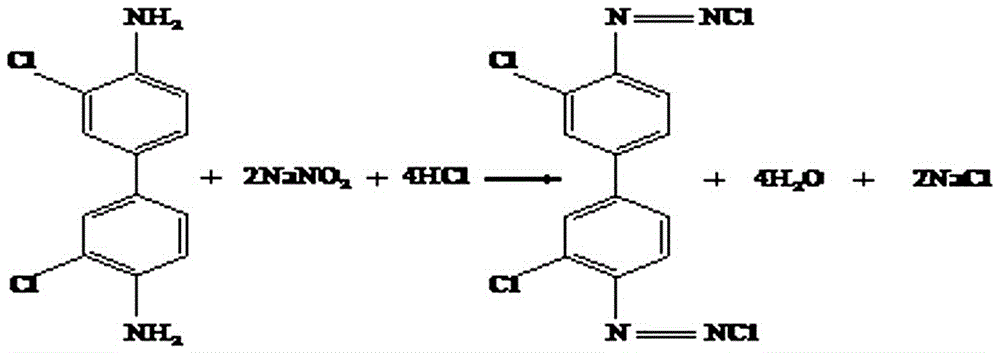
本发明属于煤焦油及精细化工领域,更具体地涉及一种环保型有机颜料联苯胺黄g的生产方法。
背景技术:
:目前中国不仅是有机颜料的生产大国,同时也逐渐成为有机颜料的应用大国。颜料已进入到人们生活的各个领域,五彩缤纷的颜色给人们带来了无尽的欢乐。随着世界物质和精神文明的迅速发展,人们对身体健康的高度重视,因而面对产品的环保性引起极大关注,针对有机颜料的安全环保问题,欧盟于2007年6月1日首先颁布了reach法规,规定有机颜料禁止使用具有致癌性的二十四种芳香胺,八大有害重金属不能超标,并且国外强调低污染化和达到高性能的两个目标结合研究;为了改善生态环境,开拓有机颜料国内外市场,有机颜料也必须达到环保要求。鉴于此,我们设计开发了环保型有机颜料联苯胺黄g。专利号为201310327338.3的国家发明专利公开了一种联苯胺黄g的重氮液的制备工艺,利用了包括以下步骤:双氯打浆:在重氮桶内加入650-750kg水,105-125kg浓度为30-35%盐酸、60-80kg双氯,搅拌打浆至少1h,加冰块,使桶内料液降温至0℃以下;重氮化:将浓度为38-42%的38.4-39kg亚硝酸钠加入桶内,于5℃以下温度反应40-90min,投入0.9-1.5kg活性炭,搅拌3-10min,加水使总体积达1050-1150l,加稀释9-11倍后太古油0.3-0.7kg,搅拌至少1min,静止;吸滤:吸滤时,将重氮液通过布袋过滤,该法公开的联苯胺黄g的重氮液的制备工艺可避免双氯发生自偶反应,产生有毒气体比较少;但是该法的缺点是:反应后期完成后ph值低,未反应的双氯不可避免的会发生自偶反应,导致联苯胺黄收率降低。技术实现要素:为解决上述问题,克服现有技术的不足,本发明提供了一种环保型有机颜料联苯胺黄g的生产方法,解决的第一个技术问题是:由于联苯胺黄g本身的亲水性/亲油性导致解吸附现象,分散稳定性差,使颜料在应用过程中,粘度较高,研磨产出效率较低,颜料含量较低,且分散体稳定性能较差;解决的第二个技术问题是:联苯胺黄g的重氮化反应中产生严重的自偶反应,导致产品收率降低;解决的第三个技术问题是:污水中盐总量较高;cod较高。本发明解决上述技术问题的具体技术方案为:环保型有机颜料联苯胺黄g的生产方法,包括打浆工序、重氮化工序、酸析工序、耦合工序及水洗、抽滤和烘干,其特征在于:所述打浆工序包括:将3,3-二氯联苯胺盐酸盐、水和31%的盐酸加入重氮罐,混合打浆0.5小时;所述重氮化工序包括:向重氮罐中加冰降温至t=-2-0℃,加入溶解好的浓度为30%的亚硝酸钠溶液,至淀粉碘化钾试纸深蓝色,搅拌1.5小时得重氮液;所述的酸析工序包括:将乙酰乙酰苯胺、水、31%液碱加入偶合罐,然后加入surfonamine胺(聚醚胺),搅拌化清;最后将浓度40%的醋酸加入偶合罐中,进行酸析,酸析时间0.5小时;所述耦合工序包括:将酸析完的温度20℃,ph=6.0的偶合液,把制备好的重氮液加入到偶合罐中,进行偶合反应,反应时间3小时,终点ph不低于3.8;偶合完毕,升温t=85-95℃,保温0.5小时后进行水洗、抽滤和烘干。进一步地,所述打浆工序中3,3-二氯联苯胺盐酸盐、水和31%盐酸反应摩尔比为:1:1.5:2-4。进一步地,所述酸析工序中乙酰乙酰苯胺、水、31%液碱反应摩尔比为:1:1.5:1.5。进一步地,所述的重氮化工序包括:向重氮罐中加冰降温至t=-2-0℃,加入溶解好的浓度30%的亚硝酸钠溶液,至淀粉碘化钾试纸深蓝色,搅拌1.5小时,然后加入碳酸钙,调整体系ph值至3-4,得重氮液。进一步地,所述乙酰乙酰苯胺与surfonamine胺(聚醚胺)反应的摩尔比为:50:1。本发明的有益效果是:1、通过本发明方法研制的联苯胺黄g收率高,与不同类型展色料或介质体系有良好的相容性和易分散性能,在水性涂料着色体系中不发胀,具有良好的储存稳定性,不发生分层与沉淀现象;2、重氮液中添加碳酸钙调整ph值,可防止已经反应好的重氮液自偶,提高收率5%,同时可减少偶合过程中液碱的添加量,减少废水中cod;3、surfonamine胺(聚醚胺)产品结构中一端的活性胺基,通过与颜料颗粒表面某些活性基团的化学反应,使其链状结构得以同颜料颗粒紧密的连接在一起,以化学作用连接到颜料表面的surfonamine胺(聚醚胺),因其结构中环氧乙烷/环氧丙烷(eo/po)长链所具有的亲水性/亲油性,从而能够改善颜料本身的亲水性/亲油性;可明显降低解吸附现象,导致粒子表面改性,改进分散稳定性,使颜料在应用过程中,可降低粘度,提高研磨产出效率,增加颜料含量,且分散体具有高的储存稳定性能,使颜料适用性更加广泛。附图说明:附图1是本发明的重氮化反应式;附图2是本发明的偶合反应式;具体实施方式:在本发明的描述中具体细节仅仅是为了能够充分理解本发明的实施例,但是作为本领域的技术人员应该知道本发明的实施并不限于这些细节。另外,公知的结构和功能没有被详细的描述或者展示,以避免模糊了本发明实施例的要点。对于本领域的普通技术人员而言,可以具体情况理解上述术语在本发明中的具体含义。本发明的具体实施方式:实施例1:1、重氮罐加水3000l,加入588kg31%盐酸、400kg3,3-二氯联苯胺盐酸盐打浆0.5小时;2、向重氮罐中加冰降温t=-2-0℃,加入浓度为30%的225kg亚硝酸钠溶液进行重氮化,淀粉碘化钾试纸深蓝色,搅拌1.5小时,然后加入40kg碳酸钙,调整体系ph值至3-4,得重氮液;3、偶合罐中加入5000l水、580kg乙酰乙酰苯胺、20kgsurfonamine胺(聚醚胺)和620kg31%液碱,搅拌化清;4、将220kg醋酸加入偶合罐中,进行酸析,酸析时间0.5小时;5、酸析完的偶合液温度20℃,ph=6.0,把重氮液加入到偶合罐中进行耦合反应,反应时间3小时,终点ph不低于3.8;6、偶合完毕,升温t=90℃,保温0.5小时后进行水洗、抽滤和烘干。7.通过本实施例,颜料收率为99%,着色力101%。实施例21、重氮罐加水3000l,加入588kg31%盐酸、400kg3,3-二氯联苯胺盐酸盐打浆0.5小时,2、向重氮罐中加冰降温t≤0℃,加入溶解好的浓度30%的225kg亚硝酸钠溶液进行重氮化,淀粉碘化钾试纸深蓝色,搅拌1.5小时,然后加入40kg碳酸钙,调整体系ph值至3-4,得重氮液;3、偶合罐中加入水5000l、580kg乙酰乙酰苯胺、20kgsurfonamine胺(聚醚胺)和620kg31%液碱,搅拌化清;4、将220kg醋酸加入偶合罐中,进行酸析,酸析时间0.5小时;5、酸析完的偶合液温度20℃,ph=6.0,把重氮液加入到偶合罐中进行耦合反应,反应时间3小时,终点ph不低于3.8;6、偶合完毕,升温t=85℃,保温0.5小时后进行水洗、抽滤和烘干。7、通过本实施例,颜料收率为95%,着色力96%。实施例31、重氮罐加水3000l,加入470kg31%盐酸、400kg3,3-二氯联苯胺盐酸盐打浆0.5小时,2、向重氮罐中加冰降温t≤0℃,加入溶解好的浓度30%的225kg亚硝酸钠溶液进行重氮化,淀粉碘化钾试纸深蓝色,搅拌1.5小时,然后加入40kg碳酸钙,调整体系ph值至3-4,得重氮液;3、偶合罐中加入5000l水、580kg乙酰乙酰苯胺、20kgsurfonamine胺(聚醚胺)和620kg31%液碱,搅拌化清;4、将220kg醋酸加入偶合罐中,进行酸析,酸析时间0.5小时;5、酸析完的偶合液温度20℃,ph=6.0,把重氮液加入到偶合罐中进行耦合反应,反应时间3小时,终点ph不低于3.8;6、偶合完毕,升温t=90℃,保温0.5小时后进行水洗、抽滤和烘干。7、通过本实施例,颜料收率95%,着色力99%。实施例41、重氮罐加水3000l,加入470kg31%盐酸、400kg3,3-二氯联苯胺盐酸盐打浆0.5小时,2、向重氮罐中加冰降温t≤0℃,加入溶解好的浓度30%的225kg亚硝酸钠溶液进行重氮化,淀粉碘化钾试纸深蓝色,搅拌1.5小时,然后加入40kg碳酸钙,调整体系ph值至3-4,得重氮液;3、偶合罐中加入5000l水、580kg乙酰乙酰苯胺和620kg31%液碱,搅拌化清;4、将220kg醋酸加入偶合罐中,进行酸析,酸析时间0.5小时;5、酸析完的偶合液温度20℃,ph=6.0,把重氮液加入到偶合罐中进行耦合反应,反应时间3小时,终点ph不低于3.8;6、偶合完毕,升温t=90℃,保温0.5小时后进行水洗、抽滤和烘干。7、通过本实施例,颜料收率93%,着色力98%。实施例51、重氮罐加水3000l,加入470kg31%盐酸、400kg3,3-二氯联苯胺盐酸盐打浆0.5小时,2、向重氮罐中加冰降温t≤0℃,加入溶解好的浓度30%的225kg亚硝酸钠溶液进行重氮化,淀粉碘化钾试纸深蓝色,搅拌1.5小时,得重氮液;3、偶合罐中加入5000l水、580kg乙酰乙酰苯胺、20kgsurfonamine胺(聚醚胺)和620kg31%液碱,搅拌化清;4、将220kg醋酸加入偶合罐中,进行酸析,酸析时间0.5小时;5、酸析完的偶合液温度20℃,ph=6.0,把重氮液加入到偶合罐中进行耦合反应,反应时间3小时,终点ph不低于3.8;6、偶合完毕,升温t=90℃,保温0.5小时后进行水洗、抽滤和烘干。7、通过本实施例,颜料收率96%,着色力99%。本发明方法中实施例1-5制备的颜料联苯胺黄g,其性能指标如下表:表1本发明方法制备的颜料联苯胺黄g性能指标项目指标检验方法(1)外观黄色粉末目视评定(2)色光与标准近似至微gb1864-80(3)着色力(与标准品相比)/%95-105gb1708-79(4)水溶物%≤2gb1718-79(5)细度(80目筛余物)%≤2gb1715-79(6)吸油量/%30-40gb1712-79表2:本发明方法制备的颜料联苯胺黄g酸析工序的工艺性能指标组别酸析工序重氮化工序颜料收率颜料色力实施例1添加聚醚胺添加碳酸钙99100实施例2添加聚醚胺添加碳酸钙9596实施例3添加聚醚胺添加碳酸钙9599实施例4添加聚醚胺——9398实施例5——添加碳酸钙9699由上表数据分析可知:在联苯胺黄g的实际生产过程中,重氮化工序添加碳酸钙,可提高颜料生产收率;酸析工序添加聚醚胺,可提高颜料色力。一:为了更加直观的展现本发明的酸析工序中添加surfonamine胺(聚醚胺)的工艺优势,特以:现有技术ⅰ:一种联苯胺黄g的重氮液的制备工艺(按照国家发明专利201310327338.3,所述的方法进行生产联苯胺黄g,以援引方式引入);实施例5:采用单一变量的原则,将酸析工序中添加surfonamine胺(聚醚胺);对比例1:相对于实施例5采用单一变量的原则,酸析工序中未采用添加surfonamine胺(聚醚胺);对制备的颜料联苯胺黄g在水性油墨中储存稳定性性能指标进行检测和评定:表3:酸析工序中添加surfonamine胺(聚醚胺)的工艺性能指标组别酸析工序重氮化工序储存反稠时间现有技术ⅰ————7天出现反稠实施例5添加聚醚胺——14天未出现反稠现象对比例1————10天出现反稠由上表数据分析可知:对比现有联苯胺黄g的生产技术,该方案在酸析工序中加入聚醚胺,可有效提高联苯胺黄g在水性油墨中的储存稳定性。二:为了更加直观的展现本发明的重氮化工序中加入碳酸钙的工艺优势,特以:现有技术ⅰ:一种联苯胺黄g的重氮液的制备工艺(按照国家发明专利201310327338.3,所述的方法进行生产联苯胺黄g,以援引方式引入);实施例4:采用单一变量的原则,将重氮化工序中加入碳酸钙;对比例2:相对于实施例4采用单一变量的原则,重氮化工序中未加入碳酸钙;对比例3:相对于实施例4采用单一变量的原则,重氮化工序中加入氢氧化钠调整体系ph值至3-4,得重氮液;对制备的颜料联苯胺黄g的收率进行检测和评定:表4:重氮化工序中加入碳酸钙性能指标组别酸析工序重氮化工序ph收率现有技术ⅰ————195实施例4——添加碳酸钙3-4100对比例2————196对比例3——加氢氧化钠3-490由上表数据分析可知:通过对比现有技术和对比例2,颜料收率基本一致;对比重氮化工序添加碳酸钙的实施例4和现有技术,发现可明显提高颜料收率;对比实施例4和对比例3发现,加入氢氧化钠调节重氮液ph值,不仅不会提高收率,反而会导致收率下降。综上所述:通过本发明方法研制的联苯胺黄g,收率高,与不同类型展色料或介质体系有良好的相容性和易分散性能,在水性涂料着色体系中不发胀,具有良好的储存稳定性,不发生分层与沉淀现象;重氮液中添加碳酸钙调整ph值,可防止已经反应好的重氮液自偶,提高收率5%,同时可减少偶合过程中液碱的添加量,减少废水中cod。当前第1页12