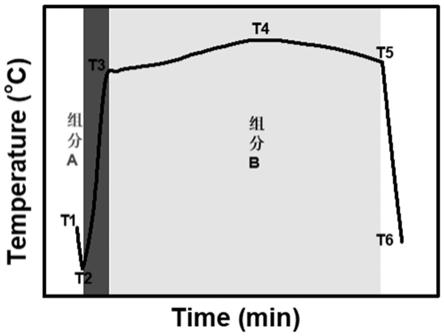
1.本发明涉及一种高性能聚烯烃材料的合成方法,属于合成树脂行业聚烯烃技术领域。
背景技术:2.聚烯烃塑料即烯烃的聚合物,是通用塑料的一种,它主要包括聚乙烯(pe)、聚丙烯(pp)、热塑性弹性体(poe)、乙烯
‑
醋酸乙烯酯共聚物(eva)等,是一类产量大、应用范围极广的高分子材料。聚烯烃材料在日常生活中以各种形式被广泛生产、加工、制造和使用,被广泛应用在如城市燃气管道、水管管道、填料膜、建筑材料等领域。目前,高端聚乙烯产品的国内外市场前景良好,尤其是在板材、管材、薄膜、电缆等行业中的需求十分旺盛,虽然高端聚乙烯产品的供应量逐年增加,但是仍然供不应求。国内外聚烯烃产品的生产工艺,可以采用双/多聚合反应釜串联工艺、双/多聚合反应釜并联工艺,也可以采用单一聚合反应釜工艺。
3.现有技术中,专利申请cn201180009019.7公开了一种在至少二个串联的淤浆环流反应器中生产用于吹塑应用的双峰聚乙烯共混物,其中一个反应器产生高分子量聚乙烯,另一个反应器产生低分子量聚乙烯的方法;其中,高分子量聚乙烯密度为0.925
‑
0.942克/立方厘米,低分子量聚乙烯的密度为0.960
‑
0.975克/立方厘米,双峰分布聚乙烯产品的密度为0.935
‑
0.960克/立方厘米。专利申请cn201280021440.4公开了一种使用齐格勒
‑
纳塔催化剂在环管反应器中单独制备两种分子量聚乙烯树脂的方法,随后将制备的聚乙烯树脂进行物理共混得到多峰聚乙烯共混物。专利申请cn201310311017.4公开了一种单反应器制备宽/双峰聚乙烯的方法,其采用二氯化锆为第一催化剂、茂金属催化剂为第二催化剂组成的串联配位金属催化体系,在单一聚合反应釜内制备宽/双峰聚乙烯的方法。由此可以看出,高性能聚烯烃共混物的生产大多采用双/多反应器串联/并联工艺或者采用双/多种活性中心复合联用催化剂的方法。如专利申请cn201180009019.7和cn201280021440.4公开的采用双聚合反应釜串联工艺,由于反应物料需要经过二个串联聚合反应釜才能生产出聚乙烯共混物,因此该工艺存在设备尺寸大、工程投资多、运行成本高、操作流程复杂等显著问题。专利申请cn201010515067.0和cn201310311017.4虽然采用工艺流程简单的单一聚合反应釜工艺制备双峰聚乙烯产品,但是存在催化体系复杂、催化剂制备条件苛刻、聚合工艺操作难度大、运行过程热稳定性差的问题。
4.出于上述问题的考虑,本发明的发明人进行了研究,目的是解决相关领域现有技术所暴露出来的问题,期望提供一种利用单反应器的预聚合升温热效应,在单反应器内实现高性能聚烯烃共混物的两段法序贯聚合,以缩短生产流程,该工艺具有流程简单、设备投资成本低、改造简单、对催化剂适用性广等显著优点,聚烯烃共混产物具有显著增强的冲击性能、耐环境应力开裂性能、挠曲度、拉伸强度和拉伸模量等特点。特别地,本发明尤其适用于活性释放快速且活化期极短的聚烯烃催化剂。本发明另一特点在于在聚合过程中预聚阶段并未加入分子量调节剂、而在第二阶段加入分子量调节剂,即后加氢生产技术。这种后加
氢生产工艺可以减少分子量调节剂分离回收装置的设备投资、提高乙烯单程转化率,进一步降低生产成本和设备投资。
技术实现要素:5.鉴于以上现有技术的不足,本发明的目的之一在于提供一种在单反应器内高效制备高性能聚烯烃共混物的方法。该制备方法能够解决现有聚烯烃共混物制备工艺中存在的工艺流程长、设备投资大、运行成本高的问题。这一单反应器聚合工艺具有生产效率高、切换操作简单、流程短、设备投入低、能耗低等优点,可以高效制备高性能聚烯烃共混物。这些聚烯烃共混物可以采用常规的双螺杆挤出、注塑或吹塑等加工工艺进行加工处理,并且加工后的产品在强度/刚性/韧性等方面都具有明显的提升,如具有显著增强的冲击性能、耐环境应力开裂性能、挠曲度、拉伸强度和拉伸模量等特点。
6.本发明所述的单反应器内两段法工艺制备高性能聚烯烃共混物的方法,有别于现有生产工艺中的双/多反应器串联,结合生产工艺参数的特点,利用第一段反应时间短、聚合放热量大且释放快的特点,能够将反应器内物系温度显著提升、并且在第一段聚合反应中并未加入任何分子量调节剂,催化剂活性释放速率快,能够制备分子量较高、支链含量较高且能够宽幅调节的聚烯烃组分a,并且能够在短时间内将物系温度提升至第二段聚合反应所需温度附近,再加入适量的分子量调节剂,可以制备分子量较低、支链含量也较低、加工性能良好的聚烯烃组分b,聚烯烃组分a和聚烯烃组分b共同构成了高性能聚烯烃共混产物。同时,由于聚烯烃组分a的生产过程为升温过程,支链更倾向于分布在聚合反应初期低温条件下制备的高分子量部分,从而实现了支链分布向高分子量聚烯烃部分的集中,而共聚单体随着聚合反应的进行,浓度显著降低、低分子量聚烯烃部分的支链分布随着聚合反应进行逐渐降低,这种支链不均匀分布(向高分子量部分聚集)的聚烯烃产物具有更强的力学性能、耐环境应力开裂性能escr和耐温性能,可以开发出性能更加优异的pe100、pe112和pe125高性能聚乙烯管材料。本发明另一特点在于在聚合过程中预聚阶段并未加入分子量调节剂、而在第二阶段加入分子量调节剂,即后加氢生产技术。这种后加氢生产工艺可以减少分子量调节剂分离回收装置的设备投资、提高乙烯单程转化率,进一步降低生产成本和设备投资。
7.本发明所述的单反应器内两段法工艺制备高性能聚烯烃共混物的方法,尤其适用于活性释放快速且稳定、活化期极短的聚烯烃催化剂。在传统的双/多反应器串联生产工艺中,由于催化剂不同活性中心的特点(生产低分子量的活性中心聚合时间短、易失活,生产高分子量的活性中心聚合时间长),第一反应器内往往在较高温度下生产低分子量聚乙烯组分,第二反应器内往往在较低温度下生产高分子量聚乙烯组分。釜内物系从高温条件向低温条件的迅速切换可以通过反应器的强撤热实现,而反应器内物系的快速升温却难以实现(受限于反应器外循环升温较慢,在现有工业条件下无法实现)。而对于活性释放快速且稳定、活化期极短的聚烯烃催化剂,在聚合反应初期会产生大量聚合热,且反应器(尤其是釜式反应器)撤热能力有限。因此,本发明通过在单反应器内聚合热效应的快速升温(即预聚热效应),实现低温和高温两种聚合条件的无缝切换连续操作。同时,由于在聚合反应末期的出料处理,可以迅速撤除大量反应热,满足高温向低温条件的迅速切换,从而可以进行下一步聚合(即下一段预聚),从而实现单反应器内两段法工艺的连续化生产。由此可见,本
发明所述的单反应器内两段法工艺可以适用于间歇法生产,也可以适用于连续化生产。
8.根据本发明的一个方面,本发明提供了一种单反应器内两段法工艺高效制备高性能聚烯烃共混物的方法,其利用单反应器内的“预聚升温效应”高效制备生产技术,具体包括如下步骤和特征:
9.1)在单反应器内和预设温度t1及压力p1下(预设条件r1),加入溶剂、共聚单体和助催化剂组分,待反应器内物系的温度和压力达到预设温度t2及压力p2时(预设条件r2),通入主催化剂和烯烃单体,预聚反应开始,聚合温度及压力指标在聚合热和反应器内/外循环撤热的共同作用下,即预聚热效应作用下,经过一段时间t1逐步达到预设温度t3及压力p3(预设条件r3),在聚合时间t1内聚合生成聚烯烃组分a;
10.2)预聚热效应作用结束后,再次向反应器内通入聚合组分,聚合组分至少包括乙烯单体和分子量调节剂(根据需要,还可加入共聚单体及其他组分),聚合温度和聚合压力升高至预设温度t4及压力p4(预设条件r4),聚合温度在达到t4后缓慢降低或保持不变,经过聚合时间t2至预设温度t5,物系压力保持不变(预设条件r5),在聚合时间t2内聚合生成聚烯烃组分b,聚合时间达到t1+t2后,反应器内产物出料得到两组分a/b比例可调的高性能聚烯烃共混物,反应器温度和压力随出料降低,达到预设温度t6及压力p6(预设条件r6);
11.在本发明中,相较于预设条件r1,物系温度t2因冷物料加入有所降低,物系压力p2有所略微提升。相较于预设条件r3,物系温度t4略微升高,聚合压力p4保持不变或者稍许提高。相较于预设条件r4,物系温度t5缓慢降低或保持不变,物系压力p5保持不变。相较于预设条件r5,物系温度t6因为出料显著降低,物系压力p6也降低至略高于常压。
12.根据本发明的一些实施方式,步骤1)中预设温度t2和预设温度t3的范围为10
‑
90℃,优选为30
‑
80℃,更优选为35
‑
78℃;步骤2)中预设温度t4和预设温度t5的范围为60
‑
110℃,优选为65
‑
100℃,更优选为70
‑
90℃;预设温度t1的温度范围为15
‑
90℃,优选为25
‑
80℃,更优选为40
‑
65℃;预设温度t6的温度范围为15
‑
90℃,优选为25
‑
80℃,更优选为40
‑
65℃;预设温度t3和预设温度t4的温差为5
‑
35℃,优选为7
‑
30℃,更优选为9
‑
25℃;预设温度t2和预设温度t3的温差为15
‑
60℃,优选为20
‑
50℃,更优选为25
‑
45℃。
13.根据本发明的一些实施方式,步骤1)中预设压力p1和预设压力p2的范围为1.01
‑
2.00bar,优选为1.01
‑
1.6bar,更优选为1.03
‑
1.4bar;预设压力p3的范围为3.0
‑
15.0bar,优选为4
‑
12bar,更优选为4.5
‑
10bar;步骤2)中预设压力p4和预设压力p5的范围为3
‑
18bar,优选为4
‑
15bar,更优选为4.5
‑
12bar;预设压力p6的范围为1.01
‑
3.00bar,优选为1.05
‑
2.5bar,更优选为1.1
‑
2.0bar。
14.在本发明的一种优选实施方式中,上述步骤1)和步骤2)为单组单反应器内两段法聚合生产工序,具有间歇法操作的特征。在此基础上,可以进一步控制预设条件r1与r6相当,从而使多个单组生产工序可以串联使用,结合成为单反应器的两段法多组连续生产工艺,具有连续法操作的特征。本发明中两段法工艺的物系温度和压力变化详见温度和压力示意图(见图1和图2)、乙烯流量动力学曲线示意图见图3。
15.根据本发明的一个实施例,所述聚合时间t2内聚合活性显著低于在聚合时间t1内的聚合活性,第二段聚合的热效应显著低于第一段的热效应,详细地,聚合时间t2内的单位时间平均聚合活性与聚合时间t1内的单位时间平均聚合活性的比值控制在1:1.5
‑
1:15,优选为1:2
‑
1:10。
16.根据本发明的一个实施例,所述聚合单体为乙烯,共聚单体为丙烯、1
‑
丁烯、1
‑
戊烯、1
‑
己烯、1
‑
庚烯、1
‑
辛烯、1
‑
壬烯、1
‑
癸烯、丁二烯、戊二烯、己二烯、苯乙烯中的一种或多种。
17.根据本发明的一个实施例,所述步骤(1)中主催化剂为茂金属催化剂、铬系催化剂、fi催化剂、ziegler
‑
natta催化剂、后过渡金属催化剂中的一种或多种;助催化剂为甲基铝氧烷、改性甲基铝氧烷、三乙基铝、三异丁基铝、氯化二乙基铝、二氯乙基铝、三丁基铝、三己基铝、三辛基铝、有机硼化物中的一种或多种。其中,助催化剂和主催化剂的摩尔比范围为1
‑
3000,优选为2
‑
2000,更优选为2
‑
1500。
18.根据本发明的一个实施例,所述聚合溶剂为1
‑
戊烷、1
‑
己烷、1
‑
庚烷、1
‑
辛烷、1
‑
壬烷、2
‑
甲基戊烷、3
‑
甲基戊烷、2
‑
甲基己烷、3
‑
甲基己烷、甲苯等线性或异构烷烃中的一种或多种。
19.根据本发明的一个实施例,所述第一段聚合时间t1占聚合总时间(t1+t2)的比例为5%
‑
30%,优选为5.5%
‑
25%,更优选为6%
‑
22%,以保证聚合热的快速释放并迅速提高聚合温度,从而形成聚合温度提升和聚合热释放的正向反馈,形成预聚升温效应。
20.根据本发明的一个实施例,所述步骤2)中加入的分子量调节剂选自氢气、氧气、丙烯、丁烯中的一种或多种,并且分子量调节剂与乙烯单体的分压比范围为0.02
‑
0.7,优选为0.05
‑
0.5,更优选为0.08
‑
0.45。
21.根据本发明的一个实施例,所述聚烯烃组分a和聚烯烃组分b的分子量差别较大,聚烯烃组分a的分子量分布于10000
‑
10000000g/mol,优选为4000
‑
8000000g/mol,聚烯烃组分b的分子量分布于1000
‑
500000g/mol,优选为1200
‑
350000g/mol。聚烯烃组分a和聚烯烃组分b的支链含量也有较大差别,聚烯烃组分a的支链含量占总支链含量的50
‑
96%,优选为60
‑
90%,更优选为65
‑
88%;且受益于预聚热效应温度的显著提升,链转移速率提升显著,聚烯烃组分a的支链含量可以根据不同催化剂类型具有更宽的调控范围,共聚单体支链更加倾向于分布在高分子量的聚乙烯链段上,这种聚烯烃共混物产物(a+b)具有显著增强的冲击性能、耐环境应力开裂性能、挠曲度、拉伸强度和拉伸模量。
附图说明
22.为了更清楚地说明本发明实施例中的技术方案,下面将对实施例描述中所需要使用的附图做简单地介绍,显而易见,下面简述中的附图仅仅是本发明的一些实施例,对于本领域普通技术人员来讲,在不付出创造性劳动的前提下,还可以根据这些附图获得其他的附图。
23.图1表示本发明方法的一个实施例中物系温度变化曲线;
24.图2表示本发明方法的一个实施例中物系压力变化曲线;
25.图3表示本发明方法的一个实施例中聚合活性变化曲线;
26.图4表示本发明方法的一个实施例中聚烯烃产物的分子量分布及支链分布。
27.具体实施方法
28.下面将结合实施例对本发明的实施方案进行详细描述,但是本领域技术人员将会理解,下列实施例仅用于说明本发明,而不应视为限定本发明的范围。实施例中未注明具体条件者,按照常规条件或制造商建议的条件进行。所用试剂或仪器未注明生产厂商者,均为
可以通过市购获得的常规产品。
29.聚合物结构及性能的表征方法:
30.(1)熔融指数:根据gb/t
‑
3682
‑
2000条件(190℃、2.16kg的负荷)测定熔体流动速率,通常记为mi2.16。
31.(2)密度:根据gb/1033
‑
1986方法测定。
32.(3)拉伸强度、杨氏模量和断裂伸长率:根据gb/t 1040
‑
2006测定。
33.(4)冲击强度:根据gb/t 1843
‑
2008测定。
34.(5)重均分子量:采用高温渗透凝胶色谱ht
‑
gpc测定。
35.(6)共聚单体插入率:根据
13
c
‑
nmr测定并计算。
36.(7)耐环境应力开裂性能:根据gb/t 1842
‑
2008测定。
37.实施例1
38.在单个500l反应釜内,通过釜内夹套升温/撤热,将反应釜内温度提升至41℃,釜内压力为1.08bar,依次加入300l己烷/戊烷/庚烷(1:1:1)混合溶剂、100ml1
‑
己烯共聚单体和250ml的0.8mol/l三乙基铝助催化剂,釜内温度降至37℃,压力为1.1bar,再通入1.5g商业ziegler
‑
natta主催化剂(助催化剂与主催化剂的摩尔比为80)和乙烯单体,第一段聚合开始进行,聚合时间控制为30min,釜内物系温度迅速提升至78℃,乙烯分压提升至5.2bar,这一阶段制备高分子量的聚烯烃组分a达14kg(以流量计计算);在预聚热效应后期,向反应釜内通入3.0bar的分子量调节剂氢气,随后立即充入乙烯单体至物系总压11.8bar,聚合温度缓慢升高至87℃,在此阶段,生成低分子量低支化度的聚烯烃组分b达46kg(以流量计计算),聚合时间控制为230min,物系温度降低至82℃,物系压力保持11.8bar不变。最后,聚烯烃共混产物出料,反应釜内物系温度降低至57℃,物系压力降低至1.2bar。该聚合反应的聚合参数详见表1。聚烯烃组分a、组分b和共混物的各项物性(分子量、支链分布、支链含量、熔融指数和力学性能)详见表6。本实施例采用间歇法进行生产。
39.表1单反应器聚合参数
[0040][0041][0042]
实施例2
[0043]
在单个500l反应釜内,通过釜内夹套升温/撤热,将反应釜内温度提升至55℃,釜
内压力为1.33bar,依次加入320l己烷/戊烷/庚烷(1:2:1)混合溶剂、85ml1
‑
己烯共聚单体和320ml的0.8mol/l三乙基铝助催化剂,釜内温度降至43℃,压力为1.28bar,再通入1.3g商业ziegler
‑
natta主催化剂(助催化剂与主催化剂的摩尔比为140)和乙烯单体,第一段聚合开始进行,聚合时间控制为25min,釜内物系温度迅速提升至75℃,乙烯分压提升至6.7bar,这一阶段制备高分子量的聚烯烃组分a达12kg(以流量计计算);在预聚热效应后期,向反应釜内通入3.2bar的分子量调节剂氢气,随后立即充入乙烯单体至物系总压11.3bar,聚合温度缓慢升高至89℃,在此阶段,生成低分子量低支化度的聚烯烃组分b达45kg(以流量计计算),聚合时间控制为250min,物系温度降低至84℃,物系压力保持11.3bar不变。最后,聚烯烃共混产物出料,反应釜内物系温度降低至55℃,物系压力降低至1.26bar。该聚合反应的聚合参数详见表2。聚烯烃组分a、组分b和共混物的各项物性(分子量、支链分布、支链含量、熔融指数和力学性能)详见表6。本实施例采用间歇法进行生产。
[0044]
表2单反应器聚合参数
[0045][0046]
实施例3
[0047]
在单个500l反应釜内,通过釜内夹套升温/撤热,将反应釜内温度提升至64℃,釜内压力为1.38bar,依次加入320l己烷/戊烷/庚烷(1:2:2)混合溶剂、80ml1
‑
己烯共聚单体和330ml的0.8mol/l三乙基铝助催化剂,釜内温度降至48℃,压力为1.32bar,再通入1.35g改进的商业ziegler
‑
natta主催化剂(助催化剂与主催化剂的摩尔比为120)和乙烯单体,第一段聚合开始进行,聚合时间控制为35min,釜内物系温度迅速提升至82℃,乙烯分压提升至4.5bar,这一阶段制备高分子量的聚烯烃组分a达15kg(以流量计计算);在预聚热效应后期,向反应釜内通入3.3bar的分子量调节剂氢气,随后立即充入乙烯单体至物系总压11.9bar,聚合温度缓慢升高至89℃,在此阶段,生成低分子量低支化度的聚烯烃组分b达60kg(以流量计计算),聚合时间控制为280min,物系温度降低至85℃,物系压力保持11.9bar不变。最后,聚烯烃共混产物出料,反应釜内物系温度降低至61℃,物系压力降低至1.16bar。该聚合反应的聚合参数详见表3。聚烯烃组分a、组分b和共混物的各项物性(分子量、支链分布、支链含量、熔融指数和力学性能)详见表6。本实施例采用间歇法进行生产。
[0048]
表3单反应器聚合参数
[0049][0050]
实施例4
[0051]
在单个500l反应釜内,通过釜内夹套升温/撤热,将反应釜内温度提升至49℃,釜内压力为1.25bar,依次加入300l己烷/戊烷/庚烷(1:1:2)混合溶剂、100ml1
‑
己烯共聚单体和230ml的0.8mol/l三乙基铝助催化剂,釜内温度降至44℃,压力为1.23bar,再通入1.38g商业ziegler
‑
natta主催化剂(助催化剂与主催化剂的摩尔比为110)和乙烯单体,第一段聚合开始进行,聚合时间控制为23min,釜内物系温度迅速提升至78℃,乙烯分压提升至5.3bar,这一阶段制备高分子量的聚烯烃组分a达16kg(以流量计计算);在预聚热效应后期,向反应釜内通入2.5bar的分子量调节剂氢气,随后立即充入乙烯单体至物系总压10.7bar,聚合温度缓慢升高至85℃,在此阶段,生成低分子量低支化度的聚烯烃组分b达57kg(以流量计计算),聚合时间控制为260min,物系温度降低至84℃,物系压力保持10.7bar不变。最后,聚烯烃共混产物出料,反应釜内物系温度降低至52℃,物系压力降低至1.22bar。该聚合反应的聚合参数详见表4。聚烯烃组分a、组分b和共混物的各项物性(分子量、支链分布、支链含量、熔融指数和力学性能)详见表6。本实施例采用连续法进行生产,后续的温度、压力、氢气加入量、共聚单体加入量、助催化剂加入量、催化剂加入量、溶剂加入量等均见表4。
[0052]
表4单反应器聚合参数
[0053][0054]
实施例5
[0055]
在单个500l反应釜内,通过釜内夹套升温/撤热,将反应釜内温度提升至53℃,釜内压力为1.12bar,依次加入350l己烷/戊烷/庚烷(1:1:1)混合溶剂、140ml1
‑
己烯共聚单体、30ml1
‑
辛烯共聚单体和290ml的0.8mol/l三乙基铝助催化剂,釜内温度降至46℃,压力为1.06bar,再通入1.55g商业ziegler
‑
natta主催化剂(助催化剂与主催化剂的摩尔比为140)和乙烯单体,第一段聚合开始进行,聚合时间控制为26min,釜内物系温度迅速提升至76℃,乙烯分压提升至5.5bar,这一阶段制备高分子量的聚烯烃组分a达20kg(以流量计计算);在预聚热效应后期,向反应釜内通入3.6bar的分子量调节剂氢气,随后立即充入乙烯单体至物系总压11.7bar,聚合温度缓慢升高至88℃,在此阶段,生成低分子量低支化度的聚烯烃组分b达77kg(以流量计计算),聚合时间控制为250min,物系温度降低至85℃,物系压力保持11.7bar不变。最后,聚烯烃共混产物出料,反应釜内物系温度降低至52℃,物系压力降低至1.15bar。该聚合反应的聚合参数详见表5。聚烯烃组分a、组分b和共混物的各项物性(分子量、支链分布、支链含量、熔融指数和力学性能)详见表6。本实施例采用连续法进行生产,后续的温度、压力、氢气加入量、共聚单体加入量、助催化剂加入量、催化剂加入量、溶剂加入量等均见表5。
[0056]
表5单反应器聚合参数
[0057][0058]
对比例1
[0059]
本实施例采用双反应器串联工艺连续法生产聚烯烃共混物,在第一个500l反应釜内,先后加入300l己烷/戊烷/庚烷(1:1:1)混合溶剂、1.5bar分子量调节剂氢气、250ml的0.8mol/l三乙基铝助催化剂、1.1g商业ziegler
‑
natta主催化剂(助催化剂与主催化剂的摩尔比为120)和乙烯单体,物系聚合温度为92℃,物系聚合压力为5.1bar,聚合时间控制为18min,这一阶段制备低分子量的聚烯烃组分a达52kg(以流量计计算),随后反应体系通过分离装置分离出98.5%的分子量调节剂氢气,再转移入第二个600l反应釜内,并加入160ml1
‑
己烯共聚单体和乙烯单体,物系聚合温度为74℃,物系聚合压力为6.5bar,聚合时间控制为230min,这一阶段制备高分子量的聚烯烃组分b达78kg(以流量计计算),最后,聚烯烃共混产物出料并后处理。聚烯烃组分a、组分b和共混物的各项物性(分子量、支链分布、支链含量、熔融指数和力学性能)详见表6。本对比例中的分离装置不仅包括氢气分离装置,还包括后续的乙烯、溶剂组分、氮气等回收循环利用装置。
[0060]
表6聚烯烃共混物各项物性指标
[0061][0062]
实施例1
‑
5和对比例1中的聚合过程及聚合装置进行对比,可以发现本发明所采用的单反应器内两段法工艺,利用预聚热效应先生产高分子量高支化度的聚烯烃组分a,再在高温及分子量调节剂的环境下生产低分子量低支化度的聚烯烃组分b的方法,可以极大地缩短工艺流程,减少反应器、分离装置等各种物质分离和循环回收装置的数量,减少设备的投资。同时,本发明所述的聚合工艺具有流程短、产品切换迅速等优点,比较适合于小批量高附加值聚烯烃产品的生产。特别地,本发明所述的聚合工艺尤其适用于活性释放快速且稳定、活化期极短的聚烯烃催化剂。
[0063]
从表6中聚烯烃共混物各项物性指标可以发现,实施例1
‑
5中所采用的单反应器内两段法工艺,无论是间歇法生产(实施例1
‑
3)还是连续法生产(实施例4
‑
5),均可以制备出高分子量高支化度的聚烯烃组分a和低分子量低支化度的聚烯烃组分b。最终的聚烯烃共混物(a+b)产品呈现出拉伸强度高、拉伸模量高、断裂伸长率高和冲击强度高的特点。这主要是由于本发明所采用的单反应器内两段法工艺,利用预聚热效应生产的高分子量高支化度聚烯烃组分a是在温度不断升高和压力不断升高的条件下聚合得到的,聚烯烃组分a内随着聚合温度升高、分子量逐渐下降、且共聚单体浓度也会下降,即聚烯烃组分a内的共聚单体更加倾向于分布在更高分子量的聚乙烯链上。根据本领域专业人员的基本知识,这种共聚单体更加集中在高分子量聚乙烯链段的聚烯烃产物具有更多的系带分子结构(如图4),可以极大的增强产物的力学性能,尤其是耐环境应力开裂性能(escr)。采用这种聚合方法,可
以开发出性能更加优异的pe100、pe112和pe125高性能聚乙烯管材料。