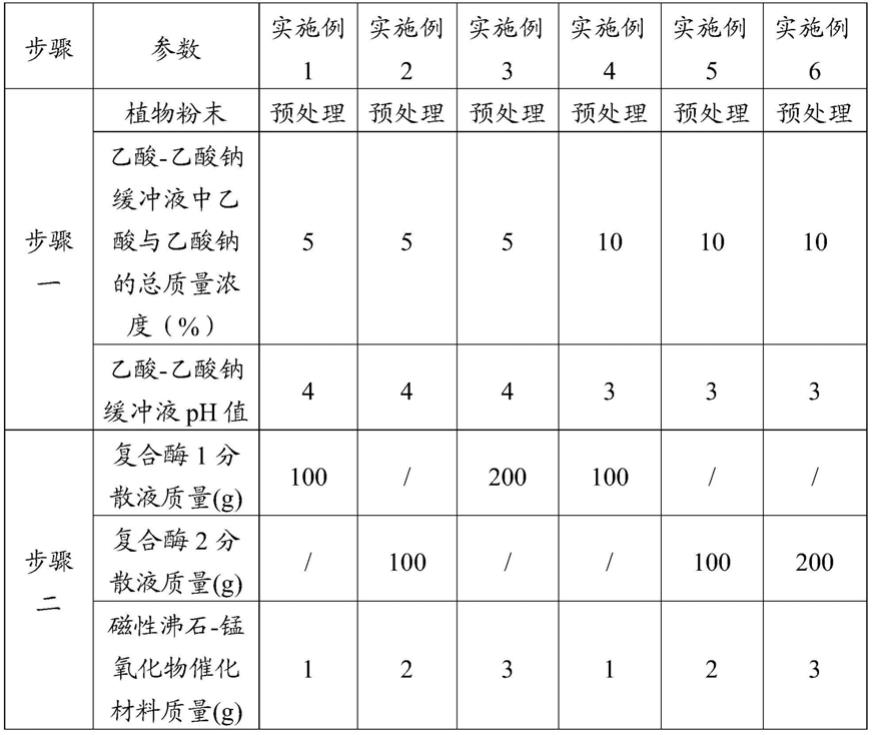
1.本发明涉及环境治理技术领域,具体涉及一种植物基固液混合碳源及其制备方法。
背景技术:2.目前,随着环保力度加大和污水排放标准的逐渐提高,总氮指标要求越来越高,普遍要求达到城市污水排放一级a标准,即tn<15mg/l,而在一些环保要求更高的地区排放标准为tn<10mg/l,这对污水处理的反硝化处理提出了更高的要求。现有的反硝化处理中往往存在碳源不足的问题,必须外加碳源,如乙酸钠、乙酸、甲醇、乙醇、葡萄糖等。乙酸、甲醇、乙醇属危化品,由于安全原因,很少被采用;葡萄糖由于反硝化速率慢而少有应用。乙酸钠由于反硝化速率快、来源广泛、使用安全而被普遍使用,但其使用成本高,不经济。近年来,研究人员正在开发各种复合碳源,旨在提高碳源cod值,以降低碳源投加量,提高性价比。
3.木质纤维素是地球上最为丰富的有机资源,每年生物圈中可产生大约850亿吨,人类仅利用了4.8%。木质纤维素中的有机成分主要包括30~40%纤维素、20~30%半纤维素和10~15%木质素等。木质纤维素通过物理、化学、生物等方法处理,得到生物质燃料,已有很多报道,但将其用于污水处理碳源尚没有报道。由于复杂的材料结构、木质素的存在等问题,木质纤维素很难直接作为污水处理厂碳源使用。因此,基于木质纤维素如何制备得到适于污水处理厂使用的碳源,是目前亟需解决的问题。
技术实现要素:4.本发明的目的在于提供一种植物基固液混合碳源及其制备方法,本发明以植物为原料制备碳源,工艺简单,且性价比高。
5.为了实现上述发明目的,本发明提供以下技术方案:
6.本发明提供了一种植物基固液混合碳源的制备方法,包括以下步骤:
7.将预处理植物粉末、酶、磁性沸石-锰氧化物催化材料与弱酸缓冲溶液混合,得到混合料液;
8.在超声条件下将所述混合料液进行酶解处理,之后将所得体系中磁性沸石-锰氧化物催化材料磁分离,得到植物基固液混合碳源。
9.优选地,所述酶包括纤维素酶、纤维二糖酶、木聚糖酶和果胶酶中的一种或几种。
10.优选地,所述酶的质量为预处理植物粉末质量的0.01~1%。
11.优选地,所述磁性沸石-锰氧化物催化材料的质量为预处理植物粉末质量的0.1~10%。
12.优选地,所述弱酸缓冲溶液的ph值为3~5,所述弱酸缓冲溶液中的弱酸包括乙酸、柠檬酸、酒石酸或葡萄糖酸。
13.优选地,所述预处理植物粉末、酶、磁性沸石-锰氧化物催化材料与弱酸缓冲溶液混合,包括以下步骤:
14.将预处理植物粉末与部分弱酸缓冲溶液混合,得到预处理植物粉末分散液;
15.将酶与剩余弱酸缓冲溶液混合,得到酶分散液;
16.将所述预处理植物粉末分散液、酶分散液与磁性沸石-锰氧化物催化材料混合。
17.优选地,所述预处理植物粉末分散液中预处理植物粉末的浓度为40~60g/l。
18.优选地,所述酶分散液中酶的质量含量为0.01~1%。
19.优选地,所述超声的频率为10~50khz、输入功率为0.01~10w/ml;所述酶解处理的温度为室温~100℃,时间为10~72h。
20.本发明提供了上述技术方案所述制备方法制备得到植物基固液混合碳源。
21.本发明提供了一种植物基固液混合碳源的制备方法,包括以下步骤:预处理植物粉末、酶、磁性沸石-锰氧化物催化材料与弱酸缓冲溶液混合,得到混合料液;在超声条件下将所述混合料液进行酶解处理,之后将所得体系中磁性沸石-锰氧化物催化材料磁分离,得到植物基固液混合碳源。本发明将植物转化为污水处理厂可利用碳源,实现了环境治理和资源化利用的有机结合。具体的,在本发明中,将磁性沸石-锰氧化物催化材料经磁分离去除后,剩余体系直接作为碳源,可直接投加到污水处理厂反消化生物系统中,整个制备过程中不产生废液,且工艺简单,条件温和,安全环保,又能科学利用自然植物,降低污水厂运行成本。
具体实施方式
22.本发明提供了一种植物基固液混合碳源的制备方法,包括以下步骤:
23.将预处理植物粉末、酶、磁性沸石-锰氧化物催化材料与弱酸缓冲溶液混合,得到混合料液;
24.在超声条件下将所述混合料液进行酶解处理,之后将所得体系中磁性沸石-锰氧化物催化材料磁分离,得到植物基固液混合碳源。
25.本发明首先对预处理植物粉末的来源进行说明。在本发明中,所述预处理植物粉末的制备方法,优选包括以下步骤:
26.将植物秸秆进行破碎处理,得到植物粉末;
27.将所述植物粉末、磁性沸石-锰氧化物催化材料与弱酸水溶液混合,在超声条件下进行预热处理,之后将所得预热处理体系进行第一固液分离,将所得第一固体物料水洗至中性,经第二固液分离后得到第二固体物料;
28.将所述第二固体物料与弱碱水溶液混合,进行热水解处理,之后将所得热水解处理体系经磁分离去除磁性沸石-锰氧化物催化材料,将剩余物料进行第三固液分离,将所得第三固体物料水洗至中性,经第四固液分离后得到预处理植物粉末。
29.本发明将植物秸秆进行破碎处理,得到植物粉末。本发明对所述植物秸秆的具体种类没有特殊限定,采用本领域技术人员熟知的植物秸秆均可,具体可以为草本植物秸秆。本发明优选将植物秸秆进行风干处理后再进行破碎处理。在本发明中,所述风干处理优选为在室温条件下自然风干;在本发明的实施例中,所述室温具体为25℃。本发明对所述破碎处理没有特殊限定,能够得到粒度满足要求的植物粉末即可,具体的,所述植物粉末的粒度优选为60~100目。
30.得到植物粉末后,本发明将所述植物粉末、磁性沸石-锰氧化物催化材料与弱酸水
溶液混合,在超声条件下进行预热处理,之后将所得预热处理体系进行第一固液分离,将所得第一固体物料水洗至中性,经第二固液分离后得到第二固体物料。在本发明中,所述弱酸水溶液中的弱酸优选包括乙酸、柠檬酸、酒石酸和葡萄糖酸中的一种或几种,所述弱酸水溶液中弱酸的质量含量优选为0.01~1%,更优选为0.05~0.5%,进一步优选为0.1~0.2%,所述弱酸水溶液与植物粉末的质量比优选为(5~10):1,更优选为(5~8):1,进一步优选为(5~6):1。在本发明中,所述磁性沸石-锰氧化物催化材料的质量优选为所述植物粉末质量的0.01~1%,更优选为0.1~1%,进一步优选为0.5~1%。
31.在本发明中,所述磁性沸石-锰氧化物催化材料优选是由沸石粉原位合成负载锰氧化物、再原位合成负载磁性四氧化三铁制备得到;在本发明中,所述磁性沸石-锰氧化物催化材料的制备方法优选如下:制备沸石负载锰氧化物;将所述沸石负载锰氧化物分散到水中,同时加入超支化聚乙烯亚胺超声分散;将所得溶液在曝气量为10~20l/min下曝气,同时加热升温至80~100℃,以及滴加预定量的亚铁盐溶液和碱液;其中,亚铁盐与碱的物质量比为1:2~3;溶液滴加完毕后,在曝气量为11~20l/min、恒温81~100℃条件下搅拌反应1~5min;将反应后的吸附催化材料依次进行磁分离、水洗和干燥,制得磁性沸石-锰氧化物催化材料。在本发明中,所述沸石负载锰氧化物的制备方法优选如下:将沸石粉在100℃水中煮沸1~3h,过滤、干燥,得到预处理沸石粉;配制一定浓度的高锰酸钾溶液;配制一定浓度的锰盐和酸溶液;将所述预处理沸石粉分散于水中,得到沸石水悬浊液;在60~80℃搅拌下,向所述沸石水悬浊液中同步滴加高锰酸钾溶液、锰盐和酸溶液,滴加完毕,70~90℃水热反应1~5h,过滤,水洗至中性,得到沸石负载锰氧化物。
32.在本发明中,进行所述预热处理时,所述超声的频率优选为20~50khz,更优选为30~40khz;所述超声的输入功率优选为0.01~1w/ml,更优选为0.01~0.1w/ml。在本发明中,所述预热处理的温度优选为60~100℃,更优选为80~100℃;所述预热处理的时间优选为0.1~5h,更优选为1~3h。本发明对所述第一固液分离、将第一固体物料水洗至中性以及第二固液分离的具体操作方式没有特殊限定,采用本领域技术人员熟知的方式即可;在本发明中,所述第一固液分离和第二固液分离具体可以为过滤。在本发明中,所述第二固体物料包括弱酸水溶液改性处理的植物粉末以及磁性沸石-锰氧化物催化材料,所述磁性沸石-锰氧化物催化材料具体是在热水解处理后经磁分离去除。在本发明中,在弱酸存在下进行预热处理的过程中,植物秸秆中存在的无机组分等可能对后续处理产生干扰和阻碍的物质被去除,同时植物秸秆表面基团被活化,有利于通过后续热水解处理去除木质素效率,其中,纤维素-半纤维素-木质素的紧密结构被破坏,木质素分解,同时尽可能不破坏纤维素以及半纤维素结构,为下一步高效进行热水解处理提供基础。
33.得到第二固体物料后,本发明将所述第二固体物料与弱碱水溶液混合,进行热水解处理,之后将所得热水解处理体系经磁分离去除磁性沸石-锰氧化物催化材料,将剩余物料进行第三固液分离,将所得第三固体物料水洗至中性,经第四固液分离后得到预处理植物粉末。在本发明中,所述弱碱水溶液中的弱碱优选包括碳酸钠、碳酸钾、碳酸氢钠、碳酸氢钾、乙酸钠、柠檬酸钠、柠檬酸钾、酒石酸钠、酒石酸钾、酒石酸钾钠、葡萄糖酸钠和葡萄糖酸钾中的一种或几种,所述弱碱水溶液中弱碱的质量含量优选为0.01~1%,更优选为0.05~0.1%,所述弱碱水溶液与植物粉末的质量比优选为(5~10):1,更优选为(5~8):1,进一步优选为(5~6):1。
34.在本发明中,所述热水解处理的温度优选为150~200℃,更优选为160~180℃;所述热水解处理的压力优选为0.45~1.5mpa,更优选为0.6~1mpa;所述热水解处理的时间优选为1~12h,更优选为3~4h。本发明对所述第三固液分离、将第二固体物料水洗至中性以及第四固液分离的具体操作方式没有特殊限定,采用本领域技术人员熟知的方式即可;在本发明中,所述第三固液分离和第四固液分离具体可以为过滤。在本发明中,所述磁分离的磁感应强度优选为100~1000mt,更优选为500~800mt。本发明对所述磁分离的具体操作方式没有特殊限定,采用本领域技术人员熟知的方法即可。在本发明中,经磁分离得到的磁性沸石-锰氧化物催化材料可重复利用。在本发明中,所述热水解处理的过程中,通过强物理化学作用,将植物秸秆中难生物利用的木质素等物质分解,转变成小分子物质释放到水溶液中,尤其是在磁性沸石-锰氧化物催化材料的催化作用下,分解效率大大提高,同时可以吸附去除n、p等物质,旨在提高后续酶解效率。而且,本发明在弱碱存在条件下进行热水解处理,能够避免对植物秸秆中纤维素以及半纤维素结构的破坏,有利于通过后续酶解工艺提高纤维素产碳源的量。
35.在本发明中,所述第一固液分离后还得到第一液体物料,所述第三固液分离后还得到第三液体物料,所述第一液体物料与第三液体物料可直接混合,二者酸碱中和后,可用于污水处理厂反消化碳源。在本发明中,所述第二固液分离以及第四固液分离后还分别得到第二液体物料以及第四液体物料,即水洗液;所述第二液体物料以及第四液体物料的处理方法与第一液体物料与第三液体物料的处理方法一致,也可以直接将第一液体物料、第二液体物料、第三液体物料以及第四液体物料混合,用于污水处理厂反消化碳源。因此本发明制备预处理植物粉末时不产生废液,可降低污水厂运行成本。
36.得到预处理植物粉末后,本发明将预处理植物粉末、酶、磁性沸石-锰氧化物催化材料与弱酸缓冲溶液混合,得到混合料液。在本发明中,所述酶优选包括纤维素酶、纤维二糖酶、木聚糖酶和果胶酶中的一种或几种,具体可以为纤维素酶与纤维二糖酶混合形成的复合酶1,也可以为纤维素酶、纤维二糖酶、木聚糖酶与果胶酶混合形成的复合酶2;所述复合酶1中纤维素酶与纤维二糖酶的质量比优选为100:(1~100),更优选为100:(35~60),进一步优选为100:50;所述复合酶2中纤维素酶、纤维二糖酶、木聚糖酶与果胶酶的质量比优选为100:(1~100):(0.1~10):(0.1~10),更优选为100:(35~60):(1~10):(1~10),进一步优选为100:50:10:10。本发明优选采用上述复合酶并控制各酶的配比在上述范围内,各种酶协同作用,能够更高效的将秸秆中纤维素和半纤维素分解为可生物利用的单糖。在本发明中,所述酶的质量优选为预处理植物粉末质量的0.01~1%,更优选为0.1~0.5%。
37.在本发明中,所述磁性沸石-锰氧化物催化材料的质量优选为预处理植物粉末质量的0.1~10%,更优选为0.5~5%。在本发明中,所述磁性沸石-锰氧化物催化材料优选是由沸石粉原位合成负载锰氧化物、再原位合成负载磁性四氧化三铁制备得到;在本发明中,所述磁性沸石-锰氧化物催化材料的制备方法优选如下:制备沸石负载锰氧化物;将所述沸石负载锰氧化物分散到水中,同时加入超支化聚乙烯亚胺超声分散;将所得溶液在曝气量为10~20l/min下曝气,同时加热升温至80~100℃,以及滴加预定量的亚铁盐溶液和碱液;其中,亚铁盐与碱的物质量比为1:2~3;溶液滴加完毕后,在曝气量为11~20l/min、恒温81~100℃,搅拌反应1~5min;将反应后的吸附催化材料进行磁分离、水洗、干燥至恒重,制得磁性沸石-锰氧化物催化材料。在本发明中,所述沸石负载锰氧化物的制备方法优选如下:
将沸石粉在100℃水中煮沸1~3h,过滤、干燥,得到预处理沸石粉;配制一定浓度的高锰酸钾溶液;配制一定浓度的锰盐和酸溶液;将所述预处理沸石粉分散于水中,得到沸石水悬浊液;在60~80℃搅拌下,向所述沸石水悬浊液中同步滴加高锰酸钾溶液、锰盐和酸溶液,滴加完毕,70~90℃水热反应1~5h,过滤,水洗至中性,得到沸石负载锰氧化物。
38.在本发明中,所述弱酸缓冲溶液的ph值优选为3~5,更优选为3~4;所述弱酸缓冲溶液中的弱酸优选包括乙酸、柠檬酸、酒石酸或葡萄糖酸。在本发明的实施例中,所述弱酸缓冲溶液具体为乙酸-乙酸钠缓冲液,所述乙酸-乙酸钠缓冲液中乙酸与乙酸钠的总质量浓度优选为5~10%。
39.在本发明中,将所述预处理植物粉末、酶、磁性沸石-锰氧化物催化材料与弱酸缓冲溶液混合,优选包括以下步骤:将预处理植物粉末与弱酸缓冲溶液混合,得到预处理植物粉末分散液;将酶与弱酸缓冲溶液混合,得到酶分散液;将所述预处理植物粉末分散液、酶分散液与磁性沸石-锰氧化物催化材料混合。在本发明中,所述预处理植物粉末分散液中预处理植物粉末的浓度优选为40~60g/l,更优选为50g/l;所述酶分散液中酶的质量含量优选为0.01~1%,更优选为0.1~0.5%。
40.得到混合料液后,本发明在超声条件下将所述混合料液进行酶解处理,之后将所得体系中磁性沸石-锰氧化物催化材料磁分离,得到植物基固液混合碳源。在本发明中,所述超声的频率优选为10~50khz,更优选为40~50khz;所述超声的输入功率优选为0.01~10w/ml,更优选为0.1~5w/ml,进一步优选为0.5~1w/ml。在本发明中,所述酶解处理的温度优选为室温~100℃,更优选为40~50℃;时间优选为10~72h,更优选为60~72h。本发明采用磁性沸石-锰氧化物化学催化和生物酶催化,结合超声处理,能够安全高效的对纤维素进行酶解处理,提高植物有机物的微生物利用效率,同时磁性沸石-锰氧化物催化材料可以吸附降低体系中氨氮、磷酸盐等对微生物有害成分。
41.本发明提供了上述技术方案所述制备方法制备得到的植物基固液混合碳源。在本发明中,所述植物基固液混合碳源包括植物基固体和植物基液体,所述植物基固体的质量含量优选为10~90%,更优选为30~40%;优选地,所述植物基液体中cod为50000~500000mg/l,bod为50000~500000mg/l,bod/cod为0.5~1,nh
3-n为1~500mg/l,tn为1~500mg/l,po
43-为0.1~50mg/l,tp为0.1~50mg/l;更优选地,所述植物基液体中cod为100000~200000mg/l,bod为60000~160000mg/l,bod/cod为0.7~0.9,nh
3-n为100~280mg/l,tn为100~300mg/l,po
43-为5~25mg/l,tp为5~30mg/l。
42.下面将结合本发明中的实施例,对本发明中的技术方案进行清楚、完整地描述。显然,所描述的实施例仅仅是本发明一部分实施例,而不是全部的实施例。基于本发明中的实施例,本领域普通技术人员在没有做出创造性劳动前提下所获得的所有其他实施例,都属于本发明保护的范围。
43.以下实施例中相关材料来源以及制备方法:
44.植物:来安水稻秸秆。
45.沸石粉:粒径200~300目,广州鑫瓷环保材料有限公司。
46.食品级纤维素酶,酶活≥5000u/g;食品级纤维二糖酶,酶活≥4000u/ml;食品级果胶酶,酶活≥60000u/ml;食品级木聚糖酶,酶活≥28万u/g,宁夏夏盛实业集团有限公司。
47.浓硫酸(98wt%)、高锰酸钾、一水硫酸锰、七水硫酸亚铁、乙酸、乙酸钠均是国药试
剂。
48.磁性沸石-锰氧化物催化材料的制备方法,包括以下步骤:
49.步骤一:将100g沸石粉在100℃水中煮沸2h,过滤后100℃条件下干燥,得到预处理沸石粉,备用;配制40ml含高锰酸钾0.48g的溶液a及40ml含一水硫酸锰0.39g和浓硫酸0.5g的溶液b,将所述预处理沸石粉分散于水中,得到沸石水悬浊液200ml,在70℃搅拌条件下,向所述沸石水悬浊液中同步滴加溶液a和溶液b(高锰酸钾和硫酸锰的摩尔比为4:3,硫酸和硫酸锰的摩尔比为2:1),滴加完毕后,90℃条件下进行水热反应3h;反应完成后,将所得产物体系过滤,将所得滤饼水洗至中性,得到沸石负载锰氧化物;
50.步骤二:将所述沸石负载锰氧化物分散到200ml水中,同时加入超支化聚乙烯亚胺0.1g,进行超声分散,得到第一中间体系;
51.步骤三:将所述第一中间体系在曝气量为15l/min的条件下曝气,同时加热升温至90℃,向所得体系中滴加20ml含七水硫酸亚铁1.8g的溶液和20ml含氢氧化钠0.6g的溶液(硫酸亚铁与氢氧化钠的摩尔比为1:2.32),得到第二中间体系;
52.步骤四:将所述第二中间体系在曝气量为15l/min的条件下,恒温90℃搅拌反应3min,得到第三中间体系;
53.步骤五:将所述第三中间体系中的磁性催化材料进行磁分离,将所得磁性催化材料水洗后干燥至恒重,得到磁性沸石-锰氧化物催化材料
54.预处理植物粉末的制备方法,包括以下步骤:
55.步骤一:将植物在室温(25℃)条件下自然风干并破碎至100目,得到植物粉末;
56.步骤二:向所述植物粉末中加入含磁性沸石-锰氧化物催化材料1g和乙酸1g的弱酸水溶液1l,在80℃、50khz、0.01w/ml超声条件下进行预热处理5h,之后过滤并将所得滤饼水洗至中性,干燥,得到改性植物粉末;
57.步骤三:向所述改性植物粉末中加入含乙酸钠1g的弱碱水溶液1l,在200℃、1.5mpa条件下进行热水解处理1h,之后先将所得体系中磁性沸石-锰氧化物催化材料磁分离,再过滤并将所得滤饼水洗至中性,干燥,得到预处理植物粉末。
58.实施例1~6
59.步骤一:将预处理植物粉末100g分散到乙酸-乙酸钠缓冲液2l中,得到植物粉末分散液;
60.步骤二:将复合酶加入到所述乙酸-乙酸钠缓冲液中,得到复合酶分散液,所述复合酶分散液中复合酶的总质量浓度为0.5%;向所述植物粉末分散液中加入磁性沸石-锰氧化物催化材料和复合酶分散液,混合均匀,得到混合液;
61.步骤三:将所述混合液在50℃、50khz、0.5w/ml条件下超声震荡72h,之后磁分离去除磁性沸石-锰氧化物催化材料,剩余反应混合物直接作为植物基固液混合碳源使用。
62.实施例1~6中各步骤中相关操作条件见表1。
63.表1实施例1~6中各步骤中相关操作条件
[0064][0065]
备注:复合酶1的组成:纤维素酶100份、纤维二糖酶50份;
[0066]
复合酶2的组成:纤维素酶100份、纤维二糖酶50份、木聚糖酶10份和果胶酶10份。
[0067]
对比例1
[0068]
方法同实施例1,不同之处仅在于,将步骤一中预处理植物粉末替换成未经过预处理的植物粉末。
[0069]
对比例2
[0070]
方法同实施例1,不同之处仅在于,步骤二中不加入磁性沸石-锰氧化物催化材料。
[0071]
对比例3
[0072]
方法同实施例1,不同之处仅在于,步骤二中不加入复合酶。
[0073]
对比例4
[0074]
方法同实施例1,不同之处仅在于,步骤三中不施加超声处理条件。
[0075]
对比例1~4中各步骤中相关操作条件见表2。
[0076]
表2对比例1~4中各步骤中相关操作条件
[0077][0078]
将实施例1~6和对比例1~4中制备的植物基固液混合碳源进行过滤,得到的液体物料为酶解滤液;测试酶解滤液cod、氨氮、磷酸盐和还原糖浓度,其中,采用gb1191489、hj535-2009和gb/t 5750.5-2006测试酶解滤液cod、氨氮和磷酸盐浓度,采用3,5-二硝基水杨酸比色法测定酶解滤液还原糖浓度,结果见表3。
[0079]
表3实施例1~6和对比例1~4中酶解滤液cod、氨氮以及磷酸盐测试结果
[0080][0081][0082]
结果表明:本发明实施例方法酶解效率较高,且固液分离的酶解滤液cod和还原糖浓度高,可以被微生物利用;氨氮和磷酸溶度低,适合污水处理厂碳源使用。而对比例方法酶解不充分,酶解滤液cod和还原糖浓度较低,不易被微生物利用,不适合污水处理厂碳源使用。
[0083]
碳源效果评价
[0084]
将取自污水处理厂缺氧池的污水搅拌均匀后,加硝酸钙调节初始总氮浓度,取1l分别装入锥形瓶中,再在各个锥形瓶中加各实施例和对比例制备得到的碳源5g,100r/min低速磁力搅拌240min,检测初始总氮浓度和反硝化240min后的总氮浓度。结果见表4。
[0085]
表4碳源效果评价结果
[0086][0087][0088]
结果表明:本发明实施例方法酶解处理的植物较易被微生物作为碳源反消化利用,降低tn浓度,适合用于污水处理厂碳源。而对比例方法酶解处理不充分,不易被微生物作为碳源反消化利用。
[0089]
以上所述仅是本发明的优选实施方式,应当指出,对于本技术领域的普通技术人员来说,在不脱离本发明原理的前提下,还可以做出若干改进和润饰,这些改进和润饰也应视为本发明的保护范围。