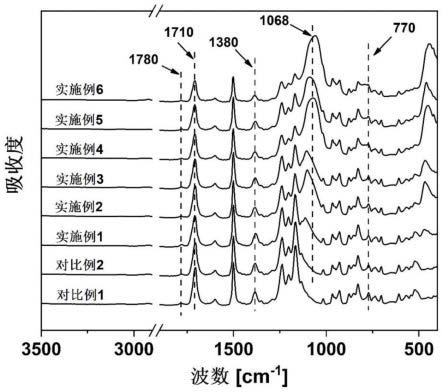
1.本发明属于功能性薄膜技术领域,具体涉及一种聚酰亚胺复合材料及其制备和应用。
背景技术:2.随着先进电工电子器件的快速发展,对于有机发光二极管显示器的需求量日益增加,它是当前柔性显示器中衬底材料主要使用的材料之一,而且其形式多样化,可以满足不同场景的使用需求。对于可折叠的柔性显示器而言,柔性显示器中柔性衬底材料需要具有良好的光学透明性、低热膨胀系数(cte)、高耐热性能和优异的机械性能。在有机高分子材料中被誉为“解决问题的能手”的聚酰亚胺(pi)材料吸引了广泛的关注。而这类材料中无色透明的pi薄膜是柔性显示材料的重要研究对象。传统聚酰亚胺薄膜的热膨胀系数在15~50ppm/℃,难以应用在柔性基板材料中,而柔性基板材料对pi薄膜的透明性也有更严苛的要求。因此,制备低cte值的无色透明聚酰亚胺薄膜显得尤为重要。
3.对于传统的全芳香族pi薄膜而言,合成方法一般是由二酐和二胺合成聚酰胺酸(paa),然后经亚胺化制得,因二胺残基具有给电子性,而二酐残基具有吸电子性,它们的相互作用导致了分子内电荷的运动,从而形成电子转移络合物(ctc),在生成ctc的同时对可见光产生明显的吸收,造成薄膜的光学性能下降。近年来,采用氢化均苯四甲酸二酐(hpmda)和4,4'-二氨基二苯醚(oda)合成可溶性pi树脂,再将这种可溶性树脂溶于极性有机溶剂中制成pi树脂溶液,在低于300℃的温度下固化成膜,最终得到一种无色透明pi薄膜的技术应用较为广泛。而对于合成树脂所用的单体而言,氢化均苯四甲酸二酐(hpmda)主要有顺式(cc-hpmda)和反式(ct-hpmda)两种结构,由顺式和反式酸酐合成的pi树脂在热学性能上有一定差异。虽然反式(ct)结构比顺式(cc)构制备的pi薄膜cte值低,但对于先进电工电子领域,这种pi薄膜的cte值仍然较高,难以真正广泛应用。
4.目前,降低pi薄膜cte的方法主要是将无机纳米粒子引入到pi薄膜中,制备有机/无机复合材料,因为无机材料本身具有优良的耐高温性能,根据复合材料的复合原理,最终所得到的有机/无机复合材料将具有较好的高温尺寸稳定性,这就达到了降低pi薄膜cte值的目的。然而,有机/无机复合材料中无机组分存在分散不均匀的问题,而且无机组分和有机材料的折射率需要匹配至小数点后第三位,才能防止光散射,由于使用过程中温度变化使树脂折射率发生变化,从而使得复合材料不透明,进而导致复合薄膜的综合性能受到影响,尤其是对复合薄膜光学性能的影响。因此,如何在赋予pi薄膜优良光学透明性的同时,实现其较低的cte值成为柔性显示领域中关注的问题。
技术实现要素:5.有鉴于此,本发明的目的在于提供一种聚酰亚胺复合材料及其制备和应用,本发明提供的聚酰亚胺薄膜在具有优良的光学透明性能的同时具有优异的热稳定性。
6.本发明提供了一种聚酰亚胺复合材料,包括共混的聚酰亚胺树脂和复合型纳米粒
子;所述复合型纳米粒子包括sio
2-细菌纤维素、sio
2-tio2或sio
2-al2o3;所述聚酰亚胺树脂和复合型纳米粒子的质量比为(95~65)∶(5~35)。
7.优选的,所述聚酰亚胺树脂具有式i所示结构:
[0008][0009]
式i中,n为聚合度,n为整数,且0《n≤200;
[0010]
r为或
[0011]
本发明还提供了上述技术方案所述聚酰亚胺复合材料的制备方法,包括以下步骤:
[0012]
将所述聚酰亚胺树脂和第一溶剂混合,得到聚酰亚胺树脂溶液;
[0013]
将复合型纳米粒子和第二溶剂混合,得到复合型纳米粒子分散液;
[0014]
将所述聚酰亚胺树脂溶液和复合型纳米粒子分散液混合后,进行固化,得到聚酰亚胺复合材料;所述复合型纳米粒子包括sio
2-细菌纤维素、sio
2-tio2或sio
2-al2o3;所述聚酰亚胺树脂和复合型纳米粒子的质量比为(95~65)∶(5~35)。
[0015]
优选的,所述聚酰亚胺树脂的制备方法包括以下步骤:
[0016]
将芳香族二胺单体、氢化均苯四甲酸二酐和第三溶剂混合后,进行聚合反应,得到聚酰胺酸溶液;
[0017]
将所述聚酰胺酸溶液、共沸剂和催化剂混合后,依次进行预酰亚胺化反应和完全酰亚胺化反应,得到聚酰亚胺树脂。
[0018]
优选的,所述芳香族二胺单体包括n,n'-(2,2'-双(三氟甲基)-[1,1'-联苯]-4,4'-二酰基)双(4-氨基苯甲酰胺)、2,2-双[4-(4-氨基苯氧基苯基)]六氟丙烷或4,4'-二氨基二苯醚;所述氢化均苯四甲酸二酐和芳香族二胺单体的摩尔比为(1.25~1.00):1。
[0019]
优选的,所述聚合反应的温度为10~35℃;所述聚合反应的时间为1~5h。
[0020]
优选的,所述聚酰亚胺树脂溶液中固含量为10~40wt.%;所述复合型纳米粒子分散液中复合型纳米粒子的浓度为5~30wt.%。
[0021]
优选的,所述固化的温度为200~300℃,所述固化的时间为2~10h,升温至所述固化的温度的速率为20~100℃/h。
[0022]
本发明还提供了上述技术方案所述的聚酰亚胺复合材料或上述技术方案所述制备方法制备得到的聚酰亚胺复合材料在柔性显示器中的应用。
[0023]
优选的,所述聚酰亚胺复合材料以聚酰亚胺复合薄膜的形式使用,所述聚酰亚胺
复合薄膜的制备方法包括以下步骤:将所述聚酰亚胺树脂溶液和复合型纳米粒子分散液混合后,复合于基板上,依次进行固化和脱模,得到聚酰亚胺复合薄膜;所述聚酰亚胺树脂溶液和复合型纳米粒子分散液为上述技术方案所述聚酰亚胺树脂溶液和复合型纳米粒子分散液。
[0024]
本发明提供了一种聚酰亚胺复合材料,包括共混的聚酰亚胺树脂和复合型纳米粒子;所述复合型纳米粒子包括sio
2-细菌纤维素、sio
2-tio2或sio
2-al2o3;所述聚酰亚胺树脂和复合型纳米粒子的质量比为(95~65)∶(5~35)。本发明提供的聚酰亚胺复合材料包括共混的聚酰亚胺树脂和复合型纳米粒子,所述复合型纳米粒子为sio2和细菌纤维素、sio2和tio2或sio2和al2o3形成的纳米粒子复合物,这种复合型纳米粒子能够均匀分散在可用于溶解聚酰亚胺树脂的溶剂中,因此它与聚酰亚胺树脂间具有良好的相容性和界面粘结性能,能够使复合型纳米粒子在聚酰亚胺树脂中均匀分散,此外,因其中无机纳米粒子具有较好的热稳定性,所以不会因温度变化而影响聚酰亚胺树脂的光学透明性能。而且复合型纳米粒子与单一无机纳米粒子sio2相比具有更强的机械性能和耐热性能、更低的热膨胀系数,从而使得聚酰亚胺薄膜在具有优良的光学透明性能的同时具有优异的热稳定性。
[0025]
进一步的,本发明在聚酰亚胺结构中引入含氟基团,氟元素具有较小的电子极化率、较高的电负性和f-c键能,含氟基团的引入可增大聚酰亚胺分子链之间的距离,降低分子链之间的相互作用,同时由于氟原子本身极强的电负性,c-f键高度极化,可以降低二胺的给电子效应,这两种效应协同阻碍了分子间或者分子内电荷转移络合物(ctc)的形成,提升了聚酰亚胺在可见光区域的透明性。
附图说明
[0026]
图1为实施例1~6的pi-sio
2-al2o3复合薄膜、对比例1的pi薄膜和对比例2的pi-sio2薄膜的红外光谱图;
[0027]
图2为实施例7~11的pi-sio
2-tio2复合薄膜、对比例3的pi薄膜和对比例4的pi-sio2薄膜的红外光谱图;
[0028]
图3为实施例12~15的pi-sio
2-bc复合薄膜、对比例5的pi薄膜和对比例6的pi-sio2薄膜的红外光谱图;
[0029]
图4为实施例1~6的pi-sio
2-al2o3复合薄膜、对比例1的pi薄膜和对比例2的pi-sio2薄膜的uv谱图;
[0030]
图5为实施例7~11的pi-sio
2-tio2复合薄膜、对比例3的pi薄膜和对比例4的pi-sio2薄膜的uv谱图;
[0031]
图6为实施例12~15的pi-sio
2-bc复合薄膜、对比例5的pi薄膜和对比例6的pi-sio2薄膜的uv谱图;
[0032]
图7为实施例1~6的pi-sio
2-al2o3复合薄膜、对比例1的pi薄膜和对比例2的pi-sio2薄膜的黄度谱图;
[0033]
图8为实施例7~11的pi-sio
2-tio2复合薄膜、对比例3的pi薄膜和对比例4的pi-sio2薄膜的黄度谱图;
[0034]
图9为实施例12~15的pi-sio
2-bc复合薄膜、对比例5的pi薄膜和对比例6的pi-sio2薄膜的黄度谱图;
[0035]
图10为实施例1~6的pi-sio
2-al2o3复合薄膜、对比例1的pi薄膜和对比例2的pi-sio2薄膜的tga谱图;
[0036]
图11为实施例7~11的pi-sio
2-tio2复合薄膜、对比例3的pi薄膜和对比例4的pi-sio2薄膜的tga谱图;
[0037]
图12为实施例12~15的pi-sio
2-bc复合薄膜、对比例5的pi薄膜和对比例6的pi-sio2薄膜的tga谱图;
[0038]
图13为实施例1~6的pi-sio
2-al2o3复合薄膜、对比例1的pi薄膜和对比例2的pi-sio2薄膜的tma谱图;
[0039]
图14为实施例7~11的pi-sio
2-tio2复合薄膜、对比例3的pi薄膜和对比例4的pi-sio2薄膜的tma谱图;
[0040]
图15为实施例12~15的pi-sio
2-bc复合薄膜、对比例5的pi薄膜和对比例6的pi-sio2薄膜的tma谱图。
具体实施方式
[0041]
本发明提供了一种聚酰亚胺复合材料,包括共混的聚酰亚胺树脂和复合型纳米粒子;所述复合型纳米粒子包括sio
2-细菌纤维素、sio
2-tio2或sio
2-al2o3;所述聚酰亚胺树脂和复合型纳米粒子的质量比为(95~65)∶(5~35)。
[0042]
在本发明中,所述聚酰亚胺树脂优选具有式i所示结构:
[0043][0044]
式i中,n为聚合度,n为整数,0《n≤200,
[0045]
r为或在本发明实施例中,所述聚酰亚胺树脂的结构具体如式ii、式iii和式iv所示:
[0046]
0<n≤100;
[0047]
0<n≤100;
[0048]
0<n≤100。
[0049]
在本发明中,所述复合型纳米粒子包括sio
2-细菌纤维素、sio
2-tio2或sio
2-al2o3;当所述复合型纳米粒子为sio
2-细菌纤维素时,所述sio2和细菌纤维素(bc)的质量比优选为(99~95):(1~5),更优选为(99~96):(2~4);当所述复合型纳米粒子为sio
2-tio2时,所述sio2和tio2的质量比优选为(95~90):(5~10),更优选为(94~92):(4~8);当所述复合型纳米粒子为sio
2-al2o3时,所述sio2和al2o3的质量比优选为(99~95):(1~5),更优选为(98~96):(2~4)。本发明对所述复合型纳米粒子的制备过程没有特殊限定,采用本领域熟知的制备过程使两种纳米粒子混合均匀即可。
[0050]
在本发明中,所述聚酰亚胺树脂和复合型纳米粒子的质量比优选为(95~65)∶(5~35),更优选为(90~75)∶(10~25)。
[0051]
本发明还提供了上述技术方案所述聚酰亚胺复合材料的制备方法,包括以下步骤:
[0052]
将所述聚酰亚胺树脂和第一溶剂混合,得到聚酰亚胺树脂溶液;
[0053]
将所述复合型纳米粒子和第二溶剂混合,得到复合型纳米粒子分散液;
[0054]
将所述聚酰亚胺树脂溶液和复合型纳米粒子分散液混合后,进行固化,得到聚酰亚胺复合材料;所述复合型纳米粒子包括sio
2-细菌纤维素、sio
2-tio2或sio
2-al2o3。
[0055]
如无特殊说明,本发明对所用原料的来源没有特殊要求,采用本领域技术人员所熟知的市售商品即可。
[0056]
本发明将所述聚酰亚胺树脂和第一溶剂混合,得到聚酰亚胺树脂溶液。
[0057]
在本发明中,所述聚酰亚胺的制备方法优选包括以下步骤:
[0058]
将芳香族二胺单体、氢化均苯四甲酸二酐和第三溶剂混合后,进行聚合反应,得到聚酰胺酸溶液;
[0059]
将所述聚酰胺酸溶液、共沸剂和催化剂混合后,依次进行预酰亚胺化反应和完全酰亚胺化反应,得到聚酰亚胺树脂。
[0060]
本发明优选将芳香族二胺单体、氢化均苯四甲酸二酐和第一溶剂混合后,进行聚合反应,得到聚酰胺酸溶液。
[0061]
在本发明中,所述芳香族二胺单体优选包括n,n'-(2,2'-双(三氟甲基)-[1,1'-联苯]-4,4'-二酰基)双(4-氨基苯甲酰胺)、2,2-双[4-(4-氨基苯氧基苯基)]六氟丙烷或4,
4'-二氨基二苯醚;
[0062]
所述n,n'-(2,2'-双(三氟甲基)-[1,1'-联苯]-4,4'-二酰基)双(4-氨基苯甲酰胺)(ab-tfmb)的cas号为1449757-11-2,结构式如下所示:
[0063][0064]
所述2,2-双[4-(4-氨基苯氧基苯基)]六氟丙烷(bdaf)的cas号为69563-88-8,结构式如下所示:
[0065][0066]
所述4,4'-二氨基二苯醚(oda)的cas号为101-80-4,结构式如下所示:
[0067][0068]
所述氢化均苯四甲酸二酐为1r,2s,4s,5r-氢化均苯四甲酸二酐(ct-hpmda),结构式如下所示:
[0069]
在本发明中,所述氢化均苯四甲酸二酐和芳香族二胺单体的摩尔比优选为(1.25-1.00):1;更优选为(1.10~1.02):1。
[0070]
在本发明中,所述第三溶剂优选包括n-甲基吡咯烷酮(nmp)、间甲酚、n,n-二甲基甲酰胺(dmf)、n,n-二甲基乙酰胺(dmac)、二甲基亚砜(dmso)和γ-丁内酯中的一种或几种,更优选为n-甲基吡咯烷酮、n,n-二甲基甲酰胺、n,n-二甲基乙酰胺或间甲酚;当所述第三溶剂为上述中的几种时,本发明对不同种类第三溶剂的配比没有特殊限定,任意配比均可;所述氢化均苯四甲酸二酐和芳香族二胺单体总质量优选为所述第三溶剂的质量的15~50wt.%,更优选为20~40wt.%。
[0071]
在本发明中,所述芳香族二胺单体、氢化均苯四甲酸二酐和第一溶剂的混合过程优选为先将芳香族二胺单体和部分第一溶剂混合,搅拌至固体溶解形成均相溶液,再加入氢化均苯四甲酸二酐和剩余第一溶剂,搅拌至固体溶解形成均相溶液。本发明对所述搅拌的过程没有特殊限定,采用本领域熟知的搅拌过程使固体物料完全溶解形成均相溶液即可。
[0072]
在本发明中,所述聚合反应的温度优选为10~35℃,更优选为15~25℃;所述聚合反应的时间优选为1~5h,更优选为1~2h;所述聚合反应优选在搅拌的条件下进行,本发明对所述搅拌的过程没有特殊限定,采用本领域熟知的搅拌过程即可;所述聚合反应优选在氮气环境中进行。在本发明中,所述聚酰胺酸溶液中固含量优选为10~40wt.%,更优选为15~30wt.%。
[0073]
得到聚酰胺酸溶液后,本发明优选将所述聚酰胺酸溶液、共沸剂和催化剂混合后,进行预酰亚胺化反应,得到预酰亚胺化反应产物。
[0074]
在本发明中,所述共沸剂优选包括甲苯;所述催化剂优选包括异喹啉;本发明对所述共沸剂和催化剂的用量没有特殊限定,采用本领域熟知的共沸剂和催化剂用量即可;所述预酰亚胺化反应的温度优选为130~140℃,更优选为130~135℃;所述预酰亚胺化反应的时间优选为2~20h,更优选为2~10h。
[0075]
预酰亚胺化反应完成后,本发明优选采用蒸馏的方式去除所述预酰亚胺化反应产物中的共沸剂。本发明对所述蒸馏的过程没有特殊限定,采用本领域熟知的蒸馏过程去除共沸剂即可。
[0076]
得到预酰亚胺化反应产物后,本发明优选将所述预酰亚胺化反应产物进行完全酰亚胺化反应,得到聚酰亚胺溶液。
[0077]
在本发明中,所述完全酰亚胺化反应的温度优选为180~250℃,更优选为180~230℃;所述完全酰亚胺化反应的时间优选为2~20h,更优选为6~15h。
[0078]
得到聚酰亚胺溶液后,本发明优选将所得聚酰亚胺溶液进行醇沉,得到聚酰亚胺树脂。
[0079]
在本发明中,所述醇沉的过程优选为在所述聚酰亚胺溶液中加入乙醇使白色聚酰亚胺树脂析出。本发明优选在进行醇沉前,将所得聚酰亚胺溶液冷却至室温,本发明对所述冷却的方式没有特殊限定,采用本领域熟知的冷却方式即可。本发明对所述乙醇的用量没有特殊限定,使聚酰亚胺完全析出即可。
[0080]
醇沉完成后,本发明优选将所述醇沉所得产物进行干燥,得到聚酰亚胺树脂。在本发明中,所述干燥的温度优选为120℃,所述干燥的时间优选为24h,所述干燥优选在真空的条件下进行。
[0081]
在本发明中,所述聚酰亚胺树脂溶液中固含量优选为5~30wt.%,更优选为10~25wt.%;所述第一溶剂优选包括n-甲基吡咯烷酮(nmp)、n,n-二甲基乙酰胺(dmac)、二甲基亚砜(dmso)和n,n-二甲基甲酰胺(dmf)中的一种或几种,更优选为n-甲基吡咯烷酮、n,n-二甲基乙酰胺、二甲基亚砜或n,n-二甲基甲酰胺;当所述第一溶剂为上述中的几种时,本发明对不同种类第一溶剂的配比没有过程没有特殊限定,采用本领域熟知的混合过程使聚酰亚胺完全溶解即可。
[0082]
本发明将所述复合型纳米粒子和第二溶剂混合,得到复合型纳米粒子分散液。
[0083]
在本发明中,所述复合型纳米粒子和第二溶剂的混合过程优选为将复合型纳米粒子和第二溶剂混合后,进行超声分散或机械搅拌,得到复合型纳米粒子分散液。在本发明中,所述超声分散的功率优选为300w,所述机械搅拌的转速优选为250rpm,所述超声分散或机械搅拌的时间独立优选为1~6h,更优选为2~4h;所述超声分散或机械搅拌的温度独立优选为10~50℃,更优选为15~40℃。本发明中,所述复合型纳米粒子分散液中复合型纳米粒子的浓度优选为5~30wt.%,更优选为10~25wt.%。
[0084]
在本发明中,所述第二溶剂优选包括n-甲基吡咯烷酮(nmp)、n,n-二甲基乙酰胺(dmac)、二甲基亚砜(dmso)和n,n-二甲基甲酰胺(dmf)中的一种或几种,更优选为n-甲基吡咯烷酮、n,n-二甲基乙酰胺、二甲基亚砜或n,n-二甲基甲酰胺;当所述第二溶剂为上述中的几种时,本发明对不同种类第二溶剂的配比没有特殊限定,任意配比均可。
sio
2-al2o3复合薄膜,该复合薄膜结构式如下:
[0094]
n=73。
[0095]
实施例2
[0096]
与实施例1的区别在于,复合型纳米粒子的质量为聚酰亚胺树脂和复合型纳米离子总质量的10%,其余内容与实施例1一致。
[0097]
实施例3
[0098]
与实施例1的区别在于,复合型纳米粒子的质量为聚酰亚胺树脂和复合型纳米离子总质量的15%,其余内容与实施例1一致。
[0099]
实施例4
[0100]
与实施例1的区别在于,复合型纳米粒子的质量为聚酰亚胺树脂和复合型纳米离子总质量的20%,其余内容与实施例1一致。
[0101]
实施例5
[0102]
与实施例1的区别在于,复合型纳米粒子的质量为聚酰亚胺树脂和复合型纳米离子总质量的25%,其余内容与实施例1一致。
[0103]
实施例6
[0104]
与实施例1的区别在于,复合型纳米粒子的质量为聚酰亚胺树脂和复合型纳米离子总质量的30%,其余内容与实施例1一致。
[0105]
实施例7
[0106]
在配有氮气入口、分水器以及温度计的1000ml三口瓶中加入55.847g(100mmol)n,n'-(2,2'-双(三氟甲基)-[1,1'-联苯]-4,4'-二酰基)双(4-氨基苯甲酰胺)(ab-tfmb)和100gn,n-二甲基乙酰胺(dmac),搅拌至溶解形成均相溶液;在上述均相溶液中加入22.417g(100mmol)氢化均苯四甲酸二酐(hpmda)及100gdmac搅拌至溶解形成均相溶液,然后在氮气环境下以25℃进行聚合反应2h,得到固含量为28wt.%的粘稠聚酰胺酸溶液;在所述聚酰胺酸溶液中加入0.5g异喹啉和150ml甲苯,在130℃下进行预酰亚胺化反应3h,然后蒸馏除去溶液中的甲苯,再升温至180℃进行完全酰亚胺反应6h,得到聚酰亚胺溶液;待所述聚酰亚胺溶液冷却至室温后,加入过量的乙醇,析出白色的聚酰亚胺树脂;将析出的聚酰亚胺树脂在120℃、真空的条件下干燥24h后,将12.04g上述聚酰亚胺树脂溶解于dmac中,配制成固含量为13wt.%聚酰亚胺树脂溶液;将0.3885gsio2、0.0205gtio2和2.7333gnmp溶剂混合后,在25℃下以300w超声分散2h,得到浓度为15wt.%的复合型纳米粒子分散液;然后将聚酰亚胺树脂溶液和复合型纳米粒子分散液混合后,在25℃下以300w超声分散4h,得到混合溶液;将所述混合溶液通过自动涂膜机均匀涂覆于干净的玻璃板上,置于100级洁净的程序控温干燥箱中,按照如下升温程序进行固化:80℃/3h,120℃/1h,150℃/1h,180℃/1h,250℃/1h,280℃/1h,将固化所得产物自然冷却至室温后,将玻璃板浸泡于去离子水中,剥离得到聚酰亚胺复合薄膜(pi-sio
2-tio2复合薄膜),该复合薄膜结构式如下:
[0107]
n=75。
[0108]
实施例8
[0109]
与实施例7的区别在于,复合型纳米粒子的质量为聚酰亚胺树脂和复合型纳米离子总质量的10%,其余内容与实施例7一致。
[0110]
实施例9
[0111]
与实施例7的区别在于,复合型纳米粒子的质量为聚酰亚胺树脂和复合型纳米离子总质量的15%,其余内容与实施例7一致。
[0112]
实施例10
[0113]
与实施例7的区别在于,复合型纳米粒子的质量为聚酰亚胺树脂和复合型纳米离子总质量的20%,其余内容与实施例7一致。
[0114]
实施例11
[0115]
与实施例7的区别在于,复合型纳米粒子的质量为聚酰亚胺树脂和复合型纳米离子总质量的25%,其余内容与实施例7一致。
[0116]
实施例12
[0117]
在配有氮气入口、分水器以及温度计的1000ml三口瓶中加入20.02g(100mmol)4,4'-二氨基二苯醚(oda)和100gn,n-二甲基乙酰胺(dmac),搅拌至溶解形成均相溶液;在上述均相溶液中加入22.417g(100mmol)氢化均苯四甲酸二酐(hpmda)及100gdmac搅拌至溶解形成均相溶液,然后在氮气环境下以25℃进行聚合反应2h,得到固含量为18wt.%的粘稠聚酰胺酸溶液;在所述聚酰胺酸溶液中加入0.5g异喹啉和150ml甲苯,在130℃下进行预酰亚胺化反应3h,然后蒸馏除去溶液中的甲苯,再升温至180℃进行完全酰亚胺化反应6h,得到聚酰亚胺溶液;待所述聚酰亚胺溶液冷却至室温后,加入过量的乙醇,析出白色的聚酰亚胺树脂;将析出的聚酰亚胺树脂在120℃、真空的条件下干燥24h后,将14.52g上述聚酰亚胺树脂溶解于n,n-二甲基乙酰胺(dmac)中,配制成固含量为16wt.%聚酰亚胺树脂溶液;将0.5978gsio2、0.0122g细菌纤维素(bc)和4.0667gnmp溶剂混合后,在25℃下以300w超声分散2h,得到浓度为15wt.%的复合型纳米粒子分散液;然后将聚酰亚胺树脂溶液和复合型纳米粒子分散液混合后,在25℃下以300w超声分散4h,得到混合溶液;将所述混合溶液通过自动涂膜机均匀涂覆于干净的玻璃板上,置于100级洁净的程序控温干燥箱中,按照如下升温程序进行固化:80℃/3h,120℃/1h,150℃/1h,180℃/1h,250℃/1h,280℃/1h,将固化所得产物自然冷却至室温后,将玻璃板浸泡于去离子水中,剥离得到聚酰亚胺复合薄膜(pi-sio
2-bc复合薄膜),该复合薄膜结构式如下:
[0118]
n=88。
[0119]
实施例13
[0120]
与实施例12的区别在于,复合型纳米粒子的质量为聚酰亚胺树脂和复合型纳米离子总质量的15%,其余内容与实施例12一致。
[0121]
实施例14
[0122]
与实施例12的区别在于,复合型纳米粒子的质量为聚酰亚胺树脂和复合型纳米离子总质量的20%,其余内容与实施例12一致。
[0123]
实施例15
[0124]
与实施例12的区别在于,复合型纳米粒子的质量为聚酰亚胺树脂和复合型纳米离子总质量的25%,其余内容与实施例12一致。
[0125]
对比例1
[0126]
与实施例1的区别在于,不加入复合型纳米粒子分散液,直接将聚酰亚胺溶液进行固化,得到聚酰亚胺薄膜(pi薄膜),其余内容与实施例1一致。
[0127]
对比例2
[0128]
与实施例1的区别在于,sio2的质量为聚酰亚胺树脂和sio2总质量的10%,得到(pi-sio2薄膜),其余内容与实施例1一致。
[0129]
对比例3
[0130]
与实施例7的区别在于,不加入复合型纳米粒子分散液,直接将聚酰亚胺溶液进行固化,得到聚酰亚胺薄膜(pi薄膜),其余内容与实施例7一致。
[0131]
对比例4
[0132]
与实施例7的区别在于,sio2的质量为聚酰亚胺树脂和sio2总质量的10%,得到(pi-sio2薄膜),其余内容与实施例7一致。
[0133]
对比例5
[0134]
与实施例12的区别在于,不加入复合型纳米粒子分散液,直接将聚酰亚胺溶液进行固化,得到聚酰亚胺薄膜(pi薄膜),其余内容与实施例12一致。
[0135]
对比例6
[0136]
与实施例12的区别在于,sio2的质量为聚酰亚胺树脂和sio2总质量的10%,得到(pi-sio2薄膜),其余内容与实施例12一致。
[0137]
性能测试:
[0138]
(1)红外光谱分析:
[0139]
采用德国bruker公司tensor 27型傅里叶变换红外光谱仪对实施例1~6的pi-sio
2-al2o3复合薄膜、对比例1的pi薄膜和对比例2的pi-sio2薄膜、实施例7~11的pi-sio
2-tio2复合薄膜、对比例3的pi薄膜和对比例4的pi-sio2薄膜、实施例12~15的pi-sio
2-bc复合薄膜、对比例5的pi薄膜和对比例6的pi-sio2薄膜进行全反射红外光谱测试,测试量程为400~4000cm-1
,结果如图1、图2和图3所示。
[0140]
由图1可知,聚酰亚胺的特征吸收峰,包括位于1780cm-1
处的不对称羰基伸缩振动峰、位于1710cm-1
处的对称羰基伸缩振动峰,以及c-n键位于1380cm-1
处的伸缩振动峰,除此之外,在1068cm-1
处观察到si-o键的特征吸收峰,该结构在对比例1中并未发现,说明sio2成功引入。
[0141]
由图2可知,聚酰亚胺的特征吸收峰,包括位于1785cm-1
处的不对称羰基伸缩振动峰、位于1710cm-1
处的对称羰基伸缩振动峰,以及c-n键位于1384cm-1
处的伸缩振动峰和位
于750cm-1
处的c=o弯曲振动峰,除此之外,在1070cm-1
处观察到si-o键的特征吸收峰,在467cm-1
处观察到ti-o键的特征吸收峰,该结构在对比例3中并未发现,说明sio2与tio2纳米粒子复合物成功引入。
[0142]
由图3可知,聚酰亚胺的特征吸收峰,包括位于1775cm-1
处的不对称羰基伸缩振动峰、位于1700cm-1
处的对称羰基伸缩振动峰,以及c-n键位于1380cm-1
处的伸缩振动峰和位于775cm-1
处的c=o弯曲振动峰,除此之外,在1068cm-1
处观察到si-o键的特征吸收峰,在2899cm-1
处观察到bc中的c-h键的特征吸收峰,该结构在对比例5中并未发现,说明sio2与bc纳米粒子复合物成功引入。
[0143]
(2)紫外-可见光谱分析:
[0144]
采用紫外-可见分光光度计(日本日立公司,u-3900)对实施例1~6的pi-sio
2-al2o3复合薄膜、对比例1的pi薄膜和对比例2的pi-sio2薄膜、实施例7~11的pi-sio
2-tio2复合薄膜、对比例3的pi薄膜和对比例4的pi-sio2薄膜、实施例12~15的pi-sio
2-bc复合薄膜、对比例5的pi薄膜和对比例6的pi-sio2薄膜进行紫外-可见光谱测试,结果如图4、图5和图6所示。
[0145]
由图4可知,测试的薄膜厚度在30~40μm之间,可以看出,sio
2-al2o3的引入并未对薄膜的透光率产生影响,实施例1~6与对比例1~2在400nm波长处的透光率均在79%以上,这说明胶体sio
2-al2o3纳米粒子能够均匀地分布在薄膜基体中,因此复合薄膜的透光率没有发生明显降低。
[0146]
由图5可知,测试的薄膜厚度在30~40μm之间,可以看出,sio
2-tio2的引入并未对薄膜的透光率产生影响,实施例7~11与对比例3~4在400nm波长处的透光率均在79%以上,这说明sio
2-tio2纳米粒子能够均匀地分布在薄膜基体中,因此复合薄膜的透光率没有发生明显降低。
[0147]
由图6可知,测试的薄膜厚度在30~40μm之间,可以看出,sio
2-bc的引入并未对薄膜的透光率产生影响,实施例12~15与对比例5~6在400nm波长处的透光率均在84%以上,这说明sio
2-bc纳米粒子能够均匀地分布在薄膜基体中,因此复合薄膜的透光率没有发生明显降低。
[0148]
(3)色度测试:
[0149]
采用测色仪(美国爱色丽公司,x-rite color i7型)对实施例1~6的pi-sio
2-al2o3复合薄膜、对比例1的pi薄膜和对比例2的pi-sio2薄膜、实施例7~11的pi-sio
2-tio2复合薄膜、对比例3的pi薄膜和对比例4的pi-sio2薄膜、实施例12~15的pi-sio
2-bc复合薄膜、对比例5的pi薄膜和对比例6的pi-sio2薄膜的色度进行测试,结果如图7、图8和图9所示。
[0150]
由图7可知,通过改变sio
2-al2o3的添加量制备了一系列复合薄膜,所有薄膜的厚度均在25~35μm之间,测试这些复合薄膜的颜色参数,可以看到,sio
2-al2o3的引入增加了薄膜的明度(l*),但sio
2-al2o3的引入并未对薄膜的颜色造成不利影响。
[0151]
由图8可知,通过改变sio
2-tio2的添加量制备了一系列复合薄膜,所有薄膜的厚度均在25~35μm之间,测试这些复合薄膜的颜色参数,可以看到,sio
2-tio2的引入增加了薄膜的明度(l*),但sio
2-tio2的引入并未对薄膜的颜色造成不利影响。
[0152]
由图9可知,通过改变sio
2-bc的添加量制备了一系列复合薄膜,所有薄膜的厚度均在25~35μm之间,测试这些复合薄膜的颜色参数,可以看到,sio
2-bc的引入增加了薄膜
的明度(l*),但sio
2-bc的引入并未对薄膜的颜色造成不利影响。
[0153]
(4)热重分析(tga)
[0154]
采用热重分析仪(美国铂金埃默尔公司,sta-8000型号)以10℃/min的升温速度在气体流量为20ml/min的氮气气氛下对实施例1~6的pi-sio
2-al2o3复合薄膜、对比例1的pi薄膜和对比例2的pi-sio2薄膜、实施例7~11的pi-sio
2-tio2复合薄膜、对比例3的pi薄膜和对比例4的pi-sio2薄膜、实施例12~15的pi-sio
2-bc复合薄膜、对比例5的pi薄膜和对比例6的pi-sio2薄膜进行热重分析测试,得到薄膜的5%失重温度(t
5%
)数据,结果如图10、图11和图12所示。
[0155]
由图10、图11和图12可知,复合型纳米粒子的引入提高了薄膜的热分解温度,随着复合型纳米粒子加入量的增加,复合薄膜的耐高温等级逐渐提高,且表现出了良好的耐热稳定性。这表明表明复合型纳米粒子的引入增加了薄膜的耐热稳定性,而这一性质的改善与所添加的无机物自身具有优良的耐热稳定性密切相关。
[0156]
(5)热膨胀系数测试:
[0157]
采用热机械分析仪(德国耐驰公司,402f3 polymer版)以10℃/min的升温速度在气体流量为20ml/min的氮气气氛下对实施例1~6的pi-sio
2-al2o3复合薄膜、对比例1的pi薄膜和对比例2的pi-sio2薄膜、实施例7~11的pi-sio
2-tio2复合薄膜、对比例3的pi薄膜和对比例4的pi-sio2薄膜、实施例12~15的pi-sio
2-bc复合薄膜、对比例5的pi薄膜和对比例6的pi-sio2薄膜进行热膨胀测试,结果如图13、图14和图15所示。
[0158]
由图13、图14和图15可知,热机械分析(tma)是表征薄膜类材料热膨胀系数常用的手段之一。通过分析测试,可以研究复合型纳米粒子的引入对薄膜高温尺寸稳定性的影响。随着复合型纳米粒子添加量的增加,复合薄膜的尺寸变化越来越小,呈现出逐渐递减的趋势。这说明复合型纳米粒子的引入明显地增加了薄膜的高温尺寸稳定性。而复合薄膜高温尺寸稳定性的增加归因于所添加无机物本身优异的热稳定性。
[0159]
(6)实施例1~6的pi-sio
2-al2o3复合薄膜、对比例1的pi薄膜和对比例2的pi-sio2薄膜、实施例7~11的pi-sio
2-tio2复合薄膜、对比例3的pi薄膜和对比例4的pi-sio2薄膜、实施例12~15的pi-sio
2-bc复合薄膜、对比例5的pi薄膜和对比例6的pi-sio2薄膜的测试性能如表1所示,测试方法如上文所述。
[0160]
表1不同案例的聚酰亚胺复合薄膜的性能
[0161][0162]
由表1可知,对比例1是未做任何改性处理的pi薄膜,对比例2是在对比例1的基础上将sio2溶液与聚酰亚胺树脂溶液复合制备pi-sio2复合薄膜,可以看到,sio2的引入使得薄膜的cte值降低。实施例1中制备的pi-sio
2-al2o3复合薄膜的综合性能得到一定改善,主要表现在透光率的保持和cte值的降低。另外,其热学性能也有了一定的改善,实施例在750℃下的残重百分数明显高于对比例。实施例2在实施例1基础上增加了sio
2-al2o3溶液的添加量,结果其在50~250℃下的cte值得到少许降低。实施例1~6俱是在对比例2的基础上使用sio
2-al2o3溶液作为无机填料,并逐渐提高sio
2-al2o3溶液的添加量,结果可以发现,与对比例2相比,实施例1~6在50~250℃下的cte值发生较为明显地降低,在400nm处的透光率均能保持在81%以上,此外,750℃下的残重百分数也得到了比较明显地增加,sio2和al2o3本身的热学性质稳定,因而pi-sio
2-al2o3复合薄膜的热学性能的改善归因于纳米无机材料的引入。
[0163]
由表1可知,对比例3是未做任何改性处理的pi薄膜,对比例4是在对比例1的基础上将sio2溶液与聚酰亚胺树脂溶液复合制备pi-sio2复合薄膜,可以看到,sio2的引入使得薄膜的cte值降低。实施例7中制备的pi-sio
2-tio2复合薄膜的综合性能得到一定改善,包括透光率的改善和cte值的降低,另外,其热学性能也有了一定的改善。实施例8在实施例7基础上增加了sio2-tio2混合液的添加量,结果其50~250℃下的cte值降低。实施例7~11俱是在对比例4的基础上使用sio
2-tio2溶液作为无机填料,并逐渐提高sio
2-tio2溶液的添加量,结果可以发现,与对比例4相比,实施例7~11在50~250℃下的cte值发生较为明显地降
低,在400nm处的透光率均能保持在79%以上,此外,750℃下的残重百分数也得到了比较明显地增加,sio2和tio2本身的热学性质稳定,因而pi-sio
2-tio2复合薄膜的热学性能的改善归因于纳米无机材料的引入。
[0164]
由表1可知,实施例12中制备的pi-sio
2-bc复合薄膜的综合性能得到一定改善,包括透光率和cte值的降低,另外,其热学性能也有了一定的改善。实施例13在实施例12基础上增加了sio
2-bc溶液的添加量,结果其50~250℃下的cte值降低,而在400nm处的透光率也得到一定提高。实施例13~15俱是在实施例12的基础上增加sio
2-bc混合液的添加量,结果可以发现,与对比例5相比,实施例13~15在50~250℃下的cte发生显著降低,在400nm处的透光率均能保持在80%以上,此外,5%失重温度也得到了一定的提高,750℃下的残重百分数也明显增加,热学性能的改善归因于纳米无机材料的引入。
[0165]
尽管上述实施例对本发明做出了详尽的描述,但它仅仅是本发明一部分实施例而不是全部实施例,人们还可以根据本实施例在不经创造性前提下获得其他实施例,这些实施例都属于本发明保护范围。