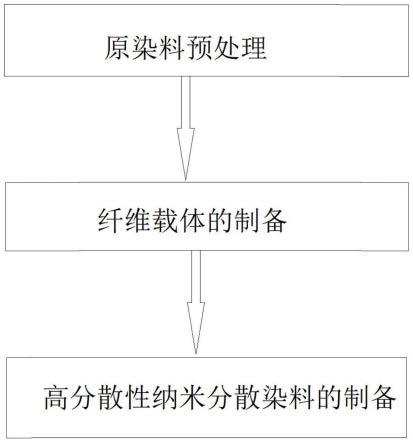
1.本发明涉及印染材料领域,具体涉及一种高分散性纳米分散染料及其制备方法。
背景技术:2.分散染料,主要用于涤纶及其混纺织物的印染,也可用于醋酸纤维、锦纶、丙纶、氯纶、腈纶等合成纤维的印染。近年来,随着聚酯类纺织品的大范围应用,分散染料也得到了前所未有的发展,已经成为品种数量最多、用量最大的染料用品。
3.通常,为了使分散染料在水中能够迅速分散成为均匀稳定的胶体状悬浮液,原染料在合成后一般还需要进行升温转晶、与分散剂进行砂磨、干燥等后处理工序方可制成商品染料。在染色过程中,作为一种非离子型染料,分散染料的水溶性极低,在染液中,分散染料借助分散剂均匀地分散在染液中,之后借助高温等作用,使得纤维膨化,纤维内部的空隙增大,使得分散染料分子能够通过扩散进入被膨化和增大的纤维空隙内,最后由纤维分子间引力和氢键固着,实现染色,因此,分散染料的染色性能主要取决于其化学结构、晶型、粒径大小、分散剂等因素的影响,尤其是分散染料的粒径大小与其上染过程密切相关。
4.一般地,当染料颗粒的粒径>30um时,染制品的表面易产生斑点、条痕等缺陷;当染料颗粒的粒径介于10~30um之间时,染制品的表面容易无光泽;当染料颗粒的粒径<5um时,可满足一般制品的使用;但对于单丝直径介于10~30um的纤维和厚度<10um的超薄膜,染料颗粒的粒径则需达到1um以下,可见,染料颗粒粒径的减小能够有效提高分散染料的适用范围、着色强度、光泽和遮盖力等综合性能,此外,染料颗粒粒径的减小还能够提高染料颗粒进入涤纶材料内部的能力、降低染色过程的难度。但是,随着染料颗粒粒径的减小,如在染料颗粒的粒径达到纳米级后,由于染料颗粒的粒度变细,单个染料颗粒的比表面积增大,染料颗粒的表面能将增加,高表面能的颗粒相遇将会自发地释放能量、降低表面能,使颗粒处于稳定的状态,而染料颗粒间相互团聚是降低表面能的有效方式,因此,纳米染料颗粒和颗粒之间极易产生团聚,分散性很差,特别是处于液体状态下的纳米染料颗粒在被干燥后纳米染料颗粒容易重新团聚为微米级染料颗粒,使得纳米分散染料在使用过程中失去了纳米染料颗粒所具备的优异性能。
5.此外,现有分散染料中的助剂含量普遍偏高,助剂的大量使用一方面会导致成本的升高和生产废水的处理难度增大,另一方面,在染色过程中,助剂的大量使用将会增大泳移现象发生的趋势。
技术实现要素:6.本发明设计出一种高分散性纳米分散染料及其制备方法,以克服现有纳米分散染料的分散性差、易团聚,以及助剂含量高的技术问题。
7.为解决上述问题,本发明公开了一种高分散性纳米分散染料的制备方法,包括步骤:
8.s1,原染料预处理:将原染料溶于有机溶剂,将所得有机溶液在搅拌下加入水溶液
中进行混合沉淀反应,生成的沉淀经破碎、干燥处理后,得预处理后的原染料粉体;
9.s2,纤维载体的制备:纤维素纤维经切断、打浆和浸蚀处理后,捞出、水洗,并沥干至纤维素短纤维的含水率为40%~80%,含水纤维素短纤维经冻干处理后,得纤维载体;
10.s3,高分散性纳米分散染料的制备:将所述预处理后的原染料粉体、纤维载体以及活性硅酸钙复合在一起,得高分散性纳米分散染料。
11.进一步的,所述步骤s1包括步骤:
12.s11,将通过反应得到的原染料溶于有机溶剂中,过滤去除杂质后,得到有机溶液a;
13.s12,将水和助剂混合均匀后,得到水溶液b;
14.s13,将所述水溶液b置于可加热容器中,升温至60~70℃后,在搅拌下缓慢将所述有机溶液a加入水溶液b中进行混合沉淀反应,将有机溶液a完全加入水溶液b中后,继续搅拌10~30min,之后将混合液置于超声波细胞破碎机进行超声粉碎30-60min,超声破碎后,通过喷雾干燥除去水和有机溶剂、得到预处理后的原染料粉体。
15.进一步的,在所述步骤s12中,所述助剂和水的重量百分比为0.5%~3%,按重量分计,所述助剂包括:
[0016][0017]
进一步的,所述步骤s2包括步骤:
[0018]
s21,将纤维素纤维切断后,与水混合并置于打浆装置中进行打浆,打浆后得含有纤维素短纤维的浆液;
[0019]
s22,向步骤s21所得的含有纤维素短纤维的浆液中加入碱性物质和浸蚀助剂,搅拌均匀后得含有纤维素短纤维的碱性处理液c,将所述碱性处理液c加热至40~50℃,在40~50℃下对其内的纤维素短纤维进行浸蚀处理0.2~3h后,捞出、水洗后,并沥干至纤维素短纤维的含水率为40%~80%后、备用;
[0020]
s23,将步骤s22所得的含水纤维素短纤维置于冻干设备中冻干后,即得所述纤维载体。
[0021]
进一步的,所述纤维素纤维为棉纤维、麻纤维、莫代尔纤维、竹纤维、木棉纤维中的一种或多种。
[0022]
进一步的,在所述步骤s22中,所述碱性处理液c中含有:氢氧化钠0.2~3g/l、有机硅0.5~5g/l、分散剂3~5g/l、丙三醇6~10g/l。
[0023]
进一步的,所述步骤s3包括步骤:
[0024]
s31,首先将活性硅酸钙和上述步骤s1制备得到的预处理后的原染料粉体分散于水中、得到混合体系d之后,再将混合体系d复合在上述步骤s2制备得到的纤维载体上,并将
得到的复合材料沥干后备用;
[0025]
s32、向上述步骤s31中沥干后的复合材料上喷淋酸性溶液,烘干后,即得本技术所述高分散性纳米分散染料。
[0026]
进一步的,在上述步骤s31中,通过复合装置将所述混合体系d复合在所述纤维载体上,所述复合装置包括:
[0027]
外壳体,所述外壳体内部中空;
[0028]
水平隔板,其沿水平方向设置在所述外壳体内,并将所述外壳体的内部空间分隔成上部空腔和下部空腔;
[0029]
所述下部空腔上设置进口和导液管,外部气体通过所述进口进入所述下部空腔内,所述下部空腔内设置所述混合体系d,在所述进口输入的气体的压强作用下,所述下部空腔内的混合体系d能够通过所述导液管进入所述上部空腔内;
[0030]
所述上部空腔内填充所述纤维载体,进入所述上部空腔内的混合体系d穿过所述纤维载体后,通过设置在所述上部空腔上的出口排出。
[0031]
进一步的,所述复合装置还包括:
[0032]
匀气盘,所述匀气盘位于所述进口的上方,所述匀气盘的直径为所述进口直径的1.5~3倍;
[0033]
环形内壁,所述环形内壁位于所述外壳体的内部,且环绕在所述匀气盘的外围,所述环形内壁的下端与所述外壳体的下底面连接,在所述环形内壁的上端设置上盖板,所述环形内壁、外壳体的下底面和所述上盖板在所述外壳体内围成内腔体,在所述环形内壁的下端设置排液口,所述排液口连通所述内腔体和下部空腔;
[0034]
安装连接件,所述安装连接件为内部中空的筒状结构,所述安装连接件的上端穿过所述上盖板后、延伸至所述水平隔板的下方,且所述安装连接件的上端与所述水平隔板之间具有间隙,下端与所述匀气盘连接,在所述安装连接件上设置溢气孔,所述溢气孔位于所述上盖板的下方。
[0035]
一种高分散性纳米分散染料,所述分散染料为上述高分散性纳米分散染料的制备方法制备的分散染料。
[0036]
本技术所述的高分散性纳米分散染料及其制备方法具有以下优点:本技术通过将除杂提纯后的纳米原染料颗粒负载在纤维载体上,通过纤维载体为纳米染料颗粒提供了支撑骨架,使其不易团聚,在使用时能够实现良好分散性,在发挥出纳米染料颗粒的优势的同时,降低了助剂的使用,更加环保高效;此外,通过活性硅酸钙的添加,在纳米染料颗粒和纤维载体之间起到了良好的架桥作用,使得染料颗粒能够被稳定的吸附在纤维载体上;再者,所述纤维载体和活性硅酸钙在染色过程中,能够利用染色时的高温高压环境,通过酸解进行去除,而不会对染色过程产生不利影响。
附图说明
[0037]
图1为本发明所述高分散性纳米分散染料的制备方法流程图;
[0038]
图2为本发明所述复合装置的立体结构示意图;
[0039]
图3为本发明所述复合装置的俯视结构示意图;
[0040]
图4为图3中a-a方向的剖面结构示意图;
[0041]
图5为图3中a-a方向的剖面结构立体示意图;
[0042]
图6为本发明所述复合装置的正视结构示意图;
[0043]
图7为图6中c-c方向的剖面结构示意图;
[0044]
图8为图3中a-a方向的另一剖面结构示意图;
[0045]
图9为图3中b-b方向的剖面结构示意图;
[0046]
图10为图3中a-a方向的另一剖面结构立体示意图;
[0047]
图11为图6中c-c方向的另一剖面结构示意图;
[0048]
图12为图6中d-d方向的剖面结构示意图。
[0049]
附图标记说明:
[0050]
1、外壳体;2、水平隔板;3、上部空腔;301、出口;302、竖直隔板;303、滤网;4、下部空腔;401、进口;402、导液管;403、匀气盘;404、安装连接件;405、环形内壁;406、上盖板;407、溢气孔;408、排液口。
具体实施方式
[0051]
为使本发明的上述目的、特征和优点能够更为明显易懂,下面结合附图对本发明的具体实施例做详细的说明。
[0052]
如图1所示,一种高分散性纳米分散染料的制备方法,其包括步骤:
[0053]
s1,原染料预处理:将原染料溶于有机溶剂,并将所得有机溶液在搅拌下加入水溶液中进行混合沉淀反应,生成的沉淀经破碎、干燥处理后,得预处理后的原染料粉体;
[0054]
s2,纤维载体的制备:纤维素纤维经切断、打浆和浸蚀处理后,捞出、水洗,并沥干至纤维素短纤维的含水率为40%~80%,含水纤维素短纤维经冻干处理后,得纤维载体;
[0055]
s3,高分散性纳米分散染料的制备:将所述预处理后的原染料粉体、纤维载体以及活性硅酸钙复合在一起,即得本技术所述的高分散性纳米分散染料。
[0056]
本技术所述分散染料的制备方法通过将除杂提纯后的纳米原染料颗粒负载在纤维载体上,通过纤维载体为纳米染料颗粒提供了支撑骨架,使其不易团聚,在使用时能够实现良好分散性,在发挥出纳米染料颗粒的优势的同时,降低了助剂的使用,更加环保高效;此外,通过活性硅酸钙的添加,在纳米染料颗粒和纤维载体之间起到了良好的架桥作用,使得染料颗粒能够被稳定的吸附在纤维载体上;再者,所述纤维载体和活性硅酸钙在染色过程中,能够利用染色时的高温高压环境,通过酸解进行去除,而不会对染色过程产生不利影响。
[0057]
具体的,所述步骤s1包括步骤:
[0058]
s11,将通过反应得到的原染料溶于有机溶剂中,过滤去除杂质后,得到有机溶液a;
[0059]
s12,将水和助剂混合均匀后,得到水溶液b;
[0060]
s13,将所述水溶液b置于可加热容器中,升温至60~70℃后,在搅拌下缓慢将所述有机溶液a加入水溶液b中进行混合沉淀反应,将有机溶液a完全加入水溶液b中后,继续搅拌10~30min,之后将混合液置于超声波细胞破碎机进行超声粉碎30-60min,超声破碎后,通过喷雾干燥除去水和有机溶剂、得到预处理后的原染料粉体。
[0061]
作为本技术的一些实施例,在所述步骤s11中,所述有机溶剂可以为乙醇、丙酮、正
丁醇、异丁醇、四氢呋喃、苯、甲苯、乙苯、二甲苯、二氯甲烷、二甲基甲酰胺、氯仿、四氯化碳中的一种或多种。
[0062]
优选的,在所述步骤s11中,原染料和有机溶剂的重量百分比为10%~30%。
[0063]
作为本技术的一些实施例,在所述步骤s11中,,原染料可以为偶氮型、蒽醌型或者杂环型染料中的一种或多种,如分散红、分散蓝等。
[0064]
进一步的,在所述步骤s12中,按重量分计,所述助剂包括:
[0065][0066]
优选的,所述分散剂为木质素磺酸盐、甲基萘磺酸甲醛缩合物、脂肪酸多元醇酯聚氧乙烯醚、苄基萘磺酸甲醛缩合物中一种或多种的组合;所述扩散剂为萘磺酸甲醛缩合物;所述乳化剂为吐温60、十二烷基磺酸钠、、op-10、sp-80和异构十三醇聚氧乙烯醚中一种或多种的组合;所述消泡剂为有机硅类消泡剂;所述表面活性剂为十二烷基苯磺酸钠、硫酸化蓖麻油、dynol 607、多元醇中的一种或多种。
[0067]
进一步的,在所述步骤s12中,助剂和水的重量百分比为0.5%~3%。
[0068]
进一步的,在所述步骤s13中,有机溶液a和水溶液b的重量百分比为30~60%。
[0069]
优选的,在所述步骤s13中,控制有机溶液a的添加速度基本均匀连续、稳定,每分钟向水溶液b中添加有机溶液a的量不应超过有机溶液a总量的10%。
[0070]
更加优选的,有机溶液a的添加速度应随着有机溶液a和水溶液b的重量百分比的增大而降低,具体的,当有机溶液a和水溶液b的重量百分比为30~40%时,每分钟向水溶液b中添加有机溶液a的量不应超过有机溶液a总量的10%;当有机溶液a和水溶液b的重量百分比为40~60%时,每分钟向水溶液b中添加有机溶液a的量不应超过有机溶液a总量的5%。
[0071]
进一步的,在所述步骤s13中,超声波细胞破碎机的超声频率为20~60khz。
[0072]
在上述步骤s1中,通过将原染料溶解于适当的有机溶剂中,能够通过过滤除去原染料中的无机盐等杂质,对原染料进行提纯;之后通过将原染料的有机溶剂与水溶液混合、进行混合沉淀反应,使得原染料析出,同时结合对混合速率的控制、以及超声波细胞破碎机的分散、破碎和乳化作用,实现原染料颗粒的细化和均匀分散,在此基础上,通过喷雾干燥除去水和溶剂后,即可得到粒径为纳米级的预处理后的原染料粉体。
[0073]
进一步的,所述步骤s2包括步骤:
[0074]
s21,将纤维素纤维切断后,与适量的水混合并置于打浆装置中进行打浆,打浆后得含有纤维素短纤维的浆液;
[0075]
s22,向步骤s21所得的含有纤维素短纤维的浆液中加入碱性物质和浸蚀助剂,搅拌均匀后得含有纤维素短纤维的碱性处理液c,将所述碱性处理液c加热至40~50℃,在40
~50℃下对其内的纤维素短纤维进行浸蚀处理0.2~3h后,捞出、水洗后,并沥干至纤维素短纤维的含水率为40%~80%后、备用;
[0076]
s23,将步骤s22所得的含水纤维素短纤维置于冻干设备中冻干后,即得所述纤维载体。
[0077]
其中,上述纤维素短纤维的含水率=(其当前重量-烘干至恒重时的重量)/烘干至恒重时的重量。
[0078]
优选的,在所述步骤s21中,将纤维素纤维切断至10~30mm后,将纤维素纤维与水按照0.02:1~0.15:1的重量比混合后加入打浆装置中进行打浆0.5~1h,打浆后得含有纤维素短纤维的浆液。
[0079]
更加优选的,在所述步骤s21中,所述纤维素纤维的用量为所述步骤s1中得到的预处理后的原染料粉体重量的20%~40%。
[0080]
作为本技术的一些实施例,所述纤维素纤维可以为棉纤维、麻纤维、莫代尔纤维、竹纤维、木棉纤维等中的一种或多种。
[0081]
优选的,在所述步骤s22中,所述碱性处理液c为氢氧化钠的水溶液。
[0082]
更加优选的,所述碱性处理液c中含有:氢氧化钠0.2~3g/l、有机硅0.5~5g/l、分散剂3~5g/l、丙三醇6~10g/l。
[0083]
在步骤s22中所述碱性溶液c中碱性成分的浸蚀作用下,所述纤维素短纤维中的酯基断裂、表面分子脱落,进而能够在所述纤维素短纤维的表面浸蚀形成大量凹坑,在增加所述纤维素短纤维比表面积的同时,能够提高所述纤维素短纤维表面的粗糙度、提升其吸附染料颗粒等固体物质的能力。
[0084]
此外,在常见的纤维素纤维,如棉纤维、竹纤维、麻纤维等中,除了纤维素纤维成分之外,还含有果胶、蜡质等与纤维素纤维共生的杂质存在,在处理过程中,这些杂质成分将会在纤维素纤维表面形成一层膜,使得染料颗粒难以接触到纤维素纤维的表面、导致纤维素纤维的吸附能力降低,在上述碱性溶液c的浸蚀过程中,碱性成分能够有效去除纤维素纤维中的果胶、蜡质等杂质,使得纤维素纤维的分子链氧化、断裂,强度和长度降低,同时,所述有机硅的添加能够利用其内可伸缩的硅氧键在纤维素纤维表面形成有机硅薄膜,增加纤维素纤维表面活性及其与染料颗粒之间的抱合力;所述分散剂和丙三醇的添加可提高纤维素纤维在碱性处理液c中的分散效果。所述分散剂为聚羧酸盐或木质素磺酸盐或亚甲基二萘磺酸钠中的一种或多种。
[0085]
再者,在步骤s22所述碱性溶液c中碱性成分的浸蚀作用下,纤维素纤维可以得到一定程度的溶胀,为后续步骤s23的进行提供良好基础。而纤维素纤维在高温的酸性染液中,可以在其表面喷淋的酸液和染液中酸性物质的作用下,快速分解,产生碳化物,不会对染色过程产生不利影响。
[0086]
优选的,在所述步骤s23中,需将含水纤维素短纤维置于零下60~100℃、压力40~70pa的冷冻环境中,在10~20khz的超声波的作用下,进行冷冻升华处理0.5~7h后取出,即得所述纤维载体。
[0087]
在所述步骤s23中,通过冻干处理能够保持打浆后的纤维素短纤维的分丝状态,同时,在冻干过程中,经过超低温冷冻处理,纤维素短纤维中的液态水分子凝结成固态后撑开并占据了纤维素分丝之间的空间,在之后的升华处理过程中,纤维素内部的固态水分子通
过升华去除,在固态水分子占据的空间位置中形成空隙。同时,在超声的作用下,可以在纤维素短纤维内部形成分布和大小较为均一的空隙,增强纤维素短纤维的比表面积和吸附能力。
[0088]
进一步的,所述步骤s3包括步骤:将所述预处理后的原染料粉体、纤维载体以及活性硅酸钙分散在水中后复合在一起,烘干后,得本技术所述的高分散性纳米分散染料。
[0089]
更进一步的,所述步骤s3包括步骤:
[0090]
s31,将上述步骤s1制备得到的预处理后的原染料粉体、上述步骤s2制备得到的纤维载体以及活性硅酸钙分散在水中后复合在一起,沥干后备用;
[0091]
s32、向上述步骤s31中沥干后的复合材料上喷淋酸性溶液,烘干后,即得本技术所述高分散性纳米分散染料。
[0092]
更进一步的,在上述步骤s31中,所述活性硅酸钙的分子式为cao
·
msio2·
nh2o,所述活性硅酸钙的粒径为0.1~10um、比表面积为60~100m2/g。所述活性硅酸钙表面的硅氧基、硅醇基等基团能够与纤维素纤维中的氢键等结合产生稳定的化学键结合力,将活性硅酸钙牢固地吸附在纤维素纤维的表面,同时,活性硅酸钙表面的孔状结构还能够吸附分散染料颗粒,在纤维素纤维和染料颗粒之间起到架桥作用,最终提高纤维素纤维对染料颗粒的吸附力和吸附量。且所述活性硅酸钙为无毒、无害的白色粉末,掺杂于染料颗粒中,不会对染料颗粒和印染织物产生不利影响。此外,所述活性硅酸钙作为一种新型高分散性的硅酸钙,其在高温下能溶于酸中,因此,在染色过程中,其可以被酸性高温染液溶解,而不会对染色过程产生不利影响。
[0093]
优选的,在上述步骤s31中,首先将上述步骤s1制备得到的预处理后的原染料粉体和活性硅酸钙分散于水中、得到混合体系d之后,再将混合体系d复合在上述步骤s2制备得到的纤维载体上。
[0094]
更加优选的,在所述步骤s31中,所述活性硅酸钙的用量为所述步骤s1中得到的预处理后的原染料粉体重量的4%~18%。
[0095]
作为本技术的一些实施例,在上述步骤s32中,所述酸性溶液可以为无机酸、有机酸、酸式盐等酸性物质的水溶液,所述酸性溶液中,酸性物质的质量百分含量为0.2%~30%。具体的,所述酸性物质可以为盐酸、硫酸、硫酸铝、羧酸等,因不同酸性物质的酸性强弱不同,所述酸性溶液中酸性物质的质量百分含量可根据需要进行调整,具体以印染时,在附着在纤维素纤维上的酸性物质和染液中的酸性物质的共同作用下,酸性物质能够完全分解纤维素纤维为宜。
[0096]
更加优选的,在上述步骤s31中,可通过图2~12所示的复合装置将混合体系d复合在上述步骤s2制备得到的纤维载体上。
[0097]
具体的,如图2~12所示,所述复合装置包括:
[0098]
外壳体1,其构成所述复合装置的外壁,所述外壳体1内部中空;
[0099]
水平隔板2,其沿水平方向设置在所述外壳体1内,并将所述外壳体1的内部空间分隔成上部空腔3和下部空腔4;
[0100]
所述下部空腔4上设置进口401和导液管402,外部气体等物质能够通过所述进口401进入所述下部空腔4内,所述下部空腔4内设置所述混合体系d,在所述进口401输入的气体的压强作用下,所述下部空腔4内的混合体系d能够通过所述导液管402进入所述上部空
腔3内;
[0101]
所述上部空腔3内填充上述步骤s2制备得到的纤维载体,进入所述上部空腔3内的混合体系d穿过所述纤维载体后,通过设置在所述上部空腔3上的出口301排出。
[0102]
进一步的,所述导液管402的下端插入所述下部空腔4的底部,所述导液管402的上端穿过所述水平隔板2后与所述上部空腔3相连通。
[0103]
进一步的,所述进口401位于所述下部空腔4的下底面上,在所述进口401的上方设置匀气盘403,在通过所述进口401向所述下部空腔4内充入气体时,所述进口401喷出的气体将首先撞击在所述匀气盘403的下表面上,之后改变运动方向、向下运动,待气体的向下的运动速度降为零后,在所述下部空腔4内液体的浮力作用下,通过所述匀气盘403的外边缘和所述外壳体1的内表面之间的间隙向上运动。
[0104]
优选的,所述匀气盘403的直径为所述进口401直径的1.5~3倍。
[0105]
优选的,所述匀气盘403与所述进口401之间的距离可根据所述进口401充入气体的压强或流速进行调整,以使得所述进口401喷出的气体撞击在所述匀气盘403后,向下运动的速度降为零时的位置不低于所述下部空腔4的下底面为宜。
[0106]
作为本技术的一些实施例,在所述下部空腔4内设置安装连接件404,所述安装连接件404的上端与所述下部空腔4的顶面连接、下端与所述匀气盘403连接,所述匀气盘403通过所述安装连接件404悬挂在所述下部空腔4内。优选的,所述安装连接件404和匀气盘403均由刚性材质制备。
[0107]
所述复合装置的使用方法包括步骤:
[0108]
t1,在所述下部空腔4内充入液态流体,如水或预处理后的原染料粉体的水溶液或活性硅酸钙的水溶液,并将所述纤维载体均匀铺设在所述上部空腔3内;
[0109]
t2,打开所述进口401向所述下部空腔4内充气,气体穿过所述下部空腔4内的液态流体后,在所述下部空腔4的上部聚集,同时,在所述下部空腔4内充入气体的压强作用下,所述下部空腔4内的液态流体被压入所述导液管402内,且随着充气的持续,所述导液管402内的液面持续升高,最终将所述下部空腔4内的液态流体压入上部空腔3内;
[0110]
t3,被压入所述上部空腔3内的液态流体与所述上部空腔3内的纤维载体混合、并穿过所述的纤维载体后,通过出口301排出。
[0111]
作为本技术的一些实施例,在所述步骤t1中,可以通过设置在所述下部空腔4侧壁上的进液口、进液管道等向其内充入液态流体。
[0112]
作为本技术的一些实施例,在所述步骤t1中,可以将上述步骤s1制备得到的预处理后的原染料粉体和活性硅酸钙分散于水中、得到混合体系d之后,直接将混合体系d充入所述下部空腔4内。
[0113]
作为本技术的另外一些实施例,在所述步骤t1中,可以在所述下部空腔4内充入去离子水;并在之后的步骤t2中,利用所述进口401向所述下部空腔4内充入的气体将上述步骤s1制备得到的预处理后的原染料粉体和活性硅酸钙颗粒充入下部空腔4内的去离子水中,形成混合体系d。
[0114]
作为本技术的另外一些实施例,在所述步骤t1中,还可以将上述步骤s1制备得到的预处理后的原染料粉体或活性硅酸钙中的一种直接分散于水中,并将该分散液充入所述下部空腔4内;并在之后的步骤t2中,利用所述进口401向所述下部空腔4内充入的气体将预
处理后的纳米原染料粉体和活性硅酸钙颗粒中的另一种充入下部空腔4内的去离子水中,形成混合体系d。
[0115]
优选的,在所述步骤t1中,将上述步骤s1制备得到的预处理后的原染料粉体直接分散于水中,并将该分散液充入所述下部空腔4内;并在之后的步骤t2中,利用所述进口401向所述下部空腔4内充入的气体将活性硅酸钙颗粒充入下部空腔4内的去离子水中,形成混合体系d。通过试验对比发现,采用这种方式进行复合时,出口301排出的水中残余的染料粉体量更少,那么,被纤维载体吸附的染料粉体量则较高。
[0116]
所述复合装置的工作原理如下:在所述下部空腔4内充入气体时,在所述匀气盘403的作用下,所述下部空腔4内不同区域的气体含量将产生差异,具体的,如图4所示,为便于说明,将所述匀气盘403和进口401之间的区域记为k1区域,将所述匀气盘403的外侧和外壳体1之间的区域记为k2,将所述匀气盘403上方的区域记为k3,受到气体的运动、溶解和析出,以及气体扩散路径的影响,所述k1、k2和k3区域的气体含量逐渐降低,这种气体含量的变化将使得所述k1、k2和k3区域的流体之间产生密度差,这种密度差将进一步导致所述k1、k2和k3区域的流体产生相对运动,相对运动使得不同区域的流体能够混合、进而使得所述k1、k2和k3区域的染料颗粒和活性硅酸钙颗粒始终处于运动状态下,不但分散均匀、且不易团聚;同时,相较于常规的机械强力搅拌,由于密度差产生的运动强度适宜,所述活性硅酸钙颗粒能够吸附、并与染料颗粒相结合。之后,在所述下部空腔4内气体压强的作用下,所述下部空腔4内的混合体系d将通过所述导液管402溢流至所述上部空腔3内,溢流能够使得混合体系d产生流动,且流动速度不至过快,这种混合体系d的低速流动,能够为纤维载体吸附混合体系d中的颗粒物提供适宜的接触速度和接触时间。
[0117]
作为本技术的一些实施例,还可以对所述复合装置进行进一步优化,具体的,如图8~12所示,所述上部空腔3内设置竖直隔板302和滤网303,所述导液管402的上端位于所述竖直隔板302的一侧,所述出口301位于所述竖直隔板302的另一侧,所述滤网303沿水平方向设置在所述竖直隔板302上,所述纤维载体位于所述滤网303上,如此,所述导液管402排入所述上部空腔3内的混合体系d必须穿过所述滤网303及其上的纤维载体后,方可流至所述竖直隔板302的另一侧、并通过所述出口301排出。
[0118]
更进一步的,所述滤网303具有两种规格,以所述竖直隔板302为界,位于所述导液管402所在一侧的滤网303的孔径远大于所述混合体系d内颗粒物的粒径、主要起到支撑纤维载体的作用;位于所述出口301所在一侧的滤网303的孔径小于所述混合体系d内颗粒物的粒径,可同时起到支撑纤维载体和过滤的作用。此时,根据情况,在必要的时候,为提高过滤速度,还可以在所述出口301处接入抽滤设备。但事实上,由于进口401进入的少量气体可以通过导液管402进入上部空间3内、并被孔径较小的滤网和其上的纤维素封闭在其中,因此,在使用时,与外部大气压相比,所述上部空间3内可产生微正压的环境,利于过滤的进行。
[0119]
作为本技术的一些实施例,还可以对所述复合装置进行进一步优化,具体的,如图8~12所示,所述下部空腔4内设置环形内壁405,所述环形内壁405位于所述匀气盘403和外壳体1之间,具体为所述环形内壁405位于所述外壳体1的内部,且环绕在所述匀气盘403的外围,所述环形内壁405的下端与所述外壳体1的下底面连接,在所述环形内壁405的上端设置上盖板406,借助所述环形内壁405、外壳体1的下底面和所述上盖板406,可以在所述外壳
体1内围成一个内腔体。
[0120]
更进一步的,在所述环形内壁405的下端设置排液口408,所述排液口408连通所述内腔体和下部空腔4。
[0121]
更进一步的,所述安装连接件404为内部中空的筒状结构,上端穿过所述上盖板406后、延伸至所述水平隔板2的下方,且所述安装连接件404的上端与所述水平隔板2之间具有间隙,使得所述安装连接件404的上端与所述下部空腔4连通;所述安装连接件404的下端与所述匀气盘403密封连接,在所述安装连接件404上设置溢气孔407,所述溢气孔407位于所述上盖板406的下方,且紧邻所述上盖板406的下表面。此时,所述安装连接件404可通过上盖板406进行固定。
[0122]
优选的,所述溢气孔407的开孔面积小于所述进口401的面积,以所述溢气孔407的排气速率小于所述进口401的进气速率为宜。
[0123]
此时,所述复合装置的使用方法包括步骤:
[0124]
t1’,在所述环形内壁405围成的内腔体中充入液态流体,并将所述纤维载体均匀铺设在所述上部空腔3内的滤网303上;
[0125]
t2’,打开所述进口401向所述内腔体内充气,气体穿过所述下部空腔4内的液态流体后,在所述内腔体的上部聚集,在所述内腔体内充入气体的压强作用下,所述内腔体内的液体通过所述排液口408排出;与此同时,聚集在所述内腔体上部的部分气体通过所述溢气孔407进入所述安装连接件404内,并通过所述安装连接件404上端的开口排至所述下部空腔4的上部,最终在所述下部空腔4的上部聚集,由于所述溢气孔407的排气速率小于所述进口401的进气速率,且进入所述上部空腔3内的气体量极少,因此,所述上部空腔3内的气体压强p0<所述下部空腔4内的气体压强p1<所述内腔体内的气体压强p2,在压强差的作用下,所述导液管402内的液面持续升高,最终将所述下部空腔4内的液态流体压入上部空腔3内;
[0126]
t3’,被压入所述上部空腔3内的液体首先进入所述竖直隔板302靠近所述导液管402的一侧,之后通过溢流穿过所述滤网303及其上的纤维载体后,流至所述竖直隔板302靠近出口301的一侧,并通过出口301排出。
[0127]
在所述复合装置中,所述内腔体将所述下部空腔4分隔为两部分,位于所述内腔体内的流体在气体密度差的直接作用下,可实现类似上述k1、k2和k3区域的相对运动;而在流体排至所述内腔体外后,流速减缓,其内的固体颗粒可在所述环形内壁405和外壳体1之间流速较低的流体中再次进行相对长时间的吸附,最终实现染料粉体和活性硅酸钙之间的良好结合。
[0128]
以下通过具体的实施例对上述高分散性纳米分散染料的制备方法进行举例说明:
[0129]
实施例1
[0130]
称取100g通过反应得到的分散蓝bgl原染料,将其溶于1kg乙醇溶液中,过滤去除杂质后,得到有机溶液a;将3kg水和15g助剂混合均匀后,得到水溶液b;其中,所述助剂包含30重量份的木质素磺酸盐、5重量份的萘磺酸甲醛缩合物、3重量份的sp-80、1重量份的有机硅类消泡剂以及0.5重量份的十二烷基苯磺酸钠;将所述水溶液b置于可加热容器中,升温至60℃后,在搅拌下缓慢将所述有机溶液a加入水溶液b中进行混合沉淀反应,将有机溶液a完全加入水溶液b中后,继续搅拌10min,之后将混合液置于超声波细胞破碎机中,在20khz
下进行超声粉碎30min,超声破碎后,通过喷雾干燥除去水和有机溶剂、得到预处理后的原染料粉体。
[0131]
称取预处理后的原染料粉体的重量的20%的天然棉纤维,将天然棉纤维切断至10mm左右后,将天然棉纤维与水按照0.02:1的重量比混合后加入打浆装置中进行打浆0.5h,打浆后得含有纤维素短纤维的浆液;之后向含有纤维素短纤维的浆液中加入碱性物质和浸蚀助剂,搅拌均匀后得含有纤维素短纤维的碱性处理液c,其中,所述碱性处理液c中含有:氢氧化钠0.2g/l、有机硅0.5g/l、分散剂3g/l、丙三醇6g/l;将所述碱性处理液c加热至40℃,在40℃下对其内的纤维素短纤维进行浸蚀处理0.2h后,捞出、水洗后,并沥干至纤维素短纤维的含水率为40%后,将含水纤维素短纤维置于冻干设备中,在零下60℃、压力40pa的冷冻环境中,在10khz的超声波的作用下,冻干0.2h后,得纤维载体。
[0132]
称取预处理后的原染料粉体重量的5%的活性硅酸钙,将其与前述步骤得到的预处理后的原染料粉体和纤维载体置于本技术所述复合装置中形成复合材料,将复合材料沥干后,向沥干后的复合材料上喷淋质量百分含量的10%的盐酸溶液,烘干后,即得本技术所述高分散性纳米分散染料。
[0133]
实施例2
[0134]
称取100g通过反应得到的分散红3b原染料,将其溶于600g乙醇溶液中,过滤去除杂质后,得到有机溶液a;将1500g水和8g助剂混合均匀后,得到水溶液b;其中,所述助剂包含40重量份的木质素磺酸盐、6重量份的萘磺酸甲醛缩合物、4重量份的吐温60、1.5重量份的有机硅类消泡剂以及0.8重份的dynol 607;将所述水溶液b置于可加热容器中,升温至68℃后,在搅拌下缓慢将所述有机溶液a加入水溶液b中进行混合沉淀反应,将有机溶液a完全加入水溶液b中后,继续搅拌25min,之后将混合液置于超声波细胞破碎机中,在30khz下进行超声粉碎50min,超声破碎后,通过喷雾干燥除去水和有机溶剂、得到预处理后的原染料粉体。
[0135]
称取预处理后的原染料粉体的重量的28%的天然棉纤维,将天然棉纤维切断至20mm左右后,将天然棉纤维与水按照0.1:1的重量比混合后加入打浆装置中进行打浆0.6h,打浆后得含有纤维素短纤维的浆液;之后向含有纤维素短纤维的浆液中加入碱性物质和浸蚀助剂,搅拌均匀后得含有纤维素短纤维的碱性处理液c,其中,所述碱性处理液c中含有:氢氧化钠1g/l、有机硅2.5g/l、分散剂3.5g/l、丙三醇8g/l;将所述碱性处理液c加热至47℃,在47℃下对其内的纤维素短纤维进行浸蚀处理1h后,捞出、水洗后,并沥干至纤维素短纤维的含水率为70%后,将含水纤维素短纤维置于冻干设备中,在零下90℃、压力60pa的冷冻环境中,在15khz的超声波的作用下,冻干5h后,得纤维载体。
[0136]
称取预处理后的原染料粉体重量的10%的活性硅酸钙,将其与前述步骤得到的预处理后的原染料粉体和纤维载体置于本技术所述复合装置中形成复合材料,将复合材料沥干后,向沥干后的复合材料上喷淋质量百分含量的20%的硫酸铝溶液,烘干后,即得本技术所述高分散性纳米分散染料。
[0137]
实施例3
[0138]
称取50g通过反应得到的分散蓝bgl原染料和50g通过反应得到的分散黄3gl原染料,将其溶于320g乙醇溶液中,过滤去除杂质后,得到有机溶液a;将530g水和15g助剂混合均匀后,得到水溶液b;其中,所述助剂包含50重量份的木质素磺酸盐、10重量份的萘磺酸甲
醛缩合物、5重量份的吐温60、2重量份的有机硅类消泡剂以及1重份的dynol 607;将所述水溶液b置于可加热容器中,升温至70℃后,在搅拌下缓慢将所述有机溶液a加入水溶液b中进行混合沉淀反应,将有机溶液a完全加入水溶液b中后,继续搅拌30min,之后将混合液置于超声波细胞破碎机中,在60khz下进行超声粉碎60min,超声破碎后,通过喷雾干燥除去水和有机溶剂、得到预处理后的原染料粉体。
[0139]
称取预处理后的原染料粉体的重量的40%的天然竹纤维,将天然竹纤维切断至30mm左右后,将天然竹纤维与水按照0.15:1的重量比混合后加入打浆装置中进行打浆1h,打浆后得含有纤维素短纤维的浆液;之后向含有纤维素短纤维的浆液中加入碱性物质和浸蚀助剂,搅拌均匀后得含有纤维素短纤维的碱性处理液c,其中,所述碱性处理液c中含有:氢氧化钠3g/l、有机硅5g/l、分散剂5g/l、丙三醇10g/l;将所述碱性处理液c加热至50℃,在50℃下对其内的纤维素短纤维进行浸蚀处理3h后,捞出、水洗后,并沥干至纤维素短纤维的含水率为80%后,将含水纤维素短纤维置于冻干设备中,在零下100℃、压力70pa的冷冻环境中,在20khz的超声波的作用下,冻干7h后,得纤维载体。
[0140]
称取预处理后的原染料粉体重量的18%的活性硅酸钙,将其与前述步骤得到的预处理后的原染料粉体和纤维载体置于本技术所述复合装置中形成复合材料,将复合材料沥干后,向沥干后的复合材料上喷淋质量百分含量的10%的盐酸溶液,烘干后,即得本技术所述高分散性纳米分散染料。
[0141]
对比例1
[0142]
称取100g通过反应得到的分散红3b原染料,将其溶于600g乙醇溶液中,过滤去除杂质后,得到有机溶液a;将1500g水和8g助剂混合均匀后,得到水溶液b;其中,所述助剂包含40重量份的木质素磺酸盐、6重量份的萘磺酸甲醛缩合物、4重量份的吐温60、1.5重量份的有机硅类消泡剂以及0.8重份的dynol 607;将所述水溶液b置于可加热容器中,升温至68℃后,在搅拌下缓慢将所述有机溶液a加入水溶液b中进行混合沉淀反应,将有机溶液a完全加入水溶液b中后,继续搅拌25min,之后将混合液置于超声波细胞破碎机中,在30khz下进行超声粉碎50min,超声破碎后,通过喷雾干燥除去水和有机溶剂、得到预处理后的原染料粉体。
[0143]
称取预处理后的原染料粉体的重量的28%的天然棉纤维,将天然棉纤维切断至20mm左右后,将天然棉纤维与水按照0.1:1的重量比混合后加入打浆装置中进行打浆0.6h,打浆后得含有纤维素短纤维的浆液;通过过滤将纤维素短纤维捞出、水洗后,并沥干至纤维素短纤维的含水率为70%后,将含水纤维素短纤维置于冻干设备中,在零下90℃、压力60pa的冷冻环境中,在15khz的超声波的作用下,冻干5h后,得纤维载体。
[0144]
称取预处理后的原染料粉体重量的10%的活性硅酸钙,将其与前述步骤得到的预处理后的原染料粉体和纤维载体置于本技术所述复合装置中形成复合材料,将复合材料沥干后,向沥干后的复合材料上喷淋质量百分含量的20%的硫酸铝溶液,烘干后,即得纳米分散染料。
[0145]
对比例2
[0146]
称取100g通过反应得到的分散红3b原染料,将其溶于600g乙醇溶液中,过滤去除杂质后,得到有机溶液a;将1500g水和8g助剂混合均匀后,得到水溶液b;其中,所述助剂包含40重量份的木质素磺酸盐、6重量份的萘磺酸甲醛缩合物、4重量份的吐温60、1.5重量份
的有机硅类消泡剂以及0.8重份的dynol 607;将所述水溶液b置于可加热容器中,升温至68℃后,在搅拌下缓慢将所述有机溶液a加入水溶液b中进行混合沉淀反应,将有机溶液a完全加入水溶液b中后,继续搅拌25min,之后将混合液置于超声波细胞破碎机中,在30khz下进行超声粉碎50min,超声破碎后,通过喷雾干燥除去水和有机溶剂、得到预处理后的原染料粉体。
[0147]
称取预处理后的原染料粉体的重量的28%的天然棉纤维,将天然棉纤维切断至20mm左右后,将天然棉纤维与水按照0.1:1的重量比混合后加入打浆装置中进行打浆0.6h,打浆后得含有纤维素短纤维的浆液;通过过滤将纤维素短纤维捞出、水洗后,并沥干至恒重后,得纤维载体。
[0148]
称取预处理后的原染料粉体重量的10%的活性硅酸钙,将其与前述步骤得到的预处理后的原染料粉体和纤维载体置于本技术所述复合装置中形成复合材料,将复合材料沥干后,向沥干后的复合材料上喷淋质量百分含量的20%的硫酸铝溶液,烘干后,即得纳米分散染料。
[0149]
对比例3
[0150]
称取100g通过反应得到的分散红3b原染料,将其溶于600g乙醇溶液中,过滤去除杂质后,得到有机溶液a;将1500g水和8g助剂混合均匀后,得到水溶液b;其中,所述助剂包含40重量份的木质素磺酸盐、6重量份的萘磺酸甲醛缩合物、4重量份的吐温60、1.5重量份的有机硅类消泡剂以及0.8重份的dynol 607;将所述水溶液b置于可加热容器中,升温至68℃后,在搅拌下缓慢将所述有机溶液a加入水溶液b中进行混合沉淀反应,将有机溶液a完全加入水溶液b中后,继续搅拌25min,之后将混合液置于超声波细胞破碎机中,在30khz下进行超声粉碎50min,超声破碎后,通过喷雾干燥除去水和有机溶剂、得到预处理后的原染料粉体。
[0151]
称取预处理后的原染料粉体的重量的28%的天然棉纤维,将天然棉纤维切断至20mm左右后,将天然棉纤维与水按照0.1:1的重量比混合后加入打浆装置中进行打浆0.6h,打浆后得含有纤维素短纤维的浆液;之后向含有纤维素短纤维的浆液中加入碱性物质和浸蚀助剂,搅拌均匀后得含有纤维素短纤维的碱性处理液c,其中,所述碱性处理液c中含有:氢氧化钠1g/l、有机硅2.5g/l、分散剂3.5g/l、丙三醇8g/l;将所述碱性处理液c加热至47℃,在47℃下对其内的纤维素短纤维进行浸蚀处理1h后,捞出、水洗后,并沥干至纤维素短纤维的含水率为70%后,将含水纤维素短纤维置于冻干设备中,在零下90℃、压力60pa的冷冻环境中,在15khz的超声波的作用下,冻干5h后,得纤维载体。
[0152]
将前述步骤得到的预处理后的原染料粉体和纤维载体置于本技术所述复合装置中形成复合材料,将复合材料沥干后,向沥干后的复合材料上喷淋质量百分含量的20%的硫酸铝溶液,烘干后,即得纳米分散染料。
[0153]
试验例1
[0154]
将上述实施例1~3制备得到的分散染料分别溶于水后配置成染液,所述染液中含有分散染料0.2g/l、助剂mf0.05g/l,用缓冲溶液将染液的ph值调节至5,取100ml染液、将其加热至70℃时,放入2g聚酯纤维面料在2.02*105pa的压力下进行染色,在30min内将染液的温度升至130℃,并在130℃保温30min后,冷却至90℃得到染色后的织物,并进行取样检测,具体包括:
[0155]
按照gb/t3921-2008对染色后织物的耐水洗色牢度进行检测,按照aatcc117对染色后织物的升华色牢度进行检测,按照aatcc8对染色后织物的耐摩擦色牢度进行检测,按照采用紫外可见分光光度计对染色残液在波长为380~750mm下的色度值,采用gb11914-89化学需氧量-重铬酸盐法测定其染色残液cod值,检测结果见下表1:
[0156]
表1染色性能检测值
[0157]
检测项目实施例1实施例2实施例3耐水洗色牢度4~5级4~5级4~5级升华色牢度4~5级4~5级5级耐摩擦色牢度(干)4~5级4~5级4~5级色度值(ads值)65.470.269.3cod值(mg/l)924876983
[0158]
此外,取上述实施例1~3对应的染色前的染液作为染液样本,同时,为防止染色织物脱落的线屑对试验结果的干扰,另取一份上述实施例1~3对应的染色前的染液,将其分别按照上述染色过程中的高温高压过程进出升温和加压处理,但并不加入聚酯纤维面料,对其按照染色过程进行处理后,作为染色残液样本,对比染色前的染液样本和染色残液样本发现:经过高温高压染色处理过程后,与染色前的染液样本相比,染色残液中活性硅酸钙颗粒含量降至初始含量的1.07%~0.2%,染色残液中纤维素纤维的含量降至初始含量的3%~0.6%,表明所述活性硅酸钙颗粒和纤维素纤维能够在染色过程中产生溶解、酸解、水解或碳化。
[0159]
试验例2
[0160]
分别取1g上述实施例1~3以及对比例1~3制备得到的分散染料,加入1000ml水搅拌至分散均匀后,在室温下静置,每隔15min使用高倍显微镜观察是否有团聚现象的出现,以及裸眼观察沉淀分层出现的时间,结果见下表2:
[0161]
表2分散性能检测结果
[0162][0163]
虽然本发明披露如上,但本发明并非限定于此。在本说明书的描述中,参考术语“一个实施例”、“一些实施例”、“示意性实施例”、“示例”、“具体示例”、或“一些示例”等的描述意指结合该实施例或示例描述的具体特征、结构、材料或者特点包含于本发明的至少一
个实施例或示例中。在本说明书中,对上述术语的示意性表述不一定指的是相同的实施例或示例。而且,描述的具体特征、结构、材料或者特点可以在任何的一个或多个实施例或示例中以合适的方式结合。任何本领域技术人员,在不脱离本发明的精神和范围内,均可作各种更动与修改,因此本发明的保护范围应当以权利要求所限定的范围为准。