽提蒸汽接触。从待生催化剂中汽提出的油气经旋风分离器后进入集气室10。汽提后的待生催化剂经斜管13进入再生器14,主风经管线16进入再生器,烧去待生催化剂上的焦炭,使失活的待生催化剂再生。烟气经管线15进入烟机。再生后的催化剂经管线17进入提升管。
[0112]
反应产物(反应油气)经过大油气管线19进入后续的分离装置20进行第一分离处理,分离得到的氢气、甲烷和乙烷经管线21引出,乙烯经管线22引出,丙烯经管线23引出,丁烯经管线24引出,丁烯可以返回或不返回催化转化反应器2的第一反应区ⅰ底部继续反应,丙烷和丁烷经管线25引出,未转化的有机含氧化合物经管线26引出,可以返回或不返回催化转化反应器2的第二反应区ⅱ底部继续反应;将初馏点为大于20℃且小于140℃的任意温度的第一催化裂化馏分油经管线27引入到烯烃分离装置29进行第二分离处理,分离得到不含烯烃的物流和富含烯烃的物流:不含烯烃的物流由管线31引出,富含烯烃的物流经管线30引入所述催化转化反应器2的第一反应区ⅰ底部继续反应,将终馏点为小于550℃且大于250℃的任意温度的第二催化裂化馏分油经管线28引入加氢处理反应器32(第一催化裂化馏分油和所述第二催化裂化馏分油之间的切割点为140-250℃之间的任意温度),加氢处理后获得轻组分和加氢第二催化裂化馏分油:轻组分由管线18引出,加氢第二催化裂化馏分
油由管线33引入催化转化反应器2的第二反应区ⅱ底部继续反应。
[0113]
本公开图1-图4中,虚线代表该组分可以返回催化转化反应器继续反应,也可以不返回催化转化反应器。
[0114]
以下通过实施例进一步详细说明本公开。实施例中所用到的原材料均可通过商购途径获得。
[0115]
(1)本公开实施例中所用的原料i和ii为重质原料油(重油i和ii),性质参见下表1-1和表1-2所示。
[0116]
表1-1(重油i)
[0117][0118]
表1-2(重油ii)
[0119][0120][0121]
(2)本公开采用的催化剂
ⅰ
通过下述制备方法制备得到:
[0122]
用4300克脱阳离子水将969克多水高岭土(中国高岭土公司产物,固含量73%)打浆,再加入781克拟薄水铝石(山东淄博铝石厂产物,固含量64%)和144毫升盐酸(浓度30%,比重1.56)搅拌均匀,在60℃静置老化1小时,保持ph为2-4,降至常温,再加入预先准备好的5000克浆液,其中中孔zsm-5分子筛和大孔y型分子筛(中国石化催化剂齐鲁分公司生产)1600g,二者重量比9:1。搅拌均匀,喷雾干燥,洗去游离na
+
,得催化剂。将得到的催化剂在800℃和100%水蒸汽下进行老化,老化后的催化剂称为催化剂
ⅰ
,催化剂
ⅰ
性质见表2。
[0123]
(3)本公开采用的催化剂
ⅱ
的商品牌号为cep-1,为中国石化催化剂齐鲁分公司生产工业产品,催化剂性质见表2。
[0124]
(4)本公开采用的催化剂
ⅲ
的商品牌号为chp-1,为中国石化催化剂齐鲁分公司生产工业产品,催化剂性质见表2。
[0125]
上述催化剂
ⅰ‑ⅲ
性质参见下表2所示:
[0126]
表2
[0127][0128][0129]
(4)本公开采用的催化剂
ⅳ
通过下述制备方法制备得到:
[0130]
称取偏钨酸铵((nh4)2w4o
13
·
18h2o,化学纯)和硝酸镍(ni(no3)2·
18h2o,化学纯),用水配成200毫升溶液。将溶液加入到氧化铝载体50克中,在室温下浸渍3小时,在浸渍过程中使用超声波处理浸渍液30分钟,冷却,过滤,放到微波炉中干燥约15分钟。该催化剂
ⅳ
的组成为:30.0重量%wo3,3.l重量%nio和余量氧化铝。
[0131]
(5)本公开采用的催化剂
ⅴ
通过下述制备方法制备得到:
[0132]
称取1000克由中国石化催化剂长岭分公司生产的拟薄水铝石,之后加入含硝酸(化学纯)10毫升的水溶液1000毫升,在双螺杆挤条机上挤条成型,并在120℃干燥4小时,800℃焙烧4小时后得到催化剂载体。用含氟化铵120克的水溶液900毫升浸渍2小时,120℃干燥3小时,600℃焙烧3小时;降至室温后,用含偏钼酸铵133克的水溶液950毫升浸渍3小时,120℃干燥3小时,600℃焙烧3小时,降至室温后,用含硝酸镍180克、偏钨酸铵320克水溶液900毫升浸渍4小时用相对于催化剂载体为0.1重%的偏钼酸铵(化学纯)和相对于催化剂载体为0.1重%的硝酸镍(化学纯)的混合水溶液浸渍含氟氧化铝载体4小时,120℃烘干3小时,在600℃下焙烧4小时,制得催化剂
ⅴ
。
[0133]
实施例1
[0134]
参见图3所示的流程,在提升管反应器的中型装置上进行试验。
[0135]
将1-戊烯和高温(≥650℃)催化转化催化剂
ⅰ
在第一反应区底部接触,在反应温度
700℃,反应压力0.1mpa,反应时间5秒,催化转化催化剂
ⅰ
与1-戊烯的重量比为40:1的条件下发生催化转化反应;
[0136]
将重油i与来自所述第一反应区的第一混合料流在第二反应区上游接触,得到第二反应料流,第二反应区上游的反应温度为530℃,反应压力为0.1mpa,反应时间为6秒,催化转化催化剂
ⅰ
与重油i的重量比为5:1。
[0137]
将甲醇与第二反应料流在第二反应区下游接触得到反应油气和待生催化剂,第二反应区下游的反应温度为500℃,反应压力为0.1mpa,反应时间为3秒,催化转化催化剂
ⅰ
与甲醇的重量比40:1,1-戊烯、重油i与甲醇重量之比为1:8:1。
[0138]
分离反应的反应产物和待生催化剂,将所得待生催化剂一起引入再生器烧焦再生,将所得反应产物一起引入组合分离系统,先进行第一分离处理,得到包括乙烯、丙烯、丁烯、未转化的甲醇、第一催化裂化馏分油(初馏点35℃,终馏点180℃)和第二催化裂化馏分油(初馏点180℃,终馏点510℃)等组分的产品;然后将所述第一催化裂化馏分油进行第二分离处理,分离出富含烯烃的物流,将第二催化裂化馏分油和加氢催化剂
ⅳ
在350℃,氢分压18mpa,体积空速1.5小时-1
,氢油体积比1500的条件下反应得到加氢第二催化裂化馏分油。
[0139]
将所述分离得到的富含烯烃的物流(含有80重量%的c5以上烯烃)引入第一反应区底部再裂化,反应温度为700℃,反应时间为5秒;将所述加氢第二催化裂化馏分油与重油i混合,再返回第二反应区上游继续进行反应。反应条件和产品分布列于表3。
[0140]
对比例1
[0141]
参见图3所示的流程,在提升管反应器的中型装置上进行试验。
[0142]
采用与实施例1类似的反应流程,在提升管反应器的中型装置上进行试验。所不同的是:反应原料不包含1-戊烯和甲醇,且富含烯烃的物流不返回所述装置。将重油i和催化转化催化剂
ⅰ
在第二反应区底部接触,在反应温度530℃,反应压力0.1mpa,反应时间6秒,催化转化催化剂
ⅰ
与重油i的重量比5:1下发生催化转化反应。分离反应的反应产物和待生催化剂,将所得待生催化剂一起引入再生器烧焦再生,将所得反应产物一起引入组合分离系统,先进行第一分离处理,得到包括乙烯、丙烯、丁烯、第一催化裂化馏分油(初馏点35℃,终馏点180℃)和第二催化裂化馏分油(初馏点180℃,终馏点510℃)等组分的产品。然后将第二催化裂化馏分油和加氢催化剂
ⅳ
在350℃,氢分压18mpa,体积空速1.5小时-1
,氢油体积比1500的条件下反应得到加氢第二催化裂化馏分油。将所得到的加氢第二催化裂化馏分油与重油i混合,再返回第二反应区上游进行反应。反应条件和产品分布列于表3。
[0143]
实施例2
[0144]
参见图3所示的流程,在提升管反应器的中型装置上进行试验。采用与实施例1类似的反应流程,所不同的是:不外加1-戊烯。
[0145]
将重油i和催化转化催化剂
ⅰ
在第二反应区上游接触,在反应温度530℃,反应压力0.1mpa,反应时间6秒,催化转化催化剂
ⅰ
与重油i的重量比5:1下发生催化转化反应,得到第二反应料流。将甲醇与第二反应料流在第二反应区下游接触,在反应温度500℃,反应压力0.1mpa,反应时间3秒,催化转化催化剂
ⅰ
与甲醇的重量比40:1条件下发生催化转化反应,重油i与甲醇重量之比为8:1。
[0146]
分离反应的反应产物和待生催化剂,将所得待生催化剂一起引入再生器烧焦再
生,将所得反应产物一起引入组合分离系统,先进行第一分离处理,得到包括乙烯、丙烯、丁烯、未转化的甲醇、第一催化裂化馏分油(初馏点35℃,终馏点180℃)和第二催化裂化馏分油(初馏点180℃,终馏点510℃)等组分的产品;然后将所述第一催化裂化馏分油进行第二分离处理,分离出富含烯烃的物流,将所述第二催化裂化馏分油和加氢催化剂
ⅳ
在350℃,氢分压18mpa,体积空速1.5小时-1
,氢油体积比1500的条件下反应得到加氢第二催化裂化馏分油。
[0147]
将所述分离得到的未转化的甲醇引入第二反应区下游继续反应;将分离得到的富含烯烃的物流(含有80重量%的c5以上烯烃)引入第一反应区底部再裂化,反应温度为700℃,反应时间为5秒;将所述加氢第二催化裂化馏分油与重油i混合,再返回第二反应区上游继续进行反应。反应条件和产品分布列于表3。
[0148]
对比例2
[0149]
在提升管反应器的中型装置上进行试验,重油i与催化转化催化剂
ⅱ
在提升管底部接触,在反应温度为610℃,催化转化催化剂
ⅱ
与重油i的重量比为16.9:1,反应压力为0.1mpa,反应时间6秒下发生催化转化反应,产物不进行加氢处理和继续反应。反应条件和产品分布列于表3。
[0150]
实施例3
[0151]
与实施例2基本相同,不同之处在于采用重油ii。第一分离处理得到的第二催化裂化馏分油(初馏点180℃,终馏点510℃)不进行深度加氢处理,而是在加氢脱硫反应器内与加氢脱硫催化剂
ⅴ
接触,在反应压力6.0mpa、反应温度350℃、氢油体积比350、体积空速2.0小时-1
下反应,得到低硫加氢第二催化裂化馏分油,与重油ii混合后返回第二反应区上游继续反应。反应条件和产品分布列于表3。
[0152]
对比例3
[0153]
在提升管反应器的中型装置上进行试验,重油ⅱ和催化转化催化剂
ⅲ
在提升管底部接触,在反应温度为530℃,催化转化催化剂
ⅲ
与重油ⅱ的重量比为5:1,反应压力0.1mpa,反应时间6秒下发生催化转化反应,加氢脱硫处理与实施例3基本相同。反应条件和产品分布列于表3。
[0154]
实施例4
[0155]
参见图1所示的流程,在提升管反应器的中型装置上进行试验。
[0156]
将1-戊烯和高温(≥650℃)催化转化催化剂
ⅰ
在第一反应区底部接触,在反应温度600℃,反应压力0.1mpa,反应时间5秒,催化转化催化剂
ⅰ
与1-戊烯的重量比为40:1的条件下发生催化转化反应;
[0157]
将重油i与甲醇一同与来自所述第一反应区的第一混合料流在第二反应区底部接触,重油i和甲醇共同与催化转化催化剂
ⅰ
在反应温度530℃,反应压力0.1mpa,反应时间6秒,催化转化催化剂
ⅰ
与重油i的重量比为5:1;催化剂与甲醇的重量比为40:1条件下发生催化转化反应。重油i与甲醇重量之比为8:1。
[0158]
分离反应的反应产物和待生催化剂,将所得待生催化剂一起引入再生器烧焦再生,将所得反应产物一起引入组合分离系统,先进行第一分离处理,得到包括乙烯、丙烯、丁烯、未转化的甲醇、第一催化裂化馏分油(初馏点35℃,终馏点300℃)和第二催化裂化馏分油(初馏点300℃,终馏点510℃)等组分的产品;然后将所述第一催化裂化馏分油进行第三
分离处理,分离出小分子烯烃物流(初馏点35℃,终馏点160℃)、大分子烯烃物流(初馏点160℃,终馏点300℃),将第二催化裂化馏分油和加氢催化剂
ⅳ
在350℃,氢分压18mpa,体积空速1.5小时-1
,氢油体积比1500的条件下进行加氢处理,得到加氢第二催化裂化馏分油。
[0159]
将所述分离得到的小分子烯烃物流(含有80重量%的c5-c9的烯烃)引入第一反应区底部再裂化,反应温度为600℃,反应时间为5秒;将分离得到的所述大分子烯烃物流(含有80重量%的c10-c18的烯烃)与所述未转化的甲醇混合后,再返回第二反应区底部继续反应;将所述加氢第二催化裂化馏分油与重油i混合,再引入催化转化反应器的第二反应区底部继续进行反应。反应条件和产品分布列于表3。
[0160]
实施例5
[0161]
参见图2所示的流程,在提升管反应器的中型装置上进行试验。
[0162]
将1-戊烯和高温(≥650℃)催化转化催化剂
ⅰ
在第一反应区底部接触,在反应温度700℃,反应压力0.1mpa,反应时间5秒,催化剂与1-戊烯的重量比为40:1的条件下发生催化转化反应;
[0163]
将重油i与来自所述第一反应区的第一混合料流在第二反应区上游接触,重油i和催化转化催化剂
ⅰ
在反应温度530℃,反应压力0.1mpa,反应时间6秒,催化剂与重油i的重量比5:1条件下发生催化转化反应,得到第二混合料流。
[0164]
将甲醇与第二混合料流在第二反应区下游接触,和催化转化催化剂
ⅰ
在反应温度500℃,反应压力0.1mpa,反应时间3秒,催化转化催化剂
ⅰ
与甲醇的重量比40:1条件下发生催化转化反应,1-戊烯、重油i与甲醇重量之比为1:8:1。
[0165]
分离反应的反应产物和待生催化剂,将所得待生催化剂一起引入再生器烧焦再生,将所得反应产物一起引入组合分离系统,先进行第一分离处理,得到包括乙烯、丙烯、丁烯、未转化的甲醇、第一催化裂化馏分油(初馏点35℃,终馏点300℃)和第二催化裂化馏分油(初馏点300℃,终馏点510℃)等的产品;然后将使所述第一催化裂化馏分油进行第三分离处理,分离出小分子烯烃物流(初馏点35℃,终馏点160℃)、大分子烯烃物流(初馏点160℃,终馏点300℃);将所述第二催化裂化馏分油和加氢催化剂
ⅳ
在350℃,氢分压18mpa,体积空速1.5小时-1
,氢油体积比1500的条件下进行加氢处理,得到加氢第二催化裂化馏分油。
[0166]
将所述分离得到的小分子烯烃物流(含有80重量%的c5-c9的烯烃)引入第一反应区底部再裂化,反应温度为700℃,反应时间为5秒;将分离得到的所述未转化的甲醇返回第二反应区下游继续反应;将所述大分子烯烃物流(含有80重量%的c10-c18的烯烃)返回第二反应区上游继续进行反应;将所述加氢第二催化裂化馏分油与重油i混合后,再返回第二反应区上游继续进行反应。反应条件和产品分布列于表3。
[0167]
表3
[0168][0169]
根据表3可以看出,与对比例1-3相比,本技术实施例1-5提供的催化转化方法具有更高的乙烯、丙烯和丁烯产率,三种烯烃总产率可达到60%以上;并且原料烯烃含量越多效果越好,当以100%烯烃含量的1-戊烯作为富含烯烃的原料时,实施例1所得产品中乙烯含量为15.31%,丙烯含量为29.26%,丁烯含量为22.00%,三者的总含量高达66.57%。
[0170]
进一步地,当采用图2所示的催化转化方法,实施例5所得产品中乙烯含量为17.48%,丙烯含量为31.66%,丁烯含量为19.96%,三者的总含量高达69.10%。
[0171]
实施例6
[0172]
参见图4所示的流程,在提升管反应器的中型装置上进行试验。
[0173]
将重油i与甲醇一同和来自所述第一反应区的第一混合料流在第二反应区底部接触,重油i和甲醇共同与催化转化催化剂
ⅰ
在反应温度530℃,反应压力0.1mpa,反应时间4秒,催化转化催化剂
ⅰ
与重油i的重量比为5:1;催化转化催化剂
ⅰ
与甲醇的重量比为40:1条件下发生催化转化反应。重油i与甲醇重量之比为8:1。
[0174]
分离反应的反应产物和待生催化剂,将所得待生催化剂一起引入再生器烧焦再生,将所得反应产物一起引入组合分离系统,先进行第一分离处理,得到包括乙烯、丙烯、丁烯、未转化的甲醇、第一催化裂化馏分油(初馏点35℃,终馏点180℃)和第二催化裂化馏分油(初馏点180℃,终馏点510℃)等组分的产品;然后将所述第一催化裂化馏分油引入烯烃分离装置进行第二分离处理,分离出富含烯烃的物流,将所述第二催化裂化馏分油和加氢催化剂
ⅳ
在350℃,氢分压18mpa,体积空速1.5小时-1
,氢油体积比1500的条件下进行加氢处理,得到加氢第二催化裂化馏分油。
[0175]
将所述分离得到的富含烯烃的物流(含有80重量%的c5以上烯烃)引入第一反应区底部再裂化,反应温度为700℃,反应时间为5秒;将所述加氢第二催化裂化馏分油与重油i混合,再返回第二反应区底部继续进行反应。所述分离得到的丁烯引入第一反应区底部再裂化(沿物料流动方向,丁烯的引入位置位于所述富含烯烃的物流引入位置的上游),反应温度为650℃,催化剂i与丁烯的重量比为100:1,反应时间为0.2s。
[0176]
本实施例所得产物中,乙烯收率为24.44%,丙烯收率为31.87%,氢气+甲烷+乙烷收率仅为3.91%,进一步提高了乙烯和丙烯产率。
[0177]
以上详细描述了本公开的优选实施方式,但是,本公开并不限于上述实施方式中的具体细节,在本公开的技术构思范围内,可以对本公开的技术方案进行多种简单变型,这些简单变型均属于本公开的保护范围。
[0178]
另外需要说明的是,在上述具体实施方式中所描述的各个具体技术特征,在不矛盾的情况下,可以通过任何合适的方式进行组合。为了避免不必要的重复,本公开对各种可能的组合方式不再另行说明。
[0179]
此外,本公开的各种不同的实施方式之间也可以进行任意组合,只要其不违背本公开的思想,其同样应当视为本公开所公开的内容。