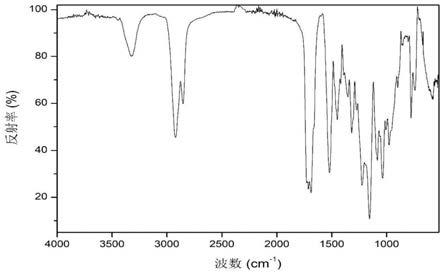
1.本技术涉及涂料和汽车漆面保护膜领域,特别涉及一种汽车漆面保护膜用耐黄变自修复涂层组合物、汽车漆面保护膜及该汽车漆面保护膜的制备方法。
背景技术:2.随着经济的发展、人们购买力的增强,汽车已经走入千家万户。作为高价值物品,汽车的维护与保养显得特别重要。汽车漆面保护膜又称隐形车衣或者车衣膜,贴在汽车面漆之上时可以有效减轻或避免物理刮擦、光照、氧气、腐蚀性物质对汽车原厂漆的伤害,同时易于修复,更换成本低。
3.目前,车衣膜的生产厂商国外主要有3m、龙膜、威固、xpel等,国内主要有康得新、乐凯、博卡等。由于国内起步较晚,产品质量相较国外差一些,但根据市场反馈,即使是高端的tpu车衣膜,在防污、抗刮、耐黄变、修复性上仍存在大大小小不同的问题。为了解决以上问题,目前通用的方案是优化tpu基膜上涂布的自修复涂层。例如,中国专利cn 202011571702.7公开了一种具有自修复功能的耐黄变隐形车衣保护膜,在自修复涂层中添加小分子紫外线吸收剂,有效的改善了车衣膜的耐黄变性能。但是,该技术添加的紫外线吸收剂是小分子,不参与树脂体系的反应,在使用过程中仍有析出风险。
技术实现要素:4.本技术之目的在于提供一种耐黄变自修复涂层组合物,从而解决上述技术问题。
5.本技术之目的还在于提供一种由如上所述的耐黄变自修复涂层组合物制成的汽车漆面保护膜。
6.本技术之目的还在于提供一种如上所述的汽车漆面保护膜的制备方法。
7.为了解决上述技术问题,本技术提供下述技术方案:
8.在第一方面中,本技术提供一种耐黄变自修复涂层组合物,其特征在于,以重量份数为基准计,其包含以下原料:
[0009][0010]
其中所述羟基封端聚氨酯预聚体与所述支链化羟基聚酯共100重量份。
[0011]
在第一方面的一种实施方式中,所述羟基封端聚氨酯预聚体由以下原料合成:聚
醚三元醇;聚酯二元醇;反应性润湿流平剂;反应性滑爽剂;反应性紫外线吸收剂;抗氧剂;脂肪族二异氰酸酯;第二溶剂以及第二催化剂。
[0012]
在第一方面的一种实施方式中,所述的聚醚三元醇选自但不限于聚氧化丙烯/氧化乙烯共聚三醇、聚氧化丙烯三醇中的一种或多种,且所述的聚醚三元醇的数均分子量为1000-10000。
[0013]
在第一方面的一种实施方式中,所述的聚酯二元醇选自但不限于聚己内酯二醇、聚己二酸新戊二醇酯二醇、聚己二酸己二醇酯二醇、聚二甘醇己二酸酯二醇、聚丁二醇新戊二醇己二酸酯二醇、聚己二酸甲基丙二醇酯二醇、聚碳酸酯二元醇中的一种或几种,且所述的聚酯多元醇的数均分子量为1000-4000。
[0014]
在第一方面的一种实施方式中,所述的反应性润湿流平剂为有机硅改性聚醚多元醇。
[0015]
在第一方面的一种实施方式中,所述的反应性防污滑爽剂选自全氟聚醚醇和全氟聚醚酰胺乙基醇中的一种。
[0016]
在第一方面的一种实施方式中,所述的反应性紫外线吸收剂选自带有活性羟基的二苯甲酮类和苯并三唑类紫外光吸收剂中的一种或两种。
[0017]
在第一方面的一种实施方式中,所述的脂肪族二异氰酸酯选自1,6-已二异氰酸酯、异佛尔酮二异氰酸酯、以及双环己基甲烷二异氰酸酯中的一种或两种。
[0018]
在第一方面的一种实施方式中,所述的抗氧剂选自抗氧剂1010、抗氧剂1076、抗氧剂245、抗氧剂1135中的一种。
[0019]
在第一方面的一种实施方式中,所述第二催化剂选自有机锡和有机铋催化剂中的一种。
[0020]
在第一方面的一种实施方式中,所述第二溶剂选自但不限于乙酸乙酯、乙酸丁酯、碳酸二甲酯、丁酮、甲苯和二甲苯中的一种或多种。
[0021]
在第一方面的一种实施方式中,所述的聚醚三元醇的数均分子量为3000-6000。
[0022]
在第一方面的一种实施方式中,所述有机硅改性聚醚多元醇选自端羟基单官能度有机硅改性聚醚、端羟基两官能度有机硅改性聚醚以及侧羟基两官能度有机硅改性聚醚中的一种。
[0023]
在第一方面的一种实施方式中,所述羟基封端聚氨酯预聚体通过以下方法来制备:
[0024]
1)使聚醚三元醇、聚酯二元醇、反应性润湿流平剂、反应性滑爽剂、反应性紫外线吸收剂、脂肪族异氰酸酯以及抗氧剂在第二溶剂中且在50~60℃的反应温度下混合均匀,得到第一反应混合物;
[0025]
2)向所述第一反应混合物中加入第二催化剂,逐步升温至85-95℃,常压反应,当nco含量降为零时,出料即得所述羟基封端聚氨酯预聚体。
[0026]
在第一方面的一种实施方式中,在步骤2)中,在逐步升温至85-95℃以后,常压反应4-6小时后,每半小时测定一次nco含量,直到nco含量降为零。
[0027]
在第一方面的一种实施方式中,所述支链化羟基聚酯选自科思创desmophen670和巴斯夫sovermol 1052中的一种或两种。
[0028]
在第一方面的一种实施方式中,所述的扩链剂选自1,4-丁二醇、二甘醇和新戊二
醇中的一种;
[0029]
在第一方面的一种实施方式中,所述的固化剂选自巴斯夫basonat hi100、巴斯夫basonat hi190 b/s、异佛尔酮二异氰酸酯和双环己基甲烷二异氰酸酯中的一种。
[0030]
在第一方面的一种实施方式中,所述第一催化剂选自有机锡和有机铋催化剂中的一种。
[0031]
在第一方面的一种实施方式中,所述第一溶剂选自但不限于乙酸乙酯、乙酸丁酯、碳酸二甲酯、丁酮、甲苯和二甲苯中的一种或多种。
[0032]
在第二方面中,本技术提供一种汽车漆面保护膜,所述汽车漆面保护膜从上到下依次包括pet离型膜、耐黄变自修复涂层、tpu基膜、丙烯酸压敏胶、pet离型膜,所述耐黄变自修复涂层由第一方面所述的耐黄变自修复涂层组合物制成。
[0033]
在第三方面中,本技术提供一种汽车漆面保护膜的制备方法,其特征在于,所述方法包括以下步骤:
[0034]
s1:将如第一方面所述的耐黄变自修复涂层组合物的原料组分使用分散机高速分散10min,转速为400-1000rpm,得到自修复涂布液;
[0035]
s2:将丙烯酸压敏胶水涂布于pet离型膜上,100℃烘干后形成丙烯酸胶层,并与tpu基膜复合;然后,将所述自修复涂布液涂布于tpu基膜的另一面,采用阶梯升温的方式90℃/120℃/150℃干燥固化,得到耐黄变自修复涂层,并在耐黄变自修复涂层表面复合另一pet离型膜,放入烘箱,50℃熟化,得到所述的汽车漆面保护膜。
[0036]
在第三方面的一种实施方式中,在步骤s2中,所述将所述自修复涂布液涂布于tpu基膜上包括利用线棒将所述自修复涂布液涂布于tpu基膜上。
[0037]
与现有技术相比,本技术的有益效果在于:
[0038]
(1)组合料采用支链化聚酯多元醇配合多官能度异氰酸酯固化剂,受热固化后的涂层在热水加热条件下对划痕具有快速的自修复能力,同时自修复涂层光滑致密,具有优异的抗物理划伤能力;
[0039]
(2)整个组合料体系为纯脂肪族,不含双键、苯环等不饱和键,另外通过羟基封端的聚氨酯预聚体引入反应性紫外线吸收剂,施工固化后的涂层具有优异的耐黄变性能;
[0040]
(3)通过反应性防污滑爽剂引入氟碳链段,自组装效应诱导氟碳链段迁移至涂层表面,极大的降低了涂层的表面张力,使其具有优异的防水防油防污性能;
[0041]
以及,(4)所用流平、滑爽、抗黄变类助剂皆为反应性助剂,不存在析出风险。
附图说明
[0042]
图1显示根据实施例1的羟基封端聚氨酯预聚体红外吸收光谱。
[0043]
图2显示根据实施例2的羟基封端聚氨酯预聚体红外吸收光谱。
[0044]
图3显示根据实施例3的羟基封端聚氨酯预聚体红外吸收光谱。
[0045]
图4显示根据本技术的一种实施方式的汽车漆面保护膜的示意图。
具体实施方式
[0046]
如上所述,汽车漆面保护膜需要具有优异的耐物理划伤、耐黄变以及防污防油性能,更重要的是在长期使用过程中,汽车漆面保护膜中添加的各种助剂不能析出。
[0047]
为此,在第一方面中,本技术之目的首先在于提供一种汽车漆面保护膜用耐黄变自修复涂层组合物,所述耐黄变自修复涂层组合物由以下重量份的原料组成:
[0048][0049]
其中羟基封端聚氨酯预聚体与支链化羟基聚酯共100重量份。
[0050]
在一种具体实施方式中,羟基封端聚氨酯预聚体的用量可为10重量份、15重量份、20重量份、25重量份、30重量份或者它们中任意两个数值之间的范围或子范围。相应地,支链化羟基聚酯的用量可为90重量份、85重量份、80重量份、75重量份、70重量份或者它们中任意两个数值之间的范围或子范围。
[0051]
在一种实施方式中,当羟基封端聚氨酯预聚体与支链化羟基聚酯的总用量为100重量份时,固化剂的用量可为11.7重量份、15重量份、21.7重量份、25重量份、31.7重量份、35重量份、40.8重量份或者它们中任意两个数值之间的范围或子范围。
[0052]
在一种实施方式中,当羟基封端聚氨酯预聚体与支链化羟基聚酯的总用量为100重量份时,扩链剂的用量可为0.1重量份、0.2重量份、0.3重量份、0.4重量份、0.5重量份、0.6重量份、0.7重量份、0.8重量份、0.9重量份、1重量份或者它们中任意两个数值之间的范围或子范围。
[0053]
在一种实施方式中,当羟基封端聚氨酯预聚体与支链化羟基聚酯的总用量为100重量份时,第一催化剂的用量可为0.1重量份、0.2重量份、0.3重量份。
[0054]
在一种实施方式中,当羟基封端聚氨酯预聚体与支链化羟基聚酯的总用量为100重量份时,所述第一溶剂的用量可为10重量份、15重量份、20重量份、25重量份、30重量份、35重量份、40重量份或者它们中任意两个数值之间的范围或子范围。
[0055]
羟基封端聚氨酯预聚体是本文所述的耐黄变自修复涂层组合物的重要组分之一,在多官能度异氰酸酯固化剂的作用下,羟基封端聚氨酯预聚体可与支链化羟基聚酯同时固化,进一步改善所得涂层的自修复功能。
[0056]
在一种实施方式中,所述的羟基封端聚氨酯预聚体由以下原料合成:聚醚三元醇,聚酯二元醇,反应性润湿流平剂,反应性滑爽剂,反应性紫外线吸收剂,抗氧剂,脂肪族二异氰酸酯、第二溶剂以及第二催化剂。在一种实施方式中,所述的聚醚三元醇选自但不限于聚氧化丙烯/氧化乙烯共聚三醇、聚氧化丙烯三醇中的一种或多种,所述的聚醚三元醇的数均分子量为1000-10000,优选的,数均分子量为3000-6000。例如,所述的聚醚三元醇的数均分子量的可为3000、3500、4000、4500、5000、5500、6000或者它们中任意两个数值之间的范围或子范围。
[0057]
在一种实施方式中,所述的聚酯二元醇选自但不限于聚己内酯二醇、聚己二酸新戊二醇酯二醇、聚己二酸己二醇酯二醇、聚二甘醇己二酸酯二醇、聚丁二醇新戊二醇己二酸
酯二醇、聚己二酸甲基丙二醇酯二醇、聚碳酸酯二元醇中的一种或几种。所述的聚酯二元醇的数均分子量为1000-4000。例如,所述聚酯二元醇的数均分子量可为1000、1500、2000、2500、3000、3500、4000或者它们中任意两个数值之间的范围或子范围。
[0058]
在一种实施方式中,所述的反应性润湿流平剂为有机硅改性聚醚多元醇,选自端羟基单官能度有机硅改性聚醚、端羟基两官能度有机硅改性聚醚、侧羟基两官能度有机硅改性聚醚中的一种。在一种实施方式中,所述端羟基单官能度有机硅改性聚醚和端羟基两官能度有机硅改性聚醚购自广州市斯洛柯高分子聚合物有限公司;所述侧羟基两官能度有机硅改性聚醚购自迈图公司。
[0059]
在一种实施方式中,所述的反应性防污滑爽剂选自全氟聚醚醇和全氟聚醚酰胺乙基醇中的一种。在一种实施方式中,所述的全氟聚醚醇购自苏州仓慕新材料;所述的全氟聚醚酰胺乙基醇购自中化环保有限公司。
[0060]
在一种实施方式中,所述的反应性紫外线吸收剂选自带有活性羟基的二苯甲酮类和苯并三唑类紫外光吸收剂中的一种或两种。在一种优选的实施方式中,所述的带有活性羟基的二苯甲酮类紫外线吸收剂(uv950l)购自德达志成化工,所述的带有活性羟基的苯并三唑类紫外线吸收剂(r-455)购自奇钛科技。
[0061]
在一种实施方式中,所述的脂肪族二异氰酸酯选自1,6-已二异氰酸酯(hdi)、异佛尔酮二异氰酸酯(ipdi)、双环己基甲烷二异氰酸酯(hmdi)中的一种或两种。在一种实施方式中,所述的抗氧剂选自抗氧剂1010、抗氧剂1076、抗氧剂245、抗氧剂1135中的一种。
[0062]
在一种实施方式中,所述的第一溶剂和第二溶剂各自独立地选自但不限于乙酸乙酯,乙酸丁酯,碳酸二甲酯,丁酮,甲苯和二甲苯中的一种或多种。
[0063]
在一种具体实施方式中,所述的羟基封端聚氨酯预聚体的制备方法包括以下步骤:
[0064]
1)将聚醚三元醇、聚酯二元醇、反应性润湿流平剂、反应性滑爽剂、反应性紫外线吸收剂、脂肪族异氰酸酯、抗氧剂、溶剂投入反应釜,50~60℃搅拌均匀;
[0065]
2)加入催化剂,逐步升温至85-95℃,常压反应4-6小时后,每半小时测定一次nco含量,当nco降为零时,出料即得所述羟基封端聚氨酯预聚体。
[0066]
在一种实施方式中,所述的支链化羟基聚酯选自科思创desmophen 670、巴斯夫sovermol 1052中的一种或两种;
[0067]
在一种实施方式中,所述的扩链剂选自1,4丁二醇、二甘醇、新戊二醇中的一种;
[0068]
在一种实施方式中,所述的固化剂选自巴斯夫basonat hi100、巴斯夫basonat hi190 b/s、异佛尔酮二异氰酸酯(ipdi)、双环己基甲烷二异氰酸酯(hmdi)中的一种;
[0069]
在一种实施方式中,所述第一催化剂和第二催化剂各自独立地选自有机锡和有机铋催化剂中的一种。
[0070]
在第二方面中,如图4所示,本技术提供一种汽车漆面保护膜。该汽车漆面保护膜从上到下依次包括pet离型膜50、耐黄变自修复涂层40、tpu基膜30、丙烯酸压敏胶层20、pet离型膜10。离型膜10、50可为本领域常见的pet膜。耐黄变自修复涂层40可由如第一方面所述的耐黄变自修复涂层组合物制成。tpu基膜30为市售的脂肪族热塑性聚氨酯树脂。丙烯酸压敏胶20为市售的溶剂型丙烯酸压敏胶。
[0071]
实施例
[0072]
下面将结合实施例,对本技术进行一步描述和说明。如无特别说明,所用化工原料均可从市场购买。本领域技术人员可以理解,下述实施例只是示例性的。
[0073]
制备实施例
[0074]
实施例1
[0075]
一种羟基封端聚氨酯预聚体的制备
[0076]
本实施例所用原料及质量如表1。
[0077]
表1
[0078][0079]
本实施例的羟基封端聚氨酯预聚体的制备步骤如下:
[0080]
1)将聚氧化丙烯三醇600g、聚己二酸新戊二醇酯二醇200g、流平剂侧羟基两官能度有机硅改性聚醚40g、防污滑爽剂全氟聚醚醇20g、紫外线吸收剂uv950l40g、乙酸丁酯61.5g、抗氧剂1010 0.5g、1,6-已二异氰酸酯38g投入反应釜,50℃搅拌均匀;
[0081]
2)加入有机铋催化剂0.04g,逐步升温至95℃,常压反应6小时后,每半小时测定一次nco含量,当nco降为零时,出料即得根据实施例1的羟基封端聚氨酯预聚体。实施例1的羟基封端聚氨酯预聚体的红外图谱如图1所示,从图1可知,nco官能团在2240-2280cm-1
红外特征峰完全消失,说明nco与羟基反应完全,同时生成的氨基甲酸酯键在1715cm-1
附近有很强的特征峰出现。
[0082]
实施例2
[0083]
一种羟基封端聚氨酯预聚体的制备
[0084]
本实施例所用原料及质量如表2。
[0085]
表2
[0086][0087]
本实施例的羟基封端聚氨酯预聚体的制备步骤如下:
[0088]
1)将聚氧化丙烯/氧化乙烯共聚三醇600g、聚己二酸甲基丙二醇酯二醇200g、流平剂端羟基两官能度有机硅改性聚醚40g、防污滑爽剂全氟聚醚酰胺乙基醇20g、紫外线吸收剂r-455 40g、碳酸二甲酯65g、抗氧剂1076 0.5g、异氟尔酮二异氰酸酯34.5g投入反应釜,50℃搅拌均匀;
[0089]
2)加入有机铋催化剂0.04g,逐步升温至95℃,常压反应6小时后,每半小时测定一次nco含量,当nco降为零时,出料即得根据实施例2的羟基封端聚氨酯预聚体。实施例2的羟基封端聚氨酯预聚体的红外图谱如图2所示,从图2可知,nco官能团在2240-2280cm-1
红外特征峰完全消失,说明nco与羟基反应完全,同时生成的氨基甲酸酯键在1715cm-1
附近有很强的特征峰出现。
[0090]
实施例3
[0091]
一种羟基封端聚氨酯预聚体的制备
[0092]
本实施例所用原料及质量如表3。
[0093]
表3
[0094][0095]
本实施例的羟基封端聚氨酯预聚体的制备步骤如下:
[0096]
1)将聚氧化丙烯/氧化乙烯共聚三醇600g、聚碳酸酯二醇200g、流平剂端羟基单官能度有机硅改性聚醚40g、防污滑爽剂全氟聚醚醇20g、紫外线吸收剂uv950l 40g、甲苯66g、抗氧剂245 0.5g、双环己基甲烷二异氰酸酯33.5g投入反应釜,50℃搅拌均匀;
[0097]
2)加入有机铋催化剂0.04g,逐步升温至90℃,常压反应4小时后,每半小时测定一次nco含量,当nco降为零时,出料即得根据实施例3的羟基封端聚氨酯预聚体。实施例3的羟基封端聚氨酯预聚体的红外图谱如图3所示,从图3可知,nco官能团在2240-2280cm-1
红外特征峰完全消失,说明nco与羟基反应完全,同时生成的氨基甲酸酯键在1715cm-1
附近有很强的特征峰出现。
[0098]
应用实施例
[0099]
实施例4
[0100]
(1)自修复涂布液的制备:
[0101][0102]
按照上述配料表,将物料投入料筒,使用分散机高速分散10min,转速为400rpm,静置待用。
[0103]
(2)汽车漆面保护膜的制备
[0104]
利用线棒将丙烯酸压敏胶水涂布于pet离型膜10上,100℃烘干后形成厚度为30um
的丙烯酸胶层,并与厚度为150um的tpu基膜复合;然后,利用线棒将上述制备的涂布液涂布于tpu基膜的另一面,采用阶梯升温的方式90℃/120℃/150℃干燥固化5min,得到约10um厚的涂层,并在涂层表面复合pet离型膜50,放入烘箱,50℃熟化48小时即可,得到根据实施例4的汽车漆面保护膜,并测试其性能,结果见表4。
[0105]
实施例5
[0106]
(1)自修复涂布液的制备:
[0107][0108]
按照上述配料表,将物料投入料筒,使用分散机高速分散10min,转速为400rpm,静置待用。
[0109]
(2)汽车漆面保护膜的制备
[0110]
利用线棒将丙烯酸压敏胶水涂布于pet离型膜10上,100℃烘干后形成厚度为30um的丙烯酸胶层,并与厚度为150um的tpu基膜复合;然后,利用线棒将上述制备的涂布液涂布于tpu基膜的另一面,采用阶梯升温的方式90℃/120℃/150℃干燥固化5min,得到约10um厚的涂层,并在涂层表面复合pet离型膜50,放入烘箱,50℃熟化48小时即可,得到根据实施例5的汽车漆面保护膜,并测试其性能,结果见表4。
[0111]
实施例6
[0112]
(1)自修复涂布液的制备:
[0113][0114]
按照上述配料表,将物料投入料筒,使用分散机高速分散10min,转速为400rpm,静置待用。
[0115]
(2)汽车漆面保护膜的制备
[0116]
利用线棒将丙烯酸压敏胶水涂布于pet离型膜10上,100℃烘干后形成厚度为30um的丙烯酸胶层,并与厚度为150um的tpu基膜复合;然后,利用线棒将上述制备的涂布液涂布于tpu基膜的另一面,采用阶梯升温的方式90℃/120℃/150℃干燥固化5min,得到约10um厚的涂层,并在涂层表面复合pet离型膜50,放入烘箱,50℃熟化48小时即可,得到根据实施例6的汽车漆面保护膜,并测试其性能,结果见表4。
[0117]
实施例7
[0118]
(1)自修复涂布液的制备:
[0119][0120]
按照上述配料表,将物料投入料筒,使用分散机高速分散10min,转速为400rpm,静置待用。
[0121]
(2)汽车漆面保护膜的制备
[0122]
利用线棒将丙烯酸压敏胶水涂布于pet离型膜10上,100℃烘干后形成厚度为30um的丙烯酸胶层,并与厚度为150um的tpu基膜复合;然后,利用线棒将上述制备的涂布液涂布于tpu基膜的另一面,采用阶梯升温的方式90℃/120℃/150℃干燥固化5min,得到约10um厚的涂层,并在涂层表面复合pet离型膜50,放入烘箱,50℃熟化48小时即可,得到根据实施例7的汽车漆面保护膜,并测试其性能,结果见表4。
[0123]
实施例8
[0124]
(1)自修复涂布液的制备:
[0125][0126]
按照上述配料表,将物料投入料筒,使用分散机高速分散10min,转速为400rpm,静置待用。
[0127]
(2)汽车漆面保护膜的制备
[0128]
利用线棒将丙烯酸压敏胶水涂布于pet离型膜10上,100℃烘干后形成厚度为30um的丙烯酸胶层,并与厚度为150um的tpu基膜复合;然后,利用线棒将上述制备的涂布液涂布于tpu基膜的另一面,采用阶梯升温的方式90℃/120℃/150℃干燥固化5min,得到约10um厚的涂层,并在涂层表面复合pet离型膜50,放入烘箱,50℃熟化48小时即可,得到根据实施例8的汽车漆面保护膜,并测试其性能,结果见表4。
[0129]
实施例9
[0130]
(1)自修复涂布液的制备:
[0131]
[0132][0133]
按照上述配料表,将物料投入料筒,使用分散机高速分散10min,转速为400rpm,静置待用。
[0134]
(2)汽车漆面保护膜的制备
[0135]
利用线棒将丙烯酸压敏胶水涂布于pet离型膜10上,100℃烘干后形成厚度为30um的丙烯酸胶层,并与厚度为150um的tpu基膜复合;然后,利用线棒将上述制备的涂布液涂布于tpu基膜的另一面,采用阶梯升温的方式90℃/120℃/150℃干燥固化5min,得到约10um厚的涂层,并在涂层表面复合pet离型膜50,放入烘箱,50℃熟化48小时即可,得到根据实施例9的汽车漆面保护膜,并测试其性能,结果见表4。
[0136]
表4、各应用例测试数据表
[0137][0138]
表中数据测试方法如下:
[0139]
1、修复速度:用铜刷在自修复涂层上用力划过,然后用70℃左右的热水冲洗划痕,秒表记录划痕修复时间;
[0140]
2、抗污性能:裁取尺寸为50mm
×
50mm试样,数量为9片。在15~28℃、40~80%rh的环境条件下至少放置24h。选取符合jg/t 304-2011附录a中a.3.1规定的红色油性记号笔,在膜面中心涂上(喷上)面积为20mm
×
20mm的印记,涂三组试样,每组三块,在同样的环境条件下放置2h后测试。使用沾满酒精的无绒棉布在一组试样的粘污印记上往复擦拭25次,擦
拭后观察试样状态;
[0141]
3、耐黄变性:截取6片尺寸为150mm*70mm的样品,每两片样品剥离离型膜后对贴制得3片测试样品,置于氙灯老化试验箱中测试;实验条件为灯管340nm,辐照度0.93w/m2,黑板温度63℃,相对湿度65%;实验过程中,试样架始终在旋转并持续置于光照和间歇式喷淋下,每个实验周期包括102min光照加上18min的关照加水喷淋,喷水水温为20
±
5℃;测试408h后取出试样恢复到室温;采用c光源和2
°
的测量条件测量反射光谱并计算试验后试样颜色参数l*、a*、b*,并计算试验前后色差
△eab
*。其中色差计算公式如下:
[0142][0143]
式中:
[0144]
——试验前后cie lab均匀色空间色差;
[0145]
δl
*
、δa
*
、δb
*
——分别为试验后试样颜色参数l
*
、a
*
、b
*
较实验前的变化差值;
[0146]
从上述测试结果可以看出,利用本发明提供的汽车漆面保护膜用自修复涂层树脂组合料制备的汽车漆面保护膜表现出优异的自修复速度、抗污性能以及出色的耐黄变性能,具有很好的商业利用价值。
[0147]
在本发明及上述实施例的教导下,本领域技术人员很容易预见到,本发明所列举或例举的各原料或其等同替换物、各加工方法或其等同替换物都能实现本发明,以及各原料和加工方法的参数上下限取值、区间值都能实现本发明,在此不一一列举实施例。
[0148]
上述对实施例的描述是为了便于本技术领域的普通技术人员能理解和应用本技术。熟悉本领域技术的人员显然可以容易地对这些实施例做出各种修改,并把在此说明的一般原理应用到其它实施例中而不必付出创造性的劳动。因此,本技术不限于这里的实施例,本领域技术人员根据本技术披露的内容,在不脱离本技术范围和精神的情况下做出的改进和修改都本技术的范围之内。