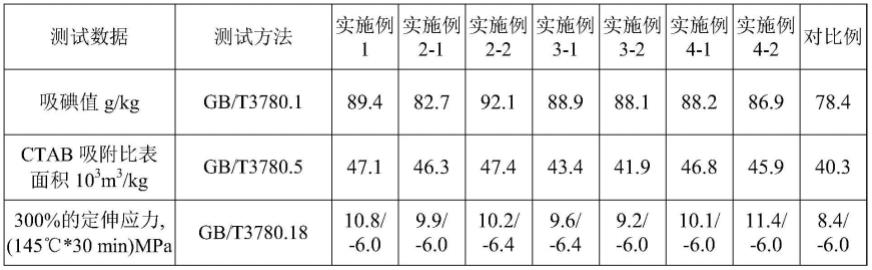
1.本发明涉及资源再利用领域,具体涉及一种报废旧轮胎炭黑深处理工艺及其造粒方法。
背景技术:2.随着汽车使用量的不断增加,轮胎用量也越来越多,造成废旧轮胎的大量堆积,导致严重的黑色污染,废旧轮胎循环利用已是当今世界的重大课题。未来我国废旧轮胎循环利用应该是一个朝阳产业,常见的回收利用废旧轮胎的方式主要包括:轮胎翻新、热裂解、生产胶粉等。由于废旧轮胎的含碳量较高,研究者大多考虑研究制备活性炭、碳黑产品,而通常的将废旧轮胎制备碳黑产品是将废旧轮胎进行热裂解处理后,将热裂解处理下来的残留物作为碳黑产品;然而这样的炭黑产品环境污染程度高,灰分较高、分散性不好,与橡胶相容性差。
3.中国专利cn 109504134 a公开了一种废旧轮胎生产炭黑处理工艺,将去除铁丝的废旧轮胎进行粉碎处理并进行活化、催化裂解制得炭黑,炭黑经过干燥后加入碱性剂,然后进行中和,中和后经过干燥加入浓硫酸进行氧化,然后加入异氰酸酯与炭黑表面的羟基键合,将炭黑与水一同进入预混机中进行混合,然后经过制粒后通过干燥窑进行干燥的到成品。该专利通过对初级炭黑粉碎、分级筛选、表面改性和造粒,增强了与橡胶的相容性。然而其采用浓硫酸对炭黑进行氧化,一方面浓硫酸为强腐蚀性试剂,使用过程的危险性极大;另一方面,浓硫酸具有强氧化性,会与炭黑发生反应消耗掉部分炭黑,尤其是反应会产生二氧化硫气体(c+2h2so4(浓)
→
co2↑
+2so2↑
+2h2o),造成环境污染。还有人提出采用硝酸代替浓硫酸,然而发明人经大量试验发现,硝酸浓度低时不能达到制备炭黑所需氧化效果,浓度太高,硝酸也会与炭黑发生反应消耗掉部分炭黑,同时会产生氮氧化物气体危害环境(c+4hno3(浓)
→
co2↑
+4no2↑
+2h2o)。而其他氧化性酸如盐酸,挥发性太强,不适合使用。
4.因此,如何优化废旧轮胎制备炭黑过程成为了废旧轮胎处理与循环应用的重点研究项目。
技术实现要素:5.本发明的目的在于提供一种报废旧轮胎炭黑深处理工艺及其造粒方法,改善炭黑活化过程危险性强、炭黑损耗大、有危害气体产生等诸多问题。
6.为实现上述目的,本发明采用的技术方案为:一种报废旧轮胎炭黑深处理工艺及其造粒方法,包括如下步骤:
7.(1)前处理:废轮胎裂解碳化工艺处理得到炭渣,经磁选除铁后,研磨至符合工业炭黑标准粒度,得到炭黑前料;
8.(2)活化:将炭黑前料与1.5-2.5mol/l的hclo4水溶液以1g/7-15ml的比例混合,反应0.5-1h,过滤得到酸洗炭黑,再将所述酸洗炭黑用有机溶剂浸泡、干燥,得到炭黑活化料;
9.(3)造粒:将炭黑活化料与碳纳米管、色氨酸和乳糖水溶液混合,搅拌均匀后造粒、
烘干,得到造粒炭黑。
10.本发明机理:轮胎裂解由于工艺和相应的胎源不同,灰分含量较商品炭黑高,一般在10wt.%-25wt.%,灰分会覆盖炭黑的活性点,阻碍炭黑表面与橡胶分子的直接接触,所述用hclo4清洗后,炭黑表面的灰分和油含量均降低,增加炭黑的微孔,使炭黑原来被覆盖的孔重新打开,因为hclo4是强氧化性酸氧化炭黑表面有机物从而出现新的微孔,提高炭黑的吸附能力;且使用的高氯酸浓度低,危险性大大降低,不挥发、不产生危害气体,环境友好。
11.裂解油覆盖在炭黑表面,使得炭黑的比表面积下降,并且裂解油会屏蔽炭黑表面的活性点,阻碍炭黑与橡胶分子链的相互作用,使橡胶定伸应力减小,用有机溶剂浸泡、抽提,将油抽提除去后,比表面积得到进一步提高;另一方面,用hclo4酸洗后,会生成少量有机物附着在炭黑表明,影响酸洗效果,有机溶剂的处理刚好弥补了采用hclo4酸洗的不足,炭黑聚集体之间排列更为疏松,聚集体之间的空隙变大,炭黑的表面微孔、介孔的含量增多,提高炭黑的吸附性。
12.另外,炭黑的表面能比橡胶的表面能高,易发生团聚,常见的高分子饱和脂类由于分子量有限,分散效果很难完全解决团聚现象,而本发明采用色氨酸,其分子量足够大,羟基和羧基等活性官能团足够多,可以与不饱和长链形成氢键,进而接枝到炭黑的长链,减轻炭黑颗粒之间的相互作用,炭黑颗粒之间的团聚程度会因此显著降低,分散性提高,且色氨酸分子中一部分基团可与炭黑无机基团表面反应形成化学键合,另一部分基团则有亲有机的性质,从而将不同性质的材料牢固结合起来。
13.所用乳糖拥有较高的粘结性、螯合性,可以将炭黑与碳纳米管和色氨酸高度融合、聚集造粒,提高造粒效果。
14.所述步骤(1)中,炭黑前料的粒度为300-400目。可以根据使用者的要求对炭黑粒度进行调整。
15.步骤(2)中,炭黑前料与hclo4水溶液混合后,在50℃的恒温水浴中机械搅拌0.5-1小时,冷却后抽滤,水洗至ph 7-9,继续抽滤,得到酸洗炭黑。所述有机溶剂为乙醇、苯、甲苯、丙酮、乙腈、乙醇胺、甲酰胺等一种或几种。酸洗炭黑与有机溶剂按照1g/5-20ml的比例混合,机械搅拌30-45分钟,加热抽提至抽提液为无色,将有机溶剂彻底除去,置于105℃干燥箱中干燥至恒重,得到炭黑活化料。
16.步骤(3)中,先将碳纳米管、色氨酸和乳糖水溶液按照质量比(0.2-8):(0.1-10):(40-100)的比例混合均匀制备成造粒液,再将炭黑活化料与造粒液混合进行造粒。所述乳糖水溶液质量浓度为3-15%,为提高混合效果,乳糖溶液分2-3次加入。炭黑活化料与造粒液按照质量比(5-8):4的比例混合进行造粒,造粒炭黑的粒度为(3
±
0.5)mm。
17.本发明通过对炭黑表面改性和造粒,增强了与橡胶的相容性,达到了工业炭黑的性能指标,提高了热解炭黑的附加值,大幅度增加了企业的经济效益,并且活化过程选用低浓度的高氯酸,不会消耗炭黑,不产生危害气体,安全可靠。
具体实施方式
18.下面结合实施例和试验数据对本发明的技术方案作进一步详述。
19.炭黑前料制备:废轮胎经裂解碳化工艺处理后,热裂解反应器排出炭渣后经预处
理单元磁选除铁机磁性除铁,去除钢丝铁屑杂质,形成粗炭黑并经料仓回收;粗炭黑经炭黑粉粉碎机超细研磨,得到粒度为300目的炭黑前料,供下述实施例和对比例使用。
20.实施例1
21.活化:配制2mol/l的hclo42l,将炭黑前料与酸液按照1g/10ml比例放入活化容器中,在50℃的恒温条件下机械搅拌1小时,冷却、抽滤水洗至ph 7,继续抽滤,收集得到酸洗炭黑;将酸洗炭黑与有机溶剂按照1g/5ml比例放入烧杯中,有机溶剂为乙醇、苯、甲苯、丙酮、乙腈、乙醇胺、甲酰胺混合物,机械搅拌45分钟,加热抽提至抽提液为无色,除去有机溶剂,置于105℃干燥箱中干燥至恒重,得到炭黑活化料。
22.造粒:先将碳纳米管、色氨酸和10%的乳糖水溶液按照质量比为1:1.2:50的比例进行混合,在常压、60℃条件下,在搅拌釜中搅拌1h,其中乳糖水溶液3次加入,搅拌均匀后将得到造粒液,再将炭黑活化料与造粒液按照质量比6:4的比例通过管道输送至造粒机中,搅拌40分钟,造粒湿的炭黑粒子,将炭黑粒子通过出料管送入干燥滚筒进行干燥,得到粒度约为3mm的造粒炭黑。
23.实施例2-1、2-2
24.按照实施例1的方法进行活化、造粒,其中酸洗炭黑与酸液比例分别为1g/15ml、1g/7ml,其他条件和数据相同。
25.实施例3-1、3-2
26.按照实施例1的方法进行活化、造粒,其中,酸洗炭黑与有机溶剂比例分别为1g/10ml、1g/15ml,其他条件和数据相同。
27.实施例4-1、4-2
28.按照实施例1的方法进行活化、造粒,其中,乳糖水溶液浓度分别为5%、15%,其他条件和数据相同。
29.对比例
30.将炭黑前料按照实施例1中记录的造粒过程直接进行造粒,得到造粒炭黑。
31.检测上述实施例和对比例中所得造粒炭黑的各种性能参数并计入下表中:
[0032][0033][0034]
本发明专利对炭黑表面改性和造粒效果很好,通过上表研究数据对比不难发现,与原样未活化造粒炭黑相比,活化再生后造粒的炭黑各项性能明显有较大改善,从炭黑吸
碘值和吸附比表面积研究数据观察,吸碘值为89.4g/kg可以证明炭黑的吸附能力得到较大提高;从45μm筛余物和倾注密度的研究数据即:45μm筛余物为473mg/kg,小于500mg/kg,可以发现本发明对炭黑的造粒率较高,倾注密度为458kg/m3,表明明显减小了炭黑单位质量的体积,造粒质量改善较为显著;从300%的定伸应力的研究数据可以证明本发明增强了造粒炭黑与橡胶的相容性,活性增强,定伸应力变大,达到了工业炭黑的使用性能指标,提高了炭黑的使用领域,增加了炭黑的经济效益,实现资源循环综合利用,积极响应了国家十四五规划中“碳减排、碳达峰”的政策。