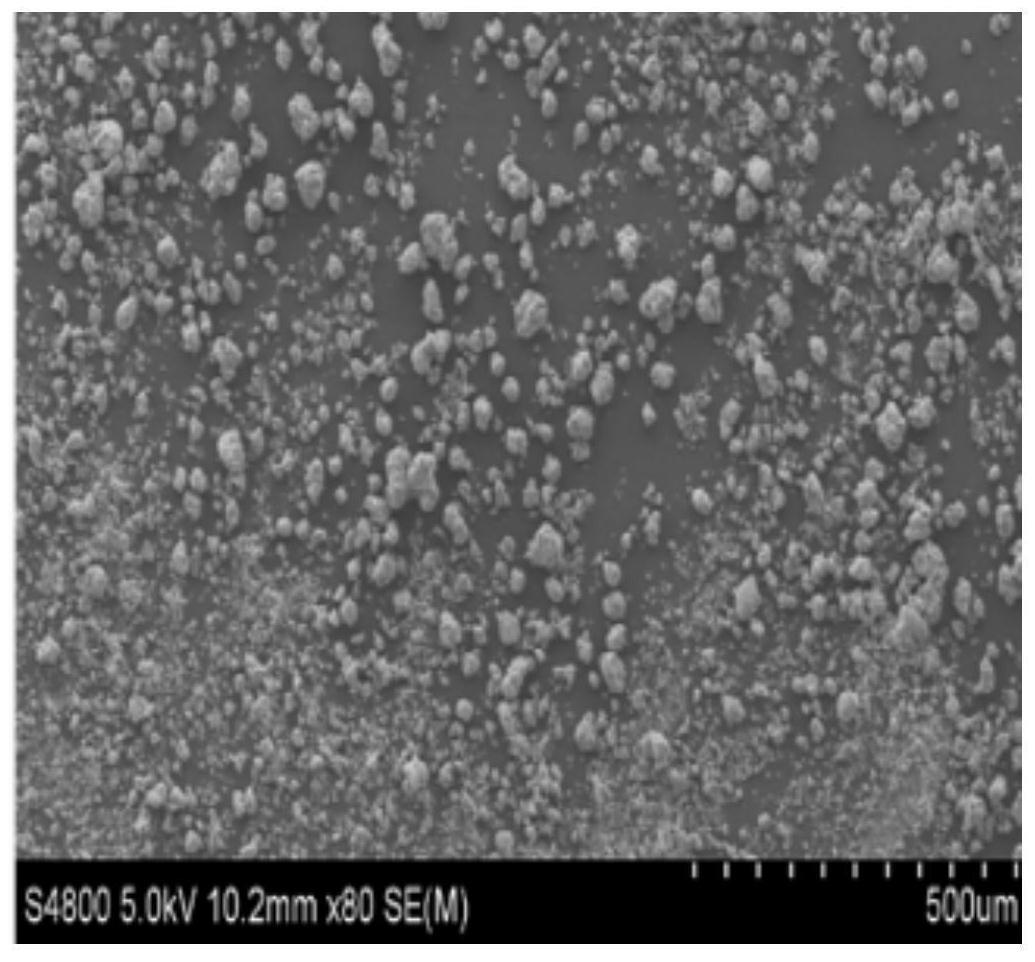
1.本发明涉及一种生物质高值化利用领域,通过催化提质及产品工程理念将生物质油转化为高分子材料加工助剂。
背景技术:2.利用生物质开发绿色化工原料和功能材料已成为目前可持续发展研究的热点与前沿。高效的生物炼制过程可以将生物质转化为小分子的液体燃料和平台化合物,再聚合制备相关产品。然而,复杂的工艺流程和生物质本身天然结构的未充分利用,使生物质转化过程技术经济性低,无法大规模应用。
3.《欧盟horizon2020计划》提出,新一代生物质利用策略应由现有的借鉴化石能源的“物性替代”,转变成面向应用的“功能替代”。近年来,涌现出一些面向生物质的分子编辑产品工程研究,如利用木质素中独特低聚物的结构特点,定向解聚将其转化为高附加值的功能材料(打印墨水等)。然而此过程需要兼顾应用的功能性和生物质的结构性,往往涉及到多学科交叉,其关键是针对生物质超分子结构,通过定向裁剪和改性的方式对生物质材料进行功能调变。
4.将农林废弃生物质原料通过热处理液化技术转化为生物质液化油是一种重要方法。但是生物热解油含有上百种产物(结构复杂、分离成本高),其含有大量含氧官能团(热值低)、低聚物(粘度高)和有机酸(酸度高、设备腐蚀)的特点等问题,替代化石燃料有一定距离。一般采用催化加氢、催化裂解等改性工艺处理含氧官能团及粘度问题,但最终面临制备能耗高、分离成本高、附加值低的“二高一低”难题。
5.纳米颗粒的均匀分散是构筑填料与聚合物的纳米结构基础,同是也决定着复合材料的性能优劣,然而目前无机纳米颗粒存在分散性差、难混入,且易在复合材料中产生无机相团聚体,不仅难以达到纳米级的复合,无法更好地发挥纳米效应,且可能增加材料缺陷,限制了其广泛应用。而目前使用的硅烷偶联剂、钛酸酯偶联剂、锆酸酯偶联剂等价格昂贵,同时需要一定毒性的有机溶剂作为助剂对无机纳米颗粒进行表面改性,且无法在常温和常压下制备,从而增大了成本,因此有必要研究和开发生物质无毒无机填料分散剂。
技术实现要素:6.为解决该问题,本发明提供一种高分子复合材料添加剂,所述高分子复合材料添加剂具有促进填料分散和増塑作用。
7.一种高分子复合材料添加剂,该复合材料添加剂是由无机颗粒和改性生物质油组成的混合物,无机颗粒和改性生物质油的质量比为100:0.5~20。
8.本发明技术方案中:所述的无机颗粒为二氧化硅、氧化铝、氧化锌、二氧化钛或碳酸钙中的一种或几种,且所述无机颗粒的d50粒径<0.5μm。
9.本发明技术方案中:所述的生物质油是木质纤维素在200
‑
600℃及0.04
‑
3mpa表压条件下液化获得。
10.本发明提供的第一种改性生物质油的制备方法为:将生物质油与环氧化试剂先进行环氧化反应,反应结束后将产物1进行烷基化反应或酯化反应,即可得到改性生物质油。
11.在一些优选的技术方案中:在固体酸催化剂的作用下,将生物质油与环氧化试剂先进行环氧化反应,反应结束后将产物1进行烷基化反应或酯化反应,即可得到改性生物质油。,固体酸催化剂占生物油质量比的0.1wt%
‑
5wt%。
12.第一种改性方法中:环氧化反应是将过氧化氢加入生物质油中,其中过氧化氢占生物油质量比的10wt%
‑
50wt%,反应温度为40
‑
80℃;反应时间为2
‑
5h;
13.第一种改性方法中:烷基化反应是将产物1与烷基化试剂进行反应,其中烷基化试剂占产物1质量比的1wt%
‑
20wt%,反应温度为80~120℃;反应时间为1
‑
3h;所述的烷基化试剂为碳原子数是4
‑
18的醇;进一步优选所述的烷基化试剂为碳原子数是8
‑
10的醇;最优选:所述的烷基化试剂为脂肪醇,如正辛醇、异辛醇、丁醇、壬醇中的一种或几种。
14.第一种改性的方法中:酯化反应是将产物1与醇类物质进行酯化反应,其中酯化试剂占产物1质量比的1wt%
‑
20wt%,反应温度为80~120℃;反应时间为1
‑
3h;所述的醇类物质为碳原子数是3
‑
6的多元醇,进一步优选:所述的醇类物质为季戊四醇、甘油、三羟甲基乙烷、木糖醇、山梨醇等多元醇其中的一种或多种。
15.本发明技术方案中:固体酸催化剂以1g无机材料与1ml 0.25
‑
1.25mol/l h2so4溶液的比例进行浸渍处理6
‑
16h,于100℃干燥6
‑
12h,再将所得样品分别经200~600℃焙烧活化1
‑
4h,即得到相应的固体酸催化剂。
16.进一步的:所述的无机材料为二氧化硅、氧化铝、氧化锌、二氧化钛或碳酸钙中的一种或几种。
17.本发明提供的第二种改性生物质油的制备方法为:将生物质油与环氧化试剂先进行环氧化反应,反应结束后将产物1进行烷基化反应,得到产物2,将产物2进行酯化反应,即可得到改性生物质油。
18.在一些优选的技术方案中:在固体酸催化剂的作用下,将生物质油与环氧化试剂先进行环氧化反应,反应结束后将产物1进行烷基化反应,得到产物2,将产物2进行酯化反应,即可得到改性生物质油。固体酸催化剂占生物油质量比的0.1wt%
‑
5wt%。
19.第二种改性方法中:环氧化反应是过氧化氢加入生物质油中,其中过氧化氢占生物油质量比的10wt%
‑
50wt%,反应温度为40
‑
80℃;反应时间为2
‑
5h。
20.第二种改性的方法中:烷基化反应是将产物1与烷基化试剂进行反应,其中烷基化试剂占产物1质量比的1wt%
‑
20wt%,反应温度为80~120℃;反应时间为1
‑
3h;所述的烷基化试剂为碳原子数是4
‑
18的长链醇;进一步优选所述的烷基化试剂为碳原子数是8
‑
10的醇;最优选:所述的烷基化试剂为脂肪醇,如正辛醇、异辛醇、丁醇、壬醇中的一种或几种。
21.第二种改性的方法中:酯化反应是将产物2与醇类物质进行酯化反应,其中酯化试剂占产物2质量比的1wt%
‑
20wt%,反应温度为80~120℃;反应时间为1
‑
3h;所述的醇类物质为碳原子数是3
‑
6的醇,进一步优选:所述的醇类物质为季戊四醇、甘油、三羟甲基乙烷、木糖醇、山梨醇等多元醇其中的一种或多种。
22.本发明技术方案中:固体酸催化剂以1g无机材料与1ml 0.25
‑
1.25mol/l h2so4溶液的比例进行浸渍处理6
‑
16h,于100℃干燥6
‑
12h,再将所得样品分别经200~600℃焙烧活化1
‑
4h,即得到相应的固体酸催化剂。
23.优选:所述的无机材料为二氧化硅、氧化铝、氧化锌、二氧化钛或碳酸钙中的一种或几种。
24.本发明提供的第三种改性生物质油的制备方法为:改性生物质油是将生物质油与环氧化试剂先进行环氧化反应,反应结束后将产物1进行酯化反应,得到产物3,将产物3进行烷基化反应,即可得到改性生物质油。
25.在一些优选的技术方案中:在固体酸催化剂的作用下,改性生物质油是将生物质油与环氧化试剂先进行环氧化反应,反应结束后将产物1进行酯化反应,得到产物3,将产物3进行烷基化反应,即可得到改性生物质油。
26.第三种方法中:环氧化反应是过氧化氢加入生物质油中,其中过氧化氢占生物油质量比的10wt%
‑
50wt%,反应温度为40
‑
80℃;反应时间为2
‑
5h。
27.第三种方法中:酯化反应是将产物1与醇类物质进行酯化反应,其中酯化试剂占产物1质量比的1wt%
‑
20wt%,反应温度为80~120℃;反应时间为1
‑
3h;所述的醇类物质为碳原子数是3
‑
6的多元醇,进一步优选:所述的醇类物质为季戊四醇、甘油、三羟甲基乙烷、木糖醇、山梨醇等多元醇其中的一种或多种。
28.第三种方法中:产物3进行烷基化反应是将产物3与烷基化试剂进行反应,其中烷基化试剂占产物3质量比的1wt%
‑
20wt%,反应温度为80~120℃;反应时间为1
‑
3h;所述的烷基化试剂为碳原子数是4
‑
18的长链醇;进一步优选所述的烷基化试剂为碳原子数是8
‑
10的醇;最优选:所述的烷基化试剂为脂肪醇,如正辛醇、异辛醇、丁醇、壬醇中的一种或几种。
29.本发明技术方案中:固体酸催化剂以1g无机材料与1ml 0.25
‑
1.25mol/l h2so4溶液的比例进行浸渍处理6
‑
16h,于100℃干燥6
‑
12h,再将所得样品分别经200~600℃焙烧活化1
‑
4h,即得到相应的固体酸催化剂。
30.最优选:所述的无机材料为二氧化硅、氧化铝、氧化锌、二氧化钛或碳酸钙中的一种或几种。
31.本发明技术方案中:所述的复合材料添加剂也可以作为高分子基体的增塑剂方面的应用。
32.本发明技术方案中,所述木质纤维素材料为麦秸秆、玉米秸秆、稻秸秆、高粱秸、荞麦秸、黄豆秸、甘蔗秸秆、甜菜秸秆、土豆秸秆、豌豆秸秆、蚕豆秸秆、稻壳、杨树皮、松树皮、碱木质素、磺酸盐木质素、硫酸盐木质素等其中的一种或多种;更优选地,稻壳、杨树皮、碱木质素;最优选地,为稻壳。
33.本发明技术方案中,无机颗粒是纳米、亚微米、微米级颗粒;优选的:无机颗粒是纳米、亚微米级颗粒。
34.本发明技术方案中,高分子聚合物基体包括天然橡胶、异戊橡胶、丁苯橡胶、顺丁橡胶、氯丁橡胶、丁腈橡胶聚乙烯、聚丙烯、聚氯乙烯、pva中的一种或几种的组合物。
35.本发明第二方面提供上高分子复合材料添加剂作为高分子复合材料增塑剂的用途。
36.优选地,所述复合材料添加剂在高分子聚合物基体中添加量为1wt%
‑
15wt%;优选地,添加量为3
‑
10wt%。
37.本发明技术方案中:微纳尺度的无机颗粒是高分子复合材料中的重要填料之一,其具有增强增韧作用并提供其他特殊功能如:导热、耐磨和可降解等,但是颗粒尺寸越小,
颗粒的尺寸效应越大,且伴随颗粒表面含氧集团的存在,使得维纳尺度的纳米颗粒在聚合物基体中极易团聚,而纳米颗粒的均匀分散是构筑复合材料的结构基础,同时也相当程度上决定了复合材料的性能。
38.由于生物质油中包含丰富的活性官能团,这种活性官能团与无机颗粒表面的羟基相互作用,形成氢键或醚键酯键等化学键,使得生物质油起到了类似偶联剂的作用,无机颗粒的分散状态得到提高。
39.虽然无机颗粒的尺寸越小越容易团聚,但在生物质油的作用下,分散状态得到保证,由此,更小的颗粒尺寸所展现的尺寸效应能更大程度地提高对高分子复合材料的积极作用。因此,本技术特别适用于小尺寸的无机颗粒。
40.无机颗粒表面的羟基容易缩合形成醚键并进而导致团聚。因此,羟基的存在往往导致无机颗粒更不容易被分散,但羟基本身性质活泼,容易与生物质油中的活性官能团形成相互作用;本技术利用生物质油与无机颗粒含氧基团的键合力,提高了无机颗粒的分散状态。
41.生物油存在酚羟基,醇羟基、醛酮和羧酸基团,打破无机填料间形成的氢键,并与无机填料上的羟基形成新的氢键或缩聚形成醚键,促进无机填料分散。
42.生物质油与无机颗粒的比例关系受到无机颗粒的含氧集团与生物质油中相对应的活性基团的比例关系的影响,同时,由于生物质油对复合材料中的聚合物基体具有増塑作用,由此,在保证均匀分散的同时,应考虑到生物质油作为增塑剂的用量。
43.生物质油是一种复杂的混合物,生物质的主要由纤维素、半纤维素和木质素组成,不同的生物质的三种组分比例不同,而不同生物质的液化油的基本组分相似,都具备丰富的活性官能团,能够提供分子间氢键、静电力、π
‑
π堆积作用和阳离子
‑
π相互作用等多种分子间作用力起到分散无机填料的目的。这些基团可以提供改性位点,根据应用需要嫁接不同基团,起到增塑作用。
44.生物质油的来源和制备方法是已知的。在不违背本技术发明构思的基础上,已知的制备方法均能用于本技术中。
45.増塑剂是高分子复合材料中一种常规添加剂,其主要作用为高沸点,低挥发性,并能与高聚物相混容的小分子物质。已知的是,增塑剂的使用能降低高分子聚合物基体的玻璃化温度和塑料成型加工时的熔体黏度,且本身保持不变,或虽起化学变化但能长期保留在塑料制品中并能改变树脂的某些物理性质。
46.本发明技术方案中:通过烷基化改性,在生物质油中引入烷基,合适的碳链提高了生物质油的疏水性,有利于提高生物质油与高分子基体的亲和性;同时,烷基的引入促进了生物质油的位阻效应,一方面提高了对无机颗粒的分散作用,同时,也进一步提高了増塑作用。
47.烷基化反应是一种已知的化学反应,在不违背本技术发明构思的基础上,任何原理已知的烷基化反应都能用于本技术中,可以理解的是,烷基化反应已知不代表将烷基化反应引入生物质油中提高生物质油对无机颗粒的分散性和其对高分子材料基体的増塑性是已知的。
48.环氧化反应是不饱和键在供氧剂作用下生成环氧官能团的过程称为环氧化,通过环氧化可以将生物质油中的双键反应去除,提高稳定性,同时环氧化的后可以嫁接支链,抑
制生物液化油挥发,同时在环氧化反应后进行烷基化反应,使得原来的双键转化为烷基,强化生物质液化油的增塑作用。环氧化反应是一种已知的反应,通过将生物质油与过氧化氢等环氧化试剂进行反应,在不违背本技术发明构思的基础上,任何现有技术中已知的环氧化反应均能用于本技术。
49.通过酯化反应,可以去除生物油中活泼性强的羧基。申请人通过实验发现,生物质油中的羧基具有腐蚀性,腐蚀性一方面对生产设备提出了更高的要求,另一方面,腐蚀性对复合材料本身也产生不利影响。
50.令人意外,通过酯化反应,去除了腐蚀性的同时,引入了疏水的烷基,一定程度上提高了生物质油的位阻效应。
51.本发明技术方案中:可以先酯化后烷基化,也可以先烷基化再酯化;但应该保证环氧化反应在烷基化反应之前,以确保生物质油中的不饱和双键得到去除。可以理解的是,相应的反应步骤直接可以是直接的串联关系,比如对于“先酯化再环氧化后烷基化”,酯化反应与环氧化反应之间、环氧化反应与烷基化反应之间不再设有其他工序;也可以是间接串联的,比如酯化反应与烷基化反应之间可以接入其他工艺,作为一种示意性的举例,该其他工序可以是干燥、提纯、去除杂质等,可以理解的是,在不违背本技术发明构思的基础上,任何基于现有技术二对该工艺顺序所作的常规调整均在本技术保护范围之内。
52.此处所指的适宜是指无机颗粒的加入对高分子复合材料的性能是有益的,无机颗粒与高分子聚合物基体或高分子复合材料中的其他添加剂呈化学惰性和/或不发生不期望的反应,作为示意性的举例,无机颗粒包括但不限于二氧化硅、氧化铝、氧化锌、二氧化钛或碳酸钙中的一种或几种;作为一种实施方式,无机颗粒可以为多种的混合物。
53.技术效果:
54.1、生物质油具有丰富的活性官能团,不仅具有活泼的化学反应活性,提供改性位点,而且能够提供分子间氢键、静电力、π
‑
π堆积作用和阳离子
‑
π相互作用等多种分子间作用力,与具有极性的聚合物分子相容性好,能够降低聚合加工摩擦热,改善聚合物高温流变性能,起到高分子复合材料增塑剂的性能。
55.2、由于生物质油的活性官能团与无机颗粒表面的羟基发生强相互作用,使得生物质油对无机颗粒具有良好的分散作用,提高无机颗粒与聚合物分子间的作用力,胶料的内聚力提高,拉伸时链段不易滑动。
56.3、生物质油同时具有分散和增塑作用,使得高分子复合材料中不必再额外添加大量的增塑剂和改性剂,避免了工业废物处理压力,有利于成本的降低和环境的保护。
57.4、通过对生物质油进行酯化改性,使得生物质油中的腐蚀性羧基被封闭,降低了生产过程中的设备要求同时,也提高了复合材料整体的稳定性。
58.5、通过对生物质油进行烷基化改性,进一步提高了无机颗粒与聚合物基体的结合力,提高了材料的整体力学性能。
59.6、在烷基化反应前,先进行环氧化反应,可以去除生物质油中的不饱和双键,提高生物质油对聚合物基体的稳定性。
附图说明
60.图1是未改性的sio2的产品sem图。
61.图2是实施例1的复合材料添加剂sem图。
62.图3是对比例7的复合材料添加剂sem图。
具体实施方式
63.下面结合实施例对本发明做进一步说明,但本发明的保护范围不限于此:
64.实施例1(环氧化+烷基化)
65.固体酸催化剂以1g无机材料50nm的sio2与1ml 0.75mol/l h2so4溶液的比例进行浸渍处理10h,于100℃干燥8h,再将所得样品分别经400℃焙烧活化3h,即得到相应的so
42
‑
/sio2固体酸催化剂;
66.取10g的稻壳粉末加入600℃,0.1mpa压力(表压)条件高温高压反应釜中制备得到生物油4.3g,反应结束后在液化生物油中加入0.1g so
42
‑
/sio2固体酸催化剂,搅拌,加热温度至40℃,然后缓慢滴加20%过氧化氢,其中过氧化氢占生物油质量比的20wt%,在加完后恒温反应2h获得改性后生物油a,加入脂肪醇:辛醇作为烷基化原料,其占生物油比例的10wt%,反应温度设置为110℃,反应3h;最后通过旋蒸除去水分获得环氧和烷基化改性生物质油。得到的改性生物质油与50nm的sio2机械混合,其中改性生物质油占两者总重量的3wt%,混合均匀制备得到复合材料添加剂,复合材料添加剂的sem的可如图2。
67.实施例2(环氧化+酯化):
68.固体酸催化剂以1g无机材料50nm的sio2与1ml 0.75mol/l h2so4溶液的比例进行浸渍处理10h,于100℃干燥8h,再将所得样品分别经400℃焙烧活化3h,即得到相应的so
42
‑
/sio2固体酸催化剂;
69.取10g的稻壳粉末加入400℃,0.2mpa(表压)条件高温高压反应釜中制备得到生物油3.8g,反应结束后在液化生物油中加入0.1g so
42
‑
/sio2固体酸催化剂,搅拌,加热温度至40℃,然后缓慢滴加20%过氧化氢,其中过氧化氢占生物油质量比的20wt%,在加完后恒温反应2h获得改性后生物油a,加入多元醇:季戊四醇作为酯化的原料,其占生物油比例的10wt%,反应温度设置为110℃,反应3h;最后通过旋蒸除去水分获得环氧和酯化改性生物质油。得到的改性生物质油与50nm的sio2机械混合,其中改性生物质油占两者总重量的3wt%,混合均匀制备得到复合材料添加剂。
70.实施例3(环氧化+烷基化+酯化):
71.固体酸催化剂以1g无机材料50nm的sio2与1ml 0.75mol/l h2so4溶液的比例进行浸渍处理10h,于100℃干燥8h,再将所得样品分别经400℃焙烧活3h,即得到相应的so
42
‑
/sio2固体酸催化剂;
72.取10g的稻壳粉末加入600℃,0.1mpa(表压)条件高温高压反应釜中制备得到生物油4.3g,反应结束后在液化生物油中加入0.1g so
42
‑
/sio2固体酸催化剂,搅拌,加热温度至40℃,然后缓慢滴加20%过氧化氢,其中过氧化氢占生物油质量比的20wt%,在加完后恒温反应2h获得改性后生物油a,加入脂肪醇:辛醇作为烷基化原料,其占生物油比例的5wt%,反应温度设置为110℃,反应3h,加入多元醇:季戊四醇作为酯化的原料,其占生物油比例的5wt%,反应温度设置为110℃,反应3h;最后通过旋蒸除去水分获环氧化,酯化和烷基化改性生物质油。得到的改性生物质油与50nm的sio2机械混合,其中改性生物质油占两者总重量的3wt%,混合均匀制备得到复合材料添加剂。
73.实施例4(环氧化+烷基化):
74.固体酸催化剂以1g无机材料100nm的tio2与1ml 0.75mol/l h2so4溶液的比例进行浸渍处理10h,于100℃干燥8h,再将所得样品分别经400℃焙烧活化3h,即得到相应的so
42
‑
/tio2固体酸催化剂;
75.取10g的稻壳粉末加入400℃,0.2mpa(表压)条件高温高压反应釜中制备得到生物油3.6g,反应结束后在液化生物油中加入0.1g so
42
‑
/to2固体酸催化剂,搅拌,加热温度至40℃,然后缓慢滴加20%过氧化氢,其中过氧化氢占生物油质量比的20wt%,在加完后恒温反应2h获得改性后生物油a,加入脂肪醇:辛醇作为烷基化原料,其占生物油比例的10wt%,反应温度设置为110℃,反应3h;最后通过旋蒸除去水分获得环氧和烷基化改性生物质油。将得到的生物质油与100nm的tio2机械混合,其中生物质油占两者总重量的3wt%,混合均匀制备得到复合材料添加剂。
76.实施例5(环氧和烷基):
77.固体酸催化剂以1g无机材料100nm的zro2与1ml 0.75mol/l h2so4溶液的比例进行浸渍处理10h,于100℃干燥8h,再将所得样品分别经400℃焙烧活化3h,即得到相应的so
42
‑
/zro2固体酸催化剂;
78.取10g的稻壳粉末加入400℃,0.2mpa(表压)条件高温高压反应釜中制备得到生物油4.3g,反应结束后在液化生物油中加入0.1g so
42
‑
/zro2固体酸催化剂,搅拌,加热温度至40℃,然后缓慢滴加20%过氧化氢,其中过氧化氢占生物油质量比的20wt%,在加完后恒温反应2h获得改性后生物油a,加入脂肪醇:辛醇作为烷基化原料,其占生物油比例的10wt%,反应温度设置为110℃,反应3h;最后通过旋蒸除去水分获得环氧和烷基化改性生物质油。将得到的改性生物质油与100nm的zro2机械混合,其中生物质油占两者总重量的3wt%,混合均匀制备得到复合材料添加剂。
79.对比例1(烷基化):
80.固体酸催化剂以1g无机材料50nm的sio2与1ml 0.75mol/l h2so4溶液的比例进行浸渍处理10h,于100℃干燥8h,再将所得样品分别经400℃焙烧活化3h,即得到相应的so
42
‑
/sio2固体酸催化剂;
81.取10g的稻壳粉末加入600℃,0.1mpa(表压)条件高温高压反应釜中制备得到生物油4.3g,在液化生物油中加入0.1g so
42
‑
/sio2固体酸催化剂,加入脂肪醇:辛醇作为烷基化的原料,其占生物油比例的10wt%,反应温度设置为110℃,反应3h;最后通过旋蒸除去水分获得烷基化改性生物质油。得到的改性生物质油与50nm的sio2机械混合,其中改性生物质油占两者总重量的3wt%,混合均匀制备得到复合材料添加剂。
82.对比例2(酯化):
83.固体酸催化剂以1g无机材料50nm的sio2与1ml 0.75mol/l h2so4溶液的比例进行浸渍处理10h,于100℃干燥8h,再将所得样品分别经400℃焙烧活化3h,即得到相应的so
42
‑
/sio2固体酸催化剂;
84.取10g的稻壳粉末加入600℃,0.1mpa(表压)条件高温高压反应釜中制备得到生物油4.3g,在液化生物油中加入0.1g so
42
‑
/sio2固体酸催化剂,多元醇:季戊四醇作为酯化的原料,其占生物油比例的10wt%,反应温度设置为110℃,反应3h;最后通过旋蒸除去水分获得酯化改性生物质油。得到的改性生物质油与50nm的sio2机械混合,其中改性生物质油占
两者总重量的3wt%,混合均匀制备得到复合材料添加剂。
85.对比例3(环氧化):
86.固体酸催化剂以1g无机材料50nm的sio2与1ml 0.75mol/l h2so4溶液的比例进行浸渍处理10h,于100℃干燥8h,再将所得样品分别经400℃焙烧活化3h,即得到相应的so
42
‑
/sio2固体酸催化剂;
87.取10g的稻壳粉末加入600℃,0.1mpa(表压)条件高温高压反应釜中制备得到生物油4.3g,反应结束后在液化生物油中加入0.1g so
42
‑
/sio2固体酸催化剂,搅拌,加热温度至40℃,然后缓慢滴加20%过氧化氢,其中过氧化氢占生物油质量比的20wt%,在加完后恒温反应2h获得改性后生物油,最后通过旋蒸除去水分获得环氧改性生物质油。得到的改性生物质油与50nm的sio2机械混合,其中改性生物质油占两者总重量的3wt%,混合均匀制备得到复合材料添加剂。
88.对比例4(烷基化和环氧)
89.固体酸催化剂以1g无机材料50nm的sio2与1ml 0.75mol/l h2so4溶液的比例进行浸渍处理10h,于100℃干燥8h,再将所得样品分别经400℃焙烧活化3h,即得到相应的so
42
‑
/sio2固体酸催化剂;
90.取10g的稻壳粉末加入600℃,0.1mpa压力(表压)条件高温高压反应釜中制备得到生物油4.3g,反应结束后在液化生物油中加入0.1g so
42
‑
/sio2固体酸催化剂,加入脂肪醇:辛醇作为烷基化原料,其占生物油比例的10wt%,反应温度设置为110℃,反应3h获得烷基化的改性生物质油b,改性生物质油b,搅拌,加热温度至40℃,然后缓慢滴加20%过氧化氢,其中过氧化氢占生物油质量比的20wt%,在加完后恒温反应2h;最后通过旋蒸除去水分获得烷基化和环氧改性生物质油。得到的改性生物质油与50nm的sio2机械混合,其中改性生物质油占两者总重量的3wt%,混合均匀制备得到复合材料添加剂。
91.对比例5(酯化和环氧)
92.固体酸催化剂以1g无机材料50nm的sio2与1ml 0.75mol/l h2so4溶液的比例进行浸渍处理10h,于100℃干燥8h,再将所得样品分别经400℃焙烧活化3h,即得到相应的so
42
‑
/sio2固体酸催化剂;
93.取10g的稻壳粉末加入600℃,0.1mpa压力(表压)条件高温高压反应釜中制备得到生物油4.3g,反应结束后在液化生物油中加入0.1g so
42
‑
/sio2固体酸催化剂,多元醇:季戊四醇作为酯化的原料,其占生物油比例的10wt%,反应温度设置为110℃,反应3h获得酯化的改性生物质油c,在搅拌下,反应温度至40℃,然后缓慢滴加20%过氧化氢,其中过氧化氢占生物油质量比的20wt%,在加完后恒温反应2h;最后通过旋蒸除去水分获得酯化和环氧改性生物质油。得到的改性生物质油与50nm的sio2机械混合,其中改性生物质油占两者总重量的3wt%,混合均匀制备得到复合材料添加剂。
94.对比例6:(未改性)
95.取10g的稻壳粉末加入600℃,0.1mpa(表压)条件高温高压反应釜中制备得到生物油4.3g,将得到的生物质油与50nm的sio2机械混合,其中生物质油占两者总重量的3wt%,混合均匀制备得到复合材料添加剂。
96.对比例7:(商业分散剂)
97.将硅烷偶联剂kh570与50nm的sio2机械混合,其中硅烷偶联剂kh570占两者总重量
的3wt%,混合均匀制备得到复合材料添加剂,如图3。
98.橡胶样品制备:
99.将100份天然胶添加到密炼机中,依次加入5份的氧化锌,2份的硬脂酸,50份的复合材料添加剂(实施例1~5,对比例1~7)混炼10min后排胶,然后再双轴开炼机进行开练依次加入1.5份的促进剂cz(n
‑
环己基
‑2‑
苯并噻唑次磺酰胺)和2.5份的硫磺开练10min。将开炼后的橡胶复合材料在170℃进行硫化25min得到橡胶复合材料.各实施例生物质油改性方法如下表:
100.表1:各实施例生物质油改性方法及物料组成
[0101][0102][0103]
性能测试方法:
[0104]
对于实施例1
‑
5和对比例1
‑
7的生物油样品和偶联剂的采用亲疏水测试方法(gb/t30693
‑
2014)和材料稳定性测试方法(gb t 13464
‑
2008)对其接触角、挥发温度进行测试。
[0105]
对未硫化的橡胶采用gb/t 1232
‑
1992在门尼粘度仪测试试样门尼粘度。(ml100℃1+4:其中m表示门尼,l表示用大转子,。1表示预热1分钟,4表示试验4分钟。)
[0106]
通过橡胶专用裁刀将橡胶复合材料(实施例1~5,对比例1~7)切成115mm的哑铃状试样,根据gb/t528
‑
2009在万能试验机上测试试样的力学强度。
[0107]
1.亲疏水测试和挥发温度
[0108]
表2:接触角、挥发温度结果
[0109] 接触角挥发温度实施例1125252实施例298249实施例3120257实施例4126278实施例5123271对比例1115225对比例272221对比例398223对比例4116225对比例5105221
对比例671193对比例7125217
[0110]
通过对比实施例1
‑
5与对比例1
‑
7可知经过改性的生物质油挥发温度显著提高,其中,烷基化由于引入了长碳链,因此,其疏水性更强,更有利于提高无机颗粒与高分聚合物基体的作用力。烷基化之前经过环氧化反应,有利于提高生物质油的稳定性,其挥发温度更高。而挥发温度的提高有利于生物质油在高分子复合材料中的稳定存在。
[0111]
2.橡胶复合材料(实施例1~5,对比例1~7)的力学性能和门尼粘度测试
[0112]
表3:力学性能和门尼粘度测试结果
[0113][0114]
通过对比实施例1
‑
5与对比例7可知,添加改性生物质油处理的纳米氧化硅后,橡胶复合材料的门尼粘度和硬度下降且定伸应力降低,说明改性生物质油的引入有效提高了高分子复合材料的塑性。
[0115]
通过比较实施例1与对比例6可知,通过环氧化+烷基化改性生物油相较于原始生物油,能够大幅提高橡胶复合材料的拉伸强度,表面改性生物油能够促进纳米氧化硅在橡胶中的分散。
[0116]
同时,对比实施例1和对比例1可知,在烷基化前引入环氧化反应,可以进一步提高材料的増塑性能和力学性能。
[0117]
通过对比图1~3,传统的分散硅烷偶联剂kh570对纳米氧化硅的分散效果差,但使用生物质油对氧化硅进行处理后,有效提高了纳米氧化硅材料的分散性。
[0118]
以上所述,仅为本发明的具体实施方式,但本发明的保护范围并不局限于此,任何熟悉本技术领域的技术人员在本发明揭露的技术范围内,可轻易想到各种等效的修改或替换,这些修改或替换都应涵盖在本发明的保护范围之内。因此,本发明的保护范围应以权利要求的保护范围为准。